Design and Fabrication of Chemiresistor Typemicro/Nano Hydrogen Gas Sensors Usinginterdigitated Electrodes
Total Page:16
File Type:pdf, Size:1020Kb
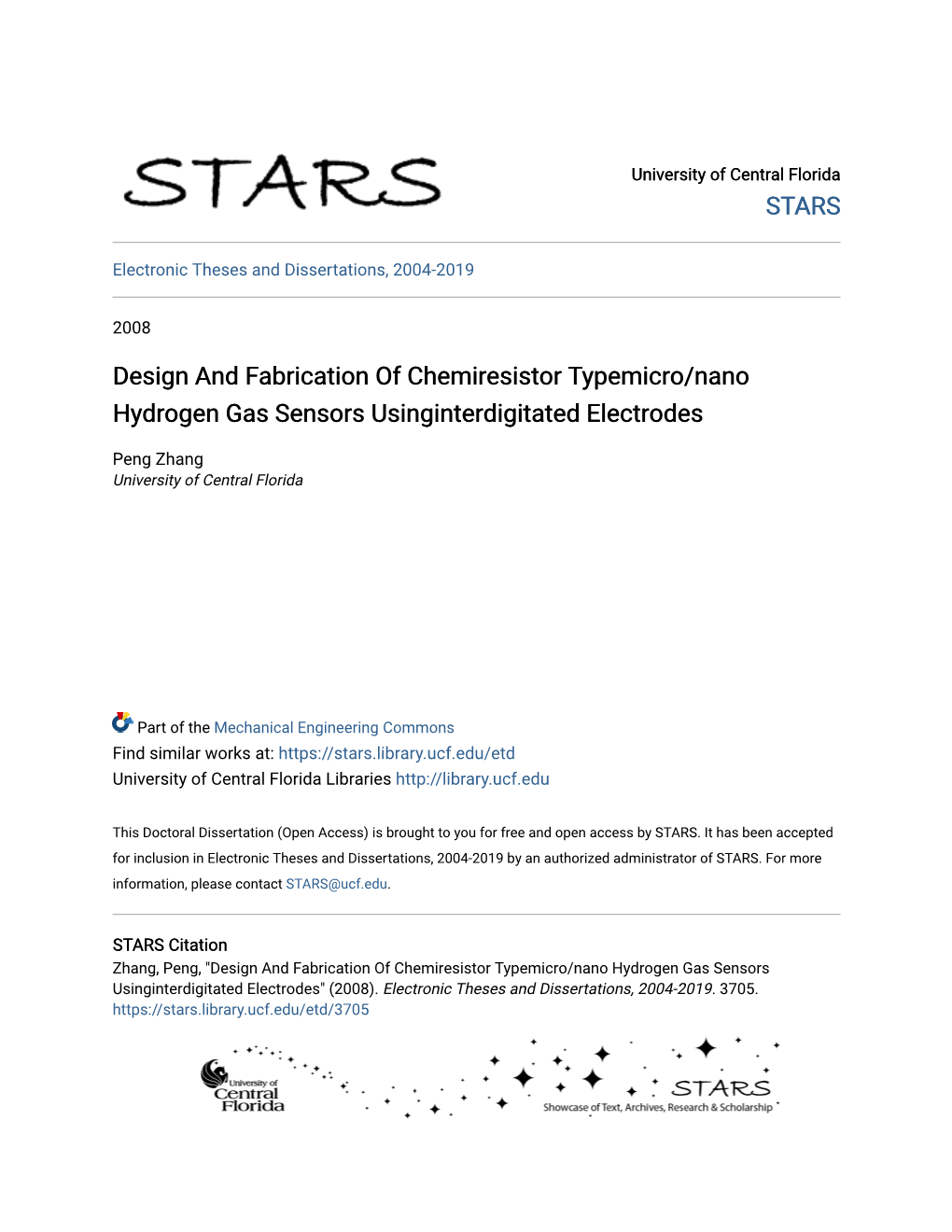
Load more
Recommended publications
-
Gas Detection Products Ammonia & Other Gases
Gas Detection Products Ammonia & Other Gases Product Catalog 2021 Table of Contents Price List .......................................................................................................................................................................................... 4-31 Controllers ....................................................................................................................................................................................... 32-39 GG-6 ....................................................................................................................................................................................... 32-33 GG-6 Remote Display ........................................................................................................................................................... 34-35 GG-2 ....................................................................................................................................................................................... 36-37 EM2 Entrance Monitor ......................................................................................................................................................... 38-39 Ammonia Sensors ............................................................................................................................................................................. 40-49 GG-NH3 ................................................................................................................................................................................. -
Highly Sensitive and Selective Chemiresistor Gas/Vapor Sensors Based on Polyaniline Nanocomposite: a Comprehensive Review
Accepted Manuscript Highly Sensitive and Selective Chemiresistor Gas/Vapor Sensors based on Polyaniline Nanocomposite: A comprehensive review Sadanand Pandey PII: S2468-2179(16)30163-0 DOI: 10.1016/j.jsamd.2016.10.005 Reference: JSAMD 67 To appear in: Journal of Science: Advanced Materials and Devices Received Date: 17 September 2016 Revised Date: 11 October 2016 Accepted Date: 12 October 2016 Please cite this article as: S. Pandey, Highly Sensitive and Selective Chemiresistor Gas/Vapor Sensors based on Polyaniline Nanocomposite: A comprehensive review, Journal of Science: Advanced Materials and Devices (2016), doi: 10.1016/j.jsamd.2016.10.005. This is a PDF file of an unedited manuscript that has been accepted for publication. As a service to our customers we are providing this early version of the manuscript. The manuscript will undergo copyediting, typesetting, and review of the resulting proof before it is published in its final form. Please note that during the production process errors may be discovered which could affect the content, and all legal disclaimers that apply to the journal pertain. ACCEPTED MANUSCRIPT Highly Sensitive and Selective Chemiresistor Gas/Vapor Sensors based on Polyaniline Nanocomposite: A comprehensive review Sadanand Pandey a,b * aDepartment of Applied chemistry, University of Johannesburg, P.O. Box 17011, Doornfontien 2028, Johannesburg, Republic of South Africa (RSA) bCentre for Nanomaterials Science Research, University of Johannesburg, Republic of South Africa (RSA) ABSTRACT This current review pays particular attention to some current breakthrough develop in the area of gas sensors based on polyaniline (PANI) nanocomposite. Conducting polymers symbolize a paramount class of organic materials with boost the resistivity towards external stimuli. -
Modeling of Vapor Sorption in Nanoparticle Chemiresistors Alexandra Oliveira [email protected]
University of Connecticut OpenCommons@UConn Honors Scholar Theses Honors Scholar Program Spring 5-16-2019 Modeling of Vapor Sorption in Nanoparticle Chemiresistors Alexandra Oliveira [email protected] Follow this and additional works at: https://opencommons.uconn.edu/srhonors_theses Part of the Other Chemical Engineering Commons, and the Semiconductor and Optical Materials Commons Recommended Citation Oliveira, Alexandra, "Modeling of Vapor Sorption in Nanoparticle Chemiresistors" (2019). Honors Scholar Theses. 610. https://opencommons.uconn.edu/srhonors_theses/610 Modeling of Vapor Sorption in Nanoparticle Chemiresistors Alexandra Oliveira, Dr. Brian G. Willis Department of Chemical and Biomolecular Engineering University of Connecticut Table of Contents Abstract .......................................................................................................................................... 3 1. Introduction ............................................................................................................................... 3 2. Objective .................................................................................................................................... 4 3. Theory ........................................................................................................................................ 6 A. AuNP Sensor Fabrication ..................................................................................................................... 6 B. Volumetric Expansion of Organic Ligands -
A Chemiresistor Sensor Array for Insect Infestation Detection By
A Chemiresistor Sensor Array for Insect Infestation Detection by Kanchana Anuruddika Kumari Weerakoon A dissertation submitted to the Graduate Faculty of Auburn University in partial fulfillment of the requirements for the Degree of Doctor of Philosophy Auburn, Alabama May 7th , 2012 Key words: Polythiophene sensor Polyaniline sensor, Polymer/carbon composite sensor, Sensor array, insect infestation, Thin film sensor array Copyright 2012 by Kanchana Anuruddika Kumari Weerakoon Approved by Bryan A. Chin, Chair, Professor of Materials Engineering Minseo Park, Associate Professor of Physics Dong Joo (Daniel) Kim, Associate Professor of Materials Engineering Zhong Yang Cheng, Associate Professor of Materials Engineering Abstract Plants emit volatile organic compounds as a defensive mechanism to protect themselves from insects and pathogens. These volatile organic chemicals, also known as phytochemicals, are given off during the early stages of insect infestation and may be detected using a chemical sensor array. The chemiresistor sensor array, investigated in this study, consists of a silicon substrate, electroactive polymer based active layer and microelectronically fabricated interdigitated electrodes. The sensor array is inexpensive, easy to fabricate, and could be used for onsite detection of insect infestation. Compared to traditional methods of detecting insect infestation such as leaf inspection and insect traps, this method is quick, inexpensive and would not require trained personal. The sensor array investigated in this dissertation uses three types of polymers as active sensing layers; polythiophene, carbon/polymer and polyaniline. The polymer coatings were deposited onto the sensor platforms via drop casting and spin coating methods. The sensor array was exposed and found to be sensitive to a variety of phytochemicals including γ-terpinene, α- pinene, p-cymene, farnesene, limonene, and cis-hexenyl acetate. -
Testing the Performance of Hydrogen Sensors
Testing the Performance of Hydrogen Sensors Nathan D. Marsh National Institute of Standards and Technology, Gaithersburg, MD USA Thomas G. Cleary National Institute of Standards and Technology, Gaithersburg, MD USA Abstract The acceptance of hydrogen as a widely-available energy source will depend to some extent on the perceived and actual safe dispensing and storage of hydrogen by the general public. Reliable detection of an accidental hydrogen gas release and mitigation of the hazard through designed safety systems is a key component of hydrogen powered systems in commercial, residential, and transportation uses. In anticipation of this emerging market, inexpensive hydrogen gas sensors based on a range of sensing technologies are becoming increasingly available. We have developed a new bench-scale test apparatus for hydrogen sensor performance, the Hydrogen Detector Environment Evaluator (HyDEE), based on our previous experience with hydrogen sensors in a small flow cell and in the Fire Emulator / Detector Evaluator. In particular, we have found that dynamic changes are relevant to hydrogen sensor performance, as they affect both response rate of the sensor and are also necessary to return the sensor environment to its baseline state. The ability to induce dynamic changes is most easily accomplished with a flow system similar to a small wind tunnel. In this system, we can expose sensors to hydrogen and other gases (particularly hydrocarbons, which many hydrogen sensors are also sensitive to) as well as humidity and changes in temperature. Improvements over the previous exploratory tests include substantially reduced volume allowing higher gas concentrations, and the ability to cool the system as well as heat it, in order to achieve a wider dynamic range in temperature and to more accurately simulate the environments to which sensors may be exposed in the real world. -
Highly Sensitive and Selective Chemiresistor Gas/Vapor Sensors Based on Polyaniline Nanocomposite: a Comprehensive Review
Journal of Science: Advanced Materials and Devices 1 (2016) 431e453 Contents lists available at ScienceDirect Journal of Science: Advanced Materials and Devices journal homepage: www.elsevier.com/locate/jsamd Review Article Highly sensitive and selective chemiresistor gas/vapor sensors based on polyaniline nanocomposite: A comprehensive review * Sadanand Pandey a, b, a Department of Applied Chemistry, University of Johannesburg, P.O. Box 17011, Doornfontien 2028, Johannesburg, South Africa b Centre for Nanomaterials Science Research, University of Johannesburg, South Africa article info abstract Article history: This review article directs particular attention to some current breakthrough developments in the area of Received 17 September 2016 gas sensors based on polyaniline (PANI) nanocomposite. Conducting polymers symbolize a paramount Received in revised form class of organic materials that boost the resistivity towards external stimuli. Nevertheless, PANI-based 11 October 2016 sensor experiences some disadvantages of relatively low reproducibility, selectivity, and stability. In Accepted 12 October 2016 order to overcome these restrictions, PANI was functionalised or incorporated with nanoparticles (NPs) Available online 18 October 2016 (metallic or bimetallic NPs, metal oxide NPs), carbon compounds (like CNT or graphene, chalcogenides, polymers), showing improved gas sensing characteristics. It has been suggested that hosteguest Keywords: Gas sensors chemistry combined with the utilization of organic and inorganic analog in nanocomposite may allow for Polyaniline improvement of the sensor performance due to synergetic/complementary effects. Herein, we summa- Sensitivity rize recent advantages in PANI nanocomposite preparation, sensor construction, and sensing properties Chemiresistive response of various PANI nanocomposite-based gas/vapor sensors, such as NH3,H2, HCl, NO2,H2S, CO, CO2,SO2, Metal oxide nanoparticles LPG, vapor of volatile organic compounds (VOCs) as well as chemical warfare agents (CWAs). -
Two-Dimensional Chemiresistive Covalent Organic Framework with 8 High Intrinsic Conductivity 9 10 Zheng Meng,1 Robert M
Page 1 of 11 Journal of the American Chemical Society 1 2 3 4 5 6 7 Two-Dimensional Chemiresistive Covalent Organic Framework with 8 High Intrinsic Conductivity 9 10 Zheng Meng,1 Robert M. Stolz,1 Katherine A. Mirica*1 11 12 1Department of Chemistry, Burke Laboratory, Dartmouth College, Hanover, New Hampshire, 03755 13 14 15 16 Supporting Information Placeholder 17 18 ABSTRACT: This paper describes the synthesis of a novel intrinsically conductive two-dimensional (2D) covalent organic 19 framework (COF) through the aromatic annulation of 2,3,9,10,16,17,23,24-octa-aminophthalocyanine nickel(II) and pyrene- 20 4,5,9,10-tetraone. The intrinsic bulk conductivity of the COF material (termed COF-DC-8) reached 2.5110-3 S/m, and increased 21 by three orders of magnitude with I2 doping. Electronic calculations revealed an anisotropic band structure, with the possibility 22 for significant contribution from out-of-plane charge-transport to the intrinsic bulk conductivity. Upon integration into 23 chemiresistive devices, this conductive COF showed excellent responses to various reducing and oxidizing gases, including NH3, 24 H2S, NO, and NO2, with parts-per-billion (ppb) level of limits of detection (LOD for NH3=70 ppb, for H2S=204 ppb, for NO=5 25 ppb, and for NO2=16 ppb based on 1.5 min exposure). Electron paramagnetic resonance spectroscopy and X-ray photoelectron 26 spectroscopy studies suggested that the chemiresistive response of the COF-DC-8 involves charge transfer interactions 27 between the analyte and nickelphthalocyanine component of the framework. 28 29 30 INTRODUCTION molecular solids,11 and conductive coordination polymers),5b, 31 5c, 12 the strategy for maximizing the intrinsic bulk 32 The development of chemically robust, porous, and conductivity of COFs can leverage through-bond and 33 electrically conductive nanomaterials drives progress in 1 2 3 through-space charge transport characteristics. -
1 Nanocomposite Nio:Au Hydrogen Sensors with High Sensitivity And
Nanocomposite NiO:Au hydrogen sensors with high sensitivity and low operating temperature M. Kandylaa*, C. Chatzimanolis-Moustakasa,b, E.P. Koumoulosb, C. Charitidisb, and M. Kompitsasa aNational Hellenic Research Foundation, Theoretical and Physical Chemistry Institute, 48 Vasileos Constantinou Avenue, 11635 Athens, Greece bNational Technical University of Athens, School of Chemical Engineering, 9 Heroon Polytechniou Street, 15780 Zografou, Greece Abstract We present results on the development of nanocomposite NiO:Au thin-film hydrogen sensors, which are able to detect hydrogen concentrations as low as 2 ppm in air, operating at low temperatures in the range 125 – 150oC. Thin NiO films were sputter- deposited on oxidized silicon substrates. The structural, morphological, and nanomechanical properties of the films were investigated with respect to post- deposition annealing. Au nanoparticles were added on the NiO surface via pulsed laser deposition and the films were tested as hydrogen sensors before and after Au deposition. The performance of the NiO films as hydrogen sensors improved significantly in the presence of Au nanoparticles on the surface. The detection limit (lowest detectable hydrogen concentration) decreased by two orders of magnitude, while the response time also decreased by a factor of three. KEYWORDS: A. composites, A. oxides, B. sputtering, B. laser deposition, D. electrochemical properties * Corresponding author: 1 M. Kandyla National Hellenic Research Foundation Theoretical and Physical Chemistry Institute 48 Vasileos Constantinou Avenue 11635 Athens, Greece Tel.: +30 210 7273826, Fax: +30 210 7273794 E-mail: [email protected] 2 1. Introduction Hydrogen is widely used in the chemical, petroleum, and metallurgical industries, as well as in power station cooling. -
Hydrogen Sensor Specifications
Control Instruments Corporation Product Specifications 25 Law Drive, Fairfield, NJ 07004-3295 USA Hydrogen Sensor for SmartMaxII Telephone 973-575-9114 Fax 973-575-0013 Email: [email protected] Internet: www.controlinstruments.com Sensor Design The Hydrogen Sensor employs electrochemical 9.375 inches technology. The sample diffuses into a micro fuel cell, where it chemically reacts to produce an electrical current. The micro fuel cell is designed so that the current produced is 3.625 inches proportional to the concentration of hydrogen present. The signal is then amplified into a mA output. The output signal is linear and readings are displayed in parts per million Cell Housing concentrations. Calibration Port Junction Box Construction Standard Specifications The sensor assembly consists of the micro fuel cell which Part Number SNR476 plugs into the electronics. The cell and electronics are Standard Range 0-1000 Parts Per Million (PPM) housed in an aluminum sensor body which connects to a Optional Range 0-2000 PPM junction box for field wiring. A collar protects the sensor Accuracy ± 5 PPM from environmental conditions and also provides a means of Response Time 40 seconds to 50% of scale introducing calibration test gas. Repeatability ± 1% full scale The micro fuel cell employs a capillary diffusion barrier Drift ± 2% full scale per month which eliminates the possibility of puncturing the membrane Assembly Rating Class 1, Division 1 and destroying the cell. The cell is a rugged and stable Assembly Material Aluminum design that is less sensitive to temperature and pressure Operating Life 2 years variations than other electrochemical cells. Storage life in container 6 months An on-board heater protects the cell and extends its Temperature Limits -20°C (-4°F) to 50°C (122°F) useful operating range in sub-freezing temperatures. -
Electronic Nose for Analysis of Volatile Organic Compounds in Air and Exhaled Breath
University of Louisville ThinkIR: The University of Louisville's Institutional Repository Electronic Theses and Dissertations 5-2017 Electronic nose for analysis of volatile organic compounds in air and exhaled breath. Zhenzhen Xie University of Louisville Follow this and additional works at: https://ir.library.louisville.edu/etd Part of the Engineering Commons Recommended Citation Xie, Zhenzhen, "Electronic nose for analysis of volatile organic compounds in air and exhaled breath." (2017). Electronic Theses and Dissertations. Paper 2707. https://doi.org/10.18297/etd/2707 This Doctoral Dissertation is brought to you for free and open access by ThinkIR: The University of Louisville's Institutional Repository. It has been accepted for inclusion in Electronic Theses and Dissertations by an authorized administrator of ThinkIR: The University of Louisville's Institutional Repository. This title appears here courtesy of the author, who has retained all other copyrights. For more information, please contact [email protected]. ELECTRONIC NOSE FOR ANALYSIS OF VOLATILE ORGANIC COMPOUNDS IN AIR AND EXHALED BREATH By Zhenzhen Xie M.S., University of Louisville, 2013 B.S., Heilongjiang University, 2011 A Dissertation Submitted to the Faculty of the J. B. Speed School of Engineering University of Louisville in Partial Fulfillment of the Requirements for the Degree of Doctor of Philosophy in Chemical Engineering Department of Chemical Engineering Louisville, KY May 2017 ELECTRONIC NOSE FOR ANALYSIS OF VOLATILE ORGANIC COMPOUNDS IN AIR AND EXHALED BREATH by Zhenzhen Xie B.S., Heilongjiang University, 2011 M.S., University of Louisville, 2013 A Dissertation Approved On 04/03/2017 by the Following Committee: ___________________________________ Dr. Xiao-An Fu, Dissertation Director ___________________________________ Dr. -
Development of a Nanocomposite Chemiresistor Sensor Based on Π
Sensors & Actuators: B. Chemical 271 (2018) 353–357 Contents lists available at ScienceDirect Sensors and Actuators B: Chemical journal homepage: www.elsevier.com/locate/snb Development of a nanocomposite chemiresistor sensor based on π- conjugated azo polymer and graphene blend for detection of dissolved T oxygen ⁎ André Olean-Oliveira, Marcos F.S. Teixeira Department of Chemistry and Biochemistry – School of Science and Technology, University of State of Sao Paulo (UNESP), Rua Roberto Simonsen, 305, CEP 19060-900 Presidente Prudente, SP, Brazil ARTICLE INFO ABSTRACT Keywords: The present paper describes the electrochemical impedance activity of a hybrid film with graphene and poly(azo- Azo conductive polymers Bismarck Brown Y) as the chemiresistor material. This nanocomposite film exhibits interesting properties based Chemiresistor on the redox properties of the azo polymer combined with the great electronic conductivity and stability of Nanocomposite graphene. Electrochemical impedance spectroscopy at the poly(azo-BBY)-rGO electrode in solutions with dif- Oxygen sensor ferent dissolved O concentrations revealed that the resistance values are very sensitive to variations in the O Graphene 2 2 concentration. 1. Introduction 2. Experimental Chemiresistors represent a new class and emerging area of electro- All measurements were performed in a conventional electro- chemical sensors [1,2]. Their operation is based on the change in the chemical cell containing three electrodes: a saturated calomel electrode electrical resistance of the material due to chemical interaction with the (SCE) as the reference; platinum wire as the counter electrode and a analyte [3]. A variety of materials have been investigated for applica- fluoride-doped tin oxide (FTO) electrode coated with a poly(azo-BBY)- tion as chemiresistors, such as semiconductor metal oxides [4], con- rGO blend as the working electrode (1.0 cm2). -
High-Sensitivity and Low-Power Flexible Schottky Hydrogen Sensor Based on Silicon Nanomembrane
Poster Session II: IoT Including Nanosensors High-sensitivity and Low-power Flexible Schottky Hydrogen Sensor based on Silicon Nanomembrane Minkyu Cho Department of Mechanical Engineering, Korea Advanced Institute of Science and Technology (KAIST) . Hydrogen (H2) is useful as a future clean energy resource and an ideal replacement for fossil fuel . Various applications such as hydrogen vehicle, petroleum refining, glass purification, semiconductor manufacturing etc. H2 is flammable at concentrations over 4% by volume, therefore high sensitivity H2 sensor with fast response time is necessary . Silicon nanomembrane based diode type H2 sensor was demonstrated exhibiting high sensitivity and low power consumption Source:http://www.hydrogen.energy.gov/systems_integration.html US Department of energy High Mobility Advantages of Si • Well established processing technique Graphene -> more freedom in sensor design Carbon Nanotubes GaAs, GaN Low flexible rigidity of thin Si *Si Poly-Si a-Si Polymers Good material candidate for Low Mobility high performance flexible/wearable H2sensors . The operation principle of the sensor is based on Schottky barrier lowering effect upon exposure to H2 . H2 gas molecules are diffused into Pd layer forming Palladium Hydride (PdHx) at Pd/Si interfaces . Device simulations show that effective current quenching has been occurred in 50 nm thickness SiNM H2 lowering standby power consumption of the sensor Reduced Si thickness Low standby power consumption Excellent mechanical properties o Low thermal budget (< 110 C) Applicable to wafer-scale process . High Sensitivity ( > 700% @ 0.5% H2 concentration) and Fast Response Time (τ10−90= 22s) . Good Linearity (R2 > 0.98) and Low Limit of Detection (50 ppm, limited by MFC) . Minor Increased Sensitivity under Tensile Strain (Piezoresistive property of SiNM) .