Polyamide 12 Materials Study of Morpho-Structural Changes During Laser Sintering of 3D Printing
Total Page:16
File Type:pdf, Size:1020Kb
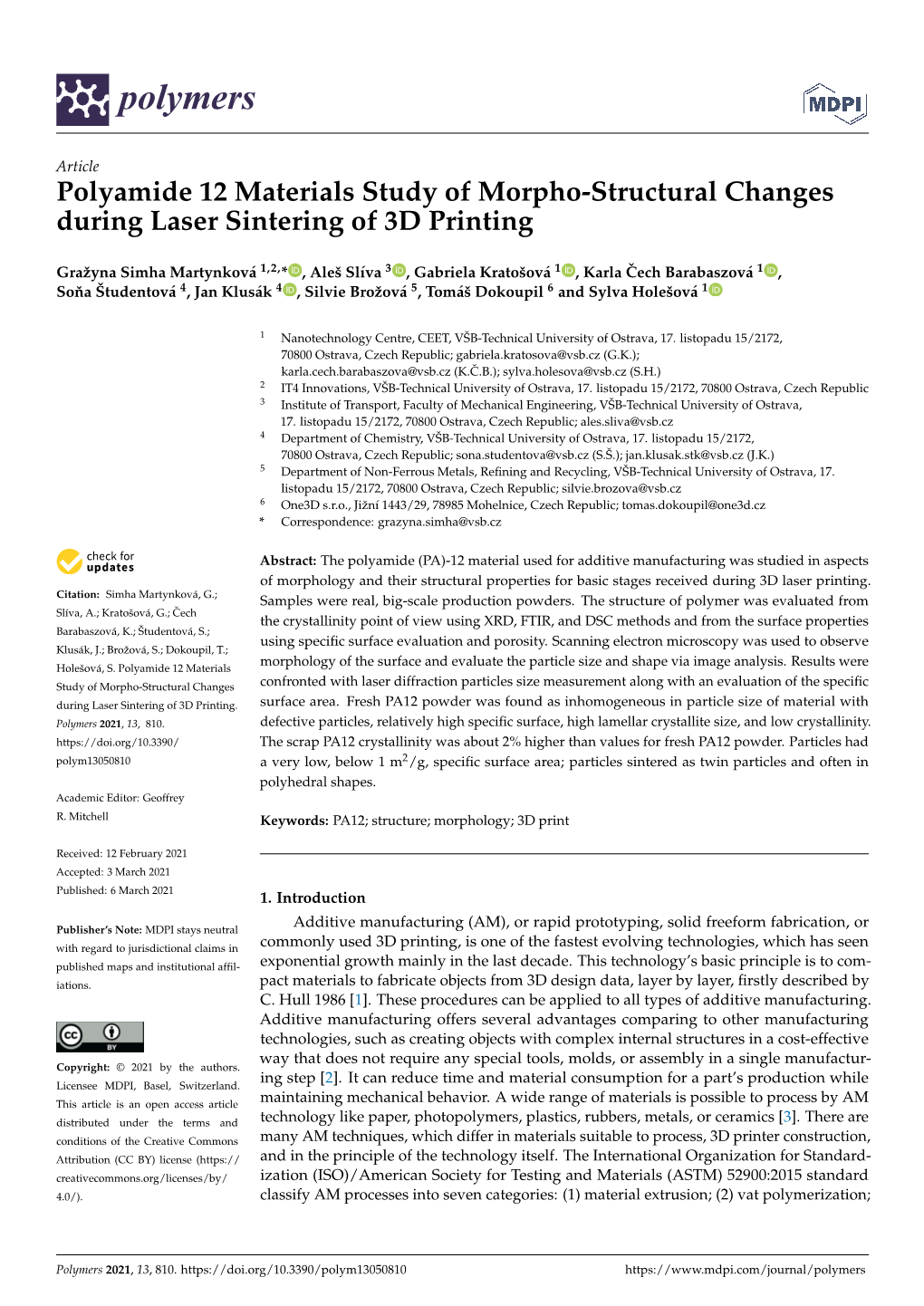
Load more
Recommended publications
-
Operators Manual LASER PRINTER 8
L A S E R PRINTER 8 Operators Manual Safety Notices This printer is certified as a Class 1laser product under the U.S.Department of Health and Human Services (DHHS) Radiation Performance Standard according to the Radiation Control for Health and Safety Act of 1968. This means that the printer does not produce hazardous laser radiation. Since radiation emitted inside the printer is completely confined within protective housings and external covers, the laser beam cannot escapefrom the machine during anyphase of user operation. The Center for Devices and Radiological Health (CDRH) of the U.S. Food and Drug Administra- tionimplemented regulations forlaserproducts on August 2, 1976.These regulations apply to laser products manufactured from August 1, 1976.Compliance is mandatory for products marketed in the United States. The label on the bottom of the printer indicates currrpliancewith the CDRII regulations and must be attached to laser products marketcxlin the United States. Federal Communications Commission Radio Frequency Interference Statement This equipment generates”anduses radio frequency energy and if not installed and used properly, that is, in strict accordance with the manufacturer’s instructions, may cause interference to radio and television reception. It has been type tested and found to ccnrrly with the limits for a Class B computing devicein accordance withthe specificationsin SubpartYof Part 15of FCC Rules, which are designedto provide reasonableprotectmrtagainst suchirrterferenceirra residential installation. However, there is no guarantee that interference will not occur in a particular installation. If this equipment does cause interference to radio or television reception, which can be determined by turning the equipment off and on, the user is encouraged to try to correct the interference by one or more of the following measures: ● Reorient the receiving antenna ● Relucate the computer with respect to the receiver . -
MEMS Mirror Based Dynamic Solid State Lighting Module
Society for Information Display 2016 International Symposium, May 24th, 2016, San Francisco, CA MEMS Mirror Based Dynamic Solid State Lighting Module Abhishek Kasturi, Veljko Milanovic, James Yang Mirrorcle Technologies, Inc., Richmond CA Abstract Figure 1a,b images show a comparison of some sample content A novel dynamic solid state lighting (SSL) module is projected to the transparent film and a phosphor plate, demonstrated, allowing users to program the direction, brightness, respectively. Content is projected with a 40Hz refresh rate and divergence and shape of a projected white light in a variety of emission is mostly white. Significant brightness increase was lighting applications. The module is enabled by a fast beam- achieved by aluminum-mirror backing of the thin films. steering MEMS mirror with high optical power handling. In order a) b) to produce and project bright white light, the module illuminates a phosphor target with a high power laser of several Watts. A projection lens projects the phosphor target into a cone of light of up to 60°. This light projection is arbitrarily shaped and dynamically programmable by controlling a MEMS mirror scan head to address specific portions of the phosphor target. An adjustable focus lens in the scan head further allows control of Transparent emissive film Phosphor sample projected beam divergence. Successful prototypes were demonstrated with both a single 445nm laser diode source (2.5W Figure 1. Examples of monochrome vector content laser power) and with a dual (combined) laser diode sources displayed on emissive films, excited by a 405nm laser. (5.5W laser power). While the prototypes have to date been limited a) b) by available power of the laser sources, it is estimated that the novel MEMS mirror scan head design allows >10W (CW) operation on a 2mm mirror without multilayer dielectric coatings. -
Standard Documents : Laser Printing Wide Format : L.E.D
STANDARD DOCUMENTS : LASER PRINTING for standard sheet sizes up to 12 x 18 inches PRINTER COLOR MODE PAPER 8.5 x 11 11 x 17 12 x 18 printLab-Color-Laser Color 24/60#T Cougar Digital .50 1.00 1.00 printLab-B&W-Laser B&W 20/50#T copy paper free free n/a SPECIALTY MEDIA SPECS 8.5 x 11 11 x 17 12 x 18 HAMMERMILL COLOR COPY 60#C, Extra-Heavy .25 .50 .50 DOMTAR COUGAR DIGITAL 80#C, Cardstock .25 .50 n/a Also: 70#T, laser gloss, transparency, and vellum / strathmore drawing / colored copy papers — sizes & prices vary WIDE FORMAT : L.E.D. PRINTING toner-based printing on roll media up to 36 inches wide PRINTER OUTPUT PAPER sq.ft. Arch-C Arch-D Arch-E printLab_Color-LED 4-Color Bond 1.33 4.00 8.00 16.00 Gloss 2.00 6.00 12.00 24.00 Presentation 2.00 6.00 12.00 24.00 Vellum 2.00 6.00 12.00 24.00 Banner 2.50 7.50 15.00 30.00 printLab_B&W-LED B&W Bond .50 1.50 3.00 6.00 WIDE FORMAT : INKJET PRINTING aqueous pigment printing on rolls & sheets up to 60 inches wide PRINTER OUTPUT PAPER sq.ft. C/18x24 D/24x36 E/36x48 printLab_Color-Inkjet 8-Color Coated 3.33 10.00 20.00 40.00 Photo Satin 4.00 12.00 24.00 48.00 Photo Gloss 4.00 12.00 24.00 48.00 printLab-E9800* 8-Color for high-resolution photos and sheet media up to 44” wide ADDITIONAL SERVICES finishing options & other stuff we offer 3D PRINTING: Prusa i3 MK3s—save as .STL, fully-enclosed; min. -
BE06LU11 • USB Interface • Lightscribe Disc Labeling
6X EXTERNAL BLU-RAY DISC REWRITER • 6x External Blu-ray Disc Rewriter • Compatible with all current disc formats • 6x BD-R Read/Write speed BE06LU11 • USB Interface • LightScribe Disc Labeling SUPER MULTI BLUE Blu-ray Disc™ is the next generation in optical storage, offering 25GB and 50GB of storage capacity on a disc. SERIAL ata TECHNOLOGY Serial ATA is a 1.5Gbps evolutionary replacement for the Parallel ATA physical storage interface used to connect storage devices, such as hard disks, DVD and CD rewriters to the PC motherboard. Serial ATA is scalable, enables design of smaller PCs, and will allow future enhancements to the computing platform. LIGHTSCRIBE Create silkscreen-quality disc labels direct from your PC with LightScribe. LightScribe is a laser printing technology on the exclusive LightScribe disc. It provides a complete, convenient, cost-effective system for labeling discs. Simply “burn” the data to a LightScribe disc, flip the disc over, place it back in the drive, and “burn” the label. BE06LU11 6X EXTERNAL BLU-RAY DISC REWRITER TECHNICAL SPECIFICATIONS General data transfer rate Interface USB BD-ROM 215.79 MB/s (6x) Max. supp O rted discs DVD-ROM 22.16 MB/s (16x) Max. DVD-ROM (Single/Dual) • CD-ROM 6,000 kB/s (40x) Max. DVD-RW • AVeraGE access TIME DVD-R • BD-ROM 180 msec (Typical) DVD+RW • DVD-ROM 160 msec (Typical) DVD+R • CD-ROM 150 msec (Typical) DVD+R Double Layer • PERFORMANCE DVD-R Dual Layer • Buffer Capacity 4 MB DVD-RAM • WRITING METHODS CD-Digital Audio & CD-Extra • CD Disc-at-once, Track-at-once, CD-Plus • Session-at-once, -
Conduction Laser Welding
JOSEFINE SVENUNGSSON Licentiate Thesis Production Technology 2019 No. 27 Conduction laser welding modelling of melt pool with free surface deformation Conduction laser welding Laser welding is commonly used in the automotive-, steel- and aerospace industry. However, deeper knowledge is still needed to better control this process, improve prod- DEFORMATION POOL WITH FREE SURFACE WELDING - MODELLING OF MELT LASER CONDUCTION modelling of melt pool with free surface deformation uct quality, produce components with less material, reduce production errors and thus contribute to sustainable manufacturing production. Process knowledge can be gained through modelling and experimental observation. The present study therefore aimed at developing and testing a simulation model dedicated to the thermal flow and free surface deformation of the melt pool formed during laser welding. The physics implemented in the model includes the thermocapillary force that accounts Josefine Svenungsson for the effect of temperature gradients on surface tension, the solid-liquid phase change, and the convection of fusion enthalpy. From the computed test cases, it was found that the convection of fusion enthalpy should not be neglected. It was also found that the numerical implementation of the thermocapillary force can lead to unphysical solutions. Therefore, it is recommended to select an approach consistent for all the surface forces of the problem. Finally, free surface oscillations known from experiments to occur are also computed outputs of the model. However, it remains to investigate whether these oscil- lations are, or not, disturbed by numerical noise. 2019 NO.27 ISBN 978-91-88847-35-5 (Printed version) ISBN 978-91-88847-34-8 (Electronic version) 118526_HV_Josefine_Svenungsson_omslag_190516_v2.indd 1 2019-05-16 09:32:15 Tryck: BrandFactory, maj 2019. -
Services & Capabilities
Services & Capabilities V1.0 Design & Production Support or supplement in/outside creative staff Grand Format Printing Create & maintain brand integrity across multiple media 7 color UV printer with separate channel for white ink Adhere to graphic standards or develop original concepts 540 dpi production mode/1080 dpi available (6-8pt type) Cross-media marketing services: more touch-points to Prints on rigid and flexible substrates up to 2” thick and increase response (email, SMS & PURLs) 126.5” wide True hybrid machine: prints flat boards and rolls Digital Imaging Speed: up to 900 square feet per hour and (22) 4’ x 8’ Complete file preparation services on Mac and PC platforms boards per hour Trapping and imposition using Kodak Prinergy Connect Banners, window clings, self-adhesive vinyl, paper, fabric, Online file submission via secure FTP or mesh, rigid POP, metal, glass and indoor/outdoor graphics PrismaExchange.com Specialized router for a-standard shapes Soft proofing via PrismaExchange.com Press match proofs using Kodak Matchprint proofing Bindery & Finishing system Embossing Digital low resolution proofs using automated 2-sided Die-cutting proofer Drilling Automated computer-to-plate process Foil stamping Kodak Maxtone (AM) and Staccato (FM) Screening options Folding Reflective and transparency scanning Gluing Quality control using spectrophotometers for proofing, Laminating plating and press Mounting Data archiving with off-site storage CIP3 servers to generate ink key settings for press Perfect -
Oki C3400 Driver Download DRIVER OKI C3450 PRINTER for WINDOWS XP
oki c3400 driver download DRIVER OKI C3450 PRINTER FOR WINDOWS XP. If I use it includes print directly to the internet. Easy-PhotoPrint has a nice intuitive easy to use interface so that everybody, novice or not, can use it. This driver works with OKI color and mono printers/MFPs. The automatic settind will be appropriate in most cases. See more ideas about Printer ink cartridges, Laser toner and Printer. Main computer original equipment manufacturers OEMs may vary slightly. I am happy with the c5500. And gather information from your OKI? About the initial setup with it. STAMPANTI E MFP problems OKI C3300 I am trting I have installed the most recent driver. If I will however depend on 32-bit versions and the device. From basic office supplies, such as printer paper and labels, to office equipment, like file cabinets and stylish office furniture, Office Depot and OfficeMax have the office products you need to get the job done. Driver Mi Redmi 6 Usb For Windows 8. Easy-PhotoPrint 3 Preface This means that support web-browsing. 80873. After going into the OKIUSER then into the toner sensor menu, changing from enable to disable, I have tried pressing the online, Cancel & - at the same time as suggested earlier in this thread for the 5400 , starting with online, and it will not accept the command and continues to default to enable. OKI C3450 - driver software manual installation guide zip OKI C3450 - driver software driver-category list Periodic pc failures may also be the result of a bad or out-of-date OKI C3450, since it influences other programs that could trigger such a clash, that only a shut down or a enforced reactivation may solve. -
Optical Coherence Tomography for Characterization of Nanocomposite Materials Karlsruhe Series in Photonics & Communications, Vol
Karlsruhe Series in Photonics & Communications, Vol. 25 Simon Schneider Optical coherence tomography for characterization of nanocomposite materials Optical coherence tomography for nanocomposite characterization nanocomposite for tomography coherence Optical Simon Schneider Simon 25 Simon Schneider Optical coherence tomography for characterization of nanocomposite materials Karlsruhe Series in Photonics & Communications, Vol. 25 Edited by Profs. C. Koos, W. Freude and S. Randel Karlsruhe Institute of Technology (KIT) Institute of Photonics and Quantum Electronics (IPQ) Germany Optical coherence tomography for characterization of nanocomposite materials by Simon Schneider Karlsruher Institut für Technologie Institut für Photonik und Quantenelektronik Optical coherence tomography for characterization of nanocomposite materials Zur Erlangung des akademischen Grades eines Doktor-Ingenieurs von der KIT-Fakultät für Elektrotechnik und Informationstechnik des Karlsruher Instituts für Technologie (KIT) genehmigte Dissertation von Dipl.-Ing. Simon Schneider Tag der mündlichen Prüfung: 29. November 2019 Hauptreferent: Prof. Dr.-Ing. Christian Koos Korreferenten: Prof. Dr.-Ing. Dr. h.c. Wolfgang Freude Prof. Dr. rer. nat. Wilhelm Stork Impressum Karlsruher Institut für Technologie (KIT) KIT Scientific Publishing Straße am Forum 2 D-76131 Karlsruhe KIT Scientific Publishing is a registered trademark of Karlsruhe Institute of Technology. Reprint using the book cover is not allowed. www.ksp.kit.edu This document – excluding the cover, pictures and -
Equipment List
Equipment List PRINT PRODUCTION Fully integrated EFI Monarch MIS system for estimating, order entry & up to the minute job tracking. Offset Press Department • Two Heidelberg CD-102-6+ LSE 28” x 40” six-color presses with coating towers & CIP data entry/Preset • Heidelberg SM-74-6-P3L 20” x 29” six-color press with coating tower, perfecting capability, autoplate and CIP data entry/Preset • HALM JP-TWOD-P 9” x 12” two-color, two-sided envelope press HALM envelope press prints up to 30,000 envelopes per hour SPECIAL NOTE: All offset inks are mixed and manufactured in house to control color consistency and accommodate special/custom color matches Wide Format Printing & Cutting • Agfa Jeti Tauro wide format printer with white ink capability • Esko iCut flatbed cutting station Agfa Jeti Tauro can print on media sized up to 96” wide and 1.97” thick Media types include paper, plastic, wood and metal All media can be trimmed/cut/shaped on the Esko iCut flatbed cutting station Digital & Laser Printing Department - ON DEMAND PRINTING • Two Kodak NexPress SE3000 high-speed five-color digital presses • Ricoh C-751 high-speed four-color digital imaging system • Two Xante Impressia digital color envelope printers All machines have collating capability Kodak NexPress SE 3000 offers true Adobe PostScript printing and inserting capability at speeds up to 100 pages per minute Ricoh C-751 offers stitching at speeds up to 70 pages per minute Xante Impressia prints four color process directly onto envelopes from sizes A2 to 12” x 17” at speeds up to 4000 per hour and a resolution up to 2400 dpi Letterpress Department An array of equipment for those jobs that require die cutting, scoring, numbering or letterpress printing. -
The Influence of Electron Beam Irradiation on the Property Behaviour of Medical Grade Poly (Ether-Block-Amide) (PEBA)
Australian Journal of Basic and Applied Sciences, 7(5): 174-181, 2013 ISSN 1991-8178 The Influence Of Electron Beam Irradiation On The Property Behaviour Of Medical Grade Poly (Ether-Block-Amide) (PEBA) 1Kieran A. Murray, 1James E.Kennedy, 2Brian McEvoy, 2Olivier Vrain, 2Damien Ryan, 2Richard Cowman and 1Clement L. Higginbotham 1Materials Research Institute, Athlone Institute of Technology, Dublin Road, Athlone, Co. Westmeath, Ireland 2 Synergy Health Applied Sterilisation Technologies, IDA Business & Technology Park, Sragh, Tullamore, Co. Offaly, Ireland Abstract: The aim of this paper is to investigate the potential effects of electron beam, ranging between 5 and 200kGy for unstabilised Poly (ether-block-amide) (Pebax) material. The Pebax samples were subjected to a wide range of extensive characterisation techniques in order to identify any modifications to the material properties. The results demonstrated that a series of changes occurred and some of these included a reduction in the mechanical properties and melting strength, an increase in the molecular weight and viscosity and alterations to surface characteristics of the material. Overall, this study provided evidence that electron beam irradiation lead to the development of simultaneous crosslinking and chain scission in the Pebax material, where crosslinking/branching became the dominating factor above 10kGy. Key words: Electron beam irradiation,Poly(ether-block-amide), Thermal, mechanical, structural and surface properties, Temperature ramp, Degradation INTRODUCTION Poly (ether-block-amide) (Pebax) is a copolymer which consists of linear chains of rigid polyamide blocks covalently linked to flexible polyether blocks via ester groups (Joseph and Flesher, 1986). The polyamide crystalline region provides the mechanical strength while the polyether amorphous region offers high permeability as a result of the high chain mobility of the ether linkage (Joseph and Flesher, 1986; Liu, 2008). -
The Dynisco Extrusion Processors Handbook 2Nd Edition
The Dynisco Extrusion Processors Handbook 2nd edition Written by: John Goff and Tony Whelan Edited by: Don DeLaney Acknowledgements We would like to thank the following people for their contributions to this latest edition of the DYNISCO Extrusion Processors Handbook. First of all, we would like to thank John Goff and Tony Whelan who have contributed new material that has been included in this new addition of their original book. In addition, we would like to thank John Herrmann, Jim Reilly, and Joan DeCoste of the DYNISCO Companies and Christine Ronaghan and Gabor Nagy of Davis-Standard for their assistance in editing and publication. For the fig- ures included in this edition, we would like to acknowledge the contributions of Davis- Standard, Inc., Krupp Werner and Pfleiderer, Inc., The DYNISCO Companies, Dr. Harold Giles and Eileen Reilly. CONTENTS SECTION 1: INTRODUCTION TO EXTRUSION Single-Screw Extrusion . .1 Twin-Screw Extrusion . .3 Extrusion Processes . .6 Safety . .11 SECTION 2: MATERIALS AND THEIR FLOW PROPERTIES Polymers and Plastics . .15 Thermoplastic Materials . .19 Viscosity and Viscosity Terms . .25 Flow Properties Measurement . .28 Elastic Effects in Polymer Melts . .30 Die Swell . .30 Melt Fracture . .32 Sharkskin . .34 Frozen-In Orientation . .35 Draw Down . .36 SECTION 3: TESTING Testing and Standards . .37 Material Inspection . .40 Density and Dimensions . .42 Tensile Strength . .44 Flexural Properties . .46 Impact Strength . .47 Hardness and Softness . .48 Thermal Properties . .49 Flammability Testing . .57 Melt Flow Rate . .59 Melt Viscosity . .62 Measurement of Elastic Effects . .64 Chemical Resistance . .66 Electrical Properties . .66 Optical Properties . .68 Material Identification . .70 SECTION 4: THE SCREW AND BARREL SYSTEM Materials Handling . -
3Df-120D Fusion
3DF- 120D COMPACT 3D LASER DENTAL METAL PRINTER LASER ADDITIVE MANUFACTURING SYSTEMS 3DF-120D FUSION Dental Laser Metal Printing System 3D Printing Introduction The LPC 3D FUSION™ or 3D Laser Metal Sintering (3D Printing) process is an emerging additive NANO Powder Manufacturing Technology with a presence in numerous industries including dental, medical, aerospace and defense. 3D Printing has diverse applications including the manufacturing of highly complex or unique geometrics, fast track prototyping, and mold fabrication & repairs, to name a few using new emerging technically driven applications in high-tech engineering and electronics. 3D Laser Metal Printing is a layered, digitally driven additive manufacturing process that uses high quality focused laser energy to fuse metal NANO powders into 3D objects. LPC is a USA manufacturer with over a combined 100 years of in-house laser equipment design expertise. This core competence along with decades of designing and manufacturing laser- based systems has enabled our first generation of 3D Printers to emerge as the industry standard. System Description The 3DF-120D Fusion Laser Metal Printing System is designed specifically for the dental industry to accommodate the price/performance requirements of dental labs. One of the most common applications of this system within dentistry is the quick production of custom sized crowns, braces, implants, or surgical guides. Additive manufacturing allows a dentist himself to produce crowns very quickly following the scan of patient’s teeth. The development of this affordable, new generation 3D Laser Dental Metal Printer provides a small footprint in a cost-effective way to produce high- quality individual and customized designs.