Key Technologies for Prefabricated Timber Buildings
Total Page:16
File Type:pdf, Size:1020Kb
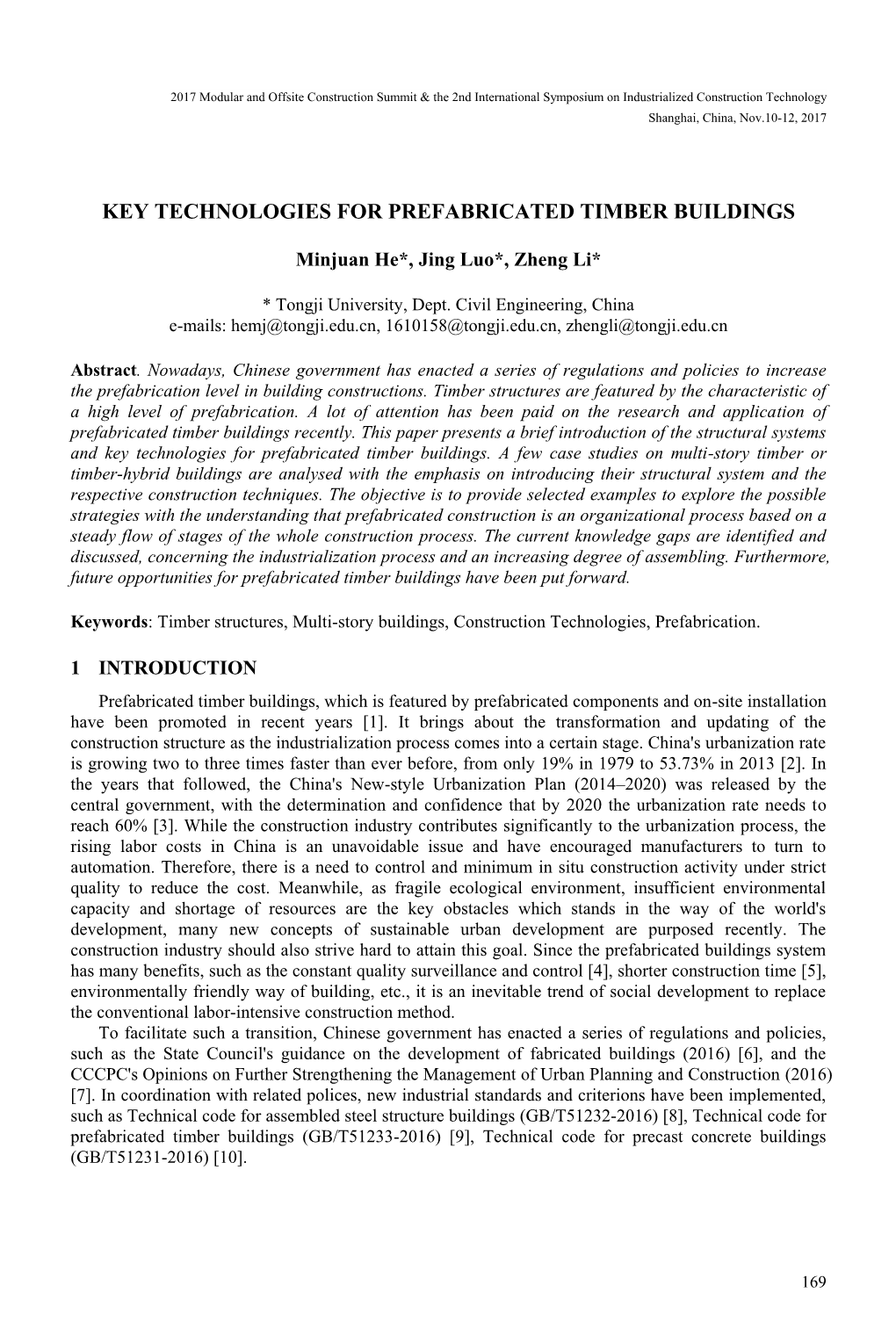
Load more
Recommended publications
-
Guide to Natural Gas/Oil Regulations & Development Projects in Mesa
Guide to Natural Gas/Oil Regulations & Development Projects in Mesa County I. Purpose This document is a guide to the Mesa County Land Development Code, as amended (Code), adopted plans and policies, and County permitting agencies related to natural gas and oil development. This guide categorizes typical natural gas/oil development activities pursued in Mesa County and maps them to the appropriate land uses defined by the Code as well as outlines the level of review required. This is an overview, and the specific and required regulations are contained in the Code that are identified in the Guide. The Code and additional information on natural gas/oil development can be found at the Mesa County Website: http://www.mesacounty.us/planning/ II. Land Uses & Where they are permitted in Mesa County All land in Mesa County is zoned, and certain uses are allowed to occur in each zoning district subject to Land Use Table 5.1. The Table details the land uses allowed in each zoning district and the review process applicable to each use. Note: if a use is not listed in these matrices, it is prohibited. If the land use has an “A” in the zoning district column, it is an Allowed use and requires Site Plan review. If the land use has a “C” in the zoning district column, it is a Conditional Use and requires a Conditional Use application. These uses, as applicable to the natural gas/oil industry, are summarized in the table on Page 3 of this Guide. The majority of natural gas/oil activity currently occurs in the AFT zoning district. -
Building Wood Towers
construction materials AIA CONTINUING EDUCATION building wood towers HOW HIGH IS UP FOR TIMBER STRUCTURES? COURTESY AART ARCHITECTS The Waterfront, a 128-unit wood-based residential development in Stavanger, Norway, designed by AART architects and Kraftvaerk for client Kruse- Smith. This first phase was completed last July; a second phase is under construction. More than 80 firms competed for the project. BY C.C. SULLIVAN, CONTRIBUTING EDITOR LEARNING OBJECTIVES After reading this article, you should be able to: he recent push for larger and taller wood structures may seem + DESCRIBE the primary approaches to large-scale like an architectural fad—plenty of hype, but only a few dozen structural wood construction, including hybrid light Tcompleted projects globally. Concrete and steel still rule the framing and engineered mass timber. world of mid- and high-rise construction. + DISCUSS the benefits and drawbacks of structural wood Still, Building Teams around the world are starting to use more systems, in particular their contribution to sustainable large-scale structural wood systems, including heavy timbers, design and green building. engineered framing systems, and other modern wood products. The + LIST current certifications, codes, and standards that number of new buildings of this kind has been trending modestly up- affect the use of large-scale modern wood structures. ward, spurred by such benefits as sustainability, cost effectiveness, + COMPARE wood systems to concrete and steel in and reduced construction impact. Leading the way: podium-type terms of availability, suitability for building types, and concrete and light-framed hybrids in the U.S., and heavier “mass performance for such factors as acoustics and fire safety. -
PREFABRICATION: the CHANGING FACE of ENGINEERING and CONSTRUCTION 2017 FMI/Bimforum Prefabrication Survey Table of Contents
PREFABRICATION: THE CHANGING FACE OF ENGINEERING AND CONSTRUCTION 2017 FMI/BIMForum Prefabrication Survey Table of Contents 1 3 25 29 Executive Summary Key Findings Business Implications Looking Ahead TODAY’S PREFAB ENVIRONMENT IS DIFFERENT 77% of respondents think today’s prefab The amount of project work using prefab has environment is different than in 2013. almost tripled between 2010 and 2016. 35% 13% YES NO 77% 23% 2010 2016 Most contractors perform single-trade Project inefficiencies and improved technologies prefabrication. are driving prefabrication. 32% 47% 21% Provide Provide Provide Multitrade Single-Trade Kitting Prefabrication Prefabrication Services THE BIG STRUGGLE TO MAKE IT WORK Contractors struggle to make Contractors using prefab on more than 50% prefabrication effective. of their projects are more effective compared to those who do less prefab. 14% 40% 46% Effective Needs Not Improvement Effective Three key challenges for making prefabrication 48% of respondents see less than 5% in effective: savings on total annual labor hours related to prefabrication. Culture Lack of Outdated Commitment Control Mindset he construction industry is back on track since the Great Recession, andT total construction employment has re- bounded to almost 6.7 million workers (still a far cry from its peak of 8 million workers in 2006). “Construction spending in November 2016 hit a 10-year high, with one-month and year-over-year increases in all major segments,” says Ken Simonson, chief economist at Associ- ated General Contractors of America. “Looking ahead, contractors say they expect more work in every category in 2017 than in 2016.” Executive Summary However, despite being about 16% below its 2006 employment peak, the industry is still struggling to find qualified labor. -
A Review of Modular Construction Shipbuilding in Malaysian Shipyard
Proceeding of Ocean, Mechanical and Aerospace November 7, 2016 -Science and Engineering-, Vol.3 A Review of Modular Construction Shipbuilding in Malaysian Shipyard Ahmad Alliff Anuar Mokhtar ,a, Mohamad Abu Ubaidah Amir Bin Abu Zarim, Kdr Halim bin Abdul Aziz TLDM (Bersara) * and Ainnur Hafizah Anuar Mokhtar ,b a) Faculty of Science and Defence Technology, National Defence University, Malaysia, Kem Perdana Sungai Besi, 57000 Kuala Lumpur, Malaysia. b) Faculty of Computing and Informatics, Universiti Malaysia Sabah, 87000 F.T. Labuan, Malaysia *Corresponding author: [email protected], [email protected], [email protected], [email protected] Paper History 1.0 INTRODUCTION Received: 25-September-2016 The maritime industry consumes a role play in associate for Received in revised form: 30-October-2016 Malaysia’s economic development . This is regard to the statement Accepted: 7-November-2016 which shipbuilding/ ship repair (SBSR) industry has been precisely recognized in the Third Industrial Master Plan (IMP3) in place of an industry that can gives something to the country’s wealth from the transportation area [1]. The shipbuilding industry ABSTRACT of Malaysia is getting larger and ship builders are adapting with the latest technology. For each project to achieve successfully, it The shipbuilding and ship repair industry in Malaysia comprises is important to manage a project within the constraint. The major of designing, building and assembling, repairing and maintaining, constraint that should be considered is cost, duration time to transforming and advancement of vessels as well as marine complete the project, safety aspect for workers and the quality of equipment . It is getting larger and always evolve in line with the the project. -
Cross Laminated Timber – the Product
CROSS-LAMINATED TIMBER A REVOLUTION IN TIMBER CONSTRUCTION ‘The best friend on earth of man is the tree. When we use the tree respectfully and economically, we have on of the greatest resources on earth.’ Frank Lloyd Wright CROSS LAMINATED TIMBER – THE PRODUCT . crosswise glued lamellas mainly in spruce . large sized structural elements for walls, ceilings and roofs . maximum dimensions 55 feet by 10 feet up to 20 inches thick . non-visible, industrial visible and domestic visible quality . 3, 5, 7 or even more layers, according to structural requirements . production made to order CROSS LAMINATED TIMBER – THE ADVANTAGES . sustainable, environmentally friendly building material . light-weight construction . short erection time due to prefabrication . extremely accurate shapes and openings . compatable with many different materials . allows for maximum architectural freedom . active climate protection – 1 m³ timber stores approx. 1 ton of CO2 BUILDING WITH TIMBER . Timber is the only renewable structural building material . Timber has the lowest energy consumption of any building material across its lifecycle . Using solid timber will reduce CO2 emissions when used in place of traditional construction materials i.e. concrete, steel, brick & block etc. Forests act as a carbon ‘sink’ removing CO2 from the atmosphere, releasing oxygen and sequestering/storing carbon BUILDING WITH TIMBER CO2 Absorbed 2,000kg 1,500kg 1,000kg 800kg 500kg Sequestered Carbon – 250kg 500kg 870kg Cross-laminated 1,700kg Timber 1,000kg Cement 1,500kg 2,000kg Steel CO2 Emitted BUILDING WITH TIMBER . Growing timber / trees removes CO2 from the atmosphere 3 3 . 1m (480-500kg/m ) of KLH panels will remove approximately 800kg of CO2 . -
Unions Electrical Workers Are Not Against Prefabrication
Unions Electrical Workers are not Against Prefabrication Adanegn G. Woldemichael, MSCM (Student) and Khalid M. Siddiqi, Ph.D. Kennesaw State University Kennesaw, Georgia Unions are vital part of growing and expanding construction industry. What union electrical workers get out of the industry depends on their readiness and competitiveness to advance the existing work methods. Prefabrication is one of these methods and many researches indicate its benefits in terms of time, cost, quality and safety. But, electrical union workers have not fully utilized these benefits & there are limited information available on the prevailing best practices of prefabrication specific to different local unions jurisdictions. Accordingly, this paper identifies the prevailing best practices of prefabrication feasible to union electrical workers. The intended audiences are union electrical workers and union electrical contractors. The study is performed by conducting survey to collect the necessary data from union electrical workers who are working under local union 613. The questions are designed to evaluate union workers attitude towards prefabrication and mainly focus on listing and comparing most useful prefabrication practices. The study helps to bring a common understanding among union electrical workers on implementation of prefabrication and it open doors for continual improvement on prevailing best practices. Ultimately, these may significantly alter union electrical workers competitive position and make them more sustainable. Keywords: Unions, Union workers, Prefabrication, Best practice, Electrical Introduction Prefabrication is a manufacturing process, generally taking place at a specialized facility, in which various materials are joined to form a component part of final installation. Prefabricated components often involve the work of single craft. The actual prefabrication can occur any place (on- site or off-site), where there is space to complete the work. -
Measuring Productivity and the Impact of Prefabrication on Productivity
ELECTRI International—The Foundation for Electrical Construction, Inc. PRODUCTIVITY ENHANCEMENT Measuring Productivity and the Impact of Prefabrication on Productivity Marquette University Mark O. Federle ELECTRI International The Foundation for Electrical Construction, Inc. Measuring Productivity and the Impact of Prefabrication on Productivity Marquette University Mark O. Federle ELECTRI Council ELECTRI International—The Foundation for Electrical Construction, Inc. As of December 2015 PRESIDENT’S COUNSEL REGENT $1,000,000 or more $250,000 or more Contractors Contractors The Hugh D. ‘Buz’ and Irene E. ‘Betty’ Allison Trust, Hugh D. ‘Buz’ Cannon & Wendt Electric Company, David E. Fagan Allison, d. Capital Electric Construction, Robert E. and Sharon Doran* - In The Richard W. and Darlene Y. McBride Trust, Richard W. McBride* memory of Robert E. Doran, Jr. The Al and Margaret Wendt Trust, Albert G. Wendt*, d. John R. Colson, TX NECA Chapters and Affiliates Maron Electric Co., Jerold H. Nixon, d., and Eric F. Nixon National Electrical Contractors Association*, John M. Grau Miller Electric Company, H. E. “Buck” Autrey* **, David Long and Henry Brown Manufacturers, Distributors, Utilities and Affiliates Robert L. Pfeil, d., IN Schneider Electric / Square D, Neal Lyons NECA Chapters and Affiliates PROGRAM GUARANTOR Chicago & Cook County Chapter NECA $500,000 or more New York City Chapter NECA*, Ciro J. Lupo Contractors Northeastern Illinois Chapter NECA, Craig Martin McCormick Systems, Jack McCormick Northern California Chapter NECA, Greg A. -
Prefabrication for Lean Building Services Distribution
PREFABRICATION FOR LEAN BUILDING SERVICES DISTRIBUTION M. J. Mawdesley1 and G. Long2 ABSTRACT This paper is concerned with the use of prefabrication for the distribution of building services (HVAC), concentrating mainly on the construction of office facilities. This is a good example of an application of lean construction methods. It assures reliable workflow and predictability in the project, it minimises waste and increases performance; it enables concurrent engineering to occur and delivers value throughout the project’s life. An analysis of the use of off-site fabricated building services as a method of lean construction is given with reference to features of its use such as design freezes, Just-in-Time (JIT) deliveries and predictable processes. However, it requires different procurement processes to be totally effective. The paper compares two procurement routes both theoretically and by the use of two real examples of construction projects. It illustrates some potential problems and shows that the solutions lie not in the technical aspects but in better communication and planning throughout the life of the project. KEY WORDS Prefabrication, Building Services, Lean Construction, Procurement 1 Dr, School of Civil Engineering, University of Nottingham UK 2 Mr, School of Civil Engineering, University of Nottingham UK Proceedings IGLC-10, Aug. 2002, Gramado, Brazil M. J. Mawdesley and G. Long 2 INTRODUCTION Lean construction is concerned with providing a better service for the client through consideration of the whole construction process. It has its roots in the concepts of lean production developed in Japan. As such, many construction practitioners may be sceptical of its applicability to their industry in the belief that construction is different. -
Fire Safety Challenges of Tall Wood Buildings (2013)
Fire Safety Challenges of Tall Wood Buildings Final Report Prepared by: Robert Gerard and David Barber Arup North America Ltd San Francisco, CA Armin Wolski San Francisco, CA © December 2013 Fire Protection Research Foundation THE FIRE PROTECTION RESEARCH FOUNDATION ONE BATTERYMARCH PARK QUINCY, MASSACHUSETTS, U.S.A. 02169-7471 E-MAIL: [email protected] WEB: www.nfpa.org/Foundation —— Page ii —— FOREWORD Recent architectural trends include the design and construction of increasingly tall buildings with structural components comprised of engineered wood referred to by names including; cross laminated timber (CLT), laminated veneer lumber (LVL), or glued laminated timber (Glulam). Construction is currently underway on a 10-story apartment building in Melbourne, Australia, with taller structures up to 30 stories under design in Norway, Austria and Vancouver. These buildings are cited for their advantages in sustainability resulting from the use of wood as a renewable construction material. Claims have been made that they are designed to be safer than buildings fabricated using structural steel due to the formation of an insulating char layer that forms on the perimeter of a laminated wood beam when exposed to a fire. The Fire Protection Research Foundation initiated this project to gain an understanding of the performance of these buildings under credible fire scenarios to ensure the safety of the occupants to emissions and thermal hazards, as well as the property protection of the building and nearby structures. The goals of this first phase project was to gather information and data from relevant studies and analyze the knowledge gaps. In addition, a framework prioritization of research needs was produced. -
Overview of Prefabrication in Residential Construction (With an Addendum on “MEP Prefabrication” by Mark Daniels, Graduate Student) Summary
Overview of Prefabrication in Residential Construction (With an addendum on “MEP Prefabrication” by Mark Daniels, Graduate student) Summary Harsh Bakliwal, Graduate Student Cameron Kostiz, Former Undergraduate Student Dr. Matt Syal, Professor Mark Daniels, Graduate Student Housing Education and Research Initiative Construction Management Program School of Planning, Design and Construction Michigan State University October 2020 Abstract The rapid growth in the automation in the construction industry is driving towards the adoption of prefabrication in construction. The construction market, especially the residential construction, is shifting towards prefabricated construction practices due to the skilled labor shortage and the need to improve the construction quality. The objective of this report is to describe different levels of prefabrication in residential construction along with their advantages and disadvantages. This report initially provides a brief overview of the residential construction industry along with statistics related to the present construction market and labor trends. It then describes different levels of prefabrication in detail. These include material prefabrication, panelization, pre-manufactured building units or modules, and factory-built homes, including the manufactured and the modular homes. In the end, it provides the advantages and disadvantages of factory-built construction based on factors such as, cost, completion time, and the type of construction methods used for factory-built 0 versus site-built construction. Finally, it provides the state of prefabrication in residential construction across the world including, the USA, China, India, Japan, Sweden, UK, and Australia. After this study was completed, additional work was done by Mark Daniels, CM graduate student, on MEP prefabrication for multi-family and commercial buildings. -
Prefabrication (“Prefab”) § Prefabrication Is the Construction of Some Parts of a Building Off- Site and Then Transporting Them to the Job Site for Final Installation
Changing the Way We Think of Prefabrication: New Solutions for Your Building Envelope Integrated sheathing is a key component 1 Changing the Way We Think of Prefabrication: New Solutions for Your Building Envelope AIA Continuing Education System (AIA/CES) § BNP Media is a Registered § Credit earned on completion of this Provider with AIA/CES. program will be reported to AIA/CES § This program is registered with Records for AIA members. Certificates of Completion for non- the AIA/CES for continuing professional education. As such, AIA members are available on request. it does not include content that may be deemed or construed to § This presentation is protected by be an approval or endorsement U.S. and international copyright by the AIA of any material of laws. Reproduction, distribution, construction or any method or display, and use of the presentation manner of handling, using, without written permission of the distributing, or dealing in any presenters is prohibited. material or product. § Completing a quiz at the end of this presentation is required in order to receive continuing education credit. Credit Designation: 1.0 LU|HSW 2 Learning Objectives Upon completion of this course, you should be able to: § 1. Discover how prefabrication offers productivity and management advantages for the building envelope. § 2. Discuss how prefabrication can address common project management issues at the job site, including weather delays, crew safety, quality control, labor shortages, and scheduling. § 3. Explore how traditionally applied WRB-AB and integrated WRB- AB sheathing solutions are impacting lean manufacturing productivity goals. § 4. Compare WRB-AB integrated sheathing solutions transportability from prefabrication factory to the job site. -
Designing Sustainable, Prefabricated Wood Buildings
CONTINUING EDUCATION DESIGNING SUSTAINABLE, Presented by: PREFABRICATED WOOD BUILDINGS LEARNING OBJECTIVES 1. Demonstrate why prefabrication is an efficient and sustainable building practice 2. Evaluate the use of wood components in sustainable prefabricated buildings as well as design and engineering challenges that wood can solve 3. Discuss the advantages of building with prefabricated wood components in terms of speed and efficiency of construction, design flexibility, waste reduction, environmental performance and improved life safety 4. Analyze, through case studies, the different stages of wood building prefabrication from design to installation CONTINUING EDUCATION AIA CREDIT: 1 LU/HSW GBCI CREDIT: 1 CE HOUR AIA COURSE NUMBER: AR072018-3 GBCI COURSE NUMBER: 0920016493 Use the learning objectives above to focus your study as you read this article. To earn credit and obtain a certificate of completion, visit http://go.hw.net/AR072018-3 and complete the quiz for free as you read this article. If you are new to Hanley Wood University, create a free learner account; returning users log in as usual. Image courtesy of Lawrence Anderson PREFABRICATION THEN AND NOW a boom in kit-of-parts building post-World TERMS War II. Consumers were enthralled with Prefabricated wood buildings should be industrial production and replication, aka mass Off-Site Manufacture (OSM) considered when designing and building both production, and prefabricated buildings helped Off-site manufacture is the manufacture of multi-family and commercial buildings, such fulfill the need for affordable, quality housing construction components or systems in a factory as multi-family housing, education, retail, environment to be transported and assembled post-war.