Crystallite Size Dependency of the Pressure and Temperature Response in Nanoparticles of Ceria and Other Oxides
Total Page:16
File Type:pdf, Size:1020Kb
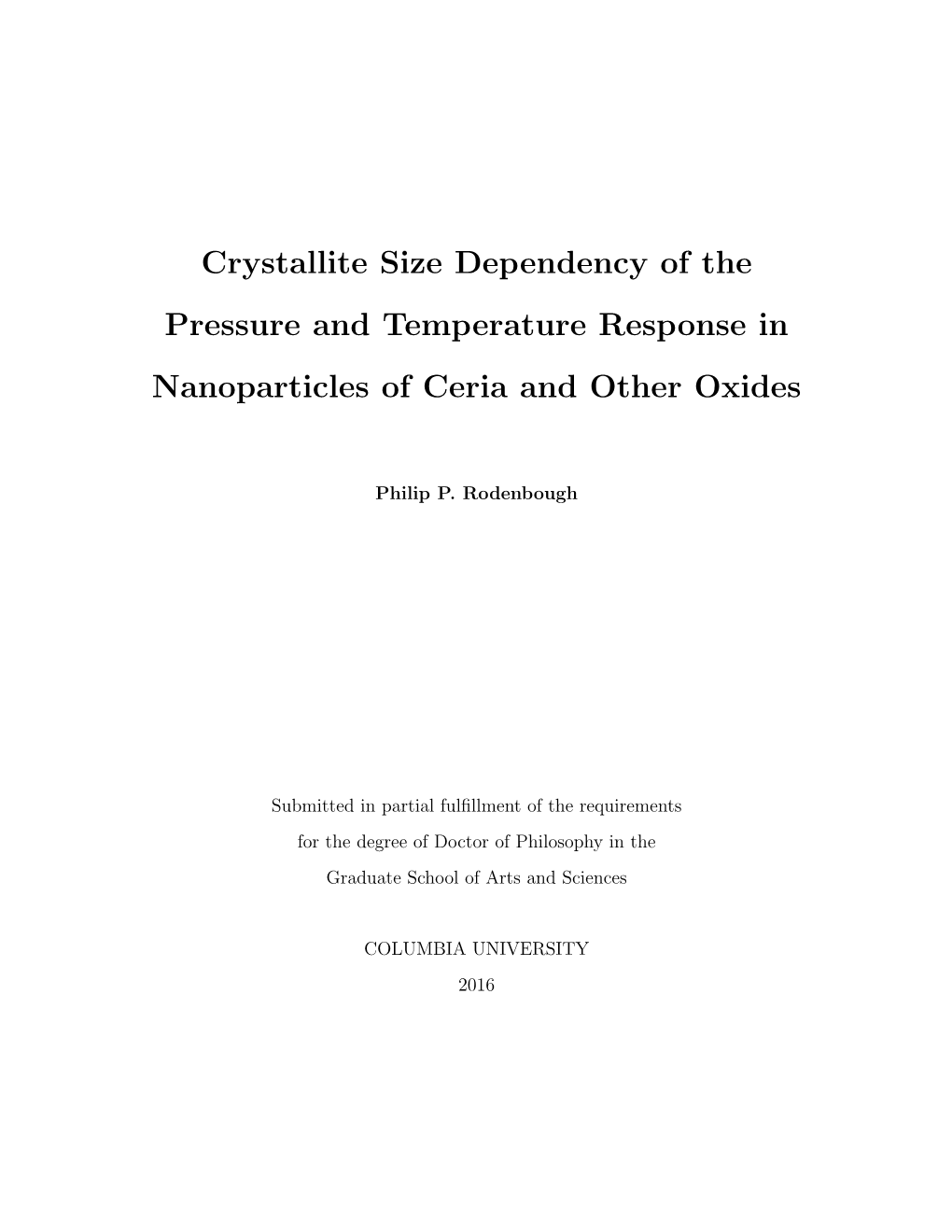
Load more
Recommended publications
-
Ceramic Matrix Composites Taking Flight at GE Aviation Featuring
AMERICAN CERAMIC SOCIETY bullemerginge ceramicstin & glass technology APRIL 2019 Ceramic matrix composites taking flight at GE Aviation Featuring: April 30 – May 1, 2019 Ceramic science in the skies: Electrification, EBCs, and PDCs | New Ohio partnership for technician training FIRING YOUR IMAGINATION FOR 100 YEARS Ads from the 1940’s and 1950’s www.harropusa.com ACerS Anniversary Ad 2.indd 1 2/13/19 3:44 PM contents April 2019 • Vol. 98 No.3 feature articles Ceramic matrix composites taking flight at 30 GE aviation The holy grail for jet engines is efficiency, and the improved high-temperature capability of CMC systems is giving General Electric a great advantage. department News & Trends . 4 by Jim Steibel Spotlight . 10 Ceramics in Energy . 19 cover story Research Briefs . 21 Nonoxide polymer-derived CMCs for 34 “super” turbines The melting point of single-crystal blades limits further columns advancement in operating temperature of gas turbines with metallic materials. Ceramics, which have much higher melt- All about aircraft . 29 ing points, hold the promise for future “super” turbines. Infographic by Lisa McDonald by Zhongkan Ren and Gurpreet Singh Deciphering the Discipline . 64 Ultra-high temperature oxidation of high entropy UHTCs Taking off: Advanced materials contribute by Lavina Backman 40 to the evolution of electrified aircraft Commercial electrified aircraft are expected to take off within the next decade—and advanced materials are play- ing an increasingly critical role in solving key technical challenges that will push the boundaries even higher. meetings 25th International Congress on by Ajay Misra Glass (ICG 2019) . 56 GFMAT-2/Bio-4 . -
Nanomaterials How to Analyze Nanomaterials Using Powder Diffraction and the Powder Diffraction File™
Nanomaterials How to analyze nanomaterials using powder diffraction and the Powder Diffraction File™ Cerium Oxide CeO2 PDF 00-064-0737 7,000 6,000 5,000 4,000 Intensity 3,000 2,000 1,000 20 30 40 50 60 70 80 90 100 110 120 Nanomaterials Table of Contents Materials with new and incredible properties are being produced around the world by controlled design at the atomic and molecular level. These nanomaterials are typically About the Powder Diffraction File ......... 1 produced in the 1-100 nm size scale, and with this small size they have tremendous About Powder Diffraction ...................... 1 surface area and corresponding relative percent levels of surface atoms. Both the size and available (reactive) surface area can contribute to unique physical properties, Analysis Tools for Nanomaterials .......... 1 such as optical transparency, high dissolution rate, and enormous strength. Crystallite Size and Particle Size ������������ 2 In this Technical Bulletin, we are primarily focused on the use of structural simulations XRPD Pattern for NaCI – An Example .... 2 in order to examine the approximate crystallite size and molecular orientation in nanomaterials. The emphasis will be on X-ray analysis of nanomaterials. However, Total Pattern Analysis and the �������������� 3 Powder Diffraction File electrons and neutrons can have similar wavelengths as X-rays, and all of the X-ray methods described have analogs with neutron and electron diffraction. The use of Pair Distribution Function Analysis ........ 3 simulations allows one to study any nanomaterials that have a known atomic and Amorphous Materials ............................ 4 molecular structure or one can use a characteristic and reproducible experimental diffraction pattern. -
Particle Size and Structural Effects in Platinum Electrocatalysis
JOURNAL OF APPLIED ELECTROCHEMISTRY 20 (1990) 537-548 REVIEWS OF APPLIED ELECTROCHEMISTRY 23 Particle size and structural effects in platinum electrocatalysis S. MUKERJEE Tata Energy Research Institute, 7 Jor Bagh, New Delhi-llO 003, India Received 4 January 1989; revised 18 October 1989 Of the several factors which influence electrocatalytic activity, particle size and structural effects are of crucial importance, but their effects and mechanism of interaction, vis-a-vis overall performance, have been, at best, vaguely understood. The situation is further aggravated by the use of a wide range of experimental conditions resulting in non-comparable data. This paper attempts systematically to present the developments to date in the understanding of these structural interactions and to point out areas for future investigation. The entire content of this review has been examined from the context of the highly dispersed Pt electrocatalyst, primarily because it has been examined in the greatest detail. In the first two sections a general idea on the correlations between surface microstructure and geometric model is presented. Subsequently, indicators of a direct correlation between particle size and catalyst support synergism are considered. The structural and particle size effect on electro- catalysis is examined from the point of view of anodic hydrogen oxidation and cathodic oxygen reduction reactions. The hydrogen and oxygen chemisorption effects, presented with the discussion on the anodic and cathodic electrocatalytic reactions, provide important clues toward resolving some of the controversial findings, especially on the dependence of particle size on the anodic hydrogen oxidation reaction. Finally, the effect of alloy formation on the cathodic oxygen reduction reaction is discussed, providing insights into the structural aspect. -
Preparation of a Ceramic Matrix Composite Made of Hydroxyapatite Nanoparticles and Polylactic Acid by Consolidation of Composite Granules
nanomaterials Article Preparation of a Ceramic Matrix Composite Made of Hydroxyapatite Nanoparticles and Polylactic Acid by Consolidation of Composite Granules Elzbieta Pietrzykowska 1,2,*, Barbara Romelczyk-Baishya 2 , Jacek Wojnarowicz 1 , Marina Sokolova 3, Karol Szlazak 2, Wojciech Swieszkowski 2, Janis Locs 3 and Witold Lojkowski 1 1 Institute of High Pressure Physics, Polish Academy of Science, Sokolowska 29/37, 01-142 Warsaw, Poland; [email protected] (J.W.); [email protected] (W.L.) 2 Faculty of Materials Science and Engineering, Warsaw University of Technology, Woloska 141, 02-507 Warsaw, Poland; [email protected] (B.R.-B.); [email protected] (K.S.); [email protected] (W.S.) 3 Rudolfs Cimdins Riga Biomaterials Innovations and Development Centre of RTU, Institute of General Chemical Engineering, Faculty of Materials Science and Applied Chemistry, Riga Technical University, Pulka Street 3, LV-1007 Riga, Latvia; [email protected] (M.S.); [email protected] (J.L.) * Correspondence: [email protected]; Tel.: +48-228-760-429 Received: 31 March 2020; Accepted: 15 May 2020; Published: 30 May 2020 Abstract: Composites made of a biodegradable polymer, e.g., polylactic acid (PLA) and hydroxyapatite nanoparticles (HAP NPs) are promising orthopedic materials. There is a particular need for biodegradable hybrid nanocomposites with strong mechanical properties. However, obtaining such composites is challenging, since nanoparticles tend to agglomerate, and it is difficult to achieve good bonding between the hydrophilic ceramic and the hydrophobic polymer. This paper describes a two-step technology for obtaining a ceramic matrix composite. The first step is the preparation of composite granules. -
The Proposed Crystallization Behavior of the Teo2-Nb2o5-Bi2o3-Er2o3
The Proposed Crystallization Behavior of the TeO2-Nb2O5-Bi2O3-Er2O3 Glass Ceramic System By Cooper Howard An Honors Thesis Submitted In Partial Fulfillment of the Requirements For the Alfred University Honors Program Under the Supervision of: Chair: Dr. Yiquan Wu Committee Members: Dr. Holly Shulman, Dr. William LaCourse Alfred, NY May 2020 The road to completing this thesis began quite a long time ago, though its actual inception was fairly recent. When I began my time at Alfred University I was entered as a mechanical engineer, I went through all of the first year courses, and then got to our explorations in the second semester. I took the one on mechanical engineering first, I found myself becoming increasingly disinterested as the class went on, disillusioned with mechanical engineering. Then, I took the ceramics exploration, and it clicked. At the beginning of the next semester after the summer, I signed the paperwork and changed my major, and found my home in the world of materials science. Ceramic engineering immediately became something I was deeply interested in, I approached all the relevant coursework with gusto and a desire to learn. My excitement grew more and more as I realized how much of an active field the discipline is, the opportunities for research and discovery at every turn. This was the first key moment in how I came to my thesis. While my love for ceramic engineering grew, I also continued to cultivate my long held interest in physics, taking a physics course in every semester up until my senior year, where my workload finally caught up with me. -
University Miaorilms International
INFORMATION TO USERS This reproduction was made from a copy of a document sent to us for microfilming. While the most advanced technology has been used to photograph and reproduce this document, the quality of the reproduction is heavily dependent upon the quality of the material submitted. The following explanation of techniques is provided to help clarify markings or notations which may appear on this reproduction. 1.The sign or “ target” for pages apparently lacking from the document photographed is “ Missing Page(s)” . I f it was possible to obtain the missing page(s) or section, they are spliced into the film along w ith adjacent pages. This may have necessitated cutting through an image and duplicating adjacent pages to assure complete continuity. 2. When an image on the film is obliterated with a round black mark, it is an indication of either blurred copy because of movement during exposure, duplicate copy, or copyrighted materials that should not have been filmed. For blurred pages, a good image of the page can be found in the adjacent frame. If copyrighted materials were deleted, a target note will appear listing the pages in the adjacent frame. 3. When a map, drawing or chart, etc., is part of the material being photographed, a definite method of “sectioning” the material has been followed. It is customary to begin film ing at the upper left hand comer o f a large sheet and to continue from left to right in equal sections with small overlaps. I f necessary, sectioning is continued again-beginning below the first row and continuing on until complete. -
Effect of Heat Treatment on the Activity and Stability of Carbon Supported Ptmo Alloy Electrocatalysts for Hydrogen Oxidation in Proton Exchange Membrane Fuel Cells
Journal of Power Sources 247 (2014) 712e720 Contents lists available at ScienceDirect Journal of Power Sources journal homepage: www.elsevier.com/locate/jpowsour Effect of heat treatment on the activity and stability of carbon supported PtMo alloy electrocatalysts for hydrogen oxidation in proton exchange membrane fuel cells Ayaz Hassan a, Alejo Carreras b, Jorge Trincavelli b, Edson Antonio Ticianelli a, * a Instituto de Quimica de São Carlos, Universidade de São Paulo, Caixa Postal 7 80, São Carlos, SP CEP 13560-970, Brazil b Instituto de Física Enrique Gaviola (IFEG)-CONICET, Facultad de Matemática, Astronomía y Física, Universidad Nacional de Córdoba, Medina Allende s/n, 5016 Córdoba, Argentina highlights The CO tolerance and stability of heat-treated carbon supported PtMo (60:40 at.%) catalysts are investigated. The PtMo/C catalyst treated at 600 C shows higher CO tolerance compared to that of the untreated material. PtMo/C electrocatalysts suffer a partial dissolution of Mo during a 5000 times cycling aging. The stability of the PtMo/C electrocatalyst is improved after the 600 C heating treatment. article info abstract Article history: The effect of heat treatment on the activity, stability and CO tolerance of PtMo/C catalysts was studied, Received 20 July 2013 due to their applicability in the anode of proton exchange membrane fuel cells (PEMFCs). To this purpose, Received in revised form a carbon supported PtMo (60:40) alloy electrocatalyst was synthesized by the formic acid reduction 29 August 2013 method, and samples of this catalyst were heat-treated at various temperatures ranging between 400 Accepted 31 August 2013 and 700 C. -
Use of High Energy Ball Milling on the Sintering Optimization of Alumina Ceramics
Seventh International Latin American Conference on Powder Technology, November 08-10, Atibaia, SP, Brazil Use of high energy ball milling on the sintering optimization of alumina ceramics Helio R. Simoni1,a, Eduardo Saito1,b, Claudinei dos Santos1,2,c, Felipe Antunes Santos1,d, Alfeu Saraiva Ramos3,e, Olivério Moreira M.Silva4,f 1 USP-EEL - Universidade de São Paulo, Escola de Engenharia de Lorena, Polo Urbo Industrial, Gleba AI6, s/n, Mondesir, Lorena-SP, Brazil, CEP12600-000 2UNIFOA - Centro Universitário de Volta Redonda, Av. Paulo Erlei Alves Abrantes, 1325, Volta Redonda-RJ, Brazil, CEP 27240-560 3 UNESP-FEG - Unersidade Estadual Paulista, Faculdade de Engenharia de Guaratinguetá, Av. Dr. Ariberto Pereirada Cunha, 333, Guaratinguetá-SP, Brazil, CEP 12516-410 4 CTA-IAE/AMR - Centro Técnico Aeroespacial, Praça Marechal do Ar Eduardo Gomes, 50, S.J. Campos-SP, Brazil, CEP 12228-904 [email protected], [email protected], [email protected], [email protected], [email protected] Keywords: Al2O3, Al2O3-Y2O3, high-energy ball milling, sintering, characterization Abstract: In this work, the effect of the milling time on the densification of the alumina ceramics with or without 5wt.%Y2O3, is evaluated, using high-energy ball milling. The milling was performed with different times of 0, 2, 5 or 10 hours. All powders, milled at different times, were characterized by X-Ray Diffraction presenting a reduction of the crystalline degree and crystallite size as function of the milling time increasing. The powders were compacted by cold uniaxial pressing and sintered at 1550°C-60min. Green density of the compacts presented an increasing as function of the milling time and sintered samples presented evolution on the densification as function of the reduction of the crystallite size of the milled powders. -
Correlation Between Crystal Structure, Surface/Interface Microstructure, and Electrical Properties of Nanocrystalline Niobium Thin Films
nanomaterials Article Correlation between Crystal Structure, Surface/Interface Microstructure, and Electrical Properties of Nanocrystalline Niobium Thin Films L. R. Nivedita 1, Avery Haubert 2, Anil K. Battu 1,3 and C. V. Ramana 1,3,* 1 Center for Advanced Materials Research, University of Texas at El Paso, 500 West University Avenue, El Paso, TX 79968, USA; [email protected] (L.R.N.); [email protected] (A.K.B.) 2 Department of Physics, University of California, Santa Barbara, Broida Hall, Santa Barbara, CA 93106, USA; [email protected] 3 Department of Mechanical Engineering, University of Texas at El Paso, 500 West University Avenue, El Paso, TX 79968, USA * Correspondence: [email protected]; Tel.: +1-915-747-8690 Received: 10 May 2020; Accepted: 26 June 2020; Published: 30 June 2020 Abstract: Niobium (Nb) thin films, which are potentially useful for integration into electronics and optoelectronics, were made by radio-frequency magnetron sputtering by varying the substrate temperature. The deposition temperature (Ts) effect was systematically studied using a wide range, 25–700 ◦C, using Si(100) substrates for Nb deposition. The direct correlation between deposition temperature (Ts) and electrical properties, surface/interface microstructure, crystal structure, and morphology of Nb films is reported. The Nb films deposited at higher temperature exhibit a higher degree of crystallinity and electrical conductivity. The Nb films’ crystallite size varied from 5 to 9 ( 1) nm and tensile strain occurs in Nb films as Ts increases. The surface/interface morphology of ± the deposited Nb films indicate the grain growth and dense, vertical columnar structure at elevated Ts. The surface roughness derived from measurements taken using atomic force microscopy reveal that all the Nb films are characteristically smooth with an average roughness <2 nm. -
The Properties of and Transport Phenomena in Oxide Films on Iron, Nickel, Chromium and Their Alloys in Aqueous Environments
View metadata, citation and similar papers at core.ac.uk brought to you by CORE provided by Julkari STUK-YTO-TR 150 January 1999 The properties of and transport phenomena in oxide films on iron, nickel, chromium and their alloys in aqueous environments T. Laitinen, M. Bojinov, I. Betova, K. Mäkelä, T. Saario VTT Manufacturing Technology In STUK this study was supervised by Seija Suksi STUK • SÄTEILYTURVAKESKUS • STRÅLSÄKERHETSCENTRALEN RADIATION AND NUCLEAR SAFETY AUTHORITY The conclusions presented in the STUK report series are those of the authors and do not necessarily represent the official position of STUK. ISBN 951-712-286-1 ISSN 0785-9325 Oy Edita Ab, Helsinki 1999 STUK-YTO-TR 150 LAITINEN, Timo, BOJINOV, Martin, BETOVA, Iva, MÄKELÄ, Kari, SAARIO, Timo. (VTT Manufactur- ing Technology). The properties of and transport phenomena in oxide films on iron, nickel, chromium and their alloys in aqueous environments. STUK-YTO-TR 150. Helsinki 1999. 75 pp. + Appendices 4 pp. ISBN 951-712-286-1 ISSN 0785-9325 Keywords: oxide films, iron, nickel, chromium, steels, nickel-based alloys, ambient and high- temperature aqueous environments, transport properties, growth mechanism, localised corrosion, activity incorporation ABSTRACT The construction materials used in coolant systems in nuclear power plants become covered with oxide films as a result of exposure to the aqueous environment. The susceptibility of the materials to different forms of corrosion, as well as the extent of the incorporation of radioactive species on the surfaces of the primary circuit, are greatly influenced by the physical and chemical properties of these oxide films. The composition and characteristics of the oxide films in turn depend on the applied water chemistry. -
Advanced Measurements of Silicon Carbide Ceramic Matrix Composites
INL/EXT-12-27032 Advanced Measurements of Silicon Carbide Ceramic Matrix Composites David Hurley Farhad Fazbod Zilong Hua Stephen Reese Marat Khafizov August 2012 The INL is a U.S. Department of Energy National Laboratory operated by Battelle Energy Alliance DISCLAIMER This information was prepared as an account of work sponsored by an agency of the U.S. Government. Neither the U.S. Government nor any agency thereof, nor any of their employees, makes any warranty, expressed or implied, or assumes any legal liability or responsibility for the accuracy, completeness, or usefulness, of any information, apparatus, product, or process disclosed, or represents that its use would not infringe privately owned rights. References herein to any specific commercial product, process, or service by trade name, trade mark, manufacturer, or otherwise, does not necessarily constitute or imply its endorsement, recommendation, or favoring by the U.S. Government or any agency thereof. The views and opinions of authors expressed herein do not necessarily state or reflect those of the U.S. Government or any agency thereof. INL/EXT-12-27032 Advanced Measurements of Silicon Carbide Ceramic Matrix Composites David Hurley Farhad Farzbod Zilong Hua Stephen Reese Marat Khafizov August, 2012 Idaho National Laboratory Materials Science and Engineering Department Idaho Falls, Idaho 83415 http://www.inl.gov Prepared for the U.S. Department of Energy Office of Nuclear Energy Under DOE Idaho Operations Office Contract DE-AC07-05ID14517 ii iii ABSTRACT Silicon carbide (SiC) is being considered as a fuel cladding material for accident tolerant fuel under the Light Water Reactor Sustainability (LWRS) Program sponsored by the Nuclear Energy Division of the Department of Energy. -
JAKO201814446220751.Pdf
Original Articles Carbon Letters Vol. 26, 81-87 (2018) Comparative study on the morphological properties of graphene nanoplatelets prepared by an oxidative and non-oxidative route Jung-Chul An1, Eun Jung Lee1, So-Young Yoon1, Seong-Young Lee2 and Yong-Jung Kim1,♠ 1Energy Materials Research Group, Research Institute of Industrial Science & Technology (RIST), Pohang 37673, Korea 2Materials Solution Research Group, Research Institute of Industrial Science & Technology (RIST), Pohang 37673, Korea Article Info Abstract Received 25 October 2017 Morphological differences in multi-layered graphene flakes or graphene nanoplatelets pre- Accepted 19 December 2017 pared by oxidative (rGO-NP, reduced graphene oxide-nanoplatelets) and non-oxidative (GIC-NP, graphite intercalation compound-nanoplatelets) routes were investigated with var- ♠Corresponding Author ious analytical methods. Both types of NPs have similar specific surface areas but very dif- E-mail: [email protected] ferent structural differences. Therefore, this study proposes an effective and simple method Tel: +82-54-279-6713 to identify structural differences in graphene-like allotropes. The adsorptive potential peaks of rGO-NP attained by the density functional theory method were found to be more scat- tered over the basal and non-basal regions than those of GIC-NP. Raman spectra and high resolution TEM images showed more distinctive crystallographic defects in the rGO-NP Open Access than in the GIC-NP. Because the R-ratio values of the edge and basal plane of the sample DOI: http://dx.doi.org/ were maintained and relatively similar in the rGO-NP (0.944 for edge & 1.026 for basal), DOI:10.5714/CL.2018.26.081 the discrepancy between those values in the GIC-NP were found to be much greater (0.918 This is an Open Access article distributed for edge & 0.164 for basal).