Packaging Engineers Guide.Pdf
Total Page:16
File Type:pdf, Size:1020Kb
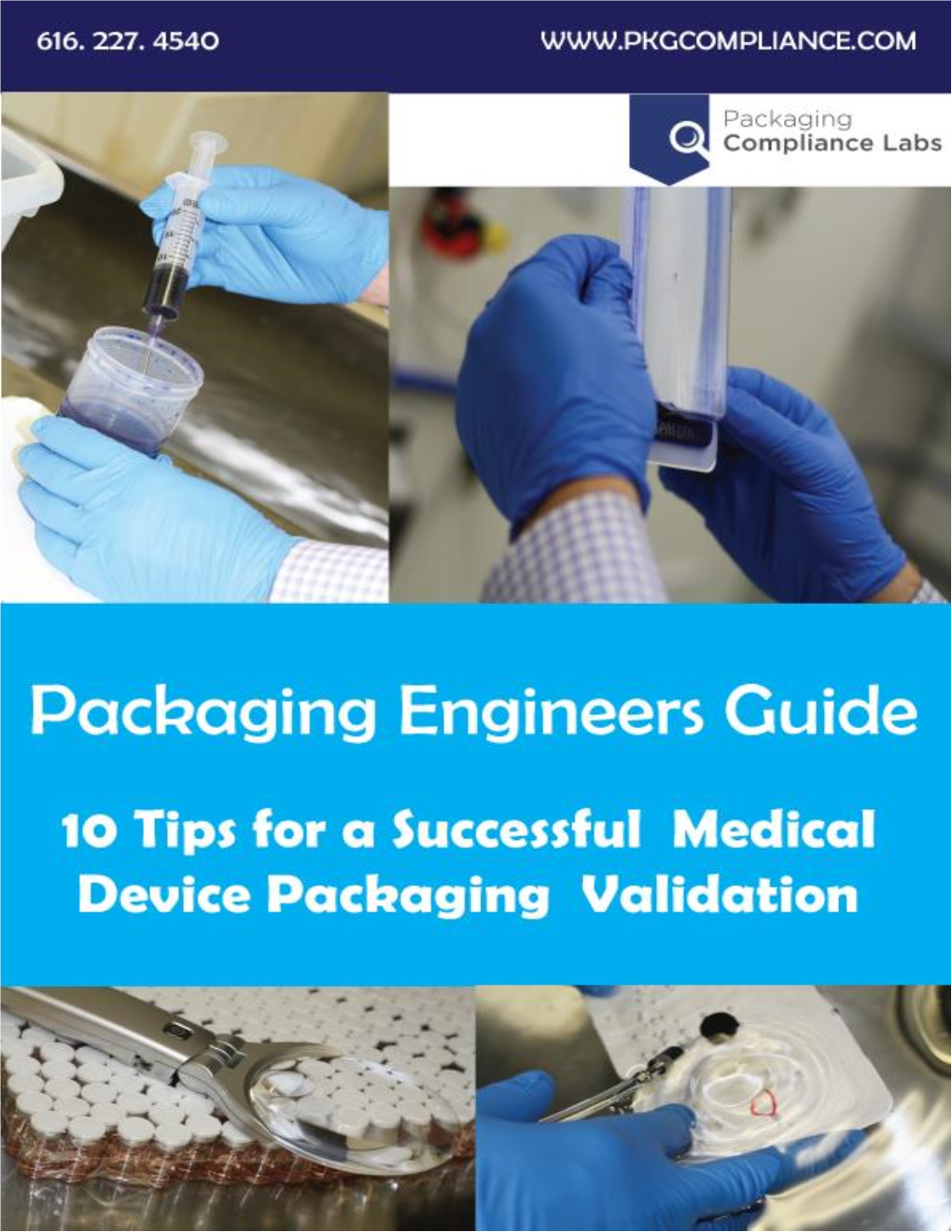
Load more
Recommended publications
-
Hi-TECH TOOLS CODING SYSTEMS
COCOON PRINT PACK SYSTEMS Reg.Off: 16A-Old Nagardas Road ,Tiwari Compound, Near Krishna Dyeing Works, Andheri (E),Mumbai -400069 Mobile N0- (0) 9224277155 Email: - cocoonprintpack @ gmail . com Web: - www.sealing-machine.co.in Profile We are manufacturing of Coding, Batch Printing, Box Strapping, Liquid Filling, Sealing & Packaging, and Form Fill Seal Machines. specially referring to machinery for industries such as food, pharmaceutical, beverages, Oil, Milk, cosmetics, Spices, distillery etc. the name Seal-Tech Coding Systems. Stands out for sheer quality of its products. Our Products Batch Printing Machines o Electro Mechanical Motorized Table Top Coder o Ink Jet Printers o Auto speed Continuous On-Line Batch o Handy Marker Coder o Hand Stamping Machine Sealing Machine o Shrink Pack Sealing Machine o Vacuum Sealing Machine ( Single / Double Chember) o Handy Induction Sealing Machine / Continous Induction Sealing Machine o Continuous (Online) Sealing Machine o Hand Sealing Machine o Paddle Sealing machine Strapping & Tapping Machines o Automatic Carton (Box) Strapping Machine o Semi Automatic Carton (Box) Strapping Machine o Carton Tapping Machine Labelling Machine (Semi Automatic) Liquid Filling Machine (Semi Automatic) (FFS) Form Fill Seal Machine Manual Cup Sealer Bar Coder Hot Air Gun Ink Jet Printers model no:- IJP - P 2128 COCOON presents HONAZ / SORVEH (Canada, Dubai) make Industrial Inkjet Printer Model IJP - P 2128 which is an economical, no maintenance , user friendly, high resolution FOUR line Non-Contact printer that can be installed on any production line to print B.No., Mfg. Date, Exp. Date, MRP Rs., Logos, Bar Codes, Real Time Clock & Calendar, Serial No. (Agmark) etc. on bottles, tins, labels, cartons, caps, pouches, etc. -
Condiments – the Power and Potential of Packaging
White Paper Condiments – the power and potential of packaging More than just a sauce Condiments and sauces can be seen on dinner tables A brief walk through any food store shows just how popular across the globe. Although often overlooked, they can be condiments have become over the years. Much time and key in adding colour, texture, taste and flavour to what is investment is given to attracting the attention of shoppers being consumed. However, the actual taste experience is in the condiments aisle and keeping them coming back for often determined as much by the packaging and branding more. Despite its significant size, the global condiments of the product as by its contents1. With packaging playing a market is projected to continue to expand, reaching USD key role in customer satisfaction and purchasing decisions2, 98.3 billion by 2024 and growing at a significant CAGR of what can manufacturers learn from consumer purchasing 5.4% during the forecast period, 2019–2024.3 behaviour and how has packaging evolved to cope with the many demands now being placed on it? The psychology of condiment packaging With competition fierce for shelf space, condiments A growing market producers have had to get ever-more creative in how Since salt and vinegar were first used to enhance the they attract shoppers to their products. Here are some flavour of foods in ancient times, people have been hooked of the ways that psychology plays a part in condiments on condiments. From the Roman practice of crushing the packaging design. innards of various fish and fermenting them in salt to create garum, to today’s brightly coloured ketchups and mustards, Capturing consumer attention: a flourishing industry has grown. -
Medical Device Packaging: Innovations in Design and Testing
2nd Annual MEDICAL DEVICE PACKAGING: INNOVATIONS IN DESIGN AND TESTING APRIL 30 - MAY 1, 2015 | BETHESDA, MD Optimizing Medical Device Package Design through Incorporating End User Feedback, Leveraging Legacy Testing Studies & Identifying Innovative Materials, while Maintaining Validation & Verification Standards through Examining Test Methods to Satisfy Global Regulatory Expectations DISTINGUISHED PRESENTERS INCLUDE: Abhishek Gautam Daniel Burgess Dhuanne Dodrill Manager, Packaging Engineering Principal Packaging Engineer Chairman CONMED CORPORATION BOSTON SCIENTIFIC ASTM INTERNATIONAL COMMITTEE F02 Catherine Olson, MSN, RN Charlie Rivera Director, Institute for Quality, Safety and Corporate Packaging Operations Manager A.J. Gruber Injury Prevention CONMED CORPORATION Executive Vice President EMERGENCY NURSES ASSOCIATION ISTA Nora Crivello Philip Desjardins Vice President Dawn Fowler Counsel WESTPAK INC. Senior Manager, Labeling & ARNOLD & PORTER LLC Documentation Shirley Gibson ENDOLOGIX Michael H. Scholla, Ph.D. Associate Vice President of Nursing Global Director, Regulatory and VCU HEALTH SYSTEM Tomas Pla Standard Sr. Development Packaging Engineer DUPONT PACKAGING Paul Marshall EXACTECH Manager, Global Packaging Art Castronovo Technologies Jonathan Bull Dir. of Labeling and Packaging SMITH & NEPHEW Director Gas and Heat Sterilization Engineering JOHNSON & JOHNSON SMITHS MEDICAL Santosh Madival Sr. Packaging Engineer Rod Patch Rients Van Werven EDWARDS LIFESCIENCES Senior Director, Execution Excellence Manager GSG Package Development COE Packaging and Product Labeling Ron Valerio JOHNSON & JOHNSON ETHICON ENDO-SURGERY Sr. Manager Medical UFP TECHNOLOGIES Darian Flewellen Dawn Hamblett Development Engineer, Packaging OR Clinical Product Coordinator Maimunatu Mansaray EXACTECH GEORGE WASHINGTON Operating Room Nurse UNIVERSITY HOSPITAL HOWARD UNIVERSITY HOSPITAL Alison Tyler Director of Technology Katie Tran Ewald Heersema BEACON CONVERTERS, INC. Lab Supervisor Technical Business Manager WESTPAK ZOTEFOAMS INC Chetan Patadiya Sr. -
Food Packaging Technology
FOOD PACKAGING TECHNOLOGY Edited by RICHARD COLES Consultant in Food Packaging, London DEREK MCDOWELL Head of Supply and Packaging Division Loughry College, Northern Ireland and MARK J. KIRWAN Consultant in Packaging Technology London Blackwell Publishing © 2003 by Blackwell Publishing Ltd Trademark Notice: Product or corporate names may be trademarks or registered Editorial Offices: trademarks, and are used only for identification 9600 Garsington Road, Oxford OX4 2DQ and explanation, without intent to infringe. Tel: +44 (0) 1865 776868 108 Cowley Road, Oxford OX4 1JF, UK First published 2003 Tel: +44 (0) 1865 791100 Blackwell Munksgaard, 1 Rosenørns Allè, Library of Congress Cataloging in P.O. Box 227, DK-1502 Copenhagen V, Publication Data Denmark A catalog record for this title is available Tel: +45 77 33 33 33 from the Library of Congress Blackwell Publishing Asia Pty Ltd, 550 Swanston Street, Carlton South, British Library Cataloguing in Victoria 3053, Australia Publication Data Tel: +61 (0)3 9347 0300 A catalogue record for this title is available Blackwell Publishing, 10 rue Casimir from the British Library Delavigne, 75006 Paris, France ISBN 1–84127–221–3 Tel: +33 1 53 10 33 10 Originated as Sheffield Academic Press Published in the USA and Canada (only) by Set in 10.5/12pt Times CRC Press LLC by Integra Software Services Pvt Ltd, 2000 Corporate Blvd., N.W. Pondicherry, India Boca Raton, FL 33431, USA Printed and bound in Great Britain, Orders from the USA and Canada (only) to using acid-free paper by CRC Press LLC MPG Books Ltd, Bodmin, Cornwall USA and Canada only: For further information on ISBN 0–8493–9788–X Blackwell Publishing, visit our website: The right of the Author to be identified as the www.blackwellpublishing.com Author of this Work has been asserted in accordance with the Copyright, Designs and Patents Act 1988. -
Packaging Engineering at Rutgers
Packaging Engineering at Rutgers ackaging engineers formulate and construct innova- tive packaging systems that increase functionality through the development of materials, design, evalu- Pation, manufacturing process, distribution, and sustainability components. They also address factors related to shelf life, tamper resistance, and quality. Packaging engineers collabo- Packaging Engineering Degrees rate with colleagues in research and development, manu- Offered and Curricular Options facturing, marketing, graphic design, and regulatory depart- ments to address technical and marketing challenges. % BS Applied Sciences in Engineering 10 0 Packaging Engineering Concentration The Rutgers Packaging Engineering program is the second EMPLOY- oldest in the nation and has the distinction of being the only MENT BS/MS Five-Year Dual Degree packaging program housed within an engineering school. PAST BS/MBA Five-Year Dual Degree 10 YEARS Student learning includes a multi-disciplinary curriculum MS drawing from the fields of chemical, industrial, materials, and mechanical engineering, as well as hands-on research, control testing, and product design with actual industry mate- rials, products, and lab equipment. The program opens doors to rewarding packaging careers in industries as diverse as consumer goods, cosmetics, food, and pharmaceuticals with Packaging Engineering a unique focus on innovation, efficiency, global marketability, Highlights and environmental sustainability. » Only US packaging program housed within “Packaging an engineering school. engineering has » Faculty members include senior execu- provided me with a tives from major beauty, consumer product, variety of learning pharmaceutical and food manufacturing and internship corporations. opportunities that » State-of-the-art laboratory facilities for 3D will help me reach design, modeling, and tool cutting software my full potential to create original product packaging. -
Packaging Technology
PACKAGING TECHNOLOGY KAZAKH NATIONAL AGRARIAN UNIVERSITY ALMATY, KAZAKHSTAN 19 - 30 OCT. 2015 by ROSNITA A. TALIB BSc (Food Sc & Tech), MSc. (Packaging Engineering) UPM PhD (Materials Engineering) Sheffield, UK. Department of Process and Food Engineering Faculty of Engineering 43400 UPM Serdang, Selangor Universiti Putra Malaysia Email: [email protected] Course Outcomes Students are able to : 1. To describe the functions, basic packaging design elements and concepts 2. To analyse various types of packaging materials for use on appropriate food 3. To differentiate standard test methods for packaging quality control 4. Describe various types of packaging equipment in food industry References/Textbooks 1. Soroka, W. (2009) Fundamentals of Packaging Technology. Naperville. Instituue of Packaging Professionals. 2. Klimchuk, M.R. and Krasovec, S.A. (2006) Packaging Design Successful Product Branding from Concept to Shelf. Hoboken. John Wileys & Sons 3. Morris, S.A. (2010). Food Packaging Engineering. Iowa: Blackwell Publishing Professional. 4. Robertson, G.L. (2006). Food Packaging - Principles and Practice (2nd Edition). Boca Raton: CRC Press. 5. Kelsey, R.J. (2004). Handbook of Package Engineering (4th Edition). Boca Raton: CRC Press. Package vs Packaging - Simple examples of package: boxes on the grocer's shelf and wrapper on a candy bar. - The crate around a machine or a bulk container for chemicals. - Generically, package is any containment form. - Package (noun) is an object. A physical form that is intended to contain, protect/preserve; aid in safe, efficient transport and distribution; and finally act to inform and motivate a purchase decision on the part of a consumer. Package vs Packaging Packaging is Packaging also - Packaging is a verb, reflecting the ever-changing nature of the The development and production of medium. -
CONFERENCE PROGRAMME @Eubioplastics #Eubpconf2016
CONFERENCE PROGRAMME @EUBioplastics #eubpconf2016 PLATINUM SPONSOR GOLD SPONSORS 29/30 November 2016 Steigenberger Hotel, Berlin SILVER SPONSOR Your contact: European Bioplastics Joanna Wilde hosted by Marienstraße 19/20 10117 Berlin +49 30 28482 358 [email protected] BRONZE SPONSORS 11th European Bioplastics Conference 29/30 November 2016, Berlin PROGRAMME - DAY 1 Thursday, 29 November 2016 08:00 Registration opens 09:00 Welcome address by the Chairman of the Board of European Bioplastics, François de Bie BIOPLASTICS POLICY – RETHINKING PLASTICS Chairperson: Joanna Dupont-Inglis, Director Industrial Biotechnology | EuropaBio 09:15 KEYNOTE PRESENTATION The potential of bioplastics in the course of the European Commission’s environment agenda Hugo-Maria Schally, Head of Unit ENV.B1 - Sustainable Production, Products & Consumption | European Commission DG Environment Mr Schally will address the need for a coherent policy approach to the bioeconomy. Against the background of the Commission’s Circular Economy Package and its main areas of ‘waste management‘, ‘biomass & bio-based products’ and ‘plastics’, Mr Schally will discuss the upcoming Plastics Strategy and the potential of reuse, recycling, and innovative products, to reduce greenhouse gas emissions and to prevent littering. 09:35 KEYNOTE PRESENTATION The European Commission’s R&D agenda for a Circular Bioeconomy Waldemar Kütt, Head of Unit Bio-based Products and Processing | European Commission DG Research & Innovation The bio-economy is a central part of a circular economy as it uses renewable and recyclable biological materials, including waste, and CO2. Bio-based products can replace fossil based products in a large number of industrial sectors, such as the energy, const- ruction, and chemicals sector. -
PACKAGING (Originalmente Publicado MDDI Octubre 2005 )
EL COSTO DE LA INTEGRIDAD DEL PACKAGING (Originalmente Publicado MDDI Octubre 2005 ) PACKAGING Medical device manufacturers often struggle to satisfy packaging requirements. However, examining five key issues can help them avoid potential pitfalls. By Michael B. Foster Many medical device manufacturers struggle to satisfy and maintain package integrity requirements while remaining cost-efficient. Such companies can save themselves time, money, and unnecessary headaches by examining key issues prior to developing their packaging. Although manufacturers may still come upon engineering and logistical problems along the way, these issues will more than likely be relatively small and manageable. In the long run, those firms that address the potential pitfalls discussed in this article will be well positioned to meet package integrity requirements. In a perfect world, every medical device manufacturer would have an engineer on staff with specialized knowledge about package design and all that it entails (e.g., package types, proper materials for specific situations, and validation testing). But in many cases, the task of designing a medical device's packaging is delegated to an engineer who is not familiar with packaging engineering and design. Considering that many medical device manufacturers are currently experiencing a shortage (or even absence) of qualified personnel, they can take major steps toward avoiding headaches while remaining within their budgets by addressing the following five issues: • Does the initial design of the packaging satisfy the needs of the specific device? • Is the packaging material the best one for the product? • Is the sample size sufficient to ensure adequate testing results? • Can the testing decisions be sufficiently justified to the necessary government organization? • Are the same testing parameters applied every time the same test is performed? In reality, a few of these questions are rhetorical, and as such, the answer is unfortunately often a no. -
ONE VARIETY, PLEASE Tubes, Bottles and All Lot Sizes from ADA International 4 EDITORIAL PREVIEW
consumer/nonwovens 01 | 2017 The OPTIMA Magazine MORE SERVICE, 10 MORE EFFICIENCY And more freedom: The new HMI TEA DOSING: 22 GENTLE ON THE LEAF The next trend in capsules is here ONE VARIETY, PLEASE Tubes, bottles and all lot sizes from ADA International 4 EDITORIAL PREVIEW IN USE 4 2 years of personalization in real-world applications Technical advantage for ADA International 14 Dosing packed with power 4 Sticking "vitamin bears" through the eye of a needle ADA Cosmetic GmbH: Even most of the niche markets today are dominated by 22 Trend: international competitors and are highly Tea in serving-size packages competitive. Hotel beauty products are Gentle and precise in the process no exception. The European market leader PRACTICAL RESEARCH ADA manages to combine both using packaging technology, quality, cost orienta- FOCUS: TECHNOLOGY SEEING INTO THE FUTURE? tion, customer service and flexibility. 10 The new HMI offers freedom of choice What hardware, Futuristic topics are once more a ma- that are proving their worth in practice at what functions? jor story in this o-com: Cobots, the next customer facilities. For instance, modular generations of HMIs and 3D printing. machine construction, which Optima Con- 19 3D printing at Optima Despite the variety in topics, the focus for sumer takes to its full potential with MOD- For rapid prototyping all projects lies unequivocally on practical ULINE. The system construction kit offers and complex small batches benefit. numerous solutions that are constantly Strategic decisions set the course being enhanced with new additions. 10 26 What are Cobots capable of? even before the beginning of new R&D This is where format flexibility and The helpers in action projects. -
Medical Device Packaging April 27-28, 2017 / Alexandria, Va June 26-27, 2017 / San Jose, Ca
6TH & 7TH SEMI-ANNUAL MEDICAL DEVICE PACKAGING APRIL 27-28, 2017 / ALEXANDRIA, VA JUNE 26-27, 2017 / SAN JOSE, CA Elevating Package Design of Medical Devices by Incorporating End User Feedback, Robust Testing Methods and Use of Innovative Materials to Reduce Cost, Ensure Safety and Surpass FDA and International Regulatory Expectations Program Overview: As medical devices have become increasingly complex, the intricacies of creating advanced packaging has progressed to ensure the continued safety and effectiveness of medical products. As such, medical device companies must consider a plethora of factors when designing and developing packaging, including human factors, sterility assurance, material characteristics and overall cost. Gathering as an industry provides packaging engineers an opportunity to hear innovative solutions for tackling the ongoing challenge of balancing cost and quality in packaging design and testing. The 6th and 7th Semi-Annual Medical Device Packaging Conferences will offer packaging engineers a comprehensive and interactive program through a series of case studies, panels and group discussions facilitated by industry, regulatory and end-user perspectives. Topics of greatest concern for medical device packaging teams will be addressed, including FDA’s expectations for documentation and audit preparation, hospital personnel insights on medical device storage, interpretations of ISO 11607 and effective distribution testing methods. Additionally, based on previous attendee feedback, the 2017 programs will feature a Materials Round-Up where participants will have the opportunity to learn about the latest technologies and materials available to advance medical device packaging. These sessions along with a workshop of nurses simulating the handling of medical devices in a hospital environment will provide attendees with a unique and invaluable experience. -
Discussion on the Control Technology in the Design of Packaging Machinery
Advances in Social Science, Education and Humanities Research (ASSEHR), volume 206 2018 International Conference on Advances in Social Sciences and Sustainable Development (ASSSD 2018) Discussion on the Control Technology in the Design of Packaging Machinery Gang Qiao 1School of Mechanical Engineering, Zhengzhou University of Industrial And Technology, 451100, China [email protected] Keywords: Packaging Machinery; Design; Control Technology Abstract: With the rapid development of China's economy, the number of enterprises in all walks of life is increasing.No matter food, daily necessities or large electrical appliances, any items should be packaged before they get out of the factory. Products of different quality and nature have different requirements for packaging. Some goods of special nature may require strict preservation of the environment. It is precisely because of the wide need for packaging, packaging has become a separate industry, and now its position is becoming more and more important in product chains. Good packaging can protect the goods from damage in the transportation and storage process, to avoid unnecessary economic losses. Packaging machinery plays an important role in the packaging process. The core content of packaging machinery, control technology, which is directly related to the quality of packaging, is fully discussed and studied in this paper. Preface Packaging machinery is an indispensable part of the packaging industry. The quality of packaging machinery is a very important factor which affects the quality of packaging and the efficiency of the factory production. The development of China's packaging industry is more backward than that in the West. The existing packaging technology and packaging machinery can not fully meet the requirements of the market for the types, quality, performance and number of packaging. -
Packaging Equipment List
DRUG PRODUCT Packaging Equipment List Complete pharmaceutical packaging services for product development, clinical trial materials and commercial supply. Solid-Dosage Bottle Packaging Fully integrated and automated bottling line with capabilities up to 60 bottles / min. PROCESS STEP EQUIPMENT CAPABILITIES Automated Bottle Kaps-All AU-3C Bottles are inverted, rinsed with ionized air, and vacuumed clean. Unscrambling and Cleaning Inserts packet style desiccants into bottles. Desiccant Inserter Multisorb APA-1000CB Dry air purge chamber and verification for desiccant placement. King TC8 Electronic Tablet Filling / Tablet Counting Individually counts each dosage unit into the bottle. Counter Filling / Tablet Counting IMA Swiftvision Individually counts each dosage unit into the bottle. Uses steel blades to cut exact lengths of coil filler and inserts Coil Inserter Lakso 52 into the bottle. Cut length from 2.5” to 7”. Sensor system for 100% inspection of presence and correct Cotton Inspection System Auto-Mate AM-D placement of coil filler. Uses pneumatic clutches to apply closures to specified Capper Kaps-All E4 torque levels. Induction Sealer AutoMate AM-250 Seals foil liners onto bottles. Uses pneumatic clutches to re-tighten closures to specified Re-torquer Kaps-All FE4 torque levels after induction sealing. Wrap around labeler to apply pressure sensitive labels to Labeler Quadrel Versaline round bottles. Vision system for 100% inspection of lot and expiry information. Limited to round or square bottles. Outserter Creative Automation 405 Glues outserts onto the tops of bottles. Bundling Equipment Eastey L-Bar Sealer and Heat Tunnel Forms, cuts, and shrinks bags of shrink film around bundles. Alcami Corporation Development Services • Analytical Testing • API • Drug Product +1 800.575.4224 www.alcaminow.com 08/2016 Blister Packaging High quality and flexible blister packaging lines with capabilities up to 225 blisters / min.