Wooden Arrow Workshop
Total Page:16
File Type:pdf, Size:1020Kb
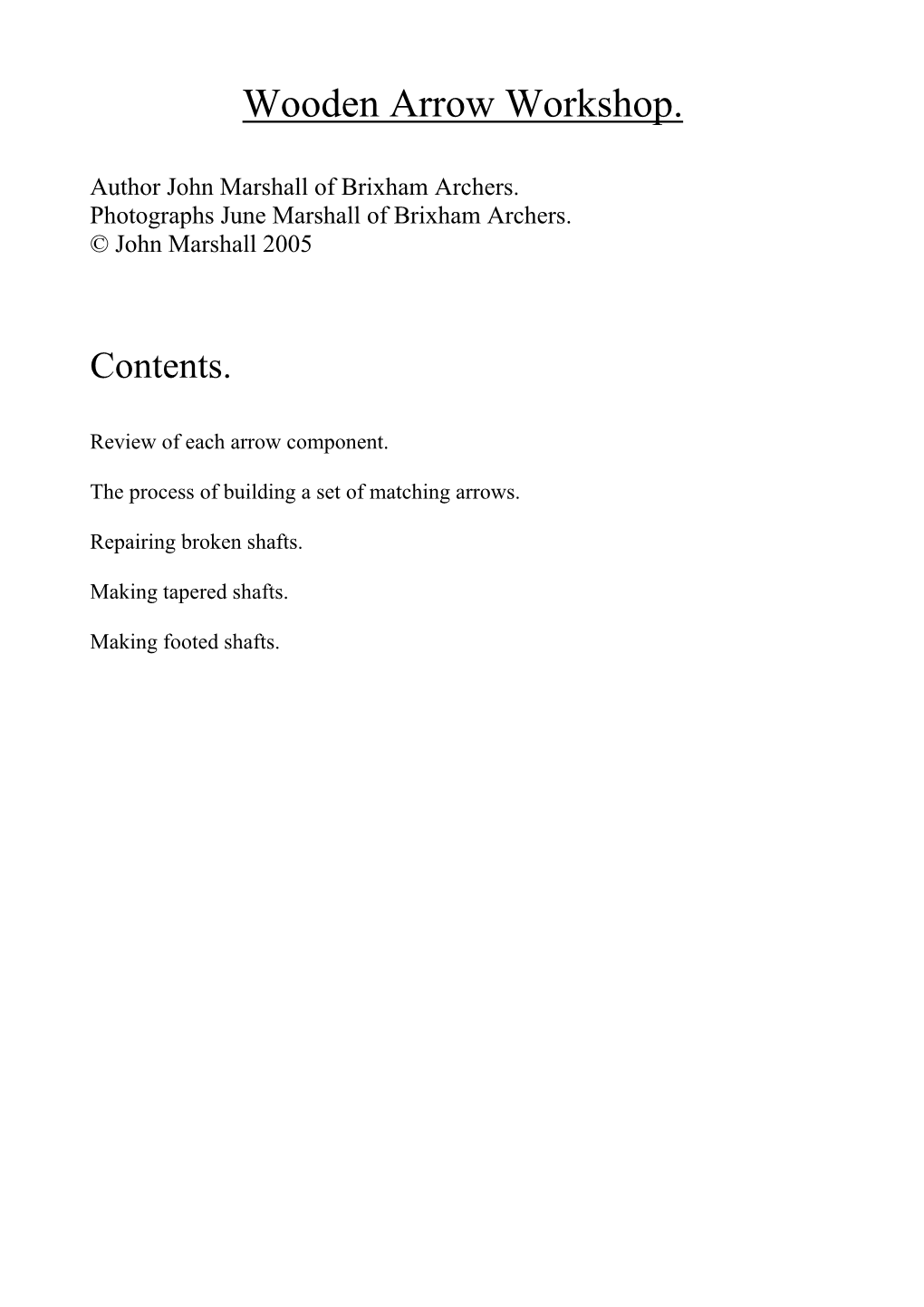
Load more
Recommended publications
-
Chapter 296-78 WAC, Sawmills and Woodworking
Chapter 296-78 WAC Introduction Sawmills and Woodworking Operations _________________________________________________________________________________________________________ Chapter 296-78 WAC Sawmills and Woodworking Operations (Form Number F414-010-000) This book contains rules for Safety Standards for sawmills and woodworking operations, as adopted under the Washington Industrial Safety and Health Act of 1973 (Chapter 49.17 RCW). The rules in this book are effective March 2018. A brief promulgation history, set within brackets at the end of this chapter, gives statutory authority, administrative order of promulgation, and date of adoption of filing. TO RECEIVE E-MAIL UPDATES: Sign up at https://public.govdelivery.com/accounts/WADLI/subscriber/new?topic_id=WADLI_19 TO PRINT YOUR OWN PAPER COPY OR TO VIEW THE RULE ONLINE: Go to https://www.lni.wa.gov/safety-health/safety-rules/rules-by-chapter/?chapter=78/ DOSH CONTACT INFORMATION: Physical address: 7273 Linderson Way Tumwater, WA 98501-5414 (Located off I-5 Exit 101 south of Tumwater.) Mailing address: DOSH Standards and Information PO Box 44810 Olympia, WA 98504-4810 Telephone: 1-800-423-7233 For all L&I Contact information, visit https://www.lni.wa.gov/agency/contact/ Also available on the L&I Safety & Health website: DOSH Core Rules Other General Workplace Safety & Health Rules Industry and Task-Specific Rules Proposed Rules and Hearings Newly Adopted Rules and New Rule Information DOSH Directives (DD’s) See http://www.lni.wa.gov/Safety-Health/ Chapter 296-78 WAC Table of Contents Sawmills and Woodworking Operations _________________________________________________________________________________________________________ Chapter 296-78 WAC SAFETY STANDARDS FOR SAWMILLS AND WOODWORKING OPERATIONS WAC Page WAC 296-78-500 Foreword. -
Watco® Danish Oil
TECHNICAL DATA WAT-02 WATCO® DANISH OIL .DESCRIPTION AND USES . PRODUCT APPLICATION (cont.) . Watco® Danish Oil is a unique blend of penetrating oil & varnish, TESTING COLOR which hardens in the wood, not on the wood. Watco Danish Oil Be sure to test your stain to verify the desired color. To test, apply penetrates deep into wood pores to protect from within and to the stain in an inconspicuous area. enhance the natural look and feel of the wood. It creates the rich, warm glow of a traditional hand-rubbed finish. Many projects can OPTIONAL STEPS be completed in less than an hour - simply brush or wipe on and wipe off. Pre-treat soft woods, such as pine, by lightly wiping the wood surface with a cloth moistened with Watco Danish Oil Natural .PRODUCTS . finish. Immediately wipe the surface completely dry and proceed with application. Gallon Quart Pint Description 65131 65141 6515H Golden Oak APPLICATION 65231 65241 65251 Cherry Use only when air (ambient) temperature is between 60-90°F 65331 65341 65351 Black Walnut (16-32°C) and relative humidity is below 85%. Allow for longer 65431 65441 65451H Fruit Wood dry times during damp and humid conditions. Mix or shake 65531 65541 65551 Light Walnut material thoroughly to ensure that any settled pigment is re- --- 214380 214381 Red Mahogany dispersed before application. Stir occasionally during use. Apply 65731 A65741 65751/303302 Natural a test sample on a small inconspicuous area before proceeding 65831 A65841 65851/303240 Dark Walnut with the entire job. Apply one coat of stain liberally with a brush or 65931 A65941 65951/303239 Medium Walnut clean lint free rag. -
Understanding Wipe-On Finishes
Understanding Wipe-on Finishes he moment of truth for many projects comes T and smooth, you have a thinned, or true, wiping long after the shop is cleaned, the tools are put varnish. If the puddle dries wrinkled and soft, itʼs away and the work is sanded. Applying a finish an oil/varnish blend. stops many woodworkers dead in their tracks. Why is it important to know what kind of wip- Finishing is the chore almost all woodworkers ing finish you have? When it comes to protecting fear most because it has the greatest potential the wood, varnish wins because it dries hard. for spoiling the project. So itʼs only natural that The reason has to do with the way the products woodworkers would seek a risk-free finish. For are manufactured. A typical oil-based varnish is this reason, many choose a finish thatʼs wiped on. made by cooking alkyd resins with an oil (usually Finishing manufacturers have capitalized on this modified soybean oil). To make a wiping varnish, fear and have developed rag-on finishes – thatʼs the finish is simply thinned with paint thinner or the good news about many products today. mineral spirits. Oil/varnish blends go further, The bad news is that the finishes you find on adding more oil and thereby further reducing the the shelves at your home centers have similar quantity of varnish in the finish. names but arenʼt alike – and you canʼt figure out Still confused about what to do? Well, the what each one does by simply reading the can. sure-fire way to get what you want is to make This is what they all have in common: You your own wiping varnish. -
Care and Preservation of Furniture and Wooden Objects by Louise Beck, Conservator, the Henry Ford
The Care and Preservation of Furniture and Wooden Objects by Louise Beck, Conservator, The Henry Ford. Introduction Antique furniture and wooden objects can be maintained for years of use and enjoyment provided that some basic care and attention is given to their preservation. The conservation staff at The Henry Ford have compiled the information in this fact sheet to help individuals care for their objects and collections. The first step in the care of collections is to understand and minimize or eliminate conditions that can cause damage. The second step is to follow basic guidelines for care, handling and cleaning. Types of Damage For most antique furniture owners, the desire to both utilize their collections and at the same time preserve them presents a formidable challenge. These two objectives are often at odds with each other. Improper handling/usage/display, environment, cleaning, and repair are the most common causes of damage to furniture and wooden objects. The primary cause of damage to furniture is careless handling and use, resulting in damage to surfaces or structural damage to the object. Inappropriate environment, both in terms of light and relative humidity, can lead to damage. Excessive light can accelerate the aging and degradation of finishes resulting in a cracked, brittle or "alligatored" appearance; it can also cause fading or softening of the finish. Since wood is a porous material it readily absorbs water when humidity levels are high. This absorption of moisture causes wood to swell. Conversely, wood shrinks in a dry environment. The shrinkage of wood in dry environments leads to the formation of structural cracks, lifting veneer and inlays, gaps in joints and the embrittlement of adhesives. -
Annex 2B: OSB (Oriented Strand Board)
Panel Guide Version 4 Annex 2B: OSB (oriented strand in panels from different manufacturers; in panels from different manufacturers it is possible to obtain ratios board) of property levels in the machine- to cross-direction of Description 1.25:1 to 2.5:1, thereby emulating the ratios found in OSB is an engineered wood-based panel material in plywood. which long strands of wood are bonded together with a synthetic resin adhesive. OSB is usually composed Appearance of three layers, with the strands of the outer two layers OSB is readily identified by its larger and longer wood orientated in a particular direction, more often than strands, compared to particleboard. The orientation not in the long direction of the panel. While there is an of the surface strands is not always visually apparent, orientation, it is often hard to see because there is quite especially in small pieces of panel. The panel tends to a large degree of variability in this orientation among have a number of holes on the surface due to the overlap adjacent strands in the panels from any one production of strands, but a smoother surface can be obtained by line, as well as between panels from different producers. sanding. However, OSB will never possess the smooth- ness of surface found in fibreboards and particleboards: rather its merits lie in the field of mechanical perfor- mance which is directly related to the use of longer and larger strands of wood. OSB varies in colour from a light straw colour to a medium brown depending on species used, resin system adopted and pressing conditions employed. -
Dyes Can Do It All Color Bare Wood Without Blotching, Tint Topcoats, and Touch up Blemishes
Dyes Can Do It All Color bare wood without blotching, tint topcoats, and touch up blemishes BY TERI MASASCHI oloring wood strikes terror in the hearts of most woodworkers. After spending six months build- Cing a piece, potentially ruining it in an hour is a definite cause for anxiety. Much of this caution stems from bad experiences applying typical hardware-store wood stains to bare wood. These mostly pigmented stains can cause results that are too dark, blotchy, and muddy. Far from enhancing the wood, the effect is to ruin the appearance. Rather than throw out the baby with the bathwater and forswear ever coloring wood, switch to dyes. Like pigments, dyes also are called stains, but instead of lying on top of the wood like a pigment stain, they penetrate the wood. This ability enhances wood by TYPES OF DYES Dyes come in three main groups: as powders to be mixed with water, alcohol or mineral spirits; in ready-to-use form as a non-grain-raising liquid; or as concentrates to be added to clear finishes. Each group has different uses and characteristics. POWDERED DYE NON-GRAIN-RAISING DYE 44 FINE WOODWORKING Photos: Mark Schofield COPYRIGHT 2006 by The Taunton Press, Inc. Copying and distribution of this article is not permitted. offering figure-revealing transparency. Dyes come in a range of colors from subtle wood tones to brilliant primaries, and they can be applied to bare wood, combined with clear coats, or used as touch-ups. Dyes come in powdered form, concentrates, and ready-to-use liq- uids. -
Woodworking Master
OHIO STATE UNIVERSITY EXTENSION OHIO 4-H MASTER PROJECTS 4-H 560M Woodworking Master By Doug Dill, Faculty Emeritus, Extension Educator, Ohio State University Extension, and Assistant Superintendent, Ohio State Fair 4-H Woodworking Day. Reviewed by Randall Reeder, Faculty Emeritus, Department of Food, Agricultural, and Biological Sciences, The Ohio State University The Woodworking Master project is for members who want to continue with woodworking after completing the Ohio 4-H woodworking projects (556 Measuring Up, 557 Making the Cut, 558 Nailing It Together, and 559 Finishing Up). Members of any age may complete this project, but must have completed the existing projects, must have woodworking experience comparable to what is required for other advanced-level 4-H projects, and must be able to plan and complete the project on their own with minimal supervision or assistance. NAME __________________________________________________________________________ AGE (as of January 1 of the current year): ______________________________________________ COUNTY: _______________________________________________________________________ CLUB NAME: _____________________________________________________________________ ADVISOR: _______________________________________________________________________ ohio4h.org CFAES provides research and related educational programs to clientele on a nondiscriminatory basis. For more information: go.osu.edu/cfaesdiversity. Project Guidelines 1. Plan, design, build, and evaluate at least one 6. If possible, have someone take pictures of you woodworking project. What you make should be working on your project at different stages as you different from what you can make within the progress from the beginning through completion, guidelines of other 4-H woodworking projects, or and attach copies of the photos in section 6 or in require specialized or professional-level skills to a separate project scrapbook. complete (beyond what would be expected in 7. -
Creating a Timber Frame House
Creating a Timber Frame House A Step by Step Guide by Brice Cochran Copyright © 2014 Timber Frame HQ All rights reserved. No part of this publication may be reproduced, stored in a retrieval system, or transmitted in any form or by any means, electronic, mechanical, recording or otherwise, without the prior written permission of the author. ISBN # 978-0-692-20875-5 DISCLAIMER: This book details the author’s personal experiences with and opinions about timber framing and home building. The author is not licensed as an engineer or architect. Although the author and publisher have made every effort to ensure that the information in this book was correct at press time, the author and publisher do not assume and hereby disclaim any liability to any party for any loss, damage, or disruption caused by errors or omissions, whether such errors or omissions result from negligence, accident, or any other cause. Except as specifically stated in this book, neither the author or publisher, nor any authors, contributors, or other representatives will be liable for damages arising out of or in connection with the use of this book. This is a comprehensive limitation of liability that applies to all damages of any kind, including (without limitation) compensatory; direct, indirect or consequential damages; income or profit; loss of or damage to property and claims of third parties. You understand that this book is not intended as a substitute for consultation with a licensed engineering professional. Before you begin any project in any way, you will need to consult a professional to ensure that you are doing what’s best for your situation. -
Finishing Techniques.Pdf
Finishing Techniques Al Miotke Sept 8, 2020 Share your ideas Agenda 1. Preparing the surface 2. Types of Finishes 3. Goals of the final finish 4. Pro’s/Con’s of each finish option 5. Filling the grain 6. Finish the finish 7. Applying a Gloss finish Good Reference materials Three stages of finishing 1. Surface preparation 2. Selecting and applying the finish 3. Finishing the finish Select the best finish for each piece Surface Preparation 1. Cut as clean as possible. 2. Go thru the grits to at least 320 or 400. • Depends on type of wood and finish you plan to apply and sheen you want. 3. Sand with the grain with last grit. 4. Don’t overheat the wood. Keep speed low. 5. Don’t over sand especially on soft or open grain woods. What are the common Finishes? 1) Oil • Natural product extracted from walnut, linseed, Tung, soy bean, etc. • Polymerized oil is heated to about 500 degrees in absence of oxygen, dryers sometimes added. Goal is to dry faster • Provided a natural looking finish but limited protection 2) Shellac • Shellac is a resin secreted by the female lac bug on trees in the forests of India and Thailand. • Friction Polish – Shellac, Alcohol, Boiled Linseed Oil, Beeswax optional 3) Varnish • Synthetic product made by cooking a drying oil and add resin like urethane or Alkalyd. • Wiping Varnish – Varnish/thinner blend 4) Lacquer • Nitrocellulose lacquer is mostly solvent-based and comprised of plant-based substances like cotton, mixed nitric and sulfuric acids. 5) Wax • Beeswax, carnuba • Provides little protection but adds sheen and maintains natural color • Used as both a finish and a polish. -
Cheery Cherry Toy Chest Download
Cheery Cherry Toy Chest A challenging classic that will last a lifetime We call this a toy chest—but it’s a book case, a knickknack box and a fun place to sit and read. And when your kids are grown, it makes one heck of a fne entry bench. Tis is one of the more challenging projects in the book. It involves biscuit joints, sunken panels and cutting tight curves. Plus, it’s made from cherry— a mistake in this material costs three times as much as a mistake in pine! So, if you’re a beginner, consider sharpening your chops on a couple of other projects before digging into this one. We show two versions of the fnished chest. One with cherry plywood panels; another with panels 18 | building unique and useful kids’ furniture 36" 1/4" 2 1/2" M 15" P R 11 1/4" 1 1/2" Q 15" 36" Top Side 1 1/4" 33" 1 1/2" 36" 9" E 1/4" 36" 1/4" 2 1/2" M F 2 1/2" M 1 1/2" D X 4 3/4" M 3/4" 15" H 15" 5 1/2" 3 1/2" 11 1/4" P R P 11 1/4" B 2 1/2" 24 1/2" R 11 1/4" 1 1/2" 24 1/2" Q 1 1/2" Q Seat T C 18 1/2" 12" U 9" U 16" W 10 1/8" V J K S 9" Front 15" 36" A 3 1/2" D 3 1/2" 15" 36" 1 1/4" 33" G 1 1/2" 1 1/4" 9" 33" E 1 1/2" 4" 9" O 1 1/2" E 1 1/2" 1" 1 1/2" 3/4" N L 3/4" 36" 33" F 1 1/2" F 37 1/2" 1 1/2" D X 4 3/4" D X 4 3/4" M 3/4" H 3/4" M 5 1/2" 36" H 3 1/2" 5 1/2" 3 1/2" 1/4" 11 1/4" B 2 1/2" 24 1/2" 11 1/4" B 2 1/2" 24 1/2" 24 1/2" 24 1/2" Seat 2 1/2" M T C 18 1/2" Seat 12" T C 18 1/2" 12" U 9" U 16" W 10 1/8" V J U 9" U 16" W 10 1/8" K V J S 9" K 15" S 9" P R 11 1/4" 1 1/2" Q A 3 1/2" D 3 1/2" A 3 1/2" D 3 1/2" G G 4" O 1 1/2" 1 1/2" 1" 4" 1 1/2" 3/4" O 1 1/2" 1 -
What Is Woodworking?
What is woodworking? Accident prevention in woodworking literally starts Never carry sharp or pointed tools in your pock- from the ground up — the floor. Whether you’re ets or use tools with burred or mushroomed heads. cutting, drilling, shaping or sanding, you will per- Check for and repair loose or damaged tool handles. form the operation more safely in a clean, unclut- tered workplace. When handling small tools, follow these suggestions: • Select the right tool for the job. Makeshift It’s easier and safer to work in a clean area tools are dangerous; • Sharp tools in good condition are safer; Remove sawdust, wood shavings and chips, • Give tools to co-workers by the handle first; and scrap lumber from the work area frequently • Carry only as many tools as you can safety throughout the day to eliminate slipping and trip- manage; ping hazards. • When carrying sharp or pointed tools, keep sharp edges and points down and never put Immediately clean up oil, grease and other liquids them in your pockets. spilled on the floor. Stop machine completely when unattended Pieces of lumber extending into aisles, materials lying around machinery and improperly stacked Unattended machinery is dangerous. The safe lumber make performing your job difficult and worker makes sure the machine is completely create hazards. stopped, not just switched off, before leaving it because an unsuspecting worker unfamiliar with the The floor itself also can become hazardous. Loose machine may touch the revolving cutting edge. All boards, protruding nails, splinters, holes or other woodworking machinery should have a magnetic surface defects can result in serious injuries if you start and stop button. -
Woodworking Joints.Key
Woodworking making joints Using Joints Basic Butt Joint The butt joint is the most basic woodworking joint. Commonly used when framing walls in conventional, stick-framed homes, this joint relies on mechanical fasteners to hold the two pieces of stock in place. Learn how to build a proper butt joint, and when to use it on your woodworking projects. Basic Butt Joint The simplest of joints is a butt joint - so called because one piece of stock is butted up against another, then fixed in place, most commonly with nails or screws. The addition of glue will add some strength, but the joint relies primarily upon its mechanical fixings. ! These joints can be used in making simple boxes or frames, providing that there will not be too much stress on the joint, or that the materials used will take nails or screws reliably. Butt joints are probably strongest when fixed using glued dowels. Mitered Butt Joint ! A mitered butt joint is basically the same as a basic butt joint, except that the two boards are joined at an angle (instead of square to one another). The advantage is that the mitered butt joint will not show any end grain, and as such is a bit more aesthetically pleasing. Learn how to create a clean mitered butt joint. Mitered Butt Joint The simplest joint that requires any form of cutting is a miter joint - in effect this is an angled butt joint, usually relying on glue alone to construct it. It requires accurate 45° cutting, however, if the perfect 90° corner is to result.