Technology Screening for Natural Gas Liquids Treatment ABSTRACT
Total Page:16
File Type:pdf, Size:1020Kb
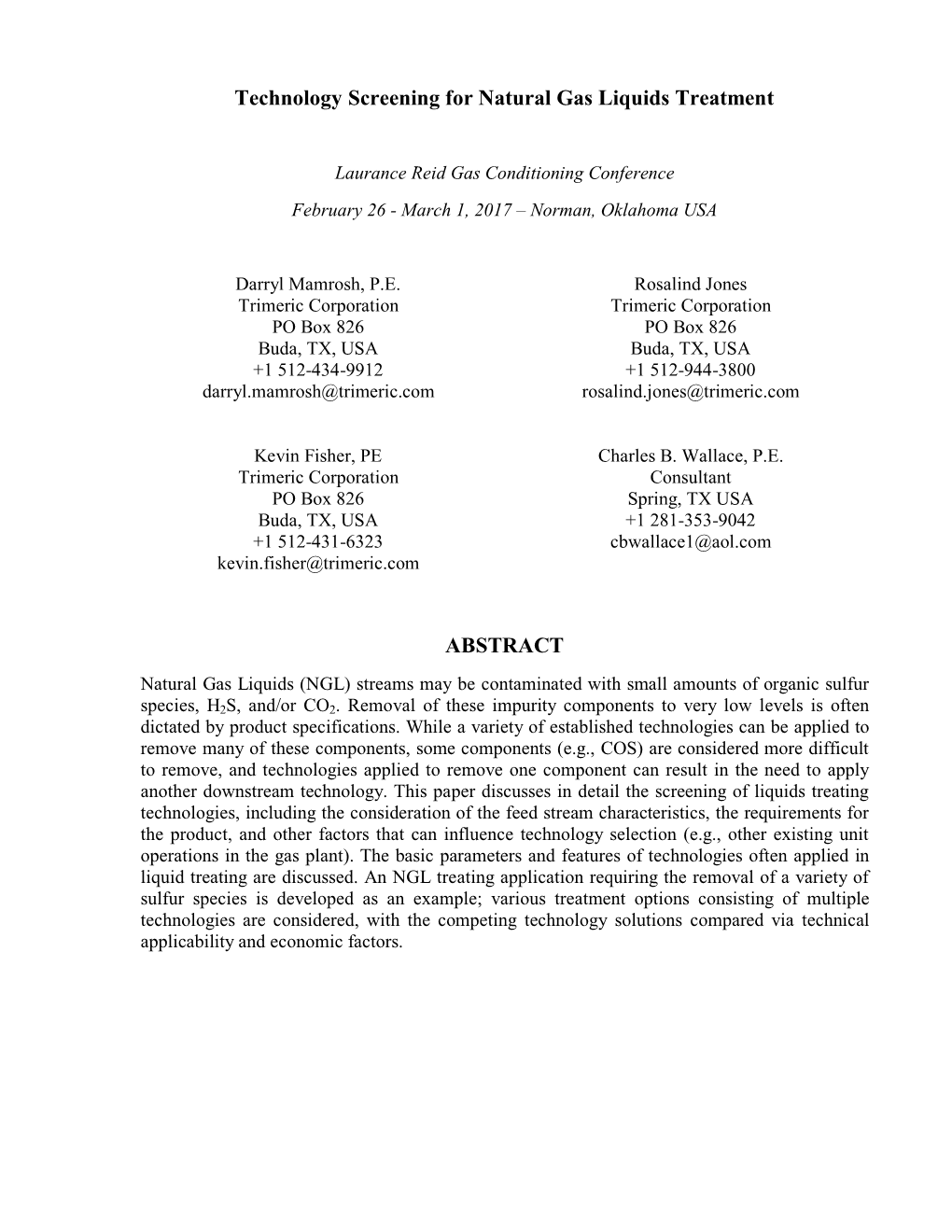
Load more
Recommended publications
-
Catalyst Precursors for Hydrodesulfurization Synthesized in Supercritical Fluids Manuel Théodet
New generation of ”bulk” catalyst precursors for hydrodesulfurization synthesized in supercritical fluids Manuel Théodet To cite this version: Manuel Théodet. New generation of ”bulk” catalyst precursors for hydrodesulfurization synthesized in supercritical fluids. Material chemistry. Université Sciences et Technologies - Bordeaux I,2010. English. NNT : 2010BOR14092. tel-00559113 HAL Id: tel-00559113 https://tel.archives-ouvertes.fr/tel-00559113 Submitted on 24 Jan 2011 HAL is a multi-disciplinary open access L’archive ouverte pluridisciplinaire HAL, est archive for the deposit and dissemination of sci- destinée au dépôt et à la diffusion de documents entific research documents, whether they are pub- scientifiques de niveau recherche, publiés ou non, lished or not. The documents may come from émanant des établissements d’enseignement et de teaching and research institutions in France or recherche français ou étrangers, des laboratoires abroad, or from public or private research centers. publics ou privés. Distributed under a Creative Commons Attribution - NonCommercial - NoDerivatives| 4.0 International License N° d’ordre : 4092 THÈSE présentée à L’UNIVERSITÉ BORDEAUX I ÉCOLE DOCTORALE DES SCIENCES CHIMIQUES Par Manuel THEODET Ingénieur ENSCPB POUR OBTENIR LE GRADE DE DOCTEUR SPÉCIALITÉ : Physico-Chimie de la Matière Condensée ___________________ NOUVELLE GENERATION DE PRECURSEURS « BULK » DE CATALYSEUR D’HYDRODESULFURATION SYNTHETISES EN MILIEU FLUIDE SUPERCRITIQUE ___________________ NEW GENERATION OF « BULK » CATALYST PRECURSORS FOR HYDRODESULFURIZATION SYNTHESIZED IN SUPERCRITICAL FLUIDS ___________________ Co-superviseurs de recherche : Cristina Martínez & Cyril Aymonier Soutenue le 03 Novembre 2010 Après avis favorable de : M. E. PALOMARES, Professor, UPV, Valencia, Spain Rapporteurs M. M. TÜRK, Professor, KIT, Karlsruhe, Germany Devant la commission d’examen formée de : M. -
Category Assessment Document For
U.S. EPA HPV Challenge Program Category Assessment Document for Acids and Caustics from Petroleum Refining Category Tar acids, cresylic, sodium salts, caustic solutions (CAS No. 68815-21-4); Neutralizing agents (petroleum), spent sodium hydroxide (CAS No. 064742- 40-1); Phenols, sodium salts, mixed with sulfur comp; gasoline alky scrubber residues (CAS No. 68988-99-8); Sludges (petroleum), acid (CAS No. 064742-24-1). Submitted by: American Petroleum Institute Petroleum HPV Testing Group American Petroleum Institute 1220 L Street NW Washington, DC 20005 Consortium Registration # 1100997 July 6, 2009 Acids and Caustics From Petroleum Refining Consortium Registration # 1100997 CATEGORY ASSESSMENT DOCUMENT Acids and Caustics from Petroleum Refining Table of Contents Tables ........................................................................................................................................... 3 Figures ......................................................................................................................................... 3 Annexes........................................................................................................................................ 3 Plain Language Summary ......................................................................................................... 4 1. Introduction ........................................................................................................................ 5 2. Category Description ........................................................................................................ -
Anaerobic Degradation of Methanethiol in a Process for Liquefied Petroleum Gas (LPG) Biodesulfurization
Anaerobic degradation of methanethiol in a process for Liquefied Petroleum Gas (LPG) biodesulfurization Promotoren Prof. dr. ir. A.J.H. Janssen Hoogleraar in de Biologische Gas- en waterreiniging Prof. dr. ir. A.J.M. Stams Persoonlijk hoogleraar bij het laboratorium voor Microbiologie Copromotor Prof. dr. ir. P.N.L. Lens Hoogleraar in de Milieubiotechnologie UNESCO-IHE, Delft Samenstelling promotiecommissie Prof. dr. ir. R.H. Wijffels Wageningen Universiteit, Nederland Dr. ir. G. Muyzer TU Delft, Nederland Dr. H.J.M. op den Camp Radboud Universiteit, Nijmegen, Nederland Prof. dr. ir. H. van Langenhove Universiteit Gent, België Dit onderzoek is uitgevoerd binnen de onderzoeksschool SENSE (Socio-Economic and Natural Sciences of the Environment) Anaerobic degradation of methanethiol in a process for Liquefied Petroleum Gas (LPG) biodesulfurization R.C. van Leerdam Proefschrift ter verkrijging van de graad van doctor op gezag van de rector magnificus van Wageningen Universiteit Prof. dr. M.J. Kropff in het openbaar te verdedigen op maandag 19 november 2007 des namiddags te vier uur in de Aula Van Leerdam, R.C., 2007. Anaerobic degradation of methanethiol in a process for Liquefied Petroleum Gas (LPG) biodesulfurization. PhD-thesis Wageningen University, Wageningen, The Netherlands – with references – with summaries in English and Dutch ISBN: 978-90-8504-787-2 Abstract Due to increasingly stringent environmental legislation car fuels have to be desulfurized to levels below 10 ppm in order to minimize negative effects on the environment as sulfur-containing emissions contribute to acid deposition (‘acid rain’) and to reduce the amount of particulates formed during the burning of the fuel. Moreover, low sulfur specifications are also needed to lengthen the lifetime of car exhaust catalysts. -
Base-Free Catalytic Aerobic Oxidation of Mercaptans for Gasoline Sweetening Over Htlcs-Derived Cuznal Catalyst
中国科技论文在线 http://www.paper.edu.cn Base-Free Catalytic Aerobic Oxidation of Mercaptans for Gasoline Sweetening over HTLcs-Derived CuZnAl Catalyst Lida Gao, Qingsong Xue, Ye Liu, and Yong Lu Shanghai Key Laboratory of Green Chemistry and Chemical Processes, Dept. of Chemistry, East China Normal University, Shanghai 200062, China DOI 10.1002/aic.11928 Published online August 13, 2009 in Wiley InterScience (www.interscience.wiley.com). An aerobic oxidative removal of mercaptans from gasoline in the absence of liquid base has been demonstrated for gasoline sweetening over CuZnAl catalyst. This pro- À cess could proceed at large WHSV of gasoline (50–70 h 1) with [95% mercaptan conversion at 150 C (or 300 C) using an O2/S molar ratio of 20–40. At 150 C, dimeri- zation of mercaptans occurred dominantly to form their disulfides. At 300C, deep oxi- dation of the mercaptans to SO2 was the dominant process in the first tens of hours, but it decreased then with prolonged time on stream and meanwhile the dimerization increased. The spent catalyst could be restored to its fresh activity level only through a calcination treatment in air. This process was also demonstrated to be effective and efficient for sweetening of a real cracking gasoline. VC 2009 American Institute of Chemical Engineers AIChE J, 55: 3214–3220, 2009 Keywords: catalysis, gasoline sweetening, aerobic oxidation, mercaptan, hydrotalcite, copper, zinc Introduction captan.2 The reaction mechanism can be summarized as overall reaction: 2RSH þ 1/2O ! RSSR þ H O. Mercaptans are widely distributed in petroleum products, 2 2 In the Merox process, an aqueous base, such as sodium especially in light oil like gasoline. -
THE H-OIL PROCESS: a Worldwxide LEADER in VACUUM RESIDUE HYDROPROCESSING” \ ^
—t&CR I'd, D 3 YJj TT-097 CONEXPO ARPEL '96 . i ' 1 "THE H-OIL PROCESS: A WORLDWXiDE LEADER IN VACUUM RESIDUE HYDROPROCESSING” \ ^ J.J. Colyar1 L.I. Wisdom2 A. Koskas3 SUMMARY With the uncertainty of market trends, refiners will need to hedge their investment strategies in the future by adding processing units that provide them with flexibility to meet the changing market. The various process configurations involving the H-Oil® Process described in this paper have been tested commercially and provide the refiner with the latest state of the art technology. ABSTRACT The H-Oil® Process is a catalytic hydrocracking process, invented by HRI, Inc., a division of IFP Enterprises, Inc. which is used to convert and upgrade petroleum residua and heavy oils. Today the H-Oil Process accounts for more than 50 percent of the worldwide vacuum residue hydroprocessing market due to its unique flexibility to handle a wide variety of heavy crudes 'while producing clean transportation fuels. The process is also flexible in terms of changes in yield selectivity and product quality. The unconverted vacuum residue from the process can be utilized for fuel oil production, blended into asphalt, routed to resid catalytic cracking, directly combusted or gasified to produce hydrogen. This paper will discuss additional background information on the H-Oil Process, some of the key advances made to the process and applications for the Latin America market. The paper will also discuss the status of recent commercial plants which are in operation or which are under design or construction and which utilize these new advances. -
Thermal Stability Analysis of Hydroprocessing Unit A
THERMAL STABILITY ANALYSIS OF HYDROPROCESSING UNIT A Thesis by YONGCHUL CHO Submitted to the Office of Graduate and Professional Studies of Texas A&M University in partial fulfillment of the requirements for the degree of MASTER OF SCIENCE Chair of Committee, M. Sam Mannan Committee Members, Mahmoud M. El-Halwagi Maria A. Barrufet Head of Department, M. Nazmul Karim May 2018 Major Subject: Chemical Engineering Copyright 2018 Yongchul Cho ABSTRACT Thermal stability is one of the most critical safety issues in the hydroprocessing units. Runaway reactions in the units can lead to catastrophic consequences as the reactors are being operated at high temperature and pressure, and the reactor effluent is a highly explosive mixture which contains hydrogen and hydrocarbons. For example, a fire and explosion due to a runaway reaction in a hydrocracking unit caused one death and forty-six injuries in 1997, in California. While the temperature runaway is the topic which has been studied extensively, most of the studies worked on simple reactions and little focused on the complex reactions such as hydroprocessing reactions. Also, in the studies on the hydroprocessing reactions, a lumping kinetic model was used which is less accurate and requires experiments for each application. In this research, the thermal stability of a naphtha hydrotreater will be analyzed by using a commercial process simulator ProMax where a novel mechanistic kinetic model, Single Event Kinetics has been integrated. Also, a simplified model will be established by using the data provided by ProMax for further analysis. The continuity and energy equations and parametric sensitivity equations will be solved by Matlab based on the methodology presented by Morbidelli and Varma. -
Hydrogen Sulfide Capture: from Absorption in Polar Liquids to Oxide
Review pubs.acs.org/CR Hydrogen Sulfide Capture: From Absorption in Polar Liquids to Oxide, Zeolite, and Metal−Organic Framework Adsorbents and Membranes Mansi S. Shah,† Michael Tsapatsis,† and J. Ilja Siepmann*,†,‡ † Department of Chemical Engineering and Materials Science, University of Minnesota, 421 Washington Avenue SE, Minneapolis, Minnesota 55455-0132, United States ‡ Department of Chemistry and Chemical Theory Center, University of Minnesota, 207 Pleasant Street SE, Minneapolis, Minnesota 55455-0431, United States ABSTRACT: Hydrogen sulfide removal is a long-standing economic and environ- mental challenge faced by the oil and gas industries. H2S separation processes using reactive and non-reactive absorption and adsorption, membranes, and cryogenic distillation are reviewed. A detailed discussion is presented on new developments in adsorbents, such as ionic liquids, metal oxides, metals, metal−organic frameworks, zeolites, carbon-based materials, and composite materials; and membrane technologies for H2S removal. This Review attempts to exhaustively compile the existing literature on sour gas sweetening and to identify promising areas for future developments in the field. CONTENTS 4.1. Polymeric Membranes 9785 4.2. Membranes for Gas−Liquid Contact 9786 1. Introduction 9755 4.3. Ceramic Membranes 9789 2. Absorption 9758 4.4. Carbon-Based Membranes 9789 2.1. Alkanolamines 9758 4.5. Composite Membranes 9790 2.2. Methanol 9758 N 5. Cryogenic Distillation 9790 2.3. -Methyl-2-pyrrolidone 9758 6. Outlook and Perspectives 9791 2.4. Poly(ethylene glycol) Dimethyl Ether 9759 Author Information 9792 2.5. Sulfolane and Diisopropanolamine 9759 Corresponding Author 9792 2.6. Ionic Liquids 9759 ORCID 9792 3. Adsorption 9762 Notes 9792 3.1. -
Treatment of Ethylene Spent Caustic Pollutant Using Sulfuric Acid
382 International Journal of Scientific & Engineering Research, Volume 6, Issue 10, October‐2015 ISSN 2229‐5518 Treatment of ethylene spent caustic pollutant using sulfuric acid ALI FARZI*, SAEID MOSLEMI BAYRAMI Abstract— Caustic soda is used in naphtha cracking units and petroleum refineries for sweetening of hydrocarbon streams. The generated caustic waste is an environmental pollutant and must be removed. Several methods are proposed for treatment of spent caustic such as wet air oxidation, biological treatment, etc. Spent caustic used in this work is prepared from Tabriz Petrochemical Company. In this work sulfuric acid was used for treatment of spent caustic which not only removes the waste, but also generates valuable product of sodium sulfate. In each experiment, 1L of spent caustic was taken and its color and phenol were removed by oxidization with H2O2. Then, 50 mL sulfuric acid was added and treatment process was performed. Different samples were taken at specified time periods to calculate percent waste conversion. The results showed that after 2.5 minutes it was about 79%, 84% and 92% at 25, 35 and 45°C, respectively. Index Terms— Spent caustic treatment, Sulfuric acid, Sodium sulfate, Response surface methodology, Analysis of variance —————————— —————————— 1 INTRODUCTION AUSTIC soda is used in petroleum refining and chemical Ellis [4] used wet air oxidation (WAO) method for Cindustries to remove sulfur compounds from treatment of refinery spent caustic. It has the advantage of not hydrocarbon streams. The resulting solution is usually producing odorous offgas. In a case study, COD of the effluent referred to as spent caustic and is deposited into the was decreased about 80% with pH of near 7 using this method environment. -
PETROLEUM: CHEMISTRY, REFINING, FUELS and PETROCHEMICALS - Petroleum: Chemistry, Refining, Fuels and Petrochemicals - Product Treating - James G
PETROLEUM: CHEMISTRY, REFINING, FUELS AND PETROCHEMICALS - Petroleum: Chemistry, Refining, Fuels and Petrochemicals - Product Treating - James G. Speight PETROLEUM: CHEMISTRY, REFINING, FUELS AND PETROCHEMICALS - PRODUCT TREATING James G. Speight 2476 Overland Road,Laramie, WY 82070-4808, USA Keywords: Caustic treating, Dualayer distillate process, Dualayer gasoline process, electrolytic mercaptan process, Ferrocyanide process, lye treatment, Mercapsol process, polysulfide treatment, Sodasol process, Solutizer process, steam regenerative caustic treatment, Unisol process, acid treating, Nalfining process, sulfuric acid treatment, clay and related processes, alkylation effluent treatment, Arosorb process, bauxite treatment, continuous contact filtration process, cyclic adsorption process, gray clay treatment, percolation filtration process, thermofor continuous percolation process, oxidative treating processes, bender process, copper sweetening process, doctor process, hypochlorite sweetening process, Merox process, solvent treating, deasphalting, solvent refining, dewaxing, gas treating, acid gas removal, gas sweetening Contents 1. Introduction 2. Caustic Processes 2.1. Dualayer Distillate Process 2.2. Dualayer Gasoline Process 2.3. Electrolytic Mercaptan Process 2.4. Ferrocyanide Process 2.5. Lye Treatment 2.6. Mercapsol Process 2.7. Polysulfide Treatment 2.8. Sodasol Process 2.9. Solutizer Process 2.10. Steam Regenerative Caustic Treatment 2.11. Unisol Process 3. Acid Processes 3.1. Nalfining Process 3.2. Sulfuric Acid Treatment 4. Clay -
Crude Expansion GHG PSD Revised Permit Application June 12, 2013
Diamond Shamrock Refining Company, L.P., a Valero Company Greenhouse Gas Prevention of Significant Deterioration Permit Application for Crude Expansion Project Valero McKee Refinery Sunray, Texas Updated December 2012 (Since the update in December 2012, this application was updated to account for responses to the EPA’s Additional Information Requests and to be consistent with those changes discussed in the cover letter of this consolidated application submittal. Refer to the “Addendum” Section at the end of this application.) 720 West Arapaho • Richardson, Texas • 75080 • 972/480-9800 • Fax 972/480-9865 TABLE OF CONTENTS SECTION 1 Introduction .................................................................................................... 1-1 1.1 Purpose of Request .................................................................................................. 1-1 1.2 Facility Information ................................................................................................. 1-2 1.3 Federal GHG Permitting Applicability ................................................................... 1-2 1.4 Application Contents ............................................................................................... 1-3 SECTION 2 Project Description......................................................................................... 2-1 2.1 Overview of Existing Refining Operations ............................................................. 2-1 2.2 Crude Expansion Project ........................................................................................ -
5.1 Petroleum Refining1
5.1 Petroleum Refining1 5.1.1 General Description The petroleum refining industry converts crude oil into more than 2500 refined products, including liquefied petroleum gas, gasoline, kerosene, aviation fuel, diesel fuel, fuel oils, lubricating oils, and feedstocks for the petrochemical industry. Petroleum refinery activities start with receipt of crude for storage at the refinery, include all petroleum handling and refining operations and terminate with storage preparatory to shipping the refined products from the refinery. The petroleum refining industry employs a wide variety of processes. A refinery's processing flow scheme is largely determined by the composition of the crude oil feedstock and the chosen slate of petroleum products. The example refinery flow scheme presented in Figure 5.1-1 shows the general processing arrangement used by refineries in the United States for major refinery processes. The arrangement of these processes will vary among refineries, and few, if any, employ all of these processes. Petroleum refining processes having direct emission sources are presented on the figure in bold-line boxes. Listed below are 5 categories of general refinery processes and associated operations: 1. Separation processes a. Atmospheric distillation b. Vacuum distillation c. Light ends recovery (gas processing) 2. Petroleum conversion processes a. Cracking (thermal and catalytic) b. Reforming c. Alkylation d. Polymerization e. Isomerization f. Coking g. Visbreaking 3.Petroleum treating processes a. Hydrodesulfurization b. Hydrotreating c. Chemical sweetening d. Acid gas removal e. Deasphalting 4.Feedstock and product handling a. Storage b. Blending c. Loading d. Unloading 5.Auxiliary facilities a. Boilers b. Waste water treatment c. Hydrogen production d. -
Process and Installation for the Treatment and Removal
JIChEC06 The Sixth Jordan International Chemical Engineering Conference 12-14 March 2101, Amman, Jordan NEW PROCESSES FOR THE TREATMENT OF THE USED ALKALINE SOLUTIONS FROM MEROX AND EXOMER PLANT Florin Oprea*, Elena-Fendu Mirela, Marilena Nicolae, Octav Pântea Universitatea Petrol – Gaze din Ploieşti, Romania Bd. Bucureşti 39, 100491 Ploieşti, Romania *) [email protected] ABSTRACT potential to process these residues but to not affect In all modern refineries there are the the environment. desulphurization installations, used to remove the sulphur compounds from intermediate or finale There are many technological solutions for treating products of the refineries. These installations and removal of these residues, mostly are expensive generate the used alkaline solutions, relative diluted both in terms of investment cost and operating cost, (5-12%) and significant amounts of organic beside are operated at relatively high temperatures compounds which include mercaptans and other and pressures. This paper presents a simple and compounds organic with sulphur, naphthenic acids, economic variant for treating these alkaline used crezilic acids, beside a great variety of compounds solutions. It is perfectly adaptable for the present organic or inorganic. Also it may be present variable desulphurization installations from the romanian amounts of hydrocarbons which constitute a distinct refineries. phase. Present paper presents two new, simple, safe, The problem of the used alkaline solutions economically technologies. These processes are The desulphurization processes for removal of the integrated for acid consumption reduction. These compounds with sulphur being in the intermediate or processes do not use high pressure and/or finale products of the refineries are widely used in temperature for treatment.