Railroad Collectibles
Total Page:16
File Type:pdf, Size:1020Kb
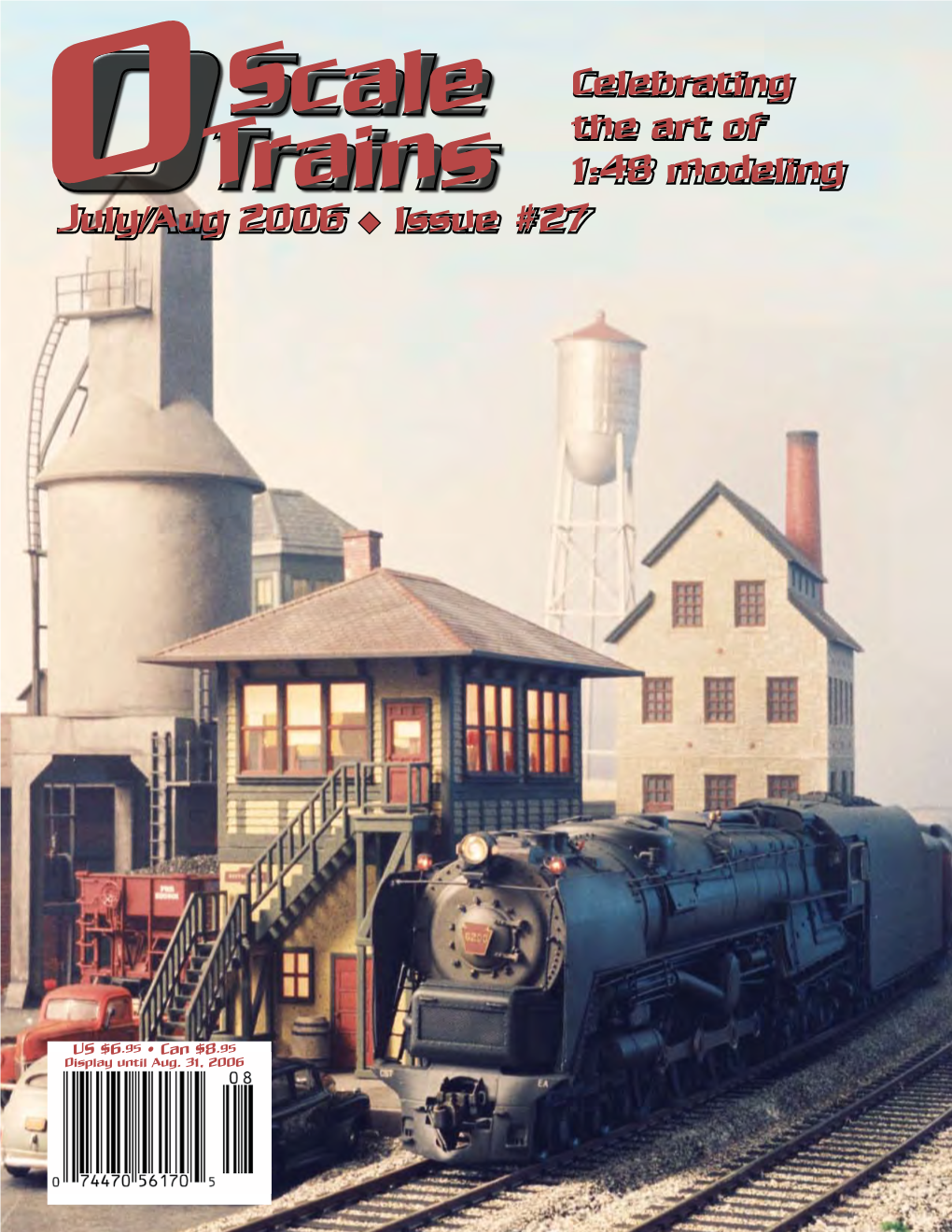
Load more
Recommended publications
-
Tlle Llotbox Youtla Model Railroading at It~ Finest!
TllE llOTBOX Youtla Model Railroading at it~ Finest! June 2()()1 l§§Ue jfJ-47 1l'hls Ke11tit: fta Alce PA llNSP Ill Naw Kexice Altd much merer I'll• .,,IJCIAI l'fl811CAf11JOM ., I'll• f'••M ASSOCIAl'IOlt ., MO••I aAIMIOAlt•U The HotBox On the Cover: P A4s 16 and 18 at the BNSF yard in Phoenix, Arizona on March 7, 2000.Nick Olek photo June 2001 (Inset) Minnesota Commercial RS27 318 idles in the back lot of their large Issue 347 roundhouse in the Midway District in St Paul, MN. Seen on July 23, 1999. Andy Inserra photo. Send Articles to: Charles Warczinsk:y 389 Gates Rd Sandusky MI 484 71 Editor: Charles W arczinsk:y [email protected] Inside this Issue: Layout Design Artist: Features: Andy Inserra • Land ofEnchantment -BNSF style Page6 Andy [email protected] • The Alco PA Page 13 • Photo Gallery Page 15 Contributions I Columns: We always need contributions in all forms. Please send the • Top7 Page 5 following in if you wish for the • LOASSB Page 10 staff to consider for an upcoming issue of The Hotbox. Departments: Feature Articles: • Directory Page3 This is what we really need. They • From the Tower Page4 can be from a half page to two • A word from the Editor Page 5 pages typed on anything related • A word from the Layout Design Artist Page5 to railroading, railfanning, model • Events Calendar Page 11 railroading, you get the idea. Page 12 Accompanying pictures are also • TAMR on the Web welcome. Columns: Another thing we can always use! If you wish to start one, please drop us a line. -
NYC Locos in S
S Scale NEW YORK CENTRAL ROLLING STOCK Compiled by Dick Karnes Locomotives Steam “Y” = currently available J-3a Hudson unpainted Standard Overland Models tender Inc. J-3a Hudson unpainted PT tender Overland Models Inc. J-3a Hudson painted Dreyfuss American Models Y Empire State Express H-6a unpainted USRA Overland Models Mikado Inc. H-10a painted Footboard River Raisin Models Mikado pilot H-10b painted Standard River Raisin Models Mikado pilot L-3b unpainted Omnicon Models Mohawk L-4a unpainted Omnicon Models Mohawk S-1b Niagara painted SouthWind Models B-62 painted 0-6-0 River Raisin Models Y Switcher (CR&I) U-3k unpainted USRA 0-8-0 Overland Models Switcher Inc. Diesel & Other Brill gas- unpainted brass Dayton Models electric and wood kit Budd RDC-1, - nickel-plated, Omnicon Models 2, and -3 unlettered EMD E-7A/B unpainted Overland Models Inc. EMD E-8/9 unpainted Overland Models Inc. A/B EMD E-8/9 A unpainted River Raisin Models EMD F-3 A/B unpainted Overland Models Inc. EMD FT A/B unpainted Overland Models Inc. EMD F-3 A/B painted/freight S Helper Service EMD F-3 A/B painted/passenger S Helper Service EMD F-7 A/B painted/freight S Helper Service EMD F-7 A/B unpainted River Raisin Models EMD F-7 A/B painted/passenger S Helper Service EMD GP-18 painted American Models Y EMD NW-2 unpainted pewter Railmaster Y kit EMD NW-2 unpainted Oriental Models EMD SW-1 unpainted Oriental Models EMD SW-7 unpainted Oriental Models EMD SW-7 unpainted pewter Railmaster Y kit EMD SW-9 painted S Helper Service EMD SW-9 unpainted Oriental Models EMD SW-1200 unpainted Oriental Models Alco RS-1 unpainted brass Locomotive Workshop kit Alco RS-1 unpainted pewter Railmaster Y kit Alco RS-2 unpainted pewter Railmaster Y kit Alco RS-3 painted/freight American Models Y Alco RS-3 unpainted Alco Models Alco RS-3 unpainted pewter Railmaster Y kit Alco S-2 unpainted pewter Railmaster Y kit Alco S-2 unpainted brass Overland Models Inc. -
Alco PA with Prime Mover 244
True Sound Project for Zimo Sounds designed by Heinz Daeppen US Diesel Seite 1 Version 200612 Alco PA with prime mover 244 Foto Wikipedia The Prototype The ALCO PA was a family of A1A-A1A diesel locomotives built to haul passenger trains. The locomotives were built in Schenectady, New York, in the United States by a partnership of the American Locomotive Company (ALCO) and General Electric (GE) between June 1946 and December 1953. Designed by General Electric's Ray Patten (along with their ALCO FA cousins), they were of a cab unit design; both cab-equipped lead A unit PA and cabless booster B unit PB models were built. While externally the PB models were slightly shorter than the PA model, they shared many of the same characteristics, both aesthetically and mechanically. However, they were not as reliable as EMD F-units. ALCO's designation of P indicates that they were geared for higher speeds and passenger use, whereas the F designation marks these locomotives as being geared primarily for freight use. However, beyond this their design was largely similar - aside from the PA/PB's both being larger A1A-A1A types with an even more striking nose - and many railroads used PA and FA locomotives for both freight and passenger service. Wikipedia True Sounds made in Switzerland True Sound Project for Zimo Sounds designed by Heinz Daeppen US Diesel Seite 2 Version 200612 Sound Project Information The sound project is made with genuine sound recordings of a prototype. F14 reduces the diesel motor sound to idling while maintaining the same speed. -
Proto-Sound 3.0
2014 HO MODEL TRAINS Proto-Sound® 3.0... THE RICHEST SET OF FEATURES IN MODEL RAILROADING! Whether you operate with a conventional transformer or in com- GREAT SMOKE They’ll run in perfect synchronization with each other at any mand mode with DCC or DCS™ (M.T.H.’s Digital Command Sys- Proto-Sound engines feature fan-driven ProtoSmoke™, the most speed. You can even set your lashup so only the lead engine’s tem), the Proto-Sound 3.0 system available in every locomotive in powerful smoke system in the hobby. You can vary the intensity bell and whistle will sound, as in real life multiple-unit operation. this catalog offers more realism, more fun, and more variety than with the smoke “volume” control on the locomotive or remotely any other locomotive control system in any scale. with any DCC or DCS controller. DCC Features VIVID ENGINE SOUNDS SYNCHRONIZED CHUFF AND PUFF Proto-Sound 3.0-equipped locomotives can be controlled in com- Proto-Sound features crystal-clear digital sounds. We strive to mand mode with any DCC-compliant command control system. Like a real steam engine, M.T.H. steamers feature puffs of smoke While you won’t have access to all of the incredible features of make our sounds as authentic as possible, using the charac- and steam chuff sounds synchronized with the drive wheels. Bet- Proto-Sound 3.0, you will have full DCC command control. This teristic whistle for a particular steam engine, for example. With ter than any other model train, an M.T.H. -
Rocky Mountaineer Unveils New Image! (CRO Exclusive Report)
Updated May 7, 2010 www.canadianrailwayobservations.com Rocky Mountaineer unveils new image! (CRO Exclusive Report) Hundreds of people gathered on April 19th, 2010 to celebrate Rocky Mountaineer’s 20th Anniversary at Rocky Mountaineer Station and to see the official unveiling and dedication of its new train design. The striking new train design, which features the company’s new gold and blue colours and Mountain logo made its debut in grand style, breaking through a 28 foot branded barrier at the west end of the Rocky Mountaineer Station. ―We are very excited to celebrate this momentous occasion and the great accomplishments along the way,‖ says Randy Powell, President and CEO of Rocky Mountaineer. ―The success of Rocky Mountaineer has been built on years of dedication and hard work and an unwavering commitment to provide our guests with unparalleled service and an unforgettable travel experience. We look forward to the future and to continued excellence as we embark on the next 20 years.‖ Yesterday’s event also included a special dedication of locomotive #8011 by Randy Powell, President and CEO of Rocky Mountaineer to Founder and Executive Chairman, Peter Armstrong. The dedication marks the epic journey of an entrepreneurs dream to turn a struggling rail service into an award-winning luxury train experience. Rocky Mountaineer offers 45 unique Canadian vacation packages and four spectacular rail routes through British Columbia and Alberta. This luxurious train travels by daylight through the wild beauty of Canada’s West and is the best way to experience the majestic Canadian Rockies. The Rocky Mountaineer also runs a three-hour journey with breathtaking scenery between Vancouver and Whistler, BC. -
Pn Set Description Msrp Class Sub Cat
PN SET DESCRIPTION MSRP CLASS SUB CAT CLUB 18228 Southern Pacific (canceled, made as 18228 Dash) Diesel AC4400 1996Land 18587 Nickel Plate Road "577", TMCC $349.95 Diesel Alco C420 1999Cla3 18588 Delaware & Hudson "412", TMCC $349.95 Diesel Alco C420 1999Cla3 18589 Lehigh Valley "409", TMCC $349.95 Diesel Alco C420 1999Cla3 18590 Nickel Plate Road "578", trad $249.95 Diesel Alco C420 1999Cla3 18591 Delaware & Hudson "411", trad $249.95 Diesel Alco C420 1999Cla3 18592 Lehigh Valley "410", trad $249.95 Diesel Alco C420 1999Cla3 28218 Lehigh Valley "407" $399.99 Diesel Alco C420 2004Cla1 28219 Seaboard "136" $399.99 Diesel Alco C420 2004Cla1 28243 Long Island "206" hi nose, scale $419.99 Diesel Alco C420 2006Vol1 28244 Norfolk & Western "417" hi nose, scale $419.99 Diesel Alco C420 2006Vol1 28505 Monon "505", TMCC $349.95 Diesel Alco C420 2000Cla1 28506 Monon "506", trad $249.95 Diesel Alco C420 2000Cla1 28507 New Haven "2556", TMCC $349.95 Diesel Alco C420 2000Cla1 28508 New Haven "2557", trad $249.95 Diesel Alco C420 2000Cla1 28515 21952 Service Station Special "1900-2000" Diesel Alco C420 2000Cla1 28516 Lehigh & Hudson River Railway "22" w/ case Diesel Alco C420 2000Unc JCP 18972 #2031 Rock Island A-A, (canceled), PW Series $599.95 Diesel Alco FA 1998Cla2 24544 New York Central FA-2 A-A, scale $599.99 Diesel Alco FA 2004Cla2 24548 Canadian National FPA-4 A-A, scale $599.99 Diesel Alco FA 2004Cla2 38147 Great Northern A-A, scale $499.99 Diesel Alco FA 2002Vol2 38176 Pennsylvania A-A, scale $499.99 Diesel Alco FA 2002Vol2 38182 Missouri -
Painting Railroad Cars Part 2 Indianapolis Fall O Scale Show Indianapolis Model Contest I Don’T Wanna Grow up JMRI for DCC Control Making Rocks Part 2 All-Nation Line
OO NEWS, REVIEWS, INFORMATION TO USE Painting Railroad Cars Part 2 Indianapolis Fall O Scale Show Indianapolis Model Contest I Don’t Wanna Grow Up JMRI for DCC control Making Rocks Part 2 All-Nation Line Vol. 1 No. 2 November/December 2013 The O Scale Resource November/December 2013 1 Bill Of Lading 2 Table of Contents Published Bi Monthly 3 Editorial 4 News and Reviews The Model Railroad Resource LLC 9 All-Nation Line Plymouth, Wisconsin The Bob Colson era Editors 18 Painting Railroad Cars Part 2 Glenn Guerra Dan Dawdy Some information on model paints 28 JMRI for DCC control Copy Editor Using the JMRI program for easy DCC Amy Dawdy programing 37 Making Rocks Part 2 November-December Gary Engle visits Dan to show how it’s done Vol 1 #2 45 The Indianapolis Fall O Scale Show 51 Contest Winners From The Indianapolis Show Welcome to the online O Scale Resource magazine. The magazine is 55 I Don’t Wanna Grow Up. presented in an easy to use format. The Dan looks at imagination in our modeling blue bar above the magazine has commands for previewing all the pages, 60 Dream City Railway advancing the pages forward or back, Roy James from England shows us his version of searching to go to a specific page, the holiday layouts we all remember as kids. enlarging pages, printing pages, 65 The O Scale Resource Classifieds enlarging the view to full screen, and downloading a copy to your computer. Front Cover Photo Keep up to date with new releases of The O Scale Resource Norm Pullan in Main sent in a photo of his model railroad based on local Click Here to sign up to receive an Email notice when we railroading in the North East. -
Pacific. ·Lie· S
qx APRIL, 1977 $1.00 Pacific. ALSO III THIS ISSUE: THE ROYAL s HUDSOII COMPLETES ITS UIlITED ·lIe· STATES TOUR, AIID MORE. r···NEVE'"RiiSS··ANOTHEii··piioiOGiiipiir- i DON'T EYER MISS ANOTHER RAILROAD EVENT! i LISTEN ON YOUR OWN SCANNER : Railroad Radio Scanning At Its Very Best i BEARCAT® I -" ,-, • I: ,'_I _"'·.. '''''0 ' RADIOS • --\ . " !.'i • The Bearcaf® Hand-Held Is BEARCAT • '"' , II the Ideal portable scanner for HAND-HELD . I access to public service and all . railroad broadcasts. Four frequencies can be monitored at a time, using crystals, with � 1 an eight-channel/second scan rate. Light � t emitting diodes show channels monitored. �, . SPECIAL OFFER: I $109.95 Four cryst.al certificates, with radio, $16. Extras@$5. • t• Th h e W ole World OPTIONAL ITEMS FOR SCANNERS Is At Your Of Scanning HAND HELD: Battery charger, AC adaptor, $8.95 each. Fingertips. The model 210 Is a Flexible rubber antenna, $7.50. Crystal certificates, $5.00. sophisticated scanning�� :Instrument�� with • .i BEARCAT MODEL 101: Mobile power supply kit, $39.95. the frequency versatility and the �operational3EI Im! ease that you've been dreaming about. Imagine selecting from all of the public service bands, local service frequencies and railroad Most scanning monitors use a : frequencies by simply pushing a tew buttons. You can forget both specific crystal to receive each crystals and programming forever. Pick the ten frequencies you frequency. The 101 does not. It want to scan and punch the numbers In on the keyboard. The large Is "synthesized. " With the 1 01 a decimal display reads out each frequency you've selected. -
HO-Scale Conversion List Handout
® HO-SCALE COUPLER CONVERSION LIST 7-8-21 The Coupler People Most of the below listings have conversion drawing and instructions on our web site at www.kadee.com/hocc.htm Newer models that have factory installed knuckle couplers are easily converted by using our standard head #148 or scale head #158 Whisker® Couplers. Always check the coupler heights with either our #205 or newer #206 Coupler Height Gauge. This coupler conversion list is our suggested starting coupler for the conversion. (Typically requiring the least modification to a model utilizing our newest couplers even though other couplers also work for the model). Our conversion’s based on only one model from a production run, there may be inconsistencies in a model’s production run that require a different coupler or model modifications to achieve the proper coupler height for coupler function. ACCURAIL ARISTO - CRAFT ATHEARN "GENESIS" All Rolling Stock .........................................NO.5® or 148 STEAM STEAM AHM (RIVAROSSI) All Steam Locomotives (Generic) ..............NO.5® or 148 USRA 2-8-2 Lt. Mikado (road pilot) .............................. STEAM ATHEARN .........................................36 Pilot, NO.5® or 148 Tender 0-4-0 Dockside .................. (Early model) 34 Pilot, 31 Rear STEAM USRA 2-8-2 Lt. Mikado (step pilot) .............................. 0-4-0 Dockside .................(Late model) 34 Pilot, 34 Rear 0-4-2 T "Little Monster" ..............................NO.5® or 148 .........................................34 Pilot, NO.5® or 148 Tender 0-4-0 Switcher w/Tender ......................................... 37 0-6-0 Switcher with Tender ........................NO.5® or 148 4-6-2 Pacific .....................36 Pilot, NO.5® or 148 Tender 0-8-0 Switcher .................38 Pilot, NO.5® or 148 Tender 4-6-2 Pacific ...............................................NO.5® or 148 4-8-2 Mt-4 ..................................................NO.5® or 148 2-4-0 Bowker (Tender only) .................................... -
All-Time Model List
All-time, All-scale NICKEL PLATE ROAD and Predecessor Railroads MODEL LIST Prepared by Nickel Plate Road Historical & Technical Society (nkphts.org) Modeling Committee Version 2.16 updated February 27, 2019 Note: Models in this list are either built to closely resemble NKP or predecessor railroad prototypes or come factory painted and lettered for NKP or a predecessor railroad. Three-rail models are included if they can be converted to scale with new trucks and couplers. Blanks or listings in red signify a need more information or confirmation. Listing marked with an asterisk* were done as NKPHTS Special Projects. Photos of some of the models appear in a gallery at the end of these listings. – Tony Koester, NKPHTS Modeling Coordinator Freight cars Z scale Open hopper Z Mfgr./importer Car description Car nos. Constructio Kit or RTR/ Photo Notes n Mfgr. no. link Full Throttle 2-bay offset-size 61224, 61288 Plastic RTR/(2-pk.) FT-3018-1 Full Throttle 2-bay offset-size 61203, 61236 Plastic RTR/(2-pk.) FT-3018-2 Freight cars N scale Boxcars N Mfgr./importer Car description Car nos. Constructio Kit or RTR/ Photo Notes n Mfgr. no. link American Z 40-ft. single- 8123 RTR Lines sheathed war- emergency Athearn 36-ft. double- 10580, 10755 Plastic RTR/10968, sheathed 10967 Atlas 1932 AAR 40-ft. 13319, Plastic RTR/36447A Also 50000754–56 13333, 13399 and B Atlas USRA 40-ft. 27826, 27914 Plastic RTR/45862– rebuilt steel 63 Atlas 40-ft. PS-1 16525 Plastic RTR/5787B Experimental HS Service paint Atlas 40-ft. -
Scale Trains
Celebrating Scale the art of MAGAZINE Trains 1:48 modeling O u July/August 2009 Issue #45 US $6.95 • Can $8.95 Display until August 31, 2009 Celebrating the art of 1:48 modeling Issue #45 Scale July/August 2009 Vol. 8 - No.4 Editor-in-Chief/Publisher Joe Giannovario Trains MAGAZINE [email protected] O Features Art Director Jaini Giannovario [email protected] 4 The Aspen & Western Ry — Red Wittman An On30 layout with many scratchbuilt structures. Managing Editor 12 Chicago March Meet Contest Photos Mike Cougill Part 2 of our contest coverage. [email protected] 15 A New Roundhouse for the Clover Leaf — Warner Clark Building a roundhouse, even to P48 specs, isn’t that difficult. Advertising Manager Jeb Kriigel 21 Greg Heier 1941 - 2009 [email protected] O Scale News editor passes away in April. Customer 23 Detailing Die-Cast Locomotives Part 2 — Joe Giannovario Service Redetailing the tender required the kindness of friends. Spike Beagle 29 Installing Lighted Train Indicators — Charles Morrill Complaints Add this slick detail to your SP and UP locomotives. L’il Bear 31 Modeler’s Trick — Bill Davis CONTRIBUTORS Here’s an inexpensive way to sort and store your strip stock. TED BYRNE GENE CLEMENTS CAREY HINch ROGER C. PARKER 34 Atlas Postwar AAR Boxcar Upgrade — Larry Kline Improve and refine the details of this commonly found model. Subscription Rates: 6 issues 38 A Home Built Rivet Embosser — John Gizzi US - Periodical Class Delivery US$35 US - First Class Delivery (1 year only) US$45 If necessity is the Mother of Invention, then frugality is its Father. -
B&O Steam Locomotive Models for 1940-1956
THE B&O MODELER Number 42 Steam Locomotive Decal Review Malvern B&O Model Sampler O-48 Gondola Kit Construction J. J. Tatum’s Hopper Ends York Locomotive Replicas B-8 Steam Engines The Lidgerwood —Model & Prototype B&O HO Steam Brass Locomotive Models The B&O Modeler Number 42 A publication of the B&O Railroad Historical Society (B&ORRHS) for the purpose of disseminating B&O modeling information. Copyright © B&ORRHS – 2016 – All Rights Reserved. May be reproduced for personal use only. Not for sale other than by the B&ORRHS. Editor—John Teichmoeller [email protected] Managing Editor—Scott Seders [email protected] Supervising Editor and Baker—Kathy Farnsworth [email protected] Model Products News Editor—Clark Cone [email protected] Index Editor—Jim Ford [email protected] Modeling Committee Chairman—Bruce Elliott [email protected] Publications Committee Chairman---Harry Meem [email protected] Manuscripts and photographs submitted for publication are welcome. Materials submitted are considered to be gratis and no reimbursement will be made to the author or the photographer(s) or his/her representative(s). Please contact the editor for information and guidelines for submission. If you submit photos send, preferably at 800x600, not less than 640x480 preferable in TIFF format. Statements and opinions made are those of the authors and do not necessarily represent those of the Society. AN INVITATION TO JOIN THE B&O RAILROAD HISTORICAL SOCIETY The Baltimore and Ohio Railroad Historical Society is an independent non-profit educational corporation. The Society's purpose is to foster interest, research, preservation, and the distribution of information concerning the B&O.