Raisbeck ZR LITE Performance System for the Learjet 35/36
Total Page:16
File Type:pdf, Size:1020Kb
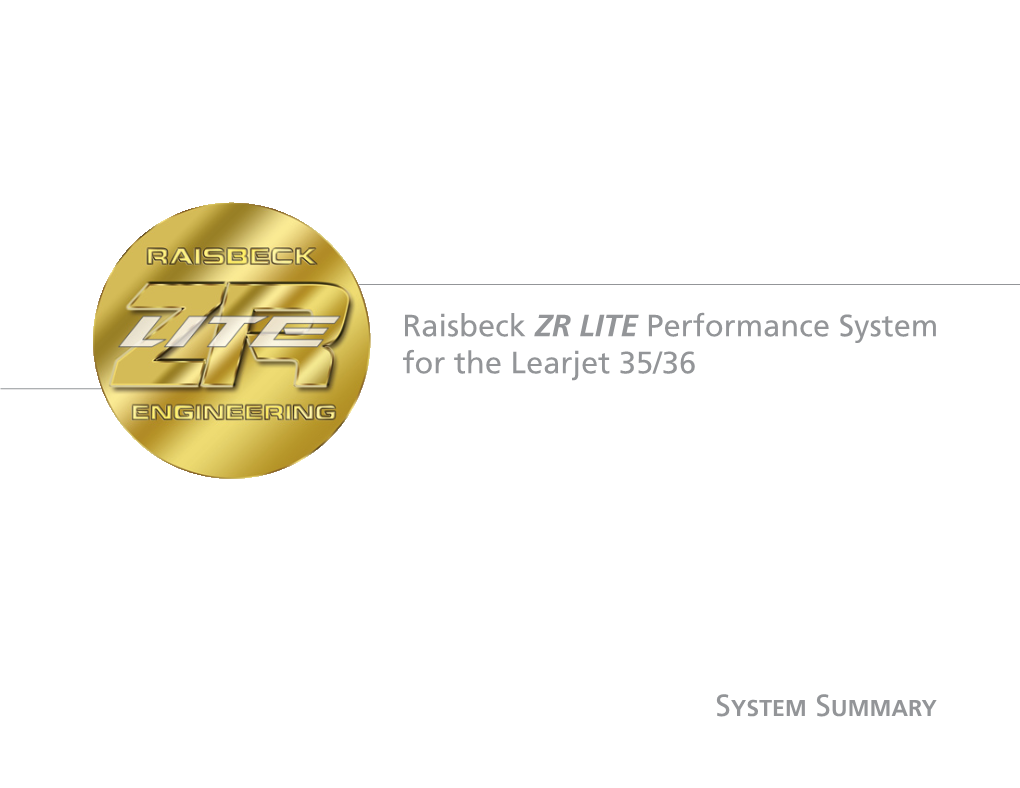
Load more
Recommended publications
-
CESSNA WING TIPS - EMPENNAGE TIPS CESSNA WING TIPS These Wing Tip Kits Consist of a Left and Right Hand Drooped Fiberglass Wing Tip
CESSNA WING TIPS - EMPENNAGE TIPS CESSNA WING TIPS These wing tip kits consist of a left and right hand drooped fiberglass wing tip. These wing tips are better than those manufactured by Cessna because they are made of fiberglass rather than a royalite type material, that bends and CM cracks after a short time on the aircraft. The superior epoxy rather than polyester fiberglass is used. Epoxy fiberglass has major advantages over a royalite type material; It is approximately six timesstronger and twelve times stiffer, it resists ultraviolet light and weathers better, and it keeps its chemical composition intact much longer. With all these advantages, they will probably be the last wingtips that will ever have to be installed on the aircraft. Should these wing tips be damaged through some unforeseen circumstances, they are easily repairable due to their fiberglass construc- tion. These kits are FAA STC’d and manufactured under a FAA PMA authority. The STC allows you to install these WP modern drooped wing tips, even if your aircraft was not originally manufactured with this newer, more aerodynamically efficient wingtip. *Does not include the Plate lens. Plate lens must be purchased separately. **Kits includes the left hand wing tip, right hand wing tip, hardware, and the plate lens Cessna Models Kit No.** Price Per Kit All 150, A150, 152, A152, 170A & B, P172, 175, 205 &L19, 172, 180, 185 for model year up through 1972.182, 206 for 05-01526 . model year up through 1971, 207 from 1970 and up (219-100) ME 05-01545 172, R172K(172XP), 172RG, 180, 185 for model year 1973 and up, 182, 206 for model year 1972 and up. -
Aircraft Winglet Design
DEGREE PROJECT IN VEHICLE ENGINEERING, SECOND CYCLE, 15 CREDITS STOCKHOLM, SWEDEN 2020 Aircraft Winglet Design Increasing the aerodynamic efficiency of a wing HANLIN GONGZHANG ERIC AXTELIUS KTH ROYAL INSTITUTE OF TECHNOLOGY SCHOOL OF ENGINEERING SCIENCES 1 Abstract Aerodynamic drag can be decreased with respect to a wing’s geometry, and wingtip devices, so called winglets, play a vital role in wing design. The focus has been laid on studying the lift and drag forces generated by merging various winglet designs with a constrained aircraft wing. By using computational fluid dynamic (CFD) simulations alongside wind tunnel testing of scaled down 3D-printed models, one can evaluate such forces and determine each respective winglet’s contribution to the total lift and drag forces of the wing. At last, the efficiency of the wing was furtherly determined by evaluating its lift-to-drag ratios with the obtained lift and drag forces. The result from this study showed that the overall efficiency of the wing varied depending on the winglet design, with some designs noticeable more efficient than others according to the CFD-simulations. The shark fin-alike winglet was overall the most efficient design, followed shortly by the famous blended design found in many mid-sized airliners. The worst performing designs were surprisingly the fenced and spiroid designs, which had efficiencies on par with the wing without winglet. 2 Content Abstract 2 Introduction 4 Background 4 1.2 Purpose and structure of the thesis 4 1.3 Literature review 4 Method 9 2.1 Modelling -
Wing Tip.Qxd
WINGTIP COUPLING AT 15,000 FEET Dangerous Experiments by C.E. “Bud” Anderson ingtip coupling evolved from an invention by Dr. Richard Vogt, a German scientist who emigrated to W the U.S. after WW II. The basic con- cept involved increasing an aircraft’s range by attaching two “free-floating,” fuel-carrying aerodynamic panels to the wingtips. This could be accomplished without undue struc- tural weight penalties as long as the panels were free to articulate and support themselves with their own aerodynamic lift. The panels would increase the basic wing configuration’s aspect ratio and would therefore significantly reduce induced drag; the “free” extra fuel car- ried by this more efficient wing would consid- erably increase an aircraft’s range. Soon, other logical uses of this unusual concept became apparent: for example, two escort fighters might be carried along “free” on a large bomber without sacrificing its range. To be feasible, the wingtip extensions, But there was also the problem of how such fuel-carrying extensions could be handled on the ground. How would they be supported without airflow to or panels, whatever they were, would have to hold them up?—perhaps by the use of a retractable outrigger landing gear, but what about runway width requirements? And—the big question—what about be kept properly aligned, preferably by a sim- the stability and control problems that might be induced by such a configura- ple and automatic flight-control system. tion; would the extensions be easy to control? Many questions are also immedi- 64 FLIGHT JOURNAL The second wingtip-coupling experiment involved an ETB-29A and two EF-84Bs (photo courtesy of Peter M. -
Fast 49 Airbus Technical Magazine Worthiness Fast 49 January 2012 4049July 2007
JANUARY 2012 FLIGHT AIRWORTHINESS SUPPORT 49 TECHNOLOGY FAST AIRBUS TECHNICAL MAGAZINE FAST 49 FAST JANUARY 2012 4049JULY 2007 FLIGHT AIRWORTHINESS SUPPORT TECHNOLOGY Customer Services Events Spare part commonality Ensuring A320neo series commonality 2 with the existing A320 Family AIRBUS TECHNICAL MAGAZINE Andrew James MASON Publisher: Bruno PIQUET Graham JACKSON Editor: Lucas BLUMENFELD Page layout: Quat’coul Biomimicry Cover: Radio Altimeters When aircraft designers learn from nature 8 Picture from Hervé GOUSSE ExM Company Denis DARRACQ Authorization for reprint of FAST Magazine articles should be requested from the editor at the FAST Magazine e-mail address given below Radio Altimeter systems Customer Services Communications 15 Tel: +33 (0)5 61 93 43 88 Correct maintenance practices Fax: +33 (0)5 61 93 47 73 Sandra PREVOT e-mail: [email protected] Printer: Amadio Ian GOODWIN FAST Magazine may be read on Internet http://www.airbus.com/support/publications ELISE Consulting Services under ‘Quick references’ ILS advanced simulation technology 23 ISSN 1293-5476 Laurent EVAIN © AIRBUS S.A.S. 2012. AN EADS COMPANY Jean-Paul GENOTTIN All rights reserved. Proprietary document Bruno GUTIERRES By taking delivery of this Magazine (hereafter “Magazine”), you accept on behalf of your company to comply with the following. No other property rights are granted by the delivery of this Magazine than the right to read it, for the sole purpose of information. The ‘Clean Sky’ initiative This Magazine, its content, illustrations and photos shall not be modified nor Setting the tone 30 reproduced without prior written consent of Airbus S.A.S. This Magazine and the materials it contains shall not, in whole or in part, be sold, rented, or licensed to any Axel KREIN third party subject to payment or not. -
Commercial Aircraft Performance Improvement Using Winglets
Nikola N. Gavrilović Commercial Aircraft Performance Graduate Research Assistant Improvement Using Winglets University of Belgrade Faculty of Mechanical Engineering Aerodynamic drag force breakdown of a typical transport aircraft shows Boško P. Rašuo that lift-induced drag can amount to as much as 40% of total drag at Full Professor cruise conditions and 80-90% of the total drag in take-off configuration. University of Belgrade Faculty of Mechanical Engineering One way of reducing lift-induced drag is by using wing-tip devices. By applying several types of winglets, which are already used on commercial George S. Dulikravich airplanes, we study their influence on aircraft performance. Numerical Full Professor investigation of five configurations of winglets is described and Florida International University preliminary indications of their aerodynamic performance are provided. Department of Mechanical and Materials Engineering, Miami, Florida, USA Moreover, using advanced multi-objective design optimization software an optimal one-parameter winglet configuration was detrmined that Vladimir Parezanović simultaneously minimizes drag and maximizes lift. Researcher Institute PPRIME, CNRS UPR3346 Poitiers, France Keywords: Winglet, Bionics, Computational fluid dynamics, Drag reduction, Lift-induced drag, Optimization 1. INTRODUCTION of soaring birds and their use of tip feathers to control flight, continued on the quest to reduce induced drag The main motivation for using wingtip devices is and improve aircraft performance and further develop reduction of lift-induced drag force. Environmental the concept of winglets in the late 1970s [4]. This issues and rising operational costs have forced industry research provided a fundamental knowledge and design to improve efficiency of commercial air transport and approach required for extremely attractive option to this has led to some innovative developments for improve aerodynamic efficiency of civilian aircraft, reducing lift-induced drag. -
Chapter 12 Design of Control Surfaces
Aileron Design Chapter 12 Design of Control Surfaces From: Aircraft Design: A Systems Engineering Approach Mohammad Sadraey 792 pages September 2012, Hardcover Wiley Publications 12.4.1. Introduction The primary function of an aileron is the lateral (i.e. roll) control of an aircraft; however, it also affects the directional control. Due to this reason, the aileron and the rudder are usually designed concurrently. Lateral control is governed primarily through a roll rate (P). Aileron is structurally part of the wing, and has two pieces; each located on the trailing edge of the outer portion of the wing left and right sections. Both ailerons are often used symmetrically, hence their geometries are identical. Aileron effectiveness is a measure of how good the deflected aileron is producing the desired rolling moment. The generated rolling moment is a function of aileron size, aileron deflection, and its distance from the aircraft fuselage centerline. Unlike rudder and elevator which are displacement control, the aileron is a rate control. Any change in the aileron geometry or deflection will change the roll rate; which subsequently varies constantly the roll angle. The deflection of any control surface including the aileron involves a hinge moment. The hinge moments are the aerodynamic moments that must be overcome to deflect the control surfaces. The hinge moment governs the magnitude of augmented pilot force required to move the corresponding actuator to deflect the control surface. To minimize the size and thus the cost of the actuation system, the ailerons should be designed so that the control forces are as low as possible. -
Theoretical Aspects and Practical Us Age of Hoerner Wing Tip
THEORETICAL ASPECTS AND PRACTICAL US AGE OF HOERNER WING TIP AN EFFICIENT WING TIP-WHAT'S NEEDED? Dr. Hoerner showed that the efficiency of a wing tip depends on six critical areas. His findings were: 1. The tip must be as thin as possible but still maintain a round leading edge. 2. A blending of wing top and bottom surfaces along a straight line. 3. The edge formed at this blend to be as thin as possible. 4. Obtain a sharp trailing edge leading to a corner, this corner to be in a straight a line as possible with the entire wing trailing edge. 5. The top of the tip to remain in a level plane with the top of the wing. 6. The bottom plane to be brought up in a convex curve. The primary reasons for this design are as follows: A square wing tip gives the greatest wing area for the least span. A smoothly finished, thin, leading edge provides for the best possible airflow over the tip. The convex underside accelerates the speed of the air passing under the tip to a velocity more equal to that of the air flowing over the top of the tip, thereby creating streamline flow. This flow reduces turbulence, which markedly decreases the size and intensity of tip vortices. By having a deep, straight trailing edge we are moving the point at which the vortex begins away from and behind the main surface of the wing, which means less drag and better control. By keeping the outermost point of the wing in a level plane with the wing top surface, we effectively increase wing dihedral angles. -
A Look Back at Flying Wings Part 1
NORTHROP FLYING WING S - P A R T 1 AVION MODEL 1, N - 1 M & N - 9M EDITED BY:TONY R. LANDIS WRITER/ARCHIVIST, HQ AFMC HISTORY OFFICE DISTRIBUTION STATEMENT A: APPROVED FOR PUBLIC RELEASE NORTHROP FLYING WING S - P A R T 1 Northrop’s latest aircraft, the B-21A Raider is the culmination of John K. Northrop’s dream of all wing design whose evolution stretches back to 1929. This is the first in a series of articles that will take a look back to the early days of aviation to show the birth of John Northrop’s dream. The Avion (Northrop) Model 1, commonly known as the 1929 Flying Wing, was the first rudimentary attempt at an all-wing vehicle, though it retained a simple boom- mounted tail assembly for added stability. Breaking away from the standard protocol of using wood for the structural assembly, Northrop chose 24S Alclad aluminum for the Model-1. Powered by a 90 HP 4 cylinder, inline, inverted Cirrus engine center- mounted inside the fuselage in a pusher (rear mounted) arrangement, the Avion Model 1 made its first flight at Mines Field, California on July 30, 1929 when test pilot Eddie Bellande performed two short hops during high speed taxi runs. Shortly there- after the aircraft was trucked to Muroc Dry Lake in California’s Mojave Desert. The vast expanse of the dry lake gave the small test team plenty of room to test their new design. The first ‘official’ flight of the Model-1 came on September 26th at Muroc. Bel- lande performed two brief flights totaling 5 minutes on the 26th and three days later made its final Muroc flight during a 5 minute test hop around the lakebed before operations moved to United Air Terminal in Burbank where flight operations continued on November 18th. -
Calculation and Identification of the Aerodynamic Parameters for Small
sensors Article Calculation and Identification of the Aerodynamic Parameters for Small-Scaled Fixed-Wing UAVs Jieliang Shen 1, Yan Su 1,*, Qing Liang 2 and Xinhua Zhu 1,* 1 School of Mechanical Engineering, Nanjing University of Science and Technology, Nanjing 210094, China; [email protected] 2 School of Computer Technologies and Control, ITMO University, St. Petersburg 197101, Russia; [email protected] * Correspondence: [email protected] (Y.S.); [email protected] (X.Z.) Received: 9 October 2017; Accepted: 11 January 2018; Published: 13 January 2018 Abstract: The establishment of the Aircraft Dynamic Model (ADM) constitutes the prerequisite for the design of the navigation and control system, but the aerodynamic parameters in the model could not be readily obtained especially for small-scaled fixed-wing UAVs. In this paper, the procedure of computing the aerodynamic parameters is developed. All the longitudinal and lateral aerodynamic derivatives are firstly calculated through semi-empirical method based on the aerodynamics, rather than the wind tunnel tests or fluid dynamics software analysis. Secondly, the residuals of each derivative are proposed to be identified or estimated further via Extended Kalman Filter (EKF), with the observations of the attitude and velocity from the airborne integrated navigation system. Meanwhile, the observability of the targeted parameters is analyzed and strengthened through multiple maneuvers. Based on a small-scaled fixed-wing aircraft driven by propeller, the airborne sensors are chosen and the model of the actuators are constructed. Then, real flight tests are implemented to verify the calculation and identification process. Test results tell the rationality of the semi-empirical method and show the improvement of accuracy of ADM after the compensation of the parameters. -
NCAR-TN/EDD-74 the Measurement of Air Velocity and Temperature
NCAR-TN/EDD-74 /-o /2 The Measurement of Air Velocity and Temperature Using the NCAR Buffalo Aircraft Measuring Systemi , -L/ D. H. LENSCHOW , /' June 1972 NATIONAL CENTER FOR ATMOSPHERIC RESEARCH /4ol /AJ Boulder, Colorado iii PREFACE Several years ago it was recognized that the development of iner- tial navigation systems for aircraft would make possible more accurate measurements of air velocity than were previously possible. Combining this improvement in measurement capability with the mobility of air- craft results in a very powerful tool for investigating a variety of atmospheric problems--from measurements of eddy fluxes of heat, mois- ture, and momentum within a few tens of meters of the earth's surface to measurements of lee wave structure several kilometers above the surface. The development of the measuring system on NCAR's Buffalo aircraft is a joint effort of NCAR and the Desert Research Institute (DRI), Reno, Nevada. At NCAR, both the Research Aviation Facility and the Laboratory of Atmospheric Science have contributed to its development. DRI's par- ticipation is under the direction of J. Telford. This report does not discuss measurements from all the sensors on the aircraft. Other sensors include a microwave refractometer (from which humidity fluctuations can be obtained), a dew-point hygrometer, an electrochemical ozone sensor, and a variometer (rate-of-climb sensor). Furthermore, the measurements and methods of measurements discussed here are not to be considered complete or absolute. Not only do the sensors change as new and better ways of measuring become available, but in- flight comparisons with other aircraft and with ground-based sensors and wind tunnel and laboratory tests will continue to shed new light on pres- ent methods for making airborne measurements. -
Aerodynamic Interference of Wingtip and Wing Devices on Bwb Model
AERODYNAMIC INTERFERENCE OF WINGTIP AND WING DEVICES ON BWB MODEL H. D. Ceron-Muñoz∗ , D. O. Diaz-Izquierdo∗, J. Solarte-Pineda∗ , F. M. Catalano∗ ∗Aerodynamic Laboratory, São Carlos Engineering School-University of São Paulo-Brazil Keywords: Blended Wing Body, fence device, gurney flap, winglet, c-wing Abstract that generate lower operating costs, lower eco- logical climatic and acoustic impacts [2]. Fur- This work presents a computational analysis of thermore, different studies have showed that non- the behavior of different devices coupled on a conventional configurations, as BWB [3, 4] or non-conventional configuration model called the Box wing [5, 6] could have aerodynamic effi- Blended Wing Body (BWB). Two wingtip de- ciency than a conventional aircraft. vices (winglet and C-wing) and two wing de- Technological advances and new materials vices (fence and gurney flap) were analyzed in have made viable the possibility of implementing order to recognize both their properties and their and operating this sort of aircraft for civil trans- interference on the pattern of the fluid over the port in the near future. Being so, the different model. During the evolution of aircraft many de- areas of aeronautical engineering are committed vices have been studied and implemented in con- to developing and optimizing of the BWB con- ventional airplanes. These devices have several figuration. advantages, such as improving aerodynamic effi- On the other hand, the noise emission has ciency and reducing induced drag, which in turn been reduced more than 20 dB for current jet air- produce positive effects on aircraft performance. craft, through the implementation of the turbo- On the other hand, the BWB could offer better fan engine with high by pass ratio [7], there have aerodynamic characteristics than a conventional been no important reductions in noise emission aircraft. -
Numerical Analysis and Optimization of Wing-Tip Designs
Numerical Analysis and Optimization of Wing-tip Designs A project present to The Faculty of the Department of Aerospace Engineering San Jose State University in partial fulfillment of the requirements for the degree Master of Science in Aerospace Engineering By Uran Kim May 2015 approved by Dr. Nikos Mourtos Faculty Advisor © 2015 Uram Kim ALL RIGHTS RESERVED Numerical Analysis and Optimization of Wing-tip Designs by Uram Kim APPROVED FOR THE DEPARTMENT OF AEROSPACE ENGINEERING SAN JOSE SATE UNIVERSITY May 2015 Dt. Nikos l. Mourtos, Project Advisor Depodment of Aerospoce Engineeing ABSTRACT NUMERICAL ANALYSIS AND OPTIMIZATION OF WING-TIP DESIGNS By Uram Kim Vortex lattice method is used to optimize a winglet design for retrofitting a Boeing 747- 100 wing. Parametric study involved 108 configurations corresponding to three different winglet airfoils, 6 winglet dihedral angles ranging from 7 to 90, and 6 toe-out angles ranging from 0 to - 5. The optimized design features a Whitcomb winglet airfoil, 45° dihedral, and 0° toe-out, and is capable of reducing the induced drag by 12.5% in inviscid studies. Vortex lattice method, due to its limitations, is found to be incapable of capturing the toe-out effects of the winglets. Compressible flow dynamics simulation in ESI is used to validate the optimized winglet design’s effectiveness, but the lack of good understanding of turbulence modeling lead to the inability to converge a turbulence simulation to a good solution. The output of the CFD simulations do not support the performance of the winglet, but qualitative plots help to explain the physics of the flow past a wing and winglet.