Engine Testing Overview
Total Page:16
File Type:pdf, Size:1020Kb
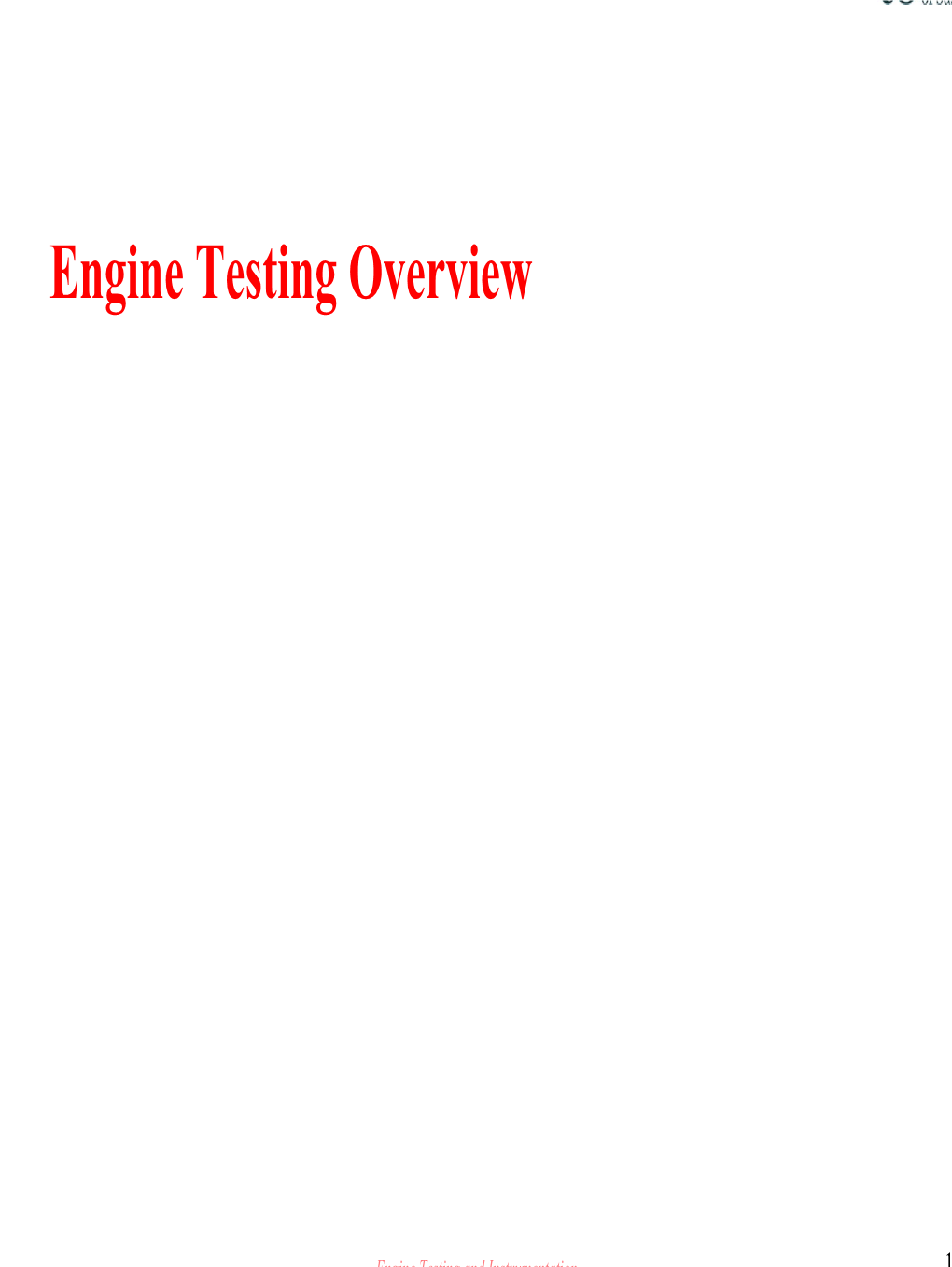
Load more
Recommended publications
-
Readout No.42E 08 Feature Article
eature Article Wheel Slip Simulation for Dynamic Road Load Simulation FFeatureApplication Article Application ReprintofReadoutNo.38 Wheel Slip Simulation for Dynamic Road Load Simulation Increasingly stringent fuel economy standards are forcing automobile Bryce Johnson manufacturers to search for efficiency gains in every part of the drive train from engine to road surface. Safety mechanisms such as stability control and anti-lock braking are becoming more sophisticated. At the same time drivers are demanding higher performance from their vehicles. Hybrid transmissions and batteries are appearing in more vehicles. These issues are forcing the automobile manufacturers to require more from their test stands. The test stand must now simulate not just simple vehicle loads such as inertia and windage, but the test stand must also simulate driveline dynamic loads. In the past, dynamic loads could be simulated quite well using Service Load Replication (SLR*1). However, non-deterministic events such as the transmission shifting or application of torque vectoring from an on board computer made SLR unusable for the test. The only way to properly simulate driveline dynamic loads for non- deterministic events is to provide a wheel-tire-road model simulation in addition to vehicle simulation. The HORIBA wheel slip simulation implemented in the SPARC power train controller provides this wheel-tire-road model simulation. *1: Service load replication is a frequency domain transfer function calculation with iterative convergence to a solution. SLR uses field collected, time history format data. Introduction frequency. The frequency will typically manifest itself between 5 and 10 Hz for cars and light trucks. (see To understand why tire-wheel simulation is required, we should first understand the type of driveline dynamics that need to be reproduced on the test stand. -
Inertial Dynamometer for Shell Eco-Marathon Engine: Validation
ICEUBI2019 International Congress on Engineering — Engineering for Evolution Volume 2020 Conference Paper Inertial Dynamometer for Shell Eco-marathon Engine: Validation Daniel Filipe da Silva Cardoso, João Manuel Figueira Neves Amaro, and Paulo Manuel Oliveira Fael Universidade da Beira Interior Abstract This paper aims to validate the construction of an inertia dynamometer. These types of dynamometers allow easy characterization of internal combustion engines. To validate the dynamometer, tests were carried out with the same engine (Honda GX 160) installed in the UBIAN car and kart, which after calculating the inertia and measuring engine acceleration in each test performed, allows to create the torque characteristic curve from the engine. Keywords: Inertia, Dynamometer, Torque, Flywheel, UBIAN Corresponding Author: Daniel Filipe da Silva Cardoso [email protected] Received: 26 November 2019 1. Introduction Accepted: 13 May 2020 Published: 2 June 2020 This work was performed at the University of Beira Interior in order to study the engine Publishing services provided by currently used at UBIAN car. This is a car build by a team that participate in Shell Knowledge E Ecomarathon. The engine used is Honda GX 160 [1]. Daniel Filipe da Silva Cardoso et al. This article is distributed This article intends to focus on demonstrating and validating a simple system of under the terms of the Creative engine characterization. To make this validation three types of tests will be performed: Commons Attribution License, the first one coupling the engine on inertia dynamometer; the second one is done using which permits unrestricted use and redistribution provided that the whole vehicle; a third test, performed on a go kart, will be used as a control test. -
Autodyn Series Brochure
AUTODYN SERIES AUTODYN SERIES CHASSIS DYNAMOMETERS HAND HELD CONTROLLER EDDY CURRENT ABSORBERS VERSATILE Simple and accessible control To simulate real-world driving With upgradeable options and while testing conditions wheel base adjustment We Make It Better 1.262.252.4301 | www.powertestdyno.com | [email protected] | Sussex, WI, USA FEATURES THAT MATTER Push-Button Wheel Base Adjustment Push-button wheel base adjustment is not only convenient; it’s also the right way to accommodate AWD vehicles because it allows the vehicles to be loaded in the same position on the rolls every time. Non-adjustable cradle rolls systems that simply stack rolls together to accommodate AWD vehicles produce inconsistencies in testing as one vehicle might land between rolls and another may land on top of the rolls, creating a different testing environment for each vehicle. Trunnion Mounted Differentials Precision, trunnion mounted differentials allow individual torque measurement of each axle (AWD models) so you can see total torque through the RPM range and also the torque split between the front and rear axles to tune for drivability. They also allow accurate measurement of dyno losses so the inertia of the dyno does not affect the test results. Further, it means SuperFlow® dynos are not susceptible to inaccuracies based on heat in the dyno components like the differentials and couplings. 2 Eddy Current Absorption High capacity eddy current absorbers allow for both inertia and loaded testing. On all models, they’re coupled to each other and to the rolls with positive mechanical couplings like differentials and driveshafts. This allows accurate measurement of parasitic horsepower losses in each individual dyno we manufacture. -
Design and Implementation of a Small Electric Motor Dynamometer for Mechanical Engineering Undergraduate Laboratory Aaron Farley University of Arkansas, Fayetteville
University of Arkansas, Fayetteville ScholarWorks@UARK Theses and Dissertations 5-2012 Design and Implementation of a Small Electric Motor Dynamometer for Mechanical Engineering Undergraduate Laboratory Aaron Farley University of Arkansas, Fayetteville Follow this and additional works at: http://scholarworks.uark.edu/etd Part of the Electro-Mechanical Systems Commons Recommended Citation Farley, Aaron, "Design and Implementation of a Small Electric Motor Dynamometer for Mechanical Engineering Undergraduate Laboratory" (2012). Theses and Dissertations. 336. http://scholarworks.uark.edu/etd/336 This Thesis is brought to you for free and open access by ScholarWorks@UARK. It has been accepted for inclusion in Theses and Dissertations by an authorized administrator of ScholarWorks@UARK. For more information, please contact [email protected], [email protected]. DESIGN AND IMPLEMENTATION OF A SMALL ELECTRIC MOTOR DYNAMOMETER FOR MECHANICAL ENGINEERING UNDERGRADUATE LABORATORY DESIGN AND IMPLEMENTATION OF A SMALL ELECTRIC MOTOR DYNAMOMETER FOR MECHANICAL ENGINEERING UNDERGRADUATE LABORATORY A thesis submitted in partial fulfillment of the requirements for the degree of Master of Science in Mechanical Engineering By Aaron Farley University of Arkansas Bachelor of Science in Mechanical Engineering, 2001 May 2012 University of Arkansas ABSTRACT This thesis set out to design and implement a new experiment for use in the second lab of the laboratory curriculum in the Mechanical Engineering Department at the University of Arkansas in Fayetteville, AR. The second of three labs typically consists of data acquisition and the real world measurements of concepts learned in the classes at the freshman and sophomore level. This small electric motor dynamometer was designed to be a table top lab setup allowing students to familiarize themselves with forces, torques, angular velocity and the sensors used to measure those quantities, i.e. -
ECE 40600 Capstone Senior Design Project II 5HP Dynamometer Retrofit
Purdue University Fort Wayne Department of Electrical and Computer Engineering ECE 40600 Capstone Senior Design Project II 5HP Dynamometer Retrofit Shehryar Azam <[email protected]> Benjamin Edwards <[email protected]> Joshua Durham <[email protected]> Matthew Gonzalez <[email protected]> Project Advisor: Dr. Chao Chen<[email protected]> Date: 05/03/2021 1 Table of Contents Acknowledgements . 7 Abstract . 8 1 Problem Statement . 9 1.1 Literature Survey . 9 1.2 Customer-Defined Constraints and Given Requirements . 9 1.3 Customer Needs and Functional Requirements for Design . 10 1.4 Applicable Engineering Standards . 11 1.5 Define Use Cases . 11 1.6 System Boundary . 12 1.7 Interface Requirements and Definitions. 1 4 2 Conceptual Design. 1 5 2.1 Product Design Decomposition (PDD). 1 5 2.2 Decision List. 17 2.3 Conceptual Design of Alternatives – Physical Solutions (PS) Selection . 18 3 Summary of the Evaluation of Design Alternatives. 20 3.1 Criteria for Selection and Testing Among Alternatives. 20 3.2 Evaluation of Software Design Alternatives . 21 3.3 Evaluation of Torque Transducer Alternatives . 22 3.4 Summary of Preliminary Design . .23 4 Detailed Design. 2 4 4.1 Design Description and Drawings . 2 4 4.2 Evaluation. 31 5 Cost Analysis. .. 32 5.1 BOM (Bill of Materials) . .. 32 6 Design Changes. .. 34 6.1 PC Hardware Change . .. 34 2 6.2 BOM Update. 35 6.3 Software Structure Change. 37 7 Building Process . .. 38 7.1 Hardware Construction . .. 38 7.2 Software Implementation. .. 46 7.3 User Interface. .. 51 7.4 Documentation. .. 54 8 Risk Analysis and Test Plan. -
We Make It Better
We Make It Better 262-252-4301 N60 W22700 Silver Spring Dr. 262-246-0436 Sussex, WI 53089 USA [email protected] www.powertestdyno.com ENGINE DYNAMOMETERS An engine dynamometer is a device used to test an engine that has been removed from a vehicle, ship, generator, or various other pieces of equipment. The purpose is to confirm performance before the engine is installed. Dynamometers can help facilities troubleshoot by determining an engine’s functionality while under load. They also verify the quality of builds, rebuilds, or repairs in a controlled environment before engines are put into use. Water Brake Eddy Current AC Series Water brake dynamometers are Specifically designed for small The AC Series Dynamometer ideal for higher power engines displacement diesel engines, generates electricity as a means with options ranging from 350 the Eddy Current (EC-Series) to absorb power from an engine to 10,000 HP. These dynos are engine dynamometer features under test. AC Dynos provide most cost effective for larger air-cooled, in-line eddy current incomparable responsiveness for internal combustion engines absorption utilizing electro- precision testing and can be used and electric motors. magnetic resistance. to supplement electrical power. Water Brake Dynamometers Our largest water brake dynamometers, the Power Test H36- Series engine dynos are designed for high torque, low speed diesel engine applications. They can be found servicing mining, construction, power generation, and marine propulsion industries around the world. Features • For high -
Measuring the Performance Characteristics of a Motorcycle
August 2019, Vol. 19, No. 4 MANUFACTURING TECHNOLOGY ISSN 1213–2489 Measuring the Performance Characteristics of a Motorcycle Adam Hamberger, Milan Daňa Regional Technological Institute, University of West Bohemia – Faculty of Mechanical Engineering, Univerzitní 8, Pilsen 306 14, Czech Republic. E-mail: [email protected] This work deals with an experiment, whose output is the comparison of power characteristics which were meas- ured in three ways. The first way used a commercially manufactured dynamometer. For the second measurement, a special dynamometer with our own computing system and a sensor within this project was created. The last way of measuring the performance characteristics was done without a dynamometer. The measurement works on the principle of acceleration the spinning of a flywheel. Due to this, the measuring is called an acceleration test. The basic principles are described before the experiment in order to grasp the characteristics. All explanations are based on schemes and easy mathematical and differential formulas to describe the construction of the dynamom- eter and the principle of its functions from the engine to the computer. The relations between published and un- published quantities defining engine dynamics are explained here. In the end, this work points to possible and intended measuring failures which are an infamous practice at many measuring stations. Keywords: Dynamometer, power characteristics, driving forces, torque, performance. Introduction These forces are divided into two basic sorts. The first one is dependent on velocity and it can be written as: All vehicle engines overcome resistances on the road. 2 Fres( v )= c21 v + c v + ( c val + sin( )) m g [ N ], (1) where: φ … climb angle [rad], v … velocity [m/s], m … full weight[kg], 2 c1,c2,croll … coefficients [-], g … gravity acceleration [m/s ]. -
Special AVL the Chassis Dynamometer As a Development Platform
Special AVL The Chassis Dynamometer as a Development Platform A Common Testing Platform for Engine and Vehicle Testbeds 40 Total Energy Efficiency Testing – The Chassis Dynamometer as a Mechatronic Development Platform 45 “Easy and Objective Benchmarking“ 49 Interview with Christoph Schmidt and Uwe Schmidt, AVL Zöllner Innovative Use of Chassis Dynamometers for the Calibration of Driveability 51 Offprint from ATZ · Automobiltechnische Zeitschrift 111 (2009) Vol. 11 | Springer Automotive Media | GWV Fachverlage GmbH, Wiesbaden SPECIAL AVL A Common Testing Platform for Engine and Vehicle Testbeds In order to achieve time-savings during vehicle development, companies are increasingly looking to run the same tests on the engine test bed as on the chassis dynamometer. The aim is to correlate results in order to highlight differences and their influencing factors, as well as to verify the engine test bed results, and to achieve the additional benefit of reusing existing tests. A common test automation and data platform is required. The article describes an application in which this has been achieved for emissions certification testing and discusses the value of upgrading the chassis dynamometer to a higher level of automation. 2 ATZ 11I2009 Volume 111 1 The Synergies between Engine, – the ability to accurately simulate the The Authors Driveline and Vehicle Testbeds missing vehicle components on the testbed (e.g.: the vehicle powertrain The product development processes at on an engine testbed) Charles Kammerer MSc. OEMs and the component development – the ability to reproduce environmen- is Product Manager process of tier 1 suppliers rely on exten- tal conditions realistically for Test System Auto- sive testing phases of the different pow- – the ability to support iterative devel- mation at AVL List ertrain components and of the complete opment loops efficiently between the GmbH in Graz (Austria). -
Transient Maneuvers and Pressure Analysis on an Automotive Torque Converter
Michigan Technological University Digital Commons @ Michigan Tech Dissertations, Master's Theses and Master's Reports 2021 Transient Maneuvers and Pressure Analysis on an Automotive Torque Converter Abigail A. Hempy Michigan Technological University, [email protected] Copyright 2021 Abigail A. Hempy Recommended Citation Hempy, Abigail A., "Transient Maneuvers and Pressure Analysis on an Automotive Torque Converter", Open Access Master's Thesis, Michigan Technological University, 2021. https://doi.org/10.37099/mtu.dc.etdr/1186 Follow this and additional works at: https://digitalcommons.mtu.edu/etdr Part of the Other Mechanical Engineering Commons TRANSIENT MANEUVERS AND PRESSURE ANALYSIS ON AN AUTOMOTIVE TORQUE CONVERTER By Abigail A. Hempy A THESIS Submitted in partial fulfillment of the requirements for the degree of MASTER OF SCIENCE In Mechanical Engineering MICHIGAN TECHNOLOGICAL UNIVERSITY 2021 © 2021 Abigail A. Hempy This thesis has been approved in partial fulfillment of the requirements for the Degree of MASTER OF SCIENCE in Mechanical Engineering. Department of Mechanical Engineering-Engineering Mechanics Thesis Co-Advisor: Jason Blough Thesis Co-Advisor: Darrell Robinette Committee Member: Carl Anderson Department Chair: William W. Predebon Table of Contents List of figures .................................................................................................................... vii List of tables ..................................................................................................................... xvi -
High Dynamic Wheel Replacement Dynamometer
High Dynamic Wheel Replacement Dynamometer System Content Introducing the MTS Series 323 MAST ADAMS dynamic models are easily MTS LOW INERTIA DYNAMOMETERS Virtual Test Lab. This new technology from inte grated into the MTS MAST Virtual MTS lets you evaluate a broad range of Test Lab. This allows you to simulate » Permanent Magnet dynamometer ADAMS based automotive components physical system simulations prior to » In-line torque measurement and subsystems models using an ADAMS actual physical testing. The virtual tests » Speed measurement model of the test system to apply the are run using the same interface that you » Lubrication and cooling support vibra tion forces in exactly the same manner will use during the physical test. FlexTest® as in a physical test. or RPC® (Remote Parameter ControlTM) MTS POWER ELECTRONICS control systems and MTS hydraulics are Typical automotive components tested on » Vector control drive modeled in this system giving you the the Series 323 Virtual MAST and standard » Isolation transformer most accurate reproduction of testing loads MAST systems include radiators, instrument for validation of component or vehicle » Power cabling panels, engine mounts, fuel tanks, seats models. Training and system operational and similar components and assemblies. MTS DIGITAL CONTROLLER issues can also be accomplished prior to » Speed and torque control The MTS MAST Virtual Test Lab, like the completion of phys ical prototypes so your » Advanced controls such as inertia actual system, provides up to six degrees operators can begin testing as soon as a simulation, traction simulation of freedom of motion and up to three specimen is available. Using the MAST and real time vehicle simulation in aux iliary control channels. -
Dynamometer DYN 6WD I Turntable TT 11.0-30T-DYN
Technical Description Dynamometer DYN 6WD_I Integrated into Turntable TT 11.0-30t-DYN Specifications: - Integrated dynamometer into turntable - For use in anechoic chambers for EMI and EMC measurements - 3 active axles, for cars and busses with rear /front – or four wheel drive - 6 independently controllable roller pairs - Independent rotation of dynamometer and turntable - Various designs and specifications on customer request available - Cooling fan, robot system, exhaust extraction system, and more available Information presented enclosed is subject to change as product enhancements are made regularly. Please contact maturo for current specifications. Pictures included are for illustration purposes only and do not represent all possible configurations. Index 1) Dynamometer Page 3 1.1) Technical Data Page 3 1.2) Brief Description Page 4 2) Software and functions of Dynamometer Page 10 3) Software Description Page 11 3.1) Operation modes Page 11 3.2) Constant Velocity Page 11 3.3) Gradient Mode Page 12 3.4) Road Simulation Page 14 3.5) Measurements Page 15 3.6) Block Rollers Page 16 4) Turntable Page 17 4.1) Technical Data Page 17 4.2) Brief Description Page 18 5) Noise measurement result of system Page 23 6) Utility requirement for the system Page 26 7) Exhaust Extraction System Page 27 8) Option: Power supply with Energy Chain Page 28 9) Robot Page 29 10) Controller NCD Page 31 10.1) Technical Data Page 31 10.2) Brief Description Page 32 2 1) Dynamometer DYN 6WD_I Fig.: Turntable with integrated dynamometer at Nissan, USA 1.1) Technical Data: Permissible axle load 15.000 kg (each axle) Max speeds for cars with axle load of 1500 kg 150 km/h for busses 100 km/h Speed measurement accuracy +/- 0.1 km/h Wheel track between the front wheels 1000 to 2900 mm Wheelbase between axles: Axle 1 to axle 2 (for 2 axle cars and small busses) 2200 mm – 5300 mm Axle 1 to axle 3 (for 2 axle buses) 4100 mm – 6500 mm Axle 2 to axle 3 (for 3 axle buses) 1200 mm – 1900 mm Axle distance between axle 1 and 3 max. -
Use of Engine Performance Testing As a Laboratory Experiment
Session 2756 USE OF ENGINE PERFORMANCE TESTING AS A LABORATORY EXPERIMENT Emin Yılmaz Department of Technology University of Maryland Eastern Shore Princess Anne, MD 21853 (410)651-6470 E-mail: [email protected] Abstract The goal of the “ETME 499-Independent Research in Mechanical Engineering Technology” course is to introduce students to designing, manufacturing, upgrading, repairing and testing mechanical systems. The goal of laboratory part of “EDTE 341-Power and Transportation” course is to service small and/or large internal combustion engines. The purpose of this project was to service the gasoline engine, the engine dynamometer attached to it, and carry out some engine performance tests. If successful, the engine performance testing will be incorporated into the “EDTE 341-Power and Transportation course” or the “ETME 301-Thermodynamics and Heat Power” course as one or more laboratory experiments. EDTE 341 and ETME 301 are technical elective and required courses, respectively, for Mechanical Engineering Technology (MET) students. The gasoline engine was disassembled and serviced as a requirement for the laboratory part of the EDTE 341 course. Servicing of the engine-dynamometer system was completed as an ETME 499 project. Instrumentation for the fuel consumption measurements were added and the measurements were carried out. The results indicate that, at constant load, as the engine speed was increased the fuel consumption increased. The same trend was seen at constant speed; the fuel consumption increased as the load was increased. Simulated fuel economy (miles/gal) graph indicate that the engine economy was about flat at higher loads, but, was decreasing slightly at low loads when the engine speed was increased beyond about 1500 rpm.