The Effects of the Exposure of Atomic Oxygen on Polymeric Material: I Siloxane Modified Epoxy Resins II Polyetherimide Films with Additives
Total Page:16
File Type:pdf, Size:1020Kb
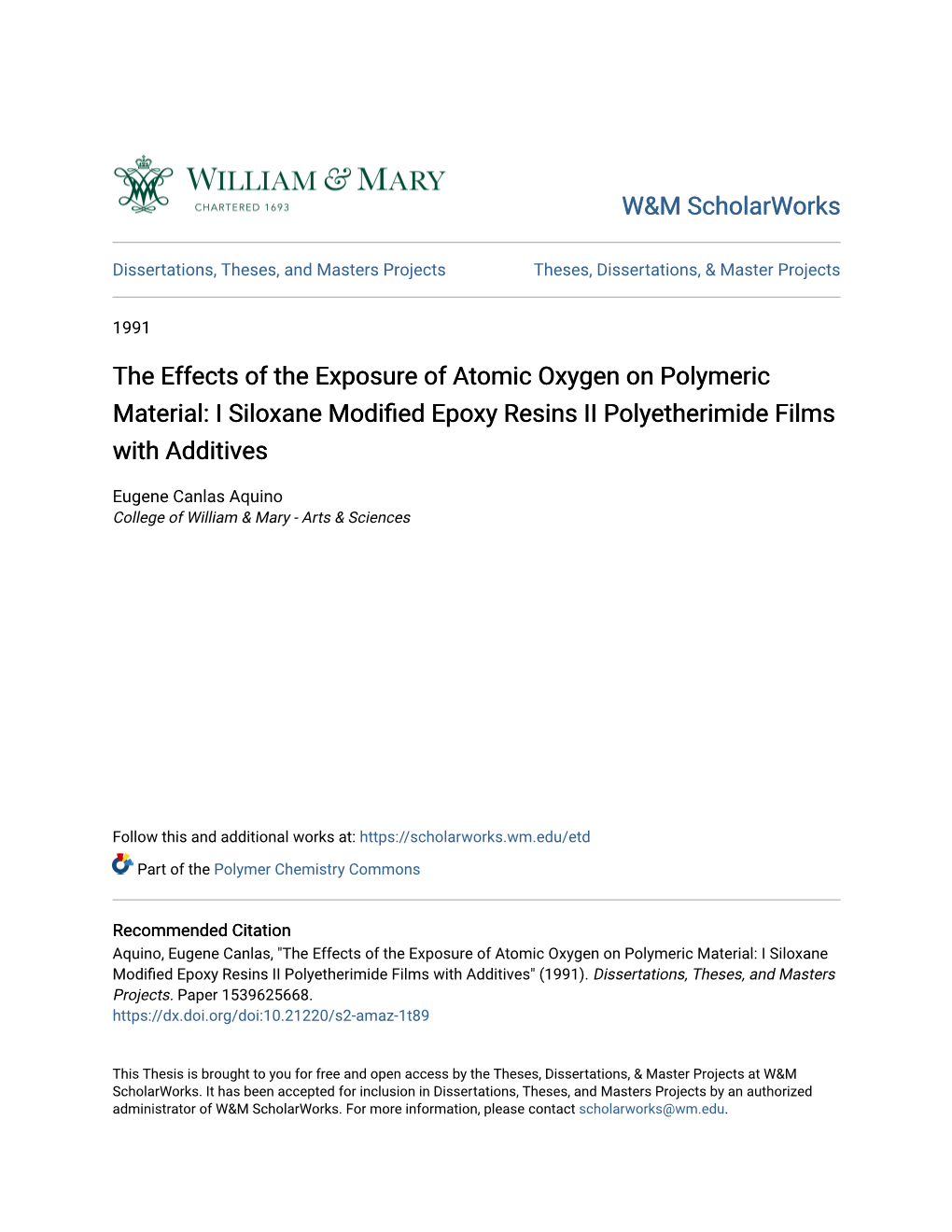
Load more
Recommended publications
-
The Effect of Conformation Order on Gas Separation Properties Of
polymers Article The Effect of Conformation Order on Gas Separation Properties of Polyetherimide Ultem Films Julia Kostina 1,*, Sergey Legkov 1, Alexander Kolbeshin 1, Roman Nikiforov 1, Denis Bezgin 1, Alexander Yu. Nikolaev 2 and Alexander Yu. Alentiev 1,* 1 A.V. Topchiev Institute of Petrochemical Synthesis Russian Academy of Sciences, 119991 Moscow, Russia; [email protected] (S.L.); [email protected] (A.K.); [email protected] (R.N.); [email protected] (D.B.) 2 A.N. Nesmeyanov Institute of Organoelement Compounds of Russian Academy of Sciences, 119334 Moscow, Russia; [email protected] * Correspondence: [email protected] (J.K.); [email protected] (A.Y.A.) Received: 16 June 2020; Accepted: 7 July 2020; Published: 16 July 2020 Abstract: Changes of the spectral characteristics of absorption bands depending on the films’ treatment method were registered for polyetherimide Ultem films. The possibility of selection of structural criteria (the ratio of the functional groups absorption bands intensities) showing all conformational changes in elementary unit with metrological processing of the results is shown. It is demonstrated that film formation from chloroform solution leads to elementary unit fragments, Ph–O–Ph0, which have an effect on macromolecule conformation and result in increasing of space between fragments of macromolecules (local polymer matrix packing loosening). Desorption of residual chloroform from films by ethanol or supercritical CO2 leads to a change of conformers set in Im–Ph–Im0 units. Quantum chemical modeling showed the possibility of convergence of these fragments in neighboring macromolecules, and consequently of interchain π–π interaction (local densification of chain packing of the polymer matrix). -
Fabrication of a High-Performance Polyetherimide Membrane for Helium Separation Y
World Academy of Science, Engineering and Technology International Journal of Chemical and Molecular Engineering Vol:13, No:10, 2019 Fabrication of a High-Performance Polyetherimide Membrane for Helium Separation Y. Alqaheem, A. Alomair, F. Altarkait, F. Alswaileh, Nusrat Tanoli metallic, ceramic, and polymeric. The metallic membranes Abstract—Helium market is continuously growing due to its have an infinite selectivity meaning that the produced gas can essential uses in the electronic and healthcare sectors. Currently, have a purity of 100%; however, the price of precious metals helium is produced by cryogenic distillation but the process is makes the membranes uneconomical. Furthermore, the uneconomical especially for low production volumes. On the other metallic membranes are easily susceptible to corrosion due to hand, polymeric membranes can provide a cost-effective solution for helium purification due to their low operating energy. However, the the rapid reaction with sulfur and other impurities. Some preparation of membranes involves the use of very toxic solvents examples of metallic membranes are platinum and palladium. such as chloroform. In this work, polyetherimide membranes were Ceramic membranes are well known for their excellent prepared using a less toxic solvent, n-methylpyrrolidone with a chemical and thermal stability. Nevertheless, it is difficult to polymer-to-solvent ratio of 27 wt%. The developed membrane reproduce the membrane due to the agglomeration of particles. showed a superior helium permeability of 15.9 Barrer that surpassed In addition, some ceramic membranes require high the permeability of membranes made by chloroform. temperature to operate and most of the sealants will fail at extreme temperatures. Silica, zeolite and mixed conductors are Keywords—Helium separation, polyetherimide, dense membrane, gas permeability, solvent. -
Ep 2644641 B1
(19) TZZ __T (11) EP 2 644 641 B1 (12) EUROPEAN PATENT SPECIFICATION (45) Date of publication and mention (51) Int Cl.: of the grant of the patent: C09D 179/08 (2006.01) C08K 5/51 (2006.01) 04.11.2015 Bulletin 2015/45 D01F 6/74 (2006.01) C08G 73/10 (2006.01) C08L 79/08 (2006.01) (21) Application number: 12382121.7 (22) Date of filing: 30.03.2012 (54) Polyetherimides, methods of manufacture, and articles formed therefrom Polyetherimide, Herstellungsverfahren und daraus hergestellte Gegenstände Polyétherimides, procédés de fabrication et articles formés à partir de ceux-ci (84) Designated Contracting States: • Peñalver, Beatriz AL AT BE BG CH CY CZ DE DK EE ES FI FR GB Chicago, IL Illinois 60622 (US) GR HR HU IE IS IT LI LT LU LV MC MK MT NL NO • Hemmer, Gregory L. PL PT RO RS SE SI SK SM TR Santa Claus, IN Indiana 47579 (US) • Odle, Roy Ray (43) Date of publication of application: Mt. Vernon, IN Indiana 47620-9367 (US) 02.10.2013 Bulletin 2013/40 (74) Representative: Carpintero Lopez, Francisco et al (73) Proprietor: SABIC Global Technologies B.V. Herrero & Asociados, S.L. 4612 PX Bergen op Zoom (NL) Alcalá, 35 28014 Madrid (ES) (72) Inventors: • Rodriguez Ordoñes, Juan Justino (56) References cited: 30390 Cartagena - Murcia (ES) EP-A2- 1 426 358 US-A- 5 229 482 • Link Guggenheim, Thomas US-A1- 2006 173 158 Mount Vernon, IN Indiana 47620-9367 (US) Note: Within nine months of the publication of the mention of the grant of the European patent in the European Patent Bulletin, any person may give notice to the European Patent Office of opposition to that patent, in accordance with the Implementing Regulations. -
Spectroscopic Analysis of Radiation-Generat Ed Changes In
NASA Tec hnica I Paper 2429 , May 1985 Spectroscopic Analysis of Radiation-Generated Changes in Tensile Properties of a Polyetherimide Film Edward R. Long, Jr., and Sheila Ann T. Long NASA Tech nica I Paper 2429 1985 Spectroscopic Analysis of Radiation-Generated Changes in Tensile Properties of a Polyetherimide Film Edward R. Long, Jr., and Sheila Ann T. Long Langley Research Center Hampton, Virginia NASA National Aeronautics and Space Administration Scientific and Technical Information Branch The use of trademarks or manufacturers' names in this publication does not constitute endorsement, either expressed or implied, by the National Aeronautics and Space Administration. SUMMARY The effects of electron radiation on Ultem, a polyetherimide manufactured by General Electric, were studied for doses from 2 x IO9 to 6 x IO9 rad. Specimens for tensile property testing and for electron paramagnetic resonance (EPR) and infrared ( IR) spectroscopic measurements of molecular striictnre were st.udied e The apectrn- scopic data were used to determine the effects of radiation on molecular structures, and these effects were used to explain the radiation-generated changes in tensile properties. Because the cross-sectional area of the electron beam was limited to a 6-inch diameter, miniature tensile specimens were used. Extensive testing was conducted to develop the size and test procedure for the tensile specimens. The miniaturization was based upon ASTM Testing Standard 882. A design for a Faraday cup and the use of a remote IR temperature sensor are also described. The Faraday cup was used to mon- itor the electron beam current; it was calibrated with NBS-traceable nylon films, which were used to measure the total dose. -
Multilayered Pei-Based Films for Co2 Adsorption And
MULTILAYERED PEI-BASED FILMS FOR CO2 ADSORPTION AND DIFFUSION A Thesis Presented to The Graduate Faculty of The University of Akron In Partial Fulfillment of the Requirements for the Degree Master of Science Jing Liu May, 2013 MULTILAYERED PEI-BASED FILMS FOR CO2 ADSORPTION AND DIFFUSION Jing Liu Thesis Approved: Accepted: Advisor Dean of the College Dr. Steven S.C. Chuang Dr. Stephen Z.D. Cheng Co-Advisor or Faculty Reader Dean of the Graduate School Dr. Li Jia Dr. George R. Newkome Department Chair Date Dr. Coleen Pugh ii ABSTRACT Polyethyleneimine (PEI), composed of the amine group on the repeating unit, o o can bind CO2 at 50–75 C and dissociate it at 100–130 C. This unique characteristic allows PEI to serve as an active molecule in solid sorbents for the thermal swing and membrane processes for CO2 separation. The nature and concentration of CO2 adsorption on amine sites of PEI can be observed and investigated by Fourier Transform Infrared Spectroscopy (FTIR) 15. In-situ FTIR was used to evaluate and determine i) the CO2 adsorption on PEI layers containing 1, 8, 21 and 35wt% of water and ii) the rate of diffusion of CO2 through multiple layers of PEI partially crosslinked with glutaraldehyde (GA). Each sequential PEI layer was prepared by increasing the degree of cross-linking with GA, generating a gradient amine concentration throughout the multiple layers thickness. Initial results show an increase of CO2 adsorption at a lower concentration of water. The multiple layered amine gradients enhanced the rate of CO2 diffusion compared to a single layer of crosslinked PEI of similar thickness. -
Investigation of the Fire Behaviour of PEEK- Based Polymers and Compounds
Investigation of the Fire Behaviour of PEEK- based Polymers and Compounds by Parina Patel A thesis submitted in partial fulfilment for the requirements of the degree of Doctor of Philosophy at the University of Central Lancashire in collaboration with Victrex plc February 2011 ABSTRACT Polyetheretherketone (PEEK) is a polymer with outstanding performance, particularly concerning temperature resistance, chemical resistance and mechanical characteristics. Literature shows a gap in the knowledge with regards to PEEK flammability and decomposition products. The aim of this thesis is to describe the decomposition and flammability behaviour of PEEK, in order to develop new fire safe PEEK-based materials. By relating the measured thermal decomposition behaviour and changes in physical properties of PEEK materials to their performance in standard flammability tests, the dependence of these tests has been investigated with regards to orientation, thickness, presence of fillers, moisture absorption and absorption of infrared radiation. This understanding can inform the development of modified PEEK materials with enhanced fire safety. Various industry standard tests have been utilised to examine PEEK such as the Cone Calorimeter (ISO 5660), UL-94 (EN 60695-10-11), Limiting Oxygen Index (LOI), Thermogravimetric Analysis (TGA) in both air and inert atmospheres and the Small Flame Ignitability Test (ISO 11925). PEEK decomposition has been investigated using Thermogravimetric Analysis (TGA), Simultaneous Thermal Analysis coupled with Fourier Transform Infrared (STA-FTIR) and Pyrolysis Gas Chromatography coupled with Mass Spectrometry (pyGC/MS). Residue analysis has been carried out using Diamond Attenuated Total Reflectance coupled with Fourier Transform Infrared (dATR-FTIR), Solid State Nuclear Magnetic Resonance (MAS-NMR) and Scanning Electron Microscopy coupled with Electron Dispersive X-ray Analysis (SEM-EDX). -
Preparation and Characterization of Carbon and Carbon/Zeolite Membranes from ODPA–ODA Type Polyetherimide
Journal of Membrane Science 474 (2015) 114–121 Contents lists available at ScienceDirect Journal of Membrane Science journal homepage: www.elsevier.com/locate/memsci Preparation and characterization of carbon and carbon/zeolite membranes from ODPA–ODA type polyetherimide Bing Zhang a,b,n, Yonghong Wu a, Yunhua Lu b,c, Tonghua Wang b, Xigao Jian b, Jieshan Qiu b,1 a School of Petrochemical Engineering, Shenyang University of Technology, Liaoyang 111003, China b Carbon Research Laboratory, Liaoning Key Lab for Energy Materials and Chemical Engineering, State Key Lab of Fine Chemicals, School of Chemical Engineering, Dalian University of Technology, Dalian 116024, China c School of Chemical Engineering, Liaoning University of Science and Technology, Anshan 114051, China article info abstract Article history: A novel precursor, 3,30,4,40-oxydiphthalic dianhydride-4,40-oxydianiline (ODPA–ODA) type polyether- Received 8 February 2014 imide (PEI), was synthesized and used to prepare carbon membranes by preoxidation and heat Received in revised form treatment. The thermal stability of the ODPA–ODA type PEI was evaluated by thermogravimetric 23 September 2014 analysis. The surface properties, elemental composition, microstructure, morphology and gas separation Accepted 26 September 2014 performance of the as-made carbon membranes were examined by the Fourier transform infrared Available online 7 October 2014 spectroscopy, elemental analysis, X-ray diffraction, scanning electron microscopy and gas permeation Keywords: techniques. The effects of the preoxidation temperature and zeolite incorporation on the microstructure Polyetherimide and gas separation performance of carbon membranes were investigated. The results have shown that Carbon membranes ODPA–ODA type PEI is a good precursor for producing carbon membranes. -
Highly Selective Oxygen/Nitrogen Separation Membrane Engineered Using a Porphyrin-Based Oxygen Carrier
membranes Article Highly Selective Oxygen/Nitrogen Separation Membrane Engineered Using a Porphyrin-Based Oxygen Carrier Jiuli Han 1,2, Lu Bai 1, Bingbing Yang 1,2, Yinge Bai 1, Shuangjiang Luo 1, Shaojuan Zeng 1, Hongshuai Gao 1, Yi Nie 1,3, Xiaoyan Ji 4, Suojiang Zhang 1,2,* and Xiangping Zhang 1,2,* 1 Beijing Key Laboratory of Ionic Liquids Clean Process, State Key Laboratory of Multiphase Complex Systems, CAS Key Laboratory of Green Process and Engineering, Institute of Process Engineering, Chinese Academy of Sciences, Beijing 100190, China 2 School of Chemical Engineering, University of Chinese Academy of Sciences, Beijing 100049, China 3 Zhengzhou Institute of Emerging Industrial Technology, Zhengzhou 450000, China 4 Energy Engineering, Division of Energy Science, Luleå University of Technology, 97187 Luleå, Sweden * Correspondence: [email protected] (S.Z.); [email protected] (X.Z.); Tel.: +86-10-82627080 (S.Z.); +86-10-82544875 (X.Z.) Received: 16 August 2019; Accepted: 30 August 2019; Published: 3 September 2019 Abstract: Air separation is very important from the viewpoint of the economic and environmental advantages. In this work, defect-free facilitated transport membranes based on poly(amide-12-b-ethylene oxide) (Pebax-2533) and tetra(p-methoxylphenyl)porphyrin cobalt chloride (T(p-OCH3)PPCoCl) were fabricated in systematically varied compositions for O2/N2 separation. T(p-OCH3)PPCoCl was introduced as carriers that selectively and reversibly interacted with O2 and facilitated O2 transport in the membrane. The T(p-OCH3)PPCoCl had good compatibility with the Pebax-2533 via the hydrogen bond interaction and formed a uniform and thin selective layer on the substrate. -
HEATS of COMBUSTION of HIGH TEMPERATURE POLYMERS Richard N
HEATS OF COMBUSTION OF HIGH TEMPERATURE POLYMERS Richard N. Walters*, Stacey M. Hackett* and Richard E. Lyon Federal Aviation Administration William J. Hughes Technical Center Fire Safety Section AAR-422 Atlantic City International Airport New Jersey 08405 *Galaxy Scientific Corporation 2500 English Creek Avenue, Building C Egg Harbor Township, New Jersey 08234 ABSTRACT The heats of combustion for forty-nine commercial and developmental polymers of known chemical structure were determined using an oxygen bomb calorimeter according to standard methods. The experimental results were compared to thermochemical calculations of the net heat of combustion from oxygen consumption and the gross heat of combustion from group additivity of the heats of formation of products and reactants. The polymers examined were thermally stable, char forming thermoplastics and thermoset resins containing a significant degree of aromaticity and heteroatoms including– nitrogen, sulfur, phosphorus, silicon, and oxygen in linear and heterocyclic structures. The gross and net heats of combustion calculated from polymer enthalpies of formation and oxygen consumption thermochemistry were within 5 percent of the experimental values from oxygen bomb calorimetry. The heat released by combustion per gram of diatomic oxygen consumed in the present study was E = 13.10 ± 0.78 kJ/g-O2 for polymers tested (n = 48). This value is indistinguishable from the universal value E = 13.1 kJ/g-O2 used in oxygen consumption combustion calorimetry. Key Words: Heat of combustion, polymers, thermochemistry, oxygen bomb calorimetry, heat release, fire INTRODUCTION Commercial passenger aircraft cabins contain several tons of combustible plastics, thermoset resins, and elastomers in sidewall panels, ceilings, seat parts, foamed cushions, carpets, etc. -
Preparation of Polyetherimide Membrane from Non-Toxic Solvents
Alqaheem et al. Chemistry Central Journal (2018) 12:80 https://doi.org/10.1186/s13065-018-0449-7 RESEARCH ARTICLE Open Access Preparation of polyetherimide membrane from non‑toxic solvents for the separation of hydrogen from methane Yousef Alqaheem* , Abdulaziz Alomair, Abdulwahab Alhendi, Sharifah Alkandari, Nusrat Tanoli, Nourah Alnajdi and Andrés Quesada‑Peréz Abstract Polymeric membranes are usually prepared from solvents like n-methylpyrrolidone (NMP) because of the strong dissolving power and high boiling point. Yet, the solvent is costly, toxic and has environmental issues. In this work, nontoxic solvents such as methyl L-lactate, ethyl lactate, propylene carbonate, tributyl o-acetylcitrate, tributyl citrate, triethyl phosphate, and γ-butyrolactone (GBL) were introduced during membrane preparation. It was found that all the solvents were unable to dissolve polyetherimide except GBL. The membranes made by GBL and NMP were evalu‑ ated for gas separation, and they have almost similar hydrogen-to-methane selectivity, but, hydrogen permeance was better in NMP membranes. Keywords: Membrane, Polyetherimide, Nontoxic solvents, Hydrogen, Methane Introduction mixing the solution to obtain a homogenous mixture, (3) Polymeric membranes were introduced in the oil/gas tape casting the solution by an applicator with a preset industry in the 1980s for the separation of hydrogen from thickness, and (4) immersing the solution in a water bath natural gas [1]. Te technology was successful because of to form the polymer flm. Te membrane is then left to the low operating cost and zero emission [2]. Later, the dry before operation. applications were expanded to include carbon dioxide Solvents like n-methylpyrrolidone (NMP) is commonly capture, air separation, and recovery of volatile organic used for membrane preparation because of the strong compounds [3]. -
Development of Microcellular Conductive Foams Based on Polyetherimide with Graphene Nanoplatelets
Development of microcellular conductive foams based on polyetherimide with graphene nanoplatelets By Hooman Abbasi In partial fulfillment of the requirements for the degree of Doctor of Philosophy In Materials Science and Engineering Director: Prof. José Ignacio Velasco Perero Co-Director: Prof. Marcelo de Sousa Pais Antunes Department of Materials Science and Metallurgy July 2019 Acta de calificación de tesis doctoral Curso académico: Nombre y apellidos Programa de doctorado Unidad estructural responsable del programa Resolución del Tribunal Reunido el Tribunal designado a tal efecto, el doctorando / la doctoranda expone el tema de la su tesis doctoral titulada _______________________________________________________________________________________________ ______________________________________________________________________________________________. Acabada la lectura y después de dar respuesta a las cuestiones formuladas por los miembros titulares del tribunal, éste otorga la calificación: NO APTO APROBADO NOTABLE SOBRESALIENTE (Nombre, apellidos y firma) (Nombre, apellidos y firma) Presidente/a Secretario/a (Nombre, apellidos y firma) (Nombre, apellidos y firma) (Nombre, apellidos y firma) Vocal Vocal Vocal ______________________, _______ de __________________ de _______________ El resultado del escrutinio de los votos emitidos por los miembros titulares del tribunal, efectuado por la Escuela de Doctorado, a instancia de la Comisión de Doctorado de la UPC, otorga la MENCIÓN CUM LAUDE: SÍ NO (Nombre, apellidos y firma) (Nombre, apellidos -
Removal of Metal Ions and Humic Acids Through Polyetherimide
www.nature.com/scientificreports OPEN Removal of metal ions and humic acids through polyetherimide membrane with grafted bentonite Received: 7 December 2017 Accepted: 1 March 2018 clay Published: xx xx xxxx Raghavendra S. Hebbar1, Arun M. Isloor1, Balakrishna Prabhu2, Inamuddin3,4, Abdullah M. Asiri3,4 & A. F. Ismail5 Functional surfaces and polymers with branched structures have a major impact on physicochemical properties and performance of membrane materials. With the aim of greener approach for enhancement of permeation, fouling resistance and detrimental heavy metal ion rejection capacity of polyetherimide membrane, novel grafting of poly (4-styrenesulfonate) brushes on low cost, natural bentonite was carried out via distillation-precipitation polymerisation method and employed as a performance modifer. It has been demonstrated that, modifed bentonite clay exhibited signifcant improvement in the hydrophilicity, porosity, and water uptake capacity with 3 wt. % of additive dosage. SEM and AFM analysis showed the increase in macrovoides and surface roughness with increased additive concentration. Moreover, the inclusion of modifed bentonite displayed an increase in permeation rate and high anti-irreversible fouling properties with reversible fouling ratio of 75.6%. The humic acid rejection study revealed that, PEM-3 membrane having rejection efciency up to 87.6% and foulants can be easily removed by simple hydraulic cleaning. Further, nanocomposite membranes can be signifcantly employed for the removal of hazardous heavy metal ions with a rejection rate of 80% and its tentative mechanism was discussed. Conspicuously, bentonite clay-bearing poly (4-styrenesulfonate) brushes are having a synergistic efect on physicochemical properties of nanocomposite membrane to enhance the performance in real feld applications.