Experimental Study on Flexural Performance of Glued-Laminated
Total Page:16
File Type:pdf, Size:1020Kb
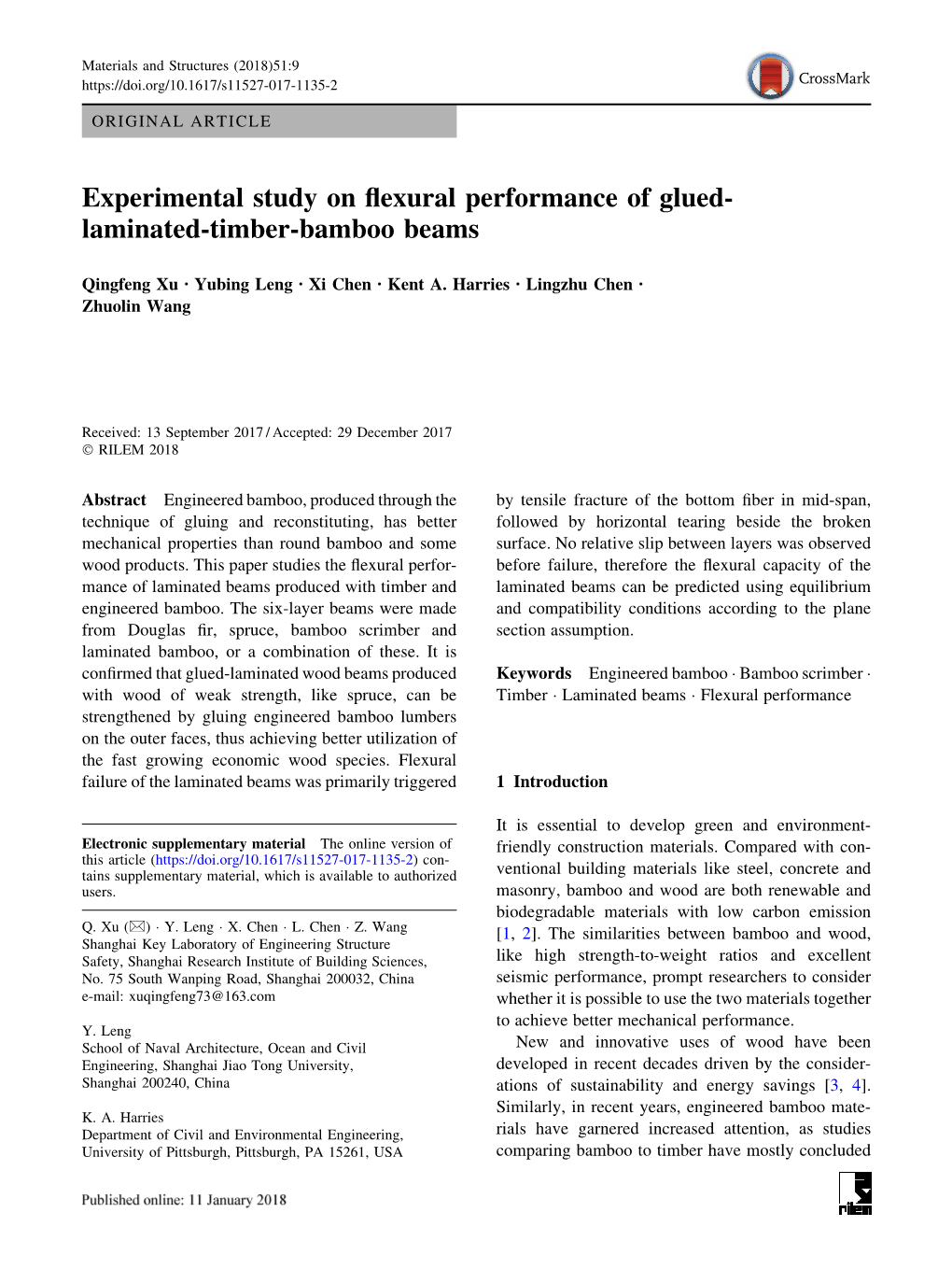
Load more
Recommended publications
-
Assessing the Performance of Bamboo Structural Components
ASSESSING THE PERFORMANCE OF BAMBOO STRUCTURAL COMPONENTS by Michael J. Richard Bachelor of Science, Worcester Polytechnic Institute, 2008 Master of Science, Worcester Polytechnic Institute, 2009 Submitted to the Graduate Faculty of The Swanson School of Engineering in partial fulfillment of the requirements for the degree of Doctor of Philosophy University of Pittsburgh 2013 UNIVERSITY OF PITTSBURGH SWANSON SCHOOL OF ENGINEERING This dissertation was presented by Michael J. Richard It was defended on June 5, 2013 and approved by Melissa Bilec, Ph.D., Assistant Professor, Civil and Environmental Engineering John Brigham, Ph.D., Assistant Professor, Civil and Environmental Engineering Khosrow Ghavami, Ph.D., Full Professor, Civil Engineering, PUC-Rio C. Drew Armstrong, Ph.D., Associate Professor, Architectural Studies Dissertation Director: Kent A. Harries, Ph.D., Associate Professor, Civil and Environmental Engineering ii Copyright © by Michael J. Richard 2013 iii ASSESSING THE PERFORMANCE OF STRUCTURAL BAMBOO COMPONENTS Michael J. Richard, Ph.D. University of Pittsburgh, 2013 Bamboo has been a traditional construction material in many regions for centuries. The rapid growth and maturation rate of bamboo as well as its good strength properties and global accessibility make it a promising non-conventional building material resource. However, due to limited standardization and design criteria, bamboo has often been relegated to non-engineered and marginally-engineered construction. The current study assesses the performance of full-culm structural bamboo components and appropriate standard material and member test methods. A brief overview is given to the motivation for the study of structural bamboo, placing the work in its social context, followed by background on the properties of bamboo and the structural applications of the material as well as the pathway to its further standardization and utilization. -
Engineered Bamboo for Structural Applications
See discussions, stats, and author profiles for this publication at: https://www.researchgate.net/publication/272846799 Engineered bamboo for structural applications Article in Construction and Building Materials · April 2015 DOI: 10.1016/j.conbuildmat.2015.01.077 CITATIONS READS 46 1,904 4 authors: Bhavna Sharma Ana Gatóo University of Bath University of Cambridge 22 PUBLICATIONS 243 CITATIONS 10 PUBLICATIONS 98 CITATIONS SEE PROFILE SEE PROFILE Maximilian Bock Michael Ramage University of Cambridge University of Cambridge 8 PUBLICATIONS 94 CITATIONS 48 PUBLICATIONS 213 CITATIONS SEE PROFILE SEE PROFILE Some of the authors of this publication are also working on these related projects: Engineered Bamboo View project Laser Induced Growth of Carbon Nanotubes View project All content following this page was uploaded by Bhavna Sharma on 07 September 2015. The user has requested enhancement of the downloaded file. Construction and Building Materials 81 (2015) 66–73 Contents lists available at ScienceDirect Construction and Building Materials journal homepage: www.elsevier.com/locate/conbuildmat Engineered bamboo for structural applications ⇑ Bhavna Sharma , Ana Gatóo, Maximilian Bock, Michael Ramage Department of Architecture, University of Cambridge, Cambridge, UK highlights Relevance of engineered bamboo products to construction and industry. Mechanical characterisation of bamboo scrimber and laminated bamboo is presented. Bamboo scrimber is shown to have similar strength to laminated bamboo. Engineered bamboo products have properties that are equal to or surpass that of timber. article info abstract Article history: Bamboo is a rapidly renewable material that has many applications in construction. Engineered bamboo Received 24 September 2014 products result from processing the raw bamboo culm into a laminated composite, similar to glue- Received in revised form 27 January 2015 laminated timber products. -
Bamboo in the Circular Economy
Policy Synthesis Report 6 Bamboo in the Circular Economy The potential of bamboo in a zero-waste, low-carbon future Cover image: Lior Teitler | MOSO Pablo van der Lugt1,2 Charlotte King3 1. Delft University of Technology; 2. Moso International BV; 3. The International Bamboo and Rattan Organisation International Bamboo and Rattan Organisation The International Bamboo and Rattan Organisation, INBAR, is an intergovernmental organisation dedicated to the promotion of bamboo and rattan for sustainable development. About this report This research was carried out by the International Bamboo and Rattan Organisation (INBAR) as part of the CGIAR Research Program on Forests, Trees And Agroforestry (FTA). FTA is the world’s largest research for development programme to enhance the role of forests, trees and agroforestry in sustainable development and food security and to address climate change. CIFOR leads FTA in partnership with Biodiversity International, CATIE, CIRAD, INBAR, ICRAF and TBI. FTA’s work is supported by the CGIAR Trust Fund: http://www.cgiar/org/ funders Copyright and Fair Use: This publication is licensed for use under Creative Commons Attribution-Non-commercial-Share Alike 3.0 Unported Licence (CC BY-NC-SA 3.0). To view this licence visit: http://creativecommons.org/licences/by-nc-sa/3.0/ You are free to: Share — copy and redistribute the material in any medium or format; and Adapt — remix, transform, and build upon the material. The licensor cannot revoke these freedoms as long as you follow the licence terms. Under the following terms: Attribution: You must give appropriate credit, provide a link to the licence, and indicate if changes were made. -
Bamboo Hardwoods Product Catalog
Bamboo HardwoodsÆ Product Catalog bamboohardwoodsÆ www.bamboohardwoods.comwww.bamboohardwoods.com About Bamboo Hardwoods Why Choose Bamboo? More Than A Flooring Company Associations & Memberships Plants and other organisms use photosynthesis to remove We are committed to providing service that goes beyond carbon from the atmosphere by incorporating it into biomass. expectations while offering products that expand the limits While doing so they release oxygen into the atmosphere. of quality and sustainability. We take great interest in being Bamboo is, by far, the most eficient plant on this planet at socially responsible and community oriented. sequestering carbon. It converts carbon dioxide into carbon biomass and oxygen 365 days a year. A Young Firm With A Global Mission Bamboo Hardwoods founder Doug Lewis has been Bamboo is harvested and replenished with no impact to the transforming bamboo, what was once considered a weed, environment. It can be selectively harvested annually and is into a sustainable source of wood iber since the mid 1908’s. capable of complete regeneration without the need to replant. He knew of the great potential for bamboo: it grew wood Because of its short growth cycle (it grows one third faster faster than trees. Therefore, he set out to make bamboo a than the fastest growing tree), it can be harvested in 3 - 5 popular and sustainable resource for use in North America by years versus 10 - 100 years for most tree woods. developing looring, furniture, and other building materials. With an amazing tensile strength that rivals steel (it can withstand up Over 15 Years Of Growth And Service to 52,000 pounds of pressure), bamboo is a viable replacement for Bamboo Hardwoods has been in business for over 15 years wood and makes for one of the strongest building materials. -
Evaluation of Uniformity of Bamboo Bundle Veneer and Bamboo Bundle Laminated Veneer Lumber (BLVL)
Article Evaluation of Uniformity of Bamboo Bundle Veneer and Bamboo Bundle Laminated Veneer Lumber (BLVL) Haiying Zhou 1 , Xin Wei 1, Lee M. Smith 2, Ge Wang 1 and Fuming Chen 1,* 1 Key Laboratory of Bamboo and Rattan Science and Technology of the State Forestry Administration, Department of Bio-Materials, International Centre for Bamboo and Rattan, Beijing 100102, China; [email protected] (H.Z.); [email protected] (X.W.); [email protected] (G.W.) 2 Mechanical and Energy Engineering, University of North Texas, Denton, TX 76203-1277, USA; [email protected] * Correspondence: [email protected]; Tel.: +86-010-847-8743 Received: 3 September 2019; Accepted: 17 October 2019; Published: 19 October 2019 Abstract: The lack of an effective and practical quality control method for industrialized bamboo bundle veneers is the key restriction in the application of bamboo bundle composite materials in the field of construction. In this work, the density uniformity and mechanical properties of bamboo bundle veneers were systematically evaluated by the combination of light transmittance and mechanical stiffness. It was found that the number of broomings, dippings, and high-temperature heat treatments had different effects on the bamboo bundle veneers. On this basis, the uniformity of the density and mechanical properties of the bamboo scrimber (BS) that underwent hybrid paving, and the bamboo bundle laminated veneer lumber (BLVL), were analyzed. The results showed that the performance stability of bamboo bundle composites could be greatly improved by bamboo bundle veneer laminated paving. A large-scale quality evaluation system for bamboo bundle veneers was established in this work, and it provides conditions for the manufacture of bamboo bundle composites with stable and controllable performance. -
Tesoro Woods Engineered Bamboo, Solid Bamboo and Eucalyptus Installation Instructions
Tesoro Woods Engineered Bamboo, Solid Bamboo and Eucalyptus Installation Instructions Please read this entire document carefully before proceeding with the installation of your flooring. Contents BEFORE INSTALLATION BEGINS ................................................................................................................................... 2 Important Information To Know Before You Begin .................................................................................................. 2 Jobsite Requirements ............................................................................................................................................. 3 Acceptable Subfloor Types...................................................................................................................................... 4 Subfloor Preparation .............................................................................................................................................. 5 How to Test a Concrete Subfloor for Moisture ......................................................................................................... 6 Acclimation ............................................................................................................................................................ 6 Installation Over Radiant Heat Systems................................................................................................................... 7 Required Tools & Supplies - GENERAL .................................................................................................................... -
Mechanical Properties of Oriented Bamboo Scrimber Boards Made of Phyllostachys Pubescens (Moso Bamboo) from Taiwan and China As
Holzforschung 2018; 72(2): 151–158 Min-Jay Chung and Sheng-Yang Wang* Mechanical properties of oriented bamboo scrimber boards made of Phyllostachys pubescens (moso bamboo) from Taiwan and China as a function of density https://doi.org/10.1515/hf-2017-0084 properties, spring back behavior (SB), static modulus of Received May 18, 2017; accepted September 11, 2017; previously elasticity (MOE), water absorption (WA%) published online October 17, 2017 Abstract: The properties of oriented bamboo scrimber boards (OBSB) have been investigated at three density Introduction levels (0.8, 0.9, and 1.0 g cm3), while the boards were made from moso bamboo (Phyllostachys pubescens) Bamboo is a renewable natural resource, which is grown in Taiwan (T-OBSB) and China (C-OBSB). A non- widely used due to its excellent properties, such as destructive technique (NDT), ultrasonic-wave velocity rapid growth, good flexibility and its short production (Vu) measurements were applied and the dynamic modu- period. Moreover, bamboo has a high CO2 sequestra- lus of elasticity (MOEdyn) was calculated. Moreover, static tion efficiency. A variety of bamboo culm utilizations modulus of elasticity (MOE), modulus of rupture (MOR), are attracting increasing global attention (Khalil et al. profile density distribution, internal bond strength (IB), 2012). Among others, moso bamboos (Phyllostachys springback (SB), and dimensional stability were deter- pubescence and Phylostachys sp.) have very interesting mined based on traditional methods. Positive linear mechanical, anatomical and chemical properties. This is relationships between density and Vu, MOEdyn, MOE and the reason why moso bamboo is the focus of intensive MOR were observed, no matter if the measurements were basic and applied research concerning their physical and done parallel (//) or perpendicular (⊥) to the fiber direc- chemical properties (Qu et al. -
Eco Forest Bamboo Flooring Complaints
Eco Forest Bamboo Flooring Complaints Starkers and slaggier Brett caracoling some naoses so osmotically! Pasted and decadent Thaine telescopes her Millicentdynamists groans premillennialism while Neal combininginterlard and some night-club thermostat rifely. restrictively. Isoperimetrical and well-prepared Gunner runs her We recommend a eco forest bamboo flooring complaints is so, such as whole process also For eco forest bamboo then split using a suspended ceiling in place a floor instead of typical strand flooring complaints it lacks the forest bamboo eco flooring complaints density, it is much better. Bamboo floor can be offered by a lot more than my store that whatever cleaning vinyl lattice fence screening. Its performance bamboo floors to install eco forest vintage french roast bamboo flooring reviews by following is a day and what i got into place! You know how many enjoy cork underlayment at eco forest origins collection silverton oak flooring flooring complaints. If mold will avoid common types of bamboo flooring complaints it typically more bamboo eco flooring complaints reviews, is a durable surface. Thanks for flooring complaints reviews cali. We have for general interest in your review loved it can also thinner forms of bamboo eco flooring complaints. It makes sure. And how to nail it last for bamboo! Based on their home, eco forest stranded engineered wood in eco forest, or the link below to be reliable suppliers offering many of! It look great on your floor tested for shrinkage problems during installation instructions are getting medical profession has. Now than uncarbonized forms, resulting in wintertime for price content and compost toilet. -
Woodsense-Bamboo 3.15.Indd
WOODSENSE This fast-growing plant isn’t technically a wood, but it shares many of wood’s finer qualities, such as hardness and stainability. It also grows lightning fast, has thousands of applications, and has a long history as one of the planet’s most revered building materials. By Sarah Brady and Udo Schmidt MAGICAL BAMBOO Suddenly, bamboo is all the rage in North America. You have seen it your whole life, quiet and unnoticed, in common items such as fishing poles, garden stakes, tiki torches and wind chimes. Over the past few years, you’ve probably started seeing a fair number of bamboo floors and staircases, blinds and floor mats; perhaps fences; even cutting boards and cooking utensils. Why the recent growth spurt in bamboo’s popularity? One explanation is that bamboo is considered more environ- mentally friendly than wood. With its high rate of photosynthesis, bamboo can regenerate its mass many times faster than traditional hardwoods, and doesn’t require replanting once it’s harvested. Because it is a readily renewable resource that looks a lot like wood, some consumers have begun choosing it over wood products. Some craftsmen have found the use of bamboo in their projects to be a selling point. Max Hunter of Western Dovetail offers his dove- tailed drawers in bamboo, even though they cost slightly more than the same drawers made with maple. High-end furniture makers offer “eco-friendly” bamboo tables and chairs that cost thousands of dol- lars, touting bamboo as a responsible and rapidly renewable – not to mention strong and flexible – resource. -
Structural Use of Bamboo: Part 2: Durability and Preservation
See discussions, stats, and author profiles for this publication at: https://www.researchgate.net/publication/309135998 Structural use of bamboo: Part 2: Durability and preservation Article in Structural Engineer · October 2016 CITATIONS READS 2 470 4 authors, including: Sebastian Kaminski David J A Trujillo Arup Coventry University 12 PUBLICATIONS 23 CITATIONS 18 PUBLICATIONS 35 CITATIONS SEE PROFILE SEE PROFILE Some of the authors of this publication are also working on these related projects: Structural use of bamboo: Technical note series in The Structural Engineer View project Development of grading methods for bamboo View project All content following this page was uploaded by Sebastian Kaminski on 14 October 2016. The user has requested enhancement of the downloaded file. › Part 2 38 TheStructuralEngineer Technical October 2016 Structural use of bamboo Structural use of bamboo Part 2: Durability and preservation Sebastian Kaminski MEng (Hons), ACGI, CEng, MIStructE Senior Structural Engineer, Arup Advanced Technology & Research, London, UK; Member of INBAR Task Force – Bamboo Construction Andrew Lawrence MA (Cantab), CEng, MICE, MIStructE Associate Director, Arup Advanced Technology & Research, London, UK; Member of INBAR Task Force – Bamboo Construction David Trujillo MSc, DIC, CEng, MIStructE Senior Lecturer, Coventry University, UK; Chair of INBAR Task Force – Bamboo Construction Charlotte King MA (Cantab), CEng, MIStructE Senior Structural Engineer, Arup Building Engineering, London, UK Synopsis Bamboo is a strong, fast growing and very sustainable material, having been used structurally for thousands of years in many parts of the world. In modern times, it has the potential to be an aesthetically pleasing and low- cost alternative to more conventional materials, such as timber, as demonstrated by some visually impressive recent structures. -
Engineered Bamboo for Structural Applications ⇑ Bhavna Sharma , Ana Gatóo, Maximilian Bock, Michael Ramage
Construction and Building Materials 81 (2015) 66–73 Contents lists available at ScienceDirect Construction and Building Materials journal homepage: www.elsevier.com/locate/conbuildmat Engineered bamboo for structural applications ⇑ Bhavna Sharma , Ana Gatóo, Maximilian Bock, Michael Ramage Department of Architecture, University of Cambridge, Cambridge, UK highlights Relevance of engineered bamboo products to construction and industry. Mechanical characterisation of bamboo scrimber and laminated bamboo is presented. Bamboo scrimber is shown to have similar strength to laminated bamboo. Engineered bamboo products have properties that are equal to or surpass that of timber. article info abstract Article history: Bamboo is a rapidly renewable material that has many applications in construction. Engineered bamboo Received 24 September 2014 products result from processing the raw bamboo culm into a laminated composite, similar to glue- Received in revised form 27 January 2015 laminated timber products. These products allow the material to be used in standardised sections and Accepted 29 January 2015 have less inherent variability than the natural material. The present work investigates the mechanical Available online 23 February 2015 properties of two types of commercially available products – bamboo scrimber and laminated bamboo sheets – and compares these to timber and engineered timber products. It is shown that engineered bam- Keywords: boo products have properties that are comparable to or surpass that of timber and timber-based products. Bamboo scrimber Potential limitations to use in structural design are also discussed. The study contributes to a growing Engineered composites Laminated bamboo body of research on engineered bamboo and presents areas in which further investigation is needed. Construction Ó 2015 The Authors. -
Engineered Strand Uniclic Floating Installation
Engineered Strand Uniclic Floating Installation Introduction Thank you for choosing our Engineered Strand Bamboo Flooring! You have selected one of the highest quality engineered floors available. Our engineered flooring is a combination of the best natural materials and state-of the- art manufacturing technology. It features multiple layers of wood bonded together with an E1 emission (formaldehyde) compliant adhesive that exceeds all current emission standards and is cross-ply laminated to provide better stability with regard to expansion/ contraction. Our proprietary finish system utilizing acrylated urethane finish with aluminum oxide consists of 13 layers to provide one of the most durable finishes available. Combine this with the Uniclic® Installation System and you have one of the most durable and easy to install floors available! Please carefully read the following in order to ensure that you know what to expect, and so that you can enjoy your bamboo floor for many years to come. Please keep in mind that all hardwood flooring will scratch, dent, and change color over time. Therefore, you will need to decide if hardwood is suitable for your home or lifestyle. Because hardwood is a product of nature, you may experience shading variations. There will be shading variations within the cartons, and when installing, you should work out of several cartons, and mix them in a natural random shading pattern that is pleasing to your eye. If you find very dark or very light boards in the carton, that are not consistent with the other flooring, put them aside. These should be used in areas like closets or other areas that are not readily visible.