Advancement in Wind Turbine Blade Technology
Total Page:16
File Type:pdf, Size:1020Kb
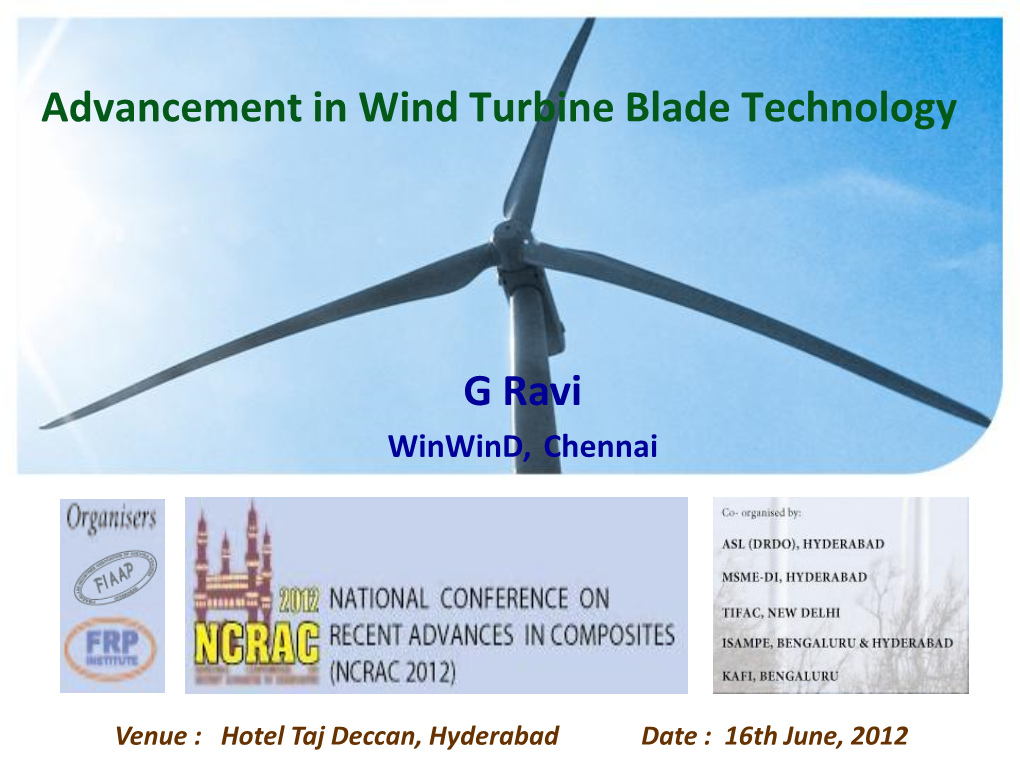
Load more
Recommended publications
-
Impact of Windfarm OWEZ on the Local Macrobenthos Communiy
Impact of windfarm OWEZ on the local macrobenthos community report OWEZ_R_261_T1_20090305 R. Daan, M. Mulder, M.J.N. Bergman Koninklijk Nederlands Instituut voor Zeeonderzoek (NIOZ) This project is carried out on behalf of NoordzeeWind, through a sub contract with Wageningen-Imares Contents Summary and conclusions 3 Introduction 5 Methods 6 Results boxcore 11 Results Triple-D dredge 13 Discussion 16 References 19 Tables 21 Figures 33 Appendix 1 44 Appendix 2 69 Appendix 3 72 Photo’s by Hendricus Kooi 2 Summary and conclusions In this report the results are presented of a study on possible short‐term effects of the construction of Offshore Windfarm Egmond aan Zee (OWEZ) on the composition of the local benthic fauna living in or on top of the sediment. The study is based on a benthic survey carried out in spring 2007, a few months after completion of the wind farm. During this survey the benthic fauna was sampled within the wind farm itself and in 6 reference areas lying north and south of it. Sampling took place mainly with a boxcorer, but there was also a limited programme with a Triple‐D dredge. The occurrence of possible effects was analyzed by comparing characteristics of the macrobenthos within the wind farm with those in the reference areas. A quantitative comparison of these characteristics with those observed during a baseline survey carried out 4 years before was hampered by a difference in sampling design and methodological differences. The conclusions of this study can be summarized as follows: 1. Based on the Bray‐Curtis index for percentage similarity there appeared to be great to very great similarity in the fauna composition of OWEZ and the majority of the reference areas. -
New & Renewable Energy
Seoul - December 6, 2010 Wind Energy in the Netherlands . History . Overview . Offshore . Examples . Conclusions 2 History of wind energy in the Netherlands A windmill is a machine which converts the energy of the wind into rotational motion by means of adjustable vanes called sails Autonomous development in Europe that started in the 11th century Development in the Netherlands leading to a large variety of mills First wind mills for drainage in 1414 Windmills for energy to saw mills, to mills used for crushing seeds, grains, etc. Cheap energy was a major contributing factor to the Golden Age (17th century) of the Netherlands Invention of steam engine (1775) signaled the end of wind mills 1,000 wind mills left out of a total of more than 10,000 3 Kinderdijk 4 Recent history of wind energy in the Netherlands A windmill is a machine which converts the energy of the wind into rotational motion by means of adjustable blades made of synthetic material Renewed interest in wind energy resulted from the oil crisis in 1973 Dutch government support from 1976 Present capacity 2,229MW Government objective to have 6GW installed by 2020 5 Overview wind energy sector in the Netherlands (1) Turbine manufacturers & developers: . Lagerwey in difficulties, restarted as Zephyros, acquired by Hara Kosan, now acquired by STX . Nedwind acquired by NEG-Micon, which in turn acquired by Vestas . Windmaster discontinued . Darwind acquired by XEMC (China) . EWT originally using Lagerwey technology, now developing its own technology . 2B Energy proto type for +6MW offshore turbine 6 Overview wind energy sector in the Netherlands (2) Marine engineering Construction & dredging Electrical design & consulting Building of specialized vessels 7 Overview wind energy sector in the Netherlands (3) Blade manufacturing & testing . -
The German Wind Energy Lobby: How to Successfully Promote Costly Technological Change
A Service of Leibniz-Informationszentrum econstor Wirtschaft Leibniz Information Centre Make Your Publications Visible. zbw for Economics Michaelowa, Axel Working Paper The German Wind Energy Lobby: How to successfully promote costly technological change HWWA Discussion Paper, No. 296 Provided in Cooperation with: Hamburgisches Welt-Wirtschafts-Archiv (HWWA) Suggested Citation: Michaelowa, Axel (2004) : The German Wind Energy Lobby: How to successfully promote costly technological change, HWWA Discussion Paper, No. 296, Hamburg Institute of International Economics (HWWA), Hamburg This Version is available at: http://hdl.handle.net/10419/19268 Standard-Nutzungsbedingungen: Terms of use: Die Dokumente auf EconStor dürfen zu eigenen wissenschaftlichen Documents in EconStor may be saved and copied for your Zwecken und zum Privatgebrauch gespeichert und kopiert werden. personal and scholarly purposes. Sie dürfen die Dokumente nicht für öffentliche oder kommerzielle You are not to copy documents for public or commercial Zwecke vervielfältigen, öffentlich ausstellen, öffentlich zugänglich purposes, to exhibit the documents publicly, to make them machen, vertreiben oder anderweitig nutzen. publicly available on the internet, or to distribute or otherwise use the documents in public. Sofern die Verfasser die Dokumente unter Open-Content-Lizenzen (insbesondere CC-Lizenzen) zur Verfügung gestellt haben sollten, If the documents have been made available under an Open gelten abweichend von diesen Nutzungsbedingungen die in der dort Content Licence -
Stochastic Dynamic Response Analysis of a 10 MW Tension Leg Platform Floating Horizontal Axis Wind Turbine
energies Article Stochastic Dynamic Response Analysis of a 10 MW Tension Leg Platform Floating Horizontal Axis Wind Turbine Tao Luo 1,*, De Tian 1, Ruoyu Wang 1 and Caicai Liao 2 1 State Key Laboratory for Alternate Electrical Power System with Renewable Energy Sources, North China Electric Power University, Beijing 102206, China; [email protected] (D.T.); [email protected] (R.W.) 2 CAS Key Laboratory of Wind Energy Utilization, Institute of Engineering Thermophysics, Chinese Academy of Sciences, Beijing 100190, China; [email protected] * Correspondence: [email protected]; Tel.: +10-6177-2682 Received: 2 October 2018; Accepted: 23 November 2018; Published: 30 November 2018 Abstract: The dynamic response of floating horizontal axis wind turbines (FHWATs) are affected by the viscous and inertia effects. In free decay motion, viscous drag reduces the amplitude of pitch and roll fluctuation, the quasi-static mooring system overestimates the resonant amplitude values of pitch and roll. In this paper, the quasi-static mooring system is modified by introducing linear damping and quadratic damping. The dynamic response characteristics of the FHAWT modified model of the DTU 10 MW tension leg platform (TLP) were studied. Dynamic response of the blade was mainly caused by wind load, while the wave increased the blade short-term damage equivalent load. The tower base bending moment was affected by inclination of the tower and the misaligned angle bwave between wind and wave. Except the yaw motion, other degrees of freedom motions of the TLP were substantially affected by bwave. Ultimate tension of the mooring system was related to the displacement caused by pitch and roll motions, and standard deviation of the tension was significantly affected by the wave frequency response. -
Wind Turbine Foundations
IFC - ESMAP - RENEWABLE ENERGY TRAINING PROGRAM Wind Module I. Technology Overview, Market Analysis and Economics Washington DC, June 16th 2014 1 Index Wind Technology Overview, Market Analysis and Economics • Introduction and Technology Overview • Market Analysis and Perspectives • Support Schemes and Price Forecasting • Grid Integration and System Flexibility • Challenges and Competitiveness 22 Wind Power Generation Wind power generation: Conversion of wind energy into electricity using wind turbines Max Power output for a wind speed: 1 W····(,) UOE A3 v C m 2 p ͻ U= 1,225 kg/m3 ї density of the air ͻ A= swept Area ͻ V= wind Speed ͻ Cp= Power Coefficient 33 Wind - Power Coefficient Power Coefficient: Efficiency of a wind turbine transforming wind power into electricity Betz Limit: Maximum Power Coefficient of an ideal wind turbine For commercial turbines, Cp is typically between 40-50% 44 Wind - Weibull Distribution Wind speeds can be modeled using the Weibull Distribution. This function represents how often winds of different speeds will be observed at a location with a certain average wind speed. The shape of the Weibull Distribution depends on a parameter called Shape. In Northern Europe and most other locations around the world the value of Shape is approximately 2, then the distribution is named Rayleigh Distribution. 55 Wind - Capacity factor Weibull Distribution of Wind Speeds for a site with an average wind speed of 7m/s. It demonstrates visually how low and moderate winds are very common, and that strong gales are relatively rare. It is used to work out the number of hours that a certain wind speeds are likely to be recorded and the likely total energy output of a WT a year. -
Offshore Technology Yearbook
Offshore Technology Yearbook 2 O19 Generation V: power for generations Since we released our fi rst offshore direct drive turbines, we have been driven to offer our customers the best possible offshore solutions while maintaining low risk. Our SG 10.0-193 DD offshore wind turbine does this by integrating the combined knowledge of almost 30 years of industry experience. With 94 m long blades and a 10 MW capacity, it generates ~30 % more energy per year compared to its predecessor. So that together, we can provide power for generations. www.siemensgamesa.com 2 O19 20 June 2019 03 elcome to reNEWS Offshore Technology are also becoming more capable and the scope of Yearbook 2019, the fourth edition of contracts more advanced as the industry seeks to Wour comprehensive reference for the drive down costs ever further. hardware and assets required to deliver an As the growth of the offshore wind industry offshore wind farm. continues apace, so does OTY. Building on previous The offshore wind industry is undergoing growth OTYs, this 100-page edition includes a section on in every aspect of the sector and that is reflected in crew transfer vessel operators, which play a vital this latest edition of OTY. Turbines and foundations role in servicing the industry. are getting physically larger and so are the vessels As these pages document, CTVs and their used to install and service them. operators are evolving to meet the changing needs The growing geographical spread of the sector of the offshore wind development community. So is leading to new players in the fabrication space too are suppliers of installation vessels, cable-lay springing up and players in other markets entering vessels, turbines and other components. -
Wind Energy Overview
An overview of Wind Power development in the Midwest Douglas J. Reinemann, Ph.D. Professor of Biological Systems Engineering University of Wisconsin – Madison Wind is one of the fastest growing Renewable energy sources in the world Annual Wind Turbine Installations Worldwide (MW) 6,000 6,000 Worldwide installed capacity (2001): 24,000 MW (~ 12.6 million homes @ 5,000 kWh/home and 30% wind capacity factor) 5,000 5,000 8,100 MW Germany 3,175 MW Spain 4,240 MW U.S. 2,417 MW Denmark 4,000 4,000 MW 45,000 MW predicted by 2005 3,000 3,000 2,000 2,000 1,000 1,000 0 0 1983 1984 1985 1986 1987 1988 1989 1990 1991 1992 1993 1994 1995 1996 1997 1998 1999 2000 2001 Source: Danish Wind Turbine Manufacturers Association & BTM Consult 1 Windmills? Early application of wind was for grinding grain (Wind-Mill) and pumping water (Windmill?) Making Electricity Wind Turbine Wind Energy Conversion System (WECS) Components of a WECS Gearbox Tower Rotor Foundation Controls Generator Illustration Source: RETScreen International www.retscreen.net 2 Where does the wind come from? Solar heating of the earth’s surface High pressure Vs. Low pressure systems Circulation Cell patterns •Hadley Cell (trade winds) •Ferrel Cell •Polar Cell Illustration source: Renewable Energy And where does it go? Power for a Sustainable Future, G. Boyle, 2004, Oxford Press Local Winds Sea Breezes Result of the seas ability to maintain temperature Daytime land heats, sea is cool Nighttime land cools faster than sea Illustration source: Renewable Energy Power for a Sustainable Future, G. -
Engineering Challenges for Floating Offshore Wind Turbines
A national laboratory of the U.S. Department of Energy Office of Energy Efficiency & Renewable Energy National Renewable Energy Laboratory Innovation for Our Energy Future Engineering Challenges for Conference Paper NREL/CP-500-38776 Floating Offshore Wind Turbines September 2007 S. Butterfield, W. Musial, and J. Jonkman National Renewable Energy Laboratory P. Sclavounos Massachusetts Institute of Technology Presented at the 2005 Copenhagen Offshore Wind Conference Copenhagen, Denmark October 26–28, 2005 NREL is operated by Midwest Research Institute ● Battelle Contract No. DE-AC36-99-GO10337 NOTICE The submitted manuscript has been offered by an employee of the Midwest Research Institute (MRI), a contractor of the US Government under Contract No. DE-AC36-99GO10337. Accordingly, the US Government and MRI retain a nonexclusive royalty-free license to publish or reproduce the published form of this contribution, or allow others to do so, for US Government purposes. This report was prepared as an account of work sponsored by an agency of the United States government. Neither the United States government nor any agency thereof, nor any of their employees, makes any warranty, express or implied, or assumes any legal liability or responsibility for the accuracy, completeness, or usefulness of any information, apparatus, product, or process disclosed, or represents that its use would not infringe privately owned rights. Reference herein to any specific commercial product, process, or service by trade name, trademark, manufacturer, or otherwise does not necessarily constitute or imply its endorsement, recommendation, or favoring by the United States government or any agency thereof. The views and opinions of authors expressed herein do not necessarily state or reflect those of the United States government or any agency thereof. -
Offshore Wind: Can the United States Catch up with Europe? January 2016
Offshore Wind: Can the United States Catch up with Europe? January 2016 Wind energy power generation is on the rise around the world, due to its low fixed prices and lack of greenhouse gas emissions. A cumulative total of 369,553 megawatts (MW) of wind energy capacity was installed globally by the end of 2014.1 Of that total, only two percent came from offshore wind farms, which are able to capture stronger and more reliable ocean winds to generate electricity.2 Most offshore wind capacity is in Europe, where there are 3,072 grid-connected offshore wind turbines at 82 farms spanning 11 countries, for a total of 10,393.6 MW of wind energy capacity as of June 30, 2015.3 China, the leader in offshore wind in Asia, had 718.9 MW of installed capacity; Japan, 52 MW; and South Korea, 5 MW as of October 2015.4, 5, 6 In comparison, the United States is just beginning to invest in offshore wind energy, and is rapidly approaching the operational launch of its first commercial offshore wind farm. There is incredible potential for offshore wind development in the United States – the National Renewable Energy Laboratory (NREL) has estimated the United States has over 4,000 gigawatts (GW) of offshore wind potential, enough to power the country four times over.7 Installed Capacity European Union Offshore Wind Installed Capacity Offshore Wind (as of first quarter 2015) (as of first quarter 2015) Netherlands, 361 MW, 3% Sweden, 212 MW, 2% 10,393.60 Other, 60 MW, 1% Belgium, 712 MW, 7% United Kingdom, Germany, 5,017.00 2,760 MW, MW, 48% 27% 0.02 776 UNITED STATES E U R O P E A N CHINA, JAPAN, Denmark, 1,271 MW, 12% UNION SOUTH KOREA Figure 1: Megawatts of offshore wind in the world8 Figure 2: E.U. -
Floating Offshore Wind 101 Webinar Q & A
Floating Offshore Wind 101 Webinar Q & A This Q&A document is based on the webinar, Floating Offshore Wind Overview. Cost and Economics Questions Answers Can you comment on the recent report that characterizes offshore wind in the We are unaware of the report being referenced, but we can say recent cost declines in Europe have been United States as too expensive? Is the industry positioned to counter that verified by NREL’s analysis of the revenue generated from negotiated power purchase agreements for assertion? the first few U.S. offshore wind projects suggest offshore wind: 1. Is no more expensive in the United States than in Europe 2. May soon be competitive in many electric markets, especially in the Northeast 3. May be able to provide additional benefits to the utility system, especially in constrained energy markets. What are the most likely financing schemes for U.S. utility-scale projects For early commercial-scale floating wind projects (e.g., those in the mid-2020s), we expect project starting construction in the mid-2020s or later without the benefit of federal tax financing arrangements that are similar to today’s financing of fixed-bottom wind projects in the United credits? Is a single-owner power purchase agreement the most likely financing States. The benefits of the fading tax credits will have to be compensated through other means to make mechanism, absent the past tax benefits for flip structures? projects bankable. These other means include lower costs or technology-specific, state-mandated power purchase agreements or offshore wind renewable energy certificates, which are known as ORECs, and they may need to be used in combination with public financing. -
IEA Wind Technology Collaboration Programme
IEA Wind Technology Collaboration Programme 2017 Annual Report A MESSAGE FROM THE CHAIR Wind energy continued its strong forward momentum during the past term, with many countries setting records in cost reduction, deployment, and grid integration. In 2017, new records were set for hourly, daily, and annual wind–generated electricity, as well as share of energy from wind. For example, Portugal covered 110% of national consumption with wind-generated electricity during three hours while China’s wind energy production increased 26% to 305.7 TWh. In Denmark, wind achieved a 43% share of the energy mix—the largest share of any IEA Wind TCP member countries. From 2010-2017, land-based wind energy auction prices dropped an average of 25%, and levelized cost of energy (LCOE) fell by 21%. In fact, the average, globally-weighted LCOE for land-based wind was 60 USD/ MWh in 2017, second only to hydropower among renewable generation sources. As a result, new countries are adopting wind energy. Offshore wind energy costs have also significantly decreased during the last few years. In Germany and the Netherlands, offshore bids were awarded at a zero premium, while a Contract for Differences auction round in the United Kingdom included two offshore wind farms with record strike prices as low as 76 USD/MWh. On top of the previous achievements, repowering and life extension of wind farms are creating new opportunities in mature markets. However, other challenges still need to be addressed. Wind energy continues to suffer from long permitting procedures, which may hinder deployment in many countries. The rate of wind energy deployment is also uncertain after 2020 due to lack of policies; for example, only eight out of the 28 EU member states have wind power policies in place beyond 2020. -
Windmill Worksheet [From the NOVA Web Site]
Windmill Worksheet [From the NOVA Web site] Teacher Notes Part of what students are doing in this activity is reverse engineering, in which students look at something that exists to figure out how it works rather than building from the ground up. On the Windmill Template (Figure A), the solid lines indicate where to cut the paper and the dot- ted lines indicate where to fold (but not crease) it. The circles indicate where to punch holes. Figure B shows how the corners of the windmill are folded over and attached to the straw and how the rubber bands are used to keep the windmill in place. Figure C shows the cup and string attachment, and Figure D shows how to hold the machine so that the straw spins freely as the windmill turns. Students will discover through trial and error how best to attach the string to the straw. Because there is no exact description of materials, student choices may vary. For example, one team may choose regular bond paper for the windmill while another may choose a card stock. This provides a good opportunity to discuss how different materials behave within the design and why. Students familiar with pinwheels will know that blowing on the windmill causes it to turn. Students may then use this information to help them understand how wheel-and-axle machines work. If students are not familiar with this type of simple machine, you may want to identify it at the activity's end. At the end of the activity, students may experiment by changing the size of the windmill, the type of paper used for the windmill, the diameter of the straw, or even substituting entirely new materials.