Page 1 TRANSPORT ACCIDENT INVESTIGATION COMMISSION
Total Page:16
File Type:pdf, Size:1020Kb
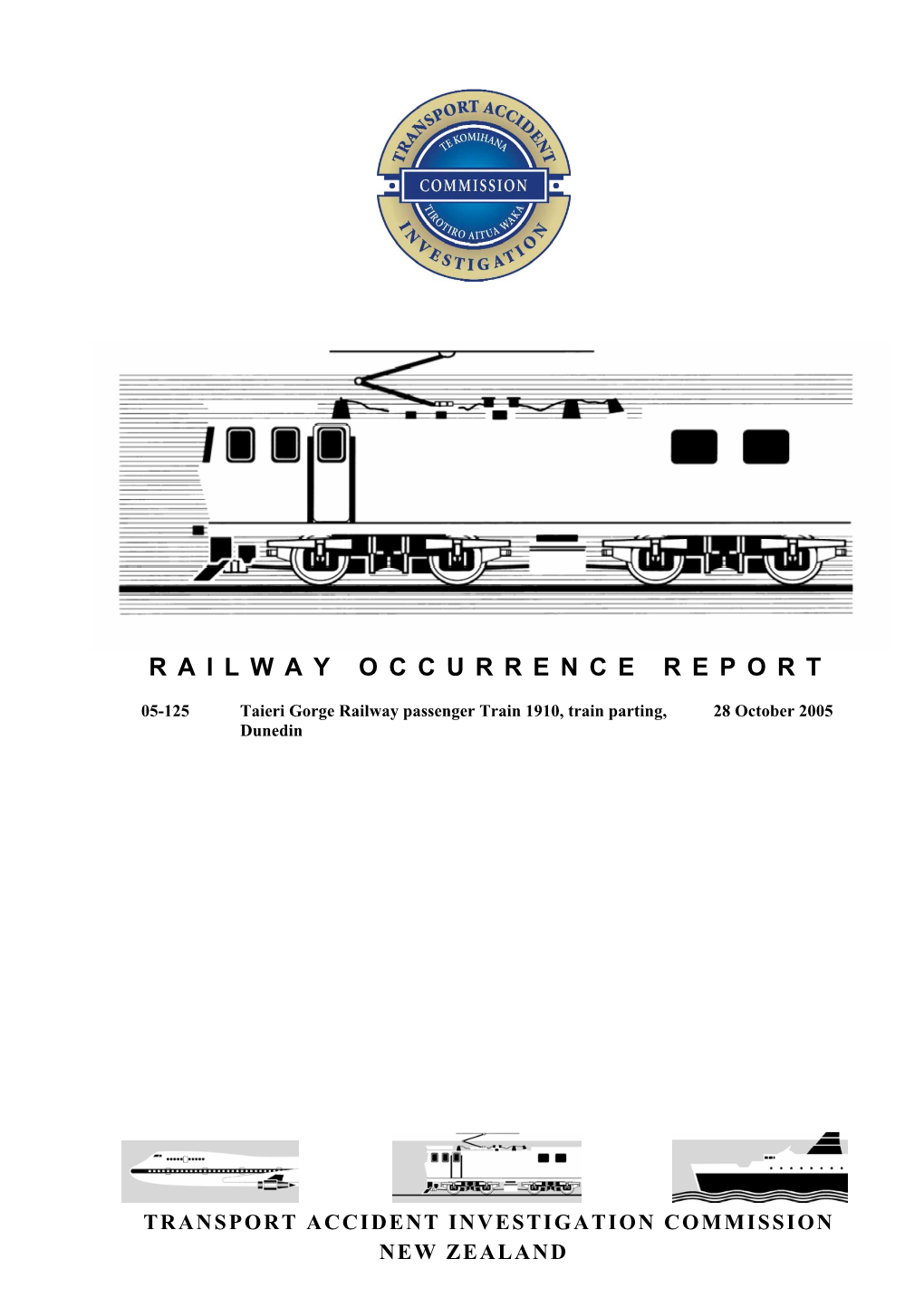
Load more
Recommended publications
-
Annual Report 2016 This Page Is Intentionally Left Blank
Annual Report 2016 This page is intentionally left blank 2 This report is published in accordance with: l the Railway Safety Directive 2004/49/EC; l the Railways and Transport Safety Act 2003; and l the Railways (Accident Investigation and Reporting) Regulations 2005. © Crown copyright 2017 You may re-use this document/publication (not including departmental or agency logos) free of charge in any format or medium. You must re-use it accurately and not in a misleading context. The material must be acknowledged as Crown copyright and you must give the title of the source publication. Where we have identified any third party copyright material you will need to obtain permission from the copyright holders concerned. This document/publication is also available at www.gov.uk/raib. Any enquiries about this publication should be sent to: RAIB Email: [email protected] The Wharf Telephone: 01332 253300 Stores Road Fax: 01332 253301 Derby UK Website: www.gov.uk/raib DE21 4BA This report is published by the Rail Accident Investigation Branch, Department for Transport. Cover image credits: Top: image taken from RAIB report 05/2016: Derailment at Godmersham. Second from top: image taken from RAIB report 09/2016: Runaway and collision at Bryn station. Third from top: image taken from RAIB report 11/2016: Derailment of a freight train near Langworth (image courtesy of Network Rail). Fourth from top: image taken from RAIB report 04/2017: Collision between a train and a tractor at Hockham Road user worked crossing. This page is intentionally left blank 4 Preface This is the Rail Accident Investigation Branch’s (RAIB) Annual Report for the calendar year 2016. -
Auckland Open Day the Strand Railway Station, Ngaoho Place, Parnell 10Am – 4Pm, Sunday 29 September 2013
Auckland Open Day The Strand Railway Station, Ngaoho Place, Parnell 10am – 4pm, Sunday 29 September 2013 Media contact: Kimberley Brady (021) 942 519 COME AND SEE: • The Exhibition Express - Jump into the drivers seat of a KiwiRail locomotive and talk with the locomotive engineer (train driver) - Get on board our new KiwiRail Scenic passenger carriages - Discover the amazing achievements of our early rail builders in our Moving through the Times display - Enjoy an experiential journey in our Moving Experience display - Learn more about the way rail Moves the Economy - Find out about the importance of Moving Safely and Responsibly when near rail • Career Opportunities - Talk with our Human Resources team about the many job opportunities that exist in KiwiRail, KiwiRail Scenic, Interislander, and KiwiRail Freight • Safety Awareness - Talk with our Safety Team about keeping safe near the track • Heritage trains on show - Take a look back in time by viewing Mainline Steam’s Ja1275, which will be on display. OTHER ACTIVITIES: Calling all Aucklanders to do ‘The Loco...motion!’ We want to rock Auckland with the largest locomotion dance ever seen! We loved it when Kylie did it – now it’s your turn. Bust out your 80s party moves, put on your dancing shoes and join in the fun! Join the ZM Black Thunders at KiwiRail “Keeping NZ on the Move” Exhibition Express open day at 11:30am and do the Locomotion. Don’t be a-freight! The Exhibition Express Prize Draw The prize of a return journey aboard KiwiRail Scenic’s Northern Explorer service for a family (2 adults and 3 children) will be drawn at the Open Day. -
02-120. Electric Multiple Units, Trains 9351 and 3647, Collision
R A I L W A Y O C C U R R E N C E R E P O R T 02-120 electric multiple units, Trains 9351 and 3647, collision, 31 August 2002 Wellington TRANSPORT ACCIDENT INVESTIGATION COMMISSION NEW ZEALAND The Transport Accident Investigation Commission is an independent Crown entity established to determine the circumstances and causes of accidents and incidents with a view to avoiding similar occurrences in the future. Accordingly it is inappropriate that reports should be used to assign fault or blame or determine liability, since neither the investigation nor the reporting process has been undertaken for that purpose. The Commission may make recommendations to improve transport safety. The cost of implementing any recommendation must always be balanced against its benefits. Such analysis is a matter for the regulator and the industry. These reports may be reprinted in whole or in part without charge, providing acknowledgement is made to the Transport Accident Investigation Commission. Report 02-120 electric multiple units Trains 9351 and 3647 collision Wellington 31 August 2002 Abstract On Saturday 31 August 2002 at about 1515, Train 9351, a Tranz Metro1 Johnsonville to Wellington electric multiple unit passenger service collided with Train 3647, a Tranz Metro Upper Hutt to Wellington electric multiple unit passenger service, as both trains were approaching the Wellington platforms on converging tracks. There were no injuries to passengers or crew and only minor damage to the trains. The safety issues identified included the well-being of the electric multiple unit driver of Train 9351 and his resulting capacity to recognise and respond to a danger signal indication. -
Rail Safety Report 2019-2020
19 20 OFFICE OF THE NATIONAL RAIL SAFETY REGULATOR Level 1, 75 Hindmarsh Square Adelaide SA 5000 PO Box 3461, Rundle Mall Adelaide SA 5000 Phone 08 8406 1500 Email [email protected] Web onrsr.com.au ISSN: 2204 - 2571 Copyright information © 2020 Office of the National Rail Safety Regulator RAIL SAFETY REPORT This material may be reproduced in whole or in part, provided the meaning is unchanged and the source is acknowledged. 2019-2020 Contents The Regulator’s Message 2 Introduction 5 About the Office of the National Rail Safety Regulator 6 About This Report 9 ONRSR 2019–2020 - At a glance 10 Rail Safety Statistical Summary 13 Railway-Related Fatalities 15 Railway-Related Serious Injuries 21 Passenger Train Derailments 26 Tram Derailments 29 Freight Train Derailments 31 Train Collisions 34 Tram Collisions 37 Signals Passed at Danger and Authorities Exceeded 40 Train Fires 42 Other Noteworthy Occurrences 44 National Priorities 47 National Priorities 2019–2020 - At a glance 48 Level Crossing Safety 51 Track Worker Safety 57 Contractor Management 60 Control Assurance 61 Data-Driven Intelligence 63 Safety Themes 65 Data Sharing 67 Appendix A: Network Statistics 72 Appendix B: Scope and Methods 74 the regulator’s message I DON’T THINK IT IS AN OVERSTATEMENT TO SUGGEST THE WORLD HAS BECOME A MORE COMPLICATED PLACE IN THE LAST 12 MONTHS. AT THE RISK OF SOUNDING SOMEWHAT CLICHÉD, THE NEED TO LOOK AFTER OURSELVES AND EACH OTHER REALLY IS MORE IMPORTANT THAN EVER. Never losing sight of why we are here and having genuine clarity of purpose has been The report also charts the progress we, as a regulator, and industry integral to the Office of the National Rail Safety Regulator’s (ONRSR) response to the collectively have made on our national priority issues – track worker safety, emergence of COVID-19. -
Sr.No. Description Page No. 1. Important Definitions, Classification of 02 Stations 2
1 INDEX Sr.No. Description Page No. 1. Important Definitions, Classification of 02 Stations 2. Signals 07 3. Defective Signals 15 4. Authorities 24 5. Systems of working 30 6. Shunting 35 7. Speed 39 8. Head light, Flasher light, Marker light 43 9. Pushing back 45 10. FOIS, COIS 48 11. ACD 51 12. ODC, Marshalling 52 13. Isolation, Interlocking 59 14. Reception and Despatch of trains 63 15. Defective Points 68 16. Temporary Single Line Working 71 17. All Communication Failure on Double Line 75 18. All Communication Failure on Single Line 78 19. Abnormal Working in Automatic Section 82 20. Train Parting, Train Dividing 93 21. Assistance to disabled engine 100 22. Sending Assisting Engine into Obstructed 101 Block Section 23. Train Delayed in Block Section 102 24. Working of Tower Wagon 103 25. Working of Material Train 105 26. Working of Lorry, Trolly and Motor Trolly 109 27. Monsoon Patrolling, Defects in Track 118 28. Working of Track Maintenance Machines 122 29. Accident 127 30. Block Instrument – Bell Code 139 31. Engine Whistle Code 142 32. Working of Train without Brake Van 145 33. Personal Store of Guard / Loco Pilot 147 34. Train Stalled on Gradient – Duties 150 35. Protection Rules 152 36. Traction Subsidiary Rules 155 37. Abbreviations 168 Traffic Faculty, Zonal Railway Training Institute, Central Railway / Bhusawal 2 Important Definitions 1. Adequate Distance: G.R.1.02 (2) – It means the distance sufficient to ensure safety. a) Block Over-lap – The distance sufficient to ensure safety for granting line clear. It shall be not less than 400 meters in TALQ signalling system and not less than 180 meters in MAUQ / MACLS signalling system. -
The Southall Rail Accident Inquiry Report Professor John Uff QC Freng
iealth 6 Safety Commission The Southall Rail Accident Inquiry Report - Professor John Uff QC FREng 2 Erratum The Southali Rail Accident Inquiry Report iSBN 0 7176 1757 2 Annex 09 Passengers & Staff believed to have sustained injury as a result of the accident Include 'Stuttard, Janis, Mrs Coach H' Delete ' Stothart, Chloe Helen, Miss Coach C' MlSC 210 HSE BOOKS 0 Crown copyright 2000 Applications for reproduction should be made in writing to: Copyright Unit, Her Majesty's Stationery Office, St Clernents House, 2-16 Colegate, Nofwich NR3 1BQ First published 2000 All rights reserved. No part of this publication may be reproduced, stored in a retrieval system, or transmitted in any form or by any means (electronic, mechanical, photocopying, recording or otherwise) without the prior written permission of the copyright owner. LIST OF CONTENTS Inquiry into Southall Railway Accident Preface Glossary Report Summary PART ONE THE ACCIDENT Chapter l How the accident happened Chapter 2 The emergency response Chapter 3 The track and signals Chapter 4 Why was the freight train crossing? Chapter 5 Driver competence and training Chapter 6 Why were the safety systems not working? Chapter 7 Why the accident happened PART TWO EVENTS SINCE SOUTJULL Chapter 8 The Inquiry and delay to progress Chapter 9 Reactions to Southall Chapter 10 Ladbroke Grove and its aftermath PART THREE WIDER SAFETY ISSUES Chapter 11 Crashworthiness and means of escape Chapter 12 Automatic Warning System (AWS) Chapter 13 Automatic Train Protection (ATP) Chapter 14 Railway Safety Issues PART FOUR CONCLUSION Chapter 15 Discussion and Conclusions Chapter 16 Lessons to be learned Chapter 17 Recommendations ANNEXES THIS Report follows an Inquiry held between September and December 1999 into the cause of a major rail accident which occurred on 19 September 1997 at Southall, 9 miles west of Paddington. -
Report RO-2014-102: High-Speed Roll-Over, Empty Passenger Train 5153, Westfield, South Auckland, 2 March 2014
Report RO-2014-102: High-speed roll-over, empty passenger Train 5153, Westfield, South Auckland, 2 March 2014 The Transport Accident Investigation Commission is an independent Crown entity established to determine the circumstances and causes of accidents and incidents with a view to avoiding similar occurrences in the future. Accordingly it is inappropriate that reports should be used to assign fault or blame or determine liability, since neither the investigation nor the reporting process has been undertaken for that purpose. The Commission may make recommendations to improve transport safety. The cost of implementing any recommendation must always be balanced against its benefits. Such analysis is a matter for the regulator and the industry. These reports may be reprinted in whole or in part without charge, providing acknowledgement is made to the Transport Accident Investigation Commission. Final Report Rail inquiry RO-2014-102, high-speed roll-over, empty passenger Train 5153, Westfield, South Auckland 2 March 2014 Approved for publication: February 2015 Transport Accident Investigation Commission About the Transport Accident Investigation Commission The Transport Accident Investigation Commission (Commission) is an independent Crown entity responsible for inquiring into maritime, aviation and rail accidents and incidents for New Zealand, and co-ordinating and co-operating with other accident investigation organisations overseas. The principal purpose of its inquiries is to determine the circumstances and causes of occurrences with a view to avoiding similar occurrences in the future. Its purpose is not to ascribe blame to any person or agency or to pursue (or to assist an agency to pursue) criminal, civil or regulatory action against a person or agency. -
A Railway Collision Avoidance System Exploiting Ad-Hoc Inter-Vehicle Communications and Galileo
A RAILWAY COLLISION AVOIDANCE SYSTEM EXPLOITING AD-HOC INTER-VEHICLE COMMUNICATIONS AND GALILEO Thomas Strang(1), Michael Meyer zu Hörste(2), Xiaogang Gu (3) German Aerospace Center (1)Institute of Communications and Navigation (2)Institute of Transportation Systems [email protected] [email protected] (3)Bombardier Transportation RailControlSolutions [email protected] ABSTRACT The introduction of the European global navigation satellite system GALILEO allows also for a modernization of automatic train control technology. This is advisable because of the still enormous amount of collisions between trains or other kinds of obstacles (construction vehicles, construction workers, pedestrians), even if comprehensive and complex technology is extensively deployed in the infrastructure which should help to avoid such collisions. Experiences from the aeronautical Traffic Alert and Collision Avoidance System (TCAS) as well as the maritime Automatic Identification System (AIS) have shown that the probability of collisions can be significantly reduced with collision avoidance support systems, which do hardly require infrastructure components. In this article, we introduce our “RCAS” approach consisting only of mobile ad-hoc components, i.e. without the necessity of extensions of the railway infrastructure. Each train determines its position, direction and speed using GALILEO and broadcasts this information, complemented with other important information such as dangerous goods classifications in the region of its current location. This information can be received and evaluated by other trains, which may – if a potential collision is detected – lead to traffic alerts and resolution advisories up to direct interventions (usually applying the brakes). STATE OF THE ART IN TRAIN CONTROL Today the safety of railway operation is mainly ensured by the interlocking which sets and locks the train route. -
Dunedin Railways Workers Propose Positive Solutions to Prevent Closure
Dunedin Railways workers propose positive solutions to prevent closure Rail and Maritime Transport Union media release FOR IMMEDIATE RELEASE Thursday 30 April 2020 Workers at Dunedin Railways Limited (DRL) have put forward a proposal to reinvigorate the company, retaining the iconic Taieri Gorge Railway and saving up to 70 jobs. Rail and Maritime Transport Union Otago Branch Secretary Dave Kearns says the union, representing about fifty workers at Dunedin Railways, has today submitted the proposal (attached) as part of the consultation process with management. Dunedin Railways is 100% owned by Dunedin City Holdings Limited, the business arm of the Dunedin City Council. Mr Kearns says the DRL Board of Directors had a ‘negative mindset’ and had recommended closing the railway to the Dunedin City Council, blaming falling revenues due to the COVID19 pandemic. Dunedin City Councillors had voted to mothball the railway instead, but Mr Kearns says he is concerned that they have not been given the correct information about how this would work. ‘The DRL plan is meaningless as it is so lacking in detail. This raises questions regarding the competence and fitness of DRL’s board and senior management.’ Mr Kearns says there are a number of opportunities for rail services that have been ignored. Options included the reconfiguration of the business away from the cruise ship market to the domestic market. There was potential for staff and rolling stock to provide commuter services to local destinations such as Mosgiel and Port Chalmers, as well as the establishment of long distance passenger services between Dunedin and other cities on the main south line. -
Summary Table of Requirements Rolled Over 'With Modification'
Introduction This table contains a summary of requirements that requiring authorities have sought to have ‘rolled-over’ with modification(s). It does not include requirements that have been rolled over without modification. It includes any changes to existing designations sought through the requiring authority’s formal (Schedule 1) roll-over notice and any subsequent amendments agreed between the requiring authority and the Council prior to 27 August 2014. For further detail please refer to the ‘roll-over notices’ included on this website, along with the planning maps and designation detail (including conditions) contained in Chapter 10 of the proposed Christchurch Replacement District Plan. Alternatively you can phone us on 941- 8999 (0800 800 169 for Banks Peninsula callers) or email us at [email protected] with any queries. Chorus New Zealand Limited CCC Ref Notation / Site Name Purpose Location Nature of Any Modifications A1 Akaroa Exchange Telecommunication and Cnr Rue Jolie & Rue Balguriel Name change only (to Chorus Radio Communication New Zealand Limited) and Ancillary Purposes A2 Akaroa Radio Station as above L’Aube Hill Name change only (to Chorus New Zealand Limited) A3 Ataahua Exchange as above State Highway 75, Ataahua Name change only (to Chorus New Zealand Limited) A4 Avonhead Exchange as above 296 Yaldhurst Road Name change only (to Chorus New Zealand Limited) A5 Cashmere Radio as above Victoria Park Road Name change only (to Chorus Station New Zealand Limited) A6 Diamond Harbour as above Where Avenue Name change only -
Inquiry RO-2012-104: Train 723 Overran Limit of Track Warrant Parikawa, Main North Line, 1 August 2012
Inquiry RO-2012-104: Train 723 overran limit of track warrant Parikawa, Main North line, 1 August 2012 The Transport Accident Investigation Commission is an independent Crown entity established to determine the circumstances and causes of accidents and incidents with a view to avoiding similar occurrences in the future. Accordingly it is inappropriate that reports should be used to assign fault or blame or determine liability, since neither the investigation nor the reporting process has been undertaken for that purpose. The Commission may make recommendations to improve transport safety. The cost of implementing any recommendation must always be balanced against its benefits. Such analysis is a matter for the regulator and the industry. These reports may be reprinted in whole or in part without charge, providing acknowledgement is made to the Transport Accident Investigation Commission. Final Report Rail inquiry RO-2012-104 Train 723 overran limit of track warrant Parikawa, Main North line 1 August 2012 Approved for publication: August 2015 Transport Accident Investigation Commission About the Transport Accident Investigation Commission The Transport Accident Investigation Commission (Commission) is a standing commission of inquiry and an independent Crown entity responsible for inquiring into maritime, aviation and rail accidents and incidents for New Zealand, and co-ordinating and co-operating with other accident investigation organisations overseas. The principal purpose of its inquiries is to determine the circumstances and causes of the occurrences with a view to avoiding similar occurrences in the future. Its purpose is not to ascribe blame to any person or agency or to pursue (or to assist an agency to pursue) criminal, civil or regulatory action against a person or agency. -
Signal Passed at Danger by Track Machine Consist 8M71, Goobang Junction, 10 May 2009 I OTSI Rail Safety Investigation
RAIL SAFETY INVESTIGATION REPORT SIGNAL PASSED AT DANGER BY TRACK MACHINE CONSIST 8M71 GOOBANG JUNCTION 10 MAY 2009 RAIL SAFETY INVESTIGATION REPORT SIGNAL PASSED AT DANGER BY TRACK MACHINE CONSIST 8M71 GOOBANG JUNCTION 10 MAY 2009 Released under the provisions of Section 45C (2) of the Transport Administration Act 1988 and Section 67 (2) of the Rail Safety Act 2008 Investigation Reference 04439 Published by: The Office of Transport Safety Investigations Postal address: PO Box A2616, Sydney South, NSW 1235 Office location: Level 17, 201 Elizabeth Street, Sydney NSW 2000 Telephone: 02 9322 9200 Accident and incident notification: 1800 677 766 Facsimile: 02 9322 9299 E-mail: [email protected] Internet: www.otsi.nsw.gov.au This Report is Copyright. In the interests of enhancing the value of the information contained in this Report, its contents may be copied, downloaded, displayed, printed, reproduced and distributed, but only in unaltered form (and retaining this notice). However, copyright in material contained in this Report which has been obtained by the Office of Transport Safety Investigations from other agencies, private individuals or organisations, belongs to those agencies, individuals or organisations. Where use of their material is sought, a direct approach will need to be made to the owning agencies, individuals or organisations. Subject to the provisions of the Copyright Act 1968, no other use may be made of the material in this Report unless permission of the Office of Transport Safety Investigations has been obtained. THE OFFICE OF TRANSPORT SAFETY INVESTIGATIONS The Office of Transport Safety Investigations (OTSI) is an independent NSW agency whose purpose is to improve transport safety through the investigation of accidents and incidents in the rail, bus and ferry industries.