Control Rod Drive System
Total Page:16
File Type:pdf, Size:1020Kb
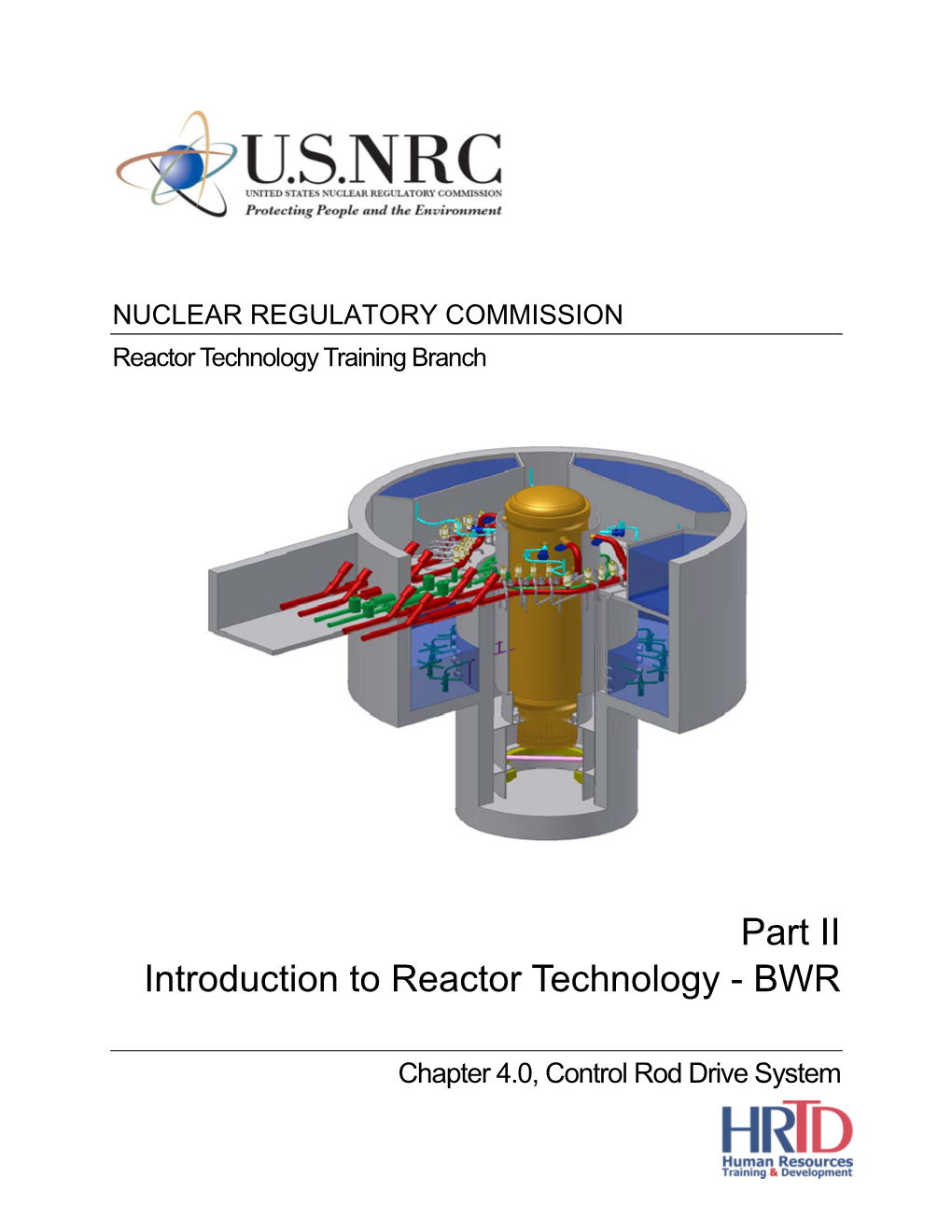
Load more
Recommended publications
-
The Nuclear Waste Primer September 2016 What Is Nuclear Waste?
The Nuclear Waste Primer September 2016 What is Nuclear Waste? Nuclear waste is the catch-all term for anything contaminated with radioactive material. Nuclear waste can be broadly divided into three categories: • Low-level waste (LLW), comprised of protective clothing, medical waste, and other lightly-contaminated items • Transuranic waste (TRU), comprised of long-lived isotopes heavier than uranium • High-level waste (HLW), comprised of spent nuclear fuel and other highly-radioactive materials Low-level waste is relatively short-lived and easy to handle. Currently, four locations for LLW disposal exist in the United States. Two of them, Energy Solutions in Clive, Utah and Waste Control Specialists in Andrews, Texas, accept waste from any U.S. state. Transuranic waste is often a byproduct of nuclear weapons production and contains long-lived radioactive elements heavier than uranium, like plutonium and americium. Currently, the U.S. stores TRU waste at the Waste Isolation Pilot Plant (WIPP) near Carlsbad, New Mexico. High-level waste includes spent nuclear fuel and the most radioactive materials produced by nuclear weapons production. Yucca Mountain is the currently designated high-level waste repository for the United States. 1 | What is Spent Nuclear Fuel? Spent nuclear fuel (SNF), alternatively referred to as used nuclear fuel, is the primary byproduct of nuclear reactors. In commercial power reactors in the U.S., fuel begins as uranium oxide clad in a thin layer of zirconium-aluminum cladding. After several years inside of the reactor, around fi ve percent of the uranium has been converted in some way, ranging from short-lived and highly radioactive fi ssion products to long-lived actinides like plutonium, americium, and neptunium. -
IAEA Guidelines and Formatting Rules for Papers for Proceeding
Interactive Computer Codes for Education and Training on Nuclear Safety and Radioprotection Francisco leszczynski∗ RA-6 Division, Nuclear Engineering Unit, Bariloche Atomic Center, CNEA, Av.E.Bustillo 8500, S.C.de Bariloche, RN, Argentina Abstract. Two interactive computer codes for education and training on nuclear safety and radioprotection developed at RA6 Reactor Division-Bariloche Atomic Center-CNEA are presented on this paper. The first code named SIMREACT has been developed in order to simulate the control of a research nuclear reactor in real time with a simple but accurate approach. The code solves the equations of neutron punctual kinetics with time variable reactivity. Utilizing the timer of the computer and the controls of a PC keyboard, with an adequate graphic interface, a simulation in real time of the temporal behavior of a research reactor is obtained. The reactivity can be changed by means of the extraction or insertion of control rods. It was implemented also the simulation of automatic pilot and scram. The use of this code is focalized on practices of nuclear reactor control like start-up from the subcritical state with external source up to power to a desired level, change of power level, calibration of a control rod with different methods, and approach to critical condition by interpolation of the answer in function of reactivity. The second code named LICEN has been developed in order to help the studies of all the topics included in examination programs for obtaining licenses for research reactor operators and radioprotection officials. Using the PC mouse, with an adequate graphic interface, the student can gradually learn the topics related with general and special licenses. -
Ncomms9592.Pdf
ARTICLE Received 9 May 2015 | Accepted 9 Sep 2015 | Published 9 Oct 2015 DOI: 10.1038/ncomms9592 OPEN High-intensity power-resolved radiation imaging of an operational nuclear reactor Jonathan S. Beaumont1, Matthew P. Mellor2, Mario Villa3 & Malcolm J. Joyce1,4 Knowledge of the neutron distribution in a nuclear reactor is necessary to ensure the safe and efficient burnup of reactor fuel. Currently these measurements are performed by in-core systems in what are extremely hostile environments and in most reactor accident scenarios it is likely that these systems would be damaged. Here we present a compact and portable radiation imaging system with the ability to image high-intensity fast-neutron and gamma-ray fields simultaneously. This system has been deployed to image radiation fields emitted during the operation of a TRIGA test reactor allowing a spatial visualization of the internal reactor conditions to be obtained. The imaged flux in each case is found to scale linearly with reactor power indicating that this method may be used for power-resolved reactor monitoring and for the assay of ongoing nuclear criticalities in damaged nuclear reactors. 1 Department of Engineering, Gillow Avenue, Lancaster University, Lancaster, LA1 4YW, UK. 2 Createc Ltd., Derwent Mills Commercial Park, Cockermouth CA13 0HT, UK. 3 Atominstitut, Vienna University of Technology, 1020 Vienna, Austria. 4 Hybrid Instruments Ltd., Unit 16, ICT Centre, Birmingham Research Park, Vincent Drive, Edgbaston B15 2SQ, UK. Correspondence and requests for materials should be addressed to J.S.B. (email: [email protected]). NATURE COMMUNICATIONS | 6:8592 | DOI: 10.1038/ncomms9592 | www.nature.com/naturecommunications 1 & 2015 Macmillan Publishers Limited. -
Study of Advanced Lwr Cores for Effective Use of Plutonium and Mox Physics Experiments
STUDY OF ADVANCED LWR CORES FOR EFFECTIVE USE OF PLUTONIUM AND MOX PHYSICS EXPERIMENTS T. YAMAMOTO, H. MATSU-URA*, M. UEJI, H. OTA XA9953266 Nuclear Power Engineering Corporation, Toranomon, Minato-ku, Tokyo T. KANAGAWA Mitsubishi Heavy Industries, Ltd, Nishi-ku, Yokohama K. SAKURADA Toshiba Corporation, Isogo-ku, Yokohama H.MARUYAMA Hitachi, Ltd, Hitachi-shi Japan Abstract Advanced technologies of full MOX cores have been studied to obtain higher Pu consumption based on the advanced light water reactors (APWRs and ABWRs). For this aim, basic core designs of high moderation lattice (H/HM ~5) have been studied with reduced fuel diameters in fuel assemblies for APWRs and those of high moderation lattice (H/HM ~6) with addition of extra water rods in fuel assemblies for ABWRs. The analysis of equilibrium cores shows that nuclear and thermal hydraulic parameters satisfy the design criteria and the Pu consumption rate increases about 20 %. An experimental program has been carried out to obtain the core parameters of high moderation MOX cores in the EOLE critical facility at the Cadarache Centre as a joint study of NUPEC, CEA and CEA's industrial partners. The experiments include a uranium homogeneous core, two MOX homogeneous cores of different moderation and a PWR assembly mock up core of MOX fuel with high moderation. The program was started from 1996 and will be completed in 2000. 1. INTRODUCTION In Japan, the MOX fuel demonstration programs have been performed successfully and reload size use of MOX fuel has been prepared. The recycling of plutonium in light water reactors is expected to continue in several decades. -
Energy Analysis for the Connection of the Nuclear Reactor DEMO to the European Electrical Grid
energies Article Energy Analysis for the Connection of the Nuclear Reactor DEMO to the European Electrical Grid Sergio Ciattaglia 1, Maria Carmen Falvo 2,* , Alessandro Lampasi 3 and Matteo Proietti Cosimi 2 1 EUROfusion Consortium, 85748 Garching, Germany; [email protected] 2 DIAEE—Department of Astronautics, Energy and Electrical Engineering, University of Rome Sapienza, 00184 Rome, Italy; [email protected] 3 ENEA Frascati, 00044 Frascati, Rome, Italy; [email protected] * Correspondence: [email protected] Received: 31 March 2020; Accepted: 22 April 2020; Published: 1 May 2020 Abstract: Towards the middle of the current century, the DEMOnstration power plant, DEMO, will start operating as the first nuclear fusion reactor capable of supplying its own loads and of providing electrical power to the European electrical grid. The presence of such a unique and peculiar facility in the European transmission system involves many issues that have to be faced in the project phase. This work represents the first study linking the operation of the nuclear fusion power plant DEMO to the actual requirements for its correct functioning as a facility connected to the power systems. In order to build this link, the present work reports the analysis of the requirements that this unconventional power-generating facility should fulfill for the proper connection and operation in the European electrical grid. Through this analysis, the study reaches its main objectives, which are the definition of the limitations of the current design choices in terms of power-generating capability and the preliminary evaluation of advantages and disadvantages that the possible configurations for the connection of the facility to the European electrical grid can have. -
Detailed B Depletion in Control Rods Operating in a Nuclear Boiling
UPTEC K11 015 Examensarbete 30 hp Februari 2011 Detailed 10B depletion in control rods operating in a Nuclear Boiling Water Reactor John Johnsson Abstract Detailed 10B depletion in control rods operating in a Nuclear Boiling Water Reactor John Johnsson Teknisk- naturvetenskaplig fakultet UTH-enheten In a nuclear power plant, control rods play a central role to control the reactivity of the core. In an inspection campaign of three control rods (CR 99) operated in the Besöksadress: KKL reactor in Leibstadt, Switzerland, during 6 respectively 7 consecutive cycles, Ångströmlaboratoriet Lägerhyddsvägen 1 defects were detected in the top part of the control rods due to swelling caused by 10 Hus 4, Plan 0 depletion of the neutron-absorbing B isotope (Boron-10). In order to correlate these defects to control rod depletion, the 10B depletion has in this study been Postadress: calculated in detail for the absorber pins in the top node of the control rods. Box 536 751 21 Uppsala Today the core simulator PLOCA7 is used for predicting the behavior of the reactor Telefon: core, where the retrievable information from the standard control rod follow-up is 018 – 471 30 03 the average 10B depletion for clusters of 19 absorber holes i.e. one axial node. 10 Telefax: However, the local B depletion in an absorber pin may be significantly different 018 – 471 30 00 from the node average depletion that is re-ceived from POLCA7. To learn more, the 10B depletion has been simulated for each absorber hole in the uppermost node using Hemsida: the stochastic Monte Carlo 3D simulation code MCNP as well as an MCNP- based http://www.teknat.uu.se/student 2D-depletion code (McScram). -
Boiling Water Reactor Control Rod CR 82M-1
Nuclear Fuel Boiling Water Reactor Control Rod CR 82M-1 Background CR 82M-1 Design The boiling water reactor (BWR) control rod of The hafnium tip of the CR 82M-1 design protects today must meet high operational demands and at the control rod from absorber material swelling the same time contribute to decreased operational when operated in the shutdown mode; i.e., costs for the plant operator. withdrawn from the core. The flexible B4C inventory allows for either matched or high- Description reactivity worth control rods. As structural material, American Iron and Steel Institute 316L stainless The Westinghouse BWR control rod design steel is an irradiation-resistant steel, not readily consists of four stainless steel sheets welded sensitized to irradiation-assisted stress corrosion together to form a cruciform-shaped rod. Each cracking. With an extremely low-cobalt content sheet has horizontally drilled holes to contain the (< 0.02%) in the wing material, these control rods absorber materials (B4C powder and hafnium). can play a significant role in as-low-as-reasonably- This design allows significantly more B4C to be achievable efforts. The design, with horizontally contained in the rod compared to the original drilled absorber holes, limits the washout of control rods of most reactors. B4C in the event of an anomaly in a wing, thus maintaining full reactivity worth. Westinghouse CR 82M-1 control rod for all types of BWRs Westinghouse BWR control rod CR 82M-1 Benefits CR 82M-1 is an evolutionary design based on 45 years of control rod operation -
Accident-Tolerant Control Rod
NEA/NSC/DOC(2013)9 Accident-tolerant control rod Hirokazu Ohta, Takashi Sawabe, Takanari Ogata Central Research Institute of Electric Power Industry (CRIEPI), Japan Boron carbide (B4C) and hafnium (Hf) metal are used for the neutron absorber materials of control rods in BWRs, and silver-indium-cadmium (Ag-In-Cd) alloy is used in PWRs. These materials are clad with stainless steel. The eutectic point of B4C and iron (Fe) is about 1 150°C and the melting point of Ag-In-Cd alloy is about 800°C, which are lower than the temperature of zircaloy – steam reaction increases rapidly (~1 200°C). Accordingly, it is possible that the control rods melt and collapse before the reactor core is significantly damaged in the case of severe accidents. Since the neutron absorber would be separated from the fuels, there is a risk of re-criticality, when pure water or seawater is injected for emergency cooling. In order to ensure sub-criticality and extend options of emergency cooling in the course of severe accidents, a concept of accident-tolerant control rod (ACT) has been derived. ACT utilises a new absorber material having the following properties: • higher neutron absorption than current control rod; • higher melting or eutectic temperature than 1 200°C where rapid zircaloy oxidation occurs; • high miscibility with molten fuel materials. The candidate of a new absorber material for ATC includes gadolinia (Gd2O3), samaria (Sm2O3), europia (Eu2O3), dysprosia (Dy2O3), hafnia (HfO2). The melting point of these materials and the liquefaction temperature with Fe are higher than the rapid zircaloy oxidation temperature. -
Meimei Li (ANL), Jonathan D
FY 2016 NEET R&D Award - Investigating Grain Dynamics in Irradiated Materials with High-Energy X-rays PIs: Meimei Li (ANL), Jonathan D. Almer (ANL), Donald W. Brown(ORNL) DOE-NE Cross-cut Coordination Meeting August 16, 2016 Motivation – In situ Multiscale Experiment of Nuclear Reactor Materials with High-Energy X-rays Interstitials, Dislocation Grains, Stress-strain vacancies, segments, twins, behavior solutes, loops, network, phases, SFT, voids, cells, inclusions, bubbles, subgrains, pores, etc. precipitates, etc. etc. LOM SEM TEM High-Energy X-rays 2 Combined In situ High-Energy X-ray Techniques (APS Beamline 1-ID) SAXS detector High-energy, high-brilliance X-rays: • • HR detector Deep penetration • Filters & stop − mm-sized specimens Lab-scale − Suite of sample environments mechanical test • In situ, real-time studies 6m 5.5m 4.5m Very far-field detectors • 3 HR detectors 1m • Trans-rotate for high q-coverage 0 Far-field detectors • Near field-HEDM • 4 GE 2x2k detectors detector • @1m: qmax~25 1/A • Tomography • Center-hole (SAXS) • Conical slit • Lasers 3 In situ Thermal-Mechanical Experiment of Neutron- Irradiated Materials 4 In situ Characterization using 2D X-ray Techniques: Grain-Average Behavior 1 in 1 Diffraction peak shifts revealed load partitioning among phases during deformation Diffraction peak broadening revealed dislocation evolution during deformation SAXS captured void formation and evolution during Voids necking 5 High-Energy Diffraction Microscopy (3D-XRD): Individual Grain Characteristics . Three-dimensional, grain-scale characterization: – Characterization of microstructural and micromechanical response of individual grains within the bulk of a polycrystalline specimen. Near-field (nf-) HEDM (similar to 3D-EBSD): – Sample-detector distance: mm – cm • Grain shape and – Not suitable for in situ study orientation map with complex environments • Detailed GB geometry . -
Unit 3: Nuclear Reactors/Energy Generation
Unit 3: Nuclear Reactors/Energy Generation Time: Three hours Objectives A. Teacher: 1. To ensure students understand how nuclear energy is generated. 2. To help students learn how a nuclear power plant works. 3. To understand how the NRC regulates commercial nuclear energy. B. At the conclusion of this unit the student should be able to — 1. Describe the fission process. 2. Identify the various kinds of nuclear power plants. 3. Discuss the process of energy generation with nuclear power plants. Investigation and Building Background 1. Introduce term: Students have little knowledge of nuclear reactors and limited understanding of the terminology used in nuclear power plants. Definitions found in dictionaries tend to be vague regarding this specialized language. 2. Resources: 1. Nuclear Power for Energy Generation "Nuclear Reactor Concepts" Workshop Manual, U.S. NRC 2. The Fission Process and Heat Production "Nuclear Reactor Concepts" Workshop Manual, U.S. NRC 3. Boiling-Water Reactor Systems "Nuclear Reactor Concepts" Workshop Manual, U.S. NRC 4. Pressurized-Water Reactor Systems "Nuclear Reactor Concepts" Workshop Manual, U.S. NRC 3. Generalizing: The purpose of a nuclear power plant is to produce or release heat and boil water. It is designed to produce electricity. It should be noted that while there are significant differences, there are many similarities between nuclear power plants and other electrical generating facilities. Uranium is used for fuel in nuclear power plants to make electricity. a. Vocabulary: Nuclear Power Plants boiling water reactor (BWR) helium pressurized water reactor (PWR) uranium dioxide uranium-235 uranium-238 sodium Questions 1. Is there a nuclear power plant near where you live? What type is it? 2. -
Apr1400 Design Control Document Tier 2
APR1400 DESIGN CONTROL DOCUMENT TIER 2 CHAPTER 4 REACTOR APR1400-K-X-FS-14002-NP REVISION 0 DECEMBER 2014 2014 KOREA ELECTRIC POWER CORPORATION & KOREA HYDRO & NUCLEAR POWER CO., LTD All Rights Reserved This document was prepared for the design certification application to the U.S. Nuclear Regulatory Commission and contains technological information that constitutes intellectual property. Copying, using, or distributing the information in this document in whole or in part is permitted only by the U.S. Nuclear Regulatory Commission and its contractors for the purpose of reviewing design certification application materials. Other uses are strictly prohibited without the written permission of Korea Electric Power Corporation and Korea Hydro & Nuclear Power Co., Ltd. Rev. 0 APR1400 DCD TIER 2 CHAPTER 4 – REACTOR TABLE OF CONTENTS NUMBER TITLE PAGE CHAPTER 4 – REACTOR ............................................................................................ 4.1-1 4.1 Summary Description ......................................................................................... 4.1-1 4.1.1 Initial Core Design Description and Permissible Changes ..................... 4.1-2 4.1.2 Analytical Techniques ............................................................................ 4.1-2 4.1.3 Combined License Information .............................................................. 4.1-2 4.2 Fuel System Design ............................................................................................. 4.2-1 4.2.1 Design Bases ......................................................................................... -
The Regulation of Fusion – a Practical and Innovation-Friendly Approach
The Regulation of Fusion – A Practical and Innovation-Friendly Approach February 2020 Amy C. Roma and Sachin S. Desai AUTHORS Amy C. Roma Sachin S. Desai Partner, Washington, D.C. Senior Associate, Washington, D.C. T +1 202 637 6831 T +1 202 637 3671 [email protected] [email protected] The authors want to sincerely thank the many stakeholders who provided feedback on this paper, and especially William Regan for his invaluable contributions and review of the technical discussion. TABLE OF CONTENTS I. EXECUTIVE SUMMARY 1 II. THE STATE OF FUSION INNOVATION 3 A) An Introduction to Fusion Energy 3 B) A Rapid Growth in Private-Sector Fusion Innovation 4 III. U.S. REGULATION OF ATOMIC ENERGY - NOT ONE SIZE FITS ALL 7 A) The Foundation of U.S. Nuclear Regulation - The Atomic Energy Act and the NRC 7 B) The Atomic Energy Act Embraces Different Regulations for Different Situations 7 1. NRC Frameworks for Different Safety Cases 8 2. Delegation of Regulatory Authority to States 9 IV. THE REGULATION OF FUSION - A PRACTICAL AND INNOVATION- FRIENDLY APPROACH 10 A) Fusion Regulation Comes to the Fore, Raising Key Questions 10 B) A Regulatory Proposal That Recognizes the Safety Case of Fusion and the Needs of Fusion Innovators 11 1. Near-Term: Regulation of Fusion Under the Part 30 Framework is Appropriate Through Development and Demonstration 11 2. Long-Term: The NRC Should Develop an Independent Regulatory Framework for Fusion at Commercial Scale, Not Adopt a Fission Framework 12 V. CONCLUSION 14 1 Hogan Lovells I. EXECUTIVE SUMMARY Fusion, the process that powers the Sun, has long been seen Most fusion technologies are already regulated by the NRC as the “holy grail” of energy production.