Source and Characterization of Particulate Matter from a Pilot-Ignited Natural Gas Fuelled Engine
Total Page:16
File Type:pdf, Size:1020Kb
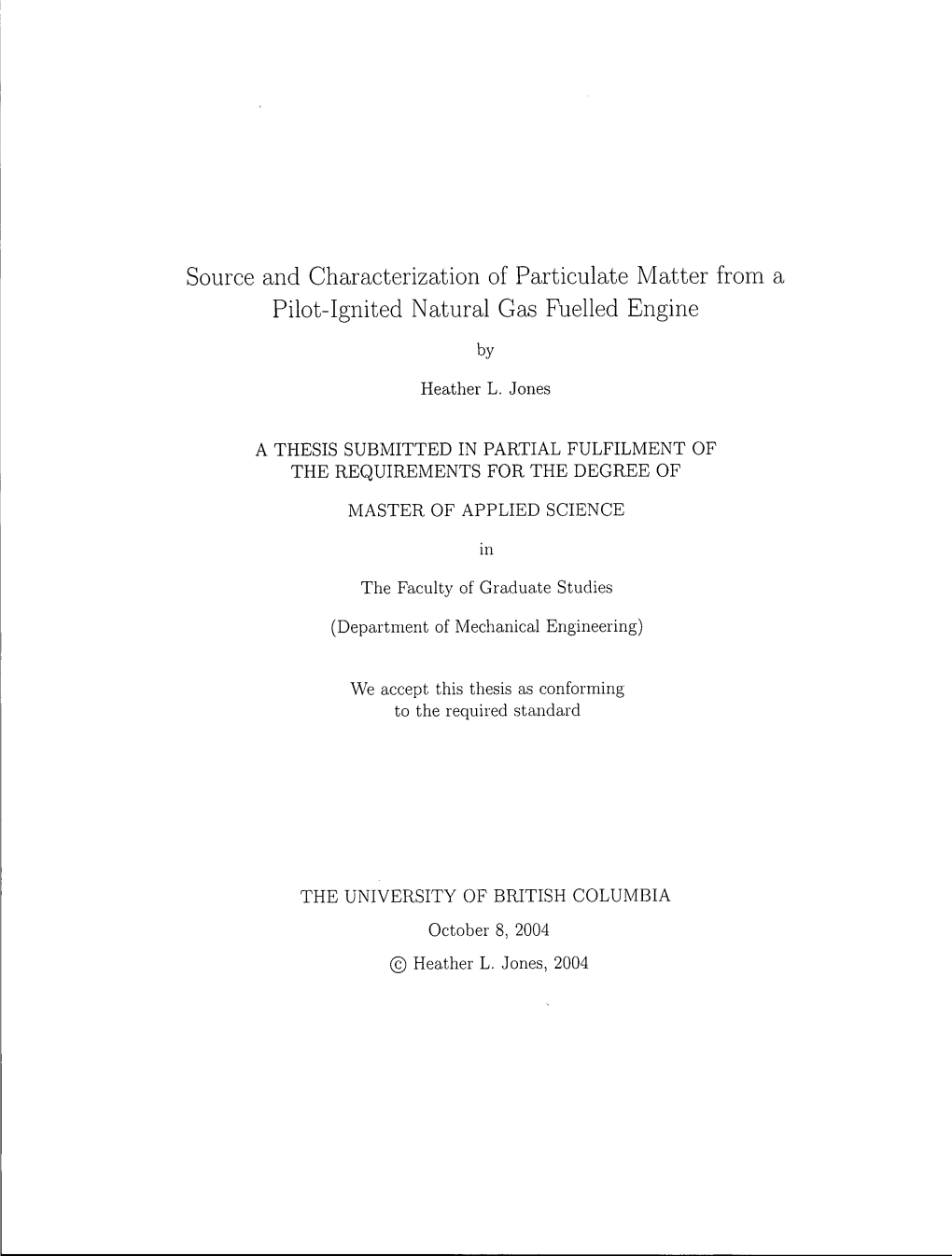
Load more
Recommended publications
-
Sustainability Report 4
CHANGING THE WAY THE WORLD MOVES 2013 ANNUAL REPORT TABLE OF CONTENTS LETTER TO SHAREHOLDERS 1 SUSTAINABILITY REPORT 4 MANAGEMENT’S DISCUSSION & ANALYSIS 11 REPORTS 31 CONSOLIDATED BALANCE SHEETS 34 CONSOLIDATED STATEMENTS OF OPERATIONS AND COMPREHENSIVE INCOME (LOSS) 35 CONSOLIDATED STATEMENTS OF SHAREHOLDERS’ EQUITY 36 CONSOLIDATED STATEMENTS OF CASH FLOWS 37 NOTES TO CONSOLIDATED FINANCIAL STATEMENTS 38 INFORMATION FOR SHAREHOLDERS 61 PLEASE NOTE, Interim and Annual Financial Statements and Management's Discussion are always available, when released, on the Westport website, WESTPORT.COM. Westport encourages you to make this environmentally responsible choice. II » WESTPORT INNOVATIONS INC. 2013 ANNUAL REPORT LETTER TO SHAREHOLDERSLETTER to SHAREHOLDERS We have concluded that the first priority should be TO OUR markets where customers spend a great deal on fuel; SHAREHOLDERS, regulation or policy are encouraging a change; and there is a full ecosystem of product distribution, service, At the end of a fiscal year, we believe it is important for fuelling infrastructure, and customer awareness. At us to review the year and mark our progress against our Westport, we spent over a decade educating, encouraging, strategic plans. 2013 was a transition year for Westport. demonstrating, and proving out the necessary components We went through a considerable change as we reconfigured of that ecosystem in different markets around the world. our business from our market creation, demonstration project culture, to a focused product business in a At the end of 2013, we believe the ecosystem was in place. strong growth market. We will start reviewing the year We were able to survey around the world and were pleased by reiterating the foundations for our strategic plan. -
Cummins Westport, Inc
Cummins Westport, Inc. Engine Overview March 2015 Cummins Westport Inc. (CWI) A Cummins JV Company . CWI was established in 2001 as a 50/50 joint venture company between Cummins Inc and Westport Innovations. – Cummins Inc. - world’s largest independent manufacturer of commercial diesel and natural gas engines. – Westport Innovations Inc. - world leader in gaseous fuel engine technology . CWI offers 8.9 and 12 liter spark ignited alternative fuel automotive engines. Engines are manufactured by Cummins in Rocky Mount, North Carolina, and Jamestown, New York. Local parts and service support through Cummins Distributor network. 2 Cummins Westport Heavy Duty Engines Designed Specifically for Alternative Fuels . Based on Reliable Cummins Engine Platforms . Common parts and design provide heavy duty performance . Engineered and Optimized Specifically for Alternative Fuel . Continued improvement in reliability and cost of ownership . Service, Parts and Training Support through the Cummins Distributor network 3 2014/16 Cummins Westport Products. 2016 6.7 Litre 8.9 Litre 11.9 Litre Spark Ignited Spark Ignited Spark Ignited SEGR SEGR SEGR Three Way Catalyst Three Way Catalyst Three Way Catalyst Up to 60,000 miles/year Up to 80,000 lb. GVW 66,000 lb. GVW 4 Natural Gas Engines: Features . ISX12 G : 12 Liters, 80,000 lb GVW . ISL G : 9 Liters, 66,000 lb GVW . Use 100% Natural Gas – Stored as CNG, LNG . Spark Ignited, In-line 6 cylinder . Wastegate Turbocharger . Charge-Air Cooled (CAC) . Stoichiometric EGR Combustion . Three Way Catalyst Aftertreatment – Maintenance Free . Base Warranty: 2 yr/250,000 miles . Extended Coverage Available 2015 Engines Aftertreatment Comparison SCR Catalyst Particulate Filter 2015 Diesel Heated Urea Tank Urea ECM Dosing Control Unit Cummins TWC Three Way Catalyst 6 Natural Gas Engine Introduction . -
And Particulate Matter Emissions from Heavy-Duty Natural Gas Engines
Graduate Theses, Dissertations, and Problem Reports 2006 Reduction of Toxic Air Contaminants (TACs) and particulate matter emissions from heavy-duty natural gas engines Hemanth K. Kappanna West Virginia University Follow this and additional works at: https://researchrepository.wvu.edu/etd Recommended Citation Kappanna, Hemanth K., "Reduction of Toxic Air Contaminants (TACs) and particulate matter emissions from heavy-duty natural gas engines" (2006). Graduate Theses, Dissertations, and Problem Reports. 1707. https://researchrepository.wvu.edu/etd/1707 This Thesis is protected by copyright and/or related rights. It has been brought to you by the The Research Repository @ WVU with permission from the rights-holder(s). You are free to use this Thesis in any way that is permitted by the copyright and related rights legislation that applies to your use. For other uses you must obtain permission from the rights-holder(s) directly, unless additional rights are indicated by a Creative Commons license in the record and/ or on the work itself. This Thesis has been accepted for inclusion in WVU Graduate Theses, Dissertations, and Problem Reports collection by an authorized administrator of The Research Repository @ WVU. For more information, please contact [email protected]. Reduction of Toxic Air Contaminants (TACs) and Particulate Matter Emissions from Heavy-Duty Natural Gas Engines Hemanth K. Kappanna Thesis Submitted to the College of Engineering and Mineral Resources at West Virginia University in partial fulfillment of the requirements for the degree of Master of Science in Mechanical Engineering Mridul Gautam, Ph.D., Chair Gregory. J. Thompson, Ph.D. W. Scott Wayne, Ph.D. Daniel. -
Overview Cummins Westport
Overview Cummins Westport January 9, 2013 Who Are We? A Joint Venture of Westport & Cummins Cummins Inc. 50% 50% Delivered over 35,000 engines. 2011 Revenue = $139M New 10 year Agreement 2012 2 Cummins Inc. More than 75 years –Leader in American diesel manufacturing . World’s largest builder of commercial diesels . Designs, manufactures, distributes, and services – electric power generation systems, engines, and related technologies, including fuel systems, controls, air handling, filtration, and emissions solutions. Headquartered in Columbus, Indiana (USA), – serves customers in approximately 190 countries and territories through a network of more than 500 company-owned and independent distributor locations and approximately 5,200 dealer locations. – Cummins reported sales of $18 billion in 2011 . Cummins product development & manufacturing alliances include: – Case, New Holland, IVECO, Komatsu, Westport, and Scania. 3 Westport Innovations Inc. Recognized as the world leader in gaseous fuel engine technology . Originated from research at UBC in early 1990’s . Public company on TSE, formed in 1995 . 170 people at Westport (including Cummins Westport, Westport Europe and Westport Germany) Vancouver, BC, Canada . State-of-the-art facilities in Vancouver, Canada: 7,400 m2 (78,000 ft2) of laboratory and office space . Leading Natural Gas expertise and industry relationships Technology Innovation and Application Award 4 Why Natural Gas Engines for Buses & Trucks? Environmental Leadership Meets Regulated 2010 EPA/CARB Lower greenhouse gas -
Remarks to US Senate Committee on Energy and Natural Resources
Remarks to US Senate Committee on Energy and Natural Resources Jim Arthurs – President, Cummins Westport Inc. May 14, 2013, Washington DC Good morning. My name is Jim Arthurs and on behalf of my colleagues at Cummins Westport, and our parent companies Cummins Inc. and Westport Innovations, it’s a pleasure to be here. The company I represent, Cummins Westport, was formed as a joint venture between Cummins and Westport in 2001 after both companies recognized the potential of natural gas as a fuel for transportation. Cummins Westport designs, engineers and markets natural gas engines for medium and heavy-duty transportation applications such as commercial trucks and buses. Our engines are designed in Columbus, Indiana and built in Cummins engine plants in Rocky Mount, North Carolina and Jamestown, New York. Since 2001, we have delivered over 34,000 natural gas engines to customers in North America and around the world. Today, natural gas provides about 27% of the energy used in the US, and is widely used in the commercial, industrial and residential segments. But it accounts for only a small portion -- less than 3% -- of the energy used for transportation. The main source of energy for transportation -- about 93% -- is petroleum, much of which is imported. With domestically produced natural gas becoming an abundant, low cost source of energy for America, we have a tremendous opportunity to reduce the cost of transportation, and reduce oil imports, by shifting some of the energy used for transportation from petroleum to natural gas. Twenty years ago, Cummins began offering natural gas engines to America’s transit bus market. -
Next Generation Natural Gas Vehicle
THE CHALLENGE FOR ENERGY SECURITY TECHNICAL TARGETS FOR VEHICLES AND CLEAN AIR The near-term target for the program is to develop a The steady increase in vehicles and travel on our roads heavy-duty LNG vehicle and a medium-duty CNG and highways is driving an ever-increasing demand for vehicle by 2004 that meet an emission goal of oil imports. With much of the worldwide oil reserves 0.5 g/bhp-h NOx (oxides of nitrogen) and 0.01 g/bhp-h located in politically volatile countries, the United PM (particulate matter). The long-term target is to States is vulnerable to disruptions in supply. At the introduce heavy- and medium-duty vehicles before same time, the increase in oil consumption is con- 2007 that meet the 2007 EPA emission regulations tributing to the degradation of the air quality in many (0.2 g/bhp-h NOx). of our cities. Economic and environmental concerns are both national and international in scope. The U.S. CUSTOMER AND INDUSTRY INVOLVEMENT Environmental Protection Agency (EPA) has mandated Underscoring their commitment to develop and intro- strict and very challenging emission requirements for duce NGVs that are commercially attractive and viable, heavy-duty vehicles in 2004 and 2007. Low emission DOE and NREL have enlisted the support of fleet technologies and low emission vehicles are critical to customers, the NGV industry, and California air quality meeting the challenge for energy security and clean air. and energy agencies to advise and collaborate on iden- tifying vehicle needs and on optimum paths to achieve NATURAL GAS VEHICLES ARE CRUCIAL the program goals. -
Westport Innovations Inc
McIntire Investment Institute At the University of Virginia Westport Innovations Inc WPRT:NASDAQ Prepared by Simratbir Singh| 01 March 2012 1 M c I n t i r e I n v e s t m e n t I n s t i t u t e Outline Company Overview Stock Overview Thesis Points Value Added Research Risks Recommendation Q & A 2 M c I n t i r e I n v e s t m e n t I n s t i t u t e Westport Innovations • Founded in 1995 • Headquarters = Vancouver, Canada • Full Time Employees = 354 • Sector = Industrials • Industry = Auto Parts • Locations = North America, Europe, China, and Australia • IPO = 1997 3 M c I n t i r e I n v e s t m e n t I n s t i t u t e Strategic Global Locations 4 M c I n t i r e I n v e s t m e n t I n s t i t u t e For Future PresentationsCompany Overview Westport Innovations is a provider of engine and fuel system technologies utilizing gaseous fuels. The company provides alternative fuels, low-emission technologies that enable engines to operate on fuels such as compressed natural gas, liquefied natural gas, hydrogen, and biofuels. 5 M c I n t i r e I n v e s t m e n t I n s t i t u t e Value Investing Conference Company Overview The Company's technology and products enable three petroleum- based fuel engines that primarily use natural gas. -
Natural Gas Charges Into the Future
POWERTRAIN SYSTEM: CNG & LNG ENGINES arge U.S. reserves and the ability to use existing engine technology make natural gas attractive. In fact, natural Natural gas charges gas price projections are significantly lower than historical averages as more information becomes available on mas- Lsive shale gas reserves. into the future Engine and fuel availability continue to by Curt Bennink expand. “We are in the stage of investment in Explore natural gas options when designing new vehicles. both infrastructure build-out and product devel- opment,” says Paul Blomerus, Senior Director, High Horsepower Corporate Development, Westport Innovations Inc., Vancouver, BC, Canada. “Where those two meet is a perfect storm of new products to meet demand and available cheap fuel. Then we will see an inflec- tion point.” In the push to transition from petroleum-based vehicles to an affordable domestic alternative, natural gas is quickly gaining favor. Any vehi- cle traditionally powered by gasoline or die- sel can be converted to natural gas. Although natural gas does produce greenhouse gases, it is much cleaner than either gasoline or diesel. It is an odorless, nontoxic, gaseous mixture of hydrocarbons—predominantly methane (CH4) and it possesses the lowest carbon con- tent of any hydrocarbon fuel. A side benefit is that compressed natural gas (CNG) fuel sys- CNG refueling of refuse trucks in Livermore, CA. NGVAMERICA OEM Off-Highway | JANUARY/FEBRUARY 2013 www.oemoffhighway.com 7 POWERTRAIN SYSTEM: CNG & LNG ENGINES tems are completely sealed, so there are no evaporative emissions. But the economic business case remains strong. “There are so many different angles and they are all predicated on economics,” says Richard Kolodziej, President of Natural Gas Vehicles for America (NGVAmerica). -
Natural Gas in High Horsepower Engine Applications Westport Innovations Dale Goudie, Peng Overview
The global leader in natural gas engines. Our products …to keep work here… this clear. Natural Gas in High Horsepower Engine Applications Westport Innovations Dale Goudie, PEng Overview Introduction to Westport Why natural gas ….Why now? Natural gas engine technology y Natural gas as a fuel y Combustion methods, performance and emissions y Westport HPDI Current high-horsepower engine development Westport at a Glance market focus position strategy Transformation from The global leader in Leverage IP to penetrate markets through petroleum-fueled to gaseous fuel engineering relationships with market- alternative-fueled engines. and technology. leading OEMs. Volvo 3 Westport Global Operations Vancouver Gothenburg Sweden Canada Beijing & Weifang Lyon China France Signal Hill Detroit Pernumia & Brescia U.S.A. U.S.A. Italy stock symbols market capitalization TSX NASDAQ CAD USD Bayswater WPT WPRT $1.4 billion ~$1.4 billion Australia 4 “The Golden Age of Natural Gas” World natural gas resources by major region, January 2010 (tcm) source: “Are We Entering a Golden Age of Gas?”, IEA, June 2011. 5 Downward Pressure on Natural Gas Prices Natural gas price projections are significantly lower than past years due to an expanded shale gas resource base natural gas spot price (Henry Hub); 2009 dollars per million Btu 10 $9/MMBtu 9 8 updated AEO2009 AEO2010 7 $7/MMBtu 6 5 AEO2011 4 Energy 3 Equivalent price 2 for Diesel: Curren $0.26 US gal 1 t price: history 2009 $1.84 projections 0 1990 1995 2000 2005 2010 2015 2020 2025 2030 2035 sources: EIA, Annual Energy Outlook 2011; EIA, Annual Energy Outlook 2010; and EIA, An Updated Annual Energy Outlook 2009 Reference Case via: Shale Gas and the Outlook for U.S. -
Westport Innovations Inc
WESTPORT INNOVATIONS INC. Presented by: Simon Fraser University March 5, 2011 Content 2 Section Overview.……………………………………………… 1 Positive Drivers.....…………………………………. 2 Negative Drivers…….…………..………………….. 3 Valuation………….…………………………………… 4 Disclaimer: This information is provided to you for informational purposes only and is intended Simon Fraser University | March, 2011 for use only by the Global Investment Research Challenge. Recommendation 3 TSE: WPT Overview Report Price Target Price Positive Drivers as of December 3, 2010 Negative Drivers $19.30 $16.38 Valuation HOLD Disclaimer: This information is provided to you for informational purposes only and is intended Simon Fraser University | March, 2011 for use only by the Global Investment Research Challenge. Westport Innovations 4 Formed in 1995, headquartered in Vancouver, Canada Overview Over 400 patent applications worldwide with over 200 issued patents 186 employees with 7 partners across the globe Positive Drivers Negative Drivers Valuation Disclaimer: This information is provided to you for informational purposes only and is intended Simon Fraser University | March, 2011 for use only by the Global Investment Research Challenge. Natural Gas Engine Technology 5 Overview Positive Drivers Negative Drivers Valuation Disclaimer: This information is provided to you for informational purposes only and is intended Simon Fraser University | March, 2011 for use only by the Global Investment Research Challenge. Joint Ventures & Partnerships 6 Juniper Engines Overview Cummins-Westport Westport Positive -
Westport Innovations Inc
PRODUCT & TECHNOLOGY UPDATE – NGVTF OCT 2016 Brad Douville, Vice President, Business Development & Product Management New Merged Company » Westport Innovations Inc. and Fuel Systems Solutions Inc. merged on June 1, 2016 to create Westport Fuel Systems Inc. » A premier, global company for the engineering, manufacturing and supply of alternative fuel systems and components. 2 Family of Brands and Breadth of Reach FAMILY OF BRANDS BREADTH OF REACH Passenger Car & Light Truck Medium-Duty Heavy-Duty Industrial High Horsepower CNG Refueling 3 Opportunity Gasoline-Derived Near Zero NOx Engines » HD gasoline engines certify to same standards as diesel engines » Established Near Zero (NZ) NOx techniques could be readily transferred to NG versions of these engines to bring them to the optional 0.02 g/bhp-hr standard » NZ NOx engines are much more cost effective than BEVs in applications such as shuttle buses » But will NZ NGVs qualify under the California SIP? Ref: “Game Changer, Next Generation Heavy Duty Natural Gas Engines Fueled By Renewable Natural Gas, Gladstein, Neandross and Associates, 2016 4 Westport Engine Technology Applications FUEL APPLICATION CHOICE ENGINE TECHNOLOGIES High Horsepower • mining • rail LNG • marine high pressure direct injection Heavy-Duty Vehicles • on-highway trucks Medium-Duty Vehicles CNG high efficiency spark ignited Light-Duty Vehicles 5 Product Progression HPDI 1.0 HPDI 1.0 Launched Production LAUNCH* Ended 2010 2011 2012 2013 2014 2015 2016 2017 Start HPDI 2.0 Program FULLY INTEGRATED SYSTEM *Series production components available for delivery to OEMs 6 »df 7 »d 8 Technology Progression: Injector Gen 1 Gen 2 9 Technology Progression: IGM Gen 1 Gen 2 Integrated Gas Module (IGM) 10 Westport LNG Tank Module » Completely Re-Designed » Cost Reduced, Quality Improved » Integrated LNG Pump » High & Low Pressure Variants » Enables cold LNG for increased range and longer hold times 11 LNG Tank Validation Testing » Example tests: . -
An Exploding World Market for Natural Gas Vehicles
DAWN OF THE AGE AN EXPLODING WORLD MARKET OF BIOMETHANE FOR NATURAL GAS VEHICLES According to Peter Boisen, head of Worldwide, the were required to burn natural gas, the Natural Gas Vehicle Association number of cars, because, compared to diesel, it emits of Europe, in Europe biomethane is trucks, and buses fewer greenhouse gases and “the next big thing” in transportation fueled by natural gas practically eliminates the particulates fuels. Boisen, the speaker at a has nearly doubled and nitrous oxides that account for the January 25th Energy Vision luncheon over the past three lion’s share—84%—of the increased sponsored by Linklaters, LLP, years to a total of cancer risk in the region, as estimates that in 20 years more than 7.1 million documented in long-term research biomethane derived from organic in 2007. This boom is conducted by the California South wastes could meet 10 to 18 percent an early harbinger of Coast Air Quality Management District. of vehicle fuel demand in 14 “massive disruption European countries. It already of the two biggest industries in the Now Cummins Westport sees its powers buses in a dozen Swedish world, energy and transportation,” markets exploding in China, India, cities as well as in Lille, Bern, and according to David R. Demers, CEO of Philippines, and Thailand and has Basel, while in Madrid, 500 natural Westport Innovations of Vancouver, customers in over 50 countries. gas garbage trucks will soon be who was the featured luncheon According to Demers, the dizzying converted to run on biomethane. speaker at the state-wide conference upward spiral of crude oil prices is co-sponsored by Energy Vision and driving the rapid pace of conversion to For years, some of the biogas emitted Rutgers University on alternative fuels, natural gas fuel in the developing during the bacterial digestion of held on January 24 in Piscataway, New world and, increasingly, in Europe.