Finite Element Analysis of Passenger Multiple Belt Restraint Configurations
Total Page:16
File Type:pdf, Size:1020Kb
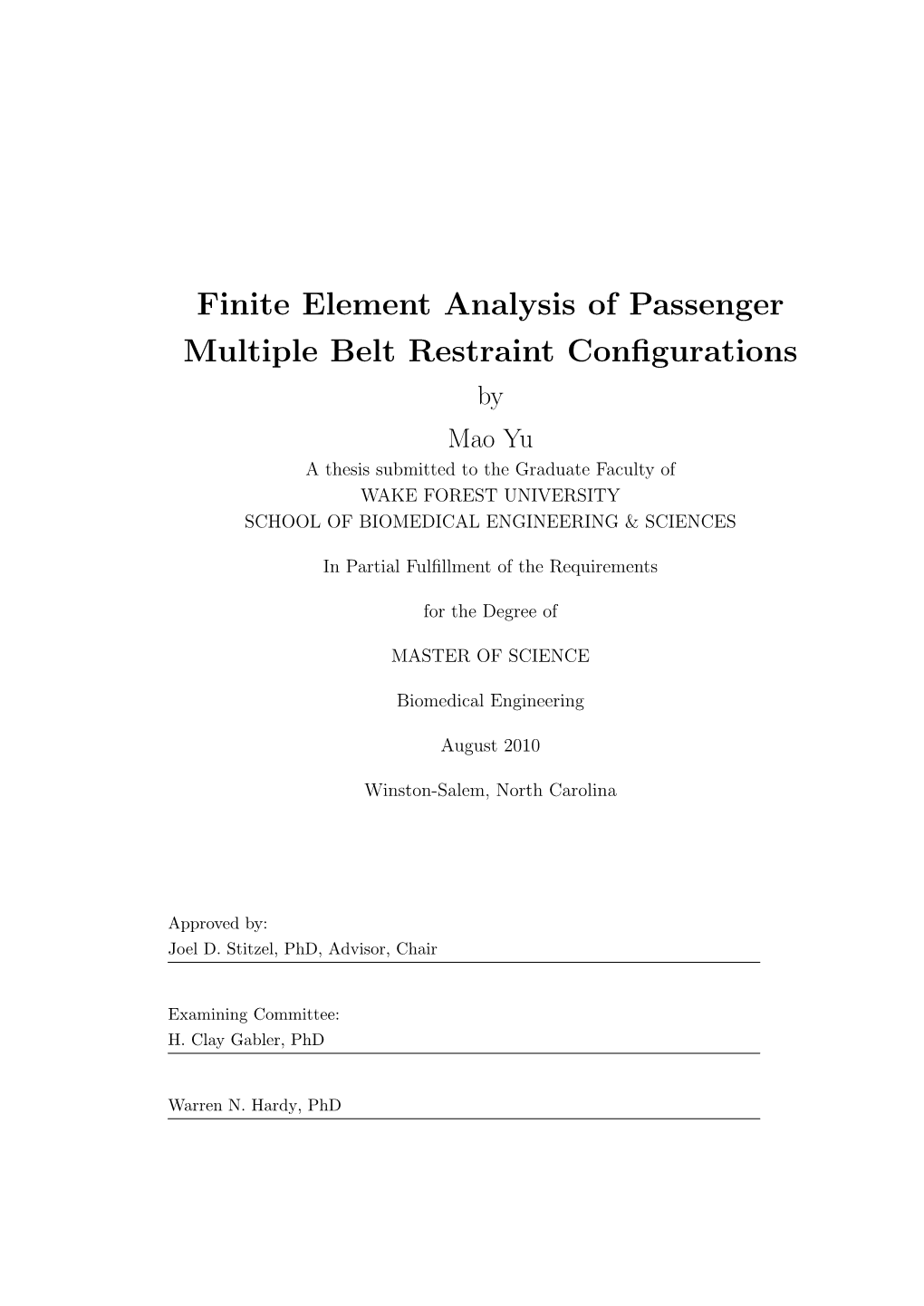
Load more
Recommended publications
-
Rainer Justen, Daimler AG, 2017-01-31 Advanced Automotive Battery Conference Europe Mainz, Germany
Requirements and Approaches for Li-Ion Batteries regarding Vehicle Safety Rainer Justen, Daimler AG, 2017-01-31 Advanced Automotive Battery Conference Europe Mainz, Germany Content 1 Mercedes-Benz Hybrid and Electric Vehicles 2 Battery Types and Challenges for Crash Safety 3 Legal Requirements and Safety Standards 4 Safety Concepts Daimler AG Crash Safety of HV-Batteries | Rainer Justen | Daimler AG | 2017-01-31 | 2 Mercedes-Benz Product Portfolio Hybrid and Electric Vehicles C 300h E 350e B-Klasse F-Cell S 300h GLC 350e smart ed GLE 500e B 250e C 350e S 500e Hybrid Vehicles Plug In Hybrid Vehicles Battery Electric Vehicles Daimler AG Crash Safety of HV-Batteries | Rainer Justen | Daimler AG | 2017-01-31 | Seite 3 Battery Types Hybrid Plug-In Hybrid Electric Dimension [mm] 450x180x150 Dimension [mm] 905x525x200 Dimension [mm] 1000x475x200 Weight / Volume 23 kg/12 Liter Weight / Volume 114 kg / 82 Liter Weight / Volume 175kg/90 Liter Cell Capacity (nominal) 50Ah Cell Capacity (nominal) 6,5Ah Cell Capacity (nominal) 22,5 Ah Cell Count 120 Cell Count 93 Cell Count 35 Cell Format PHEV 1 Cell Format HEA-50 Cell Format VL6P-round Energy@1C 8712 Wh (106Wh/l) Energy@1C 17,6 kWh Energy@1C 0,8 kWh Voltage 240V to 432V Voltage 391V Voltage 143V Peak Power > 90 kW Peak Power 75 kW Peak Power 22 kW Continuous Power 40 kW Continuous Power 55 kW Life Time 10y / 300.000 micro cycles Life Time 10y / 300.000km Life Time 10y / 300.000km Daimler AG Crash Safety of HV-Batteries | Rainer Justen | Daimler AG | 2017-01-31 | Seite 4 Challenges for Crash Safety -
Proposal of Simulation Method for Behaviour Analysis of Passengers on Longitudinal Seating in Railway Collision
IRC-15-44 IRCOBI Conference 2015 Proposal of Simulation Method for Behaviour Analysis of Passengers on Longitudinal Seating in Railway Collision Daisuke Suzuki, Kazuma Nakai, Shota Enami, Tomohiro Okino, Junichi Takano, Roberto Palacin Abstract In railway collisions, passengers are thrown from their seats and translate long distances because they are not restrained by a seatbelt. This creates the possibility of serious injury caused by collision with interior components at high velocity. It is important, therefore that passengers’ behaviours are estimated. This study focuses on a passenger seated on longitudinal seating away from a bench‐end partition. They translated and then pitched over with its head leading any other physical part. Sled tests for imitating a situation where a passenger collides with the bench‐end partition were conducted. Then, numerical simulations for reproducing the sled tests were performed with MADYMO. The dummy’s behaviours of the numerical simulations, which are collision position and collision velocity, were almost equivalent to those of the sled tests. On the other hand, the head accelerations of the simulations were different from those of the sled tests greatly. Thus the joints of the dummy model’s neck were improved. The head accelerations of the simulations after the improvement almost corresponded with those of the sled tests. Keywords behaviour analysis, longitudinal seating, multi‐body dynamics, seated passenger, railway collision. I. INTRODUCTION It is important that severe injuries are prevented when a railway collision happened. Since the railway passengers do not have a seat belt, they are thrown from their seat by the acceleration of collision and collide with interior components. -
Validation of Material Models for Crash Simulation of Automotive Carbon Fiber Composite Structures (VMM)
Validation of Material Models for Crash Simulation of Automotive Carbon Fiber Composite Structures (VMM) Libby Berger (General Motors), Omar Faruque (Ford) Co-Principal Investigators US Automotive Materials Partnership June 7, 2016 Project ID: LM084 This presentation does not contain any proprietary, confidential, or otherwise restricted information Project Overview BARRIERS . Predictive Modeling Tools TIMELINE – Validation of carbon fiber composites material models for • Project start date: 6/1/2012 crash simulation, which will be demonstrated via design, analysis, fabrication, and crash testing. • Project end date: 11/30/2016 Analyses of CAE Gaps • Percent complete: 75% – Correlate manufacturing and assembly processes to gaps in CAE material characterization and subsequent prediction through post-processing evaluation and NDE. PARTNERS . Northwestern University (sub-awardee) . University of Michigan (sub-awardee) BUDGET . Wayne State University (sub-awardee) • Total project funding . M-Tech International LLC • DOE share: $3,445,119 . ESI North America, Inc. • Contractor share : $3,445,119 . Continental Structural Plastics . Highwood Technology LLC • Funding received in FY15: $598,315 . Dow Automotive • Funding for FY16: . Shape Corp • DOE share: $1,166,669 . LSTC • Contractor share:$1,166,669 . Altair Engineering . AlphaSTAR Corp. 2 . Project Lead: USAMP (GM, Ford, FCA Group) Relevance: VMM Objective: Validation of Carbon Fiber Composite (CFC) Material Models for Crash Simulation of Automotive Structures Project Goal: Validate existing CFC material models in commercial crash codes and a selected number of models developed by previous Automotive Composites Consortium (ACC) projects with academic partners, which leveraged DOE funds. This will be accomplished by performing predictive crash simulations for critical high and low speed impact cases for a representative CFC Front Bumper and Crush Can (FBCC) System, fabricating CFC FBCCs, conducting the appropriate crash tests, and comparing the results. -
The Tracking Method of Vehicle Point Or Dummy Point in the Vehicle Crash by Calculating Linear Accelerometer and Angular Velocity
th 24 ESV Conference The tracking method of vehicle point or dummy point in the vehicle crash by calculating linear accelerometer and angular velocity Park Un-chin Song Ha-jong* Kim Hyun-chul** Florian Ganz*** Sudar Sankar*** Christian Santos*** ABSTRACT From the mathematical equations we can get the point coordinates with 3 axis linear accelerometer and 3 axis angular velocity by integration. In this research, we will introduce two unique algorithms-acceleration method and velocity method of Hyundai-Kia motors and ACTs and prove the accuracy from many kinds of dummy inboard or outboard tracking case and vehicle body point. Key Word : Gyro, Tracking, Vehicle Crash, Dummy, accelerometer, angular velocity 1. Introduction common 3 axis linear accelerometer and 3 axis angular velocity data and diadem software, not expensive sensor Target tracking is useful in the vehicle crash test or software, so we believe this can be widely and easily analysis because we can check the contact of 2 objects used in crash analysis. and compare what is different on the moving among the several tests. If we use video target tracking, it takes some more time than point tracking by calculating 3 axis linear 2. Main Subject accelerometer and 3 axis angular velocity because we should convert the high speed film file and analyze by 2.1 Theories and related formula in physics. video tracking program like TEMA. Also, the resolution of tracking data become lower because the resolution of 2.1.1 The velocity relative to fixed system "S" high speed film is 1,000Hz and that of sensor data is Considering two axis systems, "S" fixed to ground and 10,000 Hz. -
The Impact of Crash Simulation on Productivity and Problem-Solving in Automotive R&D
A Service of Leibniz-Informationszentrum econstor Wirtschaft Leibniz Information Centre Make Your Publications Visible. zbw for Economics Spethmann, Philipp; Thomke, Stefan H.; Herstatt, Cornelius Working Paper The impact of crash simulation on productivity and problem-solving in automotive R&D Working Paper, No. 43 Provided in Cooperation with: Hamburg University of Technology (TUHH), Institute for Technology and Innovation Management Suggested Citation: Spethmann, Philipp; Thomke, Stefan H.; Herstatt, Cornelius (2006) : The impact of crash simulation on productivity and problem-solving in automotive R&D, Working Paper, No. 43, Hamburg University of Technology (TUHH), Institute for Technology and Innovation Management (TIM), Hamburg This Version is available at: http://hdl.handle.net/10419/55496 Standard-Nutzungsbedingungen: Terms of use: Die Dokumente auf EconStor dürfen zu eigenen wissenschaftlichen Documents in EconStor may be saved and copied for your Zwecken und zum Privatgebrauch gespeichert und kopiert werden. personal and scholarly purposes. Sie dürfen die Dokumente nicht für öffentliche oder kommerzielle You are not to copy documents for public or commercial Zwecke vervielfältigen, öffentlich ausstellen, öffentlich zugänglich purposes, to exhibit the documents publicly, to make them machen, vertreiben oder anderweitig nutzen. publicly available on the internet, or to distribute or otherwise use the documents in public. Sofern die Verfasser die Dokumente unter Open-Content-Lizenzen (insbesondere CC-Lizenzen) zur Verfügung gestellt haben sollten, If the documents have been made available under an Open gelten abweichend von diesen Nutzungsbedingungen die in der dort Content Licence (especially Creative Commons Licences), you genannten Lizenz gewährten Nutzungsrechte. may exercise further usage rights as specified in the indicated licence. www.econstor.eu Technologie- und Innovationsmanagement W o r k i n g P a p e r The Impact of Crash Simulation on Productivity and Problem-Solving in Automotive R&D Philipp Spethmann, Stefan H. -
Computer Crash Simulations in the Development of Child Occupant Safety Policies
ARTICLE Computer Crash Simulations in the Development of Child Occupant Safety Policies Flaura Koplin Winston, MD, PhD; Kristy B. Arbogast, PhD; Lois A. Lee, MD; Rajiv A. Menon, PhD Objective: To address the predictability of injury from restrained male adults exposed to air bags or for child air bag activation by use of crash simulation software. passengers restrained in the rear seat for the crash sce- narios simulated. Methods: Using current, validated crash simulation soft- ware, the effect of air bag activation on injury risk was Conclusions: Using current crash simulation software, this assessed for the 6-year-old child, both restrained and un- study demonstrated that the risk of air bags to school- restrained. Results were compared with those for adult aged children could be predicted. Our results confirmed occupants in similar crash scenarios. the previously identified risks to unrestrained children and provided the first evidence that air bags, in their current Results: For the unrestrained child passenger, crash design, are not beneficial to restrained children. This study simulations predicted serious head, neck, and chest in- illustrates that computer crash simulations should be used juries with air bag activation, regardless of crash sever- proactively to identify injury risks to child occupants, par- ity. For the restrained child passenger, crash simula- ticularly when limited real-world data are available. tions predicted similar severe injuries for high-severity crashes only. No serious injuries were predicted for un- Arch Pediatr Adolesc Med. 2000;154:276-280 of crash scenarios. They have been used Editor’s Note: This study can have significant impact on the man- as a standard, validated tool by vehicle and ner in which automobile crashes would cause air bag injuries. -
EFFECTS of ANGLES and OFFSETS in CRASH SIMULATIONS of AUTOMOBILES with LIGHT TRUCKS John C
EFFECTS OF ANGLES AND OFFSETS IN CRASH SIMULATIONS OF AUTOMOBILES WITH LIGHT TRUCKS John C. Brewer Volpe National Transportation Systems Center United States Paper Number 308 each vehicle in each case is 50 kph. The models are ABSTRACT using LS-DYNA finite element software. Characteristics of the two models are given in Two series of finite element and lumped Table 1. parameter model vehicle-to-vehicle frontal crash simulations were conducted. The vehicles modeled are the 1994 Chevrolet C-1500 light truck and the 1997 Ford Crown Victoria. The first set of simulations involves fully-engaged angled impact. Angles range from +50° to -50°. The second set simulates offset impacts in head-on vehicle crashes. The front-end overlap ranged from 20% of the average width of the vehicles to 100% (fully engaged). Driver and passenger injury is assessed using a MADYMO model of a generic automobile interior subject to the horizontal occupant compartment translation and rotations. The results of the two simulation sets are examined for qualitative changes in structural deformation modes, energy absorption, and injury. Relative injury is assessed by head injury criterion (HIC) with a 36-millisecond Figure 1. Chevrolet C-1500 finite element model. window and 3-millisecond chest acceleration clip. These criteria are less sensitive to occupant compartment intrusion than other injury metrics. INTRODUCTION The severity of injury incurred in motor vehicle crashes is governed by a complex function of initial conditions, geometric characteristics, and material properties of both the vehicles and the occupants. Small changes in these inputs can cause significant changes in the output (i.e., occupant injury) depending on the timing and geometry of the load paths that are created and destroyed within the vehicle during the deformation process. -
Simulations of Pedestrian Impact Collisions with Virtual CRASH 3 and Comparisons with IPTM Staged Tests
Simulations of Pedestrian Impact Collisions with Virtual CRASH 3 and Comparisons with IPTM Staged Tests Tony Becker, ACTAR, Mike Reade, Bob Scurlock, Ph.D., ACTAR Introduction and dummy systems as point-like particles. From the dummy was used rather than the puck. Again we see work-energy theorem [3], we expect a change in kinetic excellent agreement between the analytic solution and In this article, we present results from a series of Virtual energy to be associated with dissipative frictional forces. simulation, with only some slight deviation at high CRASH-based pedestrian impact simulations. We That is: friction values. This is due to the dummy’s body compare the results of these Virtual CRASH pedestrian rotating toward the end of its motion at high speeds. impact simulations to data from pedestrian impact 푓 ̅ collisions staged at the Institute of Police Technology 푊 = ∫ 퐹 ∙ 푑푟̅ = ∆퐾퐸 Figure 3 illustrates the sliding distance and speed versus and Management. 푖 time for the puck and dummy, where each is given an 1 2 1 2 = 푚푣푓 − 푚푣푖 (1) initial speed of 30 mph, and a ground contact 2 2 1 Staged Pedestrian Impact Experiments coefficient-of-friction of 0.6 is used in the simulations. where the mass is displaced from point i to point f along We see very good agreement in the behaviors of the Each year the Institute of Police Technology and some path. In the one-dimensional constant frictional puck and dummy. Indeed, focusing on the velocity Management (IPTM) stages a series of pedestrian force approximation, we have: versus time behavior of the two systems in Figure 4, impact experiments as a part of its Pedestrian and first-order polynomial fits are performed to both sets of Bicycle Crash Investigation courses. -
Best Practices Simulation for Crash Modeling
NASA/TM-2002-211944 ARL-TR-2849 Best Practices for Crash Modeling and Simulation Edwin L. Fasanella and Karen E. Jackson U.S. Army Research Laboratory Vehicle Technology Directorate Langley Research Center, Hampton, Virginia October 2002 The NASA STI Program Office... in Profile Since its founding, NASA has been dedicated CONFERENCE PUBLICATION. to the advancement of aeronautics and space science. Collected papers from scientific and The NASA Scientific and Technical Information technical conferences, symposia, (STI) Program Office plays a key seminars, or other meetings sponsored or part in helping NASA maintain this co-sponsored by NASA. important role. SPECIAL PUBLICATION. Scientific, The NASA STI Program Office is operated by technical, or historical information from Langley Research Center, the lead center for NASA's NASA programs, projects, and missions, scientific and technical information. often concerned with subjects having The NASA STI Program Office provides substantial public interest. access to the NASA STI Database, the largest collection of aeronautical and space science STI in the world. The Program Office TECHNICAL TRANSLATION. English- is also NASA's institutional mechanism for language translations of foreign scientific disseminating the results of its research and and technical material pertinent to NASA's mission. development activities. These results are published by NASA in the NASA STI Report Series, which includes the following report Specialized services that complement the types: STI Program Office's diverse offerings include creating custom thesauri, building customized TECHNICAL PUBLICATION. Reports of databases, organizing and publishing completed research or a major significant research results.., even providing videos. phase of research that present the results of NASA programs and include extensive For more information about the NASA STI data or theoretical analysis. -
Vehicle Far-Side Impact Crashes
VEHICLE FAR-SIDE IMPACT CRASHES Richard Stolinski Raphael Grzebieta Department of Civil Engineering Monash University, Clayton Australia Brian Fildes Accident Research Centre Monash University, Clayton Australia. Paper 98-S8-W-23 These occupants are defined as near-side occupants. ABSTRACT All regulatory side impact test standards focus exclusively on this scenario and rely on an assessment This is a summary of a paper which first appeared provided by one test intended to represent one point in the International Journal of Crashworthiness under in the spectrum of real world near-side impact the title: “Side Impact Protection - Occupants in the crashes. Far-Side Seat”, Vol. 3, No. 2, pp 93-122. Readers are Real world crash evidence however has shown directed to the full paper for a more comprehensive that far-side occupants as illustrated in Figure 1, are discussion of the issues presented here. still subject to a risk of injury. The study by Fildes et Much of the applied vehicle side impact occupant al noted that around 40 percent of restrained side protection research to date has concentrated on impact crash casualties were far-side occupants. occupants seated beside the struck side of vehicles. Relatively little research literature is available that These occupants are defined as ‘near-side’ occupants. addresses protection of far-side occupants. The scope Real world crash evidence however has shown that of this paper thus addresses far-side occupants where occupants seated on the side away from the struck there may be opportunities for improved occupant side, defined as ‘far-side’ occupants, are still subject protection. -
Experiences During Development of a Dynamic Crash Response Automobile Model
Finite Elements in Analysis and Design 30 (1998) 279Ð295 Experiences during development of a dynamic crash response automobile model J.G. Thacker, S.W. Reagan, J.A. Pellettiere, W.D. Pilkey1,*, J.R. Crandall, E.M. Sieveka Automobile Safety Laboratory, Department of Mechanical, Aerospace, and Nuclear Engineering, University of Virginia, Charlottesville, VA 22903, USA Abstract A finite element automobile model for use in crash safety studies was developed through reverse engineering. The model was designed for calculating the response of the automobile structure during full frontal, o¤set frontal, or side impacts. The reverse engineering process involves the digitization of component surfaces as the vehicle is dismantled, the meshing and reassembly of these components into a complete finite element model, and the measurement of sti¤ness properties for structural materials. Quasi-static component tests and full-vehicle crash tests were used to validate the model, which will become part of a finite element vehicle fleet. ( 1998 Elsevier Science B.V. All rights reserved. Keywords: Automobile modeling; Non-linear finite element modeling; Reverse engineering 1. Introduction Environmental pressures have provided the incentive to look for ways to reduce the need for energy and to reduce the pollutants that are often associated with its generation. This is parti- cularly true in the automotive industry, which is closely associated with the world’s most extensive usage of fossil fuels. One of the best ways to reduce fossil fuel consumption by vehicles is to reduce their weight drastically. However, this creates a problem for the near-term, since these ªNew Generation Vehiclesº (NGVs) will be very di¤erent from the rest of the fleet in terms of both weight and structure. -
FEA Newsletter December 2000
FEA Information Co. For the LS-DYNA Global Community www.feainformation.com Third Issue, December 9, 2000 Welcome to the third issue of our newsletter. Our goal is to bring you a monthly synopsis of the additions/revisions to the FEA Information web sites and to assist you in focusing your attention to the new material when you consult our web pages on return visits. When available, we’ll bring you information from our participating companies, engineers, professors, consultants, and students of FEA Information. Feel free to have your associates send me an e-mail to be added to our private mailing list [email protected] Page Article Submitted By: 2 – 4 Implicit Notes I. Dr. Bradley Maker, LSTC Topic A. Implicit/Explicit Switching Topic B. Lanczos Eigenvalue Solver Topic C. Tied Contact Interfaces by Constraint Method 5 – 9 Case Study – DaimlerChrysler Previously Published in the CAD-FEM Infoplanar 10 The 5th LS-DYNA Users Conference Theme Korea – October 2000 11 FEA Site Summary & Future Goals Marsha Victory, FEA Information 12 Engineering Student Forum Dr. David Benson, UCSD 13 December Sponsors & Products LSTC ETA OASYS 1 Implicit Notes I Dr. Bradley Maker Livermore Software Technology Corporation Topic A Implicit/Explicit Switching LS-DYNA version 960 can perform both explicit and implicit simulations. A new feature is available which allows both formulations to be used during a single simulation. A load curve can be defined which controls formulation switching. This feature can be used, for example, to simulate a statically initialized impact: Begin with a static implicit analysis, and after applying some load, switch to dynamic explicit analysis and proceed with an impact simulation.