A Simple Motion-Planning Algorithm for General Robot Manipulators
Total Page:16
File Type:pdf, Size:1020Kb
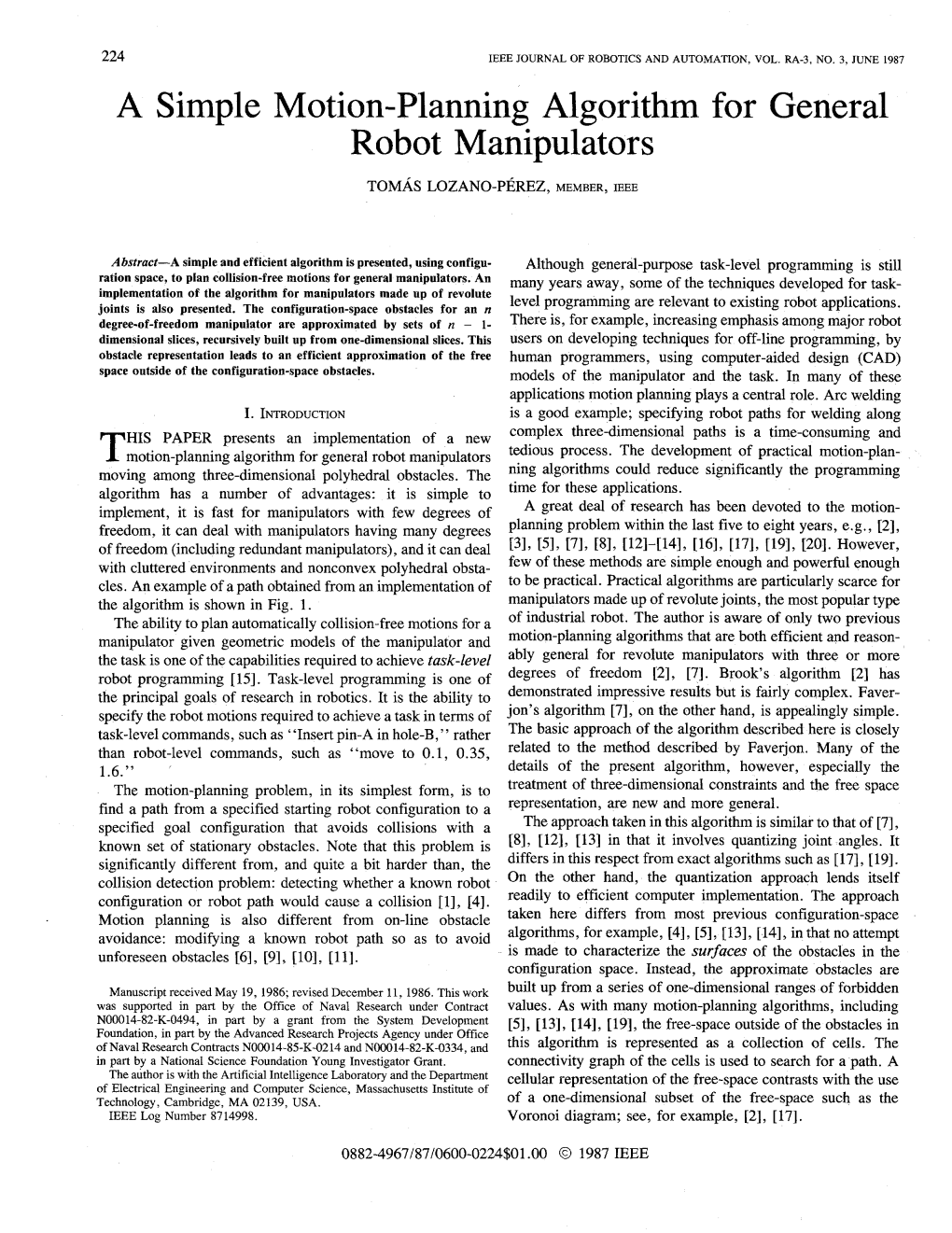
Load more
Recommended publications
-
Lazy Theta*: Any-Angle Path Planning and Path Length Analysis in 3D
Proceedings of the Twenty-Fourth AAAI Conference on Artificial Intelligence (AAAI-10) Lazy Theta*: Any-Angle Path Planning and Path Length Analysis in 3D Alex Nash∗ and Sven Koenig Craig Tovey Computer Science Department School of Industrial and Systems Engineering University of Southern California Georgia Institute of Technology Los Angeles, CA 90089-0781, USA Atlanta, GA 30332-0205, USA fanash,[email protected] [email protected] Abstract Grids with blocked and unblocked cells are often used to rep- resent continuous 2D and 3D environments in robotics and video games. The shortest paths formed by the edges of 8- neighbor 2D grids can be up to ≈ 8% longer than the short- est paths in the continuous environment. Theta* typically finds much shorter paths than that by propagating informa- tion along graph edges (to achieve short runtimes) without constraining paths to be formed by graph edges (to find short “any-angle” paths). We show in this paper that the short- Figure 1: NavMesh: Shortest Path Formed by Graph Edges est paths formed by the edges of 26-neighbor 3D grids can (left) vs. Truly Shortest Path (right), adapted from (Patel be ≈ 13% longer than the shortest paths in the continuous 2000) environment, which highlights the need for smart path plan- ning algorithms in 3D. Theta* can be applied to 3D grids in a straight-forward manner, but it performs a line-of-sight (square grids), hexagons or triangles; regular 3D grids com- check for each unexpanded visible neighbor of each expanded posed of cubes (cubic grids); visibility graphs; waypoint vertex and thus it performs many more line-of-sight checks graphs; circle based waypoint graphs; space filling volumes; per expanded vertex on a 26-neighbor 3D grid than on an navigation meshes (NavMeshes, tessellations of the contin- 8-neighbor 2D grid. -
Automated Motion Planning for Robotic Assembly of Discrete Architectural Structures by Yijiang Huang B.S
Automated Motion Planning for Robotic Assembly of Discrete Architectural Structures by Yijiang Huang B.S. Mathematics, University of Science and Technology of China (2016) Submitted to the Department of Architecture in partial fulfillment of the requirements for the degree of Master of Science in Building Technology at the MASSACHUSETTS INSTITUTE OF TECHNOLOGY June 2018 ©Yijiang Huang, 2018. All rights reserved. The author hereby grants to MIT permission to reproduce and to distribute publicly paper and electronic copies of this thesis document in whole or in part in any medium now known or hereafter created. Author................................................................ Department of Architecture May 24, 2018 Certified by. Caitlin T. Mueller Associate Professor of Architecture and Civil and Environmental Engineering Thesis Supervisor Accepted by........................................................... Sheila Kennedy Professor of Architecture, Chair of the Department Committee on Graduate Students 2 Automated Motion Planning for Robotic Assembly of Discrete Architectural Structures by Yijiang Huang Submitted to the Department of Architecture on May 24, 2018, in partial fulfillment of the requirements for the degree of Master of Science in Building Technology Abstract Architectural robotics has proven a promising technique for assembling non-standard configurations of building components at the scale of the built environment, com- plementing the earlier revolution in generative digital design. However, despite the advantages -
A Heuristic Search Based Algorithm for Motion Planning with Temporal Goals
T* : A Heuristic Search Based Algorithm for Motion Planning with Temporal Goals Danish Khalidi1, Dhaval Gujarathi2 and Indranil Saha3 Abstract— Motion planning is one of the core problems to A number of algorithms exist for solving Linear Temporal solve for developing any application involving an autonomous logic (LTL) motion planning problems in different settings. mobile robot. The fundamental motion planning problem in- For an exhaustive review on this topics, the readers are volves generating a trajectory for a robot for point-to-point navigation while avoiding obstacles. Heuristic-based search directed to the survey by Plaku and Karaman [18]. In case of algorithms like A* have been shown to be efficient in solving robots with continuous state space, we resort to algorithms such planning problems. Recently, there has been an increased that do not focus on optimality of the path, rather they focus interest in specifying complex motion plans using temporal on reducing the computation time to find a path. For example, logic. In the state-of-the-art algorithm, the temporal logic sampling based LTL motion planning algorithms compute a motion planning problem is reduced to a graph search problem and Dijkstra’s shortest path algorithm is used to compute the trajectory in continuous state space efficiently, but without optimal trajectory satisfying the specification. any guarantee on optimality (e.g [19], [20], [21]). On the The A* algorithm when used with an appropriate heuristic other hand, the LTL motion planning problem where the for the distance from the destination can generate an optimal dynamics of the robot is given in the form of a discrete transi- path in a graph more efficiently than Dijkstra’s shortest path tion system can be solved to find an optimal trajectory for the algorithm. -
Robot Motion Planning in Dynamic, Uncertain Environments Noel E
1 Robot Motion Planning in Dynamic, Uncertain Environments Noel E. Du Toit, Member, IEEE, and Joel W. Burdick, Member, IEEE, Abstract—This paper presents a strategy for planning robot Previously proposed motion planning frameworks handle motions in dynamic, uncertain environments (DUEs). Successful only specific subsets of the DUE problem. Classical motion and efficient robot operation in such environments requires planning algorithms [4] mostly ignore uncertainty when plan- reasoning about the future evolution and uncertainties of the states of the moving agents and obstacles. A novel procedure ning. When the future locations of moving agents are known, to account for future information gathering (and the quality of the two common approaches are to add a time-dimension that information) in the planning process is presented. To ap- to the configuration space, or to separate the spatial and proximately solve the Stochastic Dynamic Programming problem temporal planning problems [4]. When the future locations are associated with DUE planning, we present a Partially Closed-loop unknown, the planning problem is solved locally [5]–[7] (via Receding Horizon Control algorithm whose solution integrates prediction, estimation, and planning while also accounting for reactive planners), or in conjunction with a global planner that chance constraints that arise from the uncertain locations of guides the robot towards a goal [4], [7]–[9]. The Probabilistic the robot and obstacles. Simulation results in simple static and Velocity Obstacle approach [10] extends the local planner to dynamic scenarios illustrate the benefit of the algorithm over uncertain environments, but it is not clear how the method can classical approaches. The approach is also applied to more com- be extended to capture more complicated agent behaviors (a plicated scenarios, including agents with complex, multimodal behaviors, basic robot-agent interaction, and agent information constant velocity agent model is used). -
Sampling-Based Methods for Motion Planning with Constraints
Accepted for publication in Annual Review of Control, Robotics, and Autonomous Systems, 2018 http://www.annualreviews.org/journal/control Sampling-Based Methods for Motion Planning with Constraints Zachary Kingston,1 Mark Moll,1 and Lydia E. Kavraki1 1 Department of Computer Science, Rice University, Houston, Texas, ; email: {zak, mmoll, kavraki}@rice.edu Xxxx. Xxx. Xxx. Xxx. YYYY. AA:– Keywords https://doi.org/./((please add article robotics, robot motion planning, sampling-based planning, doi)) constraints, planning with constraints, planning for Copyright © YYYY by Annual Reviews. high-dimensional robotic systems All rights reserved Abstract Robots with many degrees of freedom (e.g., humanoid robots and mobile manipulators) have increasingly been employed to ac- complish realistic tasks in domains such as disaster relief, space- craft logistics, and home caretaking. Finding feasible motions for these robots autonomously is essential for their operation. Sampling-based motion planning algorithms have been shown to be effective for these high-dimensional systems. However, incor- porating task constraints (e.g., keeping a cup level, writing on a board) into the planning process introduces significant challenges. This survey describes the families of methods for sampling-based planning with constraints and places them on a spectrum delin- eated by their complexity. Constrained sampling-based meth- ods are based upon two core primitive operations: () sampling constraint-satisfying configurations and () generating constraint- satisfying continuous motion. Although the basics of sampling- based planning are presented for contextual background, the sur- vey focuses on the representation of constraints and sampling- based planners that incorporate constraints. Contents 1. INTRODUCTION......................................................................................... 2 2. MOTION PLANNING AND CONSTRAINTS............................................................ 5 2.1. -
ANY-ANGLE PATH PLANNING by Alex Nash a Dissertation Presented
ANY-ANGLE PATH PLANNING by Alex Nash A Dissertation Presented to the FACULTY OF THE USC GRADUATE SCHOOL UNIVERSITY OF SOUTHERN CALIFORNIA In Partial Fulfillment of the Requirements for the Degree DOCTOR OF PHILOSOPHY (COMPUTER SCIENCE) August 2012 Copyright 2012 Alex Nash Table of Contents List of Tables vii List of Figures ix Abstract xii Chapter 1: Introduction 1 1.1 PathPlanning .................................... 2 1.1.1 The Generate-Graph Problem . 3 1.1.2 Notation and Definitions . 4 1.1.3 TheFind-PathProblem. 5 1.2 Hypotheses and Contributions . ..... 12 1.2.1 Hypothesis1 ................................ 12 1.2.2 Hypothesis2 ................................ 12 1.2.2.1 Basic Theta*: Any-Angle Path Planning in Known 2D Envi- ronments............................. 14 1.2.2.2 Lazy Theta*: Any-Angle Path Planning in Known 3D Envi- ronments............................. 14 1.2.2.3 Incremental Phi*: Any-Angle Path Planning in Unknown 2D Environments .......................... 15 1.3 Dissertation Structure . ..... 17 Chapter 2: Path Planning 18 2.1 Navigation...................................... 18 2.2 PathPlanning .................................... 19 2.2.1 The Generate-Graph Problem . 20 2.2.1.1 Skeletonization Techniques . 21 2.2.1.2 Cell Decomposition Techniques . 27 2.2.1.3 Hierarchical Generate-Graph Techniques . 34 2.2.1.4 The Generate-Graph Problem in Unknown 2D Environments . 35 2.2.2 TheFind-PathProblem. 39 2.2.2.1 Single-Shot Find-Path Algorithms . 39 2.2.2.2 Incremental Find-Path Algorithms . 43 2.2.3 Post-Processing Techniques . 46 2.2.4 Existing Any-Angle Find-Path Algorithms . ...... 48 ii 2.3 Conclusions..................................... 50 Chapter 3: Path Length Analysis on Regular Grids (Contribution 1) 52 3.1 Introduction................................... -
Motion Planning Using Sequential Simplifications
Rapidly-Exploring Quotient-Space Trees: Motion Planning using Sequential Simplifications Andreas Orthey and Marc Toussaint University of Stuttgart, Germany fandreas.orthey, [email protected] Abstract. Motion planning problems can be simplified by admissible projections of the configuration space to sequences of lower-dimensional quotient-spaces, called sequential simplifications. To exploit sequential simplifications, we present the Quotient-space Rapidly-exploring Ran- dom Trees (QRRT) algorithm. QRRT takes as input a start and a goal configuration, and a sequence of quotient-spaces. The algorithm grows trees on the quotient-spaces both sequentially and simultaneously to guarantee a dense coverage. QRRT is shown to be (1) probabilistically complete, and (2) can reduce the runtime by at least one order of mag- nitude. However, we show in experiments that the runtime varies sub- stantially between different quotient-space sequences. To find out why, we perform an additional experiment, showing that the more narrow an environment, the more a quotient-space sequence can reduce runtime. 1 Introduction Motion planning algorithms are fundamental for robotic applications like man- ufacturing, object disassembly, tele-operation or space exploration [8]. Given an environment and a robot, a motion planning algorithm aims to find a feasible configuration space path from a start to a goal configuration. The complexity of a planning algorithm scales with the degrees-of-freedom (dofs) of the robot, and for high-dof robots the runtime can be prohibitive. To reduce the runtime of planning algorithms, prior work has shown that it is effective to consider certain simplifications of the planning problem, such as progressive relaxations [4], iterative constraint relaxations [2], lower-dimensional projections [20], possibility graphs [6] or quotient space sequences [11]. -
A Case-Based Approach to Robot Motion Planning
A Case-Based Approach to Robot Motion Planning Sandeep Pandya Seth Hutchinson The Beckman Institute for Advanced Science and Technology Department of Electrical and Computer Engineering University of Illinois at Urbana-Champaign Urbana,IL 61801 Abstract by building a case library of successful experiences, we We prerent a Care-Based robot motion planning syr- eliminate the need for a comprehensive domain theory tem. Case-Based Planning affords our ryrtem good 011- composed of rules that are capable of geometric rea- erage care performance by allowing it to underrtand and soning, plan construction, plan repair, etc.. The end ezploit the tradeoff between completenear and computa- result of this learning process is a knowledge base of so- tional wst, and permita it to ruccesrfurly plan and learn lutions to problems that we have encountered and may in a wmplez domain without the need for an eztenrively encounter again. engineered and porribly incomplete domain theom. Geometric approaches to robot motion planning have received much attention in the robotics community. 1 Introduction There are basically three approaches to geometric mo- tion planning: heuristic methods (e.g. artificial po- One goal of research in Artificial Intelligence is the tential fields methods [lo, 1, 9, 11, 22]), approximate creation of autonomous agents, capable of functioning methods (e.g. approximate cell decomposition methods successfully in dynamic and/or unpredictable environ- [6,23,2,17]),and exact methods (e.g. methods based on ments. Any such agent will require the ability to ma- cylindrical algebraic decompositions [21], or "roadmap" neuver effectively in its environment; this problem is methods [4]). -
Robot Motion Planning on a Chip
Robot Motion Planning on a Chip Sean Murray, Will Floyd-Jones∗, Ying Qi∗, Daniel Sorin and George Konidaris Duke Robotics Departments of Computer Science and Electrical & Computer Engineering Duke University, Durham NC 27708 Abstract—We describe a process that constructs robot-specific implement our circuits on a field-programmable gate array circuitry for motion planning, capable of generating motion plans (FPGA), which is able to find plans for the Jaco-2 6-degree- approximately three orders of magnitude faster than existing of-freedom arm in less than 1 millisecondy. methods. Our method is based on building collision detection circuits for a probabilistic roadmap. Collision detection for the roadmap edges is completely parallelized, so that the time to II. BACKGROUND determine which edges are in collision is independent of the We can describe the pose of an articulated robot—one number of edges. We demonstrate planning using a 6-degree- consisting of a set of rigid bodies connected by joints— of-freedom robot arm in less than 1 millisecond. by assigning positions to all of its joints. The space of all I. INTRODUCTION such joint positions is called the robot’s configuration space (often called C-space) [19], denoted Q. Some configurations Recent advances in robotics have the potential to dramati- would result in a collision with an obstacle in the robot’s cally change the way we live. Robots are being developed for a environment, a description of which is assumed to be given wide spectrum of real-world applications including health care, before planning commences, or the robot’s own body; the personal assistance, general-purpose manufacturing, search- remainder of Q is called free space. -
A Search Algorithm for Motion Planning with Six Degrees of Freedom*
ARTIFICIAL INTELLIGENCE 295 A Search Algorithm for Motion Planning with Six Degrees of Freedom* Bruce R. Donald Artificial Intelligence Laboratory, Massachusetts Institute of Technology, Cambridge, MA 02139, U.S.A. Recommended by H.H. Nagel and Daniel G. Bobrow ABSTRACT The motion planning problem is of central importance to the fields of robotics, spatial planning, and automated design. In robotics we are interested in the automatic synthesis of robot motions, given high-level specifications of tasks and geometric models of the robot and obstacles. The "Movers' "' problem is to find a continuous, collision-free path for a moving object through an environment containing obstacles. We present an implemented algorithm for the classical formulation of the three-dimensional Movers' problem: Given an arbitrary rigid polyhedral moving object P with three translational and three rotational degrees of freedom, find a continuous, collision-free path taking P from some initial configuration to a desired goal configuration. This paper describes an implementation of a complete algorithm (at a given resolution)for the full six degree of freedom Movers' problem. The algorithm transforms the six degree of freedom planning problem into a point navigation problem in a six-dimensional configuration space (called C-space). The C-space obstacles, which characterize the physically unachievable configurations, are directly represented by six-dimensional manifolds whose boundaries are five-dimensional C-surfaces. By characterizing these surfaces and their intersections, collision-free paths may be found by the closure of three operators which ( i) slide along five-dimensional level C-surfaces parallel to C-space obstacles; (ii) slide along one- to four-dimensional intersections of level C-surfaces; and (iii) jump between six-dimensional obstacles. -
A Comparison of Local Path Planning Techniques of Autonomous Surface Vehicles for Monitoring Applications: the Ypacarai Lake Case-Study
sensors Article A Comparison of Local Path Planning Techniques of Autonomous Surface Vehicles for Monitoring Applications: The Ypacarai Lake Case-study Federico Peralta 1 , Mario Arzamendia 1 , Derlis Gregor 1, Daniel G. Reina 2 and Sergio Toral 2,* 1 Facultad de Ingeniería, Universidad Nacional de Asunción, 2160 San Lorenzo, Paraguay; [email protected] (F.P.); [email protected] (M.A.); [email protected] (D.G.) 2 Universidad de Sevilla, 41004 Sevilla, Espana; [email protected] * Correspondence: [email protected] Received: 23 January 2020; Accepted: 7 March 2020; Published: 9 March 2020 Abstract: Local path planning is important in the development of autonomous vehicles since it allows a vehicle to adapt their movements to dynamic environments, for instance, when obstacles are detected. This work presents an evaluation of the performance of different local path planning techniques for an Autonomous Surface Vehicle, using a custom-made simulator based on the open-source Robotarium framework. The conducted simulations allow to verify, compare and visualize the solutions of the different techniques. The selected techniques for evaluation include A*, Potential Fields (PF), Rapidly-Exploring Random Trees* (RRT*) and variations of the Fast Marching Method (FMM), along with a proposed new method called Updating the Fast Marching Square method (uFMS). The evaluation proposed in this work includes ways to summarize time and safety measures for local path planning techniques. The results in a Lake environment present the advantages and disadvantages of using each technique. The proposed uFMS and A* have been shown to achieve interesting performance in terms of processing time, distance travelled and security levels. -
Autonomous Exploration and Motion Planning for an Unmanned Aerial Vehicle Navigating Rivers
Autonomous Exploration and Motion Planning for an Unmanned Aerial Vehicle Navigating Rivers •••••••••••••••••••••••••••••••••••• Stephen Nuske, Sanjiban Choudhury, Sezal Jain, Andrew Chambers, Luke Yoder, and Sebastian Scherer Robotics Institute, Carnegie Mellon University, Pittsburgh, Pennsylvania 15213 Lyle Chamberlain and Hugh Cover Near Earth Autonomy, Inc., Pittsburgh, Pennsylvania 15237-1523 Sanjiv Singh Robotics Institute, Carnegie Mellon University and Near Earth Autonomy, Inc., Pittsburgh, Pennsylvania 15237-1523 Received 12 July 2014; accepted 16 February 2015 Mapping a river’s geometry provides valuable information to help understand the topology and health of an environment and deduce other attributes such as which types of surface vessels could traverse the river. While many rivers can be mapped from satellite imagery, smaller rivers that pass through dense vegetation are occluded. We develop a micro air vehicle (MAV) that operates beneath the tree line, detects and maps the river, and plans paths around three-dimensional (3D) obstacles (such as overhanging tree branches) to navigate rivers purely with onboard sensing, with no GPS and no prior map. We present the two enabling algorithms for exploration and for 3D motion planning. We extract high-level goal-points using a novel exploration algorithm that uses multiple layers of information to maximize the length of the river that is explored during a mission. We also present an efficient modification to the SPARTAN (Sparse Tangential Network) algorithm called SPARTAN- lite, which exploits geodesic properties on smooth manifolds of a tangential surface around obstacles to plan rapidly through free space. Using limited onboard resources, the exploration and planning algorithms together compute trajectories through complex unstructured and unknown terrain, a capability rarely demonstrated by flying vehicles operating over rivers or over ground.