The Evolution of Yuzen-Dyeing Techniques and Designs After the Meiji Restoration
Total Page:16
File Type:pdf, Size:1020Kb
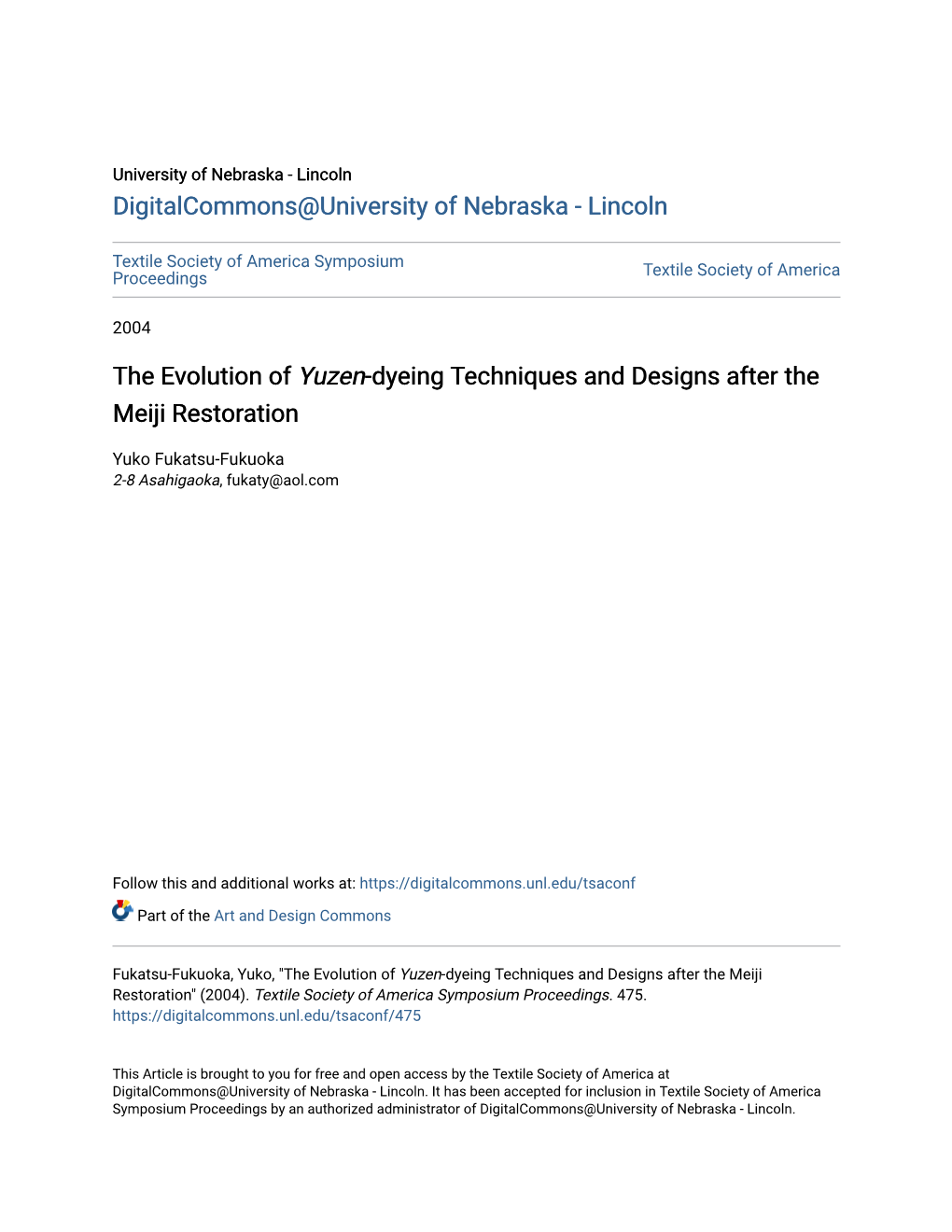
Load more
Recommended publications
-
Alum Mineral and the Importance for Textile Dyeing
Current Trends in Fashion Technology & Textile Engineering ISSN: 2577-2929 Mini-Review Curr Trends Fashion Technol Textile Eng Volume 3- Issue 4 - April 2018 Copyright © All rights are reserved by Ezatollah Mozaffari DOI: 10.19080/CTFTTE.2018.03.555619 Alum Mineral and the Importance for Textile Dyeing Ezatollah Mozaffari* and Bijan Maleki Imam khomeini international university, Qazvin, Iran Submission: Published: April 25, 2018 *Corresponding April author: 10, 2018; Email: Ezatollah Mozaffari, Imam khomeini International University, Qazvin, Iran, Tel: +9828-33901133; Abstract The importance of alum as a natural mordant in textile dyeing is explained. The history of alum mineral processing was reviewed to emphasise on the heritage knowledge inherited by current trends in fashion technology and textile engineering. The review will also demonstrate the conservative environmental preservation nature of alum mineral as mordant. The need for modern evaluation of natural dyes and mordants will be highlighted. Keywords: Alum; Mordant; Industrial heritage Introduction the calcined mass the calcined shale was barrowed to a series Alum was known as one of the most imperative components of stone leaching pits nearby with typical dimensions of 9 x of textile industry before the introduction of chemical dyes in 4.5 x 1.5m. Fresh liquid was added to the leaching tanks and the process repeated for several weeks. The waste solids were alum quarrying and trade in several geographical areas [1]. In the 1850s. Its significance could be explored when studying the literature, interesting notes on alum as a mordant for textile liquor from leaching rose to 1.12, indicating 12 tons of dissolved dyeing of yarn, cloth and leather in North America, China, Libya, eventually dug out and discarded. -
The Maiwa Guide to NATURAL DYES W H at T H Ey a R E a N D H Ow to U S E T H E M
the maiwa guide to NATURAL DYES WHAT THEY ARE AND HOW TO USE THEM WA L NUT NATURA L I ND IG O MADDER TARA SYM PL O C OS SUMA C SE Q UO I A MAR IG O L D SA FFL OWER B U CK THORN LIVI N G B L UE MYRO B A L AN K AMA L A L A C I ND IG O HENNA H I MA L AYAN RHU B AR B G A LL NUT WE L D P OME G RANATE L O G WOOD EASTERN B RA ZIL WOOD C UT C H C HAMOM IL E ( SA PP ANWOOD ) A LK ANET ON I ON S KI NS OSA G E C HESTNUT C O C H I NEA L Q UE B RA C HO EU P ATOR I UM $1.00 603216 NATURAL DYES WHAT THEY ARE AND HOW TO USE THEM Artisans have added colour to cloth for thousands of years. It is only recently (the first artificial dye was invented in 1857) that the textile industry has turned to synthetic dyes. Today, many craftspeople are rediscovering the joy of achieving colour through the use of renewable, non-toxic, natural sources. Natural dyes are inviting and satisfying to use. Most are familiar substances that will spark creative ideas and widen your view of the world. Try experimenting. Colour can be coaxed from many different sources. Once the cloth or fibre is prepared for dyeing it will soak up the colour, yielding a range of results from deep jew- el-like tones to dusky heathers and pastels. -
Textile Printing
TECHNICAL BULLETIN 6399 Weston Parkway, Cary, North Carolina, 27513 • Telephone (919) 678-2220 ISP 1004 TEXTILE PRINTING This report is sponsored by the Importer Support Program and written to address the technical needs of product sourcers. © 2003 Cotton Incorporated. All rights reserved; America’s Cotton Producers and Importers. INTRODUCTION The desire of adding color and design to textile materials is almost as old as mankind. Early civilizations used color and design to distinguish themselves and to set themselves apart from others. Textile printing is the most important and versatile of the techniques used to add design, color, and specialty to textile fabrics. It can be thought of as the coloring technique that combines art, engineering, and dyeing technology to produce textile product images that had previously only existed in the imagination of the textile designer. Textile printing can realistically be considered localized dyeing. In ancient times, man sought these designs and images mainly for clothing or apparel, but in today’s marketplace, textile printing is important for upholstery, domestics (sheets, towels, draperies), floor coverings, and numerous other uses. The exact origin of textile printing is difficult to determine. However, a number of early civilizations developed various techniques for imparting color and design to textile garments. Batik is a modern art form for developing unique dyed patterns on textile fabrics very similar to textile printing. Batik is characterized by unique patterns and color combinations as well as the appearance of fracture lines due to the cracking of the wax during the dyeing process. Batik is derived from the Japanese term, “Ambatik,” which means “dabbing,” “writing,” or “drawing.” In Egypt, records from 23-79 AD describe a hot wax technique similar to batik. -
Guide to Dyeing Yarn
presents Guide to Dyeing Yarn Learn How to Dye Yarn Using Natural Dyeing Techniques or some of us, the pleasure of using natural dyes is the connection it gives us with the earth, using plants and fungi and minerals from the environment in our Fhandmade projects. Others enjoy the challenge of finding, working with, and sometimes even growing unpredictable materials, then coaxing the desired hues. My favorite reason for using natural dyes is just plain lovely color. Sometimes subtle and always rich, the shades that skilled dyers achieve with natural dyestuffs are heart- breakingly lovely. No matter what inspires you to delve into natural dyes, this free eBook has some- thing for you. If you’re interested in connecting with the earth, follow Lynn Ruggles as she combines her gardening and fiber passions, or join Brighid’s Dyers as they harness alternative energy with solar dyeing. To test and improve your skills, begin with Dag- mar Klos’s thorough instructions. But whatever your reason, be sure to enjoy the range of natural colors on every page. One of Interweave’s oldest publications, Spin.Off inspires spinners to make beautiful yarn and find enchanting ways to use it. In addition to the quarterly magazine, we also host the spinning community spinningdaily.com, complete with blogs, forums, and free patterns. In our video workshop series, the living treasures of the spinning world share their knowledge. We’re devoted to bringing you the best spinning teachers, newest spinning techniques, and most inspiring ideas—right to your mailbox, your computer, and your very fingertips. -
Monthly Glocal News
Monthly Glocal News December 2020 Local Partnership Cooperation Division Ministry of Foreign Affairs of Japan International exchange in Miyazaki Prefecture A tale of two pottery cities – — through the prefectural association in Brazil— Arita Town, Saga Prefecture in Japan and Meissen City in Germany – (Miyazaki Prefecture) The 35th anniversary ceremony of young The 70th anniversary ceremony of agriculturist dispatching program Miyazaki Kenjinkai Seven potters from Arita Town visited Dresden of he Miyazaki Kenjinkai (prefectural association) in former East Germany in 1970 Brazil is made up of those who have emigrated from Miyazaki prefecture to Brazil and their families. The association celebrated the 70th anniversary in 20T19. Miya zaki Prefecture has been interacting with Brazil for many years through the Kenjinkai, which acts as a bridge be- tween two sides. The members of the Kenjinkai think about Miyazaki far away from their hometown. The Prefecture al- so focuses on human exchanges of young generation between Brazil and Miyazaki including students and young people who are engaged in agriculture. Saraodori dance of Arita Town was performed in Meissen wine festival in 2019 Host Town Initiative in times of COVID19 – Even if we are far apart, our heart will always be together beyond the sea- (Kanagawa Prefecture and Fujisawa City) At the booths of cultural exchanges with citizen of Ambassador of the Republic of Online Meeting between Portu- Meissen in 2019 El Salvador to Japan presented coffee guese Paralympic athletes and beans to Kanagawa Prefecture and junior high school students in Fujisawa City (September 2020) Fujisawa City (October 2020) rita Town located in Saga Prefec- ture in Japan is known as the ujisawa City together with Kanagawa Prefecture will place where the first pottery was host the Tokyo 2020 Pre-Games Training Camps as a made within Japan. -
Dyeing Tips & Methods
Dyeing Tips & Methods: - Formulas are designed to be used in all dye applications methods where acid dyes are used. Formulas will be given so that you can do immersion dyeing or direct application dyeing, mixing from stock solutions or with dry powder. Whichever method you prefer, I suggest mixing the starting dyes into 1% stock solutions first. After stock solutions are mixed, then using the formula provided, mix up whatever color you are trying to match. Depending on the weight of the fiber to be dyed, such as a 10g skein, some quantities of dye are so small that having the dye powder mixed in solution first will help you achieve the most accurate color. - If possible, sample a small 10g skein to see how the color formula looks on your fiber base. The formulas were calculated on a 10g 80%/20% superwash wool/nylon blend natural white (unbleached) skein. Different breeds of sheep and different types of protein fibers such as mohair, silk, alpaca, angora, etc., will absorb the dye differently and may influence the final color. - If you’re using a Pantoneâ “Formula Guide Uncoated” swatch book, please note that the colors may look different under different lighting conditions. Fluorescent, incandescent, and natural lighting all can shift the way a color appears. Colors have been tested and observed under a 5000K daylight bulb to ensure the closest match. - After the yarn/fiber has been dyed, and the heat has been turned off, allow the fiber to cool overnight/24 hours for best absorption of colors. - Prior to dyeing I mix a 10% solution of 100g citric acid mixed with 1000mL water and use a syringe to inject the acid into the dyepot for immersion dyeing. -
History of Japanese Colour: Traditional Natural Dyeing Methods
Colour: Design & Creativity (5) (2010): 4, 1–7 http://www.colour-journal.org/2010/5/4/ History of Japanese Colour: Traditional Natural Dyeing Methods Sachio Yoshioka Email: [email protected] Published online: 12 May 2010 Introduction The family I was born into has followed a tradition of dyeing textiles for more than 200 years in Kyoto, the capital of Japan for about 1000 years until the Emperor moved to Tokyo in 1869. The dyeing technique I use to this day involves only natural materials including tree bark, fl owers, seeds, roots and grass. This traditional dyeing method has been used in Japan for centuries, although since the invention of synthetic dyes in the 19th century, such processes are becoming less and less common. However, I strive to keep such traditions alive. I have discovered the importance of studying the history of dyeing and the use of traditional colours in Japan, learning a lot from my predecessors’ achievements in textile dyeing. Commencement of Dyeing and Weaving in Japan It is believed that the skill of sericulture – or silk farming – came to Japan from China in around the 3rd century BC, about the time when the age of plantation agriculture started. However, at that time, people could not dye colourful yarn or weave beautiful patterns with a loom. Indeed, the repertoire of the time included only a few primitive dyeing and weaving techniques. It is said that the Japanese people developed techniques for textile dyeing and weaving over the course of 2000 years. In fact, many dyeing and weaving implements were excavated from tombs of ancient and powerful clans of Japan. -
Tub Dyeing Basics Step by Step Instructions on the Next Page G with Fiber Reactive Dyes
tub dyeing basics Step by step instructions on the next page g with Fiber Reactive Dyes Use this method to dye fabric or clothing, made of natural fibers one uniform or solid color. Also called Garment Dyeing or Vat Dyeing, this method can also be done in a washing machine. Fiber Reactive Dye is the dye of choice for all cellulose (plant) fibers, like cotton, Rayon, hemp, linen, Tencel®, Modal®, bamboo, etc. (For dyeing silk, wool and other protein fibers, see Dyeing Wool and Silk with Fiber Reactive Dyes on our website) The chemical bond of these dyes is permanent, so once all the excess dye is washed out an infant can chew on the fabric and it will not come off! Fiber Reactive Dyes work in lukewarm water so these directions can also be used to dye batik (waxed) fabrics in successive colors without fear of melting the wax. WHAT You’ll need: SALT & SODA ASH REQUIREMENTS • Fiber Reactive Dye • A bucket large enough The amount of Non-Iodized Salt and Soda Ash are for your item to move a function of the amount of water used. For each • Soda Ash around in, or a top pound of dry fabric you will need about 3 gallons of • Non-Iodized Salt loading washing machine warm water. The water must cover the fabric with • Urea (optional) • Pitcher & cup enough room for thorough, tangle-free stirring; oth- erwise you get uneven dyeing and streaks. For each • Calsolene Oil (optional) • Measuring cups 1½ gallons of water use 1½ cups of Non-Iodized • Synthrapol • Spoons Salt and 1/6 cup of Soda Ash. -
Rail Pass Guide Book(English)
JR KYUSHU RAIL PASS Sanyo-San’in-Northern Kyushu Pass JR KYUSHU TRAINS Details of trains Saga 佐賀県 Fukuoka 福岡県 u Rail Pass Holder B u Rail Pass Holder B Types and Prices Type and Price 7-day Pass: (Purchasing within Japan : ¥25,000) yush enef yush enef ¥23,000 Town of History and Hot Springs! JR K its Hokkaido Town of Gourmet cuisine and JR K its *Children between 6-11 will be charged half price. Where is "KYUSHU"? All Kyushu Area Northern Kyushu Area Southern Kyushu Area FUTABA shopping! JR Hakata City Validity Price Validity Price Validity Price International tourists who, in accordance with Japanese law, are deemed to be visiting on a Temporary Visitor 36+3 (Sanjyu-Roku plus San) Purchasing Prerequisite visa may purchase the pass. 3-day Pass ¥ 16,000 3-day Pass ¥ 9,500 3-day Pass ¥ 8,000 5-day Pass Accessible Areas The latest sightseeing train that started up in 2020! ¥ 18,500 JAPAN 5-day Pass *Children between 6-11 will be charged half price. This train takes you to 7 prefectures in Kyushu along ute Map Shimonoseki 7-day Pass ¥ 11,000 *Children under the age of 5 are free. However, when using a reserved seat, Ro ¥ 20,000 children under five will require a Children's JR Kyushu Rail Pass or ticket. 5 different routes for each day of the week. hu Wakamatsu us Mojiko y Kyoto Tokyo Hiroshima * All seats are Green Car seats (advance reservation required) K With many benefits at each International tourists who, in accordance with Japanese law, are deemed to be visiting on a Temporary Visitor R Kyushu Purchasing Prerequisite * You can board with the JR Kyushu Rail Pass Gift of tabi socks for customers J ⑩ Kokura Osaka shops of JR Hakata city visa may purchase the pass. -
Contact Information for the Core Organizations (Active)
City Area Program Contact Information for the Core Organizations <Active> Center for Joint Research(Regional Affirs Department), Hirosaki University Research and Development Promotion Team, New business support group, Saga Prefectural Regional Industry Support Center 1 Bunkyo-cho, Hirosaki City, Aomori 036-8560 JAPAN 114 Yaemizo, Nabeshima-machi, Saga City, Saga 849-0932 JAPAN ■ Hirosaki ■ Saga Ariake Sea Coastal TEL:+81-172-39-3911 FAX:+81-172-39-3919 TEL:+81-95-234-4413 FAX:+81-95-234-4412 Toyo Industrial Creative Center Tsukuba Center,Inc ■ Ehime Eastern 2151-10 Ohjyoin, Niihama City, Ehime 792-0060 JAPAN ■ Tsukuba Science City 2-1-6 Sengen, Tsukuba City, Ibaraki 305-0047 JAPAN TEL:+81-89-766-1111 FAX:+81-89-766-1112 TEL:+81-29-858-6000 FAX:+81-29-858-6014 Center for Regional Collaboration in Research and Education, Iwate University Shizuoka Organization for Creation of Industries ■ Central Iwate-Kamaishi 4-3-5 Ueda, Morioka City, Iwate 020-8551 JAPAN ■ Shizuoka Central Shizuokaken Sangyo Keizai Kaikan 4F, 44-1 Otemachi, Aoi-ku, Shizuoka City, Shizuoka 420-0853 JAPAN TEL:+81-19-621-6683 FAX:+81-19-621-6892 TEL:+81-54-254-4512 FAX:+81-54-251-3024 Industrial Creation Group, Niigata Industrial Creation Organization SCIENCE CREATE Co.,Ltd. Bandaijima Building 10F,5-1 Bandaijima, Niigata City, Niigata 950-0078 JAPAN 333-9 NishiMiyukicho, Aza Hamaike, Toyohashi City, Aichi 441-8113 JAPAN ■ Nagaoka ■ Toyohashi TEL:+81-25-246-0068 FAX:+81-25-246-0033 TEL:+81-53-244-1121 FAX:+81-53-247-2010 Shizuoka Organization for Creation of Industries - -
By Municipality) (As of March 31, 2020)
The fiber optic broadband service coverage rate in Japan as of March 2020 (by municipality) (As of March 31, 2020) Municipal Coverage rate of fiber optic Prefecture Municipality broadband service code for households (%) 11011 Hokkaido Chuo Ward, Sapporo City 100.00 11029 Hokkaido Kita Ward, Sapporo City 100.00 11037 Hokkaido Higashi Ward, Sapporo City 100.00 11045 Hokkaido Shiraishi Ward, Sapporo City 100.00 11053 Hokkaido Toyohira Ward, Sapporo City 100.00 11061 Hokkaido Minami Ward, Sapporo City 99.94 11070 Hokkaido Nishi Ward, Sapporo City 100.00 11088 Hokkaido Atsubetsu Ward, Sapporo City 100.00 11096 Hokkaido Teine Ward, Sapporo City 100.00 11100 Hokkaido Kiyota Ward, Sapporo City 100.00 12025 Hokkaido Hakodate City 99.62 12033 Hokkaido Otaru City 100.00 12041 Hokkaido Asahikawa City 99.96 12050 Hokkaido Muroran City 100.00 12068 Hokkaido Kushiro City 99.31 12076 Hokkaido Obihiro City 99.47 12084 Hokkaido Kitami City 98.84 12092 Hokkaido Yubari City 90.24 12106 Hokkaido Iwamizawa City 93.24 12114 Hokkaido Abashiri City 97.29 12122 Hokkaido Rumoi City 97.57 12131 Hokkaido Tomakomai City 100.00 12149 Hokkaido Wakkanai City 99.99 12157 Hokkaido Bibai City 97.86 12165 Hokkaido Ashibetsu City 91.41 12173 Hokkaido Ebetsu City 100.00 12181 Hokkaido Akabira City 97.97 12190 Hokkaido Monbetsu City 94.60 12203 Hokkaido Shibetsu City 90.22 12211 Hokkaido Nayoro City 95.76 12220 Hokkaido Mikasa City 97.08 12238 Hokkaido Nemuro City 100.00 12246 Hokkaido Chitose City 99.32 12254 Hokkaido Takikawa City 100.00 12262 Hokkaido Sunagawa City 99.13 -
Adire Cloth: Yoruba Art Textile
IROHIN Taking Africa to the Classroom SPRING 2001 A Publication of The Center for African Studies University of Florida IROHIN Taking Africa to the Classroom SPRING 2001 A Publication of The Center for African Studies University of Florida Editor/Outreach Director: Agnes Ngoma Leslie Layout & Design: Pei Li Li Assisted by Kylene Petrin 427 Grinter Hall P.O. Box 115560 Gainesville, FL. 32611 (352) 392-2183, Fax: (352) 392-2435 Web: http://nersp.nerdc.ufl.edu/~outreach/ Center for African Studies Outreach Program at the University of Florida The Center is partly funded under the federal Title VI of the higher education act as a National Resource Center on Africa. As one of the major Resource Centers, Florida’s is the only center located in the Southeastern United States. The Center directs, develops and coordinates interdisci- plinary instruction, research and outreach on Africa. The Outreach Program includes a variety of activities whose objective is to improve the teaching of Africa in schools from K-12, colleges, universities and the community. Below are some of the regular activities, which fall under the Outreach Program. Teachers’ Workshops. The Center offers in- service workshops for K-12 teachers on the teaching of Africa. Summer Institutes. Each summer, the Center holds teaching institutes for K-12 teachers. Part of the Center’s mission is to promote Publications. The Center publishes teaching African culture. In this regard, it invites resources including Irohin, which is distributed to artists such as Dolly Rathebe, from South teachers. In addition, the Center has also pub- Africa to perform and speak in schools and lished a monograph entitled Lesson Plans on communities.