Bounding the Locus of the Center of Mass for a Part with Shape Variation
Total Page:16
File Type:pdf, Size:1020Kb
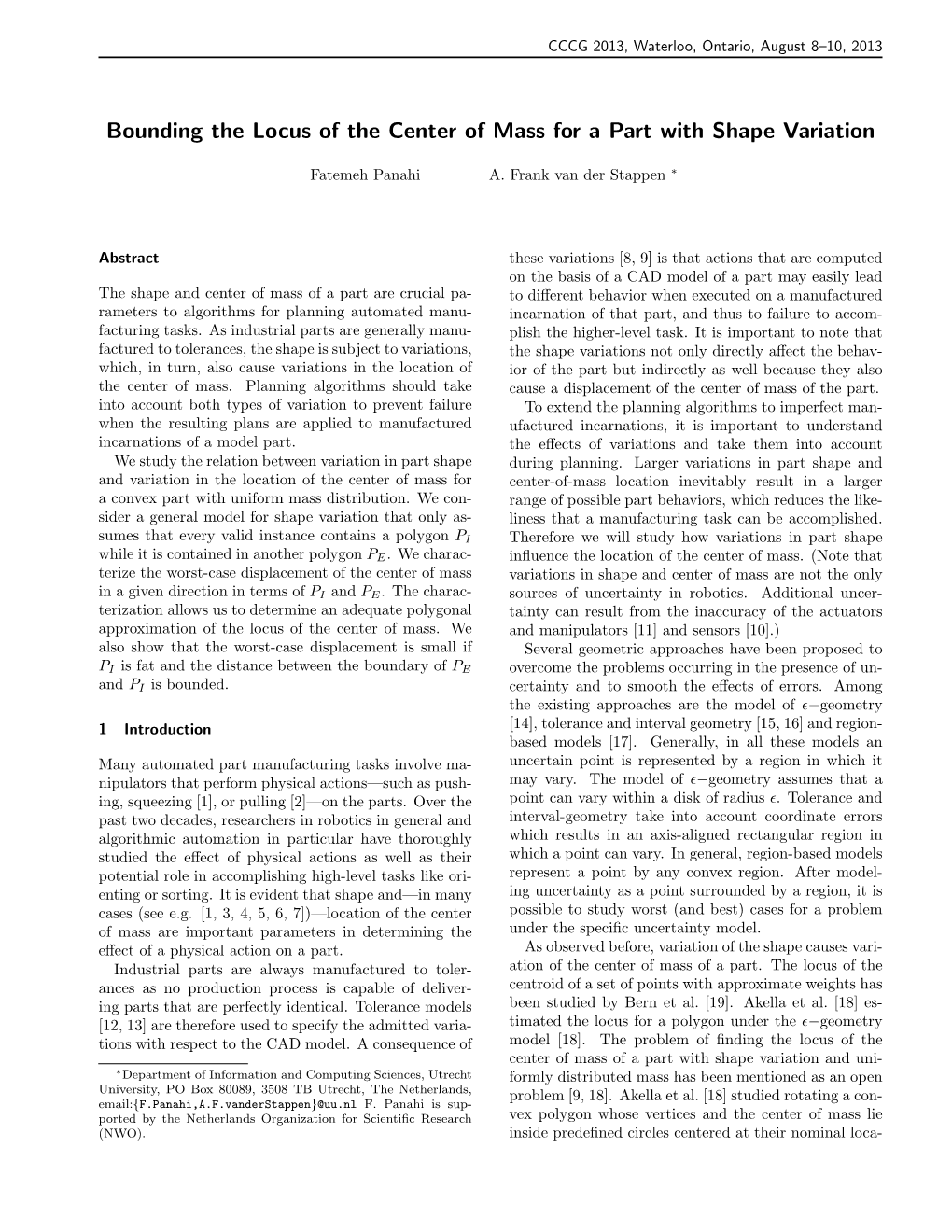
Load more
Recommended publications
-
Descartes and Coordinate, Or “Analytic” Geometry April 19 and 21, 2017
MONT 107Q { Thinking about Mathematics Discussion { Descartes and Coordinate, or \Analytic" Geometry April 19 and 21, 2017 Background In 1637, the French philosopher and mathematician Ren´eDescartes published a pamphlet called La G´eometrie as one of a series of discussions about particular sciences intended apparently as illustrations of his general ideas expressed in his work Discours de la m´ethode pour bien conduire sa raison, et chercher la v´erit´edans les sciences (in English: Discourse on the method of rightly directing one's reason and searching for truth in the sciences). This work introduced other mathematicians to a new way of dealing with geometry. Via the introduction (at first only in a rather indirect way) of numerical coordinates to describe points in the plane, Descartes showed that it was possible to define geometric objects by means of algebraic equations and to apply techniques from algebra to deduce geometric properties of those objects. He illustrated his new methods first by considering a problem first studied by the ancient Greeks after the time of Euclid: Given three (or four) lines in the plane, find the locus of points P that satisfy the relation that the square of the distance from P to the first line (or the product of the distances from P to the first two of the lines) is equal to the product of the distances from P to the other two lines. The resulting curves are called three-line or four-line loci depending on which case we are considering. For instance, the locus of points satisfying the condition above for the four lines x + 2 = 0; x − 1 = 0; y + 1 = 0; y − 1 = 0 is shown at the top on the back of this sheet. -
Chapter 14 Locus and Construction
14365C14.pgs 7/10/07 9:59 AM Page 604 CHAPTER 14 LOCUS AND CONSTRUCTION Classical Greek construction problems limit the solution of the problem to the use of two instruments: CHAPTER TABLE OF CONTENTS the straightedge and the compass.There are three con- struction problems that have challenged mathematicians 14-1 Constructing Parallel Lines through the centuries and have been proved impossible: 14-2 The Meaning of Locus the duplication of the cube 14-3 Five Fundamental Loci the trisection of an angle 14-4 Points at a Fixed Distance in the squaring of the circle Coordinate Geometry The duplication of the cube requires that a cube be 14-5 Equidistant Lines in constructed that is equal in volume to twice that of a Coordinate Geometry given cube. The origin of this problem has many ver- 14-6 Points Equidistant from a sions. For example, it is said to stem from an attempt Point and a Line at Delos to appease the god Apollo by doubling the Chapter Summary size of the altar dedicated to Apollo. Vocabulary The trisection of an angle, separating the angle into Review Exercises three congruent parts using only a straightedge and Cumulative Review compass, has intrigued mathematicians through the ages. The squaring of the circle means constructing a square equal in area to the area of a circle. This is equivalent to constructing a line segment whose length is equal to p times the radius of the circle. ! Although solutions to these problems have been presented using other instruments, solutions using only straightedge and compass have been proven to be impossible. -
Analytic Geometry
INTRODUCTION TO ANALYTIC GEOMETRY BY PEECEY R SMITH, PH.D. N PROFESSOR OF MATHEMATICS IN THE SHEFFIELD SCIENTIFIC SCHOOL YALE UNIVERSITY AND AKTHUB SULLIVAN GALE, PH.D. ASSISTANT PROFESSOR OF MATHEMATICS IN THE UNIVERSITY OF ROCHESTER GINN & COMPANY BOSTON NEW YORK CHICAGO LONDON COPYRIGHT, 1904, 1905, BY ARTHUR SULLIVAN GALE ALL BIGHTS RESERVED 65.8 GINN & COMPANY PRO- PRIETORS BOSTON U.S.A. PEE FACE In preparing this volume the authors have endeavored to write a drill book for beginners which presents, in a manner conform- ing with modern ideas, the fundamental concepts of the subject. The subject-matter is slightly more than the minimum required for the calculus, but only as much more as is necessary to permit of some choice on the part of the teacher. It is believed that the text is complete for students finishing their study of mathematics with a course in Analytic Geometry. The authors have intentionally avoided giving the book the form of a treatise on conic sections. Conic sections naturally appear, but chiefly as illustrative of general analytic methods. Attention is called to the method of treatment. The subject is developed after the Euclidean method of definition and theorem, without, however, adhering to formal presentation. The advan- tage is obvious, for the student is made sure of the exact nature of each acquisition. Again, each method is summarized in a rule stated in consecutive steps. This is a gain in clearness. Many illustrative examples are worked out in the text. Emphasis has everywhere been put upon the analytic side, that is, the student is taught to start from the equation. -
Analysis of the Cut Locus Via the Heat Kernel
Unspecified Book Proceedings Series Analysis of the Cut Locus via the Heat Kernel Robert Neel and Daniel Stroock Abstract. We study the Hessian of the logarithm of the heat kernel to see what it says about the cut locus of a point. In particular, we show that the cut locus is the set of points at which this Hessian diverges faster than t−1 as t & 0. In addition, we relate the rate of divergence to the conjugacy and other structural properties. 1. Introduction Our purpose here is to present some recent research connecting behavior of heat kernel to properties of the cut locus. The unpublished results mentioned below constitute part of the first author’s thesis, where they will proved in detail. To explain what sort of results we have in mind, let M be a compact, connected Riemannian manifold of dimension n, and use pt(x, y) to denote the heat kernel for 1 the heat equation ∂tu = 2 ∆u. As a special case of a well-known result due to Varadhan, Et(x, y) ≡ −t log pt(x, y) → E(x, y) uniformly on M × M as t & 0, where E is the energy function, given in terms of the Riemannian distance by 1 2 E(x, y) = 2 dist(x, y) . Thus, (x, y) Et(x, y) can be considered to be a geomet- rically natural mollification of (x, y) E(x, y). In particular, given a fixed x ∈ M, we can hope to learn something about the cut locus Cut(x) of x by examining derivatives of y Et(x, y). -
A Locus in Human Extrastriate Cortex for Visual Shape Analysis
A Locus in Human Extrastriate Cortex for Visual Shape Analysis Nancy Kanwisher Harvard University Roger P. Woods, Marco Iacoboni, and John C. Mazziotta Downloaded from http://mitprc.silverchair.com/jocn/article-pdf/9/1/133/1755424/jocn.1997.9.1.133.pdf by guest on 18 May 2021 University of California, Los Angeles Abstract Positron emission tomography (PET) was used to locate an fusiform gyms) when subjects viewed line drawings of area in human extrastriate cortex that subserves a specific 3dimensional objects compared to viewing scrambled draw- component process of visual object recognition. Regional ings with no clear shape interpretation. Responses were Seen blood flow increased in a bilateral extrastriate area on the for both novel and familiar objects, implicating this area in inferolateral surface of the brain near the border between the the bottom-up (i.e., memory-independent) analysis of visual occipital and temporal lobes (and a smaller area in the right shape. INTRODUCTION 1980; Glaser & Dungelhoff, 1984). Such efficiency and automaticity are characteristic of modular processes (Fo- Although neurophysiological studies over the last 25 dor, 1983). Second, abilities critical for survival (such as years have provided a richly detailed map of the 30 or rapid and accurate object recognition) are the ones most more different visual areas of the macaque brain (Felle- likely to be refined by natural selection through the man & Van Essen, 1991), the mapping of human visual construction of innate and highly specialized brain mod- cortex -
The Cut Locus of Riemannian Manifolds: a Surface of Revolution
KMITL Sci. Tech. J. Vol.16 No.1 Jan-Jun. 2016 The cut locus of Riemannian manifolds: a surface of revolution Minoru Tanaka Department of Mathematics, Tokai University, Hiratsuka City, Kanagawa Pref. 259- 1292, Japan Abstract This article reviews the structure theorems of the cut locus for very familiar surfaces of revolution. Some properties of the cut locus of a point of a Riemannian manifold are also discussed. Keywords: Riemannian manifolds, surface of revolution, homeomorphic 1. Definition of a cut point and the cut locus Let γ :[0,aM ] → denote a minimal geodesic segment emanating from a point p on a complete connected Riemannian manifold M. The end point γ (a) is called a cut point of p along the minimal geodesic segment γ if any geodesic extension γ :[0,bM ] → , where b > a, of γ is not minimal anymore. Definition 1.1 The cut locus Cp of a point p is the set of all cut points of p along minimal geodesic segments emanating from p. It is very difficult to determine the structure of the cut locus of a point in a Riemannian manifold. The cut locus for a smooth surface is not a graph anymore, although it was proved by Myers in [1] and [2] that the cut locus of a point in a compact real analytic surface is a finite graph. In fact, Gluck and Singer [3] proved that there exists a 2-sphere of revolution admitting a cut locus with infinitely many branches. Their result implies that one cannot improve the following Theorem 1.3 without any additional assumption. -
ANALYTIC GEOMETRY - GOOD PROBLEMS from Alex Pintilie
ANALYTIC GEOMETRY - GOOD PROBLEMS from Alex Pintilie Together: 1)a) Consider the fixed points A(-a,0) and B(a,0). Find the equation of the locus of the points M with the property MA2 - MB2 = k, where k is a constant. Identify the locus. b) Consider the points A (-2, 0) B(2,0). Find the equation of the locus of the points M with the property MA2 - MB2 = 12. Draw a diagram. 2)a) Consider the fixed points A(-a,0), B(a,0). Find the equation of the locus of the points M with the property MA = k MB, where k is a constant. Identify the locus. b) Consider the fixed points A(-4,0), B(4,0). Find the equation of the locus of the points M with the property MA = 2 MB. Draw a diagram. 2 2 2 2 3) Consider the concentric circles with equations x y 4 and x y 9. A radius from the centre O intersects the inner circle at P and the outer circle at Q. The line parallel to the x- axis through P meets the line parallel to the y-axis through Q at the point R. Prove that R lies on x2 y2 1 the ellipse 9 4 . Class work: 1) Let P be a variable point on the line x=1. We construct the triangle OPQ with O the origin, O=90o, OP=OQ. Find the locus of the point Q. A 2) For the equilateral triangle ABC, side BC is the diameter of a semicircle. -
On the Compatibility of Derived Structures on Critical Loci
University of Pennsylvania ScholarlyCommons Publicly Accessible Penn Dissertations 2019 On The Compatibility Of Derived Structures On Critical Loci Antonijo Mrcela University of Pennsylvania, [email protected] Follow this and additional works at: https://repository.upenn.edu/edissertations Part of the Mathematics Commons Recommended Citation Mrcela, Antonijo, "On The Compatibility Of Derived Structures On Critical Loci" (2019). Publicly Accessible Penn Dissertations. 3441. https://repository.upenn.edu/edissertations/3441 This paper is posted at ScholarlyCommons. https://repository.upenn.edu/edissertations/3441 For more information, please contact [email protected]. On The Compatibility Of Derived Structures On Critical Loci Abstract We study the problem of compatibility of derived structures on a scheme which can be presented as a critical locus in more than one way. We consider the situation when a scheme can be presented as the critical locus of a function w∈?(S) and as the critical locus of the restriction w|ₓ∈?(X) for some smooth subscheme X⊂S. In the case when S is the total space of a vector bundle over X, we prove that, under natural assumptions, the two derived structures coincide. We generalize the result to the case when X is a quantized cycle in S and also give indications how to proceed when X⊂S is a general closed embedding. Degree Type Dissertation Degree Name Doctor of Philosophy (PhD) Graduate Group Mathematics First Advisor Tony Pantev Keywords Batalin–Vilkovisky formalism, compatibility of derived structures, -
Treatise on Conic Sections
OF CALIFORNIA LIBRARY OF THE UNIVERSITY OF CALIFORNIA fY OF CALIFORNIA LIBRARY OF THE UNIVERSITY OF CALIFORNIA 9se ? uNliEHSITY OF CUIFORHU LIBRARY OF THE UNIVERSITY OF CUIfORHlA UNIVERSITY OF CALIFORNIA LIBRARY OF THE UNIVERSITY OF CALIFORNIA APOLLONIUS OF PERGA TREATISE ON CONIC SECTIONS. UonDon: C. J. CLAY AND SONS, CAMBRIDGE UNIVERSITY PRESS WAREHOUSE, AVE RIARIA LANE. ©Inaooh): 263, ARGYLE STREET. lLftp>is: P. A. BROCKHAUS. 0fto goTit: MACMILLAN AND CO. ^CNIVERSITT• adjViaMai/u Jniuppus 9lnlMus%^craticus,naufmato cum ejcctus aa UtJ ammaScrudh Geainetncn fJimmta defer,pta, cxcUnwimJIe cnim veiiigia video. coMXiXcs ita Jiatur^hcnc fperemus,Hominnm APOLLONIUS OF PEEGA TEEATISE ON CONIC SECTIONS EDITED IN MODERN NOTATION WITH INTRODUCTIONS INCLUDING AN ESSAY ON THE EARLIER HISTORY OF THE SUBJECT RV T. L. HEATH, M.A. SOMETIME FELLOW OF TRINITY COLLEGE, CAMBRIDGE. ^\€$ .•(', oh > , ' . Proclub. /\b1 txfartl PRINTED BY J. AND C. F. CLAY, AT THE UNIVERSITY PRESS. MANIBUS EDMUNDI HALLEY D. D. D. '" UNIVERSITT^ PREFACE. TT is not too much to say that, to the great majority of -*- mathematicians at the present time, Apollonius is nothing more than a name and his Conies, for all practical purposes, a book unknown. Yet this book, written some twenty-one centuries ago, contains, in the words of Chasles, " the most interesting properties of the conies," to say nothing of such brilliant investigations as those in which, by purely geometrical means, the author arrives at what amounts to the complete determination of the evolute of any conic. The general neglect of the " great geometer," as he was called by his contemporaries on account of this very work, is all the more remarkable from the contrast which it affords to the fate of his predecessor Euclid ; for, whereas in this country at least the Elements of Euclid are still, both as regards their contents and their order, the accepted basis of elementary geometry, the influence of Apollonius upon modern text-books on conic sections is, so far as form and method are concerned, practically nil. -
Straight Lines
Chapter 10 STRAIGHT LINES 10.1 Overview 10.1.1 Slope of a line If θ is the angle made by a line with positive direction of x-axis in anticlockwise direction, then the value of tan θ is called the slope of the line and is denoted by m. The slope of a line passing through points P(x1, y1) and Q (x2, y2) is given by y− y m =tan θ = 2 1 x2− x 1 10.1.2 Angle between two lines The angle θ between the two lines having slopes m1 and m2 is given by ()m− m tanθ= ± 1 2 1+ m1 m 2 m1− m 2 If we take the acute angle between two lines, then tan θ = 1+ m1 m 2 If the lines are parallel, then m1 = m2. If the lines are perpendicular, then m1m2 = – 1. 10.1.3 Collinearity of three points If three points P (h, k), Q (x1, y1) and R (x2,y2) y− k y − y are such that slope of PQ = slope of QR, i.e., 1= 2 1 x1− h x 2 − x 1 or (h – x1) (y2 – y1) = (k – y1) (x2 – x1) then they are said to be collinear. 10.1.4 Various forms of the equation of a line (i) If a line is at a distance a and parallel to x-axis, then the equation of the line is y = ± a. (ii) If a line is parallel to y-axis at a distance b from y-axis then its equation is x = ± b 18/04/18 166 EXEMPLAR PROBLEMS – MATHEMATICS (iii) Point-slope form : The equation of a line having slope m and passing through the point (x0, y0) is given by y – y0 = m (x – x0) (iv) Two-point-form : The equation of a line passing through two points (x1, y1) and (x2, y2) is given by y2− y 1 y – y1 = (x – x1) x2− x 1 (v) Slope intercept form : The equation of the line making an intercept c on y-axis and having slope m is given by y = mx + c Note that the value of c will be positive or negative as the intercept is made on the positive or negative side of the y-axis, respectively. -
Teaching Locus with a Conserved Property by Integrating Mathematical Tools and Dynamic Geometric Software
Teaching locus with a conserved property by integrating mathematical tools and dynamic geometric software Moshe Stupel, Ruti Segal & Victor Oxman Shaanan College, Haifa, Israel [email protected] [email protected] [email protected] e present investigative tasks that concern loci, which integrate the use Wof dynamic geometry software (DGS) with mathematics for proving the obtained figures. Additional conditions were added to the loci: ellipse, parabola and circle, which result in the emergence of new loci, similar in form to the original loci. The mathematical relation between the parameters of the original and new loci was found by the learners. A mathematical explanation for the general case, using the ‘surprising’ results obtained in the investigative tasks, is presented. Integrating DGS in mathematics instruction fosters an improved teaching and learning process. Introduction A conserving property may be used to solve different problems in mathematics and the identification of such a property leads to a complete and deep understanding of mathematical concepts and the relationships between them. The locus, according to this definition, conserves a certain property and can therefore be used to prove a wide variety of problems and even serve in the execution of construction problems using a straightedge and a compass, as Australian Senior Mathematics Journal vol. 30 no. 1 has been done in mathematics since antiquity. Loci can be divided into two groups: 1. Essential loci, such as: the straight line, parallel lines, the mid perpendicular of a segment, an angle bisector, the circle, the parabola, the ellipse and the hyperbola. 2. Loci which are a result of the essential loci or loci obtained as a result of satisfying several mathematical conditions. -
Math 137 Notes: Undergraduate Algebraic Geometry
MATH 137 NOTES: UNDERGRADUATE ALGEBRAIC GEOMETRY AARON LANDESMAN CONTENTS 1. Introduction 6 2. Conventions 6 3. 1/25/16 7 3.1. Logistics 7 3.2. History of Algebraic Geometry 7 3.3. Ancient History 7 3.4. Twentieth Century 10 3.5. How the course will proceed 10 3.6. Beginning of the mathematical portion of the course 11 4. 1/27/16 13 4.1. Logistics and Review 13 5. 1/29/16 17 5.1. Logistics and review 17 5.2. Twisted Cubics 17 5.3. Basic Definitions 21 5.4. Regular functions 21 6. 2/1/16 22 6.1. Logistics and Review 22 6.2. The Category of Affine Varieties 22 6.3. The Category of Quasi-Projective Varieties 24 7. 2/4/16 25 7.1. Logistics and review 25 7.2. More on Regular Maps 26 7.3. Veronese Maps 27 7.4. Segre Maps 29 8. 2/5/16 30 8.1. Overview and Review 30 8.2. More on the Veronese Variety 30 8.3. More on the Segre Map 32 9. 2/8/16 33 9.1. Review 33 1 2 AARON LANDESMAN 9.2. Even More on Segre Varieties 34 9.3. Cones 35 9.4. Cones and Quadrics 37 10. 2/10/15 38 10.1. Review 38 10.2. More on Quadrics 38 10.3. Projection Away from a Point 39 10.4. Resultants 40 11. 2/12/16 42 11.1. Logistics 42 11.2. Review 43 11.3. Projection of a Variety is a Variety 44 11.4.