Performances and Kinetic Studies of Hydrotreating of Bio-Oils in Microreactor
Total Page:16
File Type:pdf, Size:1020Kb
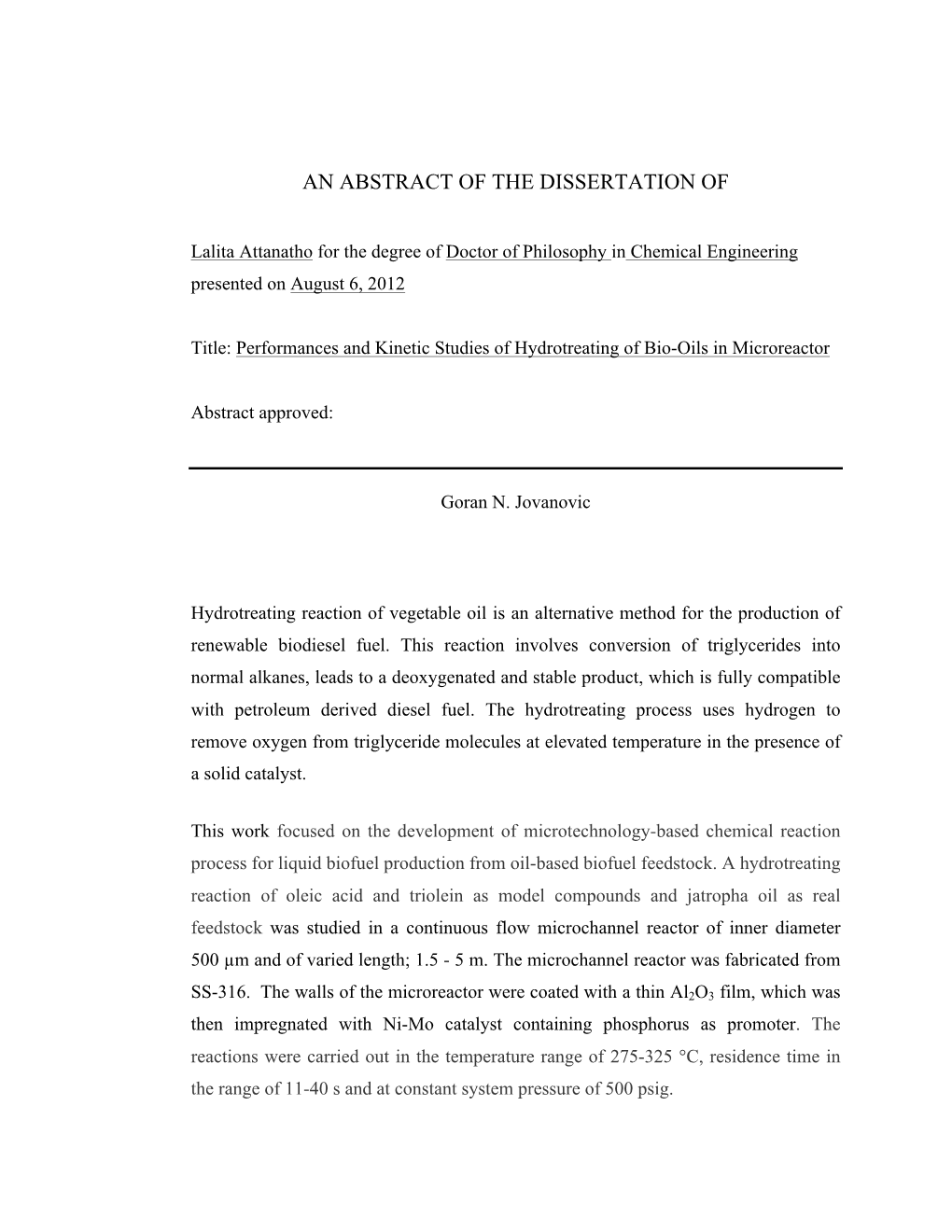
Load more
Recommended publications
-
Catalytic Transfer Hydrogenolysis Reactions for Lignin Valorization to Fuels and Chemicals
catalysts Review Catalytic Transfer Hydrogenolysis Reactions for Lignin Valorization to Fuels and Chemicals Antigoni Margellou 1 and Konstantinos S. Triantafyllidis 1,2,* 1 Department of Chemistry, Aristotle University of Thessaloniki, 54124 Thessaloniki, Greece; [email protected] 2 Chemical Process and Energy Resources Institute, Centre for Research and Technology Hellas, 57001 Thessaloniki, Greece * Correspondence: [email protected] Received: 31 October 2018; Accepted: 10 December 2018; Published: 4 January 2019 Abstract: Lignocellulosic biomass is an abundant renewable source of chemicals and fuels. Lignin, one of biomass main structural components being widely available as by-product in the pulp and paper industry and in the process of second generation bioethanol, can provide phenolic and aromatic compounds that can be utilized for the manufacture of a wide variety of polymers, fuels, and other high added value products. The effective depolymerisation of lignin into its primary building blocks remains a challenge with regard to conversion degree and monomers selectivity and stability. This review article focuses on the state of the art in the liquid phase reductive depolymerisation of lignin under relatively mild conditions via catalytic hydrogenolysis/hydrogenation reactions, discussing the effect of lignin type/origin, hydrogen donor solvents, and related transfer hydrogenation or reforming pathways, catalysts, and reaction conditions. Keywords: lignin; catalytic transfer hydrogenation; hydrogenolysis; liquid phase reductive depolymerization; hydrogen donors; phenolic and aromatic compounds 1. Introduction The projected depletion of fossil fuels and the deterioration of environment by their intensive use has fostered research and development efforts towards utilization of alternative sources of energy. Biomass from non-edible crops and agriculture/forestry wastes or by-products is considered as a promising feedstock for the replacement of petroleum, coal, and natural gas in the production of chemicals and fuels. -
Hydrodeoxygenation of Vegetable Oil in a Trickle Bed Reactor for Renewable Diesel Production
International Journal of Technology 11(7) 1292-1299 (2020) Received July 2020 / Revised November 2020 / Accepted December 2020 International Journal of Technology http://ijtech.eng.ui.ac.id Hydrodeoxygenation of Vegetable Oil in a Trickle Bed Reactor for Renewable Diesel Production Yuswan Muharam1*, Jessica Adeline Soedarsono1 1Department of Chemical Engineering, Faculty of Engineering, Universitas Indonesia, Kampus UI Depok, Depok 16424, Indonesia Abstract. The hydrodeoxygenation of vegetable oil in a trickle bed reactor for renewable diesel production was observed in this research. Vegetable oil was represented by triolein. The NiMo/Al2O3 catalyst with a composition of 6.13% w/w Ni, 12.49% w/w Mo, and 81.33% w/w Al2O3 was used. The reactions took place in the temperature range of 272–327.5°C and pressures of 5 and 15 bar. A trickle bed reactor of 2.01 cm in diameter and 24 cm in bed length was able to convert triolein into renewable diesel. C18 hydrocarbons became the dominant reacting compounds at temperatures above 310°C and a pressure of 15 bar, which reached more than 50% w/w. At 5 bar pressure, fatty acids with stearic acid as the acid with the highest concentration were the dominant reacting component, reaching more than 60% w/w at temperatures above 280°C. This led to double bond saturation once the reactants were mixed. Keywords: Hydrodeoxygenation; Renewable diesel; Trickle bed reactor 1. Introduction The Fuel is one of the basic needs for transportation and industry, which mostly comes from petroleum processing (fossil-based). Economic oil reserves are depleting, while energy demand continues to increase with population size and advancing technology. -
Catalytic Glycerol Hydrogenolysis to Produce 1,2-Propanediol with Molecular Hydrogen and in Situ Hydrogen Produced from Steam Reforming
Catalytic Glycerol Hydrogenolysis to Produce 1,2-propanediol with Molecular Hydrogen and in situ Hydrogen Produced from Steam Reforming by Yuanqing Liu A thesis presented to the University of Waterloo in fulfillment of the thesis requirement for the degree of Doctor of Philosophy in Chemical Engineering Waterloo, Ontario, Canada, 2014 ©Yuanqing Liu 2014 AUTHOR'S DECLARATION I hereby declare that I am the sole author of this thesis. This is a true copy of the thesis, including any required final revisions, as accepted by my examiners. I understand that my thesis may be made electronically available to the public. ii Abstract Biodiesel has shown great promise to supplement the fossil diesel since it is a renewable energy resource and is environmentally friendly. However, the major obstacle to biodiesel large scale commercialization is the high production cost; so converting glycerol, the by- product of a biodiesel process, into value-added products is an efficient way to promote biodiesel production. 1,2-propanediol (1,2PD), also known as propylene glycol, is an important commodity chemical used for many applications such as polyester resins, liquid detergents and anti-freeze. It can be produced via dehydration of glycerol into acetol followed by hydrogenation of acetol into 1,2PD using a bi-functional catalyst. Currently high pressure gaseous hydrogen added for hydrogenation causes safety issues as well as additional costs of hydrogen purchasing, transportation and storage. Therefore, the utilization of the in situ hydrogen produced by steam reforming of a hydrogen carrier could be a novel route for this process. In this work, processes of glycerol hydrogenolysis to produce 1,2PD have been developed using different hydrogen sources, i.e. -
Kinetics of Hydrodesulfurization of Dibenzothiophene on Sulfided Commercial Co-Mo/Γ-Al2o3catalyst IOةŸ ل
The Journal of Engineering Research Vol. 3, No. 1 (2006) 38-42 Kinetics of Hydrodesulfurization of Dibenzothiophene on Sulfided Commercial Co-Mo/γ-Al2O3 Catalyst Y.S. Al-Zeghayer1 and B.Y. Jibril*2 1Chemical Engineering Department, King Saud University, P.O. Box 800, Riyadh 11421, Saudi Arabia 2Petroleum and Chemical Engineering Department, Sultan Qaboos University, P.O. Box 33, Al-Khoud, PC 123, Muscat, Oman Received 27 April 2005; accepted 17 September 2005 …QÉŒ »àjÈc …õØM πeÉY ≈∏Y dibenzothiophene IOÉŸ á«æ«Lh~«¡dG âjȵdG ádGPG äÓYÉØJ á«côM 2@πjÈL .….Ü h 1ÒgõdG .¢S.… á≤∏£e áLQO 683 ¤G 633 ÚH Ée ájQGôM äÉLQO ~æY …QÉŒ »àjÈc …õØM πeÉY ≈∏Y É«∏ª©e â°SQhO dibenzothiophene IOÉŸ á«æ«LhQ~«¡dG âjȵdG ádGPEG äÓYÉØJ áÑ«côJ :á°UÓÿG á«∏ª©ŸG èFÉàædG §Ñæà°ùj ¿G øµÁ áHPɵdG ¤h’G áLQ~dG øe »°VÉjQ êPƒ‰ ¿G âÑKG .âe~îà°SG á«æ«LhQ~«¡dG âjȵdG ádGPGC á«∏ªY øe É¡«∏Y π°UÉ◊G DBT IOÉŸ áØ«©°V äGõ«côJ .…ƒL §¨°V 10 ~æY h (CHB) ɢª˘g ɢ¡˘«˘∏˘Y ∫ƒ˘°üÙG ᢫˘˘°ù«˘˘Fô˘˘dG äɢ˘é˘˘à˘˘æŸG ¿G ~L,, 51.7 kcal/mol …hɢ°ùJ ɢ¡˘fG ~˘˘Lh DBT IOÉe π˘jƒ˘ë˘à˘d á˘£˘°ûæŸG á˘bɢ£˘dG .ᢵ˘∏˘¡˘à˘°ùŸG DBT IOɢ˘Ÿ »£©J á©HÉààŸG ájRGƒàŸG äÓYÉØàdG ¿G ~Lhh .âHôL á©HÉààŸG ájRGƒàŸGh …RGƒàŸG äÓYÉØàdG ɪgh äÓYÉØàdG áµÑ°T øe ÚæKG ¿Gh . Biphenyl (BP) and cyclohexylbenzene (EBP) BP IOÉe ¤G DBT IOÉe πjƒëàd ᣰûæŸG ábÉ£dG º«b ¿G .IQGô◊G áLQO ≈∏Y ~ªà©J CHBIOÉe ¤G BP IOÉe áѰùf ¿Gh . -
I. a Mechanistic Study of the Hydrodesulfurization of Methanethiol Over Tungsten Disulfide; II
Iowa State University Capstones, Theses and Retrospective Theses and Dissertations Dissertations 1985 I. A mechanistic study of the hydrodesulfurization of methanethiol over tungsten disulfide; II. A urs vey of rare earth sulfides for yh drodesulfurization activity Donald Quinn Dowd Iowa State University Follow this and additional works at: https://lib.dr.iastate.edu/rtd Part of the Physical Chemistry Commons Recommended Citation Dowd, Donald Quinn, "I. A mechanistic study of the hydrodesulfurization of methanethiol over tungsten disulfide; II. A survey of rare earth sulfides for hydrodesulfurization activity " (1985). Retrospective Theses and Dissertations. 7842. https://lib.dr.iastate.edu/rtd/7842 This Dissertation is brought to you for free and open access by the Iowa State University Capstones, Theses and Dissertations at Iowa State University Digital Repository. It has been accepted for inclusion in Retrospective Theses and Dissertations by an authorized administrator of Iowa State University Digital Repository. For more information, please contact [email protected]. INFORMATION TO USERS This reproduction was made from a copy of a document sent to us for microfilming. While the most advanced technology has been used to photograph and reproduce this document, the quality of the reproduction is heavily dependent upon the quality of the material submitted. The following explanation of techniques is provided to help clarify markings or notations which may appear on this reproduction. 1. The sign or "target" for pages apparently lacking from the document photographed is "Missing Page(s)". If it was possible to obtain the missing page(s) or section, they are spliced into the film along with adjacent pages. -
Heterogeneous Catalyst Deactivation and Regeneration: a Review
Catalysts 2015, 5, 145-269; doi:10.3390/catal5010145 OPEN ACCESS catalysts ISSN 2073-4344 www.mdpi.com/journal/catalysts Review Heterogeneous Catalyst Deactivation and Regeneration: A Review Morris D. Argyle and Calvin H. Bartholomew * Chemical Engineering Department, Brigham Young University, Provo, UT 84602, USA; E-Mail: [email protected] * Author to whom correspondence should be addressed; E-Mail: [email protected]; Tel: +1-801-422-4162, Fax: +1-801-422-0151. Academic Editor: Keith Hohn Received: 30 December 2013 / Accepted: 12 September 2014 / Published: 26 February 2015 Abstract: Deactivation of heterogeneous catalysts is a ubiquitous problem that causes loss of catalytic rate with time. This review on deactivation and regeneration of heterogeneous catalysts classifies deactivation by type (chemical, thermal, and mechanical) and by mechanism (poisoning, fouling, thermal degradation, vapor formation, vapor-solid and solid-solid reactions, and attrition/crushing). The key features and considerations for each of these deactivation types is reviewed in detail with reference to the latest literature reports in these areas. Two case studies on the deactivation mechanisms of catalysts used for cobalt Fischer-Tropsch and selective catalytic reduction are considered to provide additional depth in the topics of sintering, coking, poisoning, and fouling. Regeneration considerations and options are also briefly discussed for each deactivation mechanism. Keywords: heterogeneous catalysis; deactivation; regeneration 1. Introduction Catalyst deactivation, the loss over time of catalytic activity and/or selectivity, is a problem of great and continuing concern in the practice of industrial catalytic processes. Costs to industry for catalyst replacement and process shutdown total billions of dollars per year. Time scales for catalyst deactivation vary considerably; for example, in the case of cracking catalysts, catalyst mortality may be on the order of seconds, while in ammonia synthesis the iron catalyst may last for 5–10 years. -
Effects of Catalyst Properties on Hydrodesulfurization of Fluid
The Pennsylvania State University The Graduate School Department of Energy and Mineral Engineering EFFECTS OF CATALYST PROPERTIES ON HYDRODESULFURIZATION OF FLUID CATALYTIC CRACKING DECANT OILS AS FEEDSTOCK FOR NEEDLE COKE A Thesis in Energy and Mineral Engineering by Joseph P. Abrahamson © 2015 Joseph P. Abrahamson Submitted in Partial Fulfillment of the Requirements for the Degree of Master of Science May 2015 The thesis of Joseph P. Abrahamson was reviewed and approved* by the following: Semih Eser Professor of Energy and Geo-Environmental Engineering Thesis Advisor Jonathan P. Mathews Associate Professor of Energy and Mineral Engineering Caroline Burgess Clifford Senior Research Associate Luis F. Ayala H. Associate Professor of Petroleum and Natural Gas Engineering Associate Department Head for Graduate Education *Signatures are on file in the Graduate School ii ABSTRACT This thesis investigates hydrodesulfurization of fluid catalytic cracking decant oils and its impact on carbonaceous mesophase development during carbonization. Delayed Coking of decant oils leads to the development of carbonaceous mesophase, a liquid crystalline phase, that is responsible for the structural anisotropy of needle coke. Because of its anisotropic microstructure, needle coke is used as the filler along with a coal tar pitch binder for manufacturing graphite electrodes for electric-arc furnaces. When sulfur content of the filler needle coke is high (>0.8 wt. %) an irreversible volume expansion (puffing) takes place when extruded electrodes are subjected to graphitization heat treatment. Puffing in needle coke results primarily from the evolution of sulfur in the form of CS2 and H2S. Puffing causes the formation of mico-cracks reducing the quality of electrodes. -
Kinetics of the Hydro-Deoxygenation of Stearic Acid Over
KINETICS OF THE HYDRO-DEOXYGENATION OF STEARIC ACID OVER PALLADIUM ON CARBON CATALYST IN FIXED-BED REACTOR FOR THE PRODUCTION OF RENEWABLE DIESEL Thesis Submitted to The School of Engineering of the UNIVERSITY OF DAYTON In Partial Fulfillment of the Requirements for The Degree of Master of Science in Chemical Engineering By Albert Vam Dayton, Ohio August, 2013 KINETICS OF THE HYDRO-DEOXYGENATION OF STEARIC ACID OVER PALLADIUM ON CARBON CATALYST IN FIXED-BED REACTOR FOR THE PRODUCTION OF RENEWABLE DIESEL Name: Vam, Albert APPROVED BY: Kevin J. Myers, D.Sc., P.E. Heinz J. Robota, Ph.D. Advisory Committee Chairman Research Advisor Professor; Graduate Chemical Engineering Ohio Research Scholar in Alternative Fuels Program Coordinator Alternative Fuels Group Leader Department of Chemical and Materials University of Dayton Research Institute Engineering Amy R. Ciric, Ph.D. Committee Member Senior Lecturer Department of Chemical and Materials Engineering John G. Weber, Ph.D. Tony E. Saliba, Ph.D. Associate Dean Dean, School of Engineering School of Engineering & Wilke Distinguished Professor ii ©Copyright by Albert Vam All rights reserved 2013 iii ABSTRACT KINETICS OF THE HYDRO-DEOXYGENATION OF STEARIC ACID OVER PALLADIUM ON CARBON CATALYST IN FIXED-BED REACTOR FOR THE PRODUCTION OF RENEWABLE DIESEL Name: Vam, Albert University of Dayton Advisor: Dr. Heinz J. Robota Biological oils are potential sources of liquid transportation fuels. In the presence of a precious metal catalyst under reducing conditions, the transformation of biological oils to liquid fuels proceeds sequentially. First, any double bond is quickly saturated. The double bond saturation is followed by the hydrogenolysis of the ester linkages which releases the saturated fatty acids from the propane backbone. -
Palladium on Carbon
Palladium on Carbon [7440-05-3] · Pd · Palladium on Carbon · (MW 106.42) (catalyst for hydrogenation of alkenes, alkynes, ketones, nitriles, imines, azides, nitro groups, benzenoid and heterocyclic aromatics; used for hydrogenolysis of cyclopropanes, benzyl derivatives, epoxides, hydrazines, and halides; used to dehydrogenate aromatics and deformylate aldehydes) Solubility: insol all organic solvents and aqueous acidic media. Form Supplied in: black powder or pellets containing 0.5-30 wt % of Pd (typically 5 wt %); can be either dry or moist (50 wt % of H2O). Analysis of Reagent Purity: atomic absorption. Handling, Storage, and Precautions: can be stored safely in a closed container under air but away from solvents and potential poisons such as sulfur- and phosphorus-containing compounds. Pyrophoric in the presence of solvents. General precautions for handling hydrogenation catalysts should be followed. The catalyst must be suspended in the organic solvent under an atmosphere of N2. During filtration the filter cake must not be allowed to go dry. If a filter aid is necessary, a cellulose-based material should be used if catalyst recovery is desired. Hydrogenation and Hydrogenolysis: Carbon-Carbon Bonds. The use of Pd/C for the selective reduction of alkynes to alkenes is generally not satisfactory, but a few examples have been reported. For example, the Pd/C-catalyzed reduction of 3,6-dimethyl-4-octyne-3,6- 1 diol gave the enediol in 98% yield after absorption of 1 mol of H2. Further reduction gave the diol in 99% yield. Pd on other supports, such as Pd/CaCO3 and Pd/BaCO3, are much more effective for this conversion. -
Hydrotreating of Tall Oils on a Sulfided Nimo Catalyst for The
IENCE SC • VTT SCIENCE • T S E Hydrotreating of tall oils on a sulfided NiMo catalyst N C O H I N for the production of base-chemicals in steam S O I V Dissertation L • crackers O S G T 83 Y H • R G The technology development for the production of value-added I E L S H 83 E G A I R chemicals from biomass through various thermo-chemical H C approaches is more demanding than ever. Renewable feedstocks H appear as the best starting materials to achieve these developments in an industrial perspective. Tall oil, the by-product of kraft-pulping process is already well-known as a sustainable and low cost feedstock. Hydrotreating of tall oils on a sulfided NiMo catalyst for... This research thesis validates the potential of tall oil as a renewable feedstock for the production of base-chemicals, especially olefins, as conceived in the thermo-chemical bio-refinery concept. The focus was on the use of hydrotreating and steam cracking technologies with different tall oil feedstocks. Particular advances were accomplished in terms of technology development for high yield of ethylene from a complex and challenging bio-feedstock, such as tall oil. Hydrotreating of tall oils on a sulfided NiMo catalyst for the production of base-chemicals in ISBN 978-951-38-8239-6 (Soft back ed.) ISBN 978-951-38-8240-2 (URL: http://www.vtt.fi/publications/index.jsp) steam crackers ISSN-L 2242-119X ISSN 2242-119X (Print) ISSN 2242-1203 (Online) Jinto Manjaly Anthonykutty VTT SCIENCE 83 Hydrotreating of tall oils on a sulfided NiMo catalyst for the production of base- chemicals in steam crackers Jinto Manjaly Anthonykutty VTT Technical Research Centre of Finland Ltd Thesis for the degree of Doctor of Technology to be presented with due permission of the School of Chemical Technology for public examination and criticism in Auditorium KE2 at Aalto University School of Chemical Technology (Espoo, Finland) on the 24th of April, 2015, at 12.00. -
The Art of Heterogeneous Catalytic Hydrogenation Part 1
The Art of Heterogeneous Catalytic Hydrogenation Part 1 An Introduction: Chemistry 536 by Bill Boulanger Adjunct Professor, Department of Chemistry University of Illinois at Urbana-Champaign [email protected] Recommended Books: Heterogeneous Catalysis for the Synthetic Chemist Robert L Augustine (1996) Practical Catalytic Hydrogenation, Techniques and Applications Morris Freifelder 1971 Recommended References Catalytic Hydrogenation over Platinum Metals P. N. Rylander 1967 What will Not be Covered Here: (Topics for Another Class) Homogenous catalysts Chiral catalysis What will be Covered Here: Some basic theory Catalysts Solvents, and their effects Structure effects Temperature effects Common and useful reductions with hydrogen How to use a Parr Shaker Tour of the High Pressure Lab Two Ways to Add Hydrogen: Hydrogenation: H H addition across Pi bonds A Y A Y Hydrogenolysis: Cleavage of Sigma A X A X bonds H H Catalysts: Overview Discrimination dependent upon: Metal Support Solvent Temperature Presence or absence of poisons Promoters Catalysts Overview, cont’d: Rate of reduction dependent upon: Catalyst preparation Time (in hours) since prep. of catalyst Pressure Temperature Loading of catalyst Why Choose Catalytic Hydrogenation? Simple work-up Generally clean reactions No extra ions or compounds to deal with; just remove solvent. Can be done neat. Most cost-effective choice for scale-up In Process; spent catalyst is usually recoverable for cost savings Rhenium Usually used in an oxide form (recovered in an oxide form) Requires vigorous conditions Best use is in reduction of carboxylic acids to alcohols or amides to amines Typical conditions: 200 atm and 150-250 °C Ruthenium Used as dioxide or metal on support Commercially available Active at 70-80 °C/ 60-70 atm Very resistant to poisoning Good choice for reduction of aromatic rings, but does not discriminate. -
Hydroconversion of Triglycerides Into Green Liquid Fuels
Chapter 8 Hydroconversion of Triglycerides into Green Liquid Fuels Rogelio Sotelo-Boyás, Fernando Trejo-Zárraga and Felipe de Jesús Hernández-Loyo Additional information is available at the end of the chapter http://dx.doi.org/10.5772/48710 1. Introduction Due to the depletion of crude reserves and the increasing demand for clean hydrocarbon fuels the production of renewable materials-based fuels has emerged to solve at least partially this problem in the past decade and it is expected to continue [1,2]. Green fuels can be classified as naphtha, jet fuel, and diesel. In the case of green diesel, its increasing demand could reach 900 million tons by 2020 [3]. The common ways to produce diesel-type fuel from biomass are a) by transesterification of triglycerides to obtain biodiesel, and b) by hydroprocessing to synthesize green diesel. Biodiesel is a mixture of fatty acid methyl esters (FAME) while green diesel is a mixture of hydrocarbons, mainly heptadecane and octadecane. Both fuels can be used as additives to petro-diesel. FAME can be used to enhance the lubricity of petro-diesel while green diesel can boost the cetane number. Biodiesel can be obtained with an alkaline liquid catalyst at 60 °C and atmospheric pressure, while green diesel requires a bifunctional solid catalyst (acid/metal), temperatures around 300 °C and ca. 5 MPa of hydrogen in a continuous flow process. The technology for producing green fuels from triglycerides has been used in petroleum refineries for about 60 years, for instance the same catalyst, reactor type and separation equipment used in the hydrotreating of vacuum gas oil can effectively be used for hydrotreatment of fats and vegetable oils.