Corrosion of Zinc in the Automotive Environment
Total Page:16
File Type:pdf, Size:1020Kb
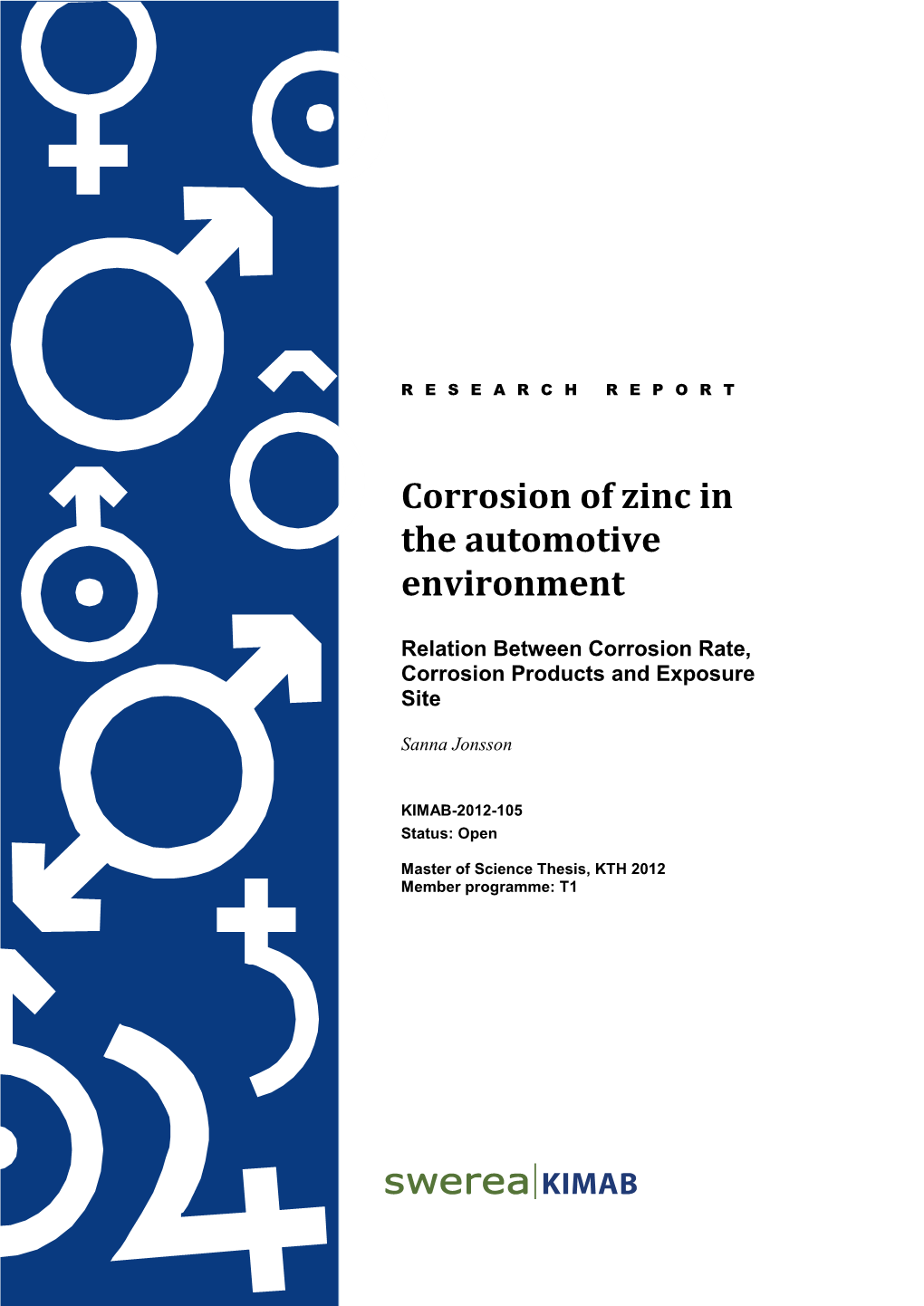
Load more
Recommended publications
-
Outside Diameter Initiated Stress Corrosion Cracking Revised Final White Paper", Developed by AREVA and Westinghouse Under PWROG Program PA-MSC-0474
Program Management Office PWROG 102 Addison Road Connecticut 06095 q .Windsor, ko'ners-- PA-MSC-0474 Project Number 694 October 14, 2010 OG-10-354 U.S. Nuclear Regulatory Commission Document Control Desk Washington, DC 20555-0001 Subject: PWR Owners Group For Information Only - Outside Diameter Initiated Stress Corrosion Crackin2 Revised Final White Paper, PA-MSC-0474 This letter transmits two (2) non-proprietary copies of PWROG document "Outside Diameter Initiated Stress Corrosion Cracking Revised Final White Paper", developed by AREVA and Westinghouse under PWROG program PA-MSC-0474. This document is being submitted for information only. No safety evaluation (SE) is expected and therefore, no review fees should be incurred. This white paper summarizes the recent occurrences of ODSCC of stainless steel piping identified at Callaway, Wolf Creek and SONGS. Available operating experience (OE) at units that have observed similar phenomena is summarized as well to give a better understanding of the issue. Each of the key factors that contribute to ODSCC was considered along with the reported operating experience to perform a preliminary assessment of areas that may be susceptible to ODSCC. Also a qualitative evaluation was performed to determine whether ODSCC of stainless steel piping represents an immediate safety concern. This white paper is meant to address the issue of ODSCC of stainless steel systems for the near term. I&E guidelines are currently being developed through the PWROG to provide long term guidance. Correspondence related to this transmittal should be addressed to: Mr. W. Anthony Nowinowski, Manager Owners Group, Program Management Office Westinghouse Electric Company 1000 Westinghouse Drive, Suite 380 Cranberry Township, PA 16066 U.S. -
Forms of Corrosion Uniform Corrosion
Chapter 4 Forms of corrosion Uniform corrosion In such type of corrosion there is a uniform decrease in the volume of the metal due to direct contact with the surrounding environment. Examples Dissolvation of Zn, Al metal in acids and Pb metal in base. Atmospheric corrosion Atmospheric corrosion take place due to direct contact between metal and atmosphere Types of atmosphere: Gas type: contain mainly oxygen gas( 23% W / W) and water vapor. Liquid type: contain mainly water and dissolved oxygen. iron rust Atmospheric corrosion involve formation of metal oxide layer when metal in direct contact with its surrounding environment. Example: Formation of iron rust due to contact with air Fe + air, H2O Fe(OH)2 Fe2O3 Fe2O3 .3H2O is Iron rust (reddish brown ppt.) Oxide layers Protective Non Protective Non active active Non porous porous Ex: Zn, Al, Ni Ex: iron rust Rate of atmospheric corrosion depends on Nature of metal or alloy. Nature of oxide layer. Factors affecting atmospheric corrosion: Type of metal or alloy. Type of atmosphere (dust, humidity, pollutant. Water vapor, gases,…) Temperature( as T increase as rate increase) Time: The extent of corrosion increases with increased time Surface Condition: more roughness, more corrosion The presence of foreign matter influence the speed of corrosion PLAY ACTIVE FIGURE Galvanic corrosion Take place due to the contact between bimetallic couple exposed to the same environment due to the potential difference. Mechanism of galvanic corrosion: For two different metals M1 and M2 when exposed to the same corrosive environment, if M1 is more active than M2 M1 M2 Anodic reaction: M M n+ + ne- (n=1, 2, 3, …) Anodic metal will be corroded. -
Introduction to Corrosion Your Friendly TSC Corrosion Staff
Introduction to Corrosion Your Friendly TSC Corrosion Staff: Daryl Little Ph.D. Materials Science & Engineering [email protected] 303-445-2384 Lee Sears Ph.D. Materials Science & Engineering [email protected] 303-445-2392 Jessica Torrey Ph.D. Materials Science & Engineering [email protected] 303-445-2376 Roger Turcotte, PE, CPS Materials Engineer [email protected] 303-445-2383 What is Corrosion? CORROSION IS DEFINED AS THE DETERIORATION OF A MATERIAL AND/OR ITS PROPERTIES CAUSED BY A REACTION WITH ITS ENVIRONMENT. Why is Corrosion a Major Concern? First and Most Important- Public Safety! • June 28, 1983: Mianus River Bridge, Greenwich, CT (TIME photo archive) • Northbound 3-lane section of I-95 bridge collapsed, killing 3 people • “Pin and Hanger” design was compromised when pin was displaced due to extensive corrosion of load-bearing components, amplified by salt from road maintenance. • Inadequate maintenance procedures were also cited as a contributing factor. • Subsequent to this failure, extensive inspections were conducted on this type of bridge across the country, and design modification were made to prevent catastrophic failures of this kind. First and Most Important- Public Safety! • April 28,1988, Aloha Airlines 737 Accident • 18 feet of cabin skin ripped off, resulting in the death of a flight attendant and many injuries • Attributed to corrosion fatigue Reclamation Case Study- Folsom Dam • Spillway gate No. 3 was damaged beyond repair, but no flooding occurred. • Replacement of No. 3 and repair of other gates cost ~$20 million and required 40% drainage of reservoir • Cause of failure: Increasing corrosion at the trunnion pin-hub interface raised the coefficient of friction and, therefore, the bending stress in the strut and the axial force in the brace exceeded limits. -
Of the Periodic Table
of the Periodic Table teacher notes Give your students a visual introduction to the families of the periodic table! This product includes eight mini- posters, one for each of the element families on the main group of the periodic table: Alkali Metals, Alkaline Earth Metals, Boron/Aluminum Group (Icosagens), Carbon Group (Crystallogens), Nitrogen Group (Pnictogens), Oxygen Group (Chalcogens), Halogens, and Noble Gases. The mini-posters give overview information about the family as well as a visual of where on the periodic table the family is located and a diagram of an atom of that family highlighting the number of valence electrons. Also included is the student packet, which is broken into the eight families and asks for specific information that students will find on the mini-posters. The students are also directed to color each family with a specific color on the blank graphic organizer at the end of their packet and they go to the fantastic interactive table at www.periodictable.com to learn even more about the elements in each family. Furthermore, there is a section for students to conduct their own research on the element of hydrogen, which does not belong to a family. When I use this activity, I print two of each mini-poster in color (pages 8 through 15 of this file), laminate them, and lay them on a big table. I have students work in partners to read about each family, one at a time, and complete that section of the student packet (pages 16 through 21 of this file). When they finish, they bring the mini-poster back to the table for another group to use. -
Stainless Steel Selection Guide
TAContentsBLE OF Discovery of Stainless Steel . .page 2 What is Stainless Steel . .page 3 Stainless Steel Classifications . .page 4 • Austenitic . .page 4 • Ferritic . .page 5 • Duplex . .page 5 • Martensitic . .page 6 • Precipitation Hardening . .page 6 Nickel Based Alloys . .page 7 Strength & Heat Treatment . .page 7 The Basics of Corrosion . .page 8 • General or Uniform Corrosion . .page 9 • Galvanic Corrosion . .page 11 • Pitting Corrosion . .page 11 • Crevice Corrosion . .page 13 • Intergranular Corrosion . .page 14 • Stress Corrosion Cracking . .page 15 • Microbiologically Influence Corrosion . .page 17 Welding Stainless Steel . .page 18 Alloy Selection . .page 22 Wrought Stainless Steel Composition . .page 24 Wrought Nickel Alloy Composition . .page 25 Stainless Steel and Nickel Alloy Filler Metal . .page 26 PR“It’sEF stainlessAC steel,E it shouldn’t rust” This is often the kind of statements heard from individuals when discussing a failure of process piping or equipment. This is also an indication of how little is actually understood about stainless steel and the applications where it is used. For years the food, beverage and pharmaceutical industries have used stainless steels in their process piping systems. Most of the time stainless steel components provide satisfactory results. Occasionally a catastrophic failure will occur. The purpose of the information contained within this document is to bring an understanding to stainless steel, it’s uses, and why it will fail under certain conditions. In the following pages we will discuss the different classes of stainless steel, heat treatment, corrosion, welding, and finally material selection. As with any failure, it is imperative the cause of the failure be identified before a proper fix can be recognized. -
The Corrosion of Iron and Its Alloys
UNIVERSITY OF ILLINOIS LIBRARY Class Book Volume ^ M rlO-20M -r - 4 'f . # f- f f > # 4 Tjh- |fe ^ lINlN^ ' ^ ^ ^* 4 if i i if i^M^'M^i^ H II I li H : : \ ; . tNP* i rHt . ; ^ * 41 W 4s T »f 4 ^ -f 4. f -4- * i 4 4 : * 1- 1 4 % 3**:- ->^> A 4- - 4- + * ,,4 * 4" T '* * 4 -f- ± f * * 4- 4 -i * 4 ^ 4* -f + > * * + 1 f * 4 # * .-j* * + * ^ £ - jjR ^^MKlF^ f ^ f- + f v * IT :/^rV :,HH':,* ^ 4 * ^ 4 -f- «f f 4- 4 4 ,,rSK|M| ; * 4 # ; || II I II II f || .- -fr 4* , «g* 4 I. ^ vmiM 4- THE CORROSION OF IRON AND ITS ALLOYS BY RUSSELL SAMUEL HOWARD THESIS FOR THE DEGREE OF BACHELOR OF SCIENCE IN CHEMISTRY IN THE COLLEGE OF SCIENCE OF THE UNIVERSITY OF ILLINOIS Presented June, 1910 UNIVERSITY OF ILLINOIS June 1 1910 THIS IS TO CERTIFY THAT THE THESIS PREPARED UNDER MY SUPERVISION BY Russel Samuel Howard ENTITLED The Corrosion of Iron and It s Alloys IS APPROVED BY ME AS FULFILLING THIS PART OF THE REQUIREMENTS FOR THE DEGREE OF Bachelor of Scienc e In Chemistry Instructor in Charge Approved: HEAD OF DEPARTMENT OF 167529 Digitized by the Internet Archive in 2013 ^ttp://archive.org/details/corrosionofironiOOhowa CORROSION OF IRON AND ITS ALLOYS. In nature everything is subject to deterioration, varying from those substances decomposed by light to those only decomposed by the strong- est agents. The deterioration of metals as effected by alloying is the sub- ject of this paper and perhaps .no subject is of more vital importance to the builder and interest to the chemist than this one of corrosion. -
INFLUENCE of Ph on the LOCALIZED CORROSION of IRON
BNL 39687 MIT/BNL-86-6 INFORMAL REPORT INFLUENCE OF pH ON THE LOCALIZED CORROSION OF IRON MIT/BNL-86-6 BNL—39687 DE87 010452 R. Webley and R. Henry Consultants: H. Isaacs and G. Cragnolino June 1986 BROOKHAVEN STATION SCHOOL OF CHEMICAL ENGINEERING PRACTICE MASSACHUSETTS INSTITUTE OF TECHNOLOGY R.O. SPROULL. DIRECTOR F.J. HRACH, ASSISTANT DIRECTOR DEPARTMENT OF APPLIED SCIENCE BROOKHAVEN NATIONAL LABORATORY ASSOCIATED UNIVERSITIES. INC. UPTON, LONG ISLAND, NEW YORK 11973 UNDER CONTRACT NO. DE-AC02-76CH00016 WITH THE UNITED STATES DEPARTMENT OF ENERGY MASTER DISTRIBUTION OF TMiS DOCUMENT IS UNLIMITED DISCLAIMER This report was prepared as an account of work sponsored by an agency of the United States Government. Neither the United States Government nor any agency thereof, nor any of their employees, nor any of their contractors, subcontrac- tors, or their employees, makes any warranty, express or implied, or assumes any legal liability or responsibility for the accuracy, completeness, or use- fulness of any information, apparatus, product, or process disclosed, or represents that its use would not infringe privately owned rights. Reference herein to any specific commercial product, process, or service by trade name, trademark, manufacturer, or otherwise, does not necessarily constitute or imply its endorsement, recommendation, or favoring by the United States Government or any agency, contractor or subcontractor thereof. The views and opinions of authors expressed herein do not necessarily state or reflect those of the United States Government or any agency, contractor or subcontractor thereof. ABSTRACT The influence of pH on the pitting corrosion of iron in chloride and sul- fate solutions was determined using two artificial pit apparatuses to obtain the pH near the surface of the pit bottom. -
Galvanic Corrosion
10 GALVANIC CORROSION X. G. ZHANG Teck Metals Ltd., Mississauga, Ontario, Canada A. Introduction graphite, are dispersed in a metal, or on a ship, where the B. Definition various components immersed in water are made of different C. Factors in galvanic corrosion metal alloys. In many cases, galvanic corrosion may result in D. Material factors quick deterioration of the metals but, in other cases, the D1. Effects of coupled materials galvanic corrosion of one metal may result in the corrosion D2. Effect of area protection of an attached metal, which is the basis of cathodic D3. Effect of surface condition protection by sacrificial anodes. E. Environmental factors Galvanic corrosion is an extensively investigated subject, E1. Effects of solution as shown in Table 10.1, and is qualitatively well understood E2. Atmospheric environments but, due to its highly complex nature, it has been difficult to E3. Natural waters deal with in a quantitative way until recently. The widespread F. Polarity reversal use of computers and the development of software have made G. Preventive measures great advances in understanding and predicting galvanic H. Beneficial effects of galvanic corrosion corrosion. I. Fundamental considerations I1. Electrode potential and Kirchhoff’s law I2. Analysis B. DEFINITION I3. Polarization and resistance I4. Potential and current distributions When two dissimilar conducting materials in electrical con- References tact with each other are exposed to an electrolyte, a current, called the galvanic current, flows from one to the other. Galvanic corrosion is that part of the corrosion that occurs at the anodic member of such a couple and is directly related to the galvanic current by Faraday’s law. -
Pitting Growth Rate in Carbon Steel Exposed to Simulated Radioactive Waste (U)
WSRC-TR-96-0024 Pitting Growth Rate in Carbon Steel Exposed to Simulated Radioactive Waste (U) by P. E. Zapp Westinghouse Savannah River Company Savannah River Site • Aiken, South Carolina 29808 DOE Contract No. DE-AC09-89SR18035 This paper was prepared in connection with work done under the above contract number with the U. S. Department of Energy. By acceptance of this paper, the publisher and/or recipient acknowledges the U. S. Government's right to retain a nonexclusive, royalty-free license in and to any copyright covering this paper, along with the right to reproduce and to authorize others to reproduce all or part of the copyrighted paper. DISTRIBUTION OF THIS DOCUMENT IS UNLIMITED DISCLAIMER Portions of this document may be illegible in electronic image products. Images are produced from the best available original document. DISCLAIMER This report was prepared as an account of work sponsored by an jagency of. the United States Government Neither the United States Government nor any agency thereof, nor any of their employees, makes any warranty, express or implied, or assumes any legal liability or •responsibility for the accuracy, completeness, or usefulness of any information, apparatus, product, or process disclosed, .or represents that its use would not infringe privately owned rights. Reference herein to any specific commercial product, process, or service by trade name, trademark, manufacturer, or otherwise does not necessarily constitute or imply its endorsement,, recommendation, or favoring by the United States Government or any agency thereof. The views and opinions of authors expressed herein do not necessarily state or reflect those of the United States Government or any agency thereof. -
In-Situ Monitoring and Analysis of the Pitting Corrosion of Carbon Steel by Acoustic Emission
applied sciences Article In-Situ Monitoring and Analysis of the Pitting Corrosion of Carbon Steel by Acoustic Emission Junlei Tang 1 , Junyang Li 2, Hu Wang 2,*, Yingying Wang 1 and Geng Chen 3 1 School of Chemistry and Chemical Engineering, Southwest Petroleum University, Chengdu 610500, China; [email protected] (J.T.); [email protected] (Y.W.) 2 School of Material Science and Engineering, Southwest Petroleum University, Chengdu 610500, China; [email protected] 3 CNOOC Energy Technology & Services-Shanghai Environmental Engineering & Technology Branch, Shanghai 200335, China; [email protected] * Correspondence: [email protected]; Tel.: +86-028-83037361 Received: 5 November 2018; Accepted: 8 February 2019; Published: 18 February 2019 Abstract: The acoustic emission (AE) technique was applied to monitor the pitting corrosion of carbon steel in NaHCO3 + NaCl solutions. The open circuit potential (OCP) measurement and corrosion morphology in-situ capturing using an optical microscope were conducted during AE monitoring. The corrosion micromorphology was characterized with a scanning electron microscope (SEM). The propagation behavior and AE features of natural pitting on carbon steel were investigated. After completion of the signal processing, including pre-treatment, shape preserving interpolation, and denoising, for raw AE waveforms, three types of AE signals were classified in the correlation diagrams of the new waveform parameters. Finally, a 2D pattern recognition method was established to calculate the similarity of different continuous AE graphics, which is quite effective to distinguish the localized corrosion from uniform corrosion. Keywords: carbon steel; pitting corrosion; acoustic emission; wavelets; pattern recognition 1. Introduction In the modern construction industry, carbon steel is widely used because of its low price and good mechanical properties. -
Brad A. James, Ph.D., P.E., FASM
Brad A. James, Ph.D., P.E., FASM Group Vice President & Principal Engineer | Materials & Corrosion Engineering 149 Commonwealth Drive | Menlo Park, CA 94025 (650) 688-7391 tel | [email protected] Professional Profile Dr. James specializes in failure analysis, failure prevention, and integrity assessment of engineering structures and components. His specific expertise includes metallurgy, materials science, fracture, fatigue, material degradation, corrosion, life prediction, and design. In his many years of engineering experience, Dr. James has conducted thousands of failure analysis investigations on widely varying engineering structures, ranging from miniscule medical devices to power- plant components. Dr. James also helps clients from various industries prevent failures, assess the integrity of their designs or equipment, as well as interact with governmental agencies. Dr. James has special interest in fractography, fracture mechanics, wear, corrosion, embrittlement phenomena, microstructural development, heat treatment, material selection, and welding and joining. The common thread in each of Dr. James' investigations is the application of metallurgical, materials science, and engineering mechanics fundamentals to help understand and solve complex problems. Dr. James has taught several graduate-level fracture mechanics and failure analysis courses at Stanford and Santa Clara Universities. He has also taught several courses for The American Society for Materials (ASM International) involving failure analysis, design, and life prediction/validation -
The Effects and Economic Impact of Corrosion
© 2000 ASM International. All Rights Reserved. www.asminternational.org Corrosion: Understanding the Basics (#06691G) CHAPTER 1 The Effects and Economic Impact of Corrosion CORROSION is a natural process. Just like water flows to the lowest level, all natural processes tend toward the lowest possible energy states. Thus, for example, iron and steel have a natural tendency to com- bine with other chemical elements to return to their lowest energy states. In order to return to lower energy states, iron and steel frequently combine with oxygen and water, both of which are present in most natu- ral environments, to form hydrated iron oxides (rust), similar in chemi- cal composition to the original iron ore. Figure 1 illustrates the corro- sion life cycle of a steel product. Finished Steel Product Air & Moisture Corrode Steel & Form Smelting & Rust Refining Adding Giving Up Energy Energy Mining Ore Iron Oxide (Ore & Rust) Fig. 1 The corrosion cycle of steel © 2000 ASM International. All Rights Reserved. www.asminternational.org Corrosion: Understanding the Basics (#06691G) 2 Corrosion: Understanding the Basics The Definition of Corrosion Corrosion can be defined in many ways. Some definitions are very narrow and deal with a specific form of corrosion, while others are quite broad and cover many forms of deterioration. The word corrode is de- rived from the Latin corrodere, which means “to gnaw to pieces.” The general definition of corrode is to eat into or wear away gradually, as if by gnawing. For purposes here, corrosion can be defined as a chemical or electrochemical reaction between a material, usually a metal, and its environment that produces a deterioration of the material and its proper- ties.