A Study on Carbon-Nanotube Local Oxidation Lithography Using an Atomic Force Microscope Kitu Kumar, Onejae Sul, Stefan Strauf, Daniel S
Total Page:16
File Type:pdf, Size:1020Kb
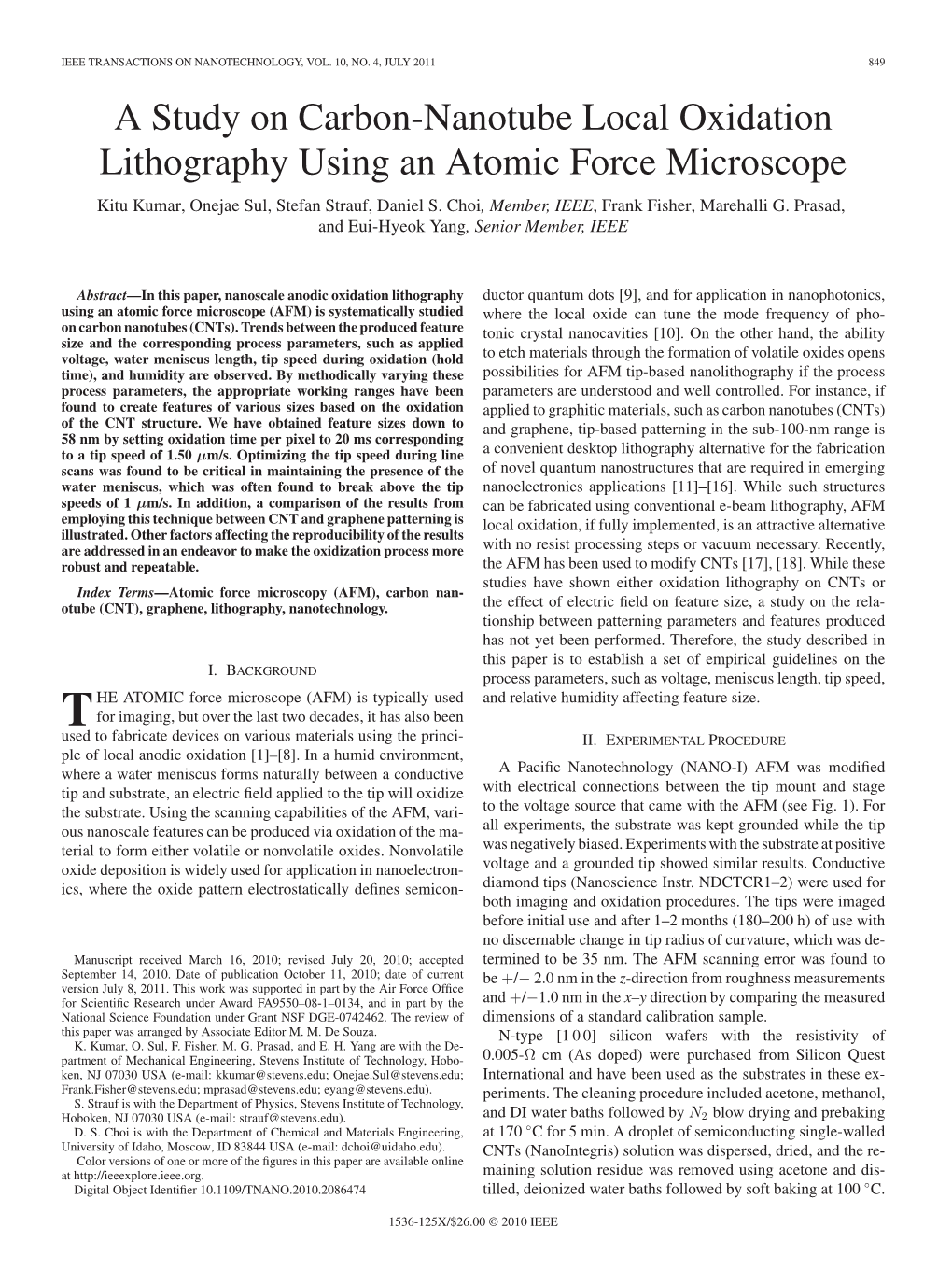
Load more
Recommended publications
-
Recent Applications of Advanced Atomic Force Microscopy in Polymer Science: a Review
polymers Review Recent Applications of Advanced Atomic Force Microscopy in Polymer Science: A Review Phuong Nguyen-Tri 1,2,*, Payman Ghassemi 2, Pascal Carriere 3, Sonil Nanda 4 , Aymen Amine Assadi 5 and Dinh Duc Nguyen 6,7 1 Institute of Research and Development, Duy Tan University, Da Nang 550000, Vietnam 2 Département de Chimie, Biochimie et Physique, Université du Québec à Trois-Rivières (UQTR), Trois-Rivières, QC G8Z 4M3, Canada; [email protected] 3 Laboratoire MAPIEM (EA 4323), Matériaux Polymères Interfaces Environnement Marin, Université de Toulon, CEDEX 9, 83041 Toulon, France; [email protected] 4 Department of Chemical and Biological Engineering, University of Saskatchewan, Saskatoon, SK S7N 5A2, Canada; [email protected] 5 ENSCR—Institut des Sciences Chimiques de Rennes (ISCR)—UMR CNRS 6226, Univ Rennes, 35700 Rennes, France; [email protected] 6 Faculty of Environmental and Food Engineering, Nguyen Tat Thanh University, 300A Nguyen Tat Thanh, District 4, Ho Chi Minh City 755414, Vietnam; [email protected] 7 Department of Environmental Energy Engineering, Kyonggi University, Suwon 16227, Korea * Correspondence: [email protected]; Tel.: +819-376-5011 (ext. 4505) Received: 5 March 2020; Accepted: 13 May 2020; Published: 17 May 2020 Abstract: Atomic force microscopy (AFM) has been extensively used for the nanoscale characterization of polymeric materials. The coupling of AFM with infrared spectroscope (AFM-IR) provides another advantage to the chemical analyses and thus helps to shed light upon the study of polymers. This paper reviews some recent progress in the application of AFM and AFM-IR in polymer science. -
Atomic Force Microscopy - Basics and Applications
Astrid Kronenberger School of Engineering and Science Atomic Force Microscopy - Basics and Applications Summer School June 2006 „Complex Materials: Cooperative Projects of the Natural, Engineering and Biosciences“ Outline • Scanning Probe Microscopy • Atomic Force Microscopy – General set-up & operation modes – Sample preparation • Applications in life science – Imaging mode –Force-distancemode •Conclusion Scanning Probe Microscopy (SPM) ~1600 Light Microscope 1938: Transmission Electron Microscope 1964: Scanning Electron Microscope 1982: Scanning Tunneling Microscope 1984: Scanning Near-field Optical Microscope 1986: Atomic Force Microscope - magnetic force, lateral force, chemical force... Scanning Probe Microscopy • Creates images of surfaces using a probe. • Probe is moved (scanned) over the sample. tip • Sample-probe interaction is monitored as function of location. sample + Image resolution limited by probe-sample interaction volume - not by diffraction . + Interaction can modify surface - nanolithography possible. - Scanning technique quite slow. - Limited maximum image size. Atomic Force Microscopy position laser sensitive beam detector cantilever with tip Molecular interaction: E = F Δs sample E ~ eV; Δs~ Å F ~ 2.10-9 N Typical AFM resolution: x-y: 1nm; z: 0.1nm Detection: - sub-Å deflection -pNforces General AFM set-up measure deflection controller quadrant laser photodiode Adjust tip- sample distance cantilever sample surface piezo x-y-z ceramic Moving tip / moving sample: Use U=+/- 220 V x-, y-axis: 1 ...125 µm z-axis: 1 ... 20 µm closed / open loop control Basic AFM modi • Imaging mode –contactmode –non contactmode – intermittent / tapping mode •Force-distancemode – force spectroscopy – combined imaging & force spectroscopy Static AFM modi •Contactmode: – tip in continuous contact with sample – preferably used for hard samples – imaging in air and liquid – high resolution detect: deflection • Force spectroscopy mode: – consecutive cycles of tip approach and retract – interaction forces between tip and sample are recorded . -
Introduction Scanning Probe Microscopy Techniques for Electrical and Electromechanical Characterization
University of Nebraska - Lincoln DigitalCommons@University of Nebraska - Lincoln Alexei Gruverman Publications Research Papers in Physics and Astronomy January 2007 Introduction Scanning Probe Microscopy Techniques for Electrical and Electromechanical Characterization Sergei Kalinin Oak Ridge National Laboratory, [email protected] Alexei Gruverman University of Nebraska-Lincoln, [email protected] Follow this and additional works at: https://digitalcommons.unl.edu/physicsgruverman Part of the Physics Commons Kalinin, Sergei and Gruverman, Alexei, "Introduction Scanning Probe Microscopy Techniques for Electrical and Electromechanical Characterization" (2007). Alexei Gruverman Publications. 43. https://digitalcommons.unl.edu/physicsgruverman/43 This Article is brought to you for free and open access by the Research Papers in Physics and Astronomy at DigitalCommons@University of Nebraska - Lincoln. It has been accepted for inclusion in Alexei Gruverman Publications by an authorized administrator of DigitalCommons@University of Nebraska - Lincoln. Published in: Scanning Probe Microscopy: Electrical and Electromechanical Phenomena at the Nanoscale, Sergei Kalinin and Alexei Gruverman, editors, 2 volumes (New York: Springer Science+Business Media, 2007). ◘ ◘ ◘ ◘ ◘ ◘ ◘ Sergei Kalinin, Oak Ridge National Laboratory Alexei Gruverman, University of Nebraska–Lincoln This document is not subject to copyright. Introduction Scanning Probe Microscopy Techniques for Electrical and Electromechanical Characterization s.Y. KALININ AND A. GRUVERMAN Progress in modem science is impossible without reliable tools for characteriza tion of structural, physical, and chemical properties of materials and devices at the micro-, nano-, and atomic scale levels. While structural information can be obtained by such established techniques as scanning and transmission electron microscopy, high-resolution examination oflocal electronic structure, electric po tential and chemical functionality is a much more daunting problem. -
Scanning Tunneling Microscope Control System for Atomically
Innovations in Scanning Tunneling Microscope Control Systems for This project will develop a microelectromechanical system (MEMS) platform technology for scanning probe microscope-based, high-speed atomic scale High-throughput fabrication. Initially, it will be used to speed up, by more than 1000 times, today’s Atomically Precise single tip hydrogen depassivation lithography (HDL), enabling commercial fabrication of 2D atomically precise nanoscale devices. Ultimately, it could be used to fabricate Manufacturing 3D atomically precise materials, features, and devices. Graphic image courtesy of University of Texas at Dallas and Zyvex Labs Atomically precise manufacturing (APM) is an emerging disruptive technology precision movement in three dimensions mechanosynthesis (i.e., moving single that could dramatically reduce energy are also needed for the required accuracy atoms mechanically to control chemical and coordination between the multiple reactions) of three dimensional (3D) use and increase performance of STM tips. By dramatically improving the devices and for subsequent positional materials, structures, devices, and geometry and control of STMs, they can assembly of nanoscale building blocks. finished goods. Using APM, every atom become a platform technology for APM and deliver atomic-level control. First, is at its specified location relative Benefits for Our Industry and an array of micro-machined STMs that Our Nation to the other atoms—there are no can work in parallel for high-speed and defects, missing atoms, extra atoms, high-throughput imaging and positional This APM platform technology will accelerate the development of tools and or incorrect (impurity) atoms. Like other assembly will be designed and built. The system will utilize feedback-controlled processes for manufacturing materials disruptive technologies, APM will first microelectromechanical system (MEMS) and products that offer new functional be commercialized in early premium functioning as independent STMs that can qualities and ultra-high performance. -
Atomic Force Microscopy*
Atomic force microscopy* Jason P. Killgore and Teresa L. Kirschling Applied Chemicals and Materials Division, National Institute of Standards and Technology, Boulder, CO 80305 I. What does the technique do? The atomic force microscope (AFM)[1] has become a universal tool for performing nanoscale characterization of surfaces. It has the resolution to image features as small as individual atoms [2], while still providing the range to investigate samples as large as several millimeters [3]. The AFM is part of a class of instruments known as scanning probe microscopes that also includes techniques such as scanning tunneling microscopy [4] and scanning near field optical microscopy [5] in addition to the more widely used atomic force microscopy. The AFM consists of a cantilever based sensor that is capable of detecting and responding to various forces that may arise between the sample and a sharpened tip located near the apex of the cantilever. The instrument has proven capable of measuring a broad range (in both magnitude and origin) of forces for a wide variety of applications. The earliest uses of the AFM were for topographic imaging of a sample surface. An image is created by scanning the cantilever tip back and forth across the sample (in a raster pattern), while recording the height of the surface. Compared to other techniques such as electron microscopies and tunneling microscopy with comparable spatial resolution, the AFM excels in its ability to image both conducting and insulating materials. The instrument is also capable of performing localized spectroscopy measurements * Publication of NIST, an agency of the US government, not subject to copyright and capturing spatially resolved maps of functional properties such as conductivity [6], elasticity [7] and adhesion [7]. -
Bruker AFM Training Notebook
SPM Training Notebook 004-130-000 (standard) 004-130-100 (cleanroom) Copyright © 2003 Bruker All rights reserved. Document Revision History: SPM Training Notebook Revision Date Section(s) Affected Reference Approval Rev. E 10/27/2003 Content and Format Update N/A C. Kowalski Rev. D 08/05/2003 Overall Content and Format Update N/A L. Burrows Rev. C 07/30/2003 Content Update N/A L. Burrows Rev. B 08/01/1998 Format Update N/A C. Fitzgerald Rev. A 05/09/1997 Initial Release N/A J. Thornton Notices: The information in this document is subject to change without notice. NOWARRANTY OF ANY KIND IS MADE WITH REGARD TO THIS MATERIAL, INCLUDING, BUT NOT LIMITED TO, THE IMPLIED WARRANTIES OF MERCHANTABILITY AND FITNESS FOR A PARTICULAR PURPOSE. No liability is assumed for errors contained herein or for incidental or consequential damages in connection with the furnishing, performance, or use of this material. This document contains proprietary information which is protected by copyright. No part of this document may be photocopied, reproduced, or translated into another language without prior written consent. Copyright: Copyright © 2003 Bruker. All rights reserved. Trademark Acknowledgments: The following are registered trademarks of Bruker Instruments Inc. All other trademarks are the property of their respective owners. Product Names: NanoScope® MultiMode™ Dimension™ BioScope™ Atomic Force Prof ler™ (AFP™) Dektak® Software Modes: TappingMode™ Tapping™ TappingMode+™ LiftMode™ AutoTune™ TurboScan™ Fast HSG™ PhaseImaging™ DekMap 2™ HyperScan™ StepFinder™ SoftScan™ Hardware Designs: TrakScan™ StiffStage™ Hardware Options: TipX® Signal Access Module™ and SAM™ Extender™ TipView™ Interleave™ LookAhead™ Quadrex™ Software Options: NanoScript™ Navigator™ FeatureFind™ Miscellaneous: NanoProbe® Table of Contents 1.0 History and Definitions in SPMs . -
Atomic Force Microscopy and Scanning Probe Microscopy
Atomic Force Microscopy and Scanning Probe Microscopy In general, a scanning probe microscope (SPM) can make height images of the surface of solid sample and can be used to determine mechanical, electrical, and magnetic properties of said surfaces. The instrument works by placing a small physical probe in close proximity to a sample and observing the reaction of the probe as it scanned laterally over the surface. Scanning probe microscopy is a very general name that can describe most any probe technique. Examples include scanning tunneling microscopy and magnetic force microscopy. Atomic force microscopy (AFM) generally implies imaging the surface to determine the morphology or roughness or mechanical properties. Most commercially available probes are made from Si. The so-called probe is generally a cantilever beam with an integrated protruding sharp tip made from etched Si. The data collected depends on the type of probe used. For most generally purpose height images, a standard etched Si cantilever/tip is used. For other types of data, a specialized tip may be required. For example, if magnetic data is desired, a magnetized tip is fabricated by coating the standard tip with a magnetic material. The most common mode of operation is the so-called tapping mode. In tapping mode, the cantilever is oscillated vertically. When the tip is close enough to the sample that it can touch the sample (at the bottom of the oscillation stroke), the tip is said to tap the sample. A feedback loop is used to maintain a constant oscillation amplitude, which in turn maintains a constant force between the tip and sample. -
Electrostatic Imaging of Encapsulated Graphene
Electrostatic Imaging of Encapsulated Graphene Michael A. Altvater1, Shuang Wu1, Zhenyuan Zhang1, Tianhui Zhu1, Guohong Li1, Kenji Watanabe2, Takashi Taniguchi2 and Eva Y. Andrei1 1 Department of Physics and Astronomy, Rutgers, the State University of New Jersey, 136 Frelinghuysen Rd, Piscataway, New Jersey 08854, USA 2 National Institute for Material Science, 305-0044 1-1 Namiki Tsukuba, Ibaraki, Japan Abstract Devices made from two-dimensional (2D) materials such as graphene and transition metal dichalcogenides exhibit remarkable electronic properties of interest to many subdisciplines of nanoscience. Owing to their 2D nature, their quality is highly susceptible to contamination and degradation when exposed to the ambient environment. Protecting the 2D layers by encapsulation between hexagonal boron nitride (hBN) layers significantly improves their quality. Locating these samples within the encapsulant and assessing their integrity prior to further processing then becomes challenging. Here we show that conductive scanning probe techniques such as electrostatic force and Kelvin force microscopy makes it possible to visualize the encapsulated layers, their charge environment and local defects including cracks and bubbles on the sub-micrometer scale. Our techniques are employed without requiring electrical contact to the embedded layer, providing valuable feedback on the device’s local electronic quality prior to any device etching or electrode deposition. We show that these measurement modes, which are simple extensions of atomic force microscopy, are perfectly suited for imaging encapsulated conductors and their local charge environments. has provided access to a wide range of intrinsic properties 1. Introduction including micron-scale ballistic transport (15), electron optics (16, 17), magnetic focusing (18), and Moiré superlattices 2D materials can display remarkable electronic properties, which exhibit interesting magneto-transport properties (19- but with all the atoms at the surface these properties are easily 21). -
Nano-FTIR Vs. Pif-IR: Comparing Nano‐IR Techniques
Featuring PiFM & PiF-IR chemical analysis Released: May 28, 2021 Whitepaper Article Nano-FTIR vs. PiF-IR: Comparing Nano‐IR Techniques Background slightly better with a resolution 3 μm horizontally and a Ever since the invention of the atomic force microscope depth of 1.6 μm, but that is still too imprecise when the (AFM), researchers have sought to invent technologies goal is to look and nanoscale features. that would bring conventional chemical analysis tech‐ niqueslikeinfraredspectroscopytoamuchsmallerspatial Principle of Nano-FTIR volume. Currently, there are a few competing techniques Onemethodtoovercomethediffractionlimitandachieve which claim to offer these abilities. higher spatial resolution is to combine FTIR with tapping Given the popularity and utility of Fourier Transform mode (TM) atomic force microscopy (AFM) to realize Infrared (FTIR) spectroscopy, one natural option is to nano-FTIR. extend this technique to the nanoscale via nano-FTIR. Based on an apertureless near-field optical microscope However, while FTIR is a robust and user-friendly tech‐ design (also known as scattering scanning near-field opti‐ nique at larger scales, the nanoscale variation has some cal microscopy, or s-SNOM), nano-FTIR utilizes a modern key limitations that other techniques like photo-induced broadband (white-light) laser source instead of a fixed- force infrared (PiF-IR) spectroscopy have alleviated. wavelength laser as would normally be used in s-SNOM. The sample arm of the Michelson interferometer is FTIR replaced by the light scattering from the tip-sample inter‐ Conventional Fourier Transform Infrared (FTIR) spec‐ faceoftheTMAFM. troscopy is a well-established analytical technique that In nano-FTIR, the tip is typically metal coated, and the acquirestheinfrared(IR)spectrumofabsorption(ortrans‐ excitation light polarized along the tip direction to exploit mission) of a solid, liquid or gas sample. -
Electric Field Based Simulations of Local Oxidation Nanolithography Using Atomic Force Microscopy in a Level Set Environment
ECS Transactions, 49 (1) 265-272 (2012) 10.1149/04901.0265ecst ©The Electrochemical Society Electric Field Based Simulations of Local Oxidation Nanolithography using Atomic Force Microscopy in a Level Set Environment Lado Filipovic a,b and Siegfried Selberherr a a Institute for Microelectronics, TU Wien, Gußhausstraße 27–29/E360, A-1040 Wien, Austria b Christian Doppler Laboratory for Reliability Issues in Microelectronics at the Institute for Microelectronics, Austria Email: {filipovic|selberherr}@iue.tuwien.ac.at During the last decades it has been shown that non-contact AFM can be used as an efficient lithographic technique capable of manufacturing nanometer sized devices on the surface of a silicon wafer. The AFM nanooxidation approach is based on generating a potential difference between a cantilever needle tip and a silicon wafer. A water meniscus builds up between the tip and the wafer, resulting in a medium for oxyions to move due to the high electric field in the region. A simulator for nanooxidation with non-contact AFM tools, implemented in a Level Set environment, was developed. The presented model uses empirical equations for the height and half-width of an AFM nanodot or nanowire with a physics based shape model. The shape model uses a particle distribution directly derived from the surface charge density, generated on the silicon surface due to the strong electric field. Introduction Conventional photolithographic methods, which are derived from optical and electron beam lithographies, are no longer capable of providing the necessary processing steps for the fabrication of modern nanosized devices. They are either too cost intensive or unsuitable for handling the extensive variety of organic and biological systems applicable to nanotechnology (1). -
Parallel Writing by Local Oxidation Nanolithography with Submicrometer Resolution Massimiliano Cavallini, Paolo Mei, and Fabio Biscarinia) CNR-ISMN Sez
APPLIED PHYSICS LETTERS VOLUME 83, NUMBER 25 22 DECEMBER 2003 Parallel writing by local oxidation nanolithography with submicrometer resolution Massimiliano Cavallini, Paolo Mei, and Fabio Biscarinia) CNR-ISMN Sez. Bologna, Via P. Gobetti 101, I-40129 Bologna, Italy Ricardo Garcı´a Instituto de Microelectronica de Madrid, CSIC, Isaac Newton 8, 28760 Tres Cantos, Madrid, Spain ͑Received 13 May 2003; accepted 20 October 2003͒ We demonstrate that the process of local oxidation of surfaces by atomic force microscopy ͑AFM͒ can be upscaled in a straightforward way by using a solid support with multiple protrusions as the cathode electrode. A metallized digital video disk DVD polymeric support has been used as a stamp to generate an array of features of variable length and 100 nm in width on a silicon surface covering a5ϫ6mm2 region. The parallel patterning process involves the formation of as many liquid bridges as there are protrusions in the stamp. The growth rate of the parallel local oxides is slightly smaller than the one obtained by AFM experiments. Nonetheless, results from AFM local oxidation experiments can be readily extended to parallel oxidation which in turn opens the possibility of patterning centimeter-square regions with 10 nm motives. © 2003 American Institute of Physics. ͓DOI: 10.1063/1.1633685͔ Local oxidation or nano-oxidation of metallic, organic, pable of similar performance in terms of positioning and and semiconducting films by a conductive probe of an feature definition, but covering centimeter-square regions. atomic force microscope ͑AFM͒ is emerging as a reliable Although parallel local oxidation was demonstrated by using and versatile method to fabricate nanometer-scale structures an array of 50ϫ1 parallel cantilevers,13 current technical and devices. -
Review Recent Progressive Use of Advanced Atomic Force Microscopy in Polymer Science: a Review
Preprints (www.preprints.org) | NOT PEER-REVIEWED | Posted: 5 March 2020 doi:10.20944/preprints202003.0082.v1 Peer-reviewed version available at Polymers 2020, 12, 1142; doi:10.3390/polym12051142 Review Recent progressive use of advanced atomic force microscopy in polymer science: A review Phuong Nguyen-Tri 1*, Payman Ghassemi1, Pascal Carriere2, Aymen Amine Assadi3, Dinh Duc Nguyen4 1. Département de chimie, biochimie et physique, Université du Québec à Trois-Rivières (UQTR), Québec, G8Z 4M3, Canada. Email : [email protected]; [email protected] 2. Laboratoire MAPIEM (EA 4323), Matériaux Polymères Interfaces Environnement Marin, Université de Toulon, Toulon, France. Email : [email protected] 3. Univ Rennes, ENSCR- Institut des Sciences Chimiques de Rennes (ISCR) - UMR CNRS 6226, France. [email protected] 4. Department of Environmental Energy Engineering, Kyonggi University, Suwon, Republic of Korea, email: [email protected] * Correspondence: [email protected]; Tel.: +819-376 5011 (ext. 4505) Abstract: Atomic force microscopy (AFM) has been extensively used for the nanoscale characterization of polymeric materials. The coupling of AFM with infrared spectroscope (AFM-IR) provides another advantage to the chemical analyses and thus helps to shed light upon the study of polymers. In this perspective paper, we review recent progress in the use of AFM-IR in polymer science. We describe first the principle of AFM-IR and the recent improvements to enhance its resolution. We discuss then the last progress in the use of AFM-IR as a super-resolution correlated scanned-probe IR spectroscopy for chemical characterization of polymer materials dealing with polymer composites, polymer blends, multilayers and biopolymers.