Gentle Survey on MIR Industrial Service Robots: Review & Design
Total Page:16
File Type:pdf, Size:1020Kb
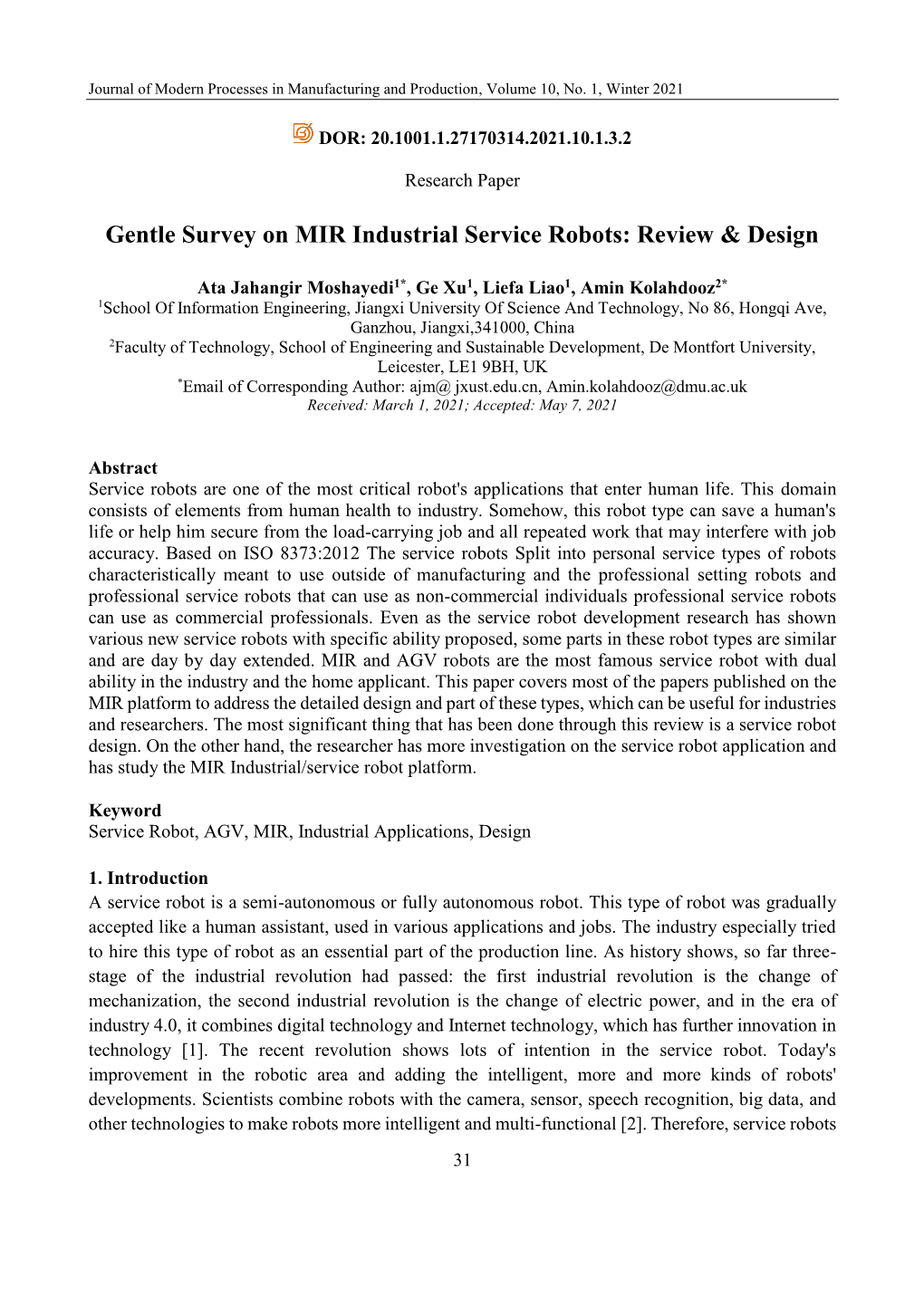
Load more
Recommended publications
-
Top Robotics Companies Continue to Innovate, Grow Market TABLE of CONTENTS SPONSORED BY
2O19 ROBOTICS BUSINESS REVIEW RBR C5OMP0ANY Top Robotics Companies Continue to Innovate, Grow Market TABLE OF CONTENTS SPONSORED BY A GROWING MARKET WHAT’S DIFFERENT THIS YEAR EXPANDING OUR “COMPANIES WE’RE WATCHING” LIST GOING SLIGHTLY BEYOND 50 “COMPANIES” ONE MORE THING … THE 2019 RBR50 WINNERS COMPONENTS COBOTS AUTONOMOUS MOBILE ROBOTS PIECE-PICKING & AI AUTONOMOUS VEHICLES AERIAL ROBOTS (AKA DRONES) AUTONOMY SOFTWARE INDUSTRIAL AUTOMATION, ROBOTICS HEALTHCARE OR SERVICE ROBOTS INFRASTRUCTURE SUPPORT FOR ROBOTICS NOTABLE TRANSACTIONS AMONG THE RBR 50 COMPANIES WE’RE WATCHING roboticsbusinessreview.com 2 2019 RBR50: TOP ROBOTICS COMPANIES CONTINUE TO INNOVATE, GROW MARKET Success comes in many flavors for robotics companies around the world. By Keith Shaw, Robotics Business Review, and John Santagate, IDC Starting and growing any business is difficult, but when you’re in an emerging market such as robotics, 2O19 ROBOTICS BUSINESS REVIEW automation, or artificial intelligence, the highs are higher and the lows can be lower. The meteoric rise of new companies and competition, along with RBR record investments and high demand from potential customers, can lead to distraction for even the most stalwart entrepreneur. Throw in an intense spotlight from a media looking 50 to make headlines around the negatives of robotics, COMPANY and you have a recipe for potential disaster at every turn. Yet the top companies in the robotics field continue to stay focused on their mission – building robots, software and services that enable companies to optimize their processes, improve efficiencies, become more profitable, or solve human worker labor shortages. For the past eight years, the RBR50 has provided the robotics industry with its own spotlight on the leaders in the robotics, AI, and autonomy industry. -
Taking ‘Every Reasonable REPORT on ICS: What Bringing Production Precaution’ During a Insights from Our Recent Roundtable on Industrial Back Home Means for Pandemic
MACHINE SAFETY: RESHORING: On taking ‘every reasonable REPORT ON ICS: What bringing production precaution’ during a Insights from our recent roundtable on industrial back home means for pandemic. p. 11 control systems. p. 14 automation. p. 22 Your resource for Canada’s industrial automation news AutomationMag.com TAKING CONTROL Building a new business during a pandemic isn’t easy, but the team at Black Controls Company is already seeing success. p. 18 Highly-rated, feature packed PLCs available at your fi ngertips, 24/7/365 Unlike other suppliers, at AutomationDirect we welcome any feedback we get on our products, especially our PLCs. We display all product reviews we receive “...We have used a variety of the CLICK on our Webstore to help others make informed buying decisions. So, if your models in many di erent types of builds supplier can’t answer the question, “What is the customer satisfaction score for from the very simple to pretty complicated. this product?”, then maybe you need a new supplier! There is a PLC and add-on’s to t just Our CLICK PLCs are an industry favorite providing simple control at an extremely about any application. We just nished a aff ordable price. Here are just a few highlights: 15 unit build for production, saved a ton • Multiple stand-alone PLC units available with different I/O confi gurations of cash. I’ve yet been disappointed with (relay, analog, AC or DC discrete I/O) the CLICK series or AutomationDirect.” • Support for Modbus RTU, ASCII, Modbus TCP and EtherNet/IP communication protocols Tim in OXFORD, AL • All CLICK PLC units use our FREE programming software with a simple but practical instruction set • Easily expand your CLICK PLC with snap-on I/O modules for up to an additional 128 discrete or 48 analog I/O points www.CLICKPLCs.com Orders over $49 get FAST FREE SHIPPING Our shipping policies make it easier than ever to order direct from the U.S.! Fast free standard shipping* is available for most orders over $49 U.S., and that includes the brokerage fees (when using an AutomationDirect nominated broker). -
Read Our Robot Teardown Paper
index. 1 Introduction pg. 6 2 Robot teardown pg. 8 pg. 9 2.1 Case Study 1: Teardown of an industrial collaborative robot 2.2 Case Study 2: Teardown of a next-gen industrial pg. 10 collaborative robot 2.3 Case Study 3: Teardown of a mobile industrial pg. 12 robot 3 Teardown-enabled security research pg. 14 4 Finding and bypassing planned obsolescence pg. 16 in robotics 4.1 controllerAdapter: UR3 controller with UR3e pg. 16 mechanics, and the other way around 4.2 armAdapter - Drive UR3 without controller pg. 17 5 Conclusions pg. 18 6 References pg. 20 Start reading Publisher Alias Robotics Authors Víctor Mayoral-Vilches1,3 Alfonso Glera-Picón1 Unai Ayucar Carbajo1 Stefan Rass3 Martin Pingzger3 Federico Maggi2 Endika Gil-Uriarte1 ABSTRACT Building a robot requires careful selection of components that interact across networks while meeting timing deadlines. Given the complexity associated, as robots get damaged or security compromised, their components will increasingly require updates and replacements. Contrary to the expectations and similar to Ford in the 1920s with cars, most robot manufacturers oppose to this. They employ planned obsolescence practices organizing dealers and system integrators into ”private networks”, providing repair parts only to ”certified” companies to discourage repairs and evade competition. In this article we introduce and advocate for robot teardown as an approach to study robot hardware architectures and fuel security research. We show how teardown can help understanding the underlying hardware and demonstrate how our approach can help researchers uncovering security vulnerabilities. Our case studies show how robot teardown becomes an essential practice to security in robotics, helping us identify and report a total of 100 security flaws with 17 new CVE IDs over a period of two years. -
Design and Development of a ROS Based Lidar Platform to Scan Environment for a Mobile Ro- Bot's Autonomous Motion
Saimaa University of Applied Sciences Faculty of Technology, Lappeenranta Mechanical Engineering and Production Technology Ilia Dobriakov Design and Development of a ROS Based LiDAR Platform to Scan Environment for a Mobile Ro- bot's Autonomous Motion Thesis 2019 Abstract Ilia Dobriakov Design and Development of a ROS Based LiDAR Platform to Scan Environ- ment for a Mobile Robot's Autonomous Motion, 75 pages, 8 appendices Saimaa University of Applied Sciences Faculty of Technology, Lappeenranta Mechanical Engineering and Production Technology Thesis 2019 Instructor: Senior Lecturer Mr. Timo Eloranta, Saimaa University of Applied Sciences. The objective of the research was to design and develop a LiDAR platform to scan the environment for a TIERA mobile robot's autonomous motion. The de- velopment of the system was done in Robot Operational System. The project was a part of a bigger project aimed to implement the autonomous charging system on the robot. The work was commissioned by the head of Laboratory of Intelligent Machines in the Lappeenranta University of Technology, Hamid Roozbahani. The information for the research was gathered from literature sources of Lap- peenranta Academic Library, the Internet and from Master’s thesis reports of pre- vious researchers, who were working on TIERA project. This research was car- ried out in a Laboratory of Intelligent Machines in the Lappeenranta University of Technology. As a result of this thesis, the robot was completely set up for autonomous navi- gation utilizing ROS and LiDAR sensor. The 2D map for navigation inside the experimental field was built. In addition, the best concept design for a future charging station was selected. -
Point-To-Point Mobile Robots Hot Sellers
Point-to-point mobile robots hot sellers By Frank Tobe | January 14, 2018 Today’s e-commerce spurs demand for reduced response times in fulfillment centers; generally has fewer products per order; and is constantly changing — increasing system complexity and the need for flexibility in automation. Today’s warehouses and distribution centers are far more complex than they were 10 years ago and employee turnover remains high; with complexity comes higher wages yet labor is increasingly hard to find — all adding to the equation. Businesses are making investments in a variety of technologies to improve their inventory control, order processing methods, labor situation and to enhance their pick and pack operations to be faster, less rigid, requiring less physical exertion, and achieve more accurate results. “These factors are contributing to the need to convert warehouses and distribution centers into assets for competitive differentiation. Mobility will be front and center in this shift, says VDC Research in their recent ‘Taking Advantage of Apps and App Modernization in Warehousing‘ report. [NOTE: Mobile robotic platforms can be “autonomous” (AMRs) also called self-driving or vision guided vehicles (SDVs or VGVs), which means they can navigate an uncontrolled environment without the need for physical or electromechanical guidance. Alternatively, mobile robots like automated guided vehicles (AGVs) rely on guidance devices that allow them to travel a pre- defined navigation route in relatively controlled spaces.] Point-to-point mobile robots Businesses of all types — from auto manufacturers to hospitals, from job shops to hotels — want to use point-to-point mobile devices instead of human messengering or towing for a variety of cost-saving reasons but mainly because it’s now achievable, cost-effective, and proven — plus there’s a real need to replace older people-dependent mobility tasks with more automated methods. -
COLLABORATIVE ROBOTICS Toll Free 800.236.0607 Portland | Seattle | Fremont | San Diego | Dallas
COLLABORATIVE ROBOTICS Toll Free 800.236.0607 Portland | Seattle | Fremont | San Diego | Dallas UR3e is our new, smaller collaborative table-top robot e for light assembly tasks and automated workbench scenarios. Weighs only 24.3 lbs (11 kg), but has a pay- load of 6.6 lbs (3 kg), 360-degree rotation on all wrist joints and infinite rotation on the end joint. Today’s most flexible, lightweight, collaborative table-top robot to work side-by-side with employees. An ideal UR3 choice for applications that require 6-axis capabilities where size, safety and costs are critical. The UR5e is a lightweight, flexible and collaborative e industrial robot from Universal Robots that lets you automate repetitive and dangerous tasks with pay- loads of up to 5 kg. Ideal for optimizing low-weight collaborative processes, such as picking, placing and testing. With a working radius of up to 850 mm, the UR5e collaborative robot puts everything within UR5 reach, freeing up your employees’ time to add value to other stages of the production. The UR10e is our largest industrial robot arm, de- e signed for bigger tasks where precision and reliabili- ty are still of paramount importance, such as packag- ing, palletizing, assembly and pick and place. With the UR10e you can automate processes and tasks that weigh up to 10 kg. With a reach radius of up to 1300 mm, the UR10e is designed to be more effective at tasks across a larger area. You can therefore save time on production lines where distance can be a factor. UR10 The UR16e is our strongest industrial robot arm, built e for heavy duty tasks like machine tending, material handling, packaging, material removal, and screw and nut driving applications. -
Design and Development of a Graphical User Interface for the Monitoring Process of an Automated Guided Vehicle Fleet
DEGREE PROJECT IN COMPUTER SCIENCE AND ENGINEERING, SECOND CYCLE, 30 CREDITS STOCKHOLM, SWEDEN 2020 Design and development of a graphical user interface for the monitoring process of an automated guided vehicle fleet JOHANNA PAUL KTH ROYAL INSTITUTE OF TECHNOLOGY SCHOOL OF ELECTRICAL ENGINEERING AND COMPUTER SCIENCE ABSTRACT Many different autonomously driving mobile robots are used for industrial transports of materials or goods in the context of internal logistic processes because of different use cases. The problem for the users that need to monitor the robots is that each manufacturer provides its own graphical user interface (GUI) with different operating modes and visual designs, which requires different trainings and constant switching between software. Therefore, this paper shows the design and development process of a graphical user interface in the form of a web application for the monitoring process of a fleet of automated guided vehicles from different manufacturers and answers the following question: "What are the main criteria when designing a graphical user interface with high usability for the monitoring process of manufacturer-independent automated guided vehicle fleets?” To answer the question, existing graphical user interfaces from different manufacturers were analyzed and interviews with developers and end-users of the GUIs were conducted. Requirements were then derived, on whose basis sketching, wireframing and high-fidelity prototyping have been performed. Usability testing and a heuristic evaluation were chosen to improve the application and its usability continually. As a result, the following six main criteria could be derived that summarize the most essential points to consider when designing such a GUI: administrability, adaptiveness, observability, analyzability, robot and job awareness, and intervention. -
Sectorwatch: Industrial Robotics May 2018 Industrial Robotics May 2018 Sector Dashboard [4]
Sectorwatch: Industrial Robotics May 2018 Industrial Robotics May 2018 Sector Dashboard [4] Public Basket Performance [5] Operational Metrics [7] Valuation Comparison [10] Recent Deals [13] Appendix [14] 7 Mile Advisors appreciates the opportunity to present this confidential information to the Company. This document is meant to be delivered only in conjunction with a verbal presentation, and is not authorized for distribution. Please see the Confidentiality Notice & Disclaimer at the end of the document. All data cited in this document was believed to be accurate at the time of authorship and came from publicly available sources. Neither 7 Mile Advisors nor 7M Securities make warranties or representations as to the accuracy or completeness of third-party data contained herein. This document should be treated as confidential and for the use of the intended recipient only. Please notify 7 Mile Advisors if it was distributed in error. 2 Overview 7MA provides Investment Banking & Advisory Services to the Business Services and Technology Industries globally. We advise on M&A and private capital transactions, and provide market assessments and benchmarking. As a close knit team with a long history together and a laser focus on our target markets, we help our clients sell their companies, raise capital, grow through acquisitions, and evaluate new markets. We publish our sectorwatch, a review of M&A and operational trends in the industries we focus. Dashboard Valuation Comparison • Summary metrics on the sector • Graphical, detailed comparison of valuation • Commentary on market momentum by multiples for the public basket comparing the most recent 12-month performance against the last 3-year averages. -
Integration of Robotics Proliferates in Beverage Operations Advancing Robotic Technology Offers New Solutions
Integration of robotics proliferates in beverage operations Advancing robotic technology offers new solutions Software innovations have made robotic solutions easier to use and offer high performance, Matt Wicks says. (Image courtesy of Intelligrated) With a growing number of products in the marketplace and October 24, 2017 an evolving retail landscape, beverage warehouses are Amanda Del Buono faced with a lot of work and a minimal amount of time and manpower to do it. As robotic technology becomes more accessible, it’s helping many manufacturers achieve their operations goals. “Robotics in the beverage industry made initial inroads in the palletizing space and continue to be a viable technology for many of these types of applications,” says Matt Wicks, vice president of product development and manufacturing systems at Intelligrated, Mason, Ohio. “We’re seeing that robotic technology has migrated to and merged with more ‘conventional’ palletizing machines to yield improved performance in case handling and machine rates.” He notes that robotic automation also can help companies dealing with the impacts of eCommerce and labor challenges. “Labor continues to be a challenge for manufacturers. Maintaining a consistent and reliable workforce is challenging as the demands of eCommerce and order fulfillment systems drain the resource pool. Leveraging automation and robotics can help to offset these challenges,” he says. Ed Mullen, vice president of sales in North America at Demark-based Mobile Industrial Robots (MiR) also notes the proliferation of robotics in the beverage industry, and notes changing regulations as among the factors influencing implementation. "As in other industry, the beverage industry is increasingly using automation and robots due, in part, to increasing food safety regulations combined with an increasing focus on maintaining competitive advantage," he says. -
OMNIVIL—An Autonomous Mobile Manipulator for Flexible Production
sensors Article OMNIVIL—An Autonomous Mobile Manipulator for Flexible Production Heiko Engemann 1,2,*, Shengzhi Du 2,* , Stephan Kallweit 1, Patrick Cönen 1 and Harshal Dawar 1 1 IaAM Institute, Faculty of Mechanical Engineering and Mechatronics, University of Applied Sciences Aachen, 52074 Aachen, Germany; [email protected] (S.K.); [email protected] (P.C.); [email protected] (H.D.) 2 Faculty of Engineering and Built Environment, Tshwane University of Technology, Pretoria 0001, South Africa * Correspondence: [email protected] (H.E.); [email protected] (S.D.) Received: 10 November 2020; Accepted: 15 December 2020; Published: 17 December 2020 Abstract: Flexible production is a key element in modern industrial manufacturing. Autonomous mobile manipulators can be used to execute various tasks: from logistics, to pick and place, or handling. Therefore, autonomous robotic systems can even increase the flexibility of existing production environments. However, the application of robotic systems is challenging due to their complexity and safety concerns. This paper addresses the design and implementation of the autonomous mobile manipulator OMNIVIL. A holonomic kinematic design provides high maneuverability and the implemented sensor setup with the underlying localization strategies are robust against typical static and dynamic uncertainties in industrial environments. For a safe and efficient human–robot collaboration (HRC), a novel workspace monitoring system (WMS) is developed to detect human co-workers and other objects in the workspace. The multilayer sensor setup and the parallel data analyzing capability provide superior accuracy and reliability. An intuitive zone-based navigation concept is implemented, based on the workspace monitoring system. Preventive behaviors are predefined for a conflict-free interaction with human co-workers. -
Application of Novel Industrial Scale Robot Automation in Elderly Care
NOL CH OG E Y T • • R E E C S N E E Application of novel industrial scale robot A I 301 R VTT TECHNOLOGY C C automation in elderly care S H • S H N 3 0 1 I G O I H S L I Elderly patients in institutional care are fragile. How can robots I V G • H S even be considered to help nurses in varying care tasks where T friendliness and the human touch are often required? It is wise to let robots perform tasks which they are good at, and particularly to take care of repetitive tasks. Embedded automation supporting robots often provides better results than the use of a robot only. For example, robots open doors poorly, but automated doors are standard equipment for hospitals and dormitories and are applicable for homes. Logistics are suitable for industrial vehicles in buildings and for autonomous vehicles outdoors. Measuring the health and condition of any person would assist preventive healthcare, which is well known to reduce the overall costs of healthcare. A p plic atio n of n ovel in d ustrial sc ale... Application of novel industrial scale robot automation in elderly ISBN 978-951-38-8553-3 (URL: http://www.vttresearch.com/impact/publications) care ISSN-L 2242-1211 ISSN 2242-122X (Online) http://urn.fi/URN:ISBN:978-951-38-8553-3 Hannu Lehtinen VTT TECHNOLOGY 301 Application of novel industrial scale robot automation in elderly care Hannu Lehtinen ISBN 978-951-38-8553-3 (URL: http://www.vttresearch.com/impact/publications) VTT Technology 301 ISSN-L 2242-1211 ISSN 2242-122X (Online) http://urn.fi/URN:ISBN:978-951-38-8553-3 Copyright © VTT 2017 JULKAISIJA – UTGIVARE – PUBLISHER Teknologian tutkimuskeskus VTT Oy PL 1000 (Tekniikantie 4 A, Espoo) 02044 VTT Puh. -
United States Securities and Exchange Commission Washington, D.C
UNITED STATES SECURITIES AND EXCHANGE COMMISSION WASHINGTON, D.C. 20549 FORM 10-K ANNUAL REPORT PURSUANT TO SECTIONS 13 OR 15(d) OF THE SECURITIES EXCHANGE ACT OF 1934 (MARK ONE) È ANNUAL REPORT PURSUANT TO SECTION 13 OR 15(d) OF THE SECURITIES EXCHANGE ACT OF 1934 For the fiscal year ended December 31, 2018 OR ‘ TRANSITION REPORT PURSUANT TO SECTION 13 OR 15(d) OF THE SECURITIES EXCHANGE ACT OF 1934 Commission file number 001-06462 TERADYNE, INC. (Exact Name of Registrant as Specified in Its Charter) MASSACHUSETTS 04-2272148 (State or Other Jurisdiction of (I.R.S. Employer Incorporation or Organization) Identification Number) 600 RIVERPARK DRIVE NORTH READING, MASSACHUSETTS 01864 (Address of Principal Executive Offices) (Zip Code) Registrant’s telephone number, including area code: (978) 370-2700 Securities registered pursuant to Section 12(b) of the Act: Title of Each Class Name of Each Exchange on Which Registered Common Stock, par value $0.125 per share Nasdaq Stock Market LLC Indicate by check mark if the registrant is a well-known seasoned issuer, as defined in Rule 405 of the Securities Act. Yes È No ‘ Indicate by check mark if the registrant is not required to file reports pursuant to Section 13 or Section 15(d) of the Exchange Act. Yes ‘ No È Indicate by check mark whether the registrant (1) has filed all reports required to be filed by Section 13 or 15(d) of the Securities Exchange Act of 1934 during the preceding 12 months (or for such shorter period that the registrant was required to file such reports), and (2) has been subject to such filing requirements for the past 90 days.