OPERATION GUIDE for Flexstat
Total Page:16
File Type:pdf, Size:1020Kb
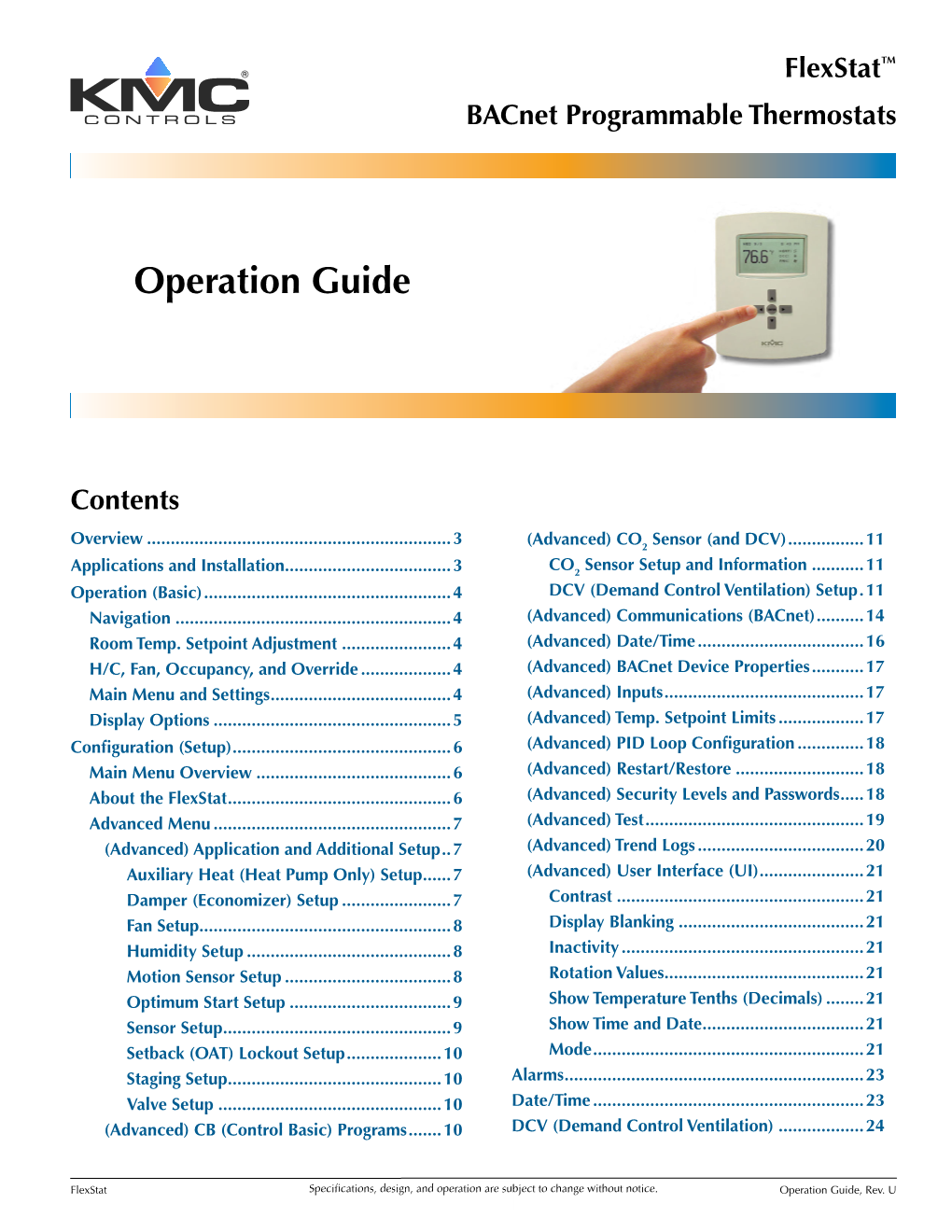
Load more
Recommended publications
-
Hvac System Covid Procedures
HVAC SYSTEM COVID PROCEDURES August 17, 2020 Prepared by: Johnson Roberts Associates 15 Properzi Way Somerville, MA 02143 Prepared for: City of Cambridge Executive Summary The HVAC COVID procedures are a compilation of Industry Standards and CDC recommendations. However, it should be noted that good PPE (personal protective equipment), social distancing, hand washing/hygiene, and surface cleaning and disinfection strategies should be performed with HVAC system measures, as studies have shown that diseases are easily transmitted via direct person to person contact, contact from inanimate objects (e.g. room furniture, door and door knob surfaces) and through hand to mucous membrane (e.g. those in nose, mouth and eyes) contact than through aerosol transmission via a building’s HVAC system. Prior to re-occupying buildings, it is recommended that existing building HVAC systems are evaluated to ensure the HVAC system is in proper working order and to determine if the existing system or its associated control operation can be modified as part of a HVAC system mitigation strategy. Any identified deficiencies should be repaired and corrected, and if the building HVAC system is a good candidate for modifications those measures should be implemented. In general HVAC system mitigation strategies should include the following recommendations: 1. Increase Outdoor Air. The OA increase must be within Unit's capacity in order to provide adequate heating or cooling so Thermal Comfort is not negatively impacted. Also use caution when increasing OA in polluted areas (e.g. High Traffic/City areas) and during times of high pollen counts. 2. Disable Demand Control Ventilation where present. -
Remember Capacity & Consumption When
HVAC/R and BAS trade news | Volume IV / 2018 kele.com | [email protected] | 888.826.9047 REMEMBER CAPACITY & CONSUMPTION WHEN SELECTING AN ELECTRONIC TO PNEUMATIC TRANSDUCER Also featured in this volume: • Kele Introduces Product Matching Solution • Is Your BAS Ready for the Cold? • Powering Multiple Devices from a Common Transformer Kele Insights | Volume IV / 2018 kele.com | 877.826.9047 | [email protected] Volume IV: Table of Contents pg 02 // Kele Introduces Product Matching Solution pg 03 // Is Your BAS Ready for the Cold? pg 05 // Remember Capacity & Consumption When Selecting an Electronic to Pneumatic Transducer pg 07 // Back to Basics: Don’t Let a Mismatched Signal Delay Profitability! pg 08 // Powering Multiple Devices from a Common Transformer pg 11 // The Best Choice for UL924 RIB® Relays pg 14 // Honoring Our Vets: A Different Type of Kele Service P74 Series – Differential Pressure Switch The Johnson Controls Model P74 Differential Pressure Switch measures the difference in pressure exerted upon its two sensing elements in the building automation application. It operates an SPDT switch at the differential pressure set point. With these differential pres- sure switches, the set point may be adjusted without removing the cover and is visible on a calibrated scale. SHOP NOW 01 Kele Insights | Volume IV / 2018 kele.com | 877.826.9047 | [email protected] KELE INTRODUCES PRODUCT MATCHING SOLUTION Initiative enhances customer user experience and buying process Need to quickly find a product accessory? What about an alternative to a tariffed part? A new feature on kele.com makes this process simple and intuitive. Customers can now view and select accessories, related products, and direct or functional alternatives on the same page/screen as the original product they intend to buy. -
Advanced Thermodynamic Analyses of Energy Intensive Building Mechanical Systems
Rochester Institute of Technology RIT Scholar Works Theses 2006 Advanced Thermodynamic Analyses of Energy Intensive Building Mechanical Systems Erin N. George Follow this and additional works at: https://scholarworks.rit.edu/theses Recommended Citation George, Erin N., "Advanced Thermodynamic Analyses of Energy Intensive Building Mechanical Systems" (2006). Thesis. Rochester Institute of Technology. Accessed from This Thesis is brought to you for free and open access by RIT Scholar Works. It has been accepted for inclusion in Theses by an authorized administrator of RIT Scholar Works. For more information, please contact [email protected]. ADVANCED THERMODYNAMIC ANALYSES OF ENERGY INTENSIVE BUILDING MECHANICAL SYSTEMS By ERIN N. GEORGE A Thesis Submitted in Partial Fulfillment of the Requirement for Master of Science in Mechanical Engineering Approved by: Department ofMechanical Engineering Committee Dr. Margaret Bailey - Thesis Advisor Dr. Robert Stevens Dr. Frank Sciremammano Dr. Edward Hensel- Dept. Representative Rochester Institute of Technology Rochester, New York 14623 March 2006 PERMISSION TO REPRODUCE THE THESIS Title of Thesis ADVANCED THERMODYNAMIC ANALYSES OF ENERGY INTENSIVE BUILDING MECHANICAL SYSTEMS I, ERIN N. GEORGE, hereby grant permission to the Wallace Memorial Library of Rochester Institute of Technology to reproduce my thesis in the whole or part. Any reproduction will not be for commercial use or profit. March 2006 ABSTRACT A review ofpast research reveals that while exergetic analysis has been performed on various building mechanical systems, there has not been extensive efforts in the areas of air distribution systems or cooling plants. Motivations for this new work include demonstrating the merits of exergetic analysis in association with retrocommissioning (RCX) an existing building air handling unit (AHU), as well as conducting an advanced analysis on an existing chiller. -
Installation and Maintenance Manual IM 1125-10 Rebel® Commercial
Installation and Maintenance Manual IM 1125-10 Group: Applied Air Systems Part Number: IM 1125 Date: August 2019 Rebel® Commercial Packaged Rooftop Systems Heating and Cooling Models DPS003 – 028A R-410A Refrigerant MicroTech® III Unit Controller Energy Recovery Wheel 3–6 tons 7–15 tons Shown with Energy Recovery 16–28 tons Shown with Energy Recovery Table of Contents Table of Contents Introduction . 3 Optional Outdoor Air Monitor . 75 General Information . 3 Thermal Dispersion Airflow Measurement Technology . 75 Unit Nameplate . 3 ECM Motor . 80 Hazard Identification Information . 3 Unit Options . 82 Mechanical Installation . 4 Economizer Enthalpy Control . 82 Installer Responsibilities . 4 External Time Clock . 82 Receiving Inspection . 4 Exhaust Fan Option . 82 Ventilation Clearance . 4 Proof-of-Airflow and Dirty Filter Switch . 82 Overhead Clearance . 4 Duct High Pressure Limit . 82 Steel Rail Installation . 6 Convenience Receptacle (Field Powered) . 83 Roof Curb Assembly and Installation . 6 Convenience Receptacle (Unit Powered) . 83 Rigging and Handling . 11 Wiring Diagrams . 84 Unit Piping - Condensate Drain Connection . 14 Sequence of Operation . 111 Damper Assemblies . 14 Operating States . 111 Cabinet Weather Protection . 15 Mechanical Cooling . 112 Installing Ductwork . 15 Economizer . 112 Electrical Installation . 18 Preparing the Unit for Start Up . 113 Refrigeration System . 23 Pre-Start of Unit . 113 Piping System . 23 Spring Isolated Fans . 113 DPS Component Description . 25 Servicing Control Panel Components . 114 DPS 016–028 Ton Component Description . 31 Power-Up . 114 VFD Compressor Operation Fan Start-Up . 114 (DPS 016–028 only) . 33 Check, Test and Start Procedures . 115 Variable Speed Scroll Compressor . 37 Economizer Start-Up . 115 Optional Modulating Hot Gas Reheat . -
Energy Savings and Collateral Impacts of a DHW Water-To-Water Heat Pump System with Subslab Earth Coupling
Energy Savings and Collateral Impacts of a DHW Water-to-Water Heat Pump System with Subslab Earth Coupling William D. Rittelmann, PE Member ASHRAE ABSTRACT This paper presents research results from simulations and a field investigation of a domestic hot water (DHW) system incor- porating a water-to-water heat pump and a subslab earth-coupled loop. The research stems from a need for nonsolar, high-effi- ciency, DHW system alternatives to help reach the whole-house energy savings goals of 50% and higher. A schematic diagram of the system is used to explain the system concept, emphasizing daily average DHW loads and the resulting load density imposed on the slab. A comparison to air-to-water heat pumps summarizes the primary advantages and market barriers of this system type. A summary of the analysis using a transient system simulation model is reviewed, and sensitivity to key system parameters and user schedules is discussed. The relative importance of subhourly simulation time steps and hot water demand schedules is explained. Collateral energy impacts of individual system components are then presented on monthly and annual bases and compared to results from a base-case simulation incorporating a conventional electric resistance water heater. Additional or reduced heat flux through the slab and standby tank losses/gains are of particular interest, as are variations due to foundation type and climate. The calculation of the net whole-house coefficient of performance is explained and total annual energy consump- tion is presented. INTRODUCTION still has a source-energy factor of 0.83, and an HPWH drops Domestic hot water (DHW) energy use accounts for an to only 0.72. -
A/Fs-1, A/Fs-1A, A/Fs-2, A/Fs-2A, A/Fs-3, A/Fs-3A, A/Fs-4, A/Fs-4A, A/Fs-5, A/Fs-5A, A/Fs-6, A/Fs-6A
Installation and Operation Instructions A/FS-1, A/FS-1A, A/FS-2, A/FS-2A, A/FS-3, A/FS-3A, A/FS-4, A/FS-4A, A/FS-5, A/FS-5A, A/FS-6, A/FS-6A Carefully Read These Instructions Before Installation! Description Electro-mechanical, low-temperature limit/cut-out thermostat with a 20 ft, 10 ft or 6 ft capillary sensing element, auto- or manual reset, and 1-SPDT or 2-SPDT switched output. Applications The thermostat and its capillary sensing element provide an antifreeze function. It detects temperature drops below a fixed safety value (setpoint), i.e. heaters in A/C units, exchangers in cooling systems, etc. Operation Any 1-foot length of the sensing element subjected to temperatures below the low cut-out setpoint setting of the thermostat will actuate the thermostat switch mechanism regardless of the temperature being sensed by the remainder of the element. The low cut-out setpoint is factory set and can be adjusted by turning the slotted screw on top of the enclosure. NOTICE: The Freeze Thermostat is factory set at 39°F. This is the ideal setting that will provide the best protection while avoiding nuisance trips. Auto-reset types will automatically switch back to the normal position if the temperature returns to normal conditions. Manual-reset types will switch back only if both the temperature returns to normal conditions and the reset button (at the enclosure’s front) is manually pushed. Wiring All wiring should comply with National and Local Electrical Codes. A M20 watertight fitting is installed in the ½” conduit knockout. -
Can You Design a Control System That Maximizes the Benefits of a Building
Kele.com [email protected] Phone: 877.826.9047 Int’l: 001.901.382.6084 Can you design a control system We’ll show you how to improve occupant comfort, reduce utility that maximizes the benefits of a costs, and help increase overall building analytics engine? operational efficiency on page 7 table of contents pg 04 – Tech Talk Do you know what the “standard” terminal designations for thermostats are? See if you’re right. pg 07 – How to Design Your Control System to Take Advantage of a Building Analytics Engine Whether you are applying analytics for a new construction project or as part of a controls upgrade, you have to keep the end game in mind at every stage of the design process. The performance of your enhanced visualization, fault detection and diagnostics, or real-time optimization will depend upon the design of your control system. pg 09 – Signaling 101 In this article, we offer an overview of several types of visual signals and applications, everything from flashing beacons to sirens and buzzers. pg 14 – Kele Announces the Acquisition of Controls Consultants, Incorporated Kele and Controls Consultants, the acquision and the future. pg 15 – Is Your Building Automation System Ready for the Cold? The cold weather is finally here -are you ready for the cooler temps? Don’t worry, Kele has you covered. pg 17 – Maintaining Balance and Efficency Through Proper Control Valve Selection In this article, we will cover the importance of proper control valve selction for increased efficiency with an emphasis on pressure independent control valves A70 SERIES ONEBOX indoor / outdoor use universal enclosures The Kele OneBox series is perfect for your everyday indoor or outdoor applications. -
Environmental – Indoor Air Quality
DEPARTMENT: FacilitiGroup POLICY DESCRIPTION: Environmental – Indoor Air Quality PAGE: 1 of 3 REPLACES POLICY DATED: 1/12/99, 7/21/99, 11/1/05 (DC.003) EFFECTIVE DATE: May 1, 2007 REFERENCE NUMBER: ENV.003 APPROVED BY: Ethics and Compliance Policy Committee SCOPE: All Company-affiliated facilities including, but not limited to, hospitals, ambulatory surgery centers, outpatient imaging centers, home health agencies, physician practices, and all Corporate Departments, Groups and Divisions and on-site subcontractors. PURPOSE: To require each facility provide a safe indoor environment for patients, employees and the public by properly maintaining the ventilation and associated systems. POLICY: 1. Each facility must maintain all ventilation equipment in proper operating condition and be certain that prescribed ventilation rates are adequate to keep the concentration of harmful chemicals, fumes, or odors below the limits for air contaminants set by the NOISH Pocket Guide (NPG). The NPG is available at http://www.cdc.gov/niosh/npg/npg.html. A table of typical chemicals found in facilities is attached. 2. Practical control measures must be taken during a construction project to minimize the adverse impact on the indoor air quality for an active health care facility operation. 3. Visual evidence of microbial amplification (mold growth) is indicative of moisture intrusion, water leaks or improper operation of HVAC equipment. Appropriate corrective action must be implemented immediately. 4. Each facility must properly respond to indoor air quality complaints. Please reference the Indoor Air Quality Checklist for actions required to maintain acceptable indoor air quality standards. The Indoor Air Quality Checklist is attached. This procedure addresses federal regulatory requirements. -
Zone Control with Variable Air Volume Controls (VAV)- KMC Controls
4/9/2014 Zone control with Variable Air Volume controls (VAV)- KMC Controls product search / > Solutions Zone control with Variable Air Volume controls (VAV) The goal of any HVAC system is to maintain a temperature within a space or zone. When the space is large, such as an Answers & Education auditorium or open factory space, the HVAC system delivers tempered supply air based on a single setpoint and space temperature. However, when the system must maintain the comfort level in several zones the problem becomes more Like 28 people like this. complex. For example, an office area system must maintain a comfortable temperature based on multiple setpoints in individual rooms. This complex problem is often solved by installing a system of variable air volume controls on branch outlets. The simplest variable air volume control (VAV) system controls air from a single supply duct and varies the airflow to each zone or room based upon the temperature in the room. A VAV system consists of four basic parts: a thermostat, a precision actuator controlled damper, an airflow sensor, and a controller. When the thermostat senses the space temperature is at the temperature setpoint, the controller closes the damper until the airflow reaches a predefined lower limit. As the room temperature moves away from setpoint, the controller opens the damper until the airflow reaches a predefined upper limit. In a typical cooling application the temperature of the air supplied air to a VAV control is 55° Fahrenheit. If the room is at the temperature setpoint, the damper in the VAV closes to minimum airflow. -
LV-Z Series Installation Manual
www.hi-velocity.com LV-Z Series Installation Manual Includes: LV-Z Series Fan Coils Product Specifications Wiring and WEG Settings Specifications & Sizing From the Manufacturers of Hi-Velocity SystemsTM www.hi-velocity.com Module-LVZ-Series-Fan-Coil-Installation-061616 Table of Contents Setting up your LV-Z System - Pg. 4 Unit Selection, Quality Assurance Fan Coil Placement - Pgs. 5 Placement, Unit Configuration, Clearances Water Cooling Module (WCM) - Pg 6 Hot Water Coil (HWC) Add-on - Pg 6 Electric Strip Heater (ESH) - Pg. 7 Return Air - Pg. 7 Return Cutout Dimensions, Return Air Base, Filter Rack Hi-Velocity Air Purification System Pg. 8 Hi-Velocity Air Purification System, HE PS Dimensions User Guide Pg 8 IAQ, Filter Maintenance, System Efficiency Installation Check List - Pg. 8 PSB Circuit Board & WEG Drive - Pgs. 9-16 PSB Board, WEG Drive, PSB Wiring Diagram, Extended WIring Diagrams Trouble Shooting - Pgs. 17-24 Motor Running Too Fast, Motor Running Too Slow, Motor Not Running, 24V Clg, 24V Htg., Outdoor Unit, Short Cycling Appendix Pages - Pgs. 25-26 LV-Z Fan Coil Specifications (Standard & Metric, Quick Product Sizing Guide) Warranty Information - Pg. 27 -2- © 1995-2020 Energy Saving Products Ltd. Module LVZ LV-Z Series Fan Coil Installation (3/28) The LV-Z System By Energy Saving Products Ltd. All Product LV-Z Fan Coil Sizing on Pg. 26 Specs Pg. 25 Heating Options Cooling Options Hot Water Coil Water Coil Module Electric Strip Coil Other Options Return Air Hi-Velocity Air Purification System -3- © 1995-2020 Energy Saving Products Ltd. Module LVZ LV-Z Series Fan Coil Installation (4/28) When sizing an LV-Z fan coil for a residential system, it Sweat water connections are 3/4” for the LV-Z 1050 and 1” for is necessary to have an accurate heat loss/gain done for the the LV-Z 1750. -
Generalaire® Models DH75 & DH100
® Wi-Fi Control Dehumidifiers Residential Whole-House (GFI #5333 & 5334) GeneralAire® Models DH75 & DH100 Dehumidifiers Breathe in the Difference Breathe Healthier With GeneralAire® DH75 & DH100 Wi-Fi Dehumidifiers Adjust Settings From Almost Anywhere Create a healthier living space Sleep better Increase productivity Feel more comfortable Decrease pest populations Lower cooling costs Reduce mold & mildew Keep decor in top shape Keep plants healthy Protect wood, art, musical instruments A Whole-House Humidifier: • Treats Your Whole House 24 / 7 / 365 • Requires Minimal Maintenance • Is Out of Sight • Runs Quietly Download online at: www.generalfilters.com/literature/spec/submittal. All information subject to change without notice. ® Enhanced Features of the GeneralAire® APP include: 5 Humidity Sensor Offset This allows you to change the calibration of the humidity sensor to match another humidity measuring device in the home. Freezestat Lockout Setpoint Your control allows you to adjustable the freeze stat temperature cut-off (28°-34°F / -2°- +1°C) and turn-on (48°-52°F / 9°-11°C). The adjustability of the freeze stat allows the dehumidifier to run efficiently in low temperature conditions. Dewpoint Lockout Setpoint – Adjustable from 36-42°F. In addition to the low ambient temperature 50°F (incoming air) on the previous version of firmware, the added low dew point temperature lockout will further ensure the dehumidifier runs more efficiently. Fan Idle Fan idle for drain cycle can be turned ON (YES) or OFF (NO). The drain cycle feature can be turned off to make the dehumidifier run more efficiently at low temperature conditions. GeneralAire® Has Your Solution - Reducing moisture Maintain the right humidity throughout your entire home with the new reduces the occurrence GeneralAire® DH75 & DH100 Wi-Fi to of mold and mildew. -
EHRS Indoor Air Quality Worksheet
Indoor Air Quality Worksheet 1/2021 JSS Indoor Air Quality Worksheet Overview The purpose of this checklist is to provide the EHRS investigator with a guide to ensure thorough and consistent indoor air quality investigations. Preliminary Investigation & Facility Contact Information Facility name: ______________________________ Facility address: _______________________________________ Facility manager or building contact: __________________________________________________________________ Location of complaint(s): ___________________________________________________________________________ Description of area: _______________________________________________________________________________ Number of individuals in this work area: _______________________________________________________________ Approximate size of the area in square feet: ____________________________________________________________ Air handler that serves the area: __________________________ Air handler location: ________________________ Other areas served by same air handler: ________________________________________________________________ Primary requester/complainants: _____________________________________________________________________ Primary requester/complainant contact information: _____________________________________________________ Date of request: ______________________ Date investigation started: _______________________ Investigator(s): ___________________________________________________________________________________ Health Hazard Survey submitted to occupant(s)