A Theoretical and Experimental Study of the Traction Properties of Agricultural Gantry Systems
Total Page:16
File Type:pdf, Size:1020Kb
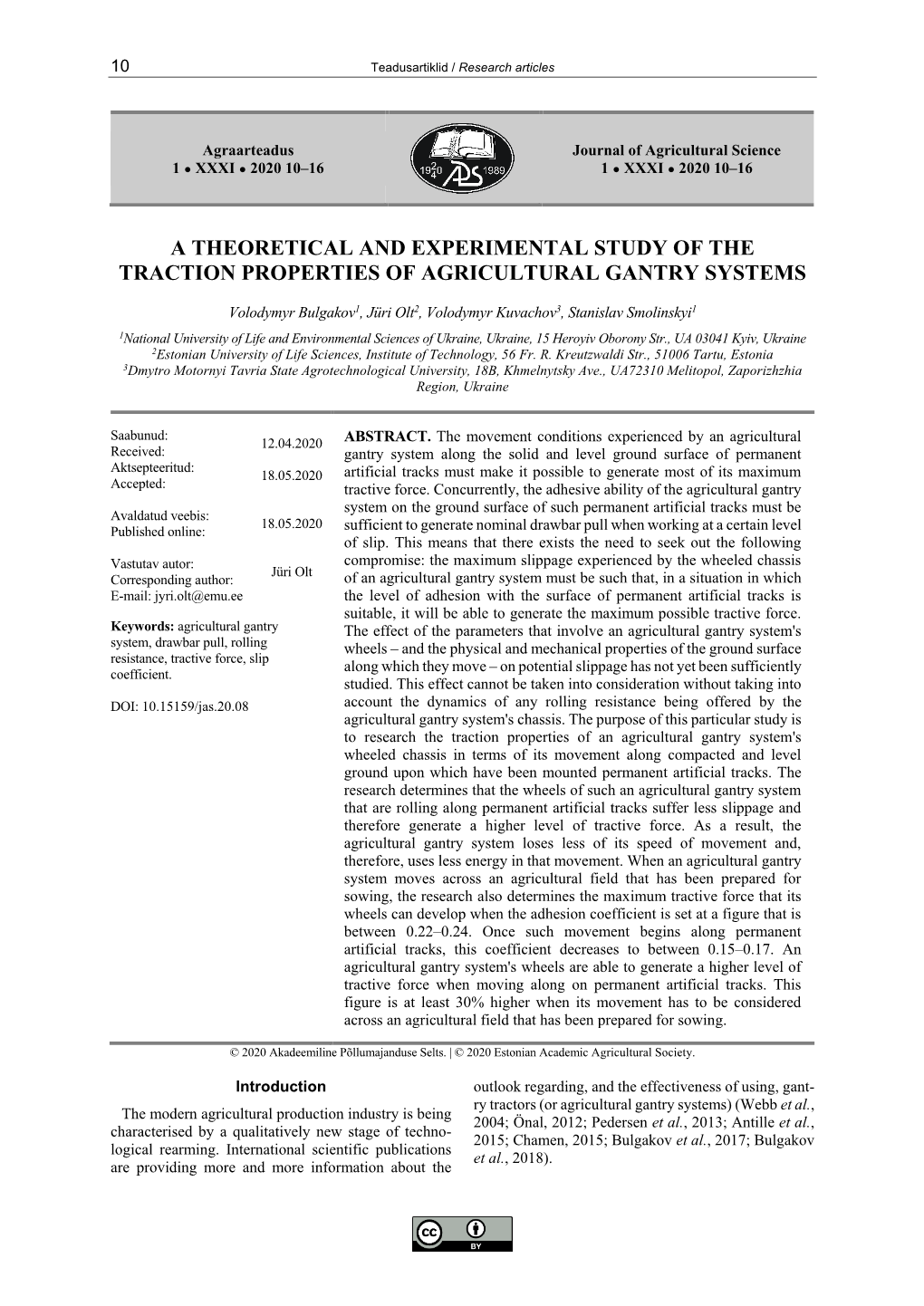
Load more
Recommended publications
-
1. What Is Uptis and What Advantages Does It Offer?
Frequently Asked Questions 1. What is Uptis and what advantages does it offer? Uptis (acronym standing for “Unique Puncture-proof Tire System”) is an assembled airless wheel structure. Uptis has been made possible through Michelin’s mastery and expertise with tire mechanics and high-tech materials. It also represents an evolution of Michelin’s expertise in TWEEL technology. Uptis can be thought of as the first in a new generation of airless solutions. This technology for passenger vehicles offers a number of advantages: ▪ Car drivers feel safer and more secure on the road due to the reduced risk of flat tires and other air loss failures that result from punctures or road hazards. ▪ Fleet owners and professional vehicle drivers optimize their business productivity (no downtime from flats, near-zero levels of maintenance). ▪ Raw material use is reduced, which in turn reduces waste. 2. Why do car drivers feel more at ease with Uptis? Uptis is designed to be impervious to traditional tire failures due to air loss. It does not use compressed air. It therefore eliminates the need for regular inflation pressure maintenance. 3. What is the strategy behind Uptis? Uptis represents Michelin’s vision for the future of mobility. Michelin illustrated its vision of sustainable mobility through the Vision concept1, which the Group unveiled at the Movin’On World Summit on Sustainable Mobility in 2017. Uptis shows how Michelin is adhering to its roadmap for research and development, which comprises these four main pillars of innovation: Airless, Connected, 3D-printed and 100% Sustainable (i.e., renewable or bio-sourced materials). -
Module 2: Dynamics of Electric and Hybrid Vehicles
NPTEL – Electrical Engineering – Introduction to Hybrid and Electric Vehicles Module 2: Dynamics of Electric and Hybrid vehicles Lecture 3: Motion and dynamic equations for vehicles Motion and dynamic equations for vehicles Introduction The fundamentals of vehicle design involve the basic principles of physics, specially the Newton's second law of motion. According to Newton's second law the acceleration of an object is proportional to the net force exerted on it. Hence, an object accelerates when the net force acting on it is not zero. In a vehicle several forces act on it and the net or resultant force governs the motion according to the Newton's second law. The propulsion unit of the vehicle delivers the force necessary to move the vehicle forward. This force of the propulsion unit helps the vehicle to overcome the resisting forces due to gravity, air and tire resistance. The acceleration of the vehicle depends on: the power delivered by the propulsion unit the road conditions the aerodynamics of the vehicle the composite mass of the vehicle In this lecture the mathematical framework required for the analysis of vehicle mechanics based on Newton’s second law of motion is presented. The following topics are covered in this lecture: General description of vehicle movement Vehicle resistance Dynamic equation Tire Ground Adhesion and maximum tractive effort Joint initiative of IITs and IISc – Funded by MHRD Page 1 of 28 NPTEL – Electrical Engineering – Introduction to Hybrid and Electric Vehicles General description of vehicle movement The vehicle motion can be completely determined by analysing the forces acting on it in the direction of motion. -
Lowering Fleet Operating Costs Through Fuel
LOWERING FLEET OPERATING KEY TAKEAWAYS COSTS THROUGH FUEL EFFICIENT Taking rolling resistance, maintenance, TIRES AND RETREADS wheel position and tires, both new and WHAT YOU NEED TO KNOW TO RUN LEANER retread, into account allows companies to maximize fuel efficiency. Author: Josh Abell, PhD • Rolling resistance has a direct and significant correlation to the fuel A retreaded tire can be just as fuel efficient, economy of the vehicle. or even better, than a new tire. • Tires become more fuel efficient as they are worn due to lessened Rolling Resistance: Why it Matters rolling resistance. Rolling resistance is a measurement of the energy it takes to roll a tire on a surface. • Even among new and retread tires For truck tires, rolling resistance has a direct and significant correlation to the fuel claiming to be Smartway certified, economy of the vehicle. Whether you run a single truck or an entire fleet, tire rolling actual rolling resistance will vary. resistance is a crucial element that should be taken into account to minimize fuel costs. Since fuel costs are one of the biggest expenses in trucking operations, as tire rolling resistance decreases, your savings add up. Tire rolling resistance is measured in a lab using realistic and well-established test parameters relied upon by tire/vehicle manufacturers and government regulators. From this testing, original tires and retreaded tires can be quantified by a rolling resistance coefficient, known as “Crr.” The lower the Crr, the better. Studies have shown that a reduction in Crr can result in real-world fuel savings. For example, a 10% reduction in Crr for your truck tires can reduce your fuel consumption by 3%, and lead to savings of $1,000 or more per truck per year.1 © 2017 Bridgestone Americas Tire Operations, LLC. -
Minimising Fuel Consumption of a Series Hybrid Electric Railway Vehicle Using Model Predictive Control
Master of Science Thesis in Electrical Engineering Department of Electrical Engineering, Linköping University, 2017 Minimising Fuel Consumption of a Series Hybrid Electric Railway Vehicle Using Model Predictive Control Niklas Sundholm Master of Science Thesis in Electrical Engineering Minimising Fuel Consumption of a Series Hybrid Electric Railway Vehicle Using Model Predictive Control Niklas Sundholm LiTH-ISY-EX--17/5095--SE Supervisor: Måns Klingspor isy, Linköping University Keiichiro Kondo Department of Electrical and Electronic Engineering, Chiba University Examiner: Martin Enqvist isy, Linköping University Automatic Control Department of Electrical Engineering Linköping University SE-581 83 Linköping, Sweden Copyright © 2017 Niklas Sundholm Abstract With the increasing demands on making railway systems more environmentally friendly, diesel railcars have been replaced by hybrid electric railway vehicles. A hybrid system holds a number of advantages as it has the possibility of recuperat- ing energy and allows the internal combustion engine (ice) to be run at optimal efficiency. However, to fully utilise the advantages of a hybrid system the hybrid electric vehicle (hev) is highly dependent on the used energy management strat- egy (ems). In this thesis, the possibility of minimising the fuel consumption of the series hy- brid electric railway vehicle, Ki-Ha E200, has been studied. This has been done by replacing the currently used ems, based on heuristics, with a model predictive controller (mpc). The heuristic ems and the mpc have been evaluated by compar- ing the performance results from three different test cases. The performance of the implemented mpc seems promising as it yields more optimal operation of the ice and improved control of the battery state of charge (soc). -
Vehicle and Trailer Tyre Replacement Policy Version
Vehicle and Trailer Tyre Replacement Policy Version 4.1 Date: 1st March 2021 Review Date: 1st March 2022 Owner Name Ruth Silcock Job title Head of Fleet Supply & Demand Mobile 07894 461702 Business units covered This policy applies to all Royal Mail Group vehicles. RM Fleet Policy document – Vehicle and trailer tyre replacement policy Page 1 of 13 Contents 1. Scope 2. Introduction 3. Policy 4. Responsibilities 5. Consequences 6. Change control 7. Glossary 8. References 9. Summary of changes to previous policy Appendix 1 Tread Type Positioning Appendix 2 Example of Re-torque Stamp RM Fleet Policy document – Vehicle and trailer tyre replacement policy Page 2 of 13 1. Scope This policy covers all vehicles and trailers used within RM Group. 2. Introduction 2.1 Tyre condition It is important for drivers, managers and technical staff to understand the legal requirements for tyre condition. Several regulations govern tyre condition. Listed below is a basic outline of the principal points: • Tyres must be suitable* for the vehicle/trailer it is being fitted to and they must be inflated to the correct pressures as recommended by either the vehicle or tyre manufacturer . *Suitability = correct size, correct load specification, speed rating and direction if applicable • No tyre shall have a break in its fabric or cut deep enough to reach or penetrate the cords. No cords must be visible either on the treaded area or on the side wall. No cut must be longer than 25 mm or 10% of the tyre’s section width, whichever is the greater. • There must be no lumps, bulges or tears caused by separation of the tyre’s structure. -
MICHELIN® Smartway® Verified Retreads Michelin Supports the U.S
MICHELIN® SmartWay® Verified Retreads Michelin supports the U.S. Environmental Protection Agency’s (EPA) SmartWay® strategy of including retread products with new tires to reduce the fuel consumption, and greenhouse gas emissions, of line-haul Class 8 trucks. Additionally, SmartWay verified MICHELIN® retreads are compliant with the California Air Resources Board (CARB) Greenhouse Gas regulation for low rolling resistance tires. MICHELIN® SmartWay® low-rolling resistance retreads reduce fleet operating costs by saving fuel and extending the life of the tire. SmartWay also aligns with Michelin’s core value of respect for the environment. More information about the SmartWay® program as well as verified low rolling resistance tires and retreads can be found at epa.gov/smartway. SmartWay® Verified DRIVE POSITION RETREADS MICHELIN® MICHELIN® MICHELIN® MICHELIN® X ONE® LINE ENERGY D X® LINE ENERGY D X ONE® XDA-HT® X® MULTI ENERGY D Pre-Mold Retread Pre-Mold Retread Pre-Mold Retread Pre-Mold Retread • No compromise fuel efficiency(1) • No compromise fuel efficiency(2) • Aggressive lug-type tread design • Guaranteed 25% longer tread life*, ® and mileage delivered by the Dual and wear resistance with Dual • Increased traction with exceptional SmartWay fuel Energy Compound Tread, with a Compound Tread Technology, efficiency(1) due to Dual Energy precisely balanced Fuel and Mileage delivering a top Mileage layer over • Increased tread wear Compound tread technology layer on top of a cool running Fuel a cool running Fuel and Durability • Optimized -
Measurement of Tractive Force in the Creep Region and Maximum Adhesion Control of High Speed Railway Systems Abstract 1. Introd
Measurement of Tractive Force in the Creep Region and Maximum Adhesion Control of High Speed Railway Systems Atsuo Kawamura (Yokohama National University, Japan) Meifen Cao (Corporation for Advanced Transport & Technology, Japan) Yosuke Takaoka, Keiichi Takeuchi,Takemasa Furuya, KantaroYoshimoto (Yokohama National University, Japan) Abstract The acceleration and deceleration rate of the train depend on the tractive force. When the wheels of the train slip on the rails, the torque is decreased to avoid the continuous slipping. This reason is that the tractive coefficient between the wheels and the rails has a peak at a certain slip velocity. But this adhesive phenomenon is not clearly examined or analyzed. Thus we have developed a new adhesion test equipment.In this paper, we measured the tractive force with this equipment, and clarified the adhesive phenomenon. Then we proposed a new tractive force control and verified the effectiveness of the proposed control scheme. 1. Introduction The strong demands for Shinkansen are the speed up of the trains, and the increase of the passenger transportation capacity while preserving the safety of high-speed railway systems. One possible approach for this is to enhance the speed adjustment capability. The end results are 1) the safety will be improved by reducing the distance for the urgent stop, 2) the train running density can be improved by increasing the average speed for the existing lines with many curves, that is called the high-density-scheduling. Generally, the speed adjustment performance can be enhanced through increasing driving or braking force that is mostly achieved by the maximum adhesion force between wheels and rails. -
Effects of Soil Moisture and Tillage Speeds on Tractive Force of Disc Ploughing in Loamy Sand Soil
European International Journal of Science and Technology Vol. 3 No. 4 May, 2014 Effects of soil moisture and tillage speeds on tractive force of disc ploughing in loamy sand soil S. O. Nkakini* and I. Fubara-Manuel Department of Agricultural and Environmental Engineering, Faculty of Engineering, Rivers State University of Science and Technology, P.M.B 5080, Port-Harcourt, Nigeria Corresponding author: email : [email protected] Abstract The effect of disc plough speeds and variations in soil moisture content on tractive force requirements was investigated using the trace-tractor technique. The results indicate that tractive forces decrease with increase in soil moisture content at constant tillage speeds of 1.94m/s, 2.22m/s and 2.5m/s respectively. The study further revealed that the optimum speed of operation for disc ploughing is 1.94m/s, while the optimum soil moisture content lies in the range of 2.5% to 25% wb. for the soil under consideration. Soil strength properties decreased with increase in soil moisture content and tillage speeds. This implies that there exists an optimum moisture content above or below which good soil tilth will not be realised. From the results, a linear relationship was established for predicting tractive force of disc plough under varying soil moisture content and plough speed of 1,94m/s, 2.22m/s and 2.5m/s. Keywords: Tractive force, tillage speeds, soil moisture, disc ploughing, loamy sand soil. 1. Introduction Land preparation is one of the major concerns in agricultural operations. Over the years, developments have taken place from the use of traditional methods of farm cultivations to the use of tractor drawn implements (Ahaneku et al., 2004). -
The Niagara Story Thomas R
The Making Of A Legend- The Niagara Story Thomas R. Get:bracht Part I diameter from 25" on the J1, to 22.5", and they in Introduction creased the stroke from 28" to 29" to take maximum In 1945, the Equipment Engineering Department of advantage of the expansive properties of higher pressure the New York Central Railroad developed and Alco exe steam. This reduction of 16 percent in cylinder swept cuted a locomotive design which had a marked impact volume was offset by a 22 percent increase in boiler pres on the steam locomotives to follow, and on the tradi sure, to 275 psi. Main engine starting tractive effort was tional measurements by which motive power would be about the same, at 43,440 lbs. for the J3, but at the same evaluated. This locomotive was so significant that its cutoffs the J3 would be more economical in the use of performance is still discussed by the men who design steam than the Jl. Weight per driving axle increased, and run locomotives. The locomotive was the New York due in part to the use of one piece engine beds and roller Central class S1 4-8-4 Niagara. bearing axles on the J3's. (Later J1's also were provided There have been a number of articles pertaining to by Alco with one piece engine beds.) The weight per this locomotive in the technical and railfan press. The driving axle of the J3 Hudsons was 65,300 lbs. compared purpose of this series is to supplement these various ar with the 60,670 lbs. -
Environmental Comparison of Michelin Tweel™ and Pneumatic Tire Using Life Cycle Analysis
ENVIRONMENTAL COMPARISON OF MICHELIN TWEEL™ AND PNEUMATIC TIRE USING LIFE CYCLE ANALYSIS A Thesis Presented to The Academic Faculty by Austin Cobert In Partial Fulfillment of the Requirements for the Degree Master’s of Science in the School of Mechanical Engineering Georgia Institute of Technology December 2009 Environmental Comparison of Michelin Tweel™ and Pneumatic Tire Using Life Cycle Analysis Approved By: Dr. Bert Bras, Advisor Mechanical Engineering Georgia Institute of Technology Dr. Jonathan Colton Mechanical Engineering Georgia Institute of Technology Dr. John Muzzy Chemical and Biological Engineering Georgia Institute of Technology Date Approved: July 21, 2009 i Table of Contents LIST OF TABLES .................................................................................................................................................. IV LIST OF FIGURES ................................................................................................................................................ VI CHAPTER 1. INTRODUCTION .............................................................................................................................. 1 1.1 BACKGROUND AND MOTIVATION ................................................................................................................... 1 1.2 THE PROBLEM ............................................................................................................................................ 2 1.2.1 Michelin’s Tweel™ ................................................................................................................................ -
Rolling Resistance During Cornering - Impact of Lateral Forces for Heavy- Duty Vehicles
DEGREE PROJECT IN MASTER;S PROGRAMME, APPLIED AND COMPUTATIONAL MATHEMATICS 120 CREDITS, SECOND CYCLE STOCKHOLM, SWEDEN 2015 Rolling resistance during cornering - impact of lateral forces for heavy- duty vehicles HELENA OLOFSON KTH ROYAL INSTITUTE OF TECHNOLOGY SCHOOL OF ENGINEERING SCIENCES Rolling resistance during cornering - impact of lateral forces for heavy-duty vehicles HELENA OLOFSON Master’s Thesis in Optimization and Systems Theory (30 ECTS credits) Master's Programme, Applied and Computational Mathematics (120 credits) Royal Institute of Technology year 2015 Supervisor at Scania AB: Anders Jensen Supervisor at KTH was Xiaoming Hu Examiner was Xiaoming Hu TRITA-MAT-E 2015:82 ISRN-KTH/MAT/E--15/82--SE Royal Institute of Technology SCI School of Engineering Sciences KTH SCI SE-100 44 Stockholm, Sweden URL: www.kth.se/sci iii Abstract We consider first the single-track bicycle model and state relations between the tires’ lateral forces and the turning radius. From the tire model, a relation between the lateral forces and slip angles is obtained. The extra rolling resis- tance forces from cornering are by linear approximation obtained as a function of the slip angles. The bicycle model is validated against the Magic-formula tire model from Adams. The bicycle model is then applied on an optimization problem, where the optimal velocity for a track for some given test cases is determined such that the energy loss is as small as possible. Results are presented for how much fuel it is possible to save by driving with optimal velocity compared to fixed average velocity. The optimization problem is applied to a specific laden truck. -
Chapter 4 Vehicle Dynamics
Chapter 4 Vehicle Dynamics 4.1. Introduction In order to design a controller, a good representative model of the system is needed. A vehicle mathematical model, which is appropriate for both acceleration and deceleration, is described in this section. This model will be used for design of control laws and computer simulations. Although the model considered here is relatively simple, it retains the essential dynamics of the system. 4.2. System Dynamics The model identifies the wheel speed and vehicle speed as state variables, and it identifies the torque applied to the wheel as the input variable. The two state variables in this model are associated with one-wheel rotational dynamics and linear vehicle dynamics. The state equations are the result of the application of Newton’s law to wheel and vehicle dynamics. 4.2.1. Wheel Dynamics The dynamic equation for the angular motion of the wheel is w& w =[Te - Tb - RwFt - RwFw]/ Jw (4.1) where Jw is the moment of inertia of the wheel, w w is the angular velocity of the wheel, the overdot indicates differentiation with respect to time, and the other quantities are defined in Table 4.1. 31 Table 4.1. Wheel Parameters Rw Radius of the wheel Nv Normal reaction force from the ground Te Shaft torque from the engine Tb Brake torque Ft Tractive force Fw Wheel viscous friction Nv direction of vehicle motion wheel rotating clockwise Te Tb Rw Ft + Fw ground Mvg Figure 4.1. Wheel Dynamics (under the influence of engine torque, brake torque, tire tractive force, wheel friction force, normal reaction force from the ground, and gravity force) The total torque acting on the wheel divided by the moment of inertia of the wheel equals the wheel angular acceleration (deceleration).