Solution-Based Chalcogenide Thin Film Deposition
Total Page:16
File Type:pdf, Size:1020Kb
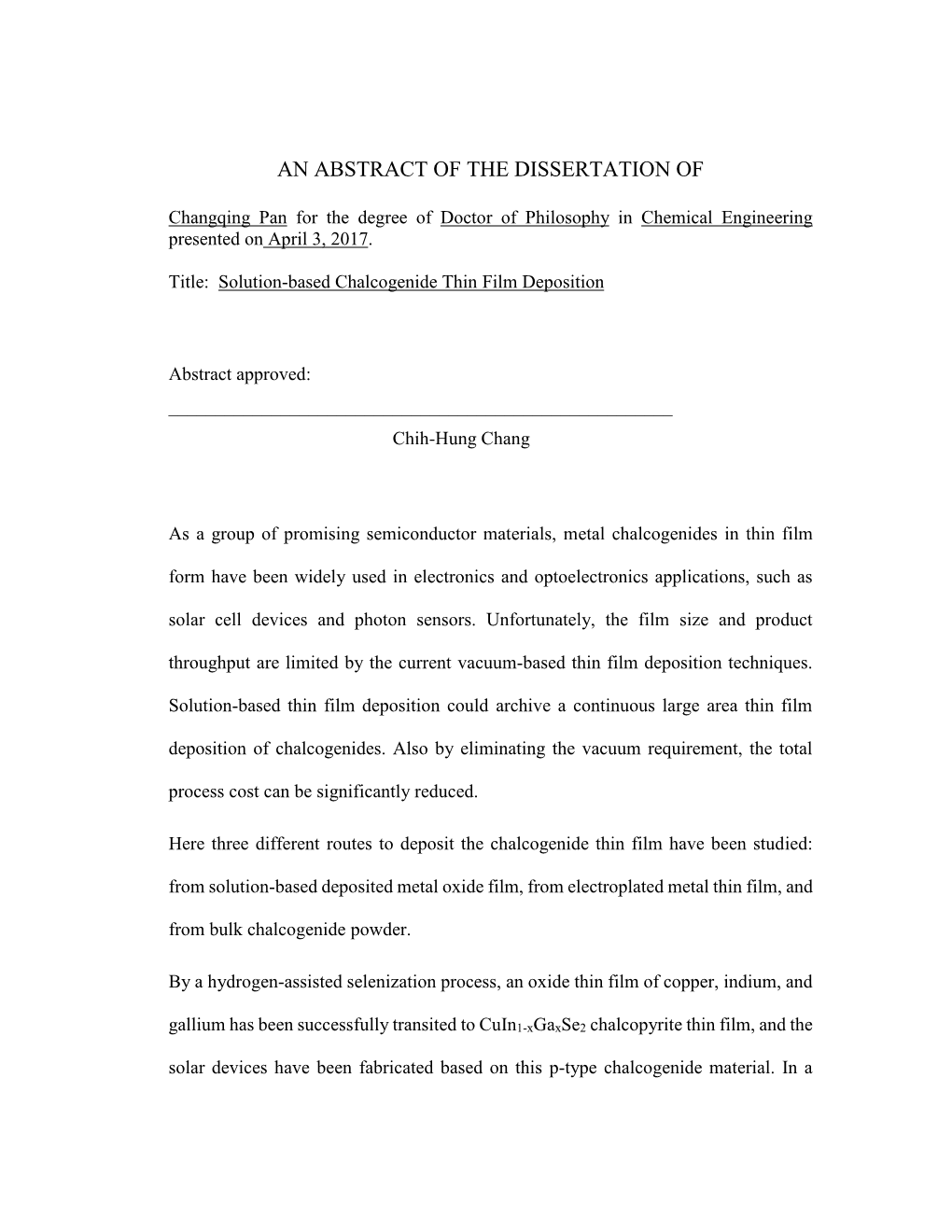
Load more
Recommended publications
-
Conductive-Bridging Random Access Memory
Jana et al. Nanoscale Research Letters (2015) 10:188 DOI 10.1186/s11671-015-0880-9 NANO REVIEW Open Access Conductive-bridging random access memory: challenges and opportunity for 3D architecture Debanjan Jana1, Sourav Roy1, Rajeswar Panja1, Mrinmoy Dutta1, Sheikh Ziaur Rahaman1, Rajat Mahapatra1,2 and Siddheswar Maikap1* Abstract The performances of conductive-bridging random access memory (CBRAM) have been reviewed for different switching materials such as chalcogenides, oxides, and bilayers in different structures. The structure consists of an inert electrode and one oxidized electrode of copper (Cu) or silver (Ag). The switching mechanism is the formation/dissolution of a metallic filament in the switching materials under external bias. However, the growth dynamics of the metallic filament in different switching materials are still debated. All CBRAM devices are switching under an operation current of 0.1 μAto 1mA,andanoperationvoltageof±2Visalsoneeded.Thedevice can reach a low current of 5 pA; however, current compliance-dependent reliability is a challenging issue. Although a chalcogenide-based material has opportunity to have better endurance as compared to an oxide-based material, data retention and integration with the complementary metal-oxide-semiconductor (CMOS) process are also issues. Devices with bilayer switching materials show better resistive switching characteristics as compared to those with a single switching layer, especially a program/erase endurance of >105 cycles with a high speed of few nanoseconds. Multi-level cell operation is possible, but the stability of the high resistance state is also an important reliability concern. These devices show a good data retention of >105 s at >85°C. However, more study is needed to achieve a 10-year guarantee of data retention for non-volatile memory application. -
UCLA Electronic Theses and Dissertations
UCLA UCLA Electronic Theses and Dissertations Title Electrochemical Performance of Titanium Disulfide and Molybdenum Disulfide Nanoplatelets Permalink https://escholarship.org/uc/item/73h6h1z6 Author Siordia, Andrew F. Publication Date 2016 Peer reviewed|Thesis/dissertation eScholarship.org Powered by the California Digital Library University of California UNIVERSITY OF CALIFORNIA Los Angeles Electrochemical Performance of Titanium Disulfide and Molybdenum Disulfide Nanoplatelets A thesis submitted in partial satisfaction of the requirements of the degree Master of Science in Materials Science and Engineering by Andrew Francisco Siordia 2016 ABSTRACT OF THESIS Electrochemical Performance of Titanium Disulfide and Molybdenum Disulfide Nanoplatelets by Andrew Francisco Siordia Master of Science in Materials Science and Engineering University of California, Los Angeles, 2016 Professor Bruce S. Dunn, Chair Single layer crystalline materials, often termed two-dimension (2D) materials, have quickly become a popular topic of research interest due to their extraordinary properties. The intrinsic electrical, mechanical, and optical properties of graphene were found to be remarkably distinct from graphite, its bulk counterpart. In conjunction with newfound processing techniques, there is renewed interest in elucidating the structure-property relationships of other 2D materials ii like the transition metal dichalcogenides (TMDCs). The energy storage capability of 2D nanoplatelets of TiS2 and MoS2 are studied here providing a contrast with investigations of corresponding bulk materials in the early 1970s. TiS2 was synthesized into nanoplatelets using a hot injection route which provided a capacity of ~143mAhg-1 from thin film electrodes as determined by cyclic voltammetry measurements. Phase identification using X-ray diffraction, scanning electron microscopy, and transmission electron microscopy to complement the electrochemical performance and impurity identification is presented. -
L. Arulmurugan, M. Ilangkumaran " Experimental Study on Graphene/Transition Metal Chalcogenide Based Energy Storage and Conversion
Journal of Ovonic Research Vol. 16, No. 4, July - August 2020, p. 197 - 211 EXPERIMENTAL STUDY ON GRAPHENE/TRANSITION METAL CHALCOGENIDE BASED ENERGY STORAGE AND CONVERSION L. ARULMURUGANa, *, M. ILANGKUMARANb, aDepartment of Electronics and Communication Engineering, Bannari Amman Institute of Technology, Sathyamangalam, Erode, Tamilnadu, India bDepartment of Mechatronics Engineering, K S Rangasamy College of Technology, Tiruchengode, Tamilnadu, India The ever-increasing energy demand and the shortage of fossil fuels force the researchers to do research on utilization and conversion of renewable energy sources. In Recent years, the graphene and Transition Metal Chalcogenide (TMC) based Phase Change material (PCM) have been reviewed towards the future energy storage and energy conversion. This PCM is considered as a promising pathway to alleviate the energy crisis. The TMC material is considered as an emerging material due to their optoelectronic behavior and stability of the material. Moreover, the integration of TMC with graphene, significantly improve the performance of the system. The storage of solar energy in the form of sensible and latent heat has become an important aspect of energy management. To improve the performance of domestic solar water heater system, the vertical spiral and cylindrical heat exchanger is designed. The spiral module and cylindrical modules filled with and without PCM are analyzed and the obtained results are compared with each other. The results show that the spiral and cylindrical heat exchanger filled with PCM store and release the thermal energy efficiently and it performs the desired functions than the without PCM module. (Received April 28, 2020; Accepted July 14, 2020) Keywords: Graphene/transition metal chalcogenide, Phase change material, Thermal management, Heat exchanger, Spiral and cylindrical module 1. -
Growth of Metal Chalcogenide Nanomaterials and Their Characterizations Yichao Zou Bachelor of Engineering
Growth of Metal Chalcogenide Nanomaterials and Their Characterizations Yichao Zou Bachelor of Engineering A thesis submitted for the degree of Doctor of Philosophy at The University of Queensland in 2016 School of Mechanical and Mining Engineering Abstract Metal chalcogenides, such as IV-VI and V-VI compounds (SnTe, Bi2Te3, Bi2Se3), are ideal candidates for applications in thermoelectricity and topological (crystalline) insulators. This PhD thesis focuses on the controllable synthesis of metal chalcogenide nanostructures via chemical vapour deposition method (CVD), and on the understanding of the crystal structure, growth mechanism, and structure-property correlation in the as-grown nanomaterials. IV-VI and V-VI compounds have attracted extensive research interest because of their excellent thermoelectric properties and exotic physical properties. Nevertheless, there still exist unresolved issues that prevent the further applications of IV-VI and V-VI nanomaterials by rational design, including (1) it is still difficult to grow these nanomaterials with controllable morphology and (2) crystal structure; (3) limited investigations of their growth mechanisms; (4) limited study on structure-property relationships in the nanostructures. Therefore, in this thesis, the controllable growth technique, growth mechanism and structure-property relation in IV-VI and V-VI based nanostructures are explored. The objective is achieved in the following steps: Realizing the morphological control of the nanostructures. (i) By catalyst engineering in Au-catalysed CVD. For SnTe nanostructures, catalyst composition was found to be a key factor controlling the morphology. AuSn catalysts induce growth of triangular SnTe nanoplates, whereas Au5Sn catalysts result in <010> SnTe NWs. For Bi2Se3 nanostructures, catalyst-nanostructure interface was found to have an impact on their growth directions. -
Crystallization Kinetics of Chalcogenide Glasses
2 Crystallization Kinetics of Chalcogenide Glasses Abhay Kumar Singh Department of Physics, Banaras Hindu University, Varanasi, India 1. Introduction 1.1 Background of chalcogenides Chalcogenide glasses are disordered non crystalline materials which have pronounced tendency their atoms to link together to form link chain. Chalcogenide glasses can be obtained by mixing the chalcogen elements, viz, S, Se and Te with elements of the periodic table such as Ga, In, Si, Ge, Sn, As, Sb and Bi, Ag, Cd, Zn etc. In these glasses, short-range inter-atomic forces are predominantly covalent: strong in magnitude and highly directional, whereas weak van der Waals' forces contribute significantly to the medium-range order. The atomic bonding structure is, in general more rigid than that of organic polymers and more flexible than that of oxide glasses. Accordingly, the glass-transition temperatures and elastic properties lay in between those of these materials. Some metallic element containing chalcogenide glasses behave as (super) ionic conductors. These glasses also behave as semiconductors or, more strictly, they are a kind of amorphous semi-conductors with band gap energies of 1±3eV (Fritzsche, 1971). Commonly, chalcogenide glasses have much lower mechanical strength and thermal stability as compared to existing oxide glasses, but they have higher thermal expansion, refractive index, larger range of infrared transparency and higher order of optical non-linearity. It is difficult to define with accuracy when mankind first fabricated its own glass but sources demonstrate that it discovered 10,000 years back in time. It is also difficult to point in time, when the field of chalcogenide glasses started. -
Thin Film Deposition Methods for Cuinse2 Solar Cells
Critical Reviews in Solid State and Materials Sciences, 30:1–31, 2005 Copyright c Taylor and Francis Inc. ISSN: 1040-8436 print DOI: 10.1080/10408430590918341 Thin Film Deposition Methods for CuInSe2 Solar Cells Marianna Kemell,∗ Mikko Ritala, and Markku Leskel¨a Laboratory of Inorganic Chemistry, Department of Chemistry, University of Helsinki, Helsinki, Finland CuInSe2 and its alloys with Ga and/or S are among the most promising absorber materials for thin film solar cells. CuInSe2-based solar cells have shown long-term stability and the highest conversion efficiencies of all thin film solar cells, above 19%. Solar cells based on these materials are also very stable, thus allowing long operational lifetimes. The preparation of a thin film solar cell is a multistage process where every step affects the resulting cell performance and the production cost. CuInSe2 and other Cu chalcopyrites can be prepared by a variety of methods, ranging from physical vapor deposition methods such as evaporation and sputtering to low- temperature liquid phase methods such as electrodeposition. The present review discusses first the concept and operation principle of thin film solar cells, as well as the most important thin film solar cell materials. Next, the properties of CuInSe2 and related compounds, as well as features of solar cells made thereof are reviewed. The last part of the text deals with deposition methods used for the preparation of CuInSe2 and Cu(In,Ga)Se2 thin film absorbers and solar cells. Although the emphasis here is on absorber preparation methods, buffer and conducting oxide preparation are discussed as well. Keywords photovoltaics, copper chalcopyrites, absorber layer, buffer layer, transparent conducting oxide Table of Contents LIST OF SYMBOLS AND ABBREVIATIONS ............................................................................................................. -
United States Patent to 4,009,052 Whittingham 45 Feb
United States Patent to 4,009,052 Whittingham 45 Feb. 22, 1977 54 CHALCOGENIDE BATTERY the anode-active material a metal selected from the group consisting of Group la metals, Group Ib metals, (75. Inventor: M. Stanley Whittingham, Fanwood, Group IIa metals, Group IIb metals, Group IIIa metals N.J. and Group IVa metals (lithium is preferred), the cath 73) Assignee: Exxon Research and Engineering ode contains as the cathode-active material a chalco Company, Linden, N.J. genide of the formula MZ wherein M is an element selected from the group consisting of titanium, zirco 22 Filed: Apr. 5, 1976 nium, hafnium, niobium, tantalum and vanadium (tita nium is preferred); Z is an element selected from the (21 Appl. No.: 673,696 group consisting of sulfur, selenium and tellurium, and x is a numerical value between about 1.8 and about 2. 1, Related U.S. Application Data and the electrolyte is one which does not chemically 63 Continuation-in-part of Ser. No. 552,599, Feb. 24, react with the anode or the cathode and which will 1975, abandoned, which is a continuation-in-part of permit the migration of ions from said anode-active Ser. No. 396,051, Sept. 10, 1973, abandoned. material to intercalate the cathode-active material. A highly useful battery may be prepared utilizing lithium (52) U.S. Cl. ............................... 429/191; 429/193; as the anode-active material, titanium disulfide as the 429/194; 429/199; 429/218; 429/229 cathode-active material and lithium perchlorate dis (51) Int. Cl’........................................ H01M 35/02 solved in tetrahydrofuran (70%) plus dimethoxyethane. -
Amorphous Chalcogenide Semiconductors and Related Materials
Amorphous Chalcogenide Semiconductors and Related Materials Keiji Tanaka · Koichi Shimakawa Amorphous Chalcogenide Semiconductors and Related Materials 123 Keiji Tanaka Koichi Shimakawa Graduate School of Engineering Faculty of Engineering Department of Applied Physics Gifu University Hokkaido University Yanaido Kita-ku Gifu 501-1193, Japan Sapporo 060-8628, Japan and [email protected] Nagoya Industrial Science Institute Nagoya 460-0008, Japan [email protected] ISBN 978-1-4419-9509-4 e-ISBN 978-1-4419-9510-0 DOI 10.1007/978-1-4419-9510-0 Springer New York Dordrecht Heidelberg London Library of Congress Control Number: 2011926594 © Springer Science+Business Media, LLC 2011 All rights reserved. This work may not be translated or copied in whole or in part without the written permission of the publisher (Springer Science+Business Media, LLC, 233 Spring Street, New York, NY 10013, USA), except for brief excerpts in connection with reviews or scholarly analysis. Use in connection with any form of information storage and retrieval, electronic adaptation, computer software, or by similar or dissimilar methodology now known or hereafter developed is forbidden. The use in this publication of trade names, trademarks, service marks, and similar terms, even if they are not identified as such, is not to be taken as an expression of opinion as to whether or not they are subject to proprietary rights. Printed on acid-free paper Springer is part of Springer Science+Business Media (www.springer.com) Preface Photonic, electronic, and photo-electric applications of non-crystalline1 solids are rapidly growing in recent years. Such growth seems to synchronize with the devel- opment of oxide glass1 fibers and related devices for optical communications, which started near the end of the last century. -
Applications of Chalcogenide Glasses: an Overview
International Journal of ChemTech Research CODEN (USA): IJCRGG ISSN : 0974-4290 Vol.6, No.11, pp 4682-4686, Oct-Nov 2014 Applications of Chalcogenide Glasses: An Overview Suresh Sagadevan*1 and Edison Chandraseelan2 *1Department of Physics, Sree Sastha Institute of Engineering and Technology, Chennai-600 123, India 2 Department of Mechanical Engineering, Sree Sastha Institute of Engineering and Technology, Chennai--600 123, India *Corres.author: [email protected] Abstract: Chalcogenides are compounds formed predominately from one or more of the chalcogen elements; sulphur, selenium and tellurium. Although first studied over fifty years ago, interest in chalcogenide glasses has, over the past few years, increased significantly as glasses, crystals and alloys find new life in a wide range of optoelectronic devices applications. Following the development of the glassy chalcogenide field, new optoelectronic materials based on these materials have been discovered. Several non-oxide glasses have been prepared and investigated in the last several decades, thus widening the groups of chalcogen materials used in various optical, electronic and optoelectronic glasses. This paper reviews the development of chalcogenide glasses, their physical properties and applications in electronics and optoelectronics. The glassy, amorphous and disordered chalcogenide materials, which are important for optoelectronic applications, are discussed. This paper also deals with an overview of representative applications these exciting optoelectronic materials. 1. Introduction The name chalcogenide originates from the Greek word “chalcos” meaning ore and “gen” meaning formation, thus the term chalcogenide is generally considered to mean ore former [1]. The elements of group sixteen of the periodic table is known as the chalcogens. The group consists of oxygen, sulphur, selenium, tellurium and polonium though oxygen is not included in the chalcogenide category. -
WS2: a New Window Layer Material for Solar Cell Application Md
www.nature.com/scientificreports OPEN WS2: A New Window Layer Material for Solar Cell Application Md. Khan Sobayel Bin Rafq 1, N. Amin2,3*, Hamad F. Alharbi4*, Monis Luqman 4, Afda Ayob2, Yahya S. Alharthi5, Nabeel H. Alharthi5, Badariah Bais2 & Md. Akhtaruzzaman1,2* Radio frequency (RF) magnetron sputtering was used to deposit tungsten disulfde (WS2) thin flms on top of soda lime glass substrates. The deposition power of RF magnetron sputtering varied at 50, 100, 150, 200, and 250 W to investigate the impact on flm characteristics and determine the optimized conditions for suitable application in thin-flm solar cells. Morphological, structural, and opto-electronic properties of as-grown flms were investigated and analyzed for diferent deposition powers. All the WS2 flms exhibited granular morphology and consisted of a rhombohedral phase with a strong preferential orientation toward the (101) crystal plane. Polycrystalline ultra-thin WS2 flms with bandgap of 2.2 eV, carrier concentration of 1.01 × 1019 cm−3, and resistivity of 0.135 Ω-cm were successfully achieved at RF deposition power of 200 W. The optimized WS2 thin flm was successfully incorporated as a window layer for the frst time in CdTe/WS2 solar cell. Initial investigations revealed that the newly incorporated WS2 window layer in CdTe solar cell demonstrated photovoltaic conversion efciency of 1.2% with Voc 2 of 379 mV, Jsc of 11.5 mA/cm , and FF of 27.1%. This study paves the way for WS2 thin flm as a potential window layer to be used in thin-flm solar cells. For many decades, transition metal dichalcogenides (TMDCs) are among the promising materials in a wide range of applications, but their superior performance in complex applications has attracted extensive research atten- tion. -
Colloidal and Deposited Products of the Interaction of Tetrachloroauric Acid with Hydrogen Selenide and Hydrogen Sulfide in Aqueous Solutions
minerals Article Colloidal and Deposited Products of the Interaction of Tetrachloroauric Acid with Hydrogen Selenide and Hydrogen Sulfide in Aqueous Solutions Sergey Vorobyev 1, Maxim Likhatski 1, Alexander Romanchenko 1, Nikolai Maksimov 1, Sergey Zharkov 2,3, Alexander Krylov 2 and Yuri Mikhlin 1,* 1 Institute of Chemistry and Chemical Technology of the Siberian Branch of the Russian Academy of Sciences, Krasnoyarsk 660036, Russia; [email protected] (S.V.); [email protected] (M.L.); [email protected] (A.R.); [email protected] (N.M.) 2 Kirensky Institute of Physics of the Siberian Branch of the Russian Academy of Sciences, Krasnoyarsk 660036, Russia; [email protected] (S.Z.); [email protected] (A.K.) 3 Electron Microscopy Laboratory, Siberian Federal University, Krasnoyarsk 660041, Russia * Correspondence: [email protected]; Tel.: +7-391-205-1928 Received: 11 October 2018; Accepted: 29 October 2018; Published: 31 October 2018 Abstract: The reactions of aqueous gold complexes with H2Se and H2S are important for transportation and deposition of gold in nature and for synthesis of AuSe-based nanomaterials but are scantily understood. Here, we explored species formed at different proportions of HAuCl4, H2Se and H2S at room temperature using in situ UV-vis spectroscopy, dynamic light scattering (DLS), zeta-potential measurement and ex situ Transmission electron microscopy (TEM), electron diffraction, X-ray diffraction (XRD), X-ray photoelectron spectroscopy (XPS), and Raman spectroscopy. Metal gold colloids arose at the molar ratios H2Se(H2S)/HAuCl4 less than 2. At higher ratios, pre-nucleation “dense liquid” species having the hydrodynamic diameter of 20–40 nm, zeta potential −40 mV to −50 mV, and the indirect band gap less than 1 eV derived from the UV-vis spectra grow into submicrometer droplets over several hours, followed by fractional nucleation in the interior and + coagulation of disordered gold chalcogenide. -
Mid-Infrared Supercontinuum Generation in Chalcogenide Glass Fibers: a Brief Review Yingying Wang1,2,3 and Shixun Dai1,2,3*
Wang and Dai PhotoniX (2021) 2:9 https://doi.org/10.1186/s43074-021-00031-3 PhotoniX REVIEW Open Access Mid-infrared supercontinuum generation in chalcogenide glass fibers: a brief review Yingying Wang1,2,3 and Shixun Dai1,2,3* * Correspondence: daishixun@nbu. edu.cn Abstract 1Laboratory of Infrared Material and Devices, The Research Institute of Chalcogenide (ChG) glasses have the characteristics of a wide transparency window 3 Advanced Technologies, Ningbo (over 20 μm) and high optical nonlinearity (up to 10 times greater than that of silica University, Ningbo 315211, China glasses), exhibiting great advantages over silica and other soft glasses in optical 2Key Laboratory of Photoelectric Materials and Devices of Zhejiang property at mid-infrared (MIR) wavelength range. These make them excellent Province, Ningbo 315211, China candidates for MIR supercontinuum (SC) generation. Over the past decades, great Full list of author information is progress has been made in MIR SC generation based on ChG fibers in terms of available at the end of the article spectral extension and output power improvement. In this paper, we introduce briefly the properties of ChG glasses and fibers including transmission, nonlinearity, and dispersion, etc. Recent progress in MIR SC generation based on ChG fibers is reviewed from the perspective of pump schemes. We also present novel ChG fibers such as As-free, Te-based, and chalcohalide fibers, which have been explored and employed as nonlinear fibers to achieve broadband SC generation. Moreover, the potential applications of MIR SC sources based on ChG fibers are discussed. Keywords: Chalcogenide glass fiber, Supercontinuum generation, Mid-infrared, Nonlinear optics Introduction Supercontinuum (SC) generation in nonlinear media originates from the interaction of ultrashort pulses and the dispersion and nonlinear effects, such as self-phase modula- tion (SPM), four wave mixing, stimulated Raman scattering (SRS), soliton self- frequency shift, etc.