Engineering Design, Fabrication, and Erection of Prefabricated Bridge Elements and Systems
Total Page:16
File Type:pdf, Size:1020Kb
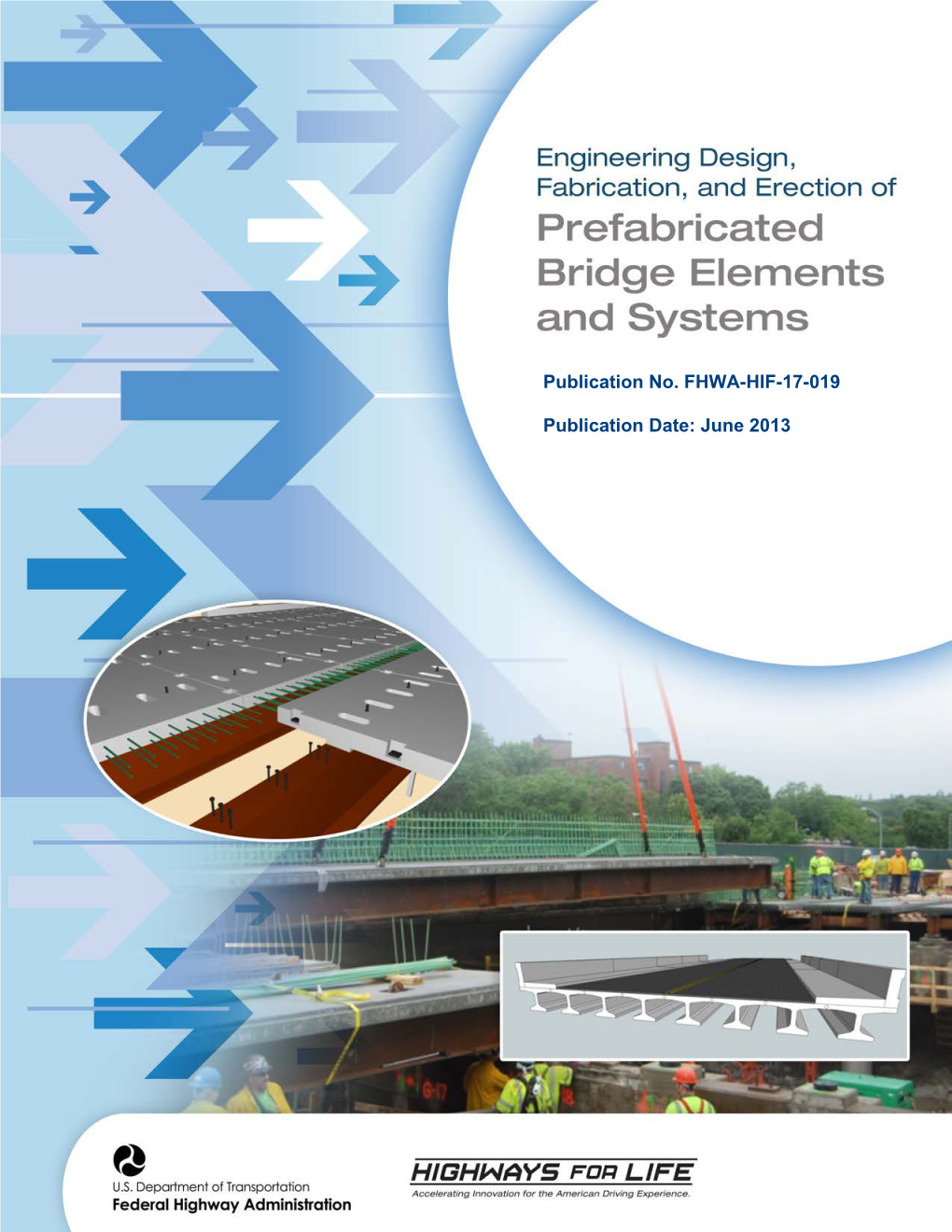
Load more
Recommended publications
-
A Comprehensive Stochastic Design Methodology for Hold-Timing Resiliency in Voltage-Scalable Design
2118 IEEE TRANSACTIONS ON VERY LARGE SCALE INTEGRATION (VLSI) SYSTEMS, VOL. 26, NO. 10, OCTOBER 2018 A Comprehensive Stochastic Design Methodology for Hold-Timing Resiliency in Voltage-Scalable Design Zhengyu Chen , Student Member, IEEE, Huanyu Wang, Student Member, IEEE, Geng Xie, Student Member, IEEE,andJieGu , Member, IEEE Abstract— In order to fulfill different demands between challenges due to the conflicting requirements between low ultralow energy consumption and high performance, integrated power consumption and high performance. To achieve low circuits are being designed to operate across a large range of power consumption, supply voltage V is typically reduced to supply voltages, in which resiliency to timing violation is the DD key requirement. Unfortunately, traditional timing analysis which near-threshold voltages, e.g., around 0.5 V. At such a voltage, focuses on setup timing tolerance for higher performance cannot stochastic variation associated with transistor threshold volt- model the hold violation efficiently across different voltages. ages becomes a major factor in determining logic timing which In this paper, we proposed a complete flow of computationally makes timing analysis extremely time consuming [1]. Conven- efficient methodology for guaranteeing hold margin, which is tional solution which introduces extra timing margin to avoid particularly important for low-power devices, e.g., Internet-of- Things devices. Leveraging both the conventional static timing timing violation at low-voltage region leads to performance analysis and a most probable point (MPP) theory, we develop a degradation at high-voltage region. In addition, the inefficiency new hold-timing closure methodology across voltages eliminating of conventional static timing analysis (STA) cannot meet the expensive Monte Carlo simulation. -
Overcoming the Challenges in Very Deep Submicron for Area Reduction, Power Reduction and Faster Design Closure
Overcoming the Challenges in Very Deep Submicron for area reduction, power reduction and faster design closure A THESIS SUBMITTED IN PARTIAL FULFILLMENT OF THE REQUIREMENTS FOR THE DEGREE OF Master of Technology in VLSI Design and Embedded System By K. RAKESH Roll No: 20507010 Department of Electronics and Communication Engineering National Institute Of Technology Rourkela 2007 Overcoming the Challenges in Very Deep Submicron for area reduction, power reduction and faster design closure A THESIS SUBMITTED IN PARTIAL FULFILLMENT OF THE REQUIREMENTS FOR THE DEGREE OF Master of Technology in VLSI Design and Embedded System By K. RAKESH Roll No: 20507010 Under the Guidance of Prof. K. K. MAHAPATRA Department of Electronics and Communication Engineering National Institute Of Technology Rourkela 2007 National Institute of Technology Rourkela CERTIFICATE This is to certify that the thesis entitled, “Overcoming the Challenges in Very Deep Submicron for area reduction, power reduction and faster design closure” submitted by Mr. Koyyalamudi Rakesh (20507010) in partial fulfillment of the requirements for the award of Master of Technology Degree in Electronics & Communication Engineering with specialization in “VLSI Design & Embedded System” at the National Institute of Technology, Rourkela (Deemed University) is an authentic work carried out by him under my supervision and guidance. To the best of my knowledge, the matter embodied in the thesis has not been submitted to any other University / Institute for the award of any Degree or Diploma. Prof. K.K. Mahapatra Dept. of Electronics & Communication Engg. Date: National Institute of Technology Rourkela-769008 ACKNOWLEDGEMENTS This project is by far the most significant accomplishment in my life and it would be impossible without people who supported me and believed in me. -
Guide to Natural Gas/Oil Regulations & Development Projects in Mesa
Guide to Natural Gas/Oil Regulations & Development Projects in Mesa County I. Purpose This document is a guide to the Mesa County Land Development Code, as amended (Code), adopted plans and policies, and County permitting agencies related to natural gas and oil development. This guide categorizes typical natural gas/oil development activities pursued in Mesa County and maps them to the appropriate land uses defined by the Code as well as outlines the level of review required. This is an overview, and the specific and required regulations are contained in the Code that are identified in the Guide. The Code and additional information on natural gas/oil development can be found at the Mesa County Website: http://www.mesacounty.us/planning/ II. Land Uses & Where they are permitted in Mesa County All land in Mesa County is zoned, and certain uses are allowed to occur in each zoning district subject to Land Use Table 5.1. The Table details the land uses allowed in each zoning district and the review process applicable to each use. Note: if a use is not listed in these matrices, it is prohibited. If the land use has an “A” in the zoning district column, it is an Allowed use and requires Site Plan review. If the land use has a “C” in the zoning district column, it is a Conditional Use and requires a Conditional Use application. These uses, as applicable to the natural gas/oil industry, are summarized in the table on Page 3 of this Guide. The majority of natural gas/oil activity currently occurs in the AFT zoning district. -
Design Closure: Power Constraints, Best Practices for an Accurate Report Power Estimation
Design Closure: Power Constraints, best practices for an accurate Report Power estimation Feb 2021 © Copyright 2021 Xilinx Design Closure Sessions Session 1 Methodology, tips, and tricks for achieving better Quality-of-Results Session 2 Using Timing Closure Assistance tools to address tough timing issues Session 3 Power Constraints, best practices for an accurate Report Power estimation 2 © Copyright 2021 Xilinx Agenda Power impact and Time to Market Design Closure an efficient approach Understanding design power Design Power Constraints Vivado Commands 3 © Copyright 2021 Xilinx Power impact and Time to Market © Copyright 2021 Xilinx Why is Power Closure so important? Board Design is Fixed Power and Thermal Issues take a long time to correct Design Changes (Typically Weeks) Re-Run P&R HDL Changes Reducing design specifications Hardware changes (Typically Months) Board Re-spin Power Delivery Changes Thermal Solution Changes 5 © Copyright 2021 Xilinx Power / Thermal / Board Design Methodology Power Estimation Thermal Design Define Power Delivery If power cannot be reduced, Thermal and Define / Simulate PDN Board Design needs to be redone Define Board / Sch Checklist (very time consuming) Constrain Vivado Modify Run report_power Design DISSECTION No Designed within • What went well? Budget? • Lessons learned? Yes Converge and ensure all original assumption/ design constraints are met SUCCESS 6 © Copyright 2021 Xilinx Design Closure an efficient approach © Copyright 2021 Xilinx Design closure – combining Timing and Power More efficient, -
Californication Biography Song List What We Play
Californication Biography about us Established in early 2004, Californication the all new Red Hot Chili Peppers Show, aims to deliver Australia’s tribute to one of the world’s most popular and distinguishable bands: the Red Hot Chili Peppers. Californication recreates an authentic and live experience that is, the Red Hot Chili Peppers. The Chili Peppers themselves first came to prominence 20 years ago by fusing funk, rock and rap music styles through their many groundbreaking albums. A typical 90 minute show performed by Californication includes all the big hits and smash anthems that have made the Chili Peppers such an enduring global act. From their breakthrough cover of Stevie Wonder’s Higher Ground to the multiplatinum singles Give it Away, Under the Bridge and Breaking the Girl; as well as Aeroplane, Scar Tissue, Otherside and Californication; fans of the Chili Peppers’ music will never walk away disappointed. Fronted by Johnny, the vocalist of the Red Hot Chili Peppers Show captures all the stage antics and high energy required to emulate Anthony Kiedis, while the rest of the band carry out the very essence of the Red Hot Chili Peppers through the attention of musical detail and a stunning visual performance worthy of the famous LAbased quartet. And now, exclusively supported by the exciting, upcoming party band Big Way Out, you can be guaranteed an enjoyable night’s worth of entertainment. Be prepared to experience Californication the Red Hot Chili Peppers Show. Coming soon to a venue near you! Song List what we play Mothers -
NOT for Printing
New York City Transit ADC60 Waste Management and Resource Efficiency in Transportation SUMMER CONFERENCE IN NEW YORK CITY JULY 13—JULY 15, 2009 2 Broadway, New York Monday July 13, 2009 Tuesday July 14, 2009 Wednesday July 15, 2009 8:30AM – Registration and Breakfast 8:30AM Registration and Breakfast 8:30AM Registration and Breakfast 9:00AM – Welcome/Opening Session 8:45AM Hazardous Materials Investigation/Remediation – 8:45AM Environmental Focus 1 PDH, .1 CM Thomas Abdallah, PE, LEED AP, NYCT Panel Discussion 1 PDH, .1 CM 1. US EPA EPA Region 2 Transportation and Construction Initia- Ernest Tollerson, MTA 1. The Triad Approach: Theory, Practice, and Expectations, Joel tive, Charles Harewood, EPA Collette Ericsson, PE, LEED AP, MTA Regional Bus S. Hayworth, PhD, PE, Hayworth Engineering 2. Hot LEED Topics, Lauren Yarmuth, LEED AP, YRG Ed Wallingford, Committee Chair TRB ADC-60 2. A TRIAD investigation combining Electrical Resistivity Imaging 3. Storm water Retrofitting to Restore Ecosystems, Ted Brown, 9:30AM Sustainability Initiatives 1PDH, .1 CM (ERI), Soil Conductivity/Membrane Interface Probe (SC/MIP), P.E., LEED AP 1. Assessing Green Building Performance, Thomas Burke, PE, Todd R. Kincaid, Ph.D., Kevin Day, P.G., Roger Lamb, P.G., 4. Western Railyards Air Quality, Helen Ginzburg &Tammy Pet- LEED AP, U.S. GSA H2H Associates sios, PB 2. Climate Change and the Port Authority, Chris Zeppie, Chrstine 3. Geologic Framework Modeling for Large Construction Projects, 10:15AM Environmental Engineering Around the World Wedig, PANYNJ Christine Vilardi, PG, CGWP, STV, Inc. 1PDH, .1 CM 3. The High-Line: Conversion of an Abandoned Railway to an Additional Panel Members 1. -
SEMICONDUCTOR COLLABORATIVE DESIGN PROCESS Enable Collaborative Design for Complex Semiconductor Projects
HIGH PERFORMANCE SEMICONDUCTOR INDUSTRY SOLUTION EXPERIENCE SEMICONDUCTOR DESIGN DATA MANAGEMENT HIGH PERFORMANCE SEMICONDUCTOR INDUSTRY SOLUTION EXPERIENCE Achieve higher efficiency and zero re-spins in developing IoT-ready systems-on-chip Project & Portfolio Requirement, Issue, Defect & Management Traceability & Change Advancements in integrated circuit (IC) density and competition for market leadership drive demand for more complex devices from semiconductor Test Management manufacturers. To compete successfully, manufacturers must use teams of diverse design specialists and complex project workflows to maximize device differentiation and team productivity. As a result, IC projects carry increasing business risk. Dassault Systèmes' High Performance Semiconductor Industry Solution Experience powered by the 3DEXPERIENCE® platform provides a portfolio of IC design and engineering performance enhancements that help mitigate project risk, shorten time-to-market, and increase product quality and yield. High Performance Semiconductor provides these benefits through: IP Management Design Data Verification Management & Validation • Efficient intellectual property (IP) management and reuse • Graphical analytics to manage design closure • Instant access to the latest design data for all design teams • End-to-end traceability, from requirements to verification and validation • Packaging reliability simulation and testing • Enhanced product variation and defect management Manufacturing Packaging Manufacturing With this solution portfolio, semiconductor -
PREFABRICATION: the CHANGING FACE of ENGINEERING and CONSTRUCTION 2017 FMI/Bimforum Prefabrication Survey Table of Contents
PREFABRICATION: THE CHANGING FACE OF ENGINEERING AND CONSTRUCTION 2017 FMI/BIMForum Prefabrication Survey Table of Contents 1 3 25 29 Executive Summary Key Findings Business Implications Looking Ahead TODAY’S PREFAB ENVIRONMENT IS DIFFERENT 77% of respondents think today’s prefab The amount of project work using prefab has environment is different than in 2013. almost tripled between 2010 and 2016. 35% 13% YES NO 77% 23% 2010 2016 Most contractors perform single-trade Project inefficiencies and improved technologies prefabrication. are driving prefabrication. 32% 47% 21% Provide Provide Provide Multitrade Single-Trade Kitting Prefabrication Prefabrication Services THE BIG STRUGGLE TO MAKE IT WORK Contractors struggle to make Contractors using prefab on more than 50% prefabrication effective. of their projects are more effective compared to those who do less prefab. 14% 40% 46% Effective Needs Not Improvement Effective Three key challenges for making prefabrication 48% of respondents see less than 5% in effective: savings on total annual labor hours related to prefabrication. Culture Lack of Outdated Commitment Control Mindset he construction industry is back on track since the Great Recession, andT total construction employment has re- bounded to almost 6.7 million workers (still a far cry from its peak of 8 million workers in 2006). “Construction spending in November 2016 hit a 10-year high, with one-month and year-over-year increases in all major segments,” says Ken Simonson, chief economist at Associ- ated General Contractors of America. “Looking ahead, contractors say they expect more work in every category in 2017 than in 2016.” Executive Summary However, despite being about 16% below its 2006 employment peak, the industry is still struggling to find qualified labor. -
Cosmic Closet Lishments; for the Most Part, They Are Run by Very Nice People Who Are Trying to Give Club & Streetwear for Girls This Music an Outlet
' . Fugazi-Red Medicine "This CD is $8, postpaid." This quote can be found at the bot- boys from D.C. haven't lost the Fugazi ferocity, but it is a bit differ- tom of every one ofFugazi's last five releases, including their latest, ent. Red Medicine. Not much has changed for these messiahs of the in die The vocal tracks seem to be split about evenly between ex-Minor world. All their concerts are still five dollars, and they are still with Threat singer, Ian Mackaye, and Guy Picciotto. Mackaye sings on Dischord Records. Where most bands have managed to catapult "Back to Base," which is probably the most up-to-speed song on the themselves into the big money-making arena, Fugazi manages to album. He opens with ~ distinctive borderline yell, "Autonomy is a do just fine looking out from below. world of difference/ they're creeping around but they know they Red Medicine is undoubtedly Fugazi's most experimental al- can't-come in." bum to-date. But what about old Fugazi? I thought the same thing, The album is filled with a lot of moments with great musical but thinking about it, I realized that being diverse and reinventive value and then some. Highlights include, "Birthday Pony," the in- is a very good thing. Would you want to play the same· kind of.stuff strumental "Combination Lock" and the energetic "Downed City." over and over again? In the album opener, "Do you like me?" the Their tempo has slowed and their concentration on playing good intro sounds like someone is dropping his guitar, setting anticipa- music has intensified. -
A Review of Modular Construction Shipbuilding in Malaysian Shipyard
Proceeding of Ocean, Mechanical and Aerospace November 7, 2016 -Science and Engineering-, Vol.3 A Review of Modular Construction Shipbuilding in Malaysian Shipyard Ahmad Alliff Anuar Mokhtar ,a, Mohamad Abu Ubaidah Amir Bin Abu Zarim, Kdr Halim bin Abdul Aziz TLDM (Bersara) * and Ainnur Hafizah Anuar Mokhtar ,b a) Faculty of Science and Defence Technology, National Defence University, Malaysia, Kem Perdana Sungai Besi, 57000 Kuala Lumpur, Malaysia. b) Faculty of Computing and Informatics, Universiti Malaysia Sabah, 87000 F.T. Labuan, Malaysia *Corresponding author: [email protected], [email protected], [email protected], [email protected] Paper History 1.0 INTRODUCTION Received: 25-September-2016 The maritime industry consumes a role play in associate for Received in revised form: 30-October-2016 Malaysia’s economic development . This is regard to the statement Accepted: 7-November-2016 which shipbuilding/ ship repair (SBSR) industry has been precisely recognized in the Third Industrial Master Plan (IMP3) in place of an industry that can gives something to the country’s wealth from the transportation area [1]. The shipbuilding industry ABSTRACT of Malaysia is getting larger and ship builders are adapting with the latest technology. For each project to achieve successfully, it The shipbuilding and ship repair industry in Malaysia comprises is important to manage a project within the constraint. The major of designing, building and assembling, repairing and maintaining, constraint that should be considered is cost, duration time to transforming and advancement of vessels as well as marine complete the project, safety aspect for workers and the quality of equipment . It is getting larger and always evolve in line with the the project. -
Design for Manufacturing (Dfm) in Submicron Vlsi Design
DESIGN FOR MANUFACTURING (DFM) IN SUBMICRON VLSI DESIGN A Dissertation by KE CAO Submitted to the Office of Graduate Studies of Texas A&M University in partial fulfillment of the requirements for the degree of DOCTOR OF PHILOSOPHY August 2007 Major Subject: Computer Engineering DESIGN FOR MANUFACTURING (DFM) IN SUBMICRON VLSI DESIGN A Dissertation by KE CAO Submitted to the Office of Graduate Studies of Texas A&M University in partial fulfillment of the requirements for the degree of DOCTOR OF PHILOSOPHY Approved by: Chair of Committee, Jiang Hu Committee Members, Weiping Shi Duncan Walker Vivek Sarin Head of Department, Costas N. Georghiades August 2007 Major Subject: Computer Engineering iii ABSTRACT Design for Manufacturing (DFM) in Submicron VLSI Design. (August 2007) Ke Cao, B.S., University of Science and Technology of China; M.S., University of Minnesota Chair of Advisory Committee: Dr. Jiang Hu As VLSI technology scales to 65nm and below, traditional communication between design and manufacturing becomes more and more inadequate. Gone are the days when designers simply pass the design GDSII file to the foundry and expect very good man- ufacturing and parametric yield. This is largely due to the enormous challenges in the manufacturing stage as the feature size continues to shrink. Thus, the idea of DFM (Design for Manufacturing) is getting very popular. Even though there is no universally accepted definition of DFM, in my opinion, one of the major parts of DFM is to bring manufacturing information into the design stage in a way that is understood by designers. Consequently, designers can act on the information to improve both manufacturing and parametric yield. -
Idioms-And-Expressions.Pdf
Idioms and Expressions by David Holmes A method for learning and remembering idioms and expressions I wrote this model as a teaching device during the time I was working in Bangkok, Thai- land, as a legal editor and language consultant, with one of the Big Four Legal and Tax companies, KPMG (during my afternoon job) after teaching at the university. When I had no legal documents to edit and no individual advising to do (which was quite frequently) I would sit at my desk, (like some old character out of a Charles Dickens’ novel) and prepare language materials to be used for helping professionals who had learned English as a second language—for even up to fifteen years in school—but who were still unable to follow a movie in English, understand the World News on TV, or converse in a colloquial style, because they’d never had a chance to hear and learn com- mon, everyday expressions such as, “It’s a done deal!” or “Drop whatever you’re doing.” Because misunderstandings of such idioms and expressions frequently caused miscom- munication between our management teams and foreign clients, I was asked to try to as- sist. I am happy to be able to share the materials that follow, such as they are, in the hope that they may be of some use and benefit to others. The simple teaching device I used was three-fold: 1. Make a note of an idiom/expression 2. Define and explain it in understandable words (including synonyms.) 3. Give at least three sample sentences to illustrate how the expression is used in context.