N-Propyl Bromide)
Total Page:16
File Type:pdf, Size:1020Kb
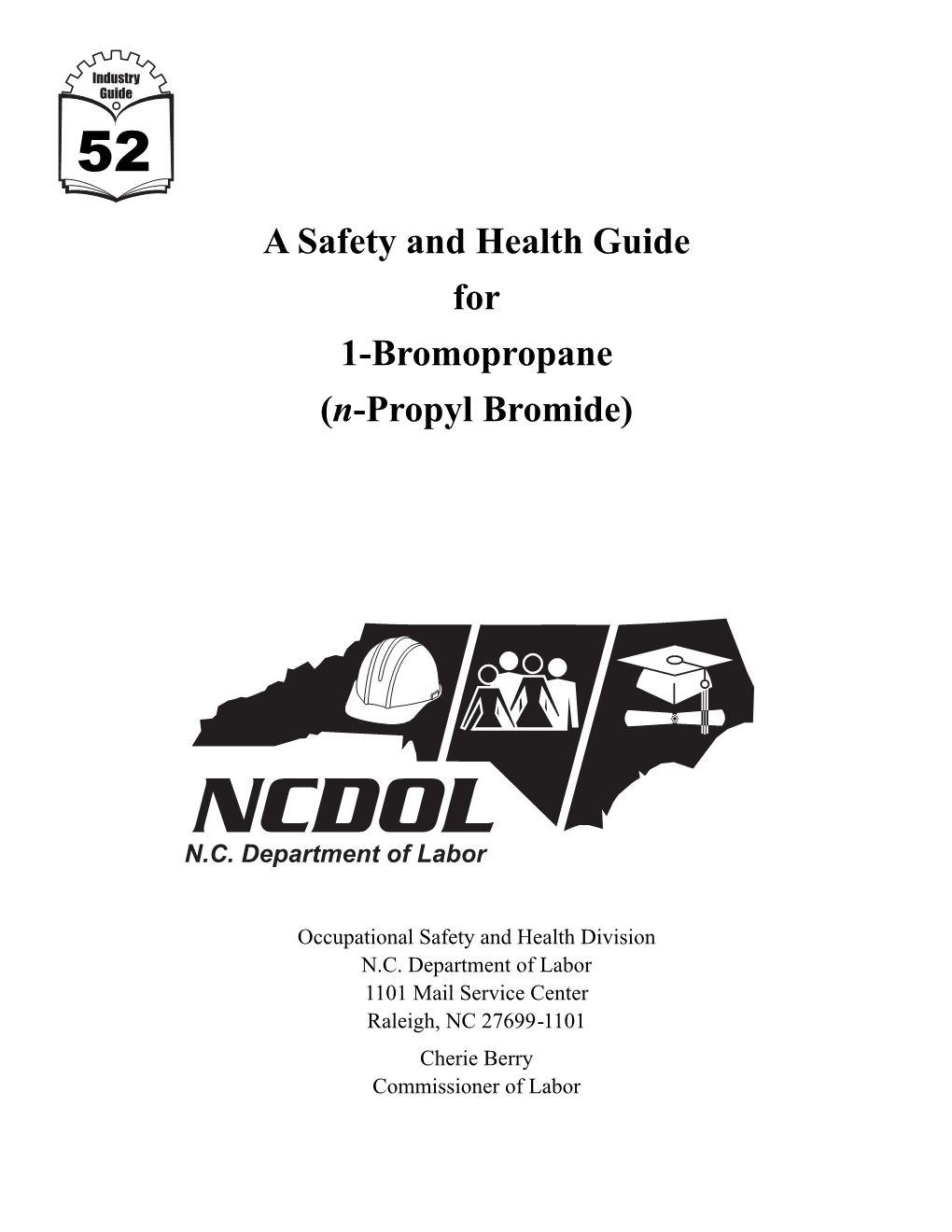
Load more
Recommended publications
-
Product Stewardship Summary Hydrobromic Acid
1801 U.S. Highway 52 West West Lafayette, IN 47906 +1-765-497-6100 +1-800-428-7947 Product Stewardship Summary Hydrobromic Acid Hydrobromic acid is a versatile chemical that is used by a number of different industries. Among its many uses, hydrobromic acid is utilized as a flux material in soldering materials, as an activator to make certain plastics, and as a chemical intermediate. It is also a raw material for the manufacture of oil field salts, useful in food safety applications, and a reactant in the manufacture of pharmaceuticals. Hydrobromic acid is a liquid made by dissolving hydrogen bromide gas in water. Because the hydrogen bromide used to make hydrobromic acid is a pressurized gas, it has different hazards than this product and has its own Product Stewardship Summary. (For more information see the Product Stewardship Summary for Anhydrous Hydrogen Bromide). Hydrobromic acid offered by Great Lakes Solutions can be produced in various concentrations, but the most common contains 48% hydrogen bromide in water. It is a clear, near water-white to yellow colored liquid with a characteristic acrid odor. Chemical Identity: Hydrobromic acid is identified by several names, all of them referring to the same chemical product. These names include: • HBr (commonly 48% HBr) • CAS Number [10035-10-6] • Aqueous hydrogen bromide, aqHBr • Hydrogen bromide aqueous solution • Example: Hydrogen bromide, 48%; • Hydrobromic acid Production: The gaseous hydrogen bromide used to make hydrobromic acid is derived from either the burning of bromine and hydrogen in a specially designed furnace or as an off-gas from a bromination reaction where it is a co-product. -
Chemical Name Federal P Code CAS Registry Number Acutely
Acutely / Extremely Hazardous Waste List Federal P CAS Registry Acutely / Extremely Chemical Name Code Number Hazardous 4,7-Methano-1H-indene, 1,4,5,6,7,8,8-heptachloro-3a,4,7,7a-tetrahydro- P059 76-44-8 Acutely Hazardous 6,9-Methano-2,4,3-benzodioxathiepin, 6,7,8,9,10,10- hexachloro-1,5,5a,6,9,9a-hexahydro-, 3-oxide P050 115-29-7 Acutely Hazardous Methanimidamide, N,N-dimethyl-N'-[2-methyl-4-[[(methylamino)carbonyl]oxy]phenyl]- P197 17702-57-7 Acutely Hazardous 1-(o-Chlorophenyl)thiourea P026 5344-82-1 Acutely Hazardous 1-(o-Chlorophenyl)thiourea 5344-82-1 Extremely Hazardous 1,1,1-Trichloro-2, -bis(p-methoxyphenyl)ethane Extremely Hazardous 1,1a,2,2,3,3a,4,5,5,5a,5b,6-Dodecachlorooctahydro-1,3,4-metheno-1H-cyclobuta (cd) pentalene, Dechlorane Extremely Hazardous 1,1a,3,3a,4,5,5,5a,5b,6-Decachloro--octahydro-1,2,4-metheno-2H-cyclobuta (cd) pentalen-2- one, chlorecone Extremely Hazardous 1,1-Dimethylhydrazine 57-14-7 Extremely Hazardous 1,2,3,4,10,10-Hexachloro-6,7-epoxy-1,4,4,4a,5,6,7,8,8a-octahydro-1,4-endo-endo-5,8- dimethanonaph-thalene Extremely Hazardous 1,2,3-Propanetriol, trinitrate P081 55-63-0 Acutely Hazardous 1,2,3-Propanetriol, trinitrate 55-63-0 Extremely Hazardous 1,2,4,5,6,7,8,8-Octachloro-4,7-methano-3a,4,7,7a-tetra- hydro- indane Extremely Hazardous 1,2-Benzenediol, 4-[1-hydroxy-2-(methylamino)ethyl]- 51-43-4 Extremely Hazardous 1,2-Benzenediol, 4-[1-hydroxy-2-(methylamino)ethyl]-, P042 51-43-4 Acutely Hazardous 1,2-Dibromo-3-chloropropane 96-12-8 Extremely Hazardous 1,2-Propylenimine P067 75-55-8 Acutely Hazardous 1,2-Propylenimine 75-55-8 Extremely Hazardous 1,3,4,5,6,7,8,8-Octachloro-1,3,3a,4,7,7a-hexahydro-4,7-methanoisobenzofuran Extremely Hazardous 1,3-Dithiolane-2-carboxaldehyde, 2,4-dimethyl-, O- [(methylamino)-carbonyl]oxime 26419-73-8 Extremely Hazardous 1,3-Dithiolane-2-carboxaldehyde, 2,4-dimethyl-, O- [(methylamino)-carbonyl]oxime. -
A Review of the Toxicity and Environmental Behaviour of Hydrogen Bromide In
w w w.environment-agency.gov.uk A Review of the Toxicity and Environmental Behaviour of Hydrogen Bromide in Air The Environment Agency is the leading public body protecting and improving the environment in England and Wales. It’s our job to make sure that air, land and water are looked after by everyone in today’s society, so that tomorrow’s generations inherit a cleaner, healthier world. Our work includes tackling flooding and pollution incidents, reducing industry’s impacts on the environment, cleaning up rivers, coastal waters and contaminated land, and improving wildlife habitats. This report is the result of research commissioned and funded by the Environment Agency’s Science Programme. Published by: Author(s): Environment Agency, Rio House, Waterside Drive, Aztec West, P Coleman, R Mascarenhas and P Rumsby Almondsbury, Bristol, BS32 4UD Tel: 01454 624400 Fax: 01454 624409 Dissemination Status: www.environment-agency.gov.uk Publicly available ISBN: 1844323552 Keywords: hydrogen bromide, inhalation toxicity, air quality, exposure, © Environment Agency January 2005 human health, air pollutant All rights reserved. This document may be reproduced with prior Research Contractor: permission of the Environment Agency. Netcen, Culham Science Centre, Culham, Abingdon, Oxfordshire, OX14 3ED The views expressed in this document are not necessarily WRc-NSF Ltd, Henley Road, Medmenham, Marlow, Bucks, those of the Environment Agency. SL7 2HD Tel: 0870 190 6437 Fax: 0870 190 6608 This report is printed on Cyclus Print, a 100% recycled stock, Website: www.netcen.co.uk. which is 100% post consumer waste and is totally chlorine free. Water used is treated and in most cases returned to source in Environment Agency’s Project Manager: better condition than removed. -
Acutely / Extremely Hazardous Waste List
Acutely / Extremely Hazardous Waste List Federal P CAS Registry Acutely / Extremely Chemical Name Code Number Hazardous 4,7-Methano-1H-indene, 1,4,5,6,7,8,8-heptachloro-3a,4,7,7a-tetrahydro- P059 76-44-8 Acutely Hazardous 6,9-Methano-2,4,3-benzodioxathiepin, 6,7,8,9,10,10- hexachloro-1,5,5a,6,9,9a-hexahydro-, 3-oxide P050 115-29-7 Acutely Hazardous Methanimidamide, N,N-dimethyl-N'-[2-methyl-4-[[(methylamino)carbonyl]oxy]phenyl]- P197 17702-57-7 Acutely Hazardous 1-(o-Chlorophenyl)thiourea P026 5344-82-1 Acutely Hazardous 1-(o-Chlorophenyl)thiourea 5344-82-1 Extemely Hazardous 1,1,1-Trichloro-2, -bis(p-methoxyphenyl)ethane Extemely Hazardous 1,1a,2,2,3,3a,4,5,5,5a,5b,6-Dodecachlorooctahydro-1,3,4-metheno-1H-cyclobuta (cd) pentalene, Dechlorane Extemely Hazardous 1,1a,3,3a,4,5,5,5a,5b,6-Decachloro--octahydro-1,2,4-metheno-2H-cyclobuta (cd) pentalen-2- one, chlorecone Extemely Hazardous 1,1-Dimethylhydrazine 57-14-7 Extemely Hazardous 1,2,3,4,10,10-Hexachloro-6,7-epoxy-1,4,4,4a,5,6,7,8,8a-octahydro-1,4-endo-endo-5,8- dimethanonaph-thalene Extemely Hazardous 1,2,3-Propanetriol, trinitrate P081 55-63-0 Acutely Hazardous 1,2,3-Propanetriol, trinitrate 55-63-0 Extemely Hazardous 1,2,4,5,6,7,8,8-Octachloro-4,7-methano-3a,4,7,7a-tetra- hydro- indane Extemely Hazardous 1,2-Benzenediol, 4-[1-hydroxy-2-(methylamino)ethyl]- 51-43-4 Extemely Hazardous 1,2-Benzenediol, 4-[1-hydroxy-2-(methylamino)ethyl]-, P042 51-43-4 Acutely Hazardous 1,2-Dibromo-3-chloropropane 96-12-8 Extemely Hazardous 1,2-Propylenimine P067 75-55-8 Acutely Hazardous 1,2-Propylenimine 75-55-8 Extemely Hazardous 1,3,4,5,6,7,8,8-Octachloro-1,3,3a,4,7,7a-hexahydro-4,7-methanoisobenzofuran Extemely Hazardous 1,3-Dithiolane-2-carboxaldehyde, 2,4-dimethyl-, O- [(methylamino)-carbonyl]oxime 26419-73-8 Extemely Hazardous 1,3-Dithiolane-2-carboxaldehyde, 2,4-dimethyl-, O- [(methylamino)-carbonyl]oxime. -
Hydrogen Bromide (CAS #10035-10-6) Information for the Public
Revised June 2005 Hydrogen Bromide (CAS #10035-10-6) Information for the Public What is hydrogen bromide? Hydrogen bromide is a colorless, or sometimes faint yellow, highly toxic gas with a sharp, irritating odor. It can also be found as a liquid, either as hydrobromic acid (hydrogen bromide dissolved in water) or as a compressed gas under pressure (anhydrous hydrogen bromide). It is an extremely dangerous substance and must be handled with caution as it can cause severe health effects and death. Hydrogen bromide can react violently when mixed with some chemicals, metals or water, forming a flammable, explosive gas. When hydrogen bromide is released into indoor air, dangerous levels will be reached very quickly. The gas is heavier than air and can travel to low- lying or confined areas. Containers of hydrogen bromide may explode when heated. How is hydrogen bromide used? Hydrogen bromide is used to make chemicals and drugs, as a solvent and as a veterinary drug. Before working with hydrogen bromide, employee training should be provided on proper safe handling and storage procedures. How can people be exposed to hydrogen bromide? Significant exposure usually occurs in the industries where hydrogen bromide is produced or used. Heating, pouring, spraying, spills and evaporation create conditions that increase the risk of employee exposure. Though unlikely, the general population may be exposed by breathing contaminated air or by drinking contaminated water from a facility using or storing hydrogen bromide, by skin or eye contact with the gas or liquid, or by eating food that has been contaminated with hydrogen bromide. -
United States Patent (19) 11 Patent Number: 6,063,749 Degroot (45) Date of Patent: May 16, 2000
US006063749A United States Patent (19) 11 Patent Number: 6,063,749 DeGroot (45) Date of Patent: May 16, 2000 54). STABILIZED ALKYL BROMIDE SOLVENTS 5,616,549 4/1997 Clark ....................................... 510/412 CONTAINING DALKYL CARBONATES 5,665,170 9/1997 Lee et al..... ... 134/19 5,665,172 9/1997 Oshima et al. ........................... 134/40 75 Inventor: Richard J. DeGroot, West Lafayette, FOREIGN PATENT DOCUMENTS O 609 004 A1 3/1994 European Pat. Off.. 73 Assignee: Great Lakes Chemical Corporation, 1952784 8/1970 Germany. West Lafayette, Ind. 1936987 2/1971 Germany. 53-127404 11/1978 Japan. 56-55322 5/1981 Japan. 21 Appl. No.: 09/112,958 1230312 4/1971 United Kingdom. Related U.S. ApplicationO O Data OTHER PUBLICATIONS 60 Provisional application No. 60/052,035, Jul. 9, 1997. 1230312 GB Archer et al. Apr. 28, 1971. 51) Int. Cl." ............................. C23G 5/028; C11D 7/30; Primary Examiner-Christine Skane C11D 7/50; B08B 3/08 Attorney, Agent, or Firm Woodard, Emhardt, Naughton 52 U.S. Cl. .............................. 510/412; 134/40; 134/42; Moriarty & McNett 252/364; 570/102 58 Field of Search ............................ 510/412; s 570/102; 57 ABSTRACT 134/42, 40; 252/364 This invention provides a stabilized alkyl bromide based Solvent System that is useful for cleaning and degreasing a 56) References Cited wide variety of metal objects. The solvent is stabilized with U.S. PATENT DOCUMENTS a stabilizer System that includes a dialkyl carbonate Such as dimethyl carbonate and optionally other Stabilizers and/or 3,730,904 5/1973 Clementson et al. ................... 252/171 acid Scavengers to inhibit the metal induced decomposition 4,018,837 4/1977 Archer et al. -
REACTION of BROMINE with FURFURAL and RELATED COMPOUNDS by Elizabeth E
U. S. DEPARTMENT OF COMMERCE NATIONAL BUREAU OF STANDARDS RESEARCH PAPER RP1276 Part of Journal of Research of the JXational Bureau of Standards, Volume 24, February 1940 REACTION OF BROMINE WITH FURFURAL AND RELATED COMPOUNDS By Elizabeth E. Hughes and S. F. Acree ABSTRACT The mechanism of the reaction of bromine in aqueous solution with furfural and with two related compounds is discussed. The bromine present and the acidity of the solutions were each determined after various periods of time at 0° C, to obtain a measure of the bromine con sumed, the amount of acid used in liberation of bromine, and the hydrobromic acid generated during the reaction. The product of the reaction of molar propor tions of bromine and furfural was precipitated with phenylhydrazine and analyzed. Its composition and the analytical data indicate that when molar proportions of bromine and furfural react, the bromine is changed to bromide ions, 2 equivalents of hydrogen ions are formed from the water, and 2 equivalents of hydroxyl ions or oxygen combine with the furfural. During a study of the quantitative determination of furfural with bromine, some phases of the mechanism of the reaction were also investigated. The determination depends upon the oAidation of furfural by bromine liberated from a solution of bromate and bromide. Work by Hill and Sanger [11/ Gilman and Wright [2], and others indicates that in some organic solvents bromine reacts with some furane derivatives by preliminary addition at a double bond, to form a dibromo compound (reactions I and II), which may then be made to lose hydrobromic acid and yield a bromofurane (reaction II). -
Experiment 7 Preparation of 1-Bromobutane
Experiment 7 Preparation of 1-Bromobutane In this experiment you will prepare 1-bromobutane (n-butyl bromide) from n-butanol (1-butanol) using a substitution reaction under acidic conditions. This is an SN2 reaction. The mechanism is shown in Figure 7.1. The purpose of the sulfuric acid is to first protonate the weakly basic hydroxyl group and thereby convert it into a good leaving group. It can then leave as neutral water. Figure 7.1 Preparation of 1-Bromobutane O H O CH3CH2CH2CH2 OH + H O S OH CH3CH2CH2CH2 O + O S OH 1-butanol O H O sulfuric acid H + - + + Na Br CH3CH2CH2CH2 O CH3CH2CH2CH2 Br + H2O + Na sodium bromide H 1-bromobutane There is a side reaction that occurs that we cannot prevent: this is the formation of HBr from the reaction of the sodium bromide, which is the source of the bromide nucleophile, and the sulfuric acid, which we need in order to protonate the OH group of the alcohol. As shown in Figure 7.2, a significant equilibrium concentration of HBr will form. HBr, like HCl, is a gas that is quite soluble in cold water, but not in hot water. Since you are going to bring the mixture to a boil, HBr will escape from the apparatus. Being a strong acid, this gas will cause damage to lungs when inhaled and will certainly sting your eyes. Your apparatus must be vented appropriately, directly into the air vent above your bench (see Figure 7.3 for the proper set-up). A section of glass tubing, bent to 90 °C, with rubber tubing attached, will be provided by the stockroom. -
24% Hbr Safety Info
24% Hydrogen Bromide Solutions Safety Guide and General Information CONFIDENTIAL Enviro Tech Chemical Services, Inc. Chemtura Corporation •Chemtura is one of the largest publicly traded specialty chemical companies in the United States and a leader in several global markets, providing products and services in 100+ countries with manufacturing worldwide. 2009 annual sales were $2.5 billion. •Chemtura, previously as Great Lakes Chemical, is a major global producer of bromine and brominated derivative chemicals like hydrobromic acid. Chemtura has been producing these chemicals in our South Arkansas facilities for over 50 years. CONFIDENTIAL Enviro Tech Chemical Services, Inc. Enviro Tech Chemical Services, Inc •Food Safety Specialty Products R & D •Supplier to the Industry for Specialty FDA and FSIS-approved chemistries such as HBr (hydrogen bromide) and PAA (peroxyacetic acid) •Hydrogen bromide patent filed with US Patent Office (for meat/poultry and water treatment) •Close Relationship with Chemtura and their mfg. and product support abilities. CONFIDENTIAL Enviro Tech Chemical Services, Inc. Facts About 24% Hydrogen Bromide Solutions •Have I used anything like 24% HBr? •A: Many household products like muriatic acid for cleaning cement, lime-scale removers, drain opening chemicals, toilet bowl cleaners, and pH adjustment chemicals for pools and spas have similar characteristics to 24% HBr. •Is HBr used in large quantities? •A: HBr is used in many applications like as a catalyst for PTA for polyester PET (beverage bottles) and is used in tens of thousands of tons at 2X the concentration (24% vs. 48%). It is also used as solder flux, as a chemical intermediate to make bromide chemicals, and to make other polymers. -
Acids, Bases, and Ph Calculations in Chemistry, Ph Is a Measure of the Acidity Or Basicity of an Aqueous Solution
ACIDS AND BASES Properties of acids 1. Acids have a sour taste. 2. Acids are corrosive. 3. Acids change the color of certain vegetable dyes, such as litmus, from blue to red. 4. Acids lose their acidity when they are combined with alkalies. The name "acid" comes from the Latin acidus, which means "sour," and refers to the sharp odor and sour taste of many acids. Examples: Vinegar tastes sour because it is a dilute solution of acetic acid in water. Lemon juice tastes sour because it contains citric acid. Milk turns sour when it spoils because lactic acid is formed, and the unpleasant, sour odor of rotten meat or butter can be attributed to compounds such as butyric acid that form when fa`t spoils. Acids, Bases, and pH Calculations In chemistry, pH is a measure of the acidity or basicity of an aqueous solution. Solutions with a pH less than 7 are said to be acidic and solutions with a pH greater than 7 are basic or alkaline. Pure water has a pH very close to 7. There are several ways to define acids and bases, but pH only refers to hydrogen ion concentration and is only meaningful when applied to aqueous (water-based) solutions. When water dissociates it yields a hydrogen ion and a hydroxide. + - H2O ↔ H + OH When calculating pH, remember that [] refers to molarity, M. + - -14 Kw = [H ][OH ] = 1x10 at 25°C for pure water [H+] = [OH-] = 1x10-7 Acidic Solution: [H+] > 1x10-7 Basic Solution: [H+] < 1x10-7 Calculate pH and [H+] + pH = - log10[H ] [H+] = 10-pH Example: Calculate the pH for a specific [H+].C4alculate pH given [H+]= 1.4 x 10-5 M + pH =- log10[H ] -5 pH = log10(1.4 x 10 ) pH = 4.85 Example: Calculate [H+] from a known pH. -
Potassium Bromide Safety Data Sheet According to Regulation (EC) 1272/2008 Issue Date: 03/01/21 Revision Date: 03/01/24
Potassium Bromide Safety Data Sheet According to Regulation (EC) 1272/2008 Issue Date: 03/01/21 Revision date: 03/01/24 SECTION 1 - Chemical Product and Company Identification 1.1 Product Identifiers Product Name : Potassium Bromide CAS # : 7758-02-3 EC# : 231-830-3 RTECS# : TS7650000 1.2 Recommended Use of the Chemical and Restrictions of Use Chemical manufacturing 1.3 Supplier Details BioSpectra Inc. 100 Majestic Way Supplier : Bangor, PA 18013 T: 610.599.3400 [email protected] 1.4 Emergency Numbers : US & Canada: 1-800-424-9300 Emergency Numbers : Outside the US & Canada: +1 703-527-3887 SECTION 2 – Hazard Identification 2.1 Classification of the Substance or Mixture GHS Classification in accordance with 29 CFR 1910 and Regulation (EC) No 1272/2008 (EU-GHS/CLP) Classified as a Hazardous Substance per GHS and EC1272/2008 2.2 GHS Label Element Including Precautionary Statements Hazard Pictogram(s): Warning Word : Warning H315 Causes Skin Irritation Hazard Statements : H319 Causes Serious Eye Irritation : H335 May Cause Respiratory Irritation Precautionary Statements : P261: Avoid breathing dust/fume/gas/mist/vapours/spray : P264: Wash thoroughly after handling : P271: Use only outdoors or in a well-ventilated area : P280 Wear Protective gloves/Eye Protection/Face Protection : P302 + P352: IF ON SKIN: Wash with plenty of soap and water : P304 + P340: IF INHALED: Remove victim to fresh air and keep at rest in a position comfortable for breathing : P305+P351+P338 IF IN EYES: Rinse cautiously with water for several minutes. Remove contact lenses, if present and easy to do. Continue Rinsing. : P312: Call a POISON CENTER or doctor/physician if you feel unwell : P332 + P313: If skin irritation occurs: Get medical attention : P337+P313 If eye irritation persists: Get medical advice/attention. -
Hydrobromic Acid
Safety data sheet according to Regulation (EC) No. 1907/2006 (REACH), amended by 2015/830/EU Hydrobromic acid ROTIPURAN®Ultra 48 % article number: HN67 date of compilation: 23.04.2018 Version: 2.0 en Revision: 26.08.2020 Replaces version of: 23.04.2018 Version: (1) SECTION 1: Identification of the substance/mixture and of the company/ undertaking 1.1 Product identifier Identification of the substance Hydrobromic acid ROTIPURAN®Ultra 48 % Article number HN67 Registration number (REACH) not relevant (mixture) Index No [ 035-002-01-8 ] EC number [ 233-113-0 ] CAS number [ 10035-10-6 ] 1.2 Relevant identified uses of the substance or mixture and uses advised against Identified uses: laboratory chemical laboratory and analytical use 1.3 Details of the supplier of the safety data sheet Carl Roth GmbH + Co KG Schoemperlenstr. 3-5 D-76185 Karlsruhe Germany Telephone: +49 (0) 721 - 56 06 0 Telefax: +49 (0) 721 - 56 06 149 e-mail: [email protected] Website: www.carlroth.de Competent person responsible for the safety data : Department Health, Safety and Environment sheet: e-mail (competent person): [email protected] 1.4 Emergency telephone number Emergency information service Poison Centre Munich: +49/(0)89 19240 SECTION 2: Hazards identification 2.1 Classification of the substance or mixture Classification according to Regulation (EC) No 1272/2008 (CLP) Classification acc. to GHS Section Hazard class Hazard class and cat- Hazard egory state- ment 2.16 substance or mixture corrosive to metals (Met. Corr. 1) H290 3.2 skin corrosion/irritation (Skin Corr. 1) H314 3.3 serious eye damage/eye irritation (Eye Dam.