GE Plastics Design Guide Intro.Qxd 6/16/99 10:58 AM Page 3
Total Page:16
File Type:pdf, Size:1020Kb
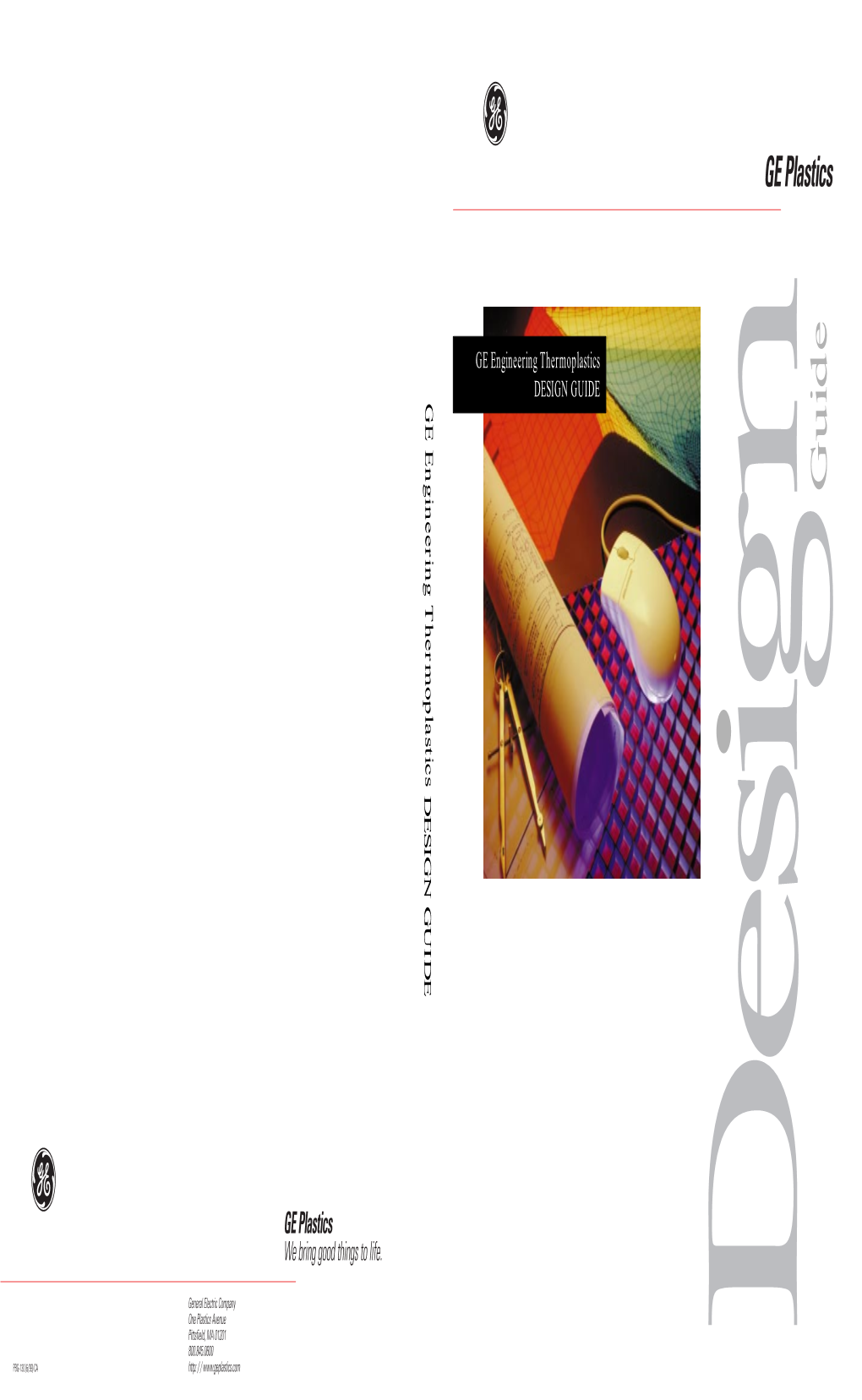
Load more
Recommended publications
-
Welding of Plastics: Fundamentals and New Developments
REVIEW ARTICLE D. Grewell*, A. Benatar Agricultural and Biosystems Eingineering, Iowa State University, Ames, IA, USA Welding of Plastics: Fundamentals and New Developments serves as the material that joins the parts and transmits the load This paper provides a general introduction to welding funda- through the joint. In welding or fusion bonding, heat is used to mentals (section 2) followed by sections on a few selected melt or soften the polymer at the interface to enable polymer welding processes that have had significant developments or intermolecular diffusion across the interface and chain entan- improvements over the last few years. The processes that are glements to give the joint strength. Each of these categories is discussed are friction welding (section 3), hot plate welding comprised of a variety of joining methods that can be used in (section 4), ultrasonic welding (section 5), laser/IR welding a wide range of applications. This paper is devoted to welding (section 6), RF welding (section 7) and hot gas/extrusion weld- processes only. Accordingly, only thermoplastics are consid- ing (section 8). ered, because thermosets cannot be welded without the addi- tion of tie-layers such as thermoplastics layers. Greater details on welding processes can be found in several monographs [1 to 4]. 1 Introduction to Joining Welding processes are often categorized and identified by the heating method that is used. All processes can be divided Despite designers’ goals of molding single component pro- into two general categories: internal heating and external heat- ducts, there are many products too complex to mold as a single ing, see Fig. -
Joining of Fibre-Reinforced Polymer Composites
JOINING OF FIBRE-REINFORCED POLYMER COMPOSITES A Good Practice Guide ACKNOWLEDGEMENTS The authors and editor would like to thank: Dr Annabel Fitzgerald, National Composites Centre, for reviewing the guide Robin Bilney, Testia Ltd, for reviewing Section 8 Non-destructive testing (NDT) Dr Lawrence Cook, bigHead Bonding Fasteners Ltd, for text and images on bigHeads Chris Minton, Minton, Treharne & Davies, for use of the text and figures on vibrational analysis Prof James Broughton, Oxford Brookes University, for support in adapting Table 8: Comparison and Rating of Disbonding Techniques. Adapted from Lu, Broughton, et al 63 Providers of other images as attributed This guide was funded by the National Composites Centre. Authors Chris Worrall, TWI Ltd Ewen Kellar, TWI Ltd Charlotte Vacogne, TWI Ltd Edited by Stella Job, Grazebrook Innovation © Composites UK Ltd, January 2020 2 CONTENTS 1. Introduction 6 1.1 Scope 6 1.2 Joining in design and specification 7 2. Goals and challenges 8 2.1 Do we need joining at all? 8 2.2 Reasons for joining composites 8 2.2.1 Functionality 9 2.2.2 Manufacturability 9 2.2.3 Cost 9 2.2.4 Aesthetics 9 2.3 Challenges 10 3. Joining possibilities 11 3.1 Types of joints 11 3.2 Joining techniques 11 4. Mechanical fastening 12 4.1 Introduction 12 4.2 Mechanical attachment 13 4.3 Mechanical fasteners 13 4.3.1 Special fasteners for composite structures 14 4.3.2 Types of fastener material 15 4.4 Machining of fastener holes 15 4.4.1 Mechanical machining 15 4.4.2 Non-mechanical machining 17 4.5 Failure modes 18 4.6 Parameters in mechanical fastening 19 4.6.1 Joining method (bolts or rivets) 20 4.6.2 Joint configuration 21 4.6.3 Geometric parameters 21 4.6.4 Lay-up (stacking sequence) 21 4.6.5 Fastener clearance 22 4.6.6 Preload or initial clamping force 23 4.7 Environmental effects on mechanical joints 23 4.8 Advantages and disadvantages of mechanical fastening 23 5. -
Products Evolved During Hot Gas Welding of Fluoropolymers
Health and Safety Executive Products evolved during hot gas welding of fluoropolymers Prepared by the Health and Safety Laboratory for the Health and Safety Executive 2007 RR539 Research Report Health and Safety Executive Products evolved during hot gas welding of fluoropolymers Chris Keen BSc CertOH Mike Troughton BSc PhD CPhys MInstP Derrick Wake BSc, Ian Pengelly BSc, Emma Scobbie BSc Health and Safety Laboratory Broad Lane Sheffield S3 7HQ This report details the findings of a research project which was performed as a collaboration between the Health and Safety Executive (HSE) and The Welding Institute (TWI). The project aim was to identify and measure the amounts of products evolved during the hot gas welding of common fluoropolymers, to attempt to identify the causative agents of polymer fume fever. Carbonyl fluoride and/or hydrogen fluoride were detected from certain fluoropolymers when these materials were heated to their maximum welding temperatures. Significant amounts of ultrafine particles were detected from all of the fluoropolymers investigated when they were hot gas welded. The report concludes that fluoropolymers should be hot gas welded at the lowest possible temperature to reduce the potential for causing polymer fume fever in operators. If temperature control is not sufficient to prevent episodes of polymer fume fever, a good standard of local exhaust ventilation (LEV) should also be employed. This report and the work it describes were funded by the Health and Safety Executive (HSE). Its contents, including any opinions and/or conclusions expressed, are those of the authors alone and do not necessarily reflect HSE policy. HSE Books © Crown copyright 2007 First published 2007 All rights reserved. -
A Research Paper on the Fundamentals of Plastic Welding
ISSN (Online) 2394-2320 International Journal of Engineering Research in Computer Science and Engineering (IJERCSE) Vol 4, Issue 8, August 2017 A Research Paper on the Fundamentals of Plastic Welding [1] S Kennedy [1] Department of Mechanical Engineering, Galgotias University, Yamuna Expressway Greater Noida, Uttar Pradesh Email id- [email protected] Abstract: Plastic is a material including a wide scope of semi-engineered or manufactured organics that are malleable and can be formed into strong objects of various shapes. Today, joining of thermoplastic composite structures is getting increasingly huge since thermoplastic composite materials are being utilized to supplant metallic or thermoset composite material to all the more likely withstand different loads in car, aviation, rural apparatuses and marine businesses. Plastic welding is accounted for in ISO 472 as a procedure of joining mollified surfaces of materials, with the assistance of warmth. Welding of thermoplastics is practiced in three progressive stages, as follows surface planning, utilization of warmth or potentially weight, and cooling. Various welding techniques have been developed for the joining of plastic materials. This paper presents advancement one of the tourist plastic welding where the sight- seeing is utilized to circuit or soften a filler thermoplastic pole and at the same time heat the surfaces to be joined. If there should arise an occurrence of hot-gas welding the parameters of welding, for example, welding temperature, stream rate, feed rate, welding power, gas, edge, filler bar, Pressure of tourist/gas, Gap separation and shoe impact the quality of the welded joint. The presentation of the above created machine was completed by getting ready seven examples of fluctuating welding, feed rate keeping different parameters steady all through the analyses. -
Joining of Nylon's Based Plastic Components
BASF Corporation JOINING OF NYLON BASED PLASTIC COMPONENTS -- VIBRATION AND HOT PLATE WELDING TECHNOLOGIES Abstract mechanical properties. Molded nylon parts are more resistant to creep, fatigue, repeated impact, Previously we reported to SPE’96 the and so on compared to the parts made of many optimized mechanical performance of linear less rigid thermoplastics. vibration welded nylon 6 and 66 butt joints. Under the optimized vibration welding There are more than a dozen classes of conditions (amplitude, pressure, meltdown, nylon resins, including nylon 6, nylon 66, nylon thickness of interface), the tensile strength at the 46, nylon 12, etc.). Welded nylons are used in nylon butt joints was equal to or 14% higher than many industrial products, the largest being the the tensile strength of the base polymer (matrix). automotive. In recent years, demands to use non-filled, fiber-glass reinforced and filled nylon H. Potente and A. Brubel presented to products to replace metals and thermosets in SPE’94 and SPE’98 an analysis of the welding power tools, lawn / garden equipment (leaf performance in a family of amorphous and semi- blowers, chain-saws, gas-tanks), and the crystalline thermoplastics including nylon 6 automotive (air induction, power train systems, using hot-plate welding technologies. For hot- fluids reservoirs, and other uses), have increased plate welded nylon 6 with a range of glass-fiber (1, 2). reinforcement from 0 to 40% (by weight), the tensile strength at the weld was 40–60% less On average a car uses 18 kg of nylon compared to the tensile strength of the base based plastics. -
Welding of Infrared Transmissive Thermoplastic Polymers Using Diode Laser Systems
Welding of Infrared Transmissive Thermoplastic Polymers using Diode Laser Systems Scott Hartley and Nicole Woosman Gentex Corporation, 324 Main Street Carbondale, PA 18407 USA Abstract Clearweld™ technology is a tool, which is readily employed for transmission laser welding of thermoplastic polymers using near infrared diode lasers. This process is accomplished through the use of specialized material systems uniquely chosen and targeted to absorb the laser light at the intended laser weld joint in order to rapidly effectuate a weld. Data will be presented showing actual weld strengths, critical process parameters, and quantification of residual stresses in a variety of thermoplastic materials. Keywords: polymer joining, plastics welding, laser transmission welding, laser materials processing, laser materials processing, Clearweld 1 Introduction The principal disadvantage of laser welding has been the need to use carbon black as an absorbent, posing a Transmission laser welding involves the use of high- limitation in applications where appearance and color density electromagnetic energy produced by a laser are important. source to create thermal energy at the joint interface necessary for weld formation. Plastics in their natural 2 The Clearweld™ Process state do not absorb near-infrared (NIR) light; therefore energy from lasers operating in the NIR efficiently A significant process advancement has been developed transmits through plastics. To successfully use lasers that offers all the advantages of conventional laser for joining polymer, this laser energy must be properly welding without the use of opaque materials or the harnessed to create the heating and intermolecular addition of unwanted color. The process can be used to diffusion critical for weld formation. -
Chapter 6 Arc Welding
Revised Edition: 2016 ISBN 978-1-283-49257-7 © All rights reserved. Published by: Research World 48 West 48 Street, Suite 1116, New York, NY 10036, United States Email: [email protected] Table of Contents Chapter 1 - Welding Chapter 2 - Fabrication (Metal) Chapter 3 - Electron Beam Welding and Friction Welding Chapter 4 - Oxy-Fuel Welding and Cutting Chapter 5 - Electric Resistance Welding Chapter 6 - Arc Welding Chapter 7 - Plastic Welding Chapter 8 - Nondestructive Testing Chapter 9 - Ultrasonic Welding Chapter 10 - Welding Defect Chapter 11 - Hyperbaric Welding and Orbital Welding Chapter 12 - Friction Stud Welding Chapter 13 WT- Welding Joints ________________________WORLD TECHNOLOGIES________________________ Chapter 1 Welding WT Gas metal arc welding ________________________WORLD TECHNOLOGIES________________________ Welding is a fabrication or sculptural process that joins materials, usually metals or thermoplastics, by causing coalescence. This is often done by melting the workpieces and adding a filler material to form a pool of molten material (the weld pool) that cools to become a strong joint, with pressure sometimes used in conjunction with heat, or by itself, to produce the weld. This is in contrast with soldering and brazing, which involve melting a lower-melting-point material between the workpieces to form a bond between them, without melting the workpieces. Many different energy sources can be used for welding, including a gas flame, an electric arc, a laser, an electron beam, friction, and ultrasound. While often an industrial process, welding can be done in many different environments, including open air, under water and in outer space. Regardless of location, welding remains dangerous, and precautions are taken to avoid burns, electric shock, eye damage, poisonous fumes, and overexposure to ultraviolet light. -
Process Analysis of the Hot Plate Welding of Drive Belts
Krzysztof Wałęsa, Ireneusz Malujda, Dominik Wilczyński DOI 10.2478/ama-2020-0012 Process Analysis of the Hot Plate Welding of Drive Belts PROCESS ANALYSIS OF THE HOT PLATE WELDING OF DRIVE BELTS Krzysztof WAŁĘSA,* Ireneusz MALUJDA,* Krzysztof TALAŚKA,* Dominik WILCZYŃSKI* *Institute of Machine Design, Poznań University of Technology, ul. Piotrowo 3, 61-138 Poznań, Poland [email protected], [email protected], [email protected], [email protected] received 11 February 2020, revised 25 May 2020, accepted 28 May 2020 Abstract: Most industrial machines use belt transmission for power transfer. These mechanisms often use the round belts of several milli- metres in diameter that are made of thermoplastic elastomers, especially polyurethane. Their production process calls for bonding the ma- terial, which is often performed by hot plate butt welding. In order to achieve proper design of an automatic welding machine, the authors analysed the hot plate welding process of round belts. This process consists of five phases. It is necessary to recognize all the physical phenomena that occur during welding, especially those connected with thermomechanical properties of material. This knowledge is neces- sary to determine the temperature distribution during each step of the process. The paper presents a standard welding cycle together with an explanation of the physical phenomena in each phase. An analysis of these fundamentals will be used to derivate the function of tem- perature distribution during all process phases. In addition, some assumptions for calculation of temperature distribution and some funda- mental physic correlations were presented. Keywords: Hot plate welding, round drive belts, heating, thermal conducting, plasticizing 1. -
Information to Users
INFORMATION TO USERS This manuscript has been reproduced from the microfilm master. UMI films the text directly from the original or copy submitted. Thus, some thesis and dissertation copies are in typewriter face, while others may be from any type of computer printer. The quality of this reproduction is dependent upon the quality of the copy submitted. Broken or indistinct print, colored or poor quality illustrations and photographs, print bleedthrougb, substandard margins, and improper alignment can adversely afreet reproduction. In the unlikely event that the author did not send UMI a complete manuscript and there are missing pages, these will be noted. Also, if unauthorized copyright material had to be removed, a note will indicate the deletion. • Oversize materials (e.g., maps, drawings, charts) are reproduced by sectioning the original, beginning at the upper left-hand comer and continuing from left to right in equal sections with small overlaps. Each original is also photographed in one exposure and is included in reduced form at the back of the book. Photographs included in the original manuscript have been reproduced xerographically in this copy. Higher quality 6" x 9" black and white photographic prints are available for any photographs or illustrations appearing in this copy for an additional charge. Contact UMI directly to order. A Bell & Howell Information Company 300 North Z e e b Road. Ann Arbor. Ml 48106-1346 USA 313/761-4700 800/521-0600 ANALYSIS OF MORPHOLOGY, CRYSTALLIZATION KINETICS, AND PROPERTIES OF HEAT AFFECTED ZONE IN HOT PLATE WELDING OF POLYPROPYLENE DISSERTATION Presented in Partial Fulfillment of the Requirements for the Degree of Philosophy in the Graduate School of The Ohio State University By Jenn-Yeu Nieh, B.S., M.S. -
Thermal Welding by the Third Phase Between Polymers: a Review for Ultrasonic Weld Technology Developments
polymers Review Thermal Welding by the Third Phase Between Polymers: A Review for Ultrasonic Weld Technology Developments Jianhui Qiu 1,*, Guohong Zhang 1 , Eiichi Sakai 1, Wendi Liu 2 and Limin Zang 3 1 Department of Mechanical Engineering, Faculty of Systems Science and Technology, Akita Prefectural University, Akita 015-0055, Japan; [email protected] (G.Z.); [email protected] (E.S.) 2 College of Transportation and Civil Engineering, Fujian Agriculture and Forestry University, Fuzhou 350108, China; [email protected] 3 MOE Key Laboratory of New Processing Technology for Nonferrous Metal & Materials, College of Materials Science and Engineering, Guilin University of Technology, Guilin 541004, China; [email protected] * Correspondence: [email protected] Received: 30 December 2019; Accepted: 8 March 2020; Published: 31 March 2020 Abstract: Ultrasonic welding (USW) is a promising method for the welds between dissimilar materials. Ultrasonic thermal welding by the third phase (TWTP) method was proposed in combination with the formation of a third phase, which was confirmed as an effective technology for polymer welding between the two dissimilar materials compared with the traditional USW. This review focused on the advances of applying the ultrasonic TWTP for thermoplastic materials. The research development on the ultrasonic TWTP of polycarbonate (PC) and polymethyl methacrylate (PMMA), polylactic acid (PLA) and polyformaldehyde (POM), and PLA and PMMA are summarized according to the preparation of the third phase, welded strength, morphologies of rupture surfaces, thermal stability, and others. The review aimed at providing guidance for using ultrasonic TWTP in polymers and a basic understanding of the welding mechanism, i.e., interdiffusion and molecular motion mechanisms between the phases. -
Publishing Programme
Publishing Programme Books | Dictionaries | Digital Products Technical Bulletins | Technical Codes | Magazines www.dvs-media.eu DVS Media GmbH Technical literature of welding - knowledge transfer in highest quality from DVS Media When it comes to technical information for welding, joining technolo- gy, separation technology and coating technology, DVS Media is the first choice. As a subsidiary of the DVS - German Welding Society, we provide the know-how transfer and pooling of expertise in our magazines, books, instructional media, technical rules and electronic media. DVS members receive a 10% membership discount on all DVS publi- cations. When ordering, please specify the membership number. (Articles of other publishers are excluded from this rule.) The information corresponds to October 2018. You can order at the following address: DVS Media GmbH Aachener Straße 172 40223 Düsseldorf / Germany P +49 (0)2 11 15 91-162/-225 F +49 (0)2 11 15 91-150 [email protected] [email protected] www.dvs-media.eu All prices plus postage costs! Errors excepted. (Please always specify the way of delivery: airmail or regular mail!) 02 | Publishing Programme 2018 Table of Contents Books DVS English Edition ..................................................................... 04 DIN-DVS-Handbooks .................................................................. 10 Dictionaries ................................................................................. 11 Conference Proceedings ............................................................ -
Vibration Welding Guide
Vibration Welding Guide Vibration Welding of Engineering Plastics Table of contents 1. Introduction 5 2 The vibration welding process 6 2.1 Basic principles 6 2.2 Process parameters 7 3 Vibration welding equipment 9 3.1 Machine Basics 9 3.2 Tooling Basics 9 3.3 Vibration Welding Systems 10 4 Materials 11 4.1 Thermoplastics 11 4.2 Type and composition of material 11 4.3 Glass fiber reinforced materials 12 4.4 Compatibility of materials 12 5 Part and weld design 14 5.1 Joint 14 5.2 Weld depth 15 5.3 Welding line 15 6 Testing 17 7 Applications 18 8 Process variants 19 Vibration Welding of Engineering Plastics 3 4 Vibration Welding Guide 1. Introduction Typical joining methods for plastic parts are screwing, snap- and press-fitting, gluing and welding. Welding is an effective method for permanently joining plastic components. There are various welding techniques such as spin-, ultrasonic-, friction-, laser- and hot plate welding. The friction or vibration welding process is ideally suited for welding of compatible thermoplastic parts along flat seams which have to be high strength, pressure tight and hermetically sealed. The process can also accommodate seams with small out-of-plane curvatures. The most effective analogy to demonstrate this process is pressing and rubbing your hands together to generate frictional heat. The same principle is applied for joining thermoplastic parts. It is the ability to control the frictional process that makes vibration welding such a very precise and repeatable process in serial production. This technique offers a large number of − Product is exposed to vibrations during required over the whole weld surface.