Data Interchange on 60 Mm Read-Only ODC - Capacity: 1,8 Gbytes TM (UMD )
Total Page:16
File Type:pdf, Size:1020Kb
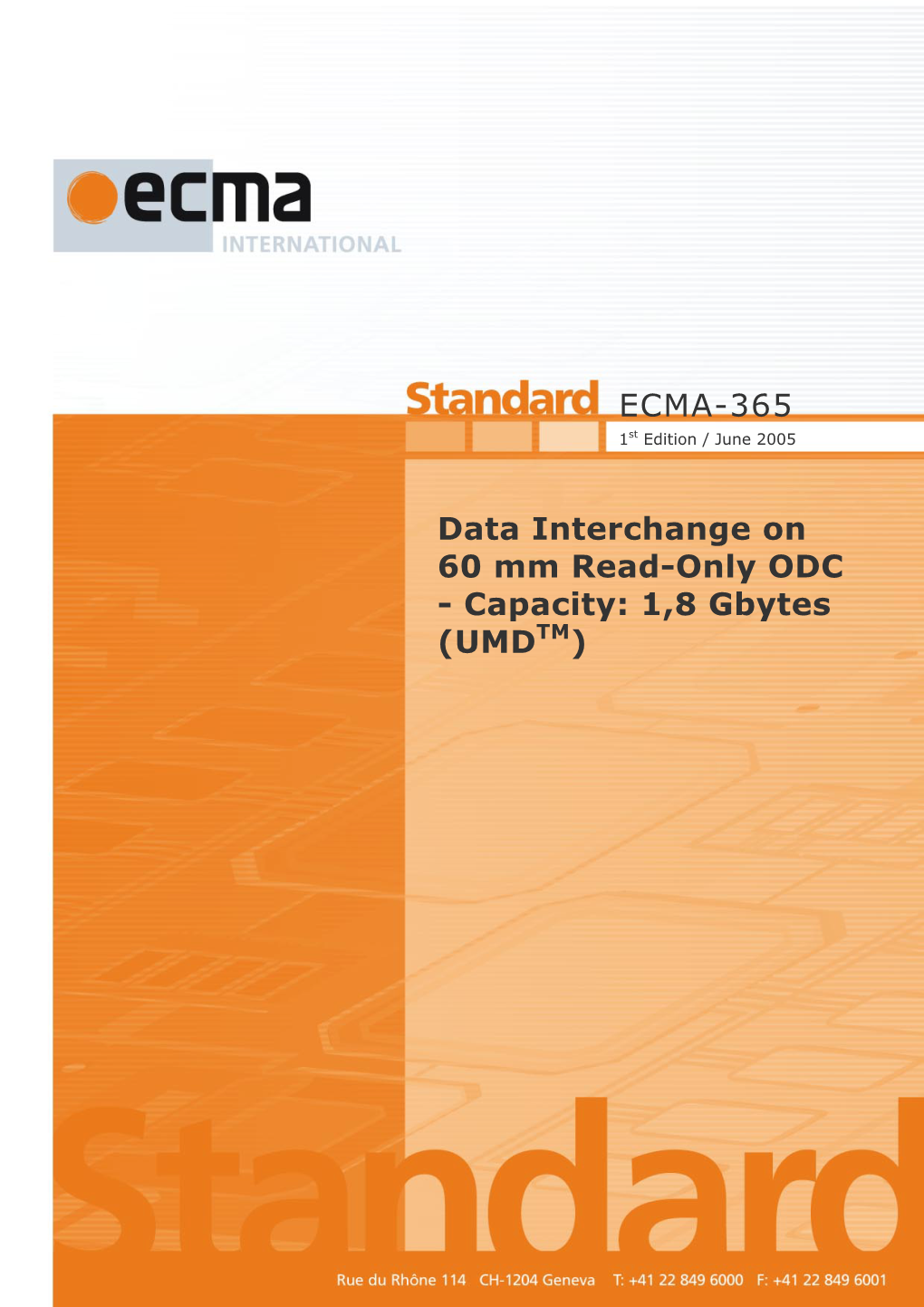
Load more
Recommended publications
-
How to Download Psp .Iso Games Despicable Me the Game PSP ISO PPSSPP Free Download
how to download psp .iso games Despicable Me The Game PSP ISO PPSSPP Free Download. Based on Universal Pictures' 3-D CGI feature, Despicable Me: The Game -- Minion Mayhem lets players use an army of minions and their abilities to complete dozens of puzzles, missions, and challenges. PSP Game: Despicable Me The Game System: PlayStation Portable Best Emulator: PPSSPP Developer: Monkey Bar Genre: Action Image Format: ISO File Size: 495 MB. Screenshots. How to play with PPSSPP Emulator? Download and install PPSSPP Emulator on your device and download Despicable Me The Game ISO rom, run the emulator and select your ISO. Play and enjoy the game. Despicable Me The Game RAR Download Size: 244 MB (Compressed) Download Now. Need to extract the file using Winrar o r Zarchiver FAQ How to download? How to extract? Best 100 PPSSPP Games to Download in 2020 – PSP Games To Download and Play now. In PES 2020 PPSSPP – PSP Iso you play with your fellow opponents through exhibition, adhoc and save game. Play master leagues and other related leagues such as champions League, Europe leagues, this game comes with latest season kits for players. Beautiful stadium grass was also improved, about 15 stadiums added and updated with clean graphics. Prince Of Persia Revelations. With Dhaka running behind the prince, you will have to deal with him and know the secret behind all those mysterious creatures and Dhaka is Immortal. How to download psp .iso games. Game titles Transformers: The Match ppsspp iso little size is the game adaptation of the most well-known robot film of all time produced in 2007, particularly Transfomers which was initially unveiled in North America in June 2007 which is obtainable on several consoles ranging from PS2, Pc, Xbox 360 and of system Playstation Moveable is also out there. -
12508 PSP E-1000 GB Web.Indd
GB Instruction Manual PSP-E1004 7017787 Table of contents Warning and caution Support WARNING······················································ 4 Troubleshooting ··········································· 28 Precautions ···················································· 6 Additional information Using the PSP® system Before disposing of or transferring Part names and functions ·····························10 the PSP® system ······································33 Charging the battery ·····································12 Specifications··············································· 34 Turning the system on and off·······················15 Compatible media ········································35 Using the XMBTM (XrossMediaBar) menu······16 Copyright and trademarks ··························· 37 Playing Universal Media Disc games ············18 Playing Memory Stick DuoTM content·············19 Using the on-screen keyboard ·····················20 Setting the parental control level ·················· 22 Updating the system software ····················· 24 Downloading games ···································· 26 2 Table of contents PSP® system documentation You can find information about the PSP® system in this manual as well as online. • Instruction Manual (this document) This manual explains hardware features and provides basic information about how to set up and operate the PSP® system, including instructions on how to download and start playing games. The manual also includes warnings and precautions for the safe and proper -
Instruction Manual
Online user's guide eu.playstation.com/psp/support/manuals PSP® official site eu.playstation.com/psp Support eu.playstation.com/support Instruction Manual PSP-E1002 © 2011 Sony Computer Entertainment Inc. All rights reserved. Printed in China PSP-E1003 4-294-406-51(1) Table of contents Warning and caution Support WARNING······················································ 4 Troubleshooting ··········································· 28 Precautions ···················································· 6 GUARANTEE ·············································· 33 Using the PSP® system Additional Information Part names and functions ···························· 10 Before disposing of or transferring the PSP® Charging the battery ···································· 12 system······················································ 37 Turning the system on and off ····················· 15 Specifications··············································· 38 Using the XMB™ (XrossMediaBar) menu ····· 16 Compatible media ········································ 40 Playing Universal Media Disc games ··········· 18 Copyright and trademarks ··························· 42 Playing Memory Stick Duo™ content ············ 19 Using the on-screen keyboard ····················· 20 Setting the parental control level·················· 22 Updating the system software ····················· 24 Downloading games ···································· 26 2 Table of contents PSP® system documentation You can find information about the PSP® system in this manual as well -
Analysis of Innovation in the Video Game Industry
Master’s Degree in Management Innovation and Marketing Final Thesis Analysis of Innovation in the Video Game Industry Supervisor Ch. Prof. Giovanni Favero Assistant Supervisor Ch. Prof. Maria Lusiani Graduand Elena Ponza Matriculation number 873935 Academic Year 2019 / 2020 I II Alla mia famiglia, che c’è stata quando più ne avevo bisogno e che mi ha sostenuta nei momenti in cui non credevo di farcela. A tutti i miei amici, vecchi e nuovi, per tutte le parole di conforto, le risate e la compagnia. A voi che siete parte di me e che, senza che vi chieda nulla, ci siete sempre. Siete i miei fiorellini. Senza di voi tutto questo non sarebbe stato possibile. Grazie, vi voglio bene. III IV Abstract During the last couple decades video game consoles and arcades have been subjected to the unexpected, swift development and spread of mobile gaming. What is it though that allowed physical platforms to yet maintain the market share they have over these new and widely accessible online resources? The aim of this thesis is to provide a deeper understanding of the concept of innovation in the quickly developing world of video games. The analysis is carried out with qualitative methods, one based on technological development in the context of business history and one on knowledge exchange and networking. Throughout this examination it has been possible to explore what kind of changes and innovations were at first applied by this industry and then extended to other fields. Some examples would be motion control technology, AR (Augmented Reality) or VR (Virtual Reality), which were originally developed for the video game industry and eventually were used in design, architecture or in the medical field. -
A Survey of Emedia-Delivered Interventions for Schizophrenia Used in Randomized Controlled Trials
Journal name: Neuropsychiatric Disease and Treatment Article Designation: Original Research Year: 2017 Volume: 13 Neuropsychiatric Disease and Treatment Dovepress Running head verso: Naeem et al Running head recto: eMedia-delivered interventions open access to scientific and medical research DOI: http://dx.doi.org/10.2147/NDT.S115897 Open Access Full Text Article ORIGINAL RESEARCH A survey of eMedia-delivered interventions for schizophrenia used in randomized controlled trials Farooq Naeem1 Background: Randomized trials evaluating electronic Media (eMedia) delivery of interventions are Tariq Munshi1 increasingly frequent in mental health. Although a number of reviews have reported efficacy of these Shuo Xiang1 interventions, none has reviewed the type of eMedia interventions and quality of their description. Megan Yang1 We therefore decided to conduct a survey of eMedia-delivered interventions for schizophrenia. Farhad Shokraneh2 Methods: We surveyed all relevant trials reliably identified in the Cochrane Schizophrenia Group’s Yumeen Syed3 comprehensive register of trials by authors working independently. Data were extracted regarding the size of the trial, interventions, outcomes and how well the intervention was described. Muhammad Ayub1 Results: eMedia delivery of interventions is increasingly frequent in trials relevant to the Clive E Adams4 care of people with schizophrenia. The trials varied considerably in sample sizes (mean =123, 5 Saeed Farooq median =87, range =20–507), and interventions were diverse, rarely evaluating the same 1Department of Psychiatry, Queens approaches and were poorly reported. This makes replication impossible. Outcomes in these University, Kingston, ON, Canada; studies are limited, have not been noted to be chosen by end users and seem unlikely to be easy 2Institute of Mental Health, Nottingham, UK; 3Trenlogic, Toronto, to apply in routine care. -
Vývoj a Vzájemná Rivalita Nejvýznamnějších Auditivních a Audiovizuálních Datových Médií
Masarykova univerzita Filozofická fakulta Ústav české literatury a knihovnictví Kabinet informačních studií a knihovnictví Karel Musil Vývoj a vzájemná rivalita nejvýznamnějších auditivních a audiovizuálních datových médií Bakalářská diplomová práce Vedoucí práce: PhDr. Michal Lorenz 2009 Prohlašuji, že jsem diplomovou práci vypracoval samostatně s využitím uvedených pramenů a literatury. Současně dávám svolení k tomu, aby tato práce byla umístěna v knihovně FF MU a používána ke studijním účelům. V Brně 29. dubna 2009 2 Na tomto místě bych chtěl poděkovat vedoucímu práce PhDr. Michalu Lorenzovi za cenné rady a Doc. PhDr. Jiřímu Voráčovi, Ph.D. za připomínky z praxe. Za podporu děkuji i své rodině a přátelům. 3 Bibliografický záznam: MUSIL, Karel. Vývoj a vzájemná rivalita nejvýznamnějších auditivních a audiovizuálních datových médií. Brno: Masarykova Univerzita, Filozofická fakulta, Kabinet informačních studií a knihovnictví, 2009, 66 s. Vedoucí diplomové práce PhDr. Michal Lorenz. Anotace: Bakalářská diplomová práce Vývoj a vzájemná rivalita nejvýznamnějších auditivních a audiovizuálních datových médií se zabývá nejvýznamnějšími záznamovými médii posledních sta let a jejich bojem s konkurencí - Edisonovým fonografem počínaje a jeho bitvou s Berlinerovým gramofonem, vývojem magnetického pásku, historií CD a DVD, současnou bitvou mezi Blu-ray a HD-DVD a konečně i pohledem do budoucnosti – ponese-li se ve znamení holografického ukládání dat, či přímo stahování obsahu z internetu bez prostředníků v podobě fyzických nosičů. Zároveň se pokouší přinést odpověď na otázku, jaké faktory ovlivňují úspěch či neúspěch formátu, který se chce ve své oblasti stát dominantním. V práci se rovněž zamýšlím nad vlivem pornografie jakožto významným faktorem ovlivňující komerční úspěch (audiovizuálního) datového média. Abstract: My Bachelor’s thesis deals with the history, development and mutual rivalry (aka format war) of the most significant data storage media of the last one hundred years. -
Pbcore Handbook Section 7
Controlled Vocabularies PBCore Controlled Vocabularies are sets of predefined, community-standardized terms for concepts related to audiovisual and broadcast collections. These terms can be used as drop-down value lists in a database or spreadsheet to ensure consistency in terminology, formatting and spelling, both internally and when exchanging information with outside organizations. PBCore Controlled Vocabularies include the agreed-upon spelling and formatting for each term, a definition, and a Unique Resource Identifier (or URI). The vocabularies provide only the terms that the community has determined are most widely used and shared, and are not 100% comprehensive. PBCore does not maintain controlled vocabularies for elements that have strong vocabulary options maintained by other authorities. Element definitions contain references to relevant external vocabularies, where applicable. pbcoreAssetTypeVocabulary Usage: for pbcoreAssetType Album Definition: A collection of recordings issued as a single item on CD, record, or another medium. URI: http://pbcore.org/pbcore-controlled-vocabularies/pbcoreassettype-vocabulary/#Album Animation Definition: A moving image production element created from static drawings or objects. URI: http://pbcore.org/pbcore-controlled-vocabularies/pbcoreassettype-vocabulary/#Animation Clip Definition: A short excerpt taken from a moving image or audio resource. A clip may not convey a complete intellectual concept. URI: http://pbcore.org/pbcore-controlled-vocabularies/pbcoreassettype-vocabulary/#Clip Collection Definition: A group of materials with some unifying characteristic. – 2. Materials assembled by a person, organization, or repository from a variety of sources; an artificial collection. URI: http://pbcore.org/pbcore-controlled-vocabularies/pbcoreassettype-vocabulary/#Collection Compilation Definition: A single asset containing multiple different sub-assets; for example, a reel with programs, clips, and raw footage. -
Hacking the PSP™
http://videogames.gigcities.com 01_778877 ffirs.qxp 12/5/05 9:29 PM Page i Hacking the PSP™ Cool Hacks, Mods, and Customizations for the Sony® PlayStation® Portable Auri Rahimzadeh 01_778877 ffirs.qxp 12/5/05 9:29 PM Page i Hacking the PSP™ Cool Hacks, Mods, and Customizations for the Sony® PlayStation® Portable Auri Rahimzadeh 01_778877 ffirs.qxp 12/5/05 9:29 PM Page ii Hacking the PSP™: Cool Hacks, Mods, and Customizations for the Sony® PlayStation® Portable Published by Wiley Publishing, Inc. 10475 Crosspoint Boulevard Indianapolis, IN 46256 www.wiley.com Copyright © 2006 by Wiley Publishing, Inc., Indianapolis, Indiana Published simultaneously in Canada ISBN-13: 978-0-471-77887-5 ISBN-10: 0-471-77887-7 Manufactured in the United States of America 10 9 8 7 6 5 4 3 2 1 1B/SR/RS/QV/IN No part of this publication may be reproduced, stored in a retrieval system or transmitted in any form or by any means, electronic, mechanical, photocopying, recording, scanning or otherwise, except as permitted under Sections 107 or 108 of the 1976 United States Copyright Act, without either the prior written permission of the Publisher, or authorization through payment of the appropriate per-copy fee to the Copyright Clearance Center, 222 Rosewood Drive, Danvers, MA 01923, (978) 750-8400, fax (978) 646-8600. Requests to the Publisher for permission should be addressed to the Legal Department, Wiley Publishing, Inc., 10475 Crosspoint Blvd., Indianapolis, IN 46256, (317) 572-3447, fax (317) 572-4355, or online at http://www.wiley.com/go/permissions. -
Introducing Critical Media Studies
See discussions, stats, and author profiles for this publication at: https://www.researchgate.net/publication/286459828 Introducing Critical Media Studies Chapter · January 2014 CITATIONS READS 0 1,284 2 authors, including: Brian L. Ott Texas Tech University 55 PUBLICATIONS 455 CITATIONS SEE PROFILE Some of the authors of this publication are also working on these related projects: Affect View project All content following this page was uploaded by Brian L. Ott on 11 December 2015. The user has requested enhancement of the downloaded file. 1 Introducing Critical Media Studies KEY CONCEPTS CONVERGENCE CRITICAL MEDIA STUDIES MOBILITY FRAGMENTATION POSTMODERNITY GLOBALIZATION SOCIALIZATION MASS MEDIA THEORY MEDIUM SIMULATION How We Know What We Know Everything we know is learned in one of two ways.1 The first way is somatically. These are the things we know through direct sensory perception of our environment. We know what some things look, smell, feel, sound, or taste like because we person- ally have seen, smelled, felt, heard, or tasted them. One of the authors of this text knows, for example, that “Rocky Mountain oysters” (bull testicles) are especially chewy because he tried them once at a country and western bar. In short, some of what we know is based on first-hand, unmediated experience. But the things we know through direct sensory perception make up a very small percentage of the total things we know. TheCOPYRIGHTED vast majority of what we know comesMATERIAL to us a second way, symbolically. These are the things we know through someone or something such as a parent, friend, teacher, museum, textbook, photograph, radio, film, television, or the internet. -
Java Nonprint Materials Data Entry Guidelines
Data Entry Guidelines for Nonprint Materials Last Updated July 20, 2011 Nonprint Materials General Guidelines for All Nonprint Materials ......................6 Searching Workflows .............................................................6 Key Parts of the Item that Must Match an Existing Record.................6 How to Find the Title Control Number of a Record ................7 Attaching a Copy to Records in Workflows ..........................8 ISBN 020 field .....................................................................8 UPC 024 field......................................................................8 Music No. 028 field ...............................................................8 Personal Author 100 field .......................................................8 Title 245 field .....................................................................9 Edition 250 field ..................................................................9 Publication 260 field .............................................................9 Physical Description 300 field ................................................ 10 Updating Records that are in the ACQ Format .................... 11 Updating 9xx Records ................................................. 14 Subfield Z in Call Numbers ........................................... 17 When should Subfield Z be used in the call number? ..................... 17 How does Subfield Z work? .................................................... 17 Why the policy with the required wording after Subfield -
The Makeover from DVD to Blu-Ray Disc
Praise for Blu-ray Disc Demystified “BD Demystified is an essential reference for designers and developers building with- in Blu-ray’s unique framework and provides them with the knowledge to deliver a compelling user experience with seamlessly integrated multimedia.” — Lee Evans, Ambient Digital Media, Inc., Marina del Rey, CA “Jim’s Demystified books are the definitive resource for anyone wishing to learn about optical media technologies.” — Bram Wessel, CTO and Co-Founder, Metabeam Corporation “As he did with such clarity for DVD, Jim Taylor (along with his team of experts) again lights the way for both professionals and consumers, pointing out the sights, warning us of the obstacles and giving us the lay of the land on our journey to a new high-definition disc format.” — Van Ling, Blu-ray/DVD Producer, Los Angeles, CA “Blu-ray Disc Demystified is an excellent reference for those at all levels of BD pro- duction. Everyone from novices to veterans will find useful information contained within. The authors have done a great job making difficult subjects like AACS encryption, BD-Java, and authoring for Blu-ray easy to understand.” — Jess Bowers, Director, Technical Services, 1K Studios, Burbank, CA “Like its red-laser predecessor, Blu-ray Disc Demystified will immediately take its rightful place as the definitive reference book on producing BD. No authoring house should undertake a Blu-ray project without this book on the author’s desk. If you are new to Blu-ray, this book will save you time, money, and heartache as it guides the DVD author through the new spec and production details of producing for Blu-ray.” — Denny Breitenfeld, CTO, NetBlender, Inc., Alexandria, VA “An all in one encyclopedia of all things BD.” — Robert Gekchyan, Lead Programmer/BD Technical Manager Technicolor Creative Services, Burbank, CA About the Authors Jim Taylor is chief technologist and general manager of the Advanced Technology Group at Sonic Solutions, the leading developer of BD, DVD, and CD creation software. -
DVD 010 Intro.Pdf
Copyright © 2003-2010 Hans Gerlitz. All rights reserved. www.pinkfloyd-forum.de/discography [email protected] This discography is a reference guide, not a book on the artwork of Pink Floyd. The photos of the artworks are used solely for the purposes of distinguishing the differences between the releases. The product names used in this document are for identification purposes only. All trademarks and registered trademarks are the property of their respective owners. Permission is granted to download and print this document for personal use. Any other use including but not limited to commercial or profitable purposes or uploading to any publicly accessibly web site is expressly forbidden without prior written consent of the author. NOTES ON DVD DISCOGRAPHY EUROPE USA JAPAN APPENDIX: Unauthorized VCD Laserdisc PINK FLOYD DVD DISCOGRAPHY Notes on DVD discography By Hans Gerlitz. DVD DISCOGRAPHY Only one Pink Floyd related title was released on HD DVD: The crime drama The Departed with the song Comfortably Numb performed by Roger Waters. You can find the HD This discography includes the official releases of Pink DVD issues in the main part of the discography. Nearby Floyd, band members and related video material on DVDs the description of each HD DVD issue you can see the HD and other optical discs. DVD logo. Counterfeits, pirates and bootlegs are not included. Blu-ray Order Blu-ray, also known as Blu-ray Disc (BD), is the name of an another high-density optical The sequence of this discography are not always disc format. Blu-ray discs offers more than according to the actual sequence of the editions, because five times the storage capacity of traditional DVDs and can some editions were released almost simultaneously.