Numerical and Experimental Studies of Sail Aerodynamics
Total Page:16
File Type:pdf, Size:1020Kb
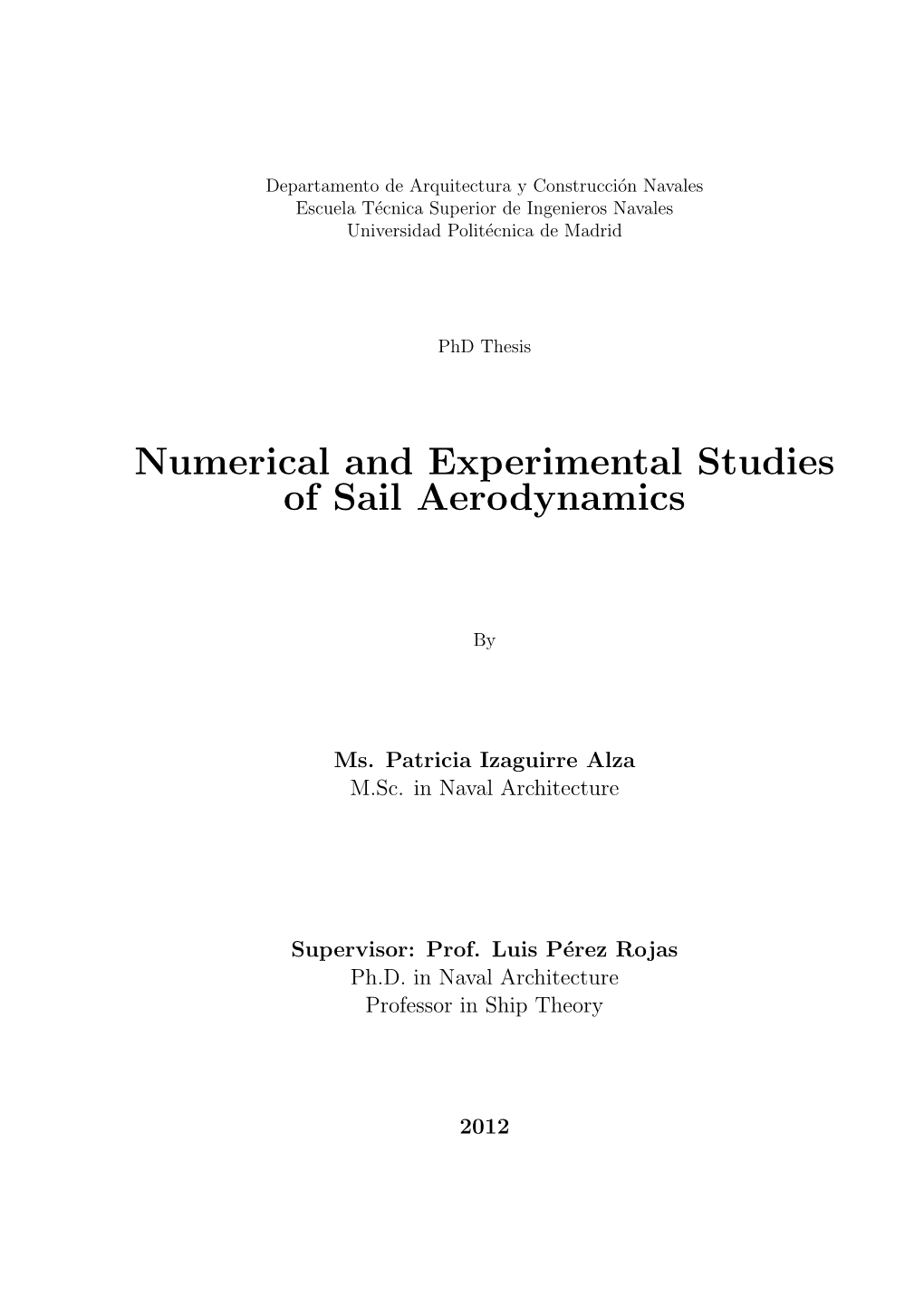
Load more
Recommended publications
-
Armed Sloop Welcome Crew Training Manual
HMAS WELCOME ARMED SLOOP WELCOME CREW TRAINING MANUAL Discovery Center ~ Great Lakes 13268 S. West Bayshore Drive Traverse City, Michigan 49684 231-946-2647 [email protected] (c) Maritime Heritage Alliance 2011 1 1770's WELCOME History of the 1770's British Armed Sloop, WELCOME About mid 1700’s John Askin came over from Ireland to fight for the British in the American Colonies during the French and Indian War (in Europe known as the Seven Years War). When the war ended he had an opportunity to go back to Ireland, but stayed here and set up his own business. He and a partner formed a trading company that eventually went bankrupt and Askin spent over 10 years paying off his debt. He then formed a new company called the Southwest Fur Trading Company; his territory was from Montreal on the east to Minnesota on the west including all of the Northern Great Lakes. He had three boats built: Welcome, Felicity and Archange. Welcome is believed to be the first vessel he had constructed for his fur trade. Felicity and Archange were named after his daughter and wife. The origin of Welcome’s name is not known. He had two wives, a European wife in Detroit and an Indian wife up in the Straits. His wife in Detroit knew about the Indian wife and had accepted this and in turn she also made sure that all the children of his Indian wife received schooling. Felicity married a man by the name of Brush (Brush Street in Detroit is named after him). -
Chapter 4: Immersed Body Flow [Pp
MECH 3492 Fluid Mechanics and Applications Univ. of Manitoba Fall Term, 2017 Chapter 4: Immersed Body Flow [pp. 445-459 (8e), or 374-386 (9e)] Dr. Bing-Chen Wang Dept. of Mechanical Engineering Univ. of Manitoba, Winnipeg, MB, R3T 5V6 When a viscous fluid flow passes a solid body (fully-immersed in the fluid), the body experiences a net force, F, which can be decomposed into two components: a drag force F , which is parallel to the flow direction, and • D a lift force F , which is perpendicular to the flow direction. • L The drag coefficient CD and lift coefficient CL are defined as follows: FD FL CD = 1 2 and CL = 1 2 , (112) 2 ρU A 2 ρU Ap respectively. Here, U is the free-stream velocity, A is the “wetted area” (total surface area in contact with fluid), and Ap is the “planform area” (maximum projected area of an object such as a wing). In the remainder of this section, we focus our attention on the drag forces. As discussed previously, there are two types of drag forces acting on a solid body immersed in a viscous flow: friction drag (also called “viscous drag”), due to the wall friction shear stress exerted on the • surface of a solid body; pressure drag (also called “form drag”), due to the difference in the pressure exerted on the front • and rear surfaces of a solid body. The friction drag and pressure drag on a finite immersed body are defined as FD,vis = τwdA and FD, pres = pdA , (113) ZA ZA Streamwise component respectively. -
12.9 Gennaker February 2013 Setting up and Sailing with the 12.9 Gennaker
12.9 Gennaker February 2013 Setting up and sailing with the 12.9 Gennaker The 12.9 Gennaker is a new bigger gennaker for the Weta. The standard gennaker is 8 sqm and the 12.9 gennaker is 12.9 sqm. The sail is designed for light to moderate breezes to help sailors racing in mixed fleets to get to a downwind mark faster. It is not intended to replace the standard 8.0 gennaker and will be sold as an extra. It is intended that one design racing fleets will stick with the 8.0 gennaker. It’s hard to say exactly what the performance difference in the sails is as it changes for different wind strengths. But with the 12.9 sqm gennaker you can sail on a generally lower (more downwind) heading than you can with the 8.0 sqm gennaker. The biggest changes are seen in a steady light breeze before you can get the boat planing. So to put it very roughly if you have two boats, one with the 8.0 and one with the 12.9 and you point both boats in a hot/tight reaching angle the 8.0 will be faster for most conditions. If you then point both boats at a low/broad reaching angle the 12.9 will be faster in most conditions. So on a windy day someone might sail further but faster with the 8.0 and get to the mark quicker than someone with the 12.9 sail who is sailing slower but less distance. For instance when Chris and I were testing, we did a day on a lake. -
Equinox Manual
Racing Manual V1.2 January 2014 Contents Introduction ...................................................................................................................................... 3 The Boat ........................................................................................................................................ 3 Positions on a Sigma 38 ................................................................................................................. 4 Points of Sail .................................................................................................................................. 5 Tacking a boat ............................................................................................................................... 6 Gybing a boat ................................................................................................................................ 7 Essential knots all sailors should know ............................................................................................... 8 Bowline ......................................................................................................................................... 8 Cleat Knot ..................................................................................................................................... 8 Clove Hitch ................................................................................................................................... 8 Reef Knot...................................................................................................................................... -
Mast Furling Installation Guide
NORTH SAILS MAST FURLING INSTALLATION GUIDE Congratulations on purchasing your new North Mast Furling Mainsail. This guide is intended to help better understand the key construction elements, usage and installation of your sail. If you have any questions after reading this document and before installing your sail, please contact your North Sails representative. It is best to have two people installing the sail which can be accomplished in less than one hour. Your boat needs facing directly into the wind and ideally the wind speed should be less than 8 knots. Step 1 Unpack your Sail Begin by removing your North Sails Purchasers Pack including your Quality Control and Warranty information. Reserve for future reference. Locate and identify the battens (if any) and reserve for installation later. Step 2 Attach the Mainsail Tack Begin by unrolling your mainsail on the side deck from luff to leech. Lift the mainsail tack area and attach to your tack fitting. Your new Mast Furling mainsail incorporates a North Sails exclusive Rope Tack. This feature is designed to provide a soft and easily furled corner attachment. The sail has less patching the normal corner, but has the Spectra/Dyneema rope splayed and sewn into the sail to proved strength. Please ensure the tack rope is connected to a smooth hook or shackle to ensure durability and that no chafing occurs. NOTE: If your mainsail has a Crab Claw Cutaway and two webbing attachment points – Please read the Stowaway Mast Furling Mainsail installation guide. Step 2 www.northsails.com Step 3 Attach the Mainsail Clew Lift the mainsail clew to the end of the boom and run the outhaul line through the clew block. -
Technology for Pressure-Instrumented Thin Airfoil Models
NASA-CR-3891 19850015493 NASA Contractor Report 3891 i 1 Technology for Pressure-Instrumented Thin Airfoil Models David A. Wigley ., ..... " .... _' /, !..... .,L_. '' CONTRACT NAS1-17571 MAY 1985 ( • " " c _J ._._l._,.. ¸_ - j, ;_.. , r_ '._:i , _ . ; . ,. NIA NASA Contractor Report 3891 Technology for Pressure-Instrumented Thin Airfoil Models David A. Wigley Applied Cryogenics & Materials Consultants, Inc. New Castle, Delaware Prepared for Langley Research Center under Contract NAS1-17571 N//X National Aeronautics and Space Administration Scientific and Technical InformationBranch 1985 Use of trademarks or names of manufacturers in this report does not constitute an official endorsement of such products or manufacturers, either expressed or implied, by the National Aeronautics and Space Administration. FINAL REPORT ON PHASE 1 OF NASA CONTRACT NASI-17571 "TECHNOLOGY FOR PRESSURE-INSTRUMENTED THIN AIRFOIL MODELS" PROJECT SU_IARY The objective of Phase 1 of this research was to identify, then select and evaluate, the most appropriate combination of materials and fabrication techniques required to produce a Pressure Instrumented Thin Airfoil model for testing in a Cryogenic wind Tunnel ( PITACT ). Particular attention was to be given to proving the feasability and reliability of each sub-stage and ensuring that they could be combined together without compromising the quality of the resultant segment or model. In order to provide a sharp focus for this research, experimental samples were to be fabricated as if they were trailing edge segments of a 6% thick supercritical airfoil, number 0631X7, scaled to a 325mm (13in.) chord, the maximum likely to be tested in the 13in. x 13in. adaptive wall test section of the 0.3m Transonic Cryogenic Tunnel at NASA Langley Research Center. -
CHAPTER TWO - Static Aeroelasticity – Unswept Wing Structural Loads and Performance 21 2.1 Background
Static aeroelasticity – structural loads and performance CHAPTER TWO - Static Aeroelasticity – Unswept wing structural loads and performance 21 2.1 Background ........................................................................................................................... 21 2.1.2 Scope and purpose ....................................................................................................................... 21 2.1.2 The structures enterprise and its relation to aeroelasticity ............................................................ 22 2.1.3 The evolution of aircraft wing structures-form follows function ................................................ 24 2.2 Analytical modeling............................................................................................................... 30 2.2.1 The typical section, the flying door and Rayleigh-Ritz idealizations ................................................ 31 2.2.2 – Functional diagrams and operators – modeling the aeroelastic feedback process ....................... 33 2.3 Matrix structural analysis – stiffness matrices and strain energy .......................................... 34 2.4 An example - Construction of a structural stiffness matrix – the shear center concept ........ 38 2.5 Subsonic aerodynamics - fundamentals ................................................................................ 40 2.5.1 Reference points – the center of pressure..................................................................................... 44 2.5.2 A different -
Spinnakers and Poles/Bowsprits Explained
SPINNAKERS AND POLES/BOWSPRITS EXPLAINED The RORC Rating Office is sometimes asked whether symmetric and asymmetric spinnakers are rated differently, and whether there is a rating increase if you use both types. The question is often prompted by the IRC application form asking questions about the spinnakers of each type carried aboard, rather than just the largest spinnaker area (SPA) and total number of spinnakers. There are two aspects of downwind sail rating: the sail itself and the type of pole (if any) it is set on - as explained below. Text in italics is taken from the IRC 2018 Rule text. SPINNAKERS For the calculation of your rating, IRC considers the largest spinnaker area (SPA) and the total number of spinnakers carried. 21.6 Spinnakers 21.6.1 Boats carrying more than three spinnakers in total on board while racing will incur an increase in rating. 21.6.2 Spinnaker area (SPA) shall be calculated from: SPA = ((SLU + SLE)/2) * ((SFL + (4 * SHW))/5) * 0.83 SLU, SLE, SFL and SHW of the largest area spinnaker on board shall be declared. The calculated area of this spinnaker will be shown on a boat’s certificate as the maximum permitted SPA. 8.10.1 Values stated on certificates for LH, Hull Beam, Bulb Weight, Draft, x, P, E, J, FL, MUW, MTW, MHW, HLUmax, HSA, PY, EY, LLY, LPY, Cutter Rig HLUmax, SPA, STL are maximum values. Are symmetric or asymmetric spinnakers rated differently? Not directly, but see the section on pole type below. Is there a rating increase if I carry both symmetric and asymmetric spinnakers? Not directly, but see the section on pole type below. -
The Aerodynamic Design of Wings with Cambered Span Having Minimum Induced Drag
https://ntrs.nasa.gov/search.jsp?R=19640006060 2020-03-24T06:40:56+00:00Z View metadata, citation and similar papers at core.ac.uk brought to you by CORE provided by NASA Technical Reports Server TR R-152 NASA- ..ZC_ L mm-4 -0-= I NATIONAL AERONAUTICS AND -----I- SPACE ADMINISTRATION LC)A~\c;i)p E AFW Wm* EP1 KIRTLANi =$= MS; TECHNICAL REPORT R-152 THE AERODYNAMIC DESIGN OF WINGS WITH CAMBERED SPAN HAVING MINIMUM INDUCED DRAG BY CLARENCE D. CONE, JR. 1963 ~ For -le by the Superintendent of Documents. US. Government Printing OIBce. Wasbingbn. D.C. 20402. Single copy price, 35 cents TECH LIBRARY KAFB, NM 00b8223 TECHNICAL REPORT R-152 THE AERODYNAMIC DESIGN OF WINGS WITH CAMBERED SPAN HAVING MINIMUM INDUCED DRAG By CLARENCE D. CONE, JR. Langley Research Center Langley Station, Hampton, Va. I CONTENTS Page SU~MMARY-________._...-.--..--.---------------------------------------- 1 INTRODUCTION __.._.._..__..___..~___.__._.._....~....~~-_--~~--~-------1 SYMBOLS___._____.___------.----------.---.--.---.---------------.--.--- 2 THE ])RAG POLAR OF CAMBERED-SPAN WINGS-_- - ...______________.__ 3 PROPERTIES OF CAMBERED WINGS HAVING MINIMUM INDUCED DRAG_._.._.___.~._.___~_._.___.._.____..__.__.-~~_-~---_---~~---------4 The Optimum Circulation IXstribution.. - -.- - -.- - - - - - - - - - - - - - - -.- - - - - - -.- - 4 The Effective Aspect Ratio ______________._._._____________________------5 THE DESIGN OF CAMBERED WINGS ____________________________________ 6 I>et,erininationof the Wing Shape for Maximum LID- - -.--_-___-___-___--__ 7 Specification of design requirements- - - - - - - - - - - - - - - -.-. - - - - - - - - - - - - - - - - 8 1)eterniination of minimum value of chord function- - - -.- - - - - - - - - - - - - - 8 Determination of wing profile-drag coefficient and optimum chord function- - 9 The optimum cruise altitude- -. -
Chapter 4: Immersed Body Flow [Pp
MECH 3492 Fluid Mechanics and Applications Univ. of Manitoba Fall Term, 2017 Chapter 4: Immersed Body Flow [pp. 445-459 (8e), or 374-386 (9e)] Dr. Bing-Chen Wang Dept. of Mechanical Engineering Univ. of Manitoba, Winnipeg, MB, R3T 5V6 When a viscous fluid flow passes a solid body (fully-immersed in the fluid), the body experiences a net force, F, which can be decomposed into two components: a drag force F , which is parallel to the flow direction, and • D a lift force F , which is perpendicular to the flow direction. • L The drag coefficient CD and lift coefficient CL are defined as follows: FD FL CD = 1 2 and CL = 1 2 , (112) 2 ρU A 2 ρU Ap respectively. Here, U is the free-stream velocity, A is the “wetted area” (total surface area in contact with fluid), and Ap is the “planform area” (maximum projected area of an object such as a wing). In the remainder of this section, we focus our attention on the drag forces. As discussed previously, there are two types of drag forces acting on a solid body immersed in a viscous flow: friction drag (also called “viscous drag”), due to the wall friction shear stress exerted on the • surface of a solid body; pressure drag (also called “form drag”), due to the difference in the pressure exerted on the front • and rear surfaces of a solid body. The friction drag and pressure drag on a finite immersed body are defined as FD,vis = τwdA and FD, pres = pdA , (113) ZA ZA Streamwise component respectively. -
Build Your Own S/V Denis Sullivan Schooner
Build Your Own S/V Denis Sullivan Schooner Materials: Directions: n Recyclable Materials: Collect building materials and supplies. ● Body (Hull) of the schooner: 1 aluminum foil, egg cartons, Before building, fill in the blanks on the S/V Denis Sullivan on next page. Label plastic bottle, carboard, etc. 2 the following parts of the schooner: ● Sails: Paper, Tissues, Paper (*Answer Key can be found at the Introduction: Towel, etc. bottom of the Activity Sheet) The S/V Denis Sullivan is the only re- ● Mast and Bowsprit: Skewers, a. Sails (Upper and Lower) creation of a 19th century Great Lakes Cargo Schooner and Wisconsin’s Flagship. Build Chopsticks, Pen, Pencils, b. Raffee Sail Schooner Straws, etc. you own S/V Denis Sullivan Schooner with c. Jib Sails (Head Sails) recyclable materials found in your home. n Pencil/Pen d. Pilot House n Paper for drawing design e. Hull Think About It: n Scissors What does a schooner look like? A sailboat n Tape/Glue f. Mast with a minimum of 2 masts that can have Denis Sullivan Denis Sullivan g. Bowsprit up to 7 with the foremast slightly shorter than the mainmast. A schooner usually has Design and draw a schooner with fore-and-aft rigged sails, but may also have 3 pencil and paper. square-rigged sails. Construct the body (hull) of the Do Ahead of Time: 4 schooner. n Gather all supplies Draw and cut out the sails using n To Take It Further: Fill testing 5 scissors. Make at least 3 sails, one Build Your Own S/V Build Your container with enough water so that for each mast, and at least one sail the boat can float freely and cannot for the bowsprit. -
Upwind Sail Aerodynamics : a RANS Numerical Investigation Validated with Wind Tunnel Pressure Measurements I.M Viola, Patrick Bot, M
Upwind sail aerodynamics : A RANS numerical investigation validated with wind tunnel pressure measurements I.M Viola, Patrick Bot, M. Riotte To cite this version: I.M Viola, Patrick Bot, M. Riotte. Upwind sail aerodynamics : A RANS numerical investigation validated with wind tunnel pressure measurements. International Journal of Heat and Fluid Flow, Elsevier, 2012, 39, pp.90-101. 10.1016/j.ijheatfluidflow.2012.10.004. hal-01071323 HAL Id: hal-01071323 https://hal.archives-ouvertes.fr/hal-01071323 Submitted on 8 Oct 2014 HAL is a multi-disciplinary open access L’archive ouverte pluridisciplinaire HAL, est archive for the deposit and dissemination of sci- destinée au dépôt et à la diffusion de documents entific research documents, whether they are pub- scientifiques de niveau recherche, publiés ou non, lished or not. The documents may come from émanant des établissements d’enseignement et de teaching and research institutions in France or recherche français ou étrangers, des laboratoires abroad, or from public or private research centers. publics ou privés. I.M. Viola, P. Bot, M. Riotte Upwind Sail Aerodynamics: a RANS numerical investigation validated with wind tunnel pressure measurements International Journal of Heat and Fluid Flow 39 (2013) 90–101 http://dx.doi.org/10.1016/j.ijheatfluidflow.2012.10.004 Keywords: sail aerodynamics, CFD, RANS, yacht, laminar separation bubble, viscous drag. Abstract The aerodynamics of a sailing yacht with different sail trims are presented, derived from simulations performed using Computational Fluid Dynamics. A Reynolds-averaged Navier- Stokes approach was used to model sixteen sail trims first tested in a wind tunnel, where the pressure distributions on the sails were measured.