The Praxis of Platinum-Palladium Printing
Total Page:16
File Type:pdf, Size:1020Kb
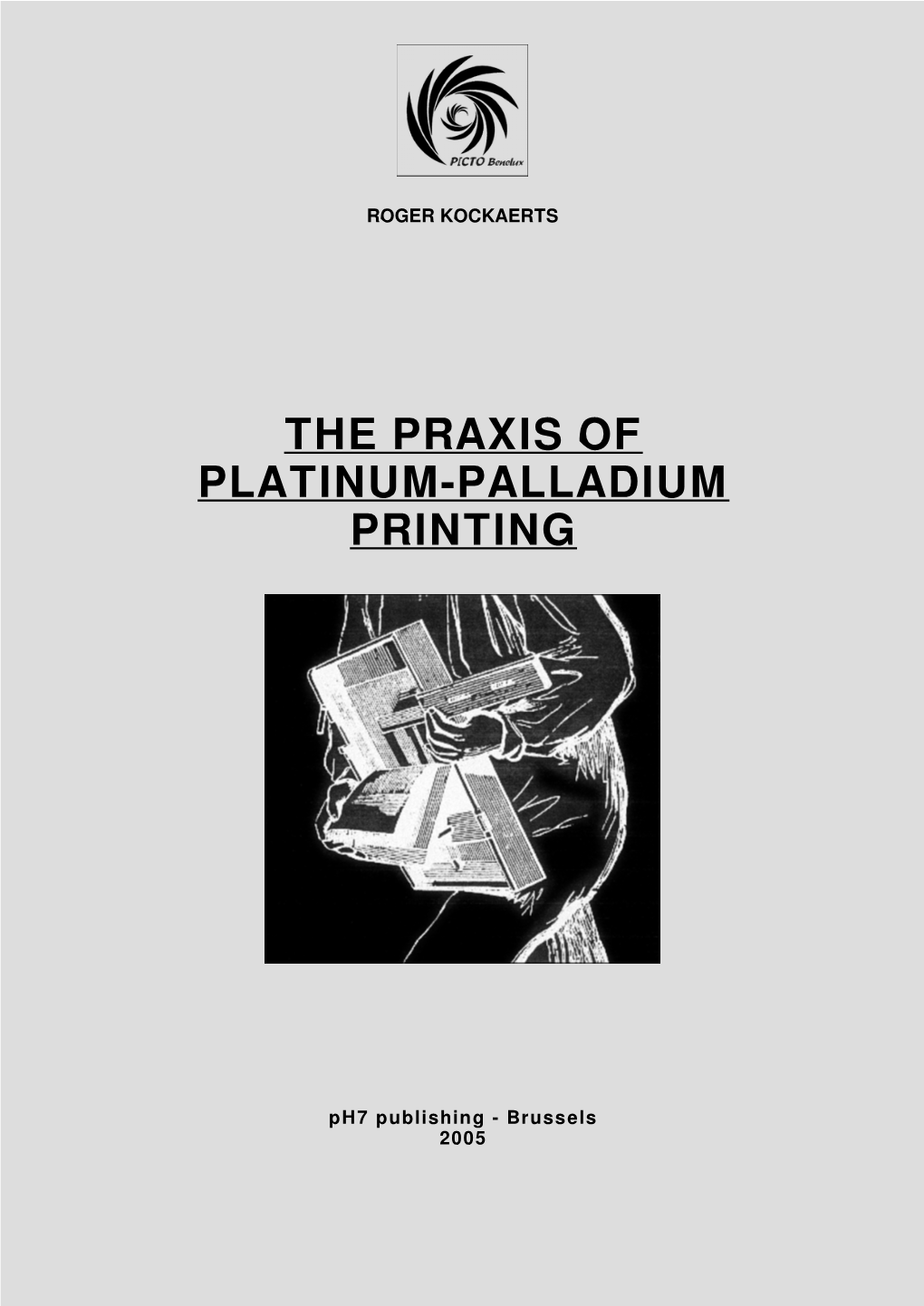
Load more
Recommended publications
-
Repoussé Work for Amateurs
rf Bi oN? ^ ^ iTION av op OCT i 3 f943 2 MAY 8 1933 DEC 3 1938 MAY 6 id i 28 dec j o m? Digitized by the Internet Archive in 2011 with funding from Boston Public Library http://www.archive.org/details/repoussworkforamOOhasl GROUP OF LEAVES. Repousse Work for Amateurs. : REPOUSSE WORK FOR AMATEURS: BEING THE ART OF ORNAMENTING THIN METAL WITH RAISED FIGURES. tfjLd*- 6 By L. L. HASLOPE. ILLUSTRATED. LONDON L. UPCOTT GILL, 170, STRAND, W.C, 1887. PRINTED BY A. BRADLEY, 170, STRAND, LONDON. 3W PREFACE. " JjJjtfN these days, when of making books there is no end," ^*^ and every description of work, whether professional or amateur, has a literature of its own, it is strange that scarcely anything should have been written on the fascinating arts of Chasing and Repousse Work. It is true that a few articles have appeared in various periodicals on the subject, but with scarcely an exception they treated only of Working on Wood, and the directions given were generally crude and imperfect. This is the more surprising when we consider how fashionable Repousse Work has become of late years, both here and in America; indeed, in the latter country, "Do you pound brass ? " is said to be a very common question. I have written the following pages in the hope that they might, in some measure, supply a want, and prove of service to my brother amateurs. It has been hinted to me that some of my chapters are rather "advanced;" in other words, that I have gone farther than amateurs are likely to follow me. -
The Platinum Print: a Catalyst for Discussion
The Platinum Print: a catalyst for discussion Defined: distinguished by its matte finish and subtle tonal gradations image is embedded into the fibers of the paper non-silver process iron salts are used to sensitize paper prior to development Upon exposure to light, a faint image appears development process converts iron salts platinum faint image becomes more pronounced1 1. The History of the Platinum Print Due to the similar qualities and processes, The terms platinotype, palladium prints and platinum prints are often used interchangeably. According to James Reilly, the platinotype and the platinum print are in fact congruent photographic processes yielding in what would be the same photographic print. Having said that please refer to figure 1.1, below. This chart demonstrates not necessarily the date of invention or discovery of the most popular historic photographic processes, but rather the years in which the process was most dominantly used. 1 Figure 1.1 Chronology of the use of photographic processes in the United States. (up to 1984.) The chart indicates that platinum prints were popular for approximately 40 years from 1870s to the 1930s, competing with the well-established albumen prints and eventually being overtaken by the gelatin silver processes which came on the scene about the same time. A long string of inventors and their inventions led to the ultimate culmination in what became known as the platinum print, one of the few non-silver processes used in photography. In 1830, Ferdinand Gehlen noted that ultraviolet light would alter the color of platinum salts and cause the ferric salts to separate out into a ferrous state. -
Testing Gold Platinum Silver.Qxp
PROCEDURES FOR TESTING GOLD, PLATINUM AND SILVER To test for the karat value of gold, platinum and silver, you will need the following materials and tools: • Black acid testing stone that is washed thoroughly with water prior to each test. • Acids. • Gold testing needles with gold tips - used for comparison with test pieces. Testing for 10K, 12K, 14K Scratch the gold piece to be tested on the stone. Next to this position, scratch the appropriate needle (10, 12 or 14K). Place a drop of the appropriate acid on the stone where the gold was rubbed off. If the gold is the same karat or higher, the color of the scratch mark for the gold piece will appear the same as the mark from the needle. If that gold piece is a lower karat, the scratched deposit will become fainter and eventually disappear. Testing for 18K Scratch the test piece on the stone and apply 18K acid. Any gold that is less than 18K will disappear in less than 30 seconds. Gold that remains on the stone is 18K or higher. Testing for 20K and 24K Scratch the gold piece on the stone. Next, scratch any item of know karat (coin or needle) on the stone. Apply one drop of acid to area. The material that starts to disappear has the lower karat. Testing for Platinum Scratch the test item on the stone and apply one drop of acid to the application on the stone. If the material is platinum, it should keep its white, bright color. White Gold The same procedure for platinum can be used for 18K white gold. -
Alternative Processes a Few Essentials Introduction
Alternative Processes A Few Essentials Introduction Chapter 1. Capture Techniques From Alternative Photographic Processes: Crafting Handmade Images Chapter 2. Digital Negatives for Gum From Gum Printing: A Step-by-Step Manual, Highlighting Artists and Their Creative Practice Chapter 3. Fugitive and Not-So-Fugitive Printing From Jill Enfield?s Guide to Photographic Alternative Processes: Popular Historical and Contemporary Techniques 2 Featured Books on Alternative Process Photography from Routledge | Focal Press Use discount code FLR40 to take 20% off all Routledge titles. Simply visit www.routledge.com/photography to browse and purchase books of interest. 3 Introduction A young art though it may be, photography already has a rich history. As media moves full steam ahead into the digital revolution and beyond, it is a natural instinct to look back at where we?ve come from. With more artists rediscovering photography?s historical processes, the practice of photography continually redefines and re-contextualizes itself. The creative possibilities of these historical processes are endless, spawning a growing arena of practice - alternative processes, which combines past, present and everything in between, in the creation of art. This collection is an introduction to and a sample of these processes and possibilities. With Alternative Photographic Processes, Brady Wilks demonstrates techniques for manipulating photographs, negatives and prints ? emphasizing the ?hand-made? touch. Bridging the gap between the simplest of processes to the most complex, Wilks? introduction demonstrates image-manipulation pre-capture, allowing the artist to get intimate with his or her images long before development. In the newly-released Gum Printing, leading gum expert Christina Z. -
The Platinum/Palladium Process
9 The Platinum/Palladium Process OVERVIEW AND EXPECTATIONS In the majority of the classes and workshops that I’ve taught over the years, “the platinum/palladium process” is the answer that surfaces first when I ask the question, “What process do you want to learn the most?” In this chapter you will learn how, and, as in previous chapters, I begin with a little history. Then you will learn the chemistry and sequence of the various stages to a finished print. This chapter gives you alternatives to traditional platinum/palladium chemistry and provides you with a simple sensitizer “drop chart” that is based on the type of negative you are working with, rather than the print you would like to make. I also provide the beginnings of a trouble-shooting list to assist in hunting down problems that may be showing up in your work. Finally, you’ll get some brief alternative ideas for combining platinum/palladium with other techniques such as Van Dyke and gum bichromate. A LITTLE HISTORY Like most refined non-silver and alternative photographic processes, the art of platinum/palladium printing was developed in pieces over time by a number of dedicated artists and scientists. In 1830, Ferdinand Gehlen recorded the action and effects of light on platinum chloride, noting that UV light would alter the color of platinum salts and cause the ferric salts to precipitate out into a ferrous state. At around the same time, Johann Wolfgang Dobereiner (1780–1849) observed the decomposition of ferric oxalate on exposure to UV light and scientifically defined its sensitivity. -
Nuances De Vie
NUANCES DE VIE: PHOTOGRAPHIC PRINTMAKING IN THREE MEDIUMS A Project Presented to the faculty of the Departments of Art and Design California State University, Sacramento Submitted in partial satisfaction of the requirements for the degree of MASTER OF ARTS in SPECIAL MAJOR (Printmaking and Photography) by Valerie Wheeler SPRING 2012 © 2012 Valerie Wheeler ALL RIGHTS RESERVED ii NUANCES DE VIE: PHOTOGRAPHIC PRINTMAKING IN THREE MEDIUMS A Project by Valerie Wheeler Approved by: ________________________________, Sponsor Sharmon Goff ________________________________, Committee Member Roger Vail ________________________________, Committee Member Nigel Poor _______________________ Date iii Student: Valerie Wheeler I certify that this student has met the requirements for format contained in the University format manual, and that this project is suitable for shelving in the Library and credit is to be awarded for the project. ______________________________, Dean ________________ Chevelle Newsome, Ph.D. Date Office of Graduate Studies iv Abstract of NUANCES DE VIE: PHOTOGRAPHIC PRINTMAKING IN THREE MEDIUMS by Valerie Wheeler The goal of this special major in printmaking and photography was to bridge the two art forms through photo etching using classical and modern methods. In the process of learning large format photography, intaglio printmaking (photogravure), and non-etch intagliotype printing, I expanded the project to include platinum and palladium printing (making platinotypes and platino-palladiotypes). The continuity among the mediums rested upon the images, a few of which were printed in more than one medium. Landscapes, floral still-lifes, architecture, and a few portraits came together in a body of complementary work consisting of fifty-two images in four sizes. The thesis exhibition was installed and open for a week in the Robert Else Gallery; it included short technical labels to explain the three mediums. -
Advertising Platinum Jewelry
FTC FACTS for Business Advertising Platinum Jewelry ftc.gov The Federal Trade Commission’s (FTC’s) Jewelry Guides describe how to accurately mark and advertise the platinum content of the jewelry you market or sell. Platinum jewelry can be alloyed with other metals: either precious platinum group metals (PGMs) — iridium, palladium, ruthenium, rhodium, and osmium — or non-precious base metals like copper and cobalt. In recent years, manufacturers have alloyed some platinum jewelry with a larger percentage of base metals. Recent revisions to the FTC’s Jewelry Guides address the marking of jewelry made of platinum and non-precious metal alloys and when disclosures are appropriate. When Disclosures Should Be Made Product descriptions should not be misleading, and they should disclose material information to jewelry buyers. If the platinum/base metal-alloyed item you are selling does not have the properties of products that are almost pure platinum or have a very high percentage of platinum, you should disclose that to prospective buyers. They may want to know about the value of the product as well as its durability, luster, density, scratch resistance, tarnish resistance, its ability to be resized or repaired, how well it retains precious metal over time, and whether it’s hypoallergenic. You may claim your product has these properties only if you have competent and reliable scientific evidence that your product — that has been alloyed with 15 to 50 percent non-precious or base metals — doesn’t differ in a material way from a product that is 85 percent or more pure platinum. Facts for Business Terms Used in Advertising • Jewelry that has 850 parts per thousand pure platinum — meaning that it is 85 percent pure • Any item that is less than 500 parts per platinum and 15 percent other metals — may be thousand pure platinum should not be marked referred to as “traditional platinum.” The other or described as platinum even if you modify the metals can include either PGMs or non-precious term by adding the piece’s platinum content in base metals. -
CHAPTER 18 the GUM BICHROMATE PROCESS Fig: 18 -1 Here, Christopher James, Alicia in Gum #2, 2012 (Gum) OVERVIEW & EXPECTATIO
CHAPTER 18 THE GUM BICHROMATE PROCESS Fig: 18 -1 here, Christopher James, Alicia in Gum #2, 2012 (gum) OVERVIEW & EXPECTATIONS Here’s the truth… in the gum bichromate process there are very few absolutely correct ways to do anything. Here’s another nugget of dependable veracity… in my experience, gum bichromate printers are the most passionate and hard-headed of all alternative process artists when it comes to their particular way of performing the process. I can just imagine so many of my friends reading that last sentence and saying, "I just know he’s talking about me!" © Christopher James, The Book of Alternative Photographic Processes: 3rd Edition, 2015 When the gum bichromate process is broken down into its three component steps, and explained in the most elementary way possible, it appears to be amazingly uncomplicated. However, to nearly every one of my students who has been taken with the process, and for those artists who are dedicated to it for life, gum bichromate slowly reveals itself to be one of the most complex in the alternative process genre. The gum bichromate process is ridiculously seductive. This is primarily due to its very limited chemistry, oh-so-simple water development, unlimited color palette using the watercolors of the artist’s choice, and very flexible ability to be coupled with a wide range of other alternative and graphic arts techniques such as platinum / palladium, cyanotype, all forms of printmaking and artist’s books. I think of gum as the photographic ambassador to the fine arts. Because of its pigment and substrate options, and brush application, gum bichromate printing is one of the few photographic processes capable of achieving that wonderful element I refer to as gesture - gesture being the evidence of the artist’s hand in the creation of an expressive and graphic mark. -
The Platinum Print B the History of the Platinum Process
THE PLATINUM PRINT B THE HISTORY OF THE PLATINUM PROCESS A REFERENCE TO THE SCIENTIFIC, COMMERCIAL, AND AESTHETIC DEVELOPMENT OF THE PLATINOTYPE JOHN HAFEY & TOM SHILLEA The Platinum Print by John Hafey and Tom Shillea ISBN 0-89938-000-X Copyright 1979 Graphic Arts Research Center Rochester Insitute of Technology This Adobe Acrobat document produced in november 2002 is based on the illustrated primer The Platinum Print written by John Hafey and Tom Shillea. It is about an exhibition called „The Contemporary Platinotype“ which took place at Rochester Institute of Technology in 1979. Unfortunately, that illustrated primer is now out of print. But the PDF-Version contains both the original text about the scientific discovery, the commercial developement and the aesthetic evolution of the Platinotype. It is requested to make use of this document for scientific research or pure information only! If any person may be offended because of misuse of copyright laws, please contact me at [email protected] Frank Rossi, 2002 Scientific Discovery and Commercial Development Ferdinand Gehlen was the first person to explore the action and effects of light rays upon platinum and record his experiments. In 1830, he discovered that a solution of platinum chloride when exposed to light, first turned a yellow color, and eventually formed a precipitate of metallic platinum.1 In 1831, experiments by the chemist Johann Wolfgang Dobereiner obtained important results. Born in Bavaria in 1780, he practiced pharmacy in Karlsruhe, and devoted himself to the study of the natural sciences, particularly chemistry. In 1810, he was given the position of professor of chemistry and pharmacy at the University of Jena, where he taught until his death in 1849.2 He observed that platinum metal was only slightly affected by the action of light, and concluded that some substance would have to be added to the pure platinum metal to in- crease its sensitivity to light. -
JD: Jewelry Design
JD: Jewelry Design JD 101 — Introduction to Jewelry JD 115 — Metal Forming Techniques: Fabrication Chasing and Repousse 2 credits; 1 lecture and 2 lab hours 1.5 credits; 3 lab hours Basic processes used in the design and Introduces students to jewelry-forming creation of jewelry. Students fabricate their techniques by making their own dapping own designs in the studio. and chasing tools by means of forging, JD 102 — Enameling Techniques for annealing, and tempering. Using these Precious Metals/Fine Jewelry/Objects tools, objects are created by repousse and D'Art other methods. 2 credits; 1 lecture and 2 lab hours Prerequisite(s): all first-semester Jewelry Vitreous enameling on precious metals. Design courses or approval of chairperson Studies include an emphasis on the "Co-requisite(s): JD 116, JD 122, JD metallurgical properties of gold, silver, and 134, JD 171, and JD 173 or approval of platinum and their chemical compatibility chairperson. with enamels. Surface treatments, ancient JD 117 — Enameling for Contemporary and modern, that intensify the jewel- Jewelry like qualities of vitreous enamel on 2 credits; 1 lecture and 2 lab hours precious metal will be explored. along with Vitreous enamel has been used for construction techniques that help students centuries as a means of adding color transform glass into beautiful, functional and richness to precious objects and jewelry and objects of art. jewelry. This course examines historical Prerequisite(s): JD 101. and contemporary uses of enamel, and JD 103 — Jewelry and Accessories explores the various methods of its Fabrication (Interdisciplinary) application, including cloisonne, limoges 2 credits; 1 lecture and 2 lab hours and champleve, the use of silver and gold This is an interdisciplinary course cross- foils, oxidation, surface finishing and setting listed with LD 103. -
The Chiba System 千葉方式 : a Non Toxic Alternative to the Dichromate
The Chiba System 千葉方式 A Non Toxic Alternative to the Dichromate Processes January 2007 Halvor Bjoerngaard Graduate School of Science and Technology CHIBA UNIVERSITY (千葉大学学位申請論文) The Chiba System 千葉方式 : A Non Toxic Alternative to the Dichromate Processes or The Production of Photographic Prints in Permanent Pigments by Utilising the Sensitivity of the Ferric Salt to the Spectre and Employing the Polymerization of Colloids. 2007年1月 千葉大学大学院自然科学研究科 情報科学専攻画像科学 Halvor Bjørngård Abstract This study has the main purpose of presenting a non-toxic, or an alternative, printing system for the dichromate based pigment processes. The two methods presented in depth are modelled on first Carbon printing then Gum Printing. Achieving non-toxicity for these systems means replacing the dichromate sensitizer and secondly to avoid the practise of hardening the substrate. An alternative sensitizer is presented and hardening is avoided by using modified working methods. The chemistry utilised for this purpose is iron based, red-ox induced, free radical polymerization. The sensitizer is ammonium ferric citrate, using either hydrogen peroxide or ammonium persulphate as developer. For Carbon Printing a solution to both the need for hardeners and the problem of oxygen inhibition, which is usual for this kind of polymerisation, is achieved. This is done by using a covering layer of agar-agar that blocks oxygen and changes the transfer system, obsolescing the use of hardeners. For Gum Printing two methods are presented. One is based on gelatine, which allows the use of a hydrogen peroxide bath for development. The second method is with gum arabicum, which necessitates inclusion of ammonium persulphate in the coating as a developing agent. -
Platinum, Silver- Platinum, and Palladium Prints
Noble Metals for the Early Modern Era: Platinum, Silver- Platinum, and Palladium Prints Constance Mc Cabe Histories of photography usually emphasize the photogra- phers’ command of the camera and the resulting pictures while offering little insight into the extensive chemical and technical artistry performed in studios and darkrooms. Research into the materials and methods behind photo- graphic prints, however, can shed light on the aesthetic goals of the photographers and help to determine which properties are the result of artistic decisions and which might be the natural effects of aging. By studying the array of platinum, silver- platinum, and palladium prints in the Thomas Walther Collection, we are given an opportunity to appreciate how photographers in the early twentieth cen- tury manipulated materials and chemicals to achieve a quasi-modern aesthetic. The aesthetic benchmark for many photographers at the dawn of the twentieth century was the platinum print, extolled for its unparalleled artistic qualities and perma- nence. Alfred Stieglitz (1864–1946) and Clarence H. White (1871–1925), both highly influential photographers and lead- ers of Pictorialism, a movement championing photography as fine art, praised platinum as the ideal photographic medium for their exhibition prints. Their disciples contin- ued to test the medium for new and unusual effects, exploiting such curiosities as multiple exposures, tone reversal, and solarization, and exploring unconventional compositional elements and abstraction. Highly attuned to the technical craft of their work, they investigated myriad products and chemical modifications to achieve their artistic fig. 1 Alfred Stieglitz. From the Back Window at “291”. April 3, 1915. Platinum print, objectives.