Progress on Ruthenium Release and Transport Under Air Ingress Conditions
Total Page:16
File Type:pdf, Size:1020Kb
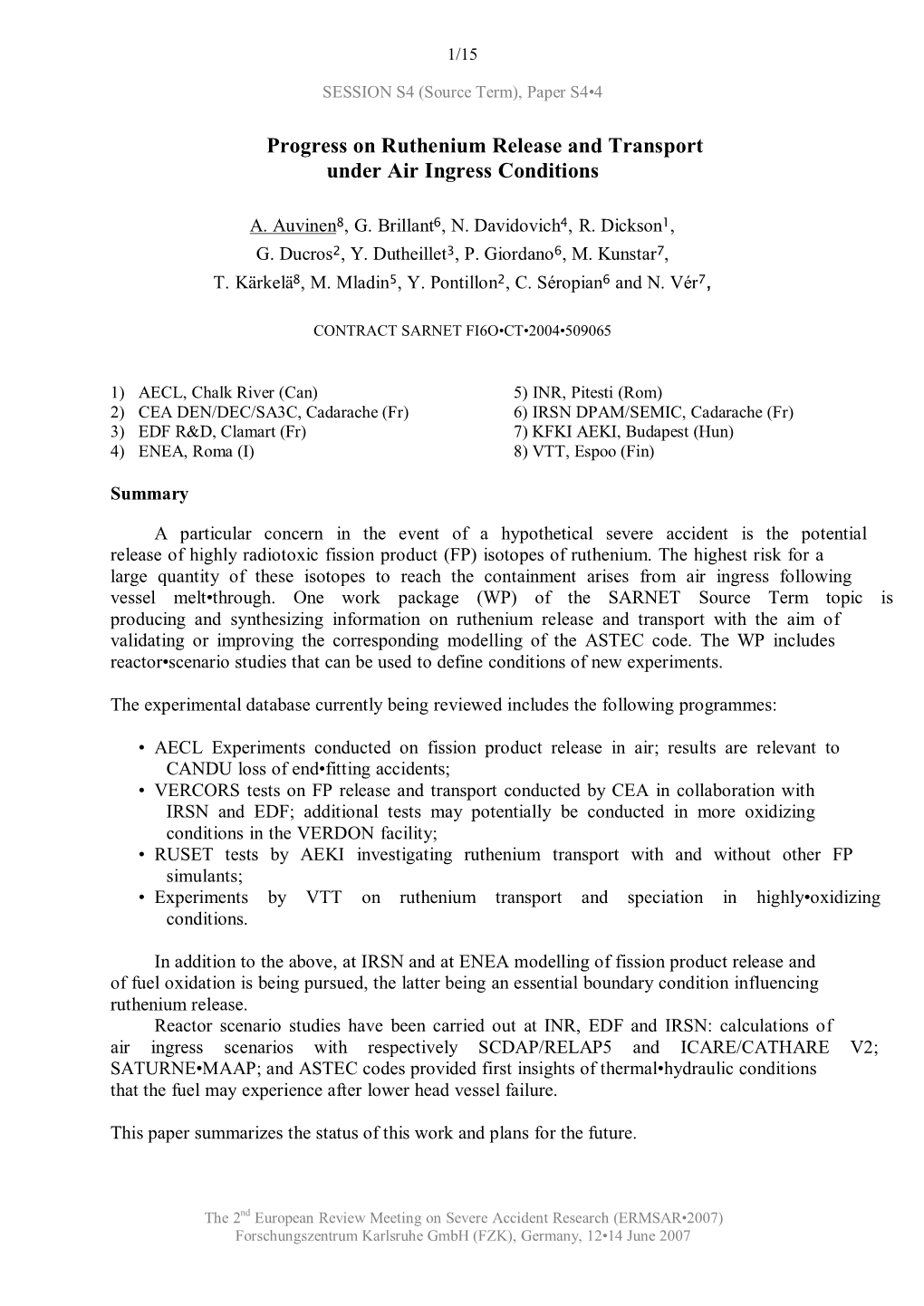
Load more
Recommended publications
-
A Window Into the Meltdown Events at the Fukushima Daiichi Nuclear
www.nature.com/scientificreports OPEN Caesium-rich micro-particles: A window into the meltdown events at the Fukushima Daiichi Nuclear Received: 12 October 2016 Accepted: 12 January 2017 Power Plant Published: 15 February 2017 Genki Furuki1,*, Junpei Imoto1,*, Asumi Ochiai1, Shinya Yamasaki2, Kenji Nanba3, Toshihiko Ohnuki4, Bernd Grambow5, Rodney C. Ewing6 & Satoshi Utsunomiya1 The nuclear disaster at the Fukushima Daiichi Nuclear Power Plant (FDNPP) in March 2011 caused partial meltdowns of three reactors. During the meltdowns, a type of condensed particle, a caesium-rich micro-particle (CsMP), formed inside the reactors via unknown processes. Here we report the chemical and physical processes of CsMP formation inside the reactors during the meltdowns based on atomic- resolution electron microscopy of CsMPs discovered near the FDNPP. All of the CsMPs (with sizes of 2.0–3.4 μm) comprise SiO2 glass matrices and ~10-nm-sized Zn–Fe-oxide nanoparticles associated with a wide range of Cs concentrations (1.1–19 wt% Cs as Cs2O). Trace amounts of U are also associated with the Zn–Fe oxides. The nano-texture in the CsMPs records multiple reaction-process steps during meltdown in the severe FDNPP accident: Melted fuel (molten core)-concrete interactions (MCCIs), incorporating various airborne fission product nanoparticles, including CsOH and CsCl, proceeded via SiO2 condensation over aggregates of Zn-Fe oxide nanoparticles originating from the failure of the reactor pressure vessels. Still, CsMPs provide a mechanism by which volatile and low-volatility radionuclides such as U can reach the environment and should be considered in the migration model of Cs and radionuclides in the current environment surrounding the FDNPP. -
Ex-Vessel Steam Explosion Analysis for Pressurized Water Reactor and Boiling Water Reactor
Nuclear Engineering and Technology 48 (2016) 72e86 Available online at ScienceDirect Nuclear Engineering and Technology journal homepage: www.elsevier.com/locate/net Original Article Ex-vessel Steam Explosion Analysis for Pressurized Water Reactor and Boiling Water Reactor * Matjaz Leskovar and Mitja Ursic Jozef Stefan Institute, Jamova cesta 39, SI-1000 Ljubljana, Slovenia article info abstract Article history: A steam explosion may occur during a severe accident, when the molten core comes into Received 8 June 2015 contact with water. The pressurized water reactor and boiling water reactor ex-vessel Received in revised form steam explosion study, which was carried out with the multicomponent three- 20 August 2015 dimensional Eulerian fuelecoolant interaction code under the conditions of the Organi- Accepted 23 August 2015 sation for Economic Co-operation and Development (OECD) Steam Explosion Resolution for Available online 28 October 2015 Nuclear Applications project reactor exercise, is presented and discussed. In reactor cal- culations, the largest uncertainties in the prediction of the steam explosion strength are Keywords: expected to be caused by the large uncertainties related to the jet breakup. To obtain some Boiling Water Reactor insight into these uncertainties, premixing simulations were performed with both avail- Fuel-Coolant Interaction able jet breakup models, i.e., the global and the local models. The simulations revealed that Pressure Load weaker explosions are predicted by the local model, compared to the global model, due to Pressurized Water Reactor the predicted smaller melt droplet size, resulting in increased melt solidification and Reactor Cavity increased void buildup, both reducing the explosion strength. Despite the lower active melt Severe Accident mass predicted for the pressurized water reactor case, pressure loads at the cavity walls Steam Explosion are typically higher than that for the boiling water reactor case. -
A Comparative Study of Flammability Limit Models for H2/CO Mixture on the Applicability of Severe Accident Conditions
Transactions of the Korean Nuclear Society Spring Meeting Jeju, Korea, May 23-24, 2019 A Comparative Study of Flammability Limit Models for H2/CO Mixture on the Applicability of Severe Accident Conditions 1 1 1 1,2 Yeon Soo Kim , Joongoo Jeon , Wonjun Choi , Sung Joong Kim * 1Department of Nuclear Engineering, Hanyang University 2Institutte of Nano Science and Technology, Hanyang University 222 Wangsimni-ro, Seongdong-gu, Seoul 04763, Republic of Korea *Corresponding author: [email protected] 1. Introduction sustainably. Lower flammability limit (LFL) is the minimum concentration while upper flammability limit Through the Fukushima accident, it was proved that (UFL) is the maximum concentration. As the amount of hydrogen released into containment building may cause combustible gas which can be generated in nuclear explosion under severe accident (SA). After the accident, power plant is limiting, LFL is mainly applied in researches have been actively conducted to predict and flammability evaluation under severe accident. mitigate the combustion risk. On the other hand, as the Because hydrogen and carbon monoxide coexist in the accident progresses to ex-vessel phase, carbon monoxide containment building at ex-vessel phase, the LFL of is generated in the containment by molten corium- H2/CO mixture should be obtained separately. In this concrete interaction (MCCI). Carbon monoxide is also section, the various method to predict the LFL of H2/CO flammable gas, which can increase the combustion risk is described in three categories; MELCOR default option, when coexisting with hydrogen. However, most of the empirical correlations and method based on the theory. previous studies have mainly focused on hydrogen and paid relatively less attention to carbon monoxide. -
The Results of Two Recent Corium-Water Thermal Interaction (CWTI)
CONF-850810—10 DE85 007897 CORIUM QUENCH IN DEEP POOL MIXING EXPERIMENTS* by B. W. Spencer, L. McUmber, D. Gregorash, R. Aeschlimann, and J. J. Sienicki Reactor Analysis and Safety Division Argonne National Laboratory Argonne, IL 60439 ABSTRACT The results of two recent corium-water thermal interaction (CWTI) tests are described in which a stream of molten corium was poured into a deep pool of water in order to determine the mixing behavior, the corf urn-to-water heat transfer rates, and the characteristic sizes of the quenched debris. The corium composition was 60% UOg, 16% ZrO2, and 24% stainless steel by weight; its initial temperature was 3080 K, ~ 160 K above the oxide phase liquidus temperature. The corium pour stream was a single-phase 2.2 cm dia liquid column which entered the water pool in film boiling at ~ 4 m/s. The water subcooling was 6 and 75C in the two tests. Test results showed that with low subcooling, rapid steam generation caused the pool to boil up into a high void fraction regime. In contrast, with large subcooling no net steam generation occurred, and the pool remained relatively quiescant. Breakup of the jet appeared to occur by surface stripping. In neither test was the breakup com- plete during transit through the 32 cm deep water pool, and molten corium channeled to the base where it formed a melt layer. The characteristic heat transfer rates measured 3.5 MJ/s and 2.7 MJ/s during the fall stage for small and large subcooling, respectively; during the initial stage of bed quench, the surface heat fluxes measured 2.4 MW/m2 and 3.7 MW/m2, respectively. -
NUREG/CR-6042, Rev. 2 [3:4] Appendix
Reactor Safety Course (R-800) 3.7 Special Consideration for BWR Facilities 3.7 Special Considerations for BWR for reactor vessel pressure control when run Facilities continuously in the recirculation mode, pumping water from the condensate storage Boiling water reactors have unique features tank back to the condensate storage tank and that would cause their behavior under severe periodically diverting a small portion of the accident conditions to differ significantly flow into the reactor vessel as necessary to from that expected for the pressurized water maintain the desired water level. The steam reactor design.1,2 This section addresses taken from the reactor vessel by the turbine several special considerations affecting BWR is passed to the pressure suppression pool as severe accident progression and mitigation. turbine exhaust, which provides a slower In this endeavor, many implications of the rate of pool temperature increase than if the phenomena described in Sections 3.1 through vessel pressure control were obtained by 3.6 (such as zirconium oxidation) will be direct passage of steam from the vessel to demonstrated by example. First, however, it the pool via the SRVs. Plants having both is necessary to review some of the BWR HPCI and RCIC systems can employ the features pertinent to severe accident HPCI turbine exclusively for pressure considerations. control while the RCIC system is used to maintain the reactor vessel water level. The 3.7.1 Pertinent BWR Features HPCI turbine is larger than the RCIC turbine and, therefore, is more effective for pressure An important distinction of the BWR design control. These systems require DC power for is that provisions are made for direct valve and turbine governor control, but have operator control of reactor vessel water level no requirement for control air. -
09 Fr0200361
09 FR0200361 ^r.^r IQ 34. IMPORTANCE OF PROTOTYPIC-CORIUM EXPERIMENTS FOR SEVERE ACCIDENT RESEARCH P. PILUSO, C. JOURNEAU, G. COGNET, D. MAGALLON*, J.M. SEILER** CEA Cadarache 13108 St Paul les Durance cedex, France *: detached from the Joint Research Centre of the European Commission ** CEA Grenoble KEY WORDS: Severe accidents, Nuclear materials, Experiments Introduction: In case of a severe accident in a nuclear reactor, very complex physical and chemical phenomena would occur. Parallel to the development of mechanistic and scenario codes, experiments are needed to determine key phenomena and coupling, develop and qualify specific models, validate codes. Due to lower costs and constraints, experiments using low temperature simulant materials (such as CORINE [1] or Scaled Simulant Spreading Experiments (S3C) [2] for spreading or BALI [3,4] for in-vessel pools) allow the testing of a large number of configurations and the determination of correlations. But some crucial corium phenomena and behaviours such as the importance of radiation heat transfer or the presence of a large liquidus-solidus interval (up to 1000 K) are not reproduced in low temperature experiments. Consequently, it is attempted to simulate real corium with high temperature simulant materials: alumina, thermite, widely used (e.g. KATS [5] or COMET [6] facilities); high temperature salts or mixtures with zirconia and/or hafnia. However, it is not feasible to simulate all the aspects of corium phenomenology, especially its high temperature behaviour. Therefore, experiments with prototypic material are performed to check the results obtained with simulants and identify possible differences. In this context, CEA has undertaken a large program on severe accidents with prototypic corium [7]. -
Analysis of Molten-Corium Concrete Interaction for Small Modular Reactor
ANALYSIS OF MOLTEN-CORIUM CONCRETE INTERACTION FOR SMALL MODULAR REACTOR SANG HO KIM, JONG HWA PARK, HWAN YEOL KIM, RAE-JOON PARK Severe Accident and PHWR Safety Research Division, Korea Atomic Energy Research Institute 989-111 Daedeok-daero, Yuseong-gu, Daejeon, 34057 – Republic of Korea ABSTRACT Molten-corium concrete interaction (MCCI) is one of the important phenomena in a severe accident analysis of a nuclear power plant. When a reactor vessel is broken, molten corium spreads out into the cavity. Various chemical reactions occur as the molten corium ablates the cavity concrete. Ex-vessel phenomena also have to be analysed for recently developed small modular reactors (SMRs). In the analysis of the MCCI, the main variables characterised in SMRs are drawn in comparison with those of large power pressurised water reactors. The designs of the core, reactor coolant system, and containment are included. The variables are controlled to analyse the effects on the MCCI. The results of the analysis showed that the ablation of concrete proceeded slowly owing to the relatively large cavity area and small amount of corium. The large metal content in corium caused an increase in hydrogen generation. 1. Introduction Nuclear fuels become melted when the core is not sufficiently cooled during an uncontrolled nuclear accident. If core melting continuously progresses, it threatens the integrity of the reactor vessel. During the damage to the reactor vessel, the molten-corium drops into the cavity. In the case of a dry cavity, it widely spreads out into the cavity. The release of radioactive materials into the environment has to be prevented for all severe accidents of a nuclear power plant. -
Analytical Measurements of Fission Products During a Severe Nuclear Accident
EPJ Web of Conferences 170, 08005 (2018) https://doi.org/10.1051/epjconf/201817008005 ANIMMA 2017 Analytical measurements of fission products during a severe nuclear accident D. Doizi1; S. Reymond la Ruinaz1 ; I. Haykal1 ; L. Manceron2, 3 ; A. Perrin4 ; V. Boudon5; J. Vander Auwera6 ; F. Kwabia tchana7 ; M. Faye2 Abstract– The Fukushima accident emphasized the fact spectrometry, molecular absorption spectrometry has been that ways to monitor in real time the evolution of a nuclear reactor proposed for the measurement of gaseous forms of iodine and during a severe accident remain to be developed. No fission ruthenium. It allows on line chemical speciation of the gaseous products were monitored during twelve days; only dose rates were forms of fission products and could enable their remote sensing. measured, which is not sufficient to carry out an online diagnosis It has been evaluated and is the subject of this paper. of the event. The first measurements were announced with little reliability for low volatile fission products. In order to improve the For fission gases such as xenon and krypton, micro gas safety of nuclear plants and minimize the industrial, ecological and health consequences of a severe accident, it is necessary to develop chromatography (micro GC) measurements have been new reliable measurement systems, operating at the earliest and proposed and characterized from the point of view of closest to the emission source of fission products. Through the detection limits and ease of installation on the chimney French program ANR « Projet d’Investissement d’Avenir », the aim of the DECA-PF project (diagnosis of core degradation from of the nuclear plant. -
Chapter 5 Development of the Core Melt Accident
Chapter 5 Development of the core melt accident 5.1. Development of the accident in the reactor vessel 5.1.1. Progression of the core melt in the reactor vessel 5.1.1.1. Introduction If the reactor core remains dry for a considerable length of time, the temperature of the fuel rods rises and may locally reach levels that cause significant and irreversible core degradation. The mechanisms of this degradation are both chemical and mechani cal. Depending on the local temperature levels, degradation may result in more or less severe hydrogen production, fission product (FP) release, and molten corium formation and propagation towards the lower head. These phenomena have been studied in many national and international research programmes [1, 2, 11, 12, 15, 22]. The main degra dation mechanisms that appear as the core temperature rises, as well as their conse quences, are described in Section 5.1.1.2. This description is followed by a presentation of the main experimental programmes that have increased the state of knowledge of the degradation mechanisms, as well as a description of the modelling and computer codes that capitalise on that knowledge. The main mechanisms involved in the evolution of the fuel rod and core degradation are schematically shown in Figures 4.1, 4.2 and 4.3 of the previous chapter. 102 Nuclear Power Reactor Core Melt Accidents 5.1.1.2. Physical phenomena 5.1.1.2.1. Cladding oxidation and hydrogen formation At temperatures above approximately 1300 K, the zircaloy in the cladding is exother mically oxidised by the steam. -
Chernobyl 25 Years On
Enhancing nuclear safety Chernobyl 25 years on In late April 1986, a major nuclear accident released a large quantity of radioactive material into the atmosphere… Collection of topics Units Some sources of radiation An introduction to the Chernobyl accident exposure for humans Becquerel The becquerel (Bq) is the unit of Natural Artificial What is radioactivity? ..................................................... p. 2 measurement of radioactivity. radioactivity radioactivity It corresponds to one decay per Abdomen second, for all types of radiation CT scan 1 n The accident ........................................................................ p. 4 emitted ( , , ). Some parts a b g of Brazil and South-West India Gray 2 n Radioactive releases .......................................................... p. 7 The gray (Gy) is the unit of absorbed dose. It corresponds to the quantity of energy La Paz (Bolivia), Average medical 3 n Spread of the radioactive plume over Europe ...... p. 8 (measured in Joules – J) altitude exposure in France transferred by ionising radiation 3660 m (CT scan, X-rays, etc.) to the mass through which it 4 n Radioactive deposits in Europe ................................... p. 12 passes (expressed in kilograms – kg). -1 5 n Contamination of various environments 1 Gy = 1 J.kg . Radon* in France Dental and the food chain ............................................................ p. 17 Sievert panoramic *Naturally X-ray The sievert (Sv) is the unit of occurring n . equivalent dose received by radioactive gas 6 Health impact in the most contaminated areas p. 24 a specific organ or tissue, and the unit of effective (whole Paris-New York 0.06 return flight n body) dose. The equivalent dose 0.006 7 Doses received in France and their is determined from the dose 0.002 associated risks ................................................................. -
SEVERE ACCIDENT PHENOMENA Part 1: In-Vessel
SEVERE ACCIDENT PHENOMENA part 1: In-vessel IAEA Workshop on Severe Accident Management Guidelines 11-15 December 2017, Vienna, Austria presented by Randall Gauntt (Sandia National Laboratories) Outline • Severe accident phenomena part 1 : In-vessel Introduction Experimental basis Role of fission products and decay heat Early phase core degradation Late phase core degradation Lower head failure Fission product release Reflood phenomena Research priorities/Conclusion Acknowledgements and References Severe accident phenomena: In-vessel 2 IAEA Introduction Severe accidents in nuclear power plants encompass a very wide range of interacting phenomena: Thermal hydraulic behaviour in the vessel and primary circuit; Degradation of the reactor core, including oxidation of fuel rod cladding, melt formation, relocation of material to the lower head, melt pool behaviour, lower head failure, ex- vessel corium recovery, molten core-concrete interactions; Release of fission products from the fuel, structural material release, transport and deposition in the primary circuit, their behaviour in the containment (especially now with special emphasis on iodine and ruthenium), aerosol behaviour; Thermal hydraulics in the containment, hydrogen behaviour, molten fuel-coolant interactions, direct TMI-2 final state containment heating. This presentation summarises the main in-vessel phenomena involved Severe accident phenomena: In-vessel 3 IAEA Stages of Reactor Accidents 1. boildown of coolant and fuel heatup DBA 2. clad balloon and rupture & 3. -
DISCOMS: Distributed Sensing for Corium Monitoring and Safety P
DISCOMS: DIstributed Sensing for COrium Monitoring and Safety P. Ferdinand, L. Maurin, S. Rougeault, H Makil, G. Cheymol, H. Maskrot, P. Le Tutour, D. Duval, Christophe Journeau, J.-F Villard, et al. To cite this version: P. Ferdinand, L. Maurin, S. Rougeault, H Makil, G. Cheymol, et al.. DISCOMS: DIstributed Sensing for COrium Monitoring and Safety. CANSMART 2015: International Conference on Smart Materials and Structures, Jul 2015, Vancouver, Canada. cea-02151741 HAL Id: cea-02151741 https://hal-cea.archives-ouvertes.fr/cea-02151741 Submitted on 9 Jun 2019 HAL is a multi-disciplinary open access L’archive ouverte pluridisciplinaire HAL, est archive for the deposit and dissemination of sci- destinée au dépôt et à la diffusion de documents entific research documents, whether they are pub- scientifiques de niveau recherche, publiés ou non, lished or not. The documents may come from émanant des établissements d’enseignement et de teaching and research institutions in France or recherche français ou étrangers, des laboratoires abroad, or from public or private research centers. publics ou privés. CANSMART 2015 : International Conference on Smart Materials and Structures SMN 2015: 5th International Conference on Smart Materials and Nanotechnology in Engineering DISCOMS: DIstributed Sensing for COrium Monitoring and Safety 1P. Ferdinand, 1L. Maurin, 1S. Rougeault, 1H. Makil, 2G. Cheymol, 2H. Maskrot, 2P. Le Tutour, 2D. Duval, 3Ch. Journeau, 3J.-F. Villard, 3J-F. Haquet, 3Q. Souquet, 3L. Barbot, 4J. Miss, 4I. Duhamel, 4B. Dechenaux, 4M. Brovchenko, 5G. Musoyan, 5S. Balleydier, 6F. Pouillé, 7G. Helleux, 7S. Fourrez, and 7L. Pichon 1CEA, LIST, F-91191 Gif-sur-Yvette, France. [email protected] 2CEA, DEN, F-91191 Gif-sur-Yvette, France.