Technical Specification for LV Automation Applied to LV Engine Trail Sites
Total Page:16
File Type:pdf, Size:1020Kb
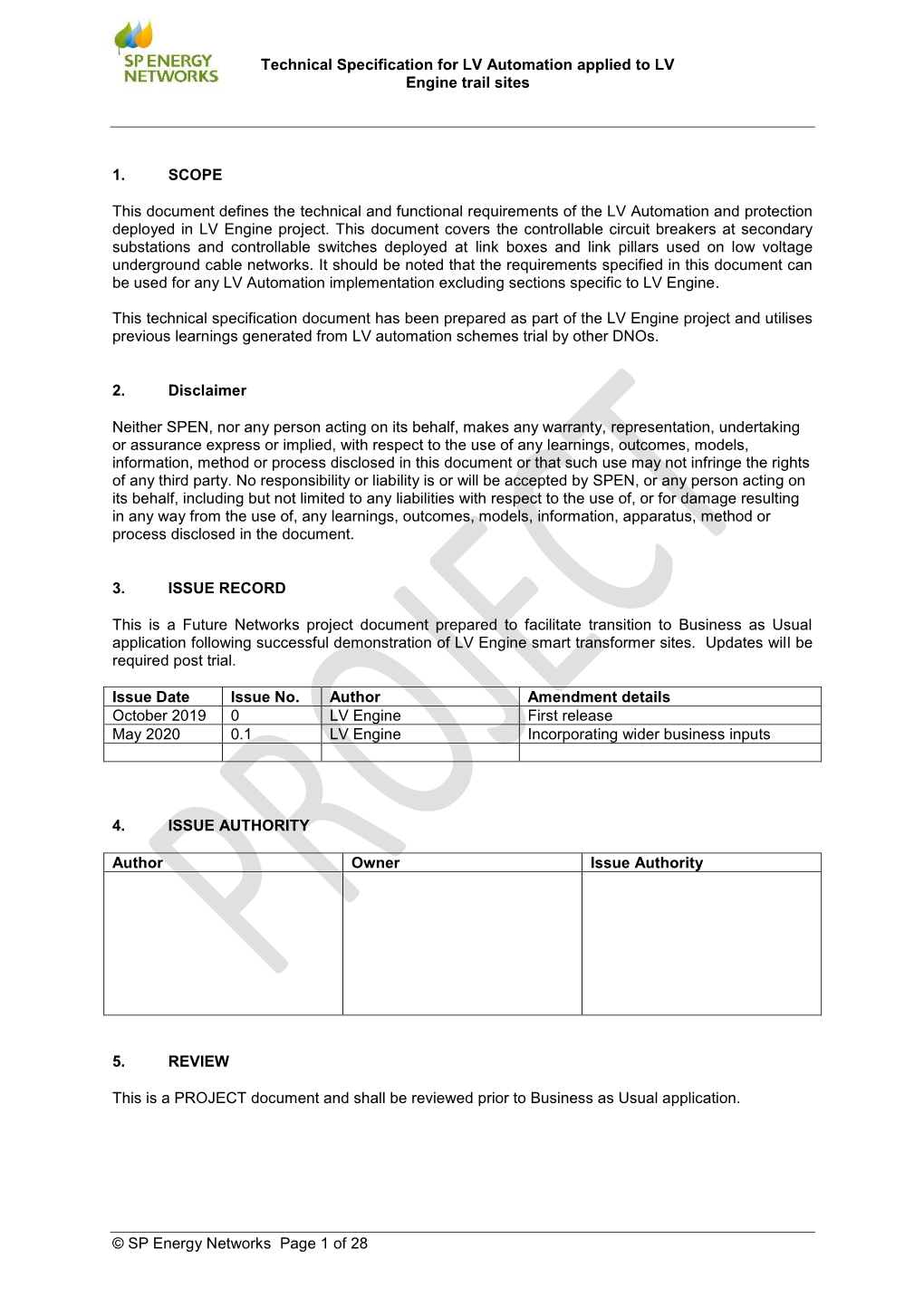
Load more
Recommended publications
-
Standards Published in 2007
IRISH STANDARDS PUBLISHED BASED ON CEN/CENELEC STANDARDS 1. I.S. CR 1100:1993 Date published 18 MARCH 2007 Memorandum on Health and Safety Standardization in Support of "New Approach" Directives – Application in the Field of Machinery 2. S.R. CR 1404:1994 Date published 18 MARCH 2007 Determination of Emissions from Appliances Burning Gaseous Fuels During Type- Testing 3. I.S. CR 12349:1996 Date published 18 MARCH 2007 Mechanical vibration - Guide to the health effects of vibration on the human body. 4. I.S. CR 12700:1997 Date published 18 MARCH 2007 Supporting document to ENV 1613:1994 - Messages for Exchange of Laboratory Information 5. CR 12787:19897 Date published 18 MARCH 2007 Status report on Diesel fuel lubricity 6. I.S. CR 1472:1997 Date published 18 MARCH 2007 General guidance for the marking of gas appliances 7. CR 12968:1997 Date published 18 MARCH 2007 Comparison document between Council Regulations (EEC) 1836/93 of June 1993 allowing voluntary participation by companies in the industrial sector in a Community eco-management and audit scheme, and the ISO 14000 series 8. I.S. CR 13033:1997 Date published 18 MARCH 2007 Personal protective equipment - Lifejackets and buoyancy aids - Guide for selection and use 9. CR 13058:1998 Date published 18 MARCH 2007 Medical Data Interchange: Mapping between the models specified in ENV 12539:1997 and NEMA PS3 Supplement 10 10. I.S. HD 632 S1:1999 Date published 15 FEBRUARY 2007 Power cables with extruded insulation and their accessories for rated voltages above 36 kV (Um = 42 kV) up to 150 kV (Um = 170 kV) 11. -
Pub Iec 2013-07
Vydané medzinárodné normy a iné publikácie IEC za obdobie od 1. 7. 2013 do 31. 7. 2013 IEC TC/SC Dokument Dátum Názov vydania TC 14 IEC 60076-SER 2013-07-31 Power transformers - ALL PARTS TC 14 IEC 60076-3 2013-07-31 Power transformers - Part 3: Insulation levels, dielectric tests and external clearances in air SC 34A IEC 60081-am5 2013-07-19 Amendment 5 - Double-capped fluorescent lamps - Performance specifications TC 95 IEC 60255-149 2013-07-30 Measuring relays and protection equipment - Part 149: Functional requirements for thermal electrical relays SC 32B IEC 60269-2 2013-07-11 Low-voltage fuses - Part 2: Supplementary requirements for fuses for use by authorized persons (fuses mainly for industrial application) - Examples of standardized systems of fuses A to K TC 40 IEC 60286-4 2013-07-26 Packaging of components for automatic handling - Part 4: Stick magazines for electronic components encapsulated in packages of different forms TC 33 IEC 60358-1 2013-07-16 Corrigendum 1 - Coupling capacitors and capacitor dividers - Part 1: General rules TC 15 IEC 60464-1 2013-07-31 Varnishes used for electrical insulation - Part 1: Definitions and general requirements TC 64 IEC/TR 60479-5 2013-07-11 Corrigendum 1 - Effects of current on human beings and livestock - Part 5: Touch voltage threshold values for physiological effects SC 62D IEC 60601-2-62 2013-07-09 Medical electrical equipment - Part 2-62: Particular requirements for the basic safety and essential performance of high intensity therapeutic ultrasound (HITU) equipment SC 62B IEC 60627 -
Standards Published in 2010
IRISH STANDARDS PUBLISHED BASED ON CEN/CENELEC STANDARDS 1. I.S. ENV 13710:2000 Date published 8 AUGUST 2010 European Ordering Rules - Ordering of characters from the Latin, Greek and Cyrillic scripts 2. I.S. ENV 13801:2000 Date published 8 AUGUST 2010 Plastics piping systems for soil and waste discharge (low and high temperature) within the building structure - Thermoplastics - Recommended practice for installation 3. I.S. CEN TS 13853:2004 Date published 13 FEBRUARY 2010 Swap bodies for combined transport – Stackable swap bodies type C 745-S16 – Dimensions, design requirements and testing 4. I.S. EN 61360-4:2005 Date published 7 JANUARY 2010 Standard data element types with associated classification scheme for electric components -- Part 4: IEC reference collection of standard data element types and component classes (IEC 61360-4:2005 (EQV)) 5. I.S. EN 1990:2002/A1:2006 Date published 29 MARCH 2010 Eurocode - Basis of structural design 6. I.S. EN 1991-4:2006 Date published 31 MARCH 2010 Eurocode 1 - Actions on structures - Part 4: Silos and tanks 7. I.S. EN 60512-13-5:2006/AC:2006 Date published 12 JANUARY 2010 Connectors for electronic equipment - Tests and measurements -- Part 13-5: Mechanical operation tests - Test 13e: Polarizing and keying method (IEC 60512-13 -5:2006 (EQV)) 8. I.S. EN 60034-9:2005/A1:2007 Date published 7 JANUARY 2010 Rotating electrical machines -- Part 9: Noise limits (IEC 60034-9:2003/A1:2007 (EQV)) 9. I.S. EN 548:2004/AC:2007 Date published 8 AUGUST 2010 Resilient floor coverings - Specification for plain and decorative linoleum 10. -
Lexium 32A 0198441113755 09/2017 0198441113755 32A Lexium
Lexium 32A 0198441113755 09/2017 Lexium 32A Servo Drive User Guide 09/2017 0198441113755.10 www.schneider-electric.com The information provided in this documentation contains general descriptions and/or technical character- istics of the performance of the products contained herein. This documentation is not intended as a substitute for and is not to be used for determining suitability or reliability of these products for specific user applications. It is the duty of any such user or integrator to perform the appropriate and complete risk analysis, evaluation and testing of the products with respect to the relevant specific application or use thereof. Neither Schneider Electric nor any of its affiliates or subsidiaries shall be responsible or liable for misuse of the information contained herein. If you have any suggestions for improvements or amendments or have found errors in this publication, please notify us. No part of this document may be reproduced in any form or by any means, electronic or mechanical, including photocopying, without express written permission of Schneider Electric. All pertinent state, regional, and local safety regulations must be observed when installing and using this product. For reasons of safety and to help ensure compliance with documented system data, only the manufacturer should perform repairs to components. When devices are used for applications with technical safety requirements, the relevant instructions must be followed. Failure to use Schneider Electric software or approved software with our hardware products may result in injury, harm, or improper operating results. Failure to observe this information can result in injury or equipment damage. © 2017 Schneider Electric. -
Guidance Notes for the Electrical Products (Safety) Regulation" (Hereinafter Referred to As "The Notes")
GuidanceGuidance NotesNotes forfor thethe ElectricalElectrical ProductsProducts (Safety)(Safety) RegulationRegulation 2019 Edition GUIDANCE NOTES FOR THE ELECTRICAL PRODUCTS (SAFETY) REGULATION 2019 EDITION CONTENTS CONTENTS CONTENTS Quick Summary Page 1 Introduction 1 2 Certificate of safety compliance 2 3 Safety requirements 3 4 Penalty 3 5 Checklists 4 A General Information A.1 Introduction 7 A.2 Products and suppliers affected by the Regulation 7 A.3 The safety requirements 8 A.4 Certificate of safety compliance 10 A.5 Advisory notes for suppliers 10 A.6 Enquiry 12 A.7 Acknowledgement 13 B The Regulation Part I Preliminary B.1 Commencement 15 B.2 Interpretation 15 B.3 Application to electrical products 21 Part II Safety Requirements B.4 Essential safety requirements for electrical products 22 B.5 Specific safety requirements for prescribed products 23 B.6 Applicable safety requirements for particular types of electrical 24 products Part III Certificate of Safety Compliance B.7 Certificate of safety compliance 28 B.8 Issue of certificate of safety compliance 30 Part IV Recognized Certification Bodies And Recognized Manufacturers B.9 Recognized certification bodies 34 B.10 Recognized manufacturers 37 CONTENTS Part V Director's Powers B.11 Director's powers 40 Part VI Offences And Penalties B.12 Offences 40 B.13 Penalties 41 B.14 Defence of due diligence 42 C Technical Guidance C.1 List of standards that are deemed to satisfy the applicable safety 45 requirements of the Regulation 1.1 Prescribed products 45 1.2 Non-prescribed products -
Návrhy Noriem IEC 2013-11
NÁVRHY NORIEM IEC PREDLOŽENÝCH NA VEREJNÉ PREROKOVANIE za obdobie od 1. novembra 2013 do 30. novembra 2013 Documents Title Closing Date 2/1728/FDIS IEC 60034-18-41 Ed.1: Rotating electrical machines - Part 18-41: Partial discharge free electrical insulation systems (Type I) used in rotating 2014-01-24 electrical machines fed from voltage converters - Qualification and quality control tests 2/1729/FDIS IEC 60034-30-1 Ed.1: Rotating electrical machines - Part 30-1: Efficiency classes of line operated AC motors (IE-code) 2014-01-24 2/1731/DTS IEC 60034-25 TS Ed.3: Rotating electrical machines - Part 25: A.C. electrical machines when used in powe drive systems - Application guide 2014-02-28 3D/221/CD IEC 61360-6/Ed.1:IEC Common Data Dictionary (IEC CDD) Quality guide 2014-02-21 9/1866A/FDIS IEC 62280: Railway applications - Communication, signalling and processing systems - Safety related communication in transmission systems 2014-01-03 9/1868/CD IEC 62845 Ed.1: Railway applications - Radio remote control system of traction vehicle for freight traffic 2014-02-07 10/936/FDIS IEC 62021-3: Insulating liquids - Determination of acidity - Part 3: Test methods for non-mineral insulating oils 2014-01-10 10/938/CD IEC 60376 Ed.3: Specification of technical grade sulfur hexafluoride (SF6) and complementary gases to be used in its mixtures for use in 2014-02-28 electrical equpment 13/1557/CD IEC 62056-8-6 ELECTRICITY METERING DATA EXCHANGE - THE DLMS/COSEM SUITE - Part 8-6: High speed PLC ISO/IEC 12139-1 2014-02-14 profile for neighbourhood networks -
Volume 52, No. 07, February 12, 2021
PUBLISHED WEEKLY BY THE AMERICAN NATIONAL STANDARDS INSTITUTE 25 WEST 43RD STREET NY, NY 10036 VOL. 52| NO. 7 February 12, 2021 CONTENTS American National Standards Project Initiation Notification System (PINS) ........................................................... 2 Call for Comment on Standards Proposals .............................................................. 8 Final Actions - (Approved ANS) .............................................................................18 Call for Members (ANS Consensus Bodies) ............................................................22 Accreditation Announcements (Standards Developers)..........................................27 American National Standards (ANS) Process ..........................................................29 ANS Under Continuous Maintenance ....................................................................30 ANSI-Accredited Standards Developer Contact Information ...................................31 International Standards ISO and IEC Draft Standards ..................................................................................34 ISO and IEC Newly Published Standards ................................................................38 International Organization for Standardization (ISO) ..............................................42 Registration of Organization Names in the United States ........................................44 Proposed Foreign Government Regulations ............................................................45 © 2021 by American National -
Standards Action Layout SAV3616.Fp5
PUBLISHED WEEKLY BY THE AMERICAN NATIONAL STANDARDS INSTITUTE 25 West 43rd Street, NY, NY 10036 VOL. 36, #16 April 22, 2005 Contents American National Standards Call for Comment on Standards Proposals................................................. 2 Call for Comment Contact Information ........................................................ 6 Initiation of Canvasses.................................................................................. 8 Final Actions .................................................................................................. 9 Project Initiation Notification System (PINS)............................................... 10 International Standards ISO and IEC Newly Published Standards..................................................... 13 Registration of Organization Names in the U.S. ........................................... 16 Proposed Foreign Government Regulations................................................. 16 Information Concerning .................................................................................. 17 Standards Action is now available via the World Wide Web For your convenience Standards Action can now be downloaded from the following web address: http://www.ansi.org/news_publications/periodicals/stan dards_action/standards_action.aspx?menuid=7 American National Standards Call for comment on proposals listed This section solicits public comments on proposed draft new American National Standards, including the national adoption of Ordering Instructions for "Call-for-Comment" -
Supplementary Requirements to IEC 61439-1 & 2 LV Switchgear
SPECIFICATION NOVEMBER S-560 2016 Supplementary Requirements to IEC 61439-1 & 2 LV Switchgear & Controlgear Acknowledgements This IOGP Specification was prepared by a Joint Industry Project 33 Standardization of Equipment Specifications for Procurement organized by IOGP with support by the World Economic Forum (WEF). Disclaimer Whilst every effort has been made to ensure the accuracy of the information contained in this publication, neither IOGP nor any of its Members past present or future warrants its accuracy or will, regardless of its or their negligence, assume liability for any foreseeable or unforeseeable use made thereof, which liability is hereby excluded. Consequently, such use is at the recipient’s own risk on the basis that any use by the recipient constitutes agreement to the terms of this disclaimer. The recipient is obliged to inform any subsequent recipient of such terms. This publication is made available for information purposes and solely for the private use of the user. IOGP will not directly or indirectly endorse, approve or accredit the content of any course, event or otherwise where this publication will be reproduced. Copyright notice The contents of these pages are © International Association of Oil & Gas Producers. Permission is given to reproduce this report in whole or in part provided (i) that the copyright of IOGP and (ii) the sources are acknowledged. All other rights are reserved. Any other use requires the prior written permission of IOGP. These Terms and Conditions shall be governed by and construed in accordance with the laws of England and Wales. Disputes arising here from shall be exclusively subject to the jurisdiction of the courts of England and Wales. -
Low Voltage Switchgear and Controlgear Technical Document
Low-Voltage Switchgear and Controlgear Technical Document 0-2 LVSAM-WP001A-EN-P - April 2009 Disclaimer The present document is designed to provide general technical information about the selection and application of low-voltage switching and control devices and does not claim to provide a comprehensive or conclusive presentation of the considered material. Errors or changes – for example as a consequence of changed standards or technical progress – cannot be excluded. This documentation has been worked out with utmost diligence. Nevertheless the authors and Rockwell Automation do not warrant the correctness of the contents and recommendations and cannot exclude typing errors. Claims on the authors or Rockwell Automation based on this documentation cannot be accepted. Rockwell Automation reserves the right to make changes at any time and at its own discretion. Correspondingly, qualified professional advice should be obtained before making decisions and initiating activities that could have an effect on technical equipment. The authors thank the International Electrotechnical Commission (IEC) for permission to reproduce information from its International Standard: IEC 60947-1 ed.5.0 (2007) / IEC 60947-4-1 Am2 (2005) / IEC 60947-2 ed.4.0 (2006) / IEC 60269-1 ed.4.0 (2006) / IEC 60947-8 ed.1.1 (2006) / IEC 60947-5-1 ed.3.0 (2003 ) / IEC 60038 ed.6.2 (2002) / IEC 60079-14 ed.4.0 (2007). All such extracts are copyright of IEC, Geneva, Switzerland. All rights reserved. Further information on the IEC is available from www.iec.ch. IEC has no responsibility for the placement and context in which the extracts and contents are reproduced by the authors, nor is IEC in any way responsible for the other content or accuracy therein. -
ITER Electrical Design Handbook Codes & Standards
ITR-20-005 ITER Electrical Design Handbook Codes & Standards Joel Hourtoule [email protected] 16 July 2020 ITR-20-005 ITER Electrical Design Handbook Codes & Standards This work is licensed under the Creative Commons Attribution-Noncommercial-NoDerivs 3.0 IGO-ported license. (CC BY-NC-ND 3.0 IGO) You are free to share this work (copy, distribute and transmit) under the following conditions: you must give credit to the ITER Organization, you cannot use the work for commercial purposes and you cannot modify it. For a full copy of this license visit: https://creativecommons.org/licenses/by-nc-nd/3.0/igo/. ITR-20-005 Introduction Terminology & Acronyms Codes and Standards ITR-20-005 Introduction Abstract This manual is provided for the use of all Departments of the ITER Organization and is addressed to system specifiers, designers and users of electrical components in otherwise non-electrical plant systems. This is an initial version of this document that has been reviewed in accordance with the ITER MQP. Review comments have in part been addressed and others will be considered in detail and addressed at the next revision. Introduction 1 ITR-20-005 Contents 1 Introduction ....................................................................................................................................... 3 1.1 Standard Voltages .......................................................................................................................... 5 1.1.1 Applicable IEC standards ............................................................................................................................. -
Catalog D 35 • June 2018
© Siemens AG 2018 SINAMICS Drives SINAMICS G120P and SINAMICS G120P Cabinet pump, fan, compressor converters Catalog Edition D 35 June 2018 siemens.com/drives © Siemens AG 2018 Related catalogs Motion Control Drives D 21.4 SIMATIC HMI / ST 80/ST PC SINAMICS S120 and SIMOTICS PC-based Automation Human Machine Interface Systems PC-based Automation E86060-K5521-A141-A1-7600 E86060-K4680-A101-C5-7600 SINAMICS G130 D 11 Industrial Communication IK PI Drive Converter Chassis Units SIMATIC NET SINAMICS G150 Drive Converter Cabinet Units E86060-K5511-A101-A6-7600 E86060-K6710-A101-B8-7600 Motion Control Drives D 31.1 SITRAIN SINAMICS Inverters for Single-Axis Drives Training for Industry Built-In Units E86060-K5531-A111-A1-7600 www.siemens.com/sitrain Motion Control Drives D 31.2 Products for Automation and Drives CA 01 SINAMICS Inverters for Single-Axis Drives Interactive Catalog Distributed Inverters Download E86060-K5531-A121-A1-7600 www.siemens.com/ca01download SIMOTICS S-1FG1 D 41 Industry Mall Servo geared motors Information and Ordering Platform Helical, Parallel shaft, Bevel and on the Internet: Helical worm geared motors E86060-K5541-A101-A3-7600 www.siemens.com/industrymall SIMOTICS GP, SD, XP, DP D 81.1 Low-Voltage Motors Additional information Type series 1FP1, 1LE1, 1MB1 and 1PC1 Frame sizes 71 to 315 You will find all the latest marketing materials, such as brochures Power range 0.09 to 200 kW and catalogs at E86060-K5581-A111-A9-7600 www.siemens.com/sinamics-g120p www.siemens.com/sinamics www.siemens.com/simotics SIMOTICS FD D81.8 www.siemens.com/ids Low-Voltage Motors Frame sizes 315 to 450 under "Information material (brochures, catalogs)".