Rolls-Royce Coachbuild: a Glorious Legacy
Total Page:16
File Type:pdf, Size:1020Kb
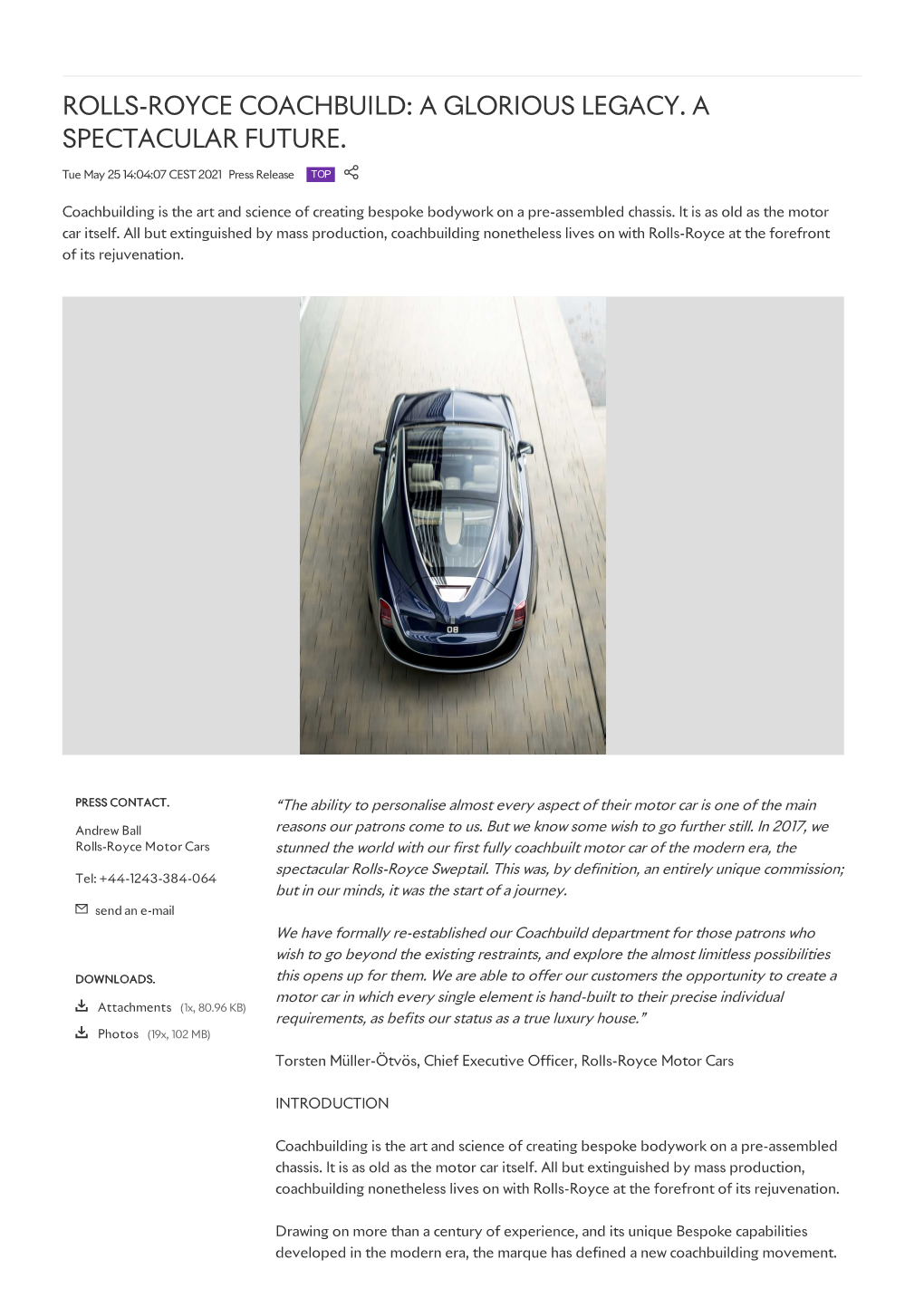
Load more
Recommended publications
-
Chassis Design for SAE Racer
University of Southern Queensland Faculty of Engineering and Surveying Chassis Design for SAE Racer A dissertation submitted by: Anthony M O’Neill In fulfilment of the requirements of ENG 4111/2 Research Project Towards the degree of Bachelor of Engineering (Mechanical) Submitted: October 2005 1 Abstract This dissertation concerns the design and construction of a chassis for the Formula SAE-Aust race vehicle – to be entered by the Motorsport Team of the University of Southern Queensland. The chassis chosen was the space frame – this was selected over the platform and unitary styles due to ease of manufacture, strength, reliability and cost. A platform chassis can be very strong, but at the penalty of excessive weight. The unitary chassis / body is very expensive to set up, and is generally used for large production runs or Formula 1 style vehicles. The space frame is simple to design and easy to fabricate – requiring only the skills and equipment found in a normal small engineering / welding workshop. The choice of material from which to make the space frame was from plain low carbon steel, AISI-SAE 4130 (‘chrome-moly’) or aluminium. The aluminium, though light, suffered from potential fatigue problems, and required precise heat / aging treatment after welding. The SAE 4130, though strong, is very expensive and also required proper heat treatment after welding, lest the joints be brittle. The plain low carbon steel met the structural requirements, did not need any heat treatments, and had the very real benefits of a low price and ready availability. It was also very economical to purchase in ERW (electric resistance welded) form, though CDS (cold drawn seamless) or DOM (drawn over mandrel) would have been preferable – though, unfortunately, much more expensive. -
Emergency Steer & Brake Assist – a Systematic Approach for System Integration of Two Complementary Driver Assistance Syste
EMERGENCY STEER & BRAKE ASSIST – A SYSTEMATIC APPROACH FOR SYSTEM INTEGRATION OF TWO COMPLEMENTARY DRIVER ASSISTANCE SYSTEMS Alfred Eckert Bernd Hartmann Martin Sevenich Dr. Peter E. Rieth Continental AG Germany Paper Number 11-0111 ABSTRACT optimized trajectory. In this respect and beside all technical and physical aspects, the human factor plays a major role for the development of this Advanced Driver Assistance Systems (ADAS) integral assistance concept. Basis for the assist the driver during the driving task to improve development of this assistance concept were subject the driving comfort and therefore indirectly traffic driver vehicle tests to study the typical driver safety, ACC (Adaptive Cruise Control) is a typical behavior in emergency situations. Objective example for a “Comfort ADAS” system. “Safety was on the one hand to analyze the relevant ADAS” directly target the improvement of safety, parameters influencing the driver decision for brake such as a forward collision warning or other and/or steer maneuvers. On the other hand the systems which assist the driver during an evaluation should result in a proposal for a emergency situation. A typical application for a preferable test setup, which can be used for use case “Safety ADAS” is EBA (Emergency Brake Assist), evasion and/or braking tests to clearly evaluate the which additionally integrates information of benefit of the system and the acceptance of normal surrounding sensors into the system function. drivers. Definition of assistance levels, warnings While systems in the longitudinal direction, such as and intervention cascade, based on physical aspects EBA, have achieved a high development status and and an analysis of driver behavior using objective are already available in the market (e.g. -
Petersen Automotive Museum Celebrates Pininfarina with New Exhibit
MARCH 2021/PRESS RELEASE PETERSEN AUTOMOTIVE MUSEUM CELEBRATES PININFARINA WITH NEW EXHIBIT “The Aesthetic of Motoring: 90 Years of Pininfarina” will showcase the diversity and versatility of the coachbuilder’s designs through four milestone examples – the 1931 Cadillac Model452A Boattail Roadster, 1947 Cisitalia 202 Coupe, 1966 Dino Berlinetta 206 GT Prototype and 2019 Automobili Pininfarina “Battista” Design Model Los Angeles, March 23 2021 – The Petersen 206 GT Prototype, the first mid-engine Ferrari; and Automotive Museum in Los Angeles will debut a 2019 Automobili Pininfarina “Battista”, which is a new exhibit celebrating Italian design firm and an early design model of the luxury hypercar rather coachbuilder Pininfarina on March 25. Located in the than a functioning automobile. A 1967 Ferrari 365P Armand Hammer Foundation Gallery, “The Aesthetic Berlinetta Speciale “Tre Posti,” the last vehicle bodied of Motoring: 90 Years of Pininfarina” will convey the by Pininfarina for a private client, will replace the 1966 significance and evolution of the Italian car design firm Dino Berlinetta 206 GT Prototype in April 2021. and coachbuilder through a curated display of four key automobiles representing its storied 90-year history. “With its commitment to elegant, aerodynamic design and small-scale production, Pininfarina has created Vehicles on display will include a 1931 Cadillac some of the most innovative and revered car designs Model452A Boattail Roadster, the first Pininfarina in the history of the automobile,” said Petersen body mounted -
Brochure G4-ENG-2020.Indd
WHEELBASE CHARACTERISTICS DIMENSIONS A B C D* D’* E F G H I J K L M N P T mm 3 600 1 574 1 305 1 200 1 305 1 893 423 897 288 175 2 022 1 045 1 045 1 089 489 697 282 TECHNICAL CHARACTERISTICS HOMOLOGATION | SEATS ELECTRIC POWERTRAIN Homologation N1 / L7e Motor AC Induction Seats 2 Type TSA200-120-250 PERFORMANCES Motor voltage 29 V AC Maximum speed 50 km/h Max peak power 16.3 kW Noise moving (R (EU) 51) 63,7 dB(A) Nominal power (S2-30 minutes) 10 kW Maximum gradient empty 30 % Torque @ max peak power 76 Nm Maximum gradient loaded | loaded with trailer 15 % | 12 % Max torque @ 0 rpm 81 Nm MASSES BRAKES Baseweight (wheelbase + doors + towing hook bracket + battery bracket) 582 kg Main brake type Dual circuit in X Maximum permissible mass** 2 100 kg Emergency brake type Hydraulic diagonal action Maximum weight of the combination (GCW) 3 500 kg (N1) | 2 385 kg (L7e) Front brake disc Ø 247 mm Tow load capacity for road approved trailers (with brakes) 1 400 kg (N1) | 291 kg (L7e) Front brake caliper Ø 48 mm Tow load capacity for road approved trailers (without brakes) 750 kg (N1) | 291 kg (L7e) Rear drum brake 230 mm DIMENSIONS Parking brake Hand actuated Overall length 3 600 mm SUSPENSIONS Overall width 1 200 mm (N1) | 1305 mm (L7e) Front suspension type McPherson Overall height 1 893 mm Travel 163 mm Wheel base 2 022 mm Rear suspension type Composite blades Front / Rear track 1 045 mm Travel 96 mm Front overhang | Rear overhang 1 089 mm | 489 mm WHEELS AND TYRES Front clearance angle 20° Tyre type Tubeless External turning radius (wall to -
Subframe Design General
Subframe design General General The subframe can be used for the following purposes: • It provides clearance for wheels and other parts which protrude above the frame. • It provides rigidity and reduces the stress in the rear overhang. • It protects the chassis frame by distributing the load from the bodywork evenly over a larger area of the chassis frame. • It contributes to dampening frame oscillations that cause discomfort. To adapt the subframe to the torsionally flexible part of the chassis frame, the sub- frame should also be torsionally flexible, provided the bodywork allows it. There- fore, the side members and crossmembers of the subframe should consist mainly of open profiles, e.g. U-profiles. 376 530 More information on chassis frames is found in the document Chassis frames. More information on chassis frames and subframes is found in the document Select- ing the subframe and attachment. More information on the concepts of torsional rigidity and torsional flexibility is found in the document Forces and movements. Scania Truck Bodybuilder 22:10-649 Issue 2 2016-09-02 © Scania CV AB 2016, Sweden 1 (8) Subframe design General The subframe can appear differently depending on the characteristics required. The subframe length can vary. It can cover the whole chassis frame or be short and only cover part of the chassis frame. The height of the chassis frame can be adjusted to the current area of application. 376 541 Example of a subframe. Scania Truck Bodybuilder 22:10-649 Issue 2 2016-09-02 © Scania CV AB 2016, Sweden 2 (8) Subframe design General Side members The subframe’s side members are usually manufactured from U-profiles, just as the chassis frame’s side members. -
A Thesis Entitled Design, Analysis and Optimization of Rear Sub-Frame Using Finite Element Modeling and Modal Analysis by Gaurav
A Thesis entitled Design, Analysis and Optimization of Rear Sub-frame using Finite Element Modeling and Modal Analysis by Gaurav Kesireddy Submitted to the Graduate Faculty as partial fulfillment of the requirements for the Master of Science Degree in Mechanical Engineering _________________________________________ Dr. Hongyan Zhang, Committee Chair _________________________________________ Dr. Sarit Bhaduri, Committee Member _________________________________________ Dr. Matthew Franchetti, Committee Member _________________________________________ Dr. Amanda Bryant-Friedrich, Dean College of Graduate Studies The University of Toledo May 2017 Copyright 2017, Gaurav Kesireddy This document is copyrighted material. Under copyright law, no parts of this document may be reproduced without the expressed permission of the author. An Abstract of Design, Analysis and Optimization of Rear Sub-frame using Finite Element Modeling and Modal Analysis by Gaurav Kesireddy Submitted to the Graduate Faculty as partial fulfillment of the requirements for the Master of Science Degree in Mechanical Engineering The University of Toledo May 2017 A sub-frame is a structural component of an automobile that carries suspension, exhaust, engine room, etc. The sub-frame is generally bolted to Body in White(BIW). It is sometimes equipped with springs and bushes to dampen vibration. The principal purposes of using a sub-frame are, to spread high chassis loads over a wide area of relatively thin sheet metal of a monocoque body shell, and to isolate vibration and harshness from the rest of the body. As a natural development from a car with a full chassis, separate front and rear sub-frames are used in modern vehicles to reduce the overall weight and cost. In addition, a sub-frame yields benefits to production in that subassemblies can be made which can be introduced to the main body shell when required on an automated line. -
Vehicle Make: Model: Chassis Number (Full): Registration/Retail Date: Registration Number: Miles/Kilometres: Assessment Date: Be
BENTLEY CERTIFIED PRE-OWNED EXTENDED SERVICE PROGRAM TECHNICAL INSPECTION TECHNICAL INSPECTION Vehicle Make: Model: Registration Number: Miles/Kilometres: Registration/Retail Date: Chassis Number (Full): Bentley Certified Technician: Assessment Date: I. CHECK FOR LEVELS AND LEAKS III. OPERATION AND CONDITION CHECK V. AFTER ROAD TEST 1. Engine Oil 37. Ignition/Starter 71. Check for Visible Leaks 2. Transmission Oil 38. Suspension and Shock Absorbers 72. Glass for Chips, Cracks, 3. Power Steering Fluid 39. Engine and Suspension Mountings Delamination and Correct/Legal Tint 4. Brake Fluid 40. Steering and Suspension Joints 73. Bodywork Commensurate with Age/Miles (no dents or scratches) 5. Hydraulic Oil 41. Wheel Bearings for wear 74. Carpets Commensurate with 6. Engine Coolant (inc specific gravity) and adjustment Age and Mileage (appearance 42. Rubber Boots and Gaiters 7. Washer Reservoir and security) 43. Propeller Shaft/Drive Shafts - 8. Fuel System Leaks 75. Upholstery and Headlining Condition/Tightness 9. Final Drive Oil (appearance and security) 44. All Drive Belts - Condition/Tightness 76. Veneers and trim (appearance II. FUNCTION TEST 45. Brake Pipes and Hoses - and security) Condition and Security 10. Check for Oustanding Recalls/ 46. Brake pads for Wear/Serviceability VI. FINAL PREPARATION Service Campaigns and Software 47. Underbody and Exhaust (including Downloads 77. Check Service History and Update the Catalytic Convertor) - Damage/ if Necessary 11. Parking Brake Operation Corrosion 78. Check the Operation of the Spare 12. Bonnet/Boot Release and 48. Check Operation of Exhaust Key Fob Safety Catch Solenoid Valve 79. Compliance with Statutory 13. Operation of Doors, Boot, 49. Clear Body Drains Glove Box etc. -
NEVER SETTLE. It’S Your Adventure
NEVER SETTLE. It’s your adventure. 2021 ENTEGRA CHASSIS GUIDE | SPARTANRVCHASSIS.COM THE PREMIER 1 Safe Haul™ integrated tow FOUNDATION. vehicle braking system 2 Side-mounted At the bottom of it all is the Spartan chassis, service center made from the finest materials and engineered to give your luxury coach a safe, 3 Campground-friendly smooth, and reliable ride. Spartan has the cooling center features and components that give you confidence from the road up. 4 Passive steer tag axle 5 Tire pressure monitoring system 6 Torsion control 7 20-year frame and cross-member warranty, assembled with American steel 8 Independent front suspension and race inspired shocks 9 Air brakes with suspended adjustable pedal 10 Equipped with E-Z Steer steering assist system 11 Spartan Connected Coach™ digital dash and passive keyless start Note: Some features available as optional content on specific OEM models (could vary by model year). The industry’s best chassis built, around safety and technology. Our industry-leading Spartan Advanced Protection System (APS) provides Spartan chassis owners with comprehensive safety technology that helps you avoid collisions and keeps you alert to anything that could go wrong. ▪ Spartan Safe Haul™ ▪ Collision Mitigation with Adaptive Cruise Control ▪ Electronic Stability Control E-Z Steer adapts to signals from the vehicle and analyzes driver ▪ Automatic Traction Control input to provide smoother, more precise steering, helping to ▪ Tire Pressure Monitoring System improve performance, reduce driver fatigue, and enhance the driving experience for anyone behind the wheel. Everything you need, on clear display. Spartan’s Connected Coach™ gives you a complete and intuitive digital dashboard display that you can customize to your exact wants and needs. -
2020 Tahoe 2Wd Police Package 9C1
2020 TAHOE 2WD POLICE PACKAGE 9C1 1 About This Publication This catalog is not updated during the model year and should not be used for This catalog is not updated during the model year and should not be used for ordering purposes. It is intended as a source of basic information. All illustrations ordering purposes. It is intended as a source of basic information. All illustrations and specifications in this literature are based on the latest product information and specifications in this literature are based on the latest product information available at the time of publication. General Motors reserves the right to make available at the time of publication. General Motors reserves the right to make changes at any time without notice. For further details, consult your local dealer. changes at any time without notice. For further details, consult your local dealer. Care must be taken during customer installation of equipment and wiring to ensure Care must be taken during customer installation of equipment and wiring to that all holes drilled in the body are corrosion protected, properly sealed and that ensure that all holes drilled in the body are corrosion protected, properly sealed vehicle wiring harnesses, piping or other components have not been displaced and that vehicle wiring harnesses, piping or other components have not been or damaged. Wiring connection or splice changes are to be removed before displaced or damaged. Aftermarket equipment installers must be mindful of the vehicle is returned to civilian use. Aftermarket equipment installers must be applicable Federal Motor Vehicle Safety Standards. This information can be mindful of applicable Federal Motor Vehicle Safety Standards. -
Lightweight Chassis Development at Ford Motor Company
Lightweight Chassis Development at Ford Motor Company Xiaoming Chen, John Uicker and David Wagner Overview • Lightweight Design Strategies • Magnesium Subframe Development • Carbon Fiber Composite Subframe Design • F-150 aluminum Cross Members • Lightweight Coil Springs • Summary Lightweight Chassis Design Strategies • Efficient structure design – Knowledge database – CAE driven opJmizaons • Lightweight material applicaons – Aluminum – Magnesium – Carbon fiber composite • Cost esmates – Variable cost – Tooling cost Magnesium Subframe Development High pressure die cast magnesium subframe Supplier partner : Meridian Magnesium CAE Driven Design Met all sJffness targets Met durability and strength requirements Analyzed strain caused by bolt proof loads Magnesium Prototype 4.8 kg (30%) weight saved Tests Planned Corrosion miJgaon Component fague Component strength Bolt load retenJon Proving ground durability, corrosion and special events Magnesium Subframe Development Design Iteration start with stiffness requirements Package investigation Design block for topology optimization Topology contour of material distribution Part geometry Magnesium Subframe Development Other Design Attributes Strain contour under extreme loads Durability life contour Strain contour under bolt proof loads CMM for dimension and tolerance control Carbon Fiber Composite Subframe Concepts Compression molded composite and UD laminates Supplier partner : Cosma Interna>onal and Magna Exteriors Steel front subframe Steel rear subframe CF front subframe CF and Al rear subframe -
GM S10 Late Rear Disc Brake Conversion Fitment
GM S10 Late Rear Disc Brake Conversion Fitment • 92-03 S-series Trucks • 93-04 Some F-Body Even if your model is listed above, if it does not have the flange shown here, then the kit will not fit. Note: The flange can be measured easily from the back side of the drum, without removing anything. Dimensions Warning • Disc brakes should only be installed by someone experienced and competent in the installation and maintenance of disc brakes. • If you are not sure of how to safely use this brake component or kit, you should not install or use it. • Do not assume anything. Improperly installed or maintained brakes are dangerous. If you are not sure, get help or return the product. Notes • As with most suspension and tire modifications (from OEM specifications), changing the brakes may alter the front to rear brake bias. Your specific needs will depend on other modifications to the system. • For added user control, the factory proportioning valve can be swapped to an adjustable proportioning valve such as Wilwood 260-10922. Installation of a Wilwood adjustable proportioning valve will require brake line work on your end to install since it is not a direct swap. • The brackets in this kit are designed to be installed without removing the differential cover. This can be done by use of a cut-off wheel or reciprocating saw to split the drum backing plate into two pieces for removal. If you wish to retain your drum backing plates, the axles can be removed from the housing by draining the fluid, then removing the differential cover, cross pin, and C-clip retainers. -
Chassis Frame and Body
UNIT 1 Chassis Frame and Body Structure 1.1 Introduction of chassis frame 1.2 Layout of chassis and its main components 1.3 Functions of the chassis frame 1.4 Types of chassis frame 1.5 Various loads acting on the chassis frame 1.6 Different bodies used in Automobiles 1.7 Requirement of bodies for various types of vehicles. Learning Objectives After studying this unit the student will able to learn about • Requirement of chassis frame • Types of Chassis frame • Loads acting on chassis frame • Layout of chassis and its parts • Different types of automobile bodies 1.1 Introduction of Chassis Frame Chassis frame is the basic frame work of the automobile. It supports all the parts of the automobile attached to it. It is made of drop forged steel. All the parts related to automobiles are attached to it only. All the systems related to automobile like powerplant,transmission, steering, suspension, braking system etc are attached to and supported by it only. 1.2 Layout of Chassis and its main components “Chassis” a French term which means the complete Automobiles without Body and it includes all the systems like power plant, transmission, steering, suspension , wheels tyres , auto electric system etc. without body. If Body is also attached to it them it is known as the particular vehicle as per the shape and design of the body. Shackel Front Shackle Frame R e a r D u m b spring Spring Iron Engine Gear box Rear Axle Radiator Clutch Propeller Shaft Side members Horizontal P e t r o l Member Tank Fig 1.1 Chassis 90 Automobile Engineering Technician 1.3 The Functions of the Chassis frame 1.