Analysis and Attenuation of Impulsive Sound Pressure in Large Caliber
Total Page:16
File Type:pdf, Size:1020Kb
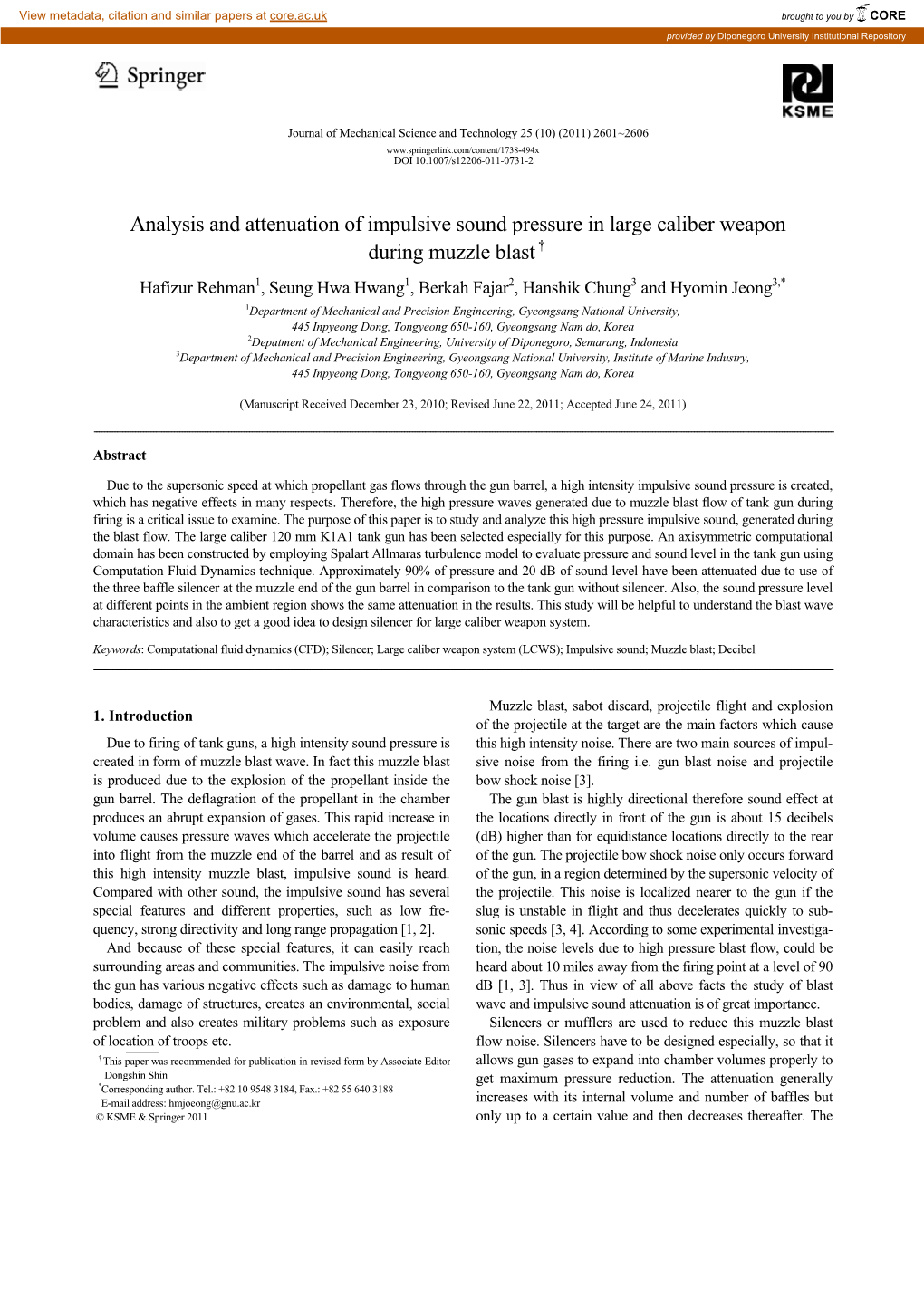
Load more
Recommended publications
-
Forensic Examination Guidelines for Silencers
FORENSIC EXAMINATION GUIDELINES FOR SILENCERS 1.0 Objective/Introduction The objective of the following guidelines is to identify the essential elements suggested for use in the forensic examination of silencers. 1.1 Establish procedures to reliably determine if a device is constructed or fabricated to reduce, suppress, attenuate or diminish the report of a firearm. 1.2 Review and/or validate established silencer examination protocols. 2.0 Definitions/Terminology Standard terminology from sources such as the Bureau of Alcohol, Tobacco, Firearms and Explosives (ATF) Federal Firearms Regulations Reference Guide, Association of Firearm and Tool Mark Examiners (AFTE) Procedures Manual and the AFTE Glossary should be used in the documentation of silencer examinations. 2.1 Commonly used terms may include: 2.1.1 Suppressor 2.1.2 Firearm muffler 2.1.3 Decibel 2.1.4 Sound meter 2.1.5 Sound pressure level 2.1.6 Report 2.1.7 Muzzle blast 2.1.8 Internal components, e.g., baffle, ported tube, wipes, end caps, bleed holes 3.0 Equipment/Supplies Proper equipment should be used and checked for acceptable accuracy when appropriate. 3.1 Equipment and supplies may include: 3.1.1 Sound meter 3.1.2 Microphone 3.1.3 X-ray apparatus 3.1.4 Optical aids – borescope, stereoscope, magnifier 3.1.5 Safety equipment – ear muffs, eye protection Forensic Examination Guidelines for Silencers Page 1 of 5 Adopted 09/27/2005 3.1.6 Chemicals for gunshot residue examinations (GSR) 3.1.7 Various tools for disassembly 3.1.8 Remote firing devices 3.1.9 Range or shooting facility 3.1.10 Distances measuring devices 4.0 Concepts 4.1 Muzzle blast is the most significant portion of the report of a firearm. -
Force and Sound Pressure Sensors Used for Modeling the Impact of the Firearm with a Suppressor
applied sciences Article Force and Sound Pressure Sensors Used for Modeling the Impact of the Firearm with a Suppressor Jaroslaw Selech 1, Arturas¯ Kilikeviˇcius 2 , Kristina Kilikeviˇciene˙ 3 , Sergejus Borodinas 4, Jonas Matijošius 2,* , Darius Vainorius 2, Jacek Marcinkiewicz 1 and Zaneta Staszak 1 1 The Faculty of Civil and Transport Engineering, Poznan University of Technology, 5 M. Skłodowska-Curie Square PL-60-965 Poznan, Poland; [email protected] (J.S.); [email protected] (J.M.); [email protected] (Z.S.) 2 Institute of Mechanical Science, Vilnius Gediminas Technical University, J. Basanaviˇciausstr. 28, LT-03224 Vilnius, Lithuania; [email protected] (A.K.); [email protected] (D.V.) 3 Department of Mechanical and Material Engineering, Vilnius Gediminas Technical University, J. Basanaviˇciausstr. 28, LT-03224 Vilnius, Lithuania; [email protected] 4 Department of Applied Mechanics, Vilnius Gediminas Technical University, Sauletekio˙ av. 11, 10223 Vilnius, Lithuania; [email protected] * Correspondence: [email protected]; Tel.: +370-684-04-169 Received: 23 December 2019; Accepted: 30 January 2020; Published: 2 February 2020 Abstract: In this paper, a mathematical model for projectiles shooting in any direction based on sensors distributed stereoscopically is put forward. It is based on the characteristics of a shock wave around a supersonic projectile and acoustical localization. Wave equations for an acoustic monopole point source of a directed effect used for physical interpretation of pressure as an acoustic phenomenon. Simulation and measurements of novel versatile mechanical and acoustical damping system (silencer), which has both a muzzle break and silencer properties studied in this paper. -
Investigation Into the Impact of Integral Suppressor Configurations on the Pressure Levels Within the Suppressor
COVER SHEET Title: Investigation into the impact of integral suppressor configurations on the pressure levels within the suppressor Authors: Aimée Helliker1 Stephen Champion1 Andrew Duncan1 Presented at 29th International Symposium on Ballistics, Edinburgh, 9th - 13th May 2016 1 Centre for Defence Engineering, Cranfield University, Defence Academy of the United Kingdom, Shrivenham, SN6 8LA, UK This paper reports on an experimental investigation supported by basic modeling in to the performance of an integral suppressor on a low power firearm. A model was developed to determine the pressure within a suppressor chamber using iterative empirical calculations of the gas properties and flow within the system. The design of a reconfigurable suppressor chamber has been undertaken allowing suppressor chamber volume to be varied through the use of baffles. Pressure transducers were used to determine the pressure within the suppressor chamber for a series of firings. The results of the firings with different configurations within the suppressor are presented allowing trends to be established. The modeling and experimental results show an increase in suppressor chamber volume results in a reduction of recorded pressure within the suppressor chamber. INTRODUCTION The use of suppressors with firearms is becoming more commonplace, especially within the UK Armed Forces where there are an increasing number of cases of hearing damage [1]. There are also applications for areas such as animal management where the British Association for Shooting and Conservation state “it may be an act of social responsibility to fit a sound moderator to a rifle” [2]. The use of suppressors reduces the sound signature of the gases from firing by allowing the superheated, high pressure gases escaping from the barrel, to expand, cool and reduce in velocity before being released into the atmosphere. -
Estimation of the Directivity Pattern of Muzzle Blasts
Estimation Of The Directivity Pattern Of Muzzle Blasts Karl-Wilhelm Hirsch1, Werner Bertels2 1Cervus Consult, Willich, [email protected] 2Wehrtechnische Dienststelle für Waffen und Munition der Bundeswehr, WTD 91, Meppen, [email protected] Introduction The WEBER model yields full information about the sound of an explosion: The radiating body is a sphere of defined size. The Sound prediction schemes are often dedicated to a certain scope of source strength is given as a FOURIER spectrum determining the application. They are called ‘engineering’ models if they consider frequency dependent sound pressure in magnitude and phase. This the features of the source, of the propagation and of the receiver spectrum can be used to calculate any desired acoustical measure of separately. Typically, such schemes start from a compatible source the source. model to sum up the correction due to the various physical phe- nomena based on particular models as separate terms to yield the For a muzzle blast, the body of radiation is certainly not a sphere. dedicated output measure. The ISO 9613-2 describes such a predic- Due to the basic rotational symmetry around the barrel axis, the tion scheme for the A-weighted long term average sound pressure radiating body still needs to be a body of revolution but estimating level for correlation purposes with annoyance. In general, the its shape and its radiation impedance is a rather challenge. The acoustic source model is therefore a decisive feature for any sound gases leaving the barrel with supersonic speed develop a so-called prediction scheme. MACH-plate. The body of radiation will be wider to the front than looking from the rear giving reason for a strong frequency depend- For many sound sources, scheme compatible sources are elemen- ent directivity pattern. -
Description of Muzzle Blast by Modified Ideal Scaling Models
1 Description of muzzle blast by modi®ed ideal scaling models Kevin S. Fansler ration need to be known accurately when peak over- U.S. Army Research Laboratory, Aberdeen Proving pressures and impulses at a ®eld point result from Ground, MD 21005, USA multiple re¯ections of the blast wave. The impulse, I, is de®ned as the time integral of the positive phase for the overpressure: Gun blast data from a large variety of weapons are scaled tc and presented for both the instantaneous energy release and I (p p ) dt; (1) the constant energy deposition rate models. For both ideal ≡ − 1 Zta explosion models, similar amounts of data scatter occur for in which t is the time for the overpressure to be- the peak overpressure but the instantaneous energy release c come zero in the blastwave. Here p is the pressure model correlated the impulse data signi®cantly better, par- and p is the atmospheric pressure, which near sea ticularly for the region in front of the gun. Two parame- 1 ters that characterize gun blast are used in conjunction with level is approximately one bar. The impulse is a very the ideal scaling models to improve the data correlation. important quantity in determining if structures are re- The gun-emptying parameter works particularly well with inforced adequately to withstand the blast wave. the instantaneous energy release model to improve data cor- The ®rst predictions of gun blast were done us- relation. In particular, the impulse, especially in the for- ing results obtained from instantaneous energy release ward direction of the gun, is correlated signi®cantly bet- blast from a point source. -
Firearm Suppressor Fact Sheet
Firearm Suppressor Fact Sheet Objectives: The foundation of the attempt to ban firearm suppressors in Virginia is built on the misconception that suppressors can render the noise of a gunshot silent or inaudible. This could hardly be further from the truth as even the quietest suppressed gunshot is as loud as a jackhammer striking concrete. Suppressors are not a danger to society and banning them will not save lives. In order to fully understand suppressors, it is imperative that you hear them for yourself. To this end, the American Suppressor Association would be happy to host an educational suppressor demonstration for any members of the legislature or media at any time of your choosing. Background: Suppressor Basics The terms “silencer” and “suppressor” refer to the same thing – a muffler for a firearm. Contrary to popular belief, no tool will ever be able to make a gunshot silent. Outside of the context of shooting, nothing will even be able to make them quiet. Guns are simply too loud. On average, suppressors reduce the noise of a gunshot by 20 – 35 decibels (dB), roughly the same sound reduction as earplugs or earmuffs. Even the most effective suppressors on the market, on the smallest and quietest calibers (.22 LR) reduce the peak sound level of a gunshot to around 110 – 120 decibels. To put that in perspective, according to the National Institute for Occupational Safety and Health (NIOSH), that is as loud as a jackhammer (110 dB) or an ambulance siren (120 dB). When a gun is fired, a controlled explosion of gunpowder propels the bullet through the barrel. -
Shot-To-Shot Variation in Gunshot Acoustics Experiments Robert C
Audio Engineering Society Conference Paper Presented at the International Conference on Audio Forensics 2019 June 18–20, Porto, Portugal This conference paper was selected based on a submitted abstract and 750-word precis that have been peer reviewed by at least two qualified anonymous reviewers. The complete manuscript was not peer reviewed. This conference paper has been reproduced from the author’s advance manuscript without editing, corrections, or consideration by the Review Board. The AES takes no responsibility for the contents. This paper is available in the AES E-Library (http://www.aes.org/e-lib), all rights reserved. Reproduction of this paper, or any portion thereof, is not permitted without direct permission from the Journal of the Audio Engineering Society. Shot-to-shot variation in gunshot acoustics experiments Robert C. Maher Electrical & Computer Engineering, Montana State University, Bozeman, MT USA 59717-3780 Correspondence should be addressed to R.C. Maher ([email protected]) ABSTRACT Audio forensic examinations may involve recordings containing gunshot sounds. Forensic questions may include determining the number of shots, what firearms were involved, the position and orientation of the firearms, and similar queries of importance to the investigation. A common question is whether a sequence of shots are attributable to a single gun fired repeatedly, or if the sounds could possibly come from two or more different guns fired in succession. This paper describes a controlled experiment comparing ten repeated shots from several common handguns and rifles. Differences between shots are observed, apparently attributable to subtle differences between ammunition cartridges. The shot-to-shot differences are also compared at different azimuths, and between different firearms. -
PASI HAKONEN FIREARM SUPPRESSORS – STRUCTURES and ALTERNATIVE MATERIALS Master of Science Thesis
PASI HAKONEN FIREARM SUPPRESSORS – STRUCTURES AND ALTERNATIVE MATERIALS Master of Science Thesis Examiner: Professor Tuomo Tiainen Examiner and topic was approved in the Faculty of Automation, Mechanical and Material Engineering council meeting in Nov 3rd, 2010 II TIIVISTELMÄ TAMPEREEN TEKNILLINEN YLIOPISTO Materiaalitekniikan koulutusohjelma HAKONEN, PASI : Äänenvaimentimet, rakenteet ja vaihtoehtoiset materiaalit Diplomityö, 47 sivua Lokakuu 2011 Pääaine: Metallimateriaalit Tarkastaja: professori Tuomo Tiainen Avainsanat: Äänenvaimennin, kuulovaurio, kivääri, kuulosuojaus Joka vuosi lukuisat metsästäjät, ampumaharrastajat ja varusmiehet kärsivät tinnituksesta ja eriasteisista kuulovaurioista. Suuri osa näistä ongelmista johtuu käsiaseiden laukausäänille altistumisesta ja epäonnistuneesta kuulonsuojauksesta ja ne olisivat vältettävissä asianmukaisilla aseisiin asennettavilla äänenvaimentimilla. Painava teräsvaimennin voi tehdä aseesta kömpelön käsiteltävän ja raskaan kantaa pitkiä matkoja, mikä voi osaltaan selittää sen miksi vaimentimien käyttö ei ole yleistynyt vielä kattavaksi. Tässä diplomityössä pyritään löytämään tähän ongelmaan ratkaisu kevyempien materiaalivaihtoehtojen avulla. Tutkimus alkoi kirjallisuusselvityksellä, jonka pohjalta suoritettiin materiaalivalinta sopivien vaihtoehtoisten materiaalien löytämiseksi. Löydetyistä materiaalivaihtoehdoista valittiin kiinnostavimmat, joista valmistettiin prototyyppi testiammuntoihin. Ensimmäinen testi keskittyi hiilikuitukomposiitin soveltuvuuteen vaimentimen ulkokuoreksi. Testissä -
THE JERSEYMAN 6 Years - Nr
4th Quarter 2008 "Rest well, yet sleep lightly and hear the call, if again sounded, to provide firepower for freedom…” THE JERSEYMAN 6 Years - Nr. 60 "Remember Pearl Harbor--Keep America Alert. Eternal Vigilance is the Price of Liberty." (Motto: Pearl Harbor Survivors) ―Can you believe the date of August 2008? Time does fly-by, and the older that we Pearl Harbor Survivors get. An important date for me will be on August 4th, when this writer of sorts hits that 89 mark, and hopefully reaches 90 in August of next year… Before you know it, December 7th will again be here and another reminder of that day of infamy on December 7, 1941. We PHS and WWII veterans have kept alive the many deeds and sacrifices we gave to win World War II. We have kept faith with all those many buried in remote islands all across the South Pacific, as they died by the thousands to take those islands in the Pacific, and the battles in the Atlantic and on other seas. Those bodies are still there, encased in tombs inside of sunken ships all over the world. We also remember the many still in their submarines, and sunken Merchant Marine ships. The many flyers whose final resting place was in the deep ocean, as their flaming planes crashed into the seas and remote jungles all over the world. And last, but not least, approximately 2,400 killed in the sneak attack on Pearl Harbor December 7, 1941, with hundreds of their bodies still in their ships sunk at Pearl. -
The American Legion Magazine Is the Officio! Publicofion of the American Legion Ond Is Owned Exclusively by the American Here Is the Most Accurate All- Legion
THE AMERICAN «^ ^V*^ SEE PAGE 27 : An account of the i NATIONAL CONVENTION LEGION SEE PAGE 16 MAGAZINE HOW SECURE IS THE PANAMA CANAL? OBER 195 4 ^ SEE PAGE 20 WHAT'S HAPPENED TO WEST COAST FOOTBALL? SEAGRAM DISTIUERS CORPORATION, NEW YORK CITY. BLENDED WHISKEY 86.8 PROOF. 65% GRAIN NEUTRAL SPIR Why is Joe smiling? Joe He knows, too, that his job is vital to the community. Like anyone who is proud of what he's doing, feeling His neighbors depend on him for the gasoline and oil they gets a lot of satisfaction out of life. He has the good need to run their cars. that comes from selling products he can believe in. Joe has another reason for being cheerful. Selling gaso- He knows that in his service station he is offering the line has always been a service business, and it attracts men finest fuels and lubricants that modern science can produce. meeting people. And most of the people Joe meets And that these products are constantly being improved. who like for are friendly to him in return. He knows that he is giving you extremely good value dollar buys 50% more Is it any wonder that Joe—the typical service-station your money . that today's gasoline is generally smiling? He gives you a great bargain every available power than the gasoline dollar of 1925. There man— time you say, "Fill 'er up!" aren't many places a dollar is actually worth more today! 2,000,000 Deff/>i<. People areore domgd« a great \obl Because Americans u bountifaj ^"^'^-^^^ sunn v f ' « for "Kejy to grantpf? fj, take industry. -
Long-Range Acoustic Localization of Artillery Shots Using Distributed Synchronous Acoustic Sensors
Long-range acoustic localization of artillery shots using distributed synchronous acoustic sensors Adrien Dagallier,1,a) Sylvain Cheinet,1 Matthias Cosnefroy,1,b) Winfried Rickert,2 Thomas Weßling,2 Pierre Wey,1 and Daniel Juve3 1French-German Research Institute of Saint-Louis, 5 rue du Gen eral Cassagnou, 68300 Saint-Louis, France 2Wehrtechnische Dienststelle 91, Schiessplatz, D49716 Meppen, Germany 3Universite de Lyon, Ecole Centrale de Lyon, Laboratoire de Mecanique des Fluides et d’Acoustique, Unite Mixte de Recherche, Centre National de la Recherche Scientifique 5509, Ecully, F-69134, France (Received 1 February 2019; revised 24 July 2019; accepted 24 July 2019; published online 31 December 2019) Acoustic recordings of artillery shots feature the signatures of the shot’s muzzle, projectile, and impact waves modulated by the environment. This study aims at improving the sensing of such shots using a set of synchronous acoustic sensors distributed over a 1 km2 area. It uses the time matching approach, which is based on finding the best match between the observed and pre-calculated times of arrivals of the various waves at each sensor. The pre-calculations introduced here account for the complex acoustic source with a 6-degrees-of-freedom ballistic trajectory model, and for the propaga- tion channel with a wavefront-tracking acoustic model including meteorological and terrain effects. The approach is demonstrated using three recordings of artillery shots measured by sensors which are more than 10 km from the point of fire and distributed at several hundred meters away from and around the target points. Using only the impact wave, it locates the impact point with an error of a few meters. -
Recording Anechoic Gunshot Waveforms of Several Firearms at 500 Kilohertz Sampling Rate
Volume 26 http://acousticalsociety.org/ 171st Meeting of the Acoustical Society of America Salt Lake City, Utah 23-27 May 2016 Engineering Acoustics: Paper 2pEA8 Recording anechoic gunshot waveforms of several firearms at 500 kilohertz sampling rate Tushar K. Routh and Robert C. Maher Department of Electrical and Computer Engineering, College of Engineering, Montana State University, Bozeman, Montana; [email protected] , [email protected] Acoustic gunshot signals consist of a high amplitude and short duration impulsive sound known as the muzzle blast and the shock wave. This experiment involved documenting gunshot muzzle blast sounds produced by eight commonly used firearms including Remington 870, Colt 45, Glock 19 with 9mm ammunition, Glock 23, Sig 239, AR15, 22LR, and Ruger SP 101 with 357 magnum and 38 special ammunition. An elevated microphone bracket (3m above the ground) was built to achieve a quasi- anechoic environment for the duration of the muzzle blast. Twelve microphones (GRAS 40DP) were mounted on the bracket in a semi-circular arc to observe the azimuthal variation of the muzzle blast. Signals were recorded using LabVIEW. Similarities and differences among waveforms are presented. Published by the Acoustical Society of America © 2016 Acoustical Society of America [DOI: 10.1121/2.0000262] Proceedings of Meetings on Acoustics, Vol. 26, 030001 (2016) Page 1 Redistribution subject to ASA license or copyright; see http://acousticalsociety.org/content/terms. Download to IP: 153.90.120.67 On: Fri, 02 Dec 2016 00:08:02 T. K. Routh and R. C. Maher Recording anechoic gunshot waveforms of several firearms INTRODUCTION Recorded gunshot signals consist of two major waveforms of interests, the muzzle blast, originated from the rapid combustion of gunpowder, and the ballistic shock wave produced by the bullet if traveling at supersonic speed (Maher, 2013).