Experimental Study of System Performance Improvements in Transcritical R744 Systems with Applications to Bottle Coolers
Total Page:16
File Type:pdf, Size:1020Kb
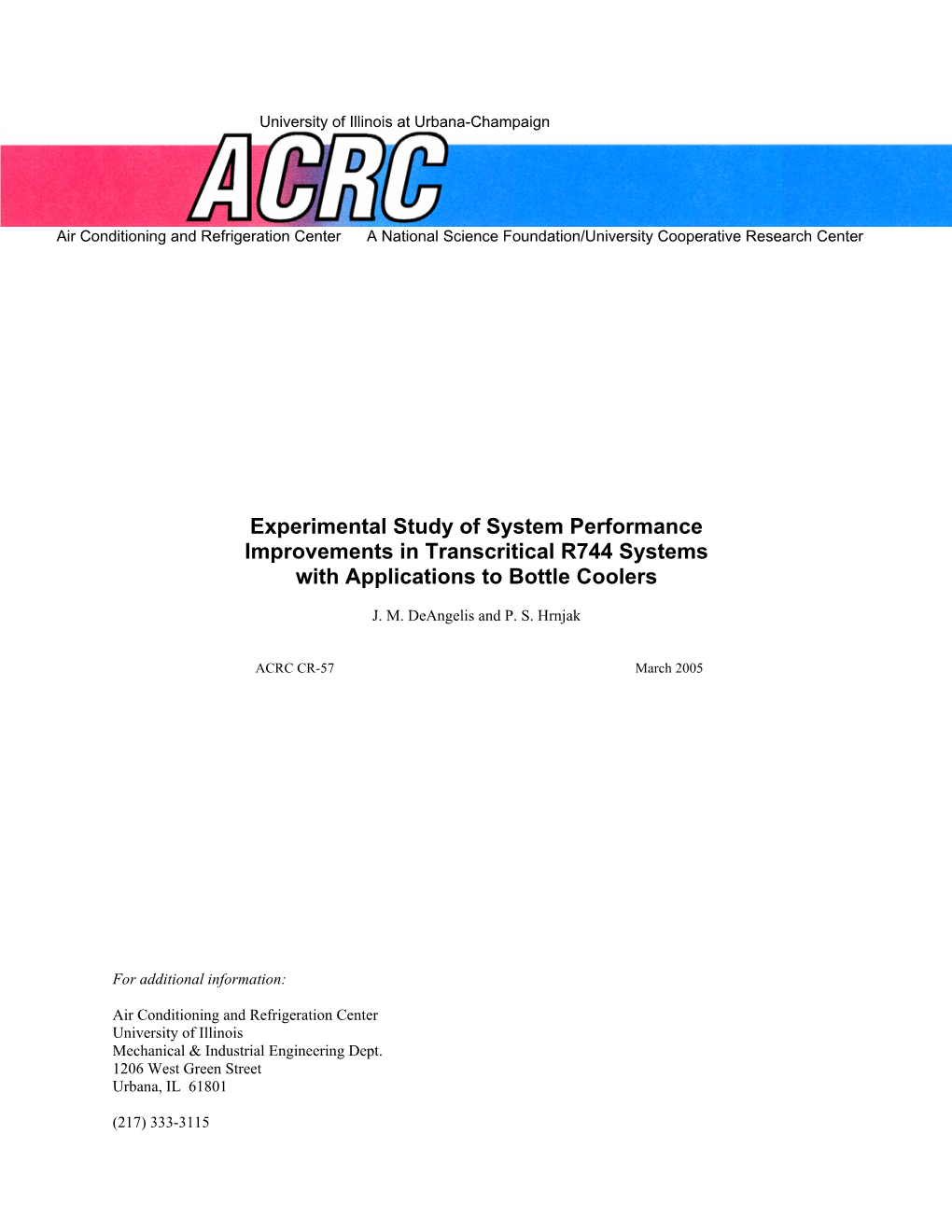
Load more
Recommended publications
-
Suitability of Polymer Heat Exchangers for Air Conditioning Applications
University of Illinois at Urbana-Champaign Air Conditioning and Refrigeration Center A National Science Foundation/University Cooperative Research Center Suitability of Polymer Heat Exchangers for Air Conditioning Applications T. Malik and C. W. Bullard ACRC TR-237 March 2005 For additional information: Air Conditioning and Refrigeration Center University of Illinois Mechanical & Industrial Engineering Dept. 1206 West Green Street Urbana, IL 61801 Prepared as part of ACRC Project #148 Exploring Component and System Design Tradeoffs (217) 333-3115 C. W. Bullard, Principal Investigator The Air Conditioning and Refrigeration Center was founded in 1988 with a grant from the estate of Richard W. Kritzer, the founder of Peerless of America Inc. A State of Illinois Technology Challenge Grant helped build the laboratory facilities. The ACRC receives continuing support from the Richard W. Kritzer Endowment and the National Science Foundation. The following organizations have also become sponsors of the Center. Arçelik A. S. Behr GmbH and Co. Carrier Corporation Cerro Flow Products, Inc. Copeland Corporation Daikin Industries, Ltd. Danfoss A/S Delphi Thermal and Interior Embraco S. A. Ford Motor Company Fujitsu General Limited General Motors Corporation Hill PHOENIX Hydro Aluminum Adrian, Inc. Ingersoll-Rand/Climate Control Lennox International, Inc. LG Electronics, Inc. Manitowoc Ice, Inc. Modine Manufacturing Co. Novelis Global Technology Centre Parker Hannifin Corporation Peerless of America, Inc. Samsung Electronics Co., Ltd. Sanden Corporation Sanyo Electric Co., Ltd. Tecumseh Products Company Trane Visteon Automotive Systems Wieland-Werke, AG Wolverine Tube, Inc. For additional information: Air Conditioning & Refrigeration Center Mechanical & Industrial Engineering Dept. University of Illinois 1206 West Green Street Urbana, IL 61801 217 333 3115 Abstract The project compares the non-metallic/polymer heat exchangers to the current technology in metallic heat exchangers. -
Applications and Control of Air Conditioning Systems Using Rapid Cycling to Modulate Capacity
University of Illinois at Urbana-Champaign Air Conditioning and Refrigeration Center A National Science Foundation/University Cooperative Research Center Applications and Control of Air Conditioning Systems Using Rapid Cycling to Modulate Capacity M. J. Poort and C. W. Bullard ACRC TR-238 May 2005 For additional information: Air Conditioning and Refrigeration Center University of Illinois Mechanical & Industrial Engineering Dept. 1206 West Green Street Prepared as part of ACRC Project #161 Urbana, IL 61801 Applications and Control of Systems Using Rapid-Cycling to Modulate Capacity (217) 333-3115 C. W. Bullard and P. S. Hrnjak, Principal Investigators The Air Conditioning and Refrigeration Center was founded in 1988 with a grant from the estate of Richard W. Kritzer, the founder of Peerless of America Inc. A State of Illinois Technology Challenge Grant helped build the laboratory facilities. The ACRC receives continuing support from the Richard W. Kritzer Endowment and the National Science Foundation. The following organizations have also become sponsors of the Center. Arçelik A. S. Behr GmbH and Co. Carrier Corporation Cerro Flow Products, Inc. Copeland Corporation Daikin Industries, Ltd. Danfoss A/S Delphi Thermal and Interior Embraco S. A. Ford Motor Company Fujitsu General Limited General Motors Corporation Hill PHOENIX Hydro Aluminum Adrian, Inc. Ingersoll-Rand/Climate Control Lennox International, Inc. LG Electronics, Inc. Manitowoc Ice, Inc. Modine Manufacturing Co. Novelis Global Technology Centre Parker Hannifin Corporation Peerless of America, Inc. Samsung Electronics Co., Ltd. Sanden Corporation Sanyo Electric Co., Ltd. Tecumseh Products Company Trane Visteon Automotive Systems Wieland-Werke, AG Wolverine Tube, Inc. For additional information: Air Conditioning & Refrigeration Center Mechanical & Industrial Engineering Dept. -
Japanese Automotive Supplier Investment Directory October 1991
Japanese Automotive Supplier Investment Directory October 1991 Fourth Edition Compiled by Brett C. Smith Report Number: UMTRI-91-37 The Office for the Study of Automotive Transportation The University of Michigan Transportation Research Institute 2901 Baxter Road Ann Arbor, MI 48109-2150 Phone: 313-764-5592 Fax: 313-936-1081 The overall objectives of the Office for the Study of Automotive Transportation (OSAT) are to provide information resources, industry analysis, comrnuni~:ation forums, and academic. research that meet the continually changing needs of the international automotive and automotive-related industries. (01991 OSAT, UMTRI) Japanese Automotive Supplier Investment Directory October 1991 Fourth Edition Compiled by Brett C. Smdth The Office for the Study of Automotive Transportation The University of Michigan Transportation Research Institute 2901 Baxter Road Ann Arbor, MI 48109-21!50 Phone: 313-764-5592 Fax: 313-936-1081 The overall objectives of the Office for the Study of Automotive Transportation (OSAT) are to provide information resources, industry analysis, communication forums, and academic research that meet the continually changing needs of the interniitional automotive and automotive-related industries. (01991 OSAT, UMTRI) OSAT AFFILIATES and SPONSORS Funds from the following organizations help to support OSAT activities, including this Directory. Aeroquip Corporation Allied-Signal Inc. 3M Automotive Industry Center Chevron Research Company Chrysler Corporation Donnelly Corporation Dow Corning Eaton Corporation Fel-Pro Inc. Ford Motor Company GE Automotive General Motors Corporation Johnson Controls, Inc. Mazda R. J. Tower Corporation Textron Inc. TRW Automotive Sealed Power Technologies Union Carbide Corporation UAW-GM Human Resource Center JAPANESE AUTOMOTIVE SUPPLIER INVESTMENT DIRECTORY Fourth Edition Table of Contents Introduction........................ -
Arti Refrigerant Database: Archival and Historical Citations
DOE/CE/23810-104 (JMC/ARTI-9909C - RDB9931) ARTI REFRIGERANT DATABASE: ARCHIVAL AND HISTORICAL CITATIONS September 1999 prepared by James M. Calm Engineering Consultant 10887 Woodleaf Lane Great Falls, VA 22066-3003 USA for the Air-Conditioning and Refrigeration Technology Institute 4301 North Fairfax Drive, Suite 425 Arlington, VA 22203 USA This report is one of a series for the Materials Compatibility and Lubricant Research (MCLR) Program, under ARTI contract number 671-50000 for grant number DE-FG02-91CE23810 from the U.S. Department of Energy. Page ii Please refer questions or comments on this document to: James M. Calm Engineering Consultant 10887 Woodleaf Lane Great Falls, VA 22066-3003 USA e-mail: [email protected] telephone: 703/450-4313 telefax: 707/516-0552 Glenn C. Hourahan Vice President Air-Conditioning and Refrigeration Technology Institute 4301 North Fairfax Drive, Suite 425 Arlington, VA 22203 USA e-mail: [email protected] telephone: 703/524-8800 telefax: 703/522-2349 Neither James M. Calm, the Air-Conditioning and Refrigeration Technology Institute (ARTI), nor any person acting on behalf of them: (a) makes any warranty, expressed or implied, with respect to the accuracy, completeness, or usefulness of any information, apparatus, material, method, or process disclosed in this document or that such use may not infringe privately owned rights; or (b) assumes any liabilities with respect to use of, or damages resulting from use of, any information, apparatus, material, method, or process disclosed in this document. Reference herein to any specific commercial product, process, or service by trade name, trademark, manufacturer, or otherwise, does not necessarily constitute or imply its endorse- ment, recommendation, or favoring.