Effects of Voltage Interharmonics on Cage Induction Motors
Total Page:16
File Type:pdf, Size:1020Kb
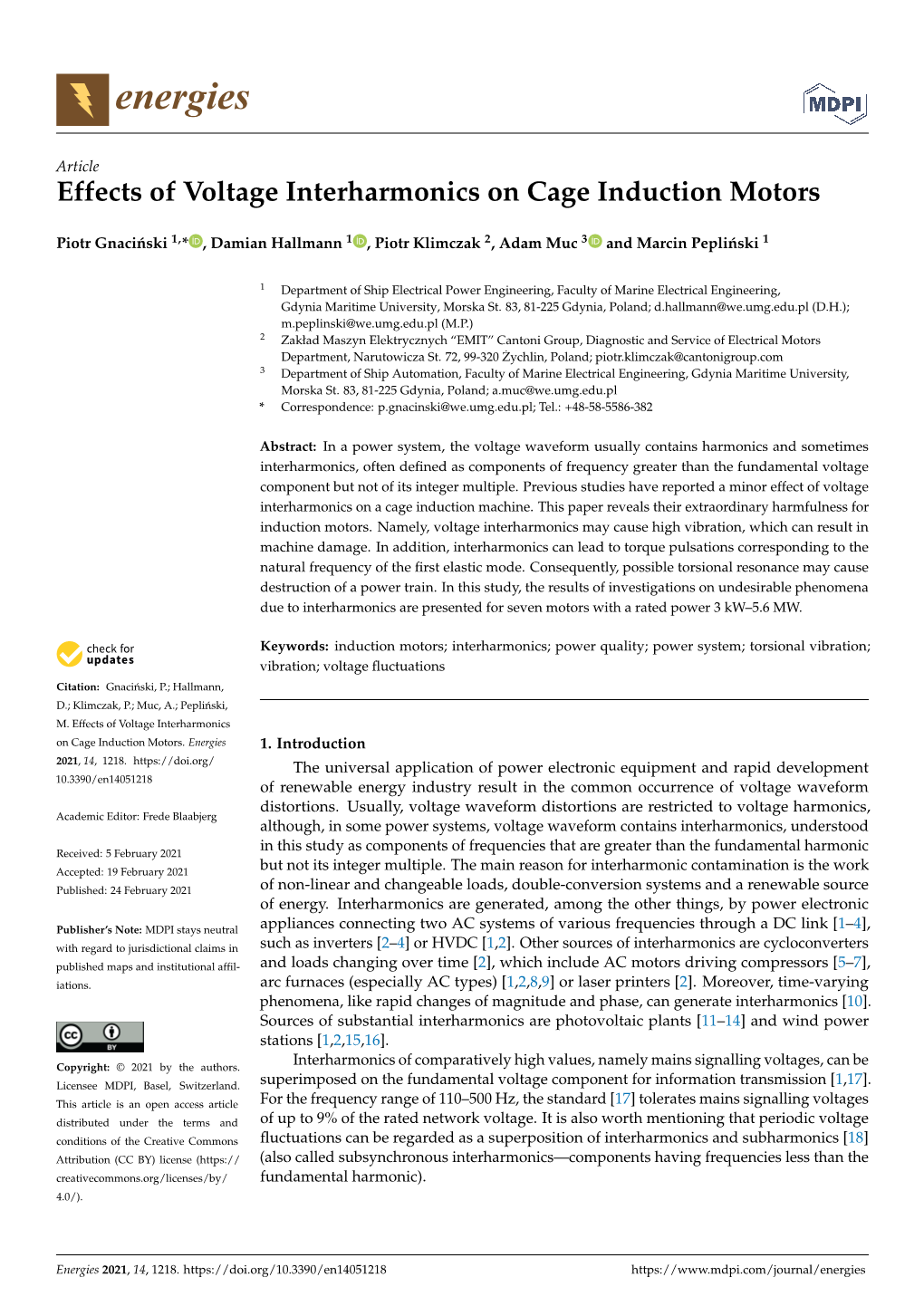
Load more
Recommended publications
-
Resultados Oficiais
Resultados Oficiais Shot Put - M QUALIFICATION Qual. rule: qualification standard 20.20m or at least best 8 qualified. Group A 07 March 2008 - 10:00 Position Bib Athlete Country Mark . 1 346 Reese Hoffa USA 21.49 Q(SB) 2 341 Christian Cantwell USA 20.91 Q. 3 13 Scott Martin AUS 20.83 Q (AR) 4 192 Dorian Scott JAM 20.62 Q (NR) 5 31 Andrei Mikhnevich BLR 20.58 Q . 6 239 Rutger Smith NED 20.30 Q . 7 154 Peter Sack GER 20.27 Q . 8 251 Tomasz Majewski POL 20.23 Q . 9 28 Hamza Alic BIH 20.00 . 10 294 Pavel Sofin RUS 19.95 . 11 304 Miran Vodovnik SLO 19.94 . 12 139 Carl Myerscough GBR 19.86 (SB) 13 310 Milan Haborák SVK 19.80 . 14 93 Manuel Martínez ESP 19.75 (SB) 15 49 Dylan Armstrong CAN 19.56 . 16 111 Robert Häggblom FIN 19.42 . 17 328 Yuriy Bilonoh UKR 19.02 . 18 78 Kim Christensen DEN 18.26 . 19 226 Ivan Emilianov MDA 18.16 . 20 261 Marco Fortes POR 17.96 . 21 324 Ming Huang Chang TPE 17.73 . Athlete 1st 2nd 3rd Reese Hoffa 21.49 Christian Cantwell 19.25 20.91 Scott Martin 20.12 19.85 20.83 Dorian Scott 19.56 20.62 Andrei Mikhnevich 20.58 Rutger Smith 19.96 19.60 20.30 Peter Sack 20.27 Tomasz Majewski 19.89 20.23 Hamza Alic 19.36 20.00 19.96 Pavel Sofin 19.71 19.95 19.95 Miran Vodovnik 19.26 18.94 19.94 Carl Myerscough X X 19.86 Milan Haborák 19.80 X X Manuel Martínez 19.56 19.64 19.75 Dylan Armstrong 19.56 X 19.03 Robert Häggblom 19.41 X 19.42 Yuriy Bilonoh 19.02 X - Kim Christensen 17.95 17.87 18.26 Ivan Emilianov 18.16 18.07 X Marco Fortes X 17.96 X Ming Huang Chang 17.73 X X High Jump - M QUALIFICATION Qual. -
High-Power Induction Motors Supplied with Voltage Containing Subharmonics
energies Article High-Power Induction Motors Supplied with Voltage Containing Subharmonics Piotr Gnaci ´nski 1,* and Piotr Klimczak 2 1 Department of Ship Electrical Power Engineering, Faculty of Marine Electrical Engineering, Gdynia Maritime University, 81-225 Gdynia, Poland 2 Diagnostic and Service of Electrical Motors Department, Zakład Maszyn Elektrycznych “EMIT” Cantoni Group, 99-320 Zychlin,˙ Poland; [email protected] * Correspondence: [email protected]; Tel.: +48-58-5586-382 Received: 14 October 2020; Accepted: 10 November 2020; Published: 12 November 2020 Abstract: In some power networks, components of frequency less than the frequency of the fundamental voltage harmonic called subharmonics or subsynchronous interharmonics occur. In this paper, the effect of voltage subharmonics on currents, power losses, speed fluctuations and electromagnetic torque is examined. The results of numerical computations using the finite element method for an induction cage motor of rated power of 5.6 MW and four motors of rated power of 200 kW with different numbers of poles are presented. An extraordinary harmful effect on high-power induction motors is demonstrated. Among other effects, voltage subharmonics cause significant torque pulsations whose frequencies may correspond to the elastic-mode natural frequency. Possible resonance can result in excessive torsional vibration and the destruction of a power train. Keywords: induction motors; interharmonics; power losses; power quality; power system; subharmonics; voltage fluctuations 1. Introduction Voltage waveform distortions exert a noxious effect on various elements of a power system, which in extreme cases may pose a threat to human safety and the environment [1]. Distorted voltage waveforms generally contain harmonic components. -
Komunikat Końcowy
35. Memoriał J. śylewicza GDA ŃSK, 07 lipca 2007 KOMUNIKAT KO ŃCOWY Obsada s ędziowska Sędzia Główny Zawodów Kazimierz Brzoza Delegat Techniczny PZLA Henryk Adamski Starterzy Łukasz Kokot Czesław Lis Tomasz Piotrowski Sędziowie Główni Biegów Jan Białek Maciej Jakubowski Jakub Kortas Sędziowie Główni Rzutów Grzegorz Batóg Bernadeta Blechacz Henryk Fiedorowicz Sędziowie Główni Skoków El Ŝbieta Korolewska Szczepan Ojrzanowski Jan Tarnowski Wiatromierz Teresa Drobi ńska Katarzyna Tarnowska Pomiar Czasu / Wyniki (FinishLynx)-DomTel-Sport Słupsk Michał Choroma ński Ryszard Pilarczyk Spiker Roman Toboła Paweł Zi ęba Bramka Piotr Gendig Leon Walenciak Wa Ŝenie sprz ętu Hubert Tobias Rzut oszczepem kobiet 07-07-0715:30 godz. zak. 15:50 RŚ: 71.54 Osleidys MENENDEZ CUB Réthymno 01/07/01 RE: 69.48 Trine HATTESTAD-SOLBERG NOR Oslo 28/07/00 Sędzia: Fiedorowicz Henryk RP: 64.08 Barbara MADEJCZYK JANTAR Ustka Malaga 28/06/06 Miejsce T/Lp Numer Imi ę i nazwisko Rocznik Klub Wynik 1 2 52 Agnieszka LEWANDOWSKA 88 AZS-AWFiS Gda ńsk 45.45 2 1 49 Agata ANTONOWICZ 87 AZS-AWFiS Gda ńsk 44.22 R. ś. z rokiem uzyskania, RP-R. Polski, RE-R. Europy, RŚ-R. Świata Strona 1 07-07-07 20:37:34 GDA ŃSK 2007 Przygotowanie: DomTel-Sport Słupsk, tel. 0602 314171 www.domtel.pl 3 4 50 Ewelina SZYBOWSKA 87 AZS-AWFiS Gda ńsk 43.80 4 3 53 Marta MALINOWSKA 90 AZS-AWFiS Gda ńsk 40.30 =PB I II III IV V VI Agnieszka LEWANDOWSKA x 40.19 45.45 40.72 44.54 40.92 Agata ANTONOWICZ 43.35 39.00 44.22 x 42.83 x Ewelina SZYBOWSKA 43.80 x 40.89 40.67 x 39.98 Marta MALINOWSKA 36.33 37.51 38.34 40.30 38.68 37.67 Rzut dyskiem kobiet 07-07-0716:30 godz. -
1St Round ROUND RESULTS
12th IAAF World Indoor Championships Valencia From Friday 7 March to Sunday 9 March 2008 4x400 Metres Relay Men ATHLETIC ATHLETIC ATHLETIC ATHLETIC ATHLETIC ATHLETIC ATHLETIC ATHLETIC ATHLETIC ATHLETIC ATHLETIC ATHLETIC ATHLETIC ATHLETIC ATHLETIC ATHLETIC ATHLETIC ATHLETIC ATHLETIC ATHLETIC ATHLETIC ATHLETIC ATHLETIC ATHL 1st Round ROUND RESULTS ATHLETIC ATHLETIC ATHLETIC ATHLETIC ATHLETIC ATHLETIC ATHLETIC ATHLETIC ATHLETIC ATHLETIC ATHLETIC ATHLETIC ATHLETIC ATHLETIC ATHLETIC ATHLETIC ATHLETIC ATHLETIC ATHLETIC ATHLETIC ATHLETIC ATHLETIC ATHLETIC ATHLETI First 2 of each heat (Q) plus 2 fastest times (q) qualified 9 March 2008 TIME Start 10:59 Heat 1 2 RANK TEAM NAT LANEREACTION TIME RESULT 1 UNITED STATES USA 4 0.176 3:08.07 Q 366 James DAVIS 367 Kelly WILLIE 368 Joel STALLWORTH 365 Jamaal TORRANCE 2 RUSSIA RUS 5 0.250 3:08.17 Q SB 275 Denis ALEKSEYEV 289 Vladislav FROLOV 291 Ivan BUZOLIN 290 Anton KOKORIN 3 GREAT BRITAIN & N.I. GBR 2 0.214 3:08.21 q SB 132 Steven GREEN 122 Richard BUCK 129 Dale GARLAND 127 Robert TOBIN 4 BAHAMAS BAH 3 0.263 3:11.77 SB 20 Andrae WILLIAMS 18 Nathaniel MCKINNEY 21 Douglas LYNES-BELL 19 Michael MATHIEU 5 LIBERIA LBR 6 0.129 3:12.14 PB 217 Bobby YOUNG 216 Hafiz GREIGRE 378 Marvin LEWIS 377 Siraj WILLIAMS INTERMEDIATE TIMES 400m RUSSIA 47.13 800m UNITED STATES 1:34.34 1200m RUSSIA 2:21.38 1 2 Issued Sunday, 09 March 2008 at 11:18 Timing and Measurement by SEIKO Data processing by EPSON 4x400 Metres Relay Men - 1st Round ROUND RESULTS 9 March 2008 TIME Start 11:11 Heat 2 2 RANK TEAM NAT LANEREACTION TIME -
Halová Ročenka
ČESKÝ ATLETICKÝ SVAZ HALOVÁ ROČENKA 2008 Praha duben 2008 OBSAH HALOVÉ RO ČENKY 2008 Mezinárodní sout ěže 2008 .................................................................................................. strana 5 Mezistátní utkání 2008 ........................................................................................................ strana 7 Halová mistrovství České republiky 2008 ......................................................................... strana 8 Halová rekordní listina České republiky ............................................................................ strana 17 Halové dlouhodobé tabulky České republiky ................................................................... strana 21 Mužské složky ...................................................................................................................... strana 24 Ženské složky ...................................................................................................................... strana 43 Dopl ňky a opravy publikace „Halová ro čenka 2007“ ....................................................... strana 59 Sestavil: Milan Urban ve spolupráci s dalšími statistiky SAS. HALOVÁ RO ČENKA ČR 2008 (Česká atletická ro čenka) Vydal: Český atletický svaz (Diska řská 100, 169 00 Praha 6 -Strahov) a Česká atletika, s.r.o. (5. kv ětna 9/1323, 140 00 Praha 4) ve spolupráci se Sdružením atletických statistik ů. K tisku p řipravil: Milan Urban Náklad 400 výtisk ů Jazyková a redak ční úprava textu nebyla tiskárnou provedena. Halová ro čenka 2008 -
ETN2010 13(Wicm)
Volume 9, No. 13 March 17, 2010 WORLD INDOOR CHAMPIONSHIPS XII—MEN Tamgho Shocks With TJ Record by Roy Conrad ers in the 60 (Dwain Chambers 6.48), 60 added by Bernard Lagat in the 3000 (7:37.97) Doha, Qatar, March 12–14—In the hurdles (Dayron Robles 7.34), 4x4 (United and Terrence Trammell in 60H (7.36). fairytale world that is modern Doha, it was States 3:03.40) and vault (Steve Hooker Lagat played a typical sit-and-kick game, only fitting that the 13th World Indoor 19-8½/6.01), with U.S.-pacing marks being explaining, “I like to be towed. It’s a champi- Championships should have a fairytale AGENCY GLADYS CHAI/ASVOM ending. The transformation of a small nation Tamgho is closing in on on the Arabian Peninsula from desert backwater to a modern architectural the indoor 59-foot barrier model mirrored the transformation of young Teddy Tamgho from burgeoning triple jump star to the best the event has ever seen indoors. The 20-year-old Frenchman worked his magic when for most the meet was already over and the stands were prob- ably less than half full. Jumping in Doha’s cool Aspire Dome, Tamgho was hot from the get- go, producing a world-leading 57-1½ (17.41) in the first round. That only lasted until the next jump- er, however, as Cuba’s Yoandri Betanzos blew him out of the water with a PR 58-½ (17.69) that moved him to No. 9 on the all-time world list. -
1St Round ROUND RESULTS
IAAF World Indoor Championships Doha From Friday 12 March to Sunday 14 March 2010 4x400 Metres Relay Men ATHLETIC ATHLETIC ATHLETIC ATHLETIC ATHLETIC ATHLETIC ATHLETIC ATHLETIC ATHLETIC ATHLETIC ATHLETIC ATHLETIC ATHLETIC ATHLETIC ATHLETIC ATHLETIC ATHLETIC ATHLETIC ATHLETIC ATHLETIC ATHLETIC ATHLETIC ATHLETIC ATHL 1st Round ROUND RESULTS ATHLETIC ATHLETIC ATHLETIC ATHLETIC ATHLETIC ATHLETIC ATHLETIC ATHLETIC ATHLETIC ATHLETIC ATHLETIC ATHLETIC ATHLETIC ATHLETIC ATHLETIC ATHLETIC ATHLETIC ATHLETIC ATHLETIC ATHLETIC ATHLETIC ATHLETIC ATHLETIC ATHLETIC First 2 of each heat (Q) plus 2 fastest times (q) qualified 13 March 2010 TIME Start 10:00 Heat 1 222 RANK TEAM NAT LANEREACTION TIME RESULT 1 UNITED STATES USA 6 0.194 3:05.78 Q SB 353 Greg NIXON 367 LeJerald BETTERS 368 Tavaris TATE 366 Kerron CLEMENT 2 JAMAICA JAM 5 0.251 3:06.03 Q SB 212 Edino STEELE 210 Sanjay AYRE 211 Lancford DAVIS 208 Ricardo CHAMBERS 3 DOMINICAN REPUBLIC DOM 3 0.147 3:06.30 q NR 99 Arismendy PEGUERO 97 Alvin HARRISON 98 Felix SÁNCHEZ 100 Joel TAPIA 4 GREAT BRITAIN & N.I. GBR 4 0.225 3:09.59 q SB 152 Conrad WILLIAMS 154 Nigel LEVINE 155 Luke LENNON-FORD 153 Christopher CLARKE 5 CZECH REPUBLIC CZE 1 0.228 3:09.76 SB 87 Jirí VOJTÍK 88 Josef PROROK 91 Pavel JIRÁN 92 Theodor JAREŠ 6 IRELAND IRL 2 0.237 3:13.00 SB 198 Nick HOGAN 195 Brian GREGAN 196 Brian MURPHY 197 Billy RYAN INTERMEDIATE TIMES 400m JAMAICA 46.43 800m UNITED STATES 1:33.33 1200m UNITED STATES 2:18.92 1 2 Issued Saturday, 13 March 2010 at 10:24 Timing and Measurement by SEIKO 4x400 Metres Relay Men - 1st -
Juvenes-Pro-Medicina-2018.Pdf
2 ISBN 978-83-947627-1-1 The Students’ Scientific Association is not responsible for the content of abstracts contained in the book. ©Copyright by the Students’ Scientific Association of the Medical University of Lodz General information Conference Dates May 25-26 2018 Conference Venue Clinical and Didactic Centre, Medical University of Lodz Lodz, 251 Pomorska St. 92-213 Łódź Official Language English Conference internet service http://jpm.umed.pl JuvenesProMedicinaInternationaMedicalCongress Contact The Students’ Scientific Association of the Medical University of Lodz www.stn.umed.pl www.jpm.umed.pl [email protected] 3 4 Contents General information ......................................................................................................................................................... 2 Patronage .............................................................................................................................................................................. 7 Sponsors ................................................................................................................................................................................ 9 Scientific Patronage ........................................................................................................................................................ 13 Partnerships ...................................................................................................................................................................... 15 Organizers -
The XXIX Olympic Games Beijing (National Stadium) (NED) - Friday, Aug 15, 2008
The XXIX Olympic Games Beijing (National Stadium) (NED) - Friday, Aug 15, 2008 100 Metres Hurdles - W HEPTATHLON ------------------------------------------------------------------------------------- Heat 1 - revised 15 August 2008 - 9:00 Position Lane Bib Athlete Country Mark . Points React 1 8 Laurien Hoos NED 13.52 (=PB) 1047 0.174 2 7 Haili Liu CHN 13.56 (PB) 1041 0.199 3 2 Karolina Tyminska POL 13.62 (PB) 1033 0.177 4 6 Javur J. Shobha IND 13.62 (PB) 1033 0.210 5 9 Kylie Wheeler AUS 13.68 (SB) 1024 0.180 6 1 Gretchen Quintana CUB 13.77 . 1011 0.171 7 5 Linda Züblin SUI 13.90 . 993 0.191 8 4 G. Pramila Aiyappa IND 13.97 . 983 0.406 9 3 Sushmitha Singha Roy IND 14.11 . 963 0.262 Heat 2 - revised 15 August 2008 - 9:08 Position Lane Bib Athlete Country Mark . Points React 1 2 Nataliya Dobrynska UKR 13.44 (PB) 1059 0.192 2 4 Jolanda Keizer NED 13.90 (SB) 993 0.247 3 9 Wassana Winatho THA 13.93 (SB) 988 0.211 4 7 Aryiró Stratáki GRE 14.05 (SB) 971 0.224 5 3 Julie Hollman GBR 14.43 . 918 0.195 6 5 Kaie Kand EST 14.47 . 913 0.242 7 8 Györgyi Farkas HUN 14.66 . 887 0.236 8 1 Yana Maksimava BLR 14.71 . 880 0.247 . 6 Irina Naumenko KAZ DNF . 0 Heat 3 - revised 15 August 2008 - 9:16 Position Lane Bib Athlete Country Mark . Points React 1 4 Aiga Grabuste LAT 13.78 . -
0 R Round Cor Relay 2L
11th IAAF World Indoor Championships Moscow From Friday 10 March to Sunday 12 March 2006 4x400 Metres Relay MEN Эстафета 4х400 метров МУЖЧИНЫ ATHLETIC ATHLETIC ATHLETIC ATHLETIC ATHLETIC ATHLETIC ATHLETIC ATHLETIC ATHLETIC ATHLETIC ATHLETIC ATHLETIC ATHLETIC ATHLETIC ATHLETIC ATHLETIC ATHLETIC ATHLETIC ATHLETIC ATHLETIC ATHLETIC ATHLETIC ATHLETIC ATHL 1st Round ROUND RESULTS 1-й круг РЕЗУЛЬТАТЫ ATHLETIC ATHLETIC ATHLETIC ATHLETIC ATHLETIC ATHLETIC ATHLETIC ATHLETIC ATHLETIC ATHLETIC ATHLETIC ATHLETIC ATHLETIC ATHLETIC ATHLETIC ATHLETIC ATHLETIC ATHLETIC ATHLETIC ATHLETIC ATHLETIC ATHLETIC ATHLETIC ATHLETI First 2 of each heat (Q) plus 2 fastest times (q) qualified Первые 2 из каждого забега (Q) и 2 с лучшим временем (q) выходят в следующий круг 12 March 2006 TIME ВРЕМЯ Heat 1 Start / Начало 10:41 Забег 1 2 RANK TEAM NAT LANEREACTION TIME RESULT МЕСТО СТРАНА СТРАНА ДОРОЖКАВРЕМЯ РЕАКЦИИ РЕЗУЛЬТАТ 1 RUSSIA RUS 6 0.251 3:08.02 Q SB РОССИЯ 377 Konstantin SVECHKAR 376 Andrey POLUKEYEV 374 Aleksandr DEREVYAGIN 375 Yevgeniy LEBEDEV 2 FRANCE FRA 5 0.171 3:08.06 Q SB ФРАНЦИЯ 144 Brice PANEL 143 Sébastien MAILLARD 145 Teddy VENEL 137 Fadil BELLAABOUSS 3 SPAIN ESP 3 0.178 3:08.07 SB ИСПАНИЯ 111 Santiago EZQUERRO 109 David CANAL 120 Salvador RODRÍGUEZ 122 David TESTA 4 UKRAINE UKR 2 0.149 3:09.46 NR УКРАИНА 447 Myhaylo KNYSH 446 Volodymyr DEMCHENKO 448 Vitaliy DUBONOSOV 444 Oleksiy RACHKOVSKY 5 ROMANIA ROM 1 0.187 3:13.93 NR РУМЫНИЯ 346 Florin SUCIU 349 Vasile BOBOS 347 Alexandru MARDAN 348 Ioan Lucian VIERU JAMAICA JAM 4 0.233 DNF ЯМАЙКА 235 DeWayne -
Komunikat Końcowy
Halowe Mistrzostwa Polski Seniorów 17-18 lutego 2007 KOMUNIKAT KOŃCOWY Obsada sędziowska Sędzia Główny Zawodów Edward Romanowski Z-ca Sędziego Głównego Jan Maszorek Komisja Odwoławcza Janusz Krynicki Janusz Rozum Anna Barbara Szymańska Delegat Techniczny PZLA Jerzy Witwicki Arbiter Biegów Wojciech Gaczkowski Arbiter Skoków Tadeusz Stawicki Arbiter Rzutów Henryk Kowalski Koordynator startu Aleksander Tynelski Starterzy Stanisław Figat Kazimierz Zabniak Sędziowie Główni Biegów Andrzej Haj Andrzej Kowalczyk Andrzej Ojrzyński Sędziowie Główni Rzutów Michał Kulesza Henryk Ryll Sędziowie Główni Skoków Ewa Gołębowska Stanisław Ojrzyński Edward Wiśniewski Sędziowie Główni Chodu Sportowego Michał Krynicki Pomiar Czasu (FinishLynx)-DomTel-Sport Słupsk Sebastian Jędrzejewski Grzegorz Lipiński Ryszard Pilarczyk Spiker Paweł Zięba Bramka Grażyna i Jerzy Fijałkowscy Operator kamery Filip Moterski Trójskok mężczyzn 07-02-17 15:00 godz. zak. 16:06 R. Ż. z rokiem uzyskania, RP-R. Polski, RE-R. Europy, RŚ-R. Świata Strona 1 07-02-18 17:28:08 SPAŁA 2007 Przygotowanie: DomTel-Sport Słupsk, tel. 0602 314171 www.domtel.pl RŚ: 17.83 Aliecer Urrutia CUB Sindelfingen 01/03/97 RE: 17.80 + Christian OLSSON SWE Göteborg 05/03/02 Sędzia: Gołębowska Ewa RP: 17.03 Michał JOACHIMOWSKI BUDOWLANI Bydgoszcz Goteborg 09/03/74 Miejsce T/Lp Numer Imię i nazwisko Rocznik Klub Wynik FINAŁ 1 6 11 Paweł KRUHLIK 83 AZS-AWF Wrocław(DOL) 16.75 PB 2 2 30 Jacek KAZIMIEROWSKI 74 BKS Bydgoszcz(KPO) 16.61 SB 3 1 232 Mateusz PARLICKI 84 AZS-AWF Katowice(SLK) 16.37 4 7 31 Robert MICHNIEWSKI -
Komunikat Końcowy
Sprawdzian kontrolny PZLA Spała, 14 lutego 2009 KOMUNIKAT KOŃCOWY 800 metrów mężczyzn 09-02-14 11:45 RŚ: 1:42.67 Wilson KIPKETER DEN Paris 09/03/97 RE: 1:42.67 Wilson KIPKETER DEN Paris 09/03/97 Sędzia: Moterski Filip RP: 1:44.78 Paweł CZAPIEWSKI LUBUSZ Słubice Wiedeń 03/03/02 Miejsce T/Lp Numer Imię i nazwisko Rocznik Klub Wynik Bieg 1/2 1 3 842 Aleksandr OSMOLOWICZ 85 UKRAINE 1:47.64 2 5 870 Sebastian PAPUGA 85 AZS-AWF Gorzów(LBU) 1:48.25 PB 3 4 75 Aleksandr BORYSJUK 85 UKRAINE 1:48.54 4 6 666 Piotr DĄBROWSKI 85 WLKS Wrocław(DOL) 1:48.79 PB 5 2 18 Mateusz DEMCZYSZAK 86 WKS Śląsk Wrocław(DOL) 1:52.20 1 46 Michał PODOLAK 85 AZS-UWM Olsztyn(WMZ) DNF 7 774 Łukasz JÓŹWIAK 83 AZS-AWF Wrocław(DOL) DNF Międzyczasy 400m 46 Michał PODOLAK 52.77 Wyniki konkurencji Miejsce B-G/Miejsce Imię i nazwisko Rocznik Klub Wynik 1 Bieg 1 1 Aleksandr OSMOLOWICZ 85 UKRAINE 1:47.64 2 Bieg 1 2 Sebastian PAPUGA 85 AZS-AWF Gorzów 1:48.25 PB 3 Bieg 1 3 Aleksandr BORYSJUK 85 UKRAINE 1:48.54 4 Bieg 1 4 Piotr DĄBROWSKI 85 WLKS Wrocław 1:48.79 PB 5 Bieg 1 5 Mateusz DEMCZYSZAK 86 WKS Śląsk Wrocław 1:52.20 6 Bieg 2 1 Przemysław MESYASZ 90 CKS Budowlani Częstochowa 1:53.57 PB 7 Bieg 2 2 Jacek WICHOWSKI 87 AZS-AWF Warszawa 1:54.85 SB 8 Bieg 2 3 Łukasz KUBIAK 88 RKS Łódź 1:55.42 PB 9 Bieg 2 4 Sebastian WÓJTOWICZ 82 MKS Polonia Warszawa 1:57.19 10 Bieg 2 5 Michał ZWIERZCHOWSKI 87 MKS Polonia Warszawa 2:02.23 11 Bieg 2 6 Paweł WNUCZEK 88 MKS Polonia Warszawa 2:03.05 PB Bieg 1 DNF Michał PODOLAK 85 AZS-UWM Olsztyn DNF Bieg 2 DNS RaFał GREF 89 WKS Śląsk Wrocław DNS Bieg 1 DNF Łukasz JÓŹWIAK 83 AZS-AWF Wrocław DNF Strona 1 Print: 09-02-14 15:30:25 DNS-nie wyst., DNF-nie ukoń., DQ-dyskw.,NM-bez wyn.,PB-r.życ.,SB-r.sez., Q,q-awans SPAŁA 2009 Przygotowanie: DomTel-Sport Słupsk, tel.