Computational Design of Scheduling Strategies for Multi-Robot Cooperative 3D Printing
Total Page:16
File Type:pdf, Size:1020Kb
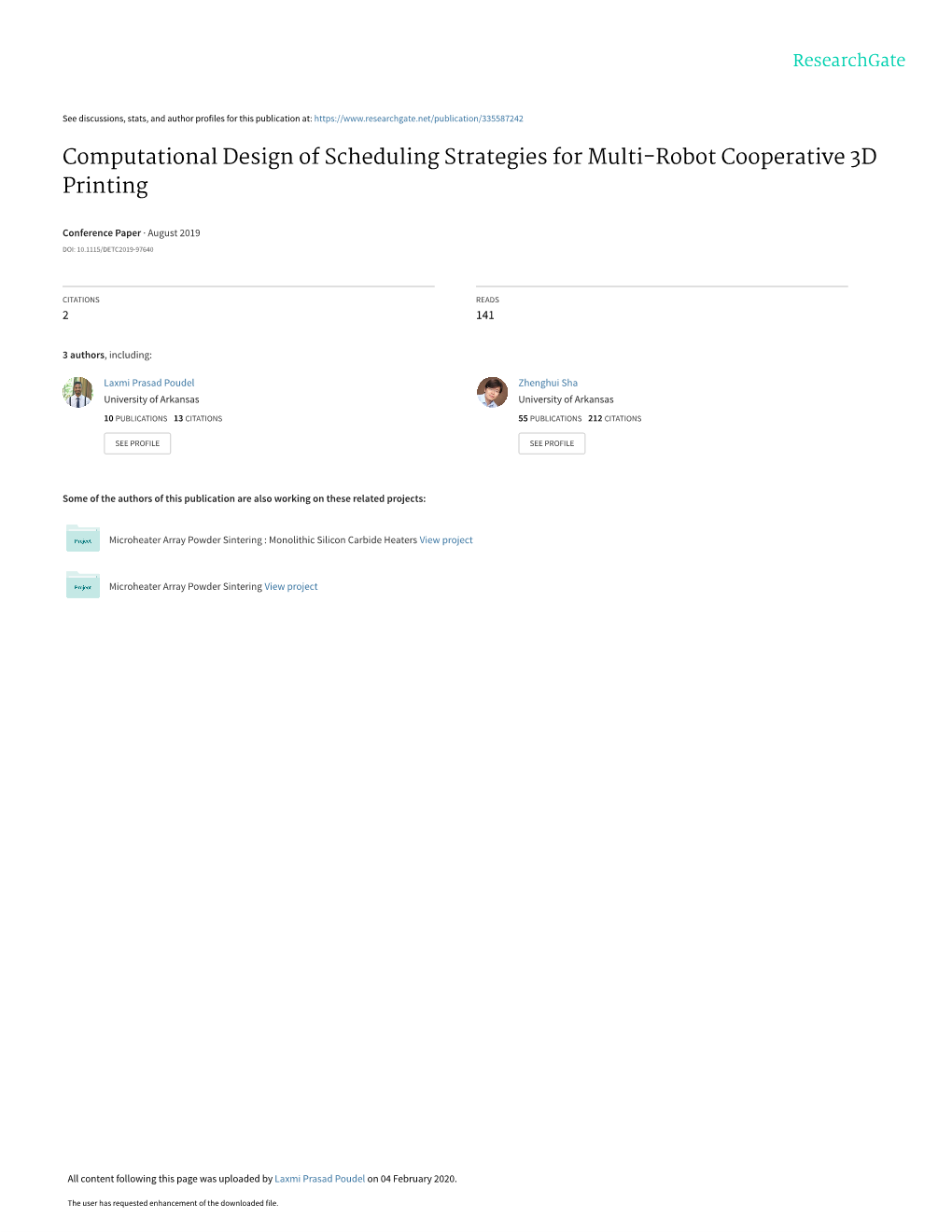
Load more
Recommended publications
-
A Novel Concept for the Study of Heterogeneous Robotic Swarms
Swarmanoid: a novel concept for the study of heterogeneous robotic swarms M. Dorigo, D. Floreano, L. M. Gambardella, F. Mondada, S. Nolfi, T. Baaboura, M. Birattari, M. Bonani, M. Brambilla, A. Brutschy, D. Burnier, A. Campo, A. L. Christensen, A. Decugni`ere, G. Di Caro, F. Ducatelle, E. Ferrante, A. F¨orster, J. Martinez Gonzales, J. Guzzi, V. Longchamp, S. Magnenat, N. Mathews, M. Montes de Oca, R. O’Grady, C. Pinciroli, G. Pini, P. R´etornaz, J. Roberts, V. Sperati, T. Stirling, A. Stranieri, T. St¨utzle, V. Trianni, E. Tuci, A. E. Turgut, and F. Vaussard. IRIDIA – Technical Report Series Technical Report No. TR/IRIDIA/2011-014 July 2011 IRIDIA – Technical Report Series ISSN 1781-3794 Published by: IRIDIA, Institut de Recherches Interdisciplinaires et de D´eveloppements en Intelligence Artificielle Universite´ Libre de Bruxelles Av F. D. Roosevelt 50, CP 194/6 1050 Bruxelles, Belgium Technical report number TR/IRIDIA/2011-014 The information provided is the sole responsibility of the authors and does not necessarily reflect the opinion of the members of IRIDIA. The authors take full responsibility for any copyright breaches that may result from publication of this paper in the IRIDIA – Technical Report Series. IRIDIA is not responsible for any use that might be made of data appearing in this publication. IEEE ROBOTICS & AUTOMATION MAGAZINE, VOL. X, NO. X, MONTH 20XX 1 Swarmanoid: a novel concept for the study of heterogeneous robotic swarms Marco Dorigo, Dario Floreano, Luca Maria Gambardella, Francesco Mondada, Stefano Nolfi, Tarek Baaboura, -
Science & Technology Trends 2020-2040
Science & Technology Trends 2020-2040 Exploring the S&T Edge NATO Science & Technology Organization DISCLAIMER The research and analysis underlying this report and its conclusions were conducted by the NATO S&T Organization (STO) drawing upon the support of the Alliance’s defence S&T community, NATO Allied Command Transformation (ACT) and the NATO Communications and Information Agency (NCIA). This report does not represent the official opinion or position of NATO or individual governments, but provides considered advice to NATO and Nations’ leadership on significant S&T issues. D.F. Reding J. Eaton NATO Science & Technology Organization Office of the Chief Scientist NATO Headquarters B-1110 Brussels Belgium http:\www.sto.nato.int Distributed free of charge for informational purposes; hard copies may be obtained on request, subject to availability from the NATO Office of the Chief Scientist. The sale and reproduction of this report for commercial purposes is prohibited. Extracts may be used for bona fide educational and informational purposes subject to attribution to the NATO S&T Organization. Unless otherwise credited all non-original graphics are used under Creative Commons licensing (for original sources see https://commons.wikimedia.org and https://www.pxfuel.com/). All icon-based graphics are derived from Microsoft® Office and are used royalty-free. Copyright © NATO Science & Technology Organization, 2020 First published, March 2020 Foreword As the world Science & Tech- changes, so does nology Trends: our Alliance. 2020-2040 pro- NATO adapts. vides an assess- We continue to ment of the im- work together as pact of S&T ad- a community of vances over the like-minded na- next 20 years tions, seeking to on the Alliance. -
Comprehensive Review on Modular Self-Reconfigurable Robot Architecture
International Research Journal of Engineering and Technology (IRJET) e-ISSN: 2395-0056 Volume: 06 Issue: 04 | Apr 2019 www.irjet.net p-ISSN: 2395-0072 Comprehensive Review on Modular Self-Reconfigurable Robot Architecture Muhammad Haziq Hasbulah1, Fairul Azni Jafar2, Mohd. Hisham Nordin2 1Centre for Graduate Studies, Universiti Teknikal Malaysia Melaka, Hang Tuah Jaya, 76100 Durian Tunggal, Melaka, Malaysia 2Faculty of Manufacturing Engineering, Universiti Teknikal Malaysia Melaka, Hang Tuah Jaya, 76100 Durian Tunggal, Melaka, Malaysia ---------------------------------------------------------------------***--------------------------------------------------------------------- Abstract - Self-reconfigurable modular robot is a new film directed by William Don Hall. In this movie, a character approach of robotic system which involves a group of identical named Hiro create a lot of Microbots that able to be robotic modules that are connecting together and forming controlled by neurotransmitter. They are designed by Hiro to structure that able to perform specific tasks. Such robotic connect together to form various shapes and perform tasks system will allows for reconfiguration of the robot and its cooperatively Hall and Williams [3]. The idea of that movie structure in order to adapting continuously to the current concept is multiple robots that able to change shape in group needs or specific tasks, without the use of additional tools. being controlled by human thought. Nowadays, the use of this type of robot is very limited because The MSR robot is build based on the electronics components, it is at the early stage of technology development. This type of computer processors, and memory and power supplies, and robots will probably be widely used in industry, search and also they might have a feature for the robot to have an ability rescue purpose or even on leisure activities in the future. -
3D Printing Quarterly Report—Q32018 3D PRINTING–A FAST MOVING MARKET Developments in 3D Printing a Sector by Sector Overview
3D Printing Quarterly Report—Q32018 3D PRINTING–A FAST MOVING MARKET Developments in 3D Printing A Sector by Sector Overview Overview This report explores developments in 3D printing across several sectors and categories for the quarterly period of July 1 to October 10, 2018. For more information, Table of Contents please contact: Overview ................................... 2 Patents & Copyright ................. 12 Food ....................................... 21 Mark E. Avsec General ..................................... 2 Auto & Transportation ............... 12 Consumer Goods & Retail ......... 22 (216) 363-4151 Materials ................................... 4 Aviation & Aerospace ............... 13 Education ................................ 23 [email protected] Printing Techniques & Health & Life Sciences ............. 14 Environmental Efforts ............... 24 Capabilities .............................. 5 Manufacturing & Construction... 17 Arts & Entertainment ................ 25 M&A and Investments ................ 9 Clothing & Wearables ............... 20 Sports ..................................... 25 www.beneschlaw.com Miscellaneous Partnerships ...... 11 3D PRINTING–A FAST MOVING MARKET 3D Printing Quarterly Report—Q3 A Sector by Sector Overview General Aurora Group to market Nano Dimension 3D printers in China The deal expands Nano Dimension’s already active presence in Asia Pacific beyond Hong Kong, South Korea, Singapore and Taiwan. Founded in 2012, Nano Dimensions develops and manufactures 3D printers for the electronics -
Robotics in Construction
GFS-1604 Robotics in Construction IQP Final Report 3/24/2016 An Interactive Qualifying Project Report Submitted to the Faculty of Worcester Polytechnic Institute In partial fulfillment of the requirements for the Degree of Bachelor by Alexander Ruggiero Sebastian Salvo Chase St. Laurent Project Advisors: Professor Michael Gennert, Robotic Engineering Professor Guillermo Salazar, Civil Engineering Dr. Luciana Burdi, Massport Sponsoring Agency: Massport This report is the product of an education program, and is intended to serve as partial documentation for the evaluation of academic achievement. The report should not be construed as a working document by the reader. Abstract This project reviews construction process and new emerging robotic technologies, all while keeping in mind the societal implications the new technologies may have. The study identifies and analyzes the benefits and limitations of a wide array of robotic applications. A roadmap and timeline are created to guide Massport on how and when to implement the various robotic applications into their construction operations. The end result of this project could be extended to the construction industry as a whole. ii | P a g e Acknowledgements The authors would like to thank the following individuals for their contributions and assistance throughout the duration of this project: Dr. Michael Schroeder Dr. Luciana Burdi, Massport Danielle Arciero, Massport Marzia Bolpagni, Massport Ruth McKeough, Secretary IRB, WPI Professor Michael Gennert, Director of Robotics, WPI Professor Guillermo Salazar, Department of Civil and Environmental Engineering, WPI iii | P a g e Authorship Chapter/Section Author(s) Abstract Chase St. Laurent Acknowledgements Chase St. Laurent Introduction Alexander Ruggiero & Sebastiano Salvo Background Chase St. -
List of Accepted Graduation Projects - Academic Year 20/21
List of Accepted Graduation Projects - Academic Year 20/21 Project ID Project Title University Name GP2021.R16.4 Smart Glove for the voiceless Canadian International Collage GP2021.R16.5 Smart Satellite Benha University GP2021.R16.6 Smart City using IoT System and Artificial Intelligence Menofia University GP2021.R16.7 Auto Updated Streets-Information on Map Cairo University GP2021.R16.9 Arabic text visualization Alexandria University ASIC Physical Design of RISC-V Core Processor for Self-Driving GP2021.R16.12 Automotive Applications Cairo University ChipNet CNN Hardware Acceleration on FPGA and ASIC for 3D GP2021.R16.13 Lidar and Camera Images in Autonomous Vehicles Zewail city of science and technology Integration of Federated Machine Learning in Smart Metering Canadian Higher Institute Technology and GP2021.R16.14 System. Management. GP2021.R16.15 Chatbot for Mode Enhancement of Drivers in Egyptian Dialect. Cairo University Analog Layout Automation using Machine GP2021.R16.16 Learning Cairo University Automatic Post-Layout Generation of Analog Designs using Reinforcement Learning to reduce the design time and increase GP2021.R16.19 productivity. Zewail city of science and technology Machine Learning Hardware Acceleration for Advanced Driving GP2021.R16.20 Assistance Systems (ADAS) Cairo university 5G Performance Improvement using Massive MIMO and GP2021.R16.21 Beamforming project "PDSCH-RX“ Cairo University A Novel Real-Time Tourist Attraction Platform for Marine Life GP2021.R16.22 Species Based on Artificial Intelligence Nile University -
Amug Conference
2019 AMUG CONFERENCE Hilton Chicago Chicago, Illinois, USA March 31 - April 4, 2019 ADDITIVE MANUFACTURING USERS GROUP For Users, By Users Additive Manufacturing Users Group 2019 AMUG Conference March 31 - April 4 Chicago, Illinois Front Cover: (left) Advanced Finishing: Praetorian Guard helmet, Andrew Sliwa, Custom Prototypes (right) Advanced Concepts: Old world engineering gets an additive makeover, Ed Graham, ProtoCam 2 2019 AMUG Conference 31st Annual Education & Training Conference TABLE OF CONTENTS PLAN YOUR TIME AT AMUG — 3 TABLE OF CONTENTS 16 FEATURED SPEAKERS 5 WELCOME LETTER 18 2019 SCHOLARSHIP RECIPIENTS 6 MISSION PHILOSOPHY 19 2018 TECHNICAL COMPETITION WINNERS 7 FIRST TIME ATTENDEES 20 CONFERENCE AGENDA 8 MOBILE APP 28 HOTEL FLOOR PLANS 9 AGENDA-AT-A-GLANCE 34 AMUG TEAM AND COMMITTEES 10 2018 CONFERENCE DEMOGRAPHICS 38 AMUG DINOS 12 GENERAL INFORMATION 40 AMUG HISTORY 14 AMUGEXPO FLOOR PLAN 43 2019 SPONSORS For Users 3 By Users AMUG educates and advances the uses and applications of additive manufacturing technologies. 4 2019 AMUG Conference 31st Annual Education & Training Conference WELCOME TO AMUG 2019 FOR USERS, BY USERS — I’d like to extend a great big WELCOME to all of you that are joining us for the first time, as well as those that are back for your 2nd, 3rd, 10th, or even 31st time. It’s hard to believe we celebrated our 30th anniversary last year, and while 31 isn’t a milestone, it’s another example of how long, yet how short, the additive manufacturing (AM) industry has been around. It is an example that reminds us how far we have come, yet how far we still have to go. -
The Triangle of Life: Evolving Robots in Real-Time and Real-Space A.E
The Triangle of Life: Evolving Robots in Real-time and Real-space A.E. Eiben1, N. Bredeche2;3, M. Hoogendoorn1, J. Stradner4, J. Timmis5, A.M. Tyrrell6, A. Winfield7 1VU University Amsterdam ([email protected], [email protected]) 2UPMC Univ Paris 06, UMR 7222, ISIR, F-75005, Paris, France ([email protected]) 3CNRS, UMR 7222, ISIR, F-75005, Paris, France 4Karl-Franzens University Graz ([email protected]) 5University of York (jon.timmis, [email protected]) 6Bristol Robotics Lab, (alan.winfi[email protected]) Abstract organism) and vice versa. In the traditional setting, being aggregated is a transient state that enables the robots to meet Evolutionary robotics is heading towards fully embodied evo- a certain challenge after which they can disassemble and re- lution in real-time and real-space. In this paper we introduce turn to normal. In contrast, we perceive being aggregated the Triangle of Life, a generic conceptual framework for such systems in which robots can actually reproduce. This frame- as a permanent state and consider aggregated structures as work can be instantiated with different hardware approaches viable robotic organisms with the ability to reproduce. That and different reproduction mechanisms, but in all cases the is, two or more organisms can recombine the (genetic) code system revolves around the conception of a new robot organ- that specifies their makeup and initiate the creation of a new ism. The other components of the Triangle capture the prin- robotic organism. This differs from earlier work aiming at cipal stages of such a system; the Triangle as a whole serves self-replication self-reconfiguration as a guide for realizing this anticipated breakthrough and and in that a ‘child or- building systems where robot morphologies and controllers ganism’ is neither a replica of its parents, nor is it a recon- can evolve in real-time and real-space. -
3D Printing and International Security, PRIF Report No
www.ssoar.info 3D printing and international security: risks and challenges of an emerging technology Fey, Marco Veröffentlichungsversion / Published Version Arbeitspapier / working paper Zur Verfügung gestellt in Kooperation mit / provided in cooperation with: Hessische Stiftung Friedens- und Konfliktforschung (HSFK) Empfohlene Zitierung / Suggested Citation: Fey, M. (2017). 3D printing and international security: risks and challenges of an emerging technology. (PRIF Reports, 144). Frankfurt am Main: Hessische Stiftung Friedens- und Konfliktforschung. https://nbn-resolving.org/ urn:nbn:de:0168-ssoar-51867-8 Nutzungsbedingungen: Terms of use: Dieser Text wird unter einer Deposit-Lizenz (Keine This document is made available under Deposit Licence (No Weiterverbreitung - keine Bearbeitung) zur Verfügung gestellt. Redistribution - no modifications). We grant a non-exclusive, non- Gewährt wird ein nicht exklusives, nicht übertragbares, transferable, individual and limited right to using this document. persönliches und beschränktes Recht auf Nutzung dieses This document is solely intended for your personal, non- Dokuments. Dieses Dokument ist ausschließlich für commercial use. All of the copies of this documents must retain den persönlichen, nicht-kommerziellen Gebrauch bestimmt. all copyright information and other information regarding legal Auf sämtlichen Kopien dieses Dokuments müssen alle protection. You are not allowed to alter this document in any Urheberrechtshinweise und sonstigen Hinweise auf gesetzlichen way, to copy it for public or commercial purposes, to exhibit the Schutz beibehalten werden. Sie dürfen dieses Dokument document in public, to perform, distribute or otherwise use the nicht in irgendeiner Weise abändern, noch dürfen Sie document in public. dieses Dokument für öffentliche oder kommerzielle Zwecke By using this particular document, you accept the above-stated vervielfältigen, öffentlich ausstellen, aufführen, vertreiben oder conditions of use. -
Cheap Technology Will Challenge U.S. Tactical Dominance
Chairman and CEO of AeroVironment briefs Chief of Naval Operations Admiral Jonathan Greenert on capabilities and potential applications of Global Observer, a long-range, long-duration UAV, Simi Valley, California, November 2014 (U.S. Navy/Peter D. Lawlor) Cheap Technology Will Challenge U.S. Tactical Dominance By T.X. Hammes he convergence of dramatic ties—extending even to the individual. internal combustion engines, radio, improvements in the fields of This new diffusion of power has major radar, and weapons. In 1914, at the T robotics, artificial intelligence, implications for the conduct of warfare, beginning of World War I, battleships materials, additive manufacturing, and not the least of which are the major were considered the decisive weapon for nanoenergetics is dramatically chang- hazards or opportunities that it presents fleet engagements, and the size of the ing the character of conflict in all to medium and even small powers. The battleship fleet was seen as a reasonable domains. This convergence is creating a outcome will depend on the paths they proxy for a navy’s strength. The war’s massive increase in capabilities available choose. single major fleet action, the Battle of to increasingly smaller political enti- Jutland, seemed to prove these ideas Historical Case correct. Accordingly, during the inter- Fortunately, this level of technological war period, battleships received the change and convergence is not unprec- lion’s share of naval investments. Navies Dr. T.X. Hammes is a Distinguished Research edented. From 1914 to 1939, there took advantage of rapid technologi- Fellow in the Center for Strategic Research, Institute for National Strategic Studies, at the were technological breakthroughs in cal gains to dramatically improve the National Defense University. -
Robotics on the Battlefield Part II the Coming Swarm
OCTOBER Robotics on the Battlefield Part II 2014 The Coming Swarm By Paul Scharre Also in this series: “20YY: Preparing for War in the Robotic Age” by Robert O. Work and Shawn Brimley “Robotics on the Battlefield Part I: Range, Persistence and Daring” by Paul Scharre Acknowledgements I would like to thank the numerous colleagues at CNAS and elsewhere who assisted in the development of this report. Liz Fontaine led the production and design of this report. Adam Elkus provided invaluable assistance in understanding animal and robotic swarms. CNAS research interns James Marshall and Matthew Seeley assisted in background research. In addi- tion, a number of outside experts provided valuable insights on a range of issues. I would like to thank Russell Rumbaugh of the Stimson Center, Michael Sulmeyer of the Office of the Secretary of Defense, Dean Wilkening of Lawrence Livermore National Laboratory, David Scheidt of Johns Hopkins University Applied Physics Laboratory, Sachin Jain of Aurora Flight Sciences, Timothy Chung of the Naval Postgraduate School and Andrew Herr of Helicase for their assistance, corrections and insights. I would also like to thank the numerous colleagues at CNAS and other institutions who provided feedback on draft versions of this report. Any errors of analysis, fact or omission are mine alone. CNAS does not take institutional positions. Cover Image A flock of auklet birds exhibit swarm behavior. (U.S. FISH AND WILDLIFE SERVICE) TABLE OF CONTENTS I. Executive Summary 5 VII. Enemy Swarms and Countermeasures 42 II. Introduction: 10 VIII. Conclusion: Building the Swarm 44 The Reconnaissance-Strike Swarm IX. Recommendations 50 III. -
A Generative Approach for Scheduling Multi-Robot Cooperative 3D Printing
Journal of Computing and Information Science in Engineering A Generative Approach for Scheduling Multi-Robot Cooperative 3D Printing Laxmi Poudel Graduate Research Assistant, SiDi Lab University of Arkansas, Fayetteville AR 72701 [email protected] ASME student member Wenchao Zhou Assistant Professor, AM3 Lab University of Arkansas, Fayetteville AR 72701 [email protected] ASME member Zhenghui Sha1 Assistant Professor, SiDi Lab University of Arkansas, Fayetteville AR 72701 [email protected] ASME member ABSTRACT Cooperative 3D printing (C3DP) is a novel approach to additive manufacturing, where multiple printhead-carrying mobile robots work cooperatively to print the desired part. The core of C3DP is the chunk-based printing strategy in which the desired part is first split into smaller chunks, and then the chunks are assigned to individual robots to print and bond. These robots will work simultaneously in a scheduled sequence to print the entire part. Although promising, C3DP lacks a generative approach that enables automatic chunking and scheduling. In this study, we aim to develop a generative approach that can automatically generate different print schedules for a chunked object by exploring a larger solution space that is often beyond the capability of human cognition. The generative approach contains 1) a random generator of diverse print schedules based on an adjacency matrix that represents a directed dependency tree structure of chunks; 2) a set of geometric constraints against which the randomly generated schedules will be checked for validation; and 3) a printing time evaluator for comparing the performance of all valid schedules. We demonstrate the efficacy of the generative approach using two case studies: a large simple rectangular bar and a miniature folding SUV with more complicated geometry.