Reduction of Titania-Ferrous Ore by Carbon Monoxide
Total Page:16
File Type:pdf, Size:1020Kb
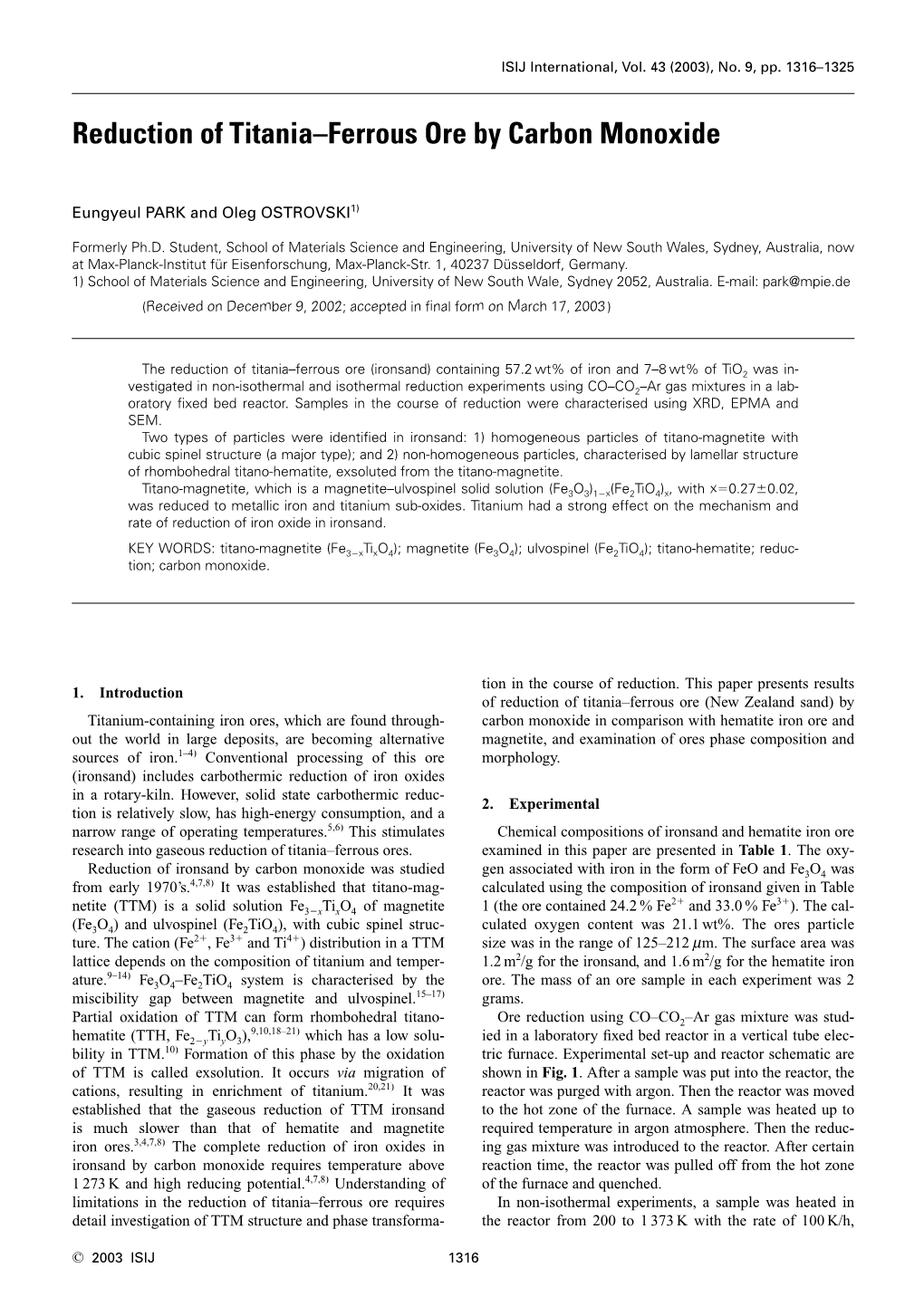
Load more
Recommended publications
-
“The Next Generation in Iron Ore”
“The Next Generation in Iron Ore” Amex Resources Ltd (ASX(ASX::AXZ)AXZ) Amex Resources Ltd (‘Amex’) is an iron ore focused, mineral resources development company listed on the Australian Securities Exchange (ASX). The Company is currently concentrating on Feasibility Studies and Development of its Mba Delta Ironsand Project, in the Fiji Islands. Philosophy The Company’s philosophy is to: “To acquire, explore and develop mineral properties that show real potential for production of economic iron ore mineralisation, in order to increase shareholder wealth” Projects The Company’s focus is the Mba Delta Ironsand Project in Fiji. Amex also maintains an aggressive program of exploration and project generation. The Company’s project portfolio includes: • Mba Delta Ironsand Project, Viti Levu, Fiji – Development, • Mt Maguire Iron Ore Project, Ashburton, WA – Exploration, • Paraburdoo South Iron Ore Project, Pilbara, WA – Exploration, • Channar West Iron Ore Project, Pilbara, WA – Application. The Company continues to evaluate iron ore properties in the Asia-Pacific region for addition to its project portfolio. Recent Highlights Amex is currently completing Feasibility Studies over its Mba Delta Ironsand Project. Highlights from the Company’s exploration and development program include: • Increased JORC Resource and status upgraded to ‘Indicated’: 220 Million Tonnes @ 10.9% Fe (Iron) • Pilot plant commissioned and producing samples of concentrate for export from Fiji for evaluation by potential end users and strategic partners in China. • Concentrates high quality, grading >58% Fe through simple magnetic separation, with low impurities: 58.5% Fe & 0.65% V2O5 with 5.2% Al 2O3 0.37% CaO 0.05% K 20 3.4% MgO 0.04% Na 2O 0.03% P <0.01% S, 1.5% SiO 2 & 6.5% TiO 2. -
AGI3754 Silica Ironsand
CI/SfB I | IYp1| | Specialist silica sands Garside Sands Ironsand OHS61759 FM96927 EMS96928 A fine top dressing sand. Applications Mechanical analysis • Top dressing Sieve size (mm) Specification (% Passing) • Rootzone mix 1.00 100 • Slit drainage 0.50 40 - 95 • Lime mortar sand. 0.355 15 - 65 Sectors 0.25 0 - 30 • Sports and leisure 0.18 0 - 20 • Industrial and manufacturing. 0.150 Available in 0.125 0 - 10 • Loose: tippers Colour Brown • Bulk bags (tote). Specific gravity apparent 2.74 Water absorption 0.4 Soluble chloride salts 0.0009 Sulphate content 0.007 pH 7.6 Garside Ironsand Size range: 1.00 – 0.18mm Source: Leighton Buzzard, Bedfordshire Geology: Lower Greensand of the Cretaceous period Composition: Quartz Grain shape: Sub angular to rounded Garside Sands Ironsand Manufacturing standard Sustainability and local sourcing Policies All aggregate Industries products are Energy use: Aggregate Industries is at the Aggregate Industries’ policies on the manufactured in accordance with ISO 9001 forefront of sustainability and has committed environment and community, health and with factory compliance to ISO 14001. to reduce carbon emissions by 20% by safety and sustainable solutions for different 2016 based on a 2012 base line. product applications can be viewed on our Chemical analysis website www.aggregate.com Recyclable: 100% of the product can be Chemical analysis % recycled thus reducing the amount of COSHH data Silica SiO 87.54 material that is sent to landfill. 2 Full COSHH data on Garside Sands Alumina Al2O3 1.01 Manufacturing location: produced in the products is available on request. Please call UK, with locally sourced materials under the Technical helpline on 01525 237911. -
The Story of Taranaki's Steel Industry
IRONSAND AND IRONWILL: The Story of Taranaki's Steel Industry Locals too long away from the black sands of Taranaki’s beaches, quickly forget its foot-blistering summer heat and all-pervading sprinkling on picnic sandwiches. Geologically, the result of erosion of the andesite volcanos of the western North Island, the sands have high concentrations of the mineral, titanomagnetite, the raw material of the iron industry. The history of the industry is little known outside the region and the antecedents of the export operations at Taharoa (Kawhia) and Waipipi (Waverley) surprises even many locals. To begin, therefore, at the beginning. We are asked to believe that immediately after the culture shock of first setting foot on a rat and sandfly infested beach on a remote South Pacific island, reliably reported to be inhabited by ferocious tattooed cannibals and birds the size of a well-bred shire horse, one tiny entrepreneurial Plymouth Company immigrant had the wit to recognize the commercial potential of Taranaki ironsands during his six kilometre trudge up the beach to the embryonic settlement of New Plymouth. This gentleman, recorded as a carpenter in the 1841 ship’s manifest of the Amelia Thompson, had, by the time of a 1917 account, increased his status to that of a "previous proprietor of an iron foundry in Cornwall"! To John Perry however, must go the honour of the 1848 first of a lamentable series of failures, which has tended to signal “progress” in the local iron-smelting industry. Following Perry's unsuccessful smelting attempt of 1848, samples of ironsand were shipped 'Home' at regular intervals to the established foundries of the Black Country. -
Geophysical Study of the Taharoa Ironsand Deposit, West Coast, North Island, New Zealand
New Zealand Journal of Geology and Geophysics ISSN: 0028-8306 (Print) 1175-8791 (Online) Journal homepage: http://www.tandfonline.com/loi/tnzg20 Geophysical study of the Taharoa ironsand deposit, west coast, North Island, New Zealand Donald C. Lawton & Manfred P. Hochstein To cite this article: Donald C. Lawton & Manfred P. Hochstein (1993) Geophysical study of the Taharoa ironsand deposit, west coast, North Island, New Zealand, New Zealand Journal of Geology and Geophysics, 36:2, 141-160, DOI: 10.1080/00288306.1993.9514564 To link to this article: http://dx.doi.org/10.1080/00288306.1993.9514564 Published online: 23 Mar 2010. Submit your article to this journal Article views: 245 View related articles Citing articles: 1 View citing articles Full Terms & Conditions of access and use can be found at http://www.tandfonline.com/action/journalInformation?journalCode=tnzg20 Download by: [125.239.173.16] Date: 29 August 2017, At: 22:51 New Zealand Journal of Geology and Geophysics, 1993, Vol. 36: 141-160 141 0028-8306/93/3602-0141 $2.50/0 © The Royal Society of New Zealand 1993 Geophysical study of the Taharoa ironsand deposit, west coast, North Island, New Zealand DONALD C. LAWTON Although titanomagnetite concentrations in the sands can 2 Department of Geology and Geophysics produce a gravitational effect of up to 10 um/s , residual The University of Calgary gravity anomalies could not be used to assess concentration 2500 University Drive N.W. patterns independently because the anomalies are disturbed by Calgary, Alberta T2N 1N4, Canada larger effects associated with the irregular greywacke basement. However, gravity interpretation models were used MANFRED P. -
Reduction of Titania-Ferrous Ore by Hydrogen
ISIJ International, Vol. 44 (2004), No. 6, pp. 999–1005 Reduction of Titania–Ferrous Ore by Hydrogen Eungyeul PARK and Oleg OSTROVSKI1) Former PhD Student, School of Materials Science and Engineering, University of New South Wales, Sydney 2052, Australia, now at Max-Planck-Institut für Eisenforschung, Max-Planck Str. 1, D-40237 Düsseldorf, Germany. E-mail: [email protected] 1) School of Materials Science and Engineering, University of New South Wales, Sydney 2052, Australia. (Received on November 4, 2003; accepted in final form on February 16 2004 ) The reduction of titania–ferrous ore (ironsand) containing 57.2 mass% of iron and 7–8 mass% of TiO2 was investigated in isothermal experiments using H2–Ar gas mixtures in a laboratory fixed bed reactor in the temperature range from 973 to 1 373 K. The degree of reduction was measured using an on-line Dew Point sensor and the samples in the course of reduction were characterized using SEM and XRD analyses. The complete reduction of iron oxide in the ore by 25vol%H2–Ar was achieved within 60 min at tempera- ture higher than 1 123 K. At 1 173 K, the reduction rate increased with hydrogen content in the reducing gas up to 25 vol%H2. The composition of samples after 2-h reduction by 25vol%H2–Ar depended on the reduc- tion temperature. Below 1 073 K, the final sample contained iron and iron–titanium oxides. At temperatures above 1 173 K, the final sample was composed of iron and titanium oxide. The reduction path at tempera- tures above 1 173 K is suggested as follows: → ϩ → ϩ → ϩ Ͻ Ͻ Ϫ Fe3ϪxTixO4 ‘FeO’ Fe3ϪxϪdTixϩdO4 Fe Fe3ϪxϪdTixϩdO4 Fe xTiO2,(0d 1 x) KEY WORDS: ironsand; titanimagnetite; reduction; hydrogen; reduction path. -
New Zealand Steel Water Matters
NEW ZEALAND STEEL WATER MATTERS Steelmaking, using the black ironsands of the West Coast of New Zealand’s North Island, has been present on the banks of the Waiuku Estuary for over 50 years. Today, New Zealand Steel operates as the world’s only producer of steel manufactured from ironsand, and is the largest single manufacturing site in Franklin employing over 1200 people. Over the next few editions of the West Franklin Breeze, we will be taking a closer look at the steel mill and its environmental position within the community. This month we focus on water, where it is sourced, how it is process at the mine, and for the steelmaking processes at the used, how it is returned back into the environment, and the Glenbrook mill. sustainability around these points of interest. The transportation of the ironsand requires around 7000 Much of the water used in the steelmaking and finishing tonnes of water each day. The river water is mixed with ironsand processes is drawn from the Waikato River, 18 kilometres away. to form a slurry which is then pumped to the Glenbrook mill River water is supplemented by the large volume of stormwater through an underground pipe. back into the mill water circuits. collected from across the industrial site. At the mill, water is used for cleaning waste gases, produc- New Zealand Steel’s environment management system places Water is extracted at a point on the Waikato River about 14 ing steam in the boilers, cooling, spraying and rinsing product, great importance on its commitment to minimise any effects kilometres from the river mouth. -
Explanatory Notes for the Mineral-Resources Map of the Circum-Pacific Region Southwest Quadrant 1:10,000,000
U.S. DEPARTMENT OF THE INTERIOR TO ACCOMPANY MAP CP-42 U.S. GEOLOGICAL SURVEY EXPLANATORY NOTES FOR THE MINERAL-RESOURCES MAP OF THE CIRCUM-PACIFIC REGION SOUTHWEST QUADRANT 1:10,000,000 CIRCUM-PACIFIC ENERGY AND MINERAL ill/ I RESOURCES 1996 CIRCUM-PACIFIC COUNCIL FOR ENERGY AND MINERAL RESOURCES Michel T. Halbouty, Chair CIRCUM-PACIFIC MAP PROJECT John A. Reinemund, Director George Gryc, General Chair EXPLANATORY NOTES FOR THE MINERAL-RESOURCES MAP OF THE CIRCUM-PACIFIC REGION SOUTHWEST QUADRANT Scale: 1:10,000,000 By LAND RESOURCES W.D. Palfreyman, Australian Geological Survey Organisation, Canberra, A.C.T. 2601, Australia C.M. Mock, Australian Geological Survey Organisation, Canberra, A.C.T. 2601, Australia R.L. Brathwaite, New Zealand Geological Survey, Department of Scientific and Industrial Research, Lower Hutt, New Zealand R.N. Brothers, University of Auckland, Auckland, New Zealand (deceased) George Gryc, U.S. Geological Survey, Menlo Park, California 94025, U.S.A. SEAFLOOR RESOURCES David Z. Piper, U.S. Geological Survey, Menlo Park, California 94025, U.S.A. Theresa R. Swint-Iki, U.S. Geological Survey, Menlo Park, California 94025, U.S.A. Floyd W. McCoy, Associated Scientists at Woods Hole, Woods Hole, Massachusetts 02543, U.S.A. Frank T. Manheim, U.S. Geological Survey, Woods Hole, Massachusetts 02543, U.S.A. Candice M. Lane-Bostwick, U.S. Geological Survey, Woods Hole, Massachusetts 02543, U.S.A. 1996 Explanatory Notes to Supplement the MINERAL-RESOURCES MAP OF THE CIRCUM-PACIFIC REGION SOUTHWEST QUADRANT R. W. Johnson, Chair Southwest Quadrant Panel LAND RESOURCES W. David Palfreyman, Australian Geological Survey Organisation, Canberra, A.C.T. -
Iron Sand Extraction in South Taranaki Bight: Effects on Seawater Trace Metal Concentrations
Iron sand extraction in South Taranaki Bight: effects on seawater trace metal concentrations AUT Client report: TTRL 20138 August 2013 Iron sand extraction in South Taranaki Bight: effects on seawater trace metal concentrations Kay Vopel John Robertson Peter S. Wilson Prepared for Trans–Tasman Resources Ltd. AUT Client report: TTRL 20138 August 2013 Institute for Applied Ecology New Zealand School of Applied Sciences Auckland University of Technology Private Bag 92006 Auckland 1142 Phone +64 9 921 9999 ext. 6461 www.aut.ac.nz Content Executive summary 3 Introduction 5 Material and methods 8 Approach 8 Section A 8 Section B 8 Sample collection and preparation 8 South Taranaki Bight sediment 8 Reference sediment 11 Processed sediment 11 Analyses 12 Particle size, organic matter and water content 12 Sediment extractions: AVS 12 Sediment extractions: trace metals 13 Standard elutriation 13 Standard elutriate test 14 Trace metals in sediment slurry 14 Results and discussion 15 Section A: sediment cores and sediment slurry 15 Physical properties 15 Acid volatile sulfides 17 Trace metals in sediment 17 Trace metals in sediment suspensions 19 Chromium and nickel in RC slurry 20 Section B: processed iron sand 23 Physical properties 23 Acid volatile sulfides 24 Trace metals in sediment 24 Trace metals in sediment suspensions 26 Summary and conclusions 27 References 29 Appendix I AUT Client report: TTRL 20138 2 Executive summary Trans–Tasman Resources Limited (hereafter, TTR) plans to exploit a source of vanadium-titanomagnetite in South Taranaki Bight, New Zealand, with an offshore dredge-mining operation. Because this operation will displace, modify and suspend deep anoxic sediment, it may make sediment-bound contaminants available to pelagic and benthic biota. -
National Slag Association
NATIONAL SLAG MF 205-1 ASSOCIATION Water Improvement Initiatives in New Zealand Using Melter Slag Filter Beds Bill Bourke, SteelServ Ltd, Auckland, New Zealand ABSTRACT The ability of iron and steel industry slag aggregates to remove phosphorous and certain heavy metals from degraded water has been understood and well researched for many years (e.g. Yamada et al.1986). Aggregates from the unique, ironsand based steel industry at New Zealand Steel exhibit similar properties. This paper gives a brief overview of the iron and steel making operation at New Zealand Steel and then examines some recent initiatives to further expand the use of these materials in water improvement projects: as well as reviewing the results from installations that have been in place for some time. Key words: iron sand, slag, phosphorous, zinc, suspended solids, pH, waste water, storm water. INTRODUCTION Iron Making at New Zealand Steel The iron and steel making operation at New Zealand Steel’s Glenbrook mill in South Auckland, New Zealand is unique compared to its international contemporaries. The Glenbrook operation is the only iron and steel manufacturing process based on the utilization of iron sand and commenced operation in the early 1970’s. The iron sand deposits were the result of a series of eruptions around 2.5 million years ago, centered on a series of volcanoes on the west coast of New Zealand’s North Island, the last remaining being Mt Taranaki (Appendix 1). The results of these eruptions deposited large quantities of titanomagnetite iron bearing material, which were ground by the action of the sea, then swept by currents up and down the west coast of New Zealand’s North Island to eventually be deposited in large dunes, some of which are 90 metres high and extend up to two kilometers inland. -
Making the New Zealand House 1792 – 1982 by Nigel
MAKING THE NEW ZEALAND HOUSE 1792 – 1982 BY NIGEL PHILIP ISAACS A thesis submitted to the Victoria University of Wellington in fulfilment of the requirements for the degree of Doctor of Philosophy Victoria University of Wellington 2015 ABSTRACT A systematic investigation was undertaken of the techniques (materials and technologies) used to construct the shell of the New Zealand house (envelope and interior linings) between 1792 and 1982. Using census, manufacturing and import statistics with analysis of local and international archives and publications, principal techniques were selected and documented. A review of local construction and building publications provide a background to the development of construction education and training, as well as the speed of change. Analysis of census data showed that from 1858 to 1981 the majority of dwelling walls in terms of construction (appearance) were timber, brick, board or concrete, while the structure was timber frame. Analysis of import data for seven materials (galvanised iron, asbestos cement, cement, window glass, wood nails, gypsum and roofing slate) from 1870 to 1965 found the UK was a majority supplier until 1925, except for USA gypsum. For the rest of the period, the UK continued to play a preeminent role with increasing Australian imports and local manufacture. Examination of archival and published information on techniques used for the sub-floor, floor, wall (construction and structure), fenestration, roof and thermal insulation provide an overview of country of orign, decade of arrival, spread of use and, if relevant, reasons for failure. Forty materials (including earth and brick, stone, cement and concrete, timber and ferrous metals) and twenty-four technologies are documented. -
Reduction Kinetics of Oxidized New Zealand Ironsand Pellets in H2 at Temperatures up to 1443 K
University of Wollongong Research Online Faculty of Engineering and Information Faculty of Engineering and Information Sciences - Papers: Part B Sciences 2020 Reduction Kinetics of Oxidized New Zealand Ironsand Pellets in H2 at Temperatures up to 1443 K Ao Zhang University of Wollongong, [email protected] Brian J. Monaghan University of Wollongong, [email protected] Raymond Longbottom University of Wollongong, [email protected] Mohammad Nusheh Chris Bumby Follow this and additional works at: https://ro.uow.edu.au/eispapers1 Part of the Engineering Commons, and the Science and Technology Studies Commons Recommended Citation Zhang, Ao; Monaghan, Brian J.; Longbottom, Raymond; Nusheh, Mohammad; and Bumby, Chris, "Reduction Kinetics of Oxidized New Zealand Ironsand Pellets in H2 at Temperatures up to 1443 K" (2020). Faculty of Engineering and Information Sciences - Papers: Part B. 3807. https://ro.uow.edu.au/eispapers1/3807 Research Online is the open access institutional repository for the University of Wollongong. For further information contact the UOW Library: [email protected] Reduction Kinetics of Oxidized New Zealand Ironsand Pellets in H2 at Temperatures up to 1443 K Abstract 2020, The Minerals, Metals & Materials Society and ASM International. Direct reduction of iron ore pellets using hydrogen gas has the potential to significantly reduce CO2 emissions from the ironmaking process. In this work, green pellets of titanomagnetite ironsand from New Zealand were oxidatively sintered to form titanohematite. These sintered pellets were then reduced by H2 gas at temperatures ≥ 1043 K, and a maximum reduction degree of ~ 97 pct was achieved. Fully reduced pellets contained metallic Fe as the main product phase, but several different (Fe, Ti) oxides were also present as minor inclusions. -
SONG YINGXING's ILLUSTRATIONS of IRON PRODUCTION1 Donald B
SONG YINGXING’S ILLUSTRATIONS OF IRON PRODUCTION1 Donald B. Wagner2 This extract from a longer article is intended as an addendum to Peter Golas’s contribution,3 in which he gives a critical and erudite discus- sion of numerous issues raised by the illustrations in Song Yingxing’s Ͳ̠ɓ Tiangong kaiwu ƲŸÒŒ. I consider only the description of iron production, and only the illustrations in the 1637 edition. Much research is needed to identify the sources of the Tiangong kaiwu. Some of Song Yingxing’s descriptions may be eyewitness accounts, but it seems impossible that he could have seen all of the technologies he describes. The range of the book is simply too broad for one man’s personal observation. In particular, we do not know how much control Song Yingxing had over the illustrations in his book. For all we know his publisher may have supplied all of the illustrations, and Song may have been deeply unhappy at the result—I hasten to add that I do not consider this the most likely possibility, but many academic authors’ experience with commercial publishers suggests it. If we are to use the Tiangong kaiwu as a source for Ming technolo- gies it will be important to come as close to an answer to this question as possible—it matters a great deal where the information in Song Yingxing’s book comes from. In the following I take up three pas- sages in his description of iron production and attempt to show that in these cases (1) his text is accurate; (2) the illustrations are accurate; but (3) the illustrations do not always show the same technologies as the text.4 ——— 1 Extracted from Wagner 2006.