HGR-B9023-Is01-Steel Rivets & Riveting
Total Page:16
File Type:pdf, Size:1020Kb
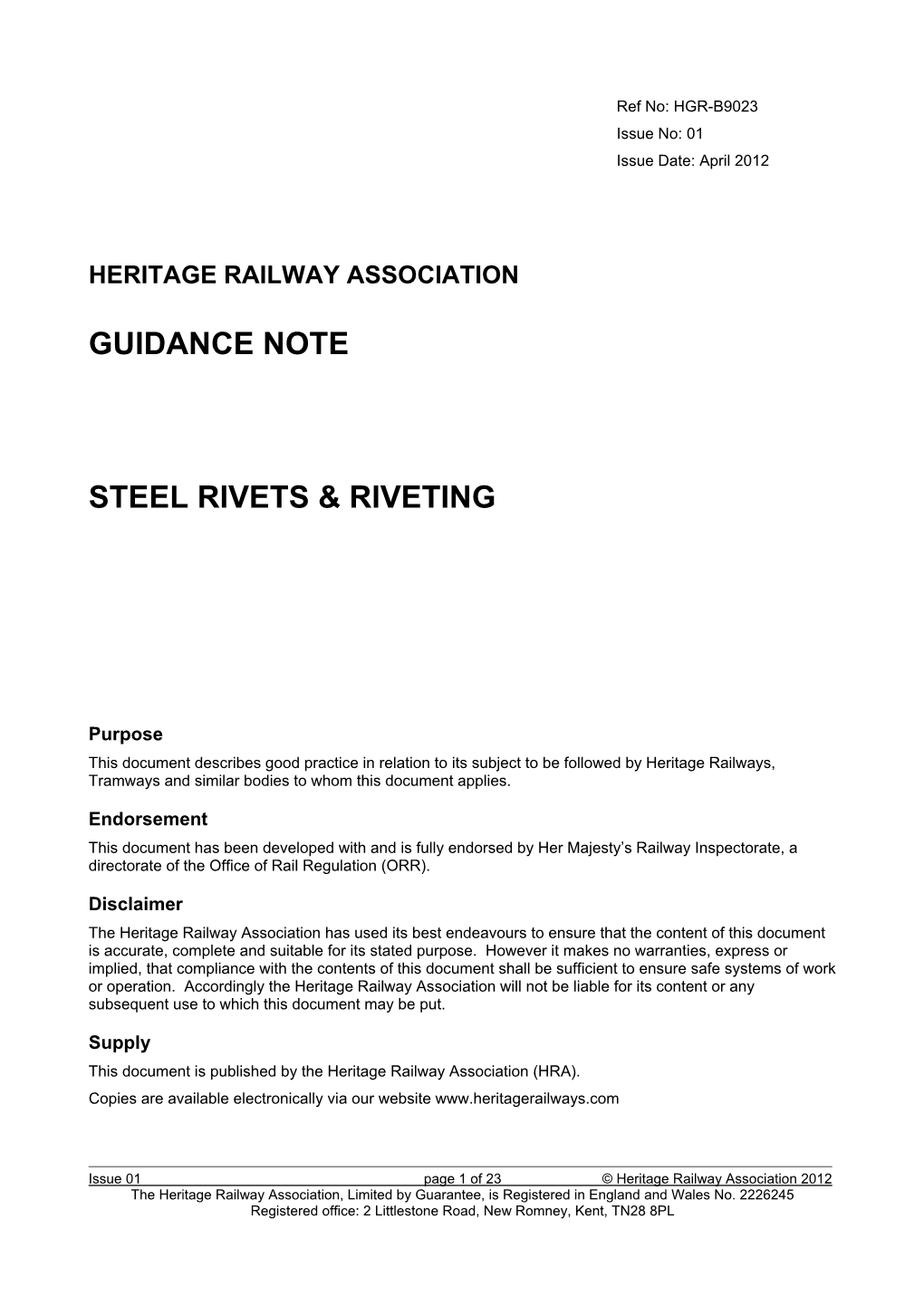
Load more
Recommended publications
-
Overview of Current Challenges in Self-Pierce Riveting of Lightweight Materials †
Proceedings Overview of Current Challenges in Self-Pierce Riveting of Lightweight Materials † Mathias Jäckel *, Thomas Grimm, Ronald Niegsch and Welf-Guntram Drossel Department Mechanical Joining of the Fraunhofer Institute for Machine Tools and Forming Technology IWU, Nöthnitzer Str. 44, 01187 Dresden, Germany; [email protected] (T.G.); [email protected] (R.N.); [email protected] (W.-G.D.) * Correspondence: [email protected] † Presented at the 18th International Conference on Experimental Mechanics, Brussels, Belgium, 1–5 July 2018. Published: 9 May 2018 Abstract: This paper shows an overview of different analyses regarding current challenges at self-pierce riveting with solid rivets as well as semi-tubular rivets of lightweight materials like aluminum die casting, carbon fiber reinforced plastic and 7xxx series aluminum alloy. The joining process analyses will demonstrate the cause and the development as well as the influence on joint quality of individual joining process-induced defects. In addition, methods are described how these imperfections can be avoided or reduced. Keywords: mechanical joining; lightweight materials; self-pierce riveting 1. Introduction The importance of environment friendly mobility strengthens the need of lightweight design in the automotive industry. Due to this need, lightweight materials such as aluminum and carbon fiber reinforced plastics (CFRP) are used more and more in automotive car body constructions. According to the limited weldability, joining these materials by mechanical joining techniques such as self-pierce riveting with solid (SPR-S) or semi-tubular rivets (SRP-ST) has been established. The challenge in this regard is that these materials have limited forming capacities (e.g., aluminum die casting, CFRP) or vulnerability regarding stress corrosion cracking (e.g., 7xxx series aluminum alloy), while the joining processes locally induce large plastic deformations and tensile stresses. -
Rafael A. Barrantes QAS 515 Human Factors Pneumatic Rivet Gun Exchange Program on the C-17 Program November 29, 2005
Rafael A. Barrantes QAS 515 Human Factors Pneumatic Rivet Gun Exchange Program on the C-17 Program November 29, 2005 History Charles Brady King of Detroit invented the pneumatic hammer in 1890. In the late 1800’s and early 1900’s the rivet guns where were used in the rail road industry. The guns were used on small rivets on locomotives as well as swaging and sealing boiler tubes. The guns were also used for breaking old welds in thin steel. The first successful all metal airplane was built in 1915 in Germany by Junkers. The first American metal airplane to be produced in large numbers was the Ford Tri-Motor. The planes were built from 1926 thru 1933. With the advent of the metal plane, rivets were used as the primary fastener to bond skins to primary structure. Process Description Riveting is a two person task. One person is typically inside the aircraft and the other outside. The workers switch between riveting and holding a bucking bar behind the rivet. Workers communicate verbally with or without radio head sets. Workers drive approximately 400-600 rivets per day. The holes to be riveted are drilled out then reamed out to final hole size with a hand drill. The rivets are then placed in the open hole. The bucking bar is positioned behind the rivet by one worker and the rivet gun is held at the head of the rivet by the other worker. The rivet gun operator then squeezes the trigger in several short bursts to drive the rivet into place. -
Construction Manual, Which, Together with a Complete Set of Drawings Will Help You to Accomplish This Wonderful Feat: to Build and Fly Your Own Two-Seat Aircraft
FOREWORD Dear Builder: Congratulations on your decision to build a Zenith aircraft. Here is the construction manual, which, together with a complete set of drawings will help you to accomplish this wonderful feat: to build and fly your own two-seat aircraft. The first part of the manual deals with some of the tools required for this project and the procedure with which to use them efficiently. Materials and hardware are also presented as well as tips on workmanship, corrosion protection and tolerances. The second part is a progressive step-by-step construction guide; beginning with the rudder assembly, it describes every aspect of airframe construction. The last part of this manual is a “weight and balance form”. The drawings and manual have been laid out to allow the average builder to understand them without having to write or call the designer or factory. They are not "perfect" or in color but supply all the information required completing your aircraft to the design specifications. It is important to remember that builders have used the proposed building sequence successfully for over two decades. It would therefore be wise to use this experience and stick to the sequence. The secret of good progress is not to work like crazy in sudden short-lived spurts; it lies in steady and continuous effort. Homebuilding your aircraft is a tremendously rewarding hobby. You are the one with enough courage to do what others only dream of. Homebuilding is a useful, educational and recreational activity. While learning, you will enjoy building, and then flying... and you are contributing to the progress of aviation. -
Metabo Introduces the 18V Brushless Rivet
Contact: Andrea Brogan Metabo Corp. Phone: (610) 436-5900 1231 Wilson Dr. Fax: (610) 436-9072 West Chester, PA 19380 [email protected] www.metabousa.com PRESS RELEASE Metabo introduces the 18V Brushless Blind Rivet Gun Compact, powerful and ergonomic solution for riveting July 2018 – West Chester, PA - Metabo Corporation, a leading international manufacturer of industrial grade cordless and corded power tools and accessories, introduces the 18V Brushless Blind Rivet Gun. The 18V Brushless Blind Rivet Gun (NP 18 LTX BL 5.0) is perfect for securing steel/stainless steel or aluminum in place. It can rivet up to 3/16” in steel and ¼” in aluminum. And with a compact 4.0 Ah LiHD (Lithium High Density) battery, it can secure 2,000 3/16” rivets on a single charge and has a pulling force of 2,250 lbs. “Metabo has thought of everything when creating this cordless tool. It is not only as fast as an air tool but is a problem solver on many levels. Metabo revolutionizes the sheet metal assembly process by making it cordless,” says Antoine Derché, Metabo’s Director of Product and Marketing. This one-handed rivet gun is extremely fast, lightweight and balanced for maximized ergonomics. It includes safety features, such as; hand protection guard, balancing loop, integrated nose piece storage and a LED light for illumining work. It also has a transparent container attached to the back for convenient storage of pins that doubles as a tool for quick changing nose pieces. The 18V Brushless Blind Cordless Rivet Gun, when combined with the Metabo 18V High-speed Drill (BE 18 LTX 6) creates a powerful duo for all your riveting needs! The 18V High-speed Drill has a no-load speed of 4,000 rpm, 35 inch lbs. -
ASTM-B-211 Aluminum
This international standard was developed in accordance with internationally recognized principles on standardization established in the Decision on Principles for the Development of International Standards, Guides and Recommendations issued by the World Trade Organization Technical Barriers to Trade (TBT) Committee. Designation: B211/B211M − 19 Standard Specification for Aluminum and Aluminum-Alloy Rolled or Cold Finished Bar, Rod, and Wire1 This standard is issued under the fixed designation B211/B211M; the number immediately following the designation indicates the year of original adoption or, in the case of revision, the year of last revision. A number in parentheses indicates the year of last reapproval. A superscript epsilon (´) indicates an editorial change since the last revision or reapproval. This standard has been approved for use by agencies of the U.S. Department of Defense. 1. Scope* 2.2 ASTM Standards:3 B221 Specification for Aluminum and Aluminum-Alloy Ex- 1.1 This specification2 covers rolled or cold-finished bar, truded Bars, Rods, Wire, Profiles, and Tubes rod, and wire in alloys (Note 1) and tempers as shown in Table B221M Specification for Aluminum and Aluminum-Alloy 2 [Table 3]. Extruded Bars, Rods, Wire, Profiles, and Tubes (Metric) NOTE 1—Throughout this specification use of the term alloy in the B316/B316M Specification for Aluminum and Aluminum- general sense includes aluminum as well as aluminum alloy. Alloy Rivet and Cold-Heading Wire and Rods NOTE 2—The term cold finished is used to indicate the type of surface B557 Test Methods for Tension Testing Wrought and Cast finish, sharpness of angles, and dimensional tolerances produced by Aluminum- and Magnesium-Alloy Products drawing through a die. -
Hand Tools 8 21 12 Paginated.Fm
280 Pearlgreen Corporation Tools, Hand The Industrial Supply Group Gooseneck Crow Bar STANLEY TOOLS Phillips Bit Wonder Bar 2” Length • S-2 tool steel • Rockwell Hardness 60-64 • Length: 2 in. Contoured bar. Ideal for pulling nails, prying, lifting, scraping. Bevelled nail slot both ends. 4 per box., Width: 1 3/8 in., Length: 12 1/2 in. Mfg. No. Size PG No. 45008 #1 BIT-PX1 Mfg. No. PG No. 45010 #2 BIT-PX2 55-515 ST55-515 45012 #3 BIT-PX3 Fully painted black gooseneck wrecking bar. Used to open crates and boxes. STANLEY TOOLS Slotted Bit Nail Puller Handle Diameter Length Mfg. No. (in.) (in.) PG No. MM2332 ¹⁄₂ 12 BAR-12 • S-2 tool steel MM2342 ⁵⁄₈ 18 BAR-18 • Rockwell Hardness 60-64 ³⁄₄ MM2352 24 BAR-24 • Length: 1 in. MM2362 ³⁄₄ 30 BAR-30 • Double end puller features 90 deg. and 30 deg. offset claws MM2372 ³⁄₄ 36 BAR-36 • Fully sharpened claw tips Mfg. No. Size PG No. Stripping Bar • Size: 5/8 in. 45020 #6 - 8 BIT-S06 • Overall Length: 11 in. 45022 #8 - 10 BIT-S08 45024 #10 - 12 BIT-S10 Mfg. No. PG No. Spanner Bit 55-035 ST55-035 48 in. Stripping Bar with Claw Philips Bit Mfg. No. PG No. 1168800 BAR-48 Security Bit, Fits all power and hand held bit drives, various sizes Straight Crow Bar • S-2 tool steel • Rockwell Hardness 60-64 Mfg. No. Size (in.) PG No. • Length: 1 in. 1916 #6 SPANNER-B06 1918 #8 SPANNER-B08 1920 #10 SPANNER-B10 Mfg. No. Size PG No. -
Blind Rivet Nuts Blind Rivet Nuts Easily Adaptable for Your Materials and Production Processes
Blind Rivet Nuts Blind Rivet Nuts Easily adaptable for your materials and production processes. Performance Fasteners For Versatile Assembly Everywhere that you need to join components reliably and efficiently the POP Avdel product range offers innovative fastening systems and the most suitable installation tools and assembly stations. Wherever you need high quality, load bearing threads in thin materials, POP Avdel Blind Rivet Nut Systems offer the ideal solution. Installation Quickly and reliably installed without rework or damage to the parent application, even with painted sheet materials and tubes where there is no blind side access. Applications Our blind rivet nuts are most commonly used in the automotive, vehicle, electronics chassis manufacturing, equipment manufacturing and shipbuilding industries. The wide variety of POP Avdel blind rivet nuts provides perfect engineering results and economic solutions in every application. Mission STANLEY Engineered Fastening provides assembly systems that simplify your production process and improve the quality of your products. We are not just a provider of fasteners and equipment, together we are a design and development partner for our customers engineering teams. - 2 - stanleyengineeredfastening.com Table of Contents Systems Range Overview Blind Rivet Nuts 4 Benefits of Assembly 5 Design Features and Benefits 6 Customised Designs 7 Design Parameters 8 Selecting a Blind Rivet Nut 9 Selection Guide 10-12 The Range of POP Avdel Eurosert® 13 Blind Rivet Nuts Nutsert® 14 Hexsert®/Euro Hexsert® -
View Our Welding Kit Catalog
PARTSMASTER WILL KEEP YOU RUNNING MILITARY CATALOG MILITARY OPERATIONS DEPLOYMENT READY SOLUTIONS • Partsmaster sells to the Army, Navy, Air Force, Marines, and National Guard. • Partsmaster military solutions are created by veterans. • Partsmaster hires experienced veterans to help grow the expanding military business. Rob Ramsey Stan Blitz Director of Military Accounts Army Account Manager Chief Warrant Officer 4, Retired Chief Warrant Officer 3, Retired US Army US Army Ray Larry Channel Manager Sergeant First Class, Retired US Army PARTSMASTER MAINTENANCE REPAIR OPERATING SUPPLY Partsmaster is a specialty MRO (Maintenance, Repair and Operating Supply) company dedicated to making our customers’ work easier. Our superior products are developed with a focus on increased productivity, asset longevity, safer user experience, and environmental responsibility. Partsmaster sells industrial maintenance supplies for welding, concrete repairs, specialty abrasives, fasteners and hardware, hand tools and cutting tools. Partsmaster was established in 1968 as a division of NCH Corporation, a global leader in industrial and commercial maintenance products and services since 1919. NCH has over 8,000 employees, with offices and manufacturing plants located on five continents. NCH is relied upon by companies in over 50 countries to solve maintenance problems with the most innovative and effective products and services. NCH GLOBAL NORTH AMERICA EUROPE COVERAGE 2 COUNTRIES 26 COUNTRIES 1,133 SALES ASSOCIATES 2,134 SALES ASSOCIATES • Founded in 1919 • Family -
Magnesium Casting Technology for Structural Applications
Available online at www.sciencedirect.com Journal of Magnesium and Alloys 1 (2013) 2e22 www.elsevier.com/journals/journal-of-magnesium-and-alloys/2213-9567 Full length article Magnesium casting technology for structural applications Alan A. Luo a,b,* a Department of Materials Science and Engineering, The Ohio State University, Columbus, OH, USA b Department of Integrated Systems Engineering, The Ohio State University, Columbus, OH, USA Abstract This paper summarizes the melting and casting processes for magnesium alloys. It also reviews the historical development of magnesium castings and their structural uses in the western world since 1921 when Dow began producing magnesium pistons. Magnesium casting technology was well developed during and after World War II, both in gravity sand and permanent mold casting as well as high-pressure die casting, for aerospace, defense and automotive applications. In the last 20 years, most of the development has been focused on thin-wall die casting ap- plications in the automotive industry, taking advantages of the excellent castability of modern magnesium alloys. Recently, the continued expansion of magnesium casting applications into automotive, defense, aerospace, electronics and power tools has led to the diversification of casting processes into vacuum die casting, low-pressure die casting, squeeze casting, lost foam casting, ablation casting as well as semi-solid casting. This paper will also review the historical, current and potential structural use of magnesium with a focus on automotive applications. The technical challenges of magnesium structural applications are also discussed. Increasing worldwide energy demand, environment protection and government regulations will stimulate more applications of lightweight magnesium castings in the next few decades. -
Roof Side Rail Supercrew
3/23/2021 2021 F-150 501-28 Roof Sheet Metal Repairs 2021 F-150 Removal and Installation Procedure revision date: 10/8/2020 Roof Side Rail - SuperCrew Special Tool(s) / General Equipment 6.5 mm Drill Bit Polydrive Bit Socket Self-Piercing Rivet (SPR) Remover/Installer Belt Sander Blind Rivet Gun Hot Air Gun Locking Pliers Materials Name Specification Metal Bonding Adhesive - TA-1, TA-1-B, 3M™ 08115, LORD Fusor® 108B Seam Sealer - TA-2-B, 3M™ 08308, LORD Fusor® 803DTM Removal WARNING: Electric vehicles damaged by a crash may have compromised high voltage safety systems and present a potential high voltage electrical shock hazard. Exercise caution and wear appropriate Personal Protective Equipment (PPE) safety gear, including high voltage safety gloves and boots. Remove all metallic jewelry, including watches and rings. Isolate the HV system as directed by the Ford Emergency Response Guide for the vehicle. Failure to follow these instructions may result in serious personal injury or death. NOTICE: Battery electric vehicle (BEV), hybrid electric vehicle (HEV) and plug-in hybrid electric vehicle (PHEV) contain a high-voltage battery. Before cutting or welding near the high-voltage battery it must be removed to avoid damage. 1. WARNING: Before beginning any service procedure in this manual, refer to health and safety warnings in section 100-00 General Information. Failure to follow this instruction may result in serious personal injury. Refer to: Health and Safety Precautions (100-00 General Information, Description and Operation). Refer to: High Voltage System Health and Safety Precautions - Overview (100-00 General Information, Description and Operation). -
Alloys for Pressure Die Casting RHEINFELDEN ALLOYS
Primary Aluminium Alloys for Pressure Die Casting RHEINFELDEN ALLOYS Table of contents RHEINFELDEN ALLOYS – Aluminium Alloys for Pressure Die Casting General 2 ALUMINIUM RHEINFELDEN group 3 RHEINFELDEN FAST ALLOYS 4 Forms of delivery 5 Customer support and research and development 6 – 7 Aluminium casting alloys by RHEINFELDEN ALLOYS 8 – 9 Profile of the alloys for the die casters 10 Publications Alloys 11 – 20 Castasil ®-37 – AlSi9MnMoZr 21 – 24 Castasil ®-21 – AlSi9Sr 25 – 36 Silafont ®-36 – AlSi10MnMg 37 – 38 Silafont ®-38 – AlSi9MnMgZn 39 – 40 Castaman ®-35 – AlSi10MnMg 41 – 42 Thermodur ®-72/-73 – AlMg7Si3Mn – AlSi11Cu2Ni2Mg2Mn 43 – 53 Magsimal ®-59 – AlMg5Si2Mn Processing datasheets 54 Technical informations / Processing datasheets 55 Castasil ®-37 56 Castasil ®-21 57 Silafont ®-36 58 Silafont ®-38 59 Thermodur ®-72 60 Magsimal ®-59 Technical information 61 – 62 Surface coating 63 Joining techniques for die castings 64 Eight target levels for HPDC 65 Disclaimer and imprint 1 ALUMINIUM RHEINFELDEN group “Progress by tradition” Our policy ALUMINIUM RHEINFELDEN group: This history of aluminium Our RHEINFELDEN ALLOYS GmbH & Co. KG innovative char- in Germany started at Rheinfelden. In 1898 Europe’s first acter is what allows us to adapt rapidly to fast changing market river power station brought about the establishment of the first needs. The agility of a private family owned operated company, aluminium smelter in Germany, at Rheinfelden, Baden. the central geographic location in the European cast metal The company has always operated in three business segments market, the know-how and experience of our team, are factors and in October 2008 restructuring turned ALUMINIUM making a difference for Customers looking for reliable tradition RHEINFELDEN GmbH into a holding company and the former and modern innovation. -
Hydraulic Tools Riveting Machines
EN 2.004.0 / 02.19 Riveting Machines Riveting Hydraulic Tools EN 2.004.0 / 02.19 Your partner for expertise in components, complete systems and service With more than 9,000 employees, 48 subsidiaries and over 500 sales and service partners worldwide, we are in close contact with our customers, HYDAC SERVICENTER providing engineering advice, production, installation and service. Robust, durable and extremely versatile Riveting can be used to join various materials. This method can be used regardless of the chemical composition or any previous surface treatment of the parts that are to be joined. It is also possible to join more than two components. A rivet connection is a permanent connection, so the connected parts can only be separated by destroying the rivet. The rivet is the simplest and the cheapest connection element. A rivet connection is a permanent bond and can be created without sparks or vapours being generated, unlike a weld, for example. Complete systems and individual components Our service portfolio includes extensive consultation, calculation, modelling, design and construction for all types of mobile and stationary hydraulic systems for cold- and hot-riveting. The range of services that we provide also includes commissioning on the customer’s premises and comprehensive after-sales and spare part support. Production Design LIFE CYCLE MANAGEMENT Engineering Services 02.19 / EN 2.004.0 2 Mobile riveting machines The diverse range of applications for mobile riveting machines covers: l Lorry frame construction l Wagon construction l Pylons l Bridge building and similar applications. Our mobile riveting machines are particularly useful for complex geometries and hard-to-access areas.