Review on Inlet/Outlet Oil Coordinated Control for Electro-Hydraulic Power Mechanism Under Sustained Negative Load
Total Page:16
File Type:pdf, Size:1020Kb
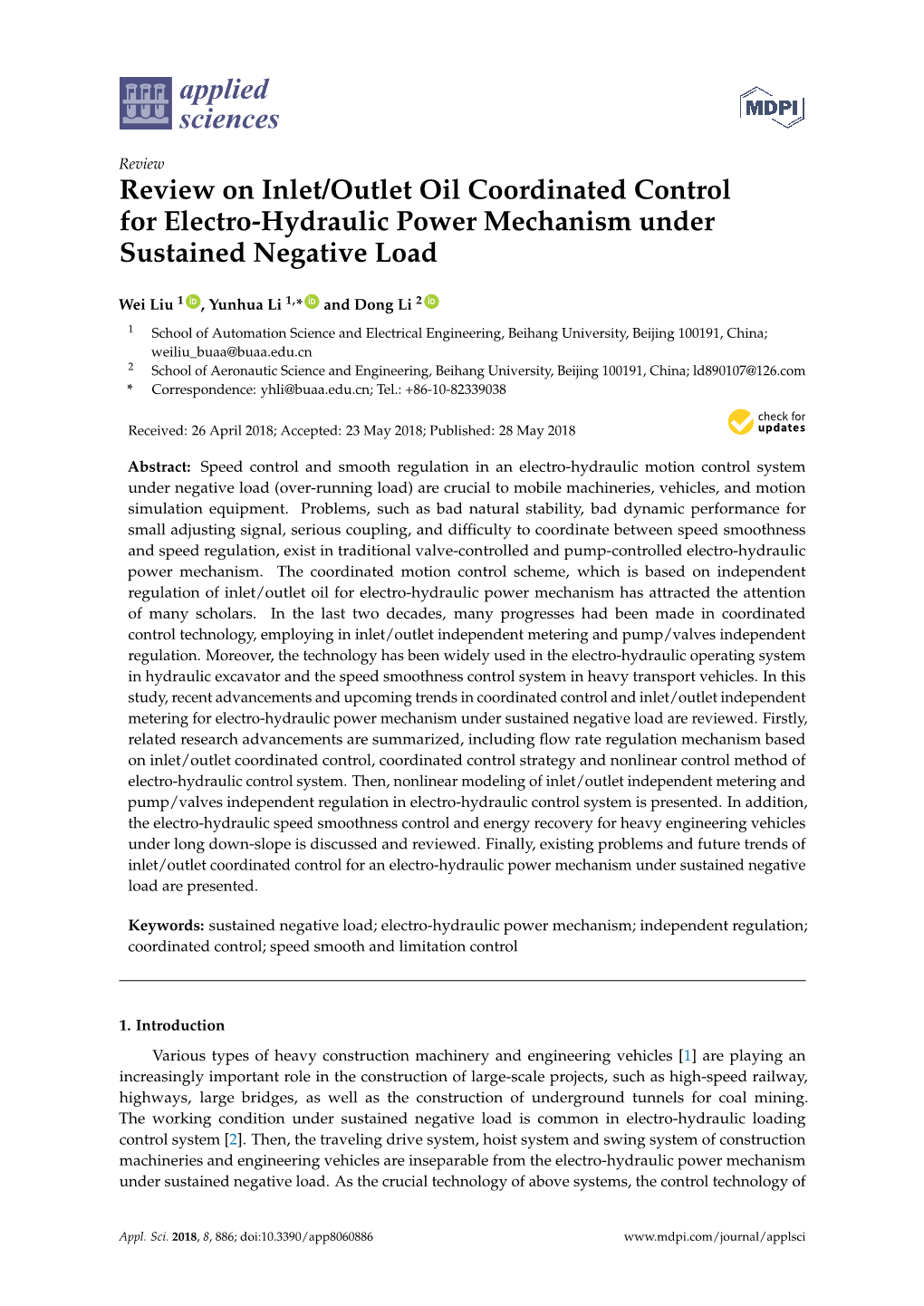
Load more
Recommended publications
-
Accumulator Technology. E 3.000.14/03.16 1
Accumulator Technology. E 3.000.14/03.16 1. HYDAC ACCUMULATOR TECHNOLOGY FLUID ENGINEERING EFFICIENCY VIA ENERGY MANAGEMENT. HYDAC Accumulator Technology has over 50 years' experience in research & development, design and production of Hydac accumulators. Bladder, piston, diaphragm and metal bellows accumulators from HYDAC together form an unbeatable range and as components or units, support hydraulic systems in almost all sectors. The main applications of our accumulators are: z Energy storage, z Emergency and safety functions, z Damping of vibrations, fluctuations, pulsations (pulsation damper), shocks (shock absorber) and noise (silencer), z Suction flow stabilisation, z Media separation, z Volume and leakage oil adjustment, z Weight equalization, z Energy recovery. Using accumulators improves the performance of the whole system and in detail this has the following benefits: z Improvement in the functions z Increase in service life z Reduction in operating and maintenance costs z Reduction in pulsations and noise On the one hand, this means greater safety and comfort for operator and machine. On the other hand, HYDAC accumulators enable efficient working in all applications. 2. QUALITY In conjunction with the customer service department at HYDAC's headquarters, Basic criteria, such as: Quality, safety and reliability are paramount service is possible worldwide. z for all HYDAC accumulator components. Design pressure, HYDAC's worldwide distributor network z Design temperature, They comply with the current regulations means that trained staff are close at hand (or standards) for pressure vessels in the to help our customers. z Fluid displacement volume, individual countries of installation. z Discharge / Charging velocity, In taking delivery of a HYDAC hydraulic z Fluid, accumulator therefore, the customer is This ensures that HYDAC customers have the support of an experienced workforce z Acceptance specifications and also assured of a high-quality accumulator product which can be used in every both before and after sale. -
Modelling, Testing and Analysis of a Regenerative Hydraulic Shock Absorber System
energies Article Modelling, Testing and Analysis of a Regenerative Hydraulic Shock Absorber System Ruichen Wang *, Fengshou Gu, Robert Cattley and Andrew D. Ball School of Computing and Engineering, University of Huddersfield, Queensgate, Huddersfield HD1 3DH, UK; [email protected] (F.G.); [email protected] (R.C.); [email protected] (A.D.B.) * Correspondence: [email protected]; Tel.: +44-01484-473640 Academic Editor: Paul Stewart Received: 31 March 2016; Accepted: 12 May 2016; Published: 19 May 2016 Abstract: To improve vehicle fuel economy whilst enhancing road handling and ride comfort, power generating suspension systems have recently attracted increased attention in automotive engineering. This paper presents our study of a regenerative hydraulic shock absorber system which converts the oscillatory motion of a vehicle suspension into unidirectional rotary motion of a generator. Firstly a model which takes into account the influences of the dynamics of hydraulic flow, rotational motion and power regeneration is developed. Thereafter the model parameters of fluid bulk modulus, motor efficiencies, viscous friction torque, and voltage and torque constant coefficients are determined based on modelling and experimental studies of a prototype system. The model is then validated under different input excitations and load resistances, obtaining results which show good agreement between prediction and measurement. In particular, the system using piston-rod dimensions of 50–30 mm achieves recoverable power of 260 W with an efficiency of around 40% under sinusoidal excitation of 1 Hz frequency and 25 mm amplitude when the accumulator capacity is set to 0.32 L with the load resistance 20 W. -
Final Report MO-2017-203: Burst Nitrogen Cylinder Causing Fatality, Passenger Cruise Ship Emerald Princess, 9 February 2017
Final report MO-2017-203: Burst nitrogen cylinder causing fatality, passenger cruise ship Emerald Princess, 9 February 2017 The Transport Accident Investigation Commission is an independent Crown entity established to determine the circumstances and causes of accidents and incidents with a view to avoiding similar occurrences in the future. Accordingly it is inappropriate that reports should be used to assign fault or blame or determine liability, since neither the investigation nor the reporting process has been undertaken for that purpose. The Commission may make recommendations to improve transport safety. The cost of implementing any recommendation must always be balanced against its benefits. Such analysis is a matter for the regulator and the industry. These reports may be reprinted in whole or in part without charge, providing acknowledgement is made to the Transport Accident Investigation Commission. Final Report Marine inquiry MO-2017-203 Burst nitrogen cylinder causing fatality, passenger cruise ship Emerald Princess, 9 February 2017 Approved for publication: November 2018 Transport Accident Investigation Commission About the Transport Accident Investigation Commission The Transport Accident Investigation Commission (Commission) is a standing commission of inquiry and an independent Crown entity responsible for inquiring into maritime, aviation and rail accidents and incidents for New Zealand, and co-ordinating and co-operating with other accident investigation organisations overseas. The principal purpose of its inquiries is to determine the circumstances and causes of occurrences with a view to avoiding similar occurrences in the future. Its purpose is not to ascribe blame to any person or agency or to pursue (or to assist an agency to pursue) criminal, civil or regulatory action against a person or agency. -
Handheld Hydraulic Equipment Your Business Is in Good Hands
HANDHELD HYDRAULIC EQUIPMENT YOUR BUSINESS IS IN GOOD HANDS Hydraulics lets you do more in less time. It allows tools to hit harder with less vibration and noise. Hydraulics is simply better. The first time you see a hydraulic horsepower power pack delivers the small enough to fit on a shelf or in breaker you might think it’s nothing same power at the tool tip as a 20 a service van saving you fuel. Two special. It’s compact, quiet and horsepower diesel compressor engine. people can carry the power pack with appears to vibrate less than electric ease. and pneumatic tools. But there’s more In fact, for the price of one compressor to it than meets the eye. and breaker you can buy two If you already use hydraulic tools, you complete hydraulic power pack/ know what you get. If you’re new to When you press the trigger you’ll be breaker packages. And hydraulics hydraulics, you and your business are in for a surprise. Hydraulic oil is a pays even when it’s turned off. The in good hands. powerful energy transmitter. A nine energy efficient power packs are 2 KNOW YOUR HYDRAULICS Here are the essentials on why and when hydraulics is the best choice to get the work done on time and on budget. With just one or two moving parts, Association) standards. That means tools can be connected to a range there’s minimal wear and very few easy, fast and safe connections of different power sources such as parts to replace. -
Electro-Hydraulic Components and Systems
Hydraulic Systems Volume 2 Electro-Hydraulic Components and Systems Dr. Medhat Kamel Bahr Khalil, Ph.D, CFPHS, CFPAI. Director of Professional Education and Research Development, Applied Technology Center, Milwaukee School of Engineering, Milwaukee, WI, USA. Compu Draulic LLC www.CompuDraulic.com Compu Draulic LLC Hydraulic System Volume 2 Electro-Hydraulic Components and Systems ISBN: 978-0-9977634-2-3 Printed in the United States of America First Published by 2017 Revised by January 2019 All rights reserved for CompuDraulic LLC. 3850 Scenic Way, Franksville, WI, 53126 USA. www.compudraulic.com No part of this book may be reproduced or utilized in any form or by any means, electronic or physical, including photocopying and microfilming, without written permission from CompuDraulic LLC at the address above. Disclaimer It is always advisable to review the relevant standards and the recommendations from the system manufacturer. However, the content of this book provides guidelines based on the author's experience. Any portion of information presented in this book could be not applicable for some applications due to various reasons. Since errors can occur in circuits, tables, and text, the author/publisher assumes no liability for the safe and/or satisfactory operation of any system designed based on the information in this book. The author/publisher does not endorse or recommend any brand name product by including such brand name products in this book. Conversely the author/publisher does not disapprove any brand name product by not including such brand name in this book. The publisher obtained data from catalogs, literatures, and material from hydraulic components and systems manufacturers based on their permissions. -
Offshore Availability for Wind Turbines with a Hydraulic Drive Train
Offshore availability for wind turbines with a hydraulic drive train James Carroll*, Alasdair McDonald †, David McMillan ‡, Julian Feuchtwang • *University of Strathclyde, Scotland. [email protected], †University of Strathclyde, Scotland. [email protected]. ‡University of Strathclyde, Scotland. [email protected]. • University of Strathclyde, Scotland. [email protected] Keywords: Reliability, Availability, Hydraulic, Drive train. a hydraulic drive train using a number of different data sources. Failure rates and repair times will be estimated Abstract through past publications [1] and the use of offshore reliability data from the oil and gas industry [2]. Recent Hydraulic drive trains for wind turbines are under papers [3, 4] that estimate offshore availability include a development by a number of different companies; at least one number of different offshore drive train types but due to the hydraulic drive train is in the final stages of development by a non-availability of data the hydraulic drive train was leading wind turbine manufacturer. Hydraulic drive trains excluded. have a number of advantages such as redundancy, modularity, compactness and track record in other industries. Currently Reference [3] uses a model based on a probabilistic-statistical there are few or no installed wind turbines with hydraulic approach to calculate the turbine access delays caused due to drive trains onshore or offshore. As no data exists on poor sea conditions. Along with estimated failure rates and reliability or failure rates for wind turbines with hydraulic repair times for the hydraulic drive train, this model will be drive trains, this paper estimates failure rates, repair time and used to work out the overall availability for the different drive availability for said turbines. -
Modeling and Analysis of Hydraulic Energy Storage System for Hybrid Locomotives
A Thesis entitled Modeling and Analysis of Hydraulic Energy Storage System for Hybrid Locomotives by Boya Zhang Submitted to the Graduate Faculty as partial fulfillment of the requirements for the Master of Science Degree in Mechanical Engineering Dr. Walter W. Olson, Committee Chair Dr. Hongyan Zhang, Committee Member Dr. Yong Gan, Committee Member Dr. Patricia R. Komuniecki, Dean College of Graduate Studies The University of Toledo Dec 2010 Copyright 2010, Boya Zhang This document is copyrighted material. Under copyright law, no parts of this document may be reproduced without the expressed permission of the author. An Abstract of Modeling and Analysis of Hydraulic Energy Storage System for Hybrid Locomotives by Boya Zhang Submitted to the Graduate Faculty as partial fulfillment of the requirement for the Master of Science in Mechanical Engineering The University of Toledo Dec 2010 Hybrid locomotive have more than one power source to provide driving power. The prime power source of a hybrid locomotive can be a diesel engine or fuel cell, and the on-board energy storage system can provide a secondary power. The rechargeable energy storage system (RESS) of hybrid locomotives can temporarily store energy which is captured from braking action or redundant energy produced by the diesel engine to reduce fuel consumption and pollution. The Electro-mechanical Battery (EMB) which is a energy storage system for hybrid locomotives, consisting of the accumulator, pump/motor, reservoir and an electric motor/generator is introduced in this thesis. The hydraulic energy storage system has the advantages of high power density and low cost compared to the other vehicle‟s energy storage systems and has the potential to be an energy storage system for hybrid locomotives. -
Condition Monitoring Systems for Hydraulic Accumulators – Improvements in Efficiency, Productivity and Quality
Group 6 Predictive maintenance Paper 6-4 195 CONDITION MONITORING SYSTEMS FOR HYDRAULIC ACCUMULATORS – IMPROVEMENTS IN EFFICIENCY, PRODUCTIVITY AND QUALITY Christian Nisters*, Dr.-Ing. Frank Bauer, Marco Brocker HYDAC Technology GmbH, Industriestraße, 66280, Sulzbach/Saar, Germany * Corresponding author: Tel.: +49 6897 5099555; E-mail address: [email protected] ABSTRACT This paper addresses the necessity of a correct hydraulic accumulator pre-charge pressure for the optimum performance and in some cases even the essential function of the corresponding hydraulic application. In this context HYDAC has developed a smart product for predictive monitoring of the pre-charge pressure without any need to do a measurement on the gas side of the accumulator – the p0-Guard. The paper gives an overview on the conventional way of checking the pre-charge pressure, the function of the monitoring device and points out the benefits of a predictive monitoring of the accumulator pre- charge pressure. The benefits are clearly depicted by an analytical view as well as on practical example. Keywords: Efficiency, Hydraulic accumulator, Pre-charge pressure, Predictive monitoring, p0-Guard 1. INTRODUCTION various types of accumulator accessories and safety equipment which makes the hydraulic In various hydraulic applications hydraulic accumulator ready for essential future accumulators are used for energy and requirements in automation and safety. performance support as well as for emergency functions. Due to the fact that the hydraulic medium is practically incompressible (and therefore unable to store energy) the hydraulic accumulator introduces the benefits of a compressible gas to the hydraulics. The capacity of energy storage is directly affected by the pre- charge pressure of the nitrogen gas (p0) inside the accumulator [1]. -
Electro-Hydraulic
A4 US A4 US Electro-hydraulic The RFS range of electro-hydraulic valve actuators are of a robust, yet compact, modular design built to achieve the highest degree of reliability. Special consideration was given in the design process to facilitate installation and integration into customer control and communication systems. They utilise a scotch yoke mechanism which is field proven the world over in all types of fluid power applications. Our control system, like our actuators, is also of a modular design. Common control functions (i.e. remote/local, open and close) are provided as standard. The modular system facilitates integration of optional requirements such as automatic line break, high or low pressure close and differential pressure systems. Field modifications are practical and relatively easy to accomplish. This standardised product approach offers a higher standard of performance and a lower cost of ownership than a central hydraulic power unit solution. Electro-hydraulic Digital communication via Rotork Pakscan or other common valve actuators industry systems is an available option. Pakscan is the most secure of all bus highway systems. Unlike other systems, Pakscan can achieve long distance transmission without the need for repeaters. The two-wire system can communicate Design Features with up to 240 devices over a loop up to 20 km long. It is truly • Scotch yoke actuator in either double-acting or redundant, able to withstand a short circuit, open circuit or spring-return configurations. ground fault and continue to communicate with all devices in the loop. It will also provide the location and nature of • Closed hydraulic muliti-function system. -
Modeling and Simulation of the Dynamic Effects of Pressure Variations on Hydraulic Bladder and Piston Style Accumulators
University of Tennessee, Knoxville TRACE: Tennessee Research and Creative Exchange Masters Theses Graduate School 8-2019 MODELING AND SIMULATION OF THE DYNAMIC EFFECTS OF PRESSURE VARIATIONS ON HYDRAULIC BLADDER AND PISTON STYLE ACCUMULATORS Colin Loudermilk University of Tennessee, [email protected] Follow this and additional works at: https://trace.tennessee.edu/utk_gradthes Recommended Citation Loudermilk, Colin, "MODELING AND SIMULATION OF THE DYNAMIC EFFECTS OF PRESSURE VARIATIONS ON HYDRAULIC BLADDER AND PISTON STYLE ACCUMULATORS. " Master's Thesis, University of Tennessee, 2019. https://trace.tennessee.edu/utk_gradthes/5542 This Thesis is brought to you for free and open access by the Graduate School at TRACE: Tennessee Research and Creative Exchange. It has been accepted for inclusion in Masters Theses by an authorized administrator of TRACE: Tennessee Research and Creative Exchange. For more information, please contact [email protected]. To the Graduate Council: I am submitting herewith a thesis written by Colin Loudermilk entitled "MODELING AND SIMULATION OF THE DYNAMIC EFFECTS OF PRESSURE VARIATIONS ON HYDRAULIC BLADDER AND PISTON STYLE ACCUMULATORS." I have examined the final electronic copy of this thesis for form and content and recommend that it be accepted in partial fulfillment of the requirements for the degree of Master of Science, with a major in Mechanical Engineering. Ahmad Vakili, Major Professor We have read this thesis and recommend its acceptance: Steve Brooks, Gregory Power Accepted for the Council: Dixie L. Thompson Vice Provost and Dean of the Graduate School (Original signatures are on file with official studentecor r ds.) MODELING AND SIMULATION OF THE DYNAMIC EFFECTS OF PRESSURE VARIATIONS ON HYDRAULIC BLADDER AND PISTON STYLE ACCUMULATORS A Thesis Presented for the Master of Science Degree The University of Tennessee, Knoxville Colin Cross Loudermilk August 2019 ACKNOWLEDGEMENTS The author wishes to express appreciation to his advisor, Dr. -
Life Cycle Management Perfect Down to the Last Detail Increase the Service Life and Performance of Your System
Life Cycle Management perfect down to the last detail Increase the service life and performance of your system In a chain, the weakest link always determines the load-carrying capacity. This is also true for hydraulic systems. Why running great risks for the entire hydraulic system whereas savings are minimal? Life Cycle Management 3 02 Increase the service life and performance of your system 04 Filter systems: State-of-the-art fluid management 06 Bladder and diaphragm accumulators: Reserves for energy efficiency 08 Cooler systems: Optimum fluid temperature with low noise emission 10 Information advantage for a longer service life thanks to Rexroth sensorics 13 Lifelong partnership We offer you a wide portfolio of hydraulic products that Be it filters for optimal fluid conditioning or low-noise oil/ perfectly suit the high efficiency and long service life of air coolers, bladder and diaphragm accumulators, measur- hydraulic solutions. ing and maintenance sensors – the Rexroth product range provides the preconditions for continuingly high perfor- Your advantage: mance and a long service life of your system. Components in proven large-series quality that are available worldwide and the certainty that our products, which In addition, you benefit from the experience of our world- perfectly match your system, reduce your life cycle cost wide service network. Our specialists in more than 80 lastingly. countries are pleased to render advice in all questions around your hydraulic system – irrespective of the year of At Rexroth all developments undergo the same strict quality construction and the manufacturer. We are on your side, assessment during the design process – complex power when it comes to a swift replacement of components, units just as seemingly simple components. -
Electro-Hydraulic Servo System
Mechanical Engineering Department Mechatronics Engineering Program Bachelor Thesis Graduation Project Electro-Hydraulic Servo System Project Team Ashraf Issa Project Supervisor Eng. Hussein Amro Hebron- Palestine June, 2012 Palestine Polytechnic University Hebron-Palestine College of Engineering and Technology Department of Mechanical Engineering Electro-Hydraulic Servo System Project team Ashraf Issa According to the directions of the project supervisor and by the agreement of all examination committee members, this project is presented to the department of Mechanical Engineering at College of Engineering and Technology, for partial fulfillment Bachelor of engineering degree requirements. Supervisor Signature Supervisor Signature Committee Member Signature Department Head Signature II Abstract This project concerns of building an electro-hydraulic servo system model to be used in the industrial hydraulics lab to achieve the controlling of a hydraulic flow and pressure using a hydraulic servo valves, understanding the internal construction and the operational principles of servo hydraulic valves, understanding the mathematical model of a simple hydraulic system using hydraulic servo valve. The mathematical model for the built system was constructed and the simulation for linear mathematical model was done, and showed that the instability of the system and large steady state error. So indeed the system need an external controller to be designed. III Dedication To Our Beloved Palestine To my parents and family. To the souls that i love and can't see. To all my friends. To Palestine Polytechnic University. To all my teachers. May ALLAH Bless you. And for you i dedicate this project IV Acknowledgments I could not forget my family, who stood beside me, with their support, love and care for my whole life; they were with me with their bodies and souls, and helped me to accomplish this project.