Environmental Issues of Synthetic Transportation Fuels from Coal (Part 5 of 9)
Total Page:16
File Type:pdf, Size:1020Kb
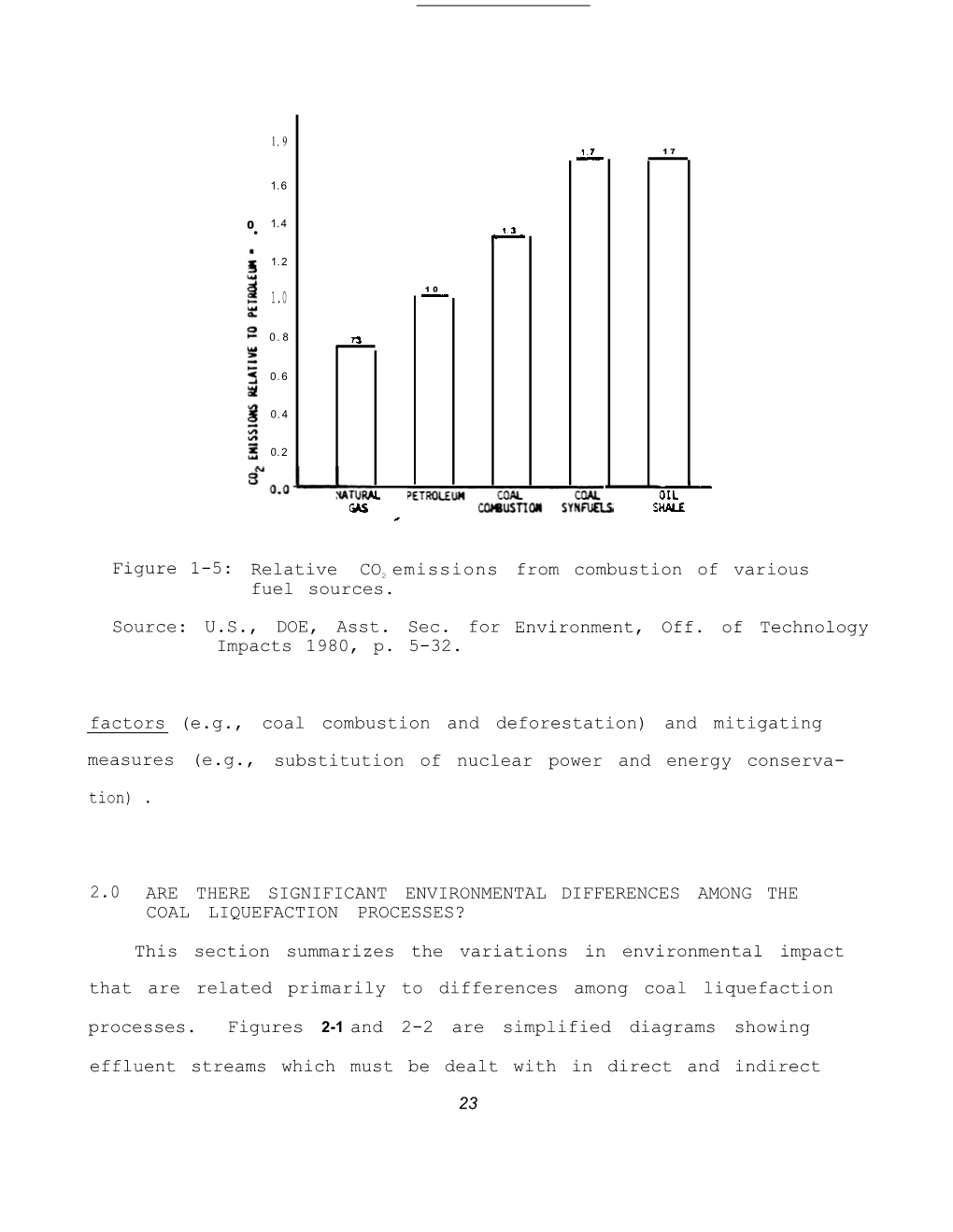
Load more
Recommended publications
-
Wave Liquefaction™ Combines Gaseous and Solid Hydrocarbons to Cleanly and Efficiently Produce Liquid Fuels Or Chemicals and Ca
Wave Liquefaction™ The Novel Coal-Biomass to Liquids Process George Skoptsov [email protected] H Quest Vanguard, Inc James Strohm [email protected] 750 William Pitt Way : Pittsburgh, PA 15238 Wave Liquefaction™ With only 15% biomass feed combines gaseous and solid and no CCS, lifecycle CO2 hydrocarbons to cleanly and emissions are 22% less than efficiently produce liquid fuels or for transportation fuels from chemicals and carbon char. Gases Solids Liquids Carbon conventional oil refining. SYNCRUDE COMPOSITION BACKGROUND TECHNOLOGY VERSATILITY Wave Liquefaction™ syncrude yields are Wave Liquefaction™ process was originally developed with the specific goal of establishing Properties of the Wave Liquefaction™ liquid product (aromaticity, density, 50%-65% wt (on dry, ash-free basis). the vast US coal resources as an alternative, cost-effective domestic source of military jet H:C ratio) can be widely varied by adjusting energy input, feedstock and Liquid product flows at room temperature, fuel with the lifecycle greenhouse gas emissions below those of a conventional crude oil gas composition. The product aromaticity can be made close to 100%, has API > 10, and < 50% aromaticity. Low refining process. Blending coal with 15% biomass by weight will decrease lifecycle CO2 with as much as 20% of the liquid yield consisting of the BTEX fraction. asphaltene content reduces requirements emissions by more than 20% relative to conventional gasoline production without use of Industrial non-fuel uses for these liquid and solid products include: for downstream hydrotreating needed to any carbon capture or sequestration solutions. Carbon pitch for production of aluminum smelting anodes: produce finished fuels. -
Recent Advances in Direct Coal Liquefaction
Energies 2010, 3, 155-170; doi:10.3390/en3020155 OPEN ACCESS energies ISSN 1996-1073 www.mdpi.com/journal/energies Review Recent Advances in Direct Coal Liquefaction Hengfu Shui 1, Zhenyi Cai 1 and Chunbao (Charles) Xu 2,* 1 School of Chemistry and Chemical Engineering, Anhui University of Technology, Maanshan 243002, Anhui, China; E-Mails: [email protected] (H.S.); [email protected] (Z.C.) 2 Department of Chemical Engineering, Lakehead University, Thunder Bay, Ontario P7B 5E1, Canada * Author to whom correspondence should be addressed; E-Mail: [email protected]; Tel.: +1-807-343-8761; Fax: +1-807-343-8928. Received: 16 November 2009 / Accepted: 19 January 2010 / Published: 27 January 2010 Abstract: The growing demand for petroleum, accompanied by the declining petroleum reserves and the concerns over energy security, has intensified the interest in direct coal liquefaction (DCL), particularly in countries such as China which is rich in coal resources, but short of petroleum. In addition to a general introduction on the mechanisms and processes of DCL, this paper overviews some recent advances in DCL technology with respect to the influencing factors for DCL reactions (temperature, solvent, pressure, atmospheres, etc.), the effects of coal pre-treatments for DCL (swelling, thermal treatment, hydrothermal treatment, etc.), as well as recent development in multi-staged DCL processes, DCL catalysts and co-liquefaction of coal with biomass. Keywords: direct coal liquefaction (DCL); processes; influencing factors; coal pre-treatment; catalysts; co-liquefaction; biomass 1. Introduction Due to the rapid increase in demand for petroleum and its declining reserves, the concern over energy security has intensified the interest in coal liquefaction, especially for those countries which are short of oil resources but have abundant coal reserves, such as the United States and China, etc. -
COAL CONFERENCE University of Pittsburgh · Swanson School of Engineering ABSTRACTS BOOKLET
Thirty-Fifth Annual INTERNATIONAL PITTSBURGH COAL CONFERENCE University of Pittsburgh · Swanson School of Engineering ABSTRACTS BOOKLET Clean Coal-based Energy/Fuels and the Environment October 15-18, 2018 New Century Grand Hotel Xuzhou Hosted by: The conference acknowledges the support of Co-hosted by: K. C. Wong Education Foundation, Hong Kong A NOTE TO THE READER This Abstracts Booklet is prepared solely as a convenient reference for the Conference participants. Abstracts are arranged in a numerical order of the oral and poster sessions as published in the Final Conference Program. In order to facilitate the task for the reader to locate a specific abstract in a given session, each paper is given two numbers: the first designates the session number and the second represents the paper number in that session. For example, Paper No. 25.1 is the first paper to be presented in the Oral Session #25. Similarly, Paper No. P3.1 is the first paper to appear in the Poster Session #3. It should be cautioned that this Abstracts Booklet is prepared based on the original abstracts that were submitted, unless the author noted an abstract change. The contents of the Booklet do not reflect late changes made by the authors for their presentations at the Conference. The reader should consult the Final Conference Program for any such changes. Furthermore, updated and detailed full manuscripts, published in the Conference Proceedings, will be sent to all registered participants following the Conference. On behalf of the Thirty-Fifth Annual International Pittsburgh Coal Conference, we wish to express our sincere appreciation and gratitude to Ms. -
Environmental, Health and Safety Guidelines for Coal Processing
Environmental, Health, and Safety Guidelines COAL PROCESSING WORLD BANK GROUP Environmental, Health and Safety Guidelines for Coal Processing Introduction such as host country context, assimilative capacity of the environment, and other project factors, are taken into account. The Environmental, Health, and Safety (EHS) Guidelines are The applicability of specific technical recommendations should technical reference documents with general and industry- be based on the professional opinion of qualified and specific examples of Good International Industry Practice experienced persons. When host country regulations differ 1 (GIIP) . When one or more members of the World Bank Group from the levels and measures presented in the EHS are involved in a project, these EHS Guidelines are applied as Guidelines, projects are expected to achieve whichever is more required by their respective policies and standards. These stringent. If less stringent levels or measures than those industry sector EHS guidelines are designed to be used provided in these EHS Guidelines are appropriate, in view of together with the General EHS Guidelines document, which specific project circumstances, a full and detailed justification provides guidance to users on common EHS issues potentially for any proposed alternatives is needed as part of the site- applicable to all industry sectors. For complex projects, use of specific environmental assessment. This justification should multiple industry-sector guidelines may be necessary. A demonstrate that the choice for any alternate performance complete list of industry-sector guidelines can be found at: levels is protective of human health and the environment www.ifc.org/ifcext/enviro.nsf/Content/EnvironmentalGuidelines Applicability The EHS Guidelines contain the performance levels and measures that are generally considered to be achievable in The EHS Guidelines for Coal Processing cover the processing new facilities by existing technology at reasonable costs. -
Coal Liquefaction and Desulfurization
COAL LIQUEFACTION AND DESULFURIZATION J. A. GUIN, Y. A. LIU, C. W. CURTIS, A. R. TARRER AND D. C. WILLIAMS The program is presently the Auburn University largest university-based coal research Auburn, AL 36849 program in the Southeastern region, and current support is . .. about $450,000 annually. ALABAMA IS A SIGNIFICANT producer of coal in the United States, particularly in the Gulf province. There are large reserves of coal in Ala aspects of the Auburn coal liquefaction research bama; 35 billion tons lie in the northern and program. It has made available its resources and central counties, enough for hundreds of years at facilities at the 6 tons/day solvent-refined-coal our present rate of production. Lignite deposits (SRC) pilot plant located at Wilsonville, Alabama in southern Alabama counties await the technology (90 miles from Auburn) for support of the super to properly realize their value. Thus, a strong vised internship and hands-on research training of recommendation of a statewide conference on the Auburn program. The largest utility coal user "Energy and the Future of Alabama" sponsored in the Northeast, the New England Electric by Auburn University in 1972 was for "research, System, has also actively participated in the Au development and technical liaison in the areas of burn coal desulfurization research since 1978. coal production, coal processing and coal usage." Auburn University acted upon this recommenda COAL RESEARCH FACULTY AND FACILITIES tion, and with major support from the National The Auburn coal liquefaction research program Science Foundation (NSF), established the Au is presently being directed by a number of burn Coal Conversion Research Laboratory in chemical engineering faculty, including Drs. -
Organic Petrology: an Overview
8 Organic Petrology: An Overview Suárez-Ruiz Isabel Instituto Nacional del Carbón (INCAR-CSIC) Oviedo Spain 1. Introduction Organic Petrology is a branch of the Earth Science that studies fossil organic matter in sedimentary sequences including coal and the finely dispersed organic matter in rocks (DOM). It was developed from coal petrology that dates back to the end of the 19th century. The organic petrology is usually expressed by two fundamental parameters: the nature and proportions of the organic constituents, and by the rank or maturity of these organic components. In the case of coals the amount and composition of its mineral matter (grade of a coal) is another parameter to be taken into account. The work carried out by the International Committee for Coal and Organic Pertrology (ICCP) related to the development of the maceral nomenclature, classification, standardization and the use of petrographic methods has been reported in various editions of the “ International Handbook of Coal Petrology” (ICCP, 1963, 1971, 1975, 1993) and other publications such as ICCP (1998, 2001) and Sýkorová et al. (2005). There are also several monographs focused on organic petrology such as those by Stach et al., (1982) and Taylor et al., (1998). Recently Suárez-Ruiz and Crelling (2008) edited a book on coal petrology and coal utilization. Other references in which organic petrology and/or coal petrology are discussed at some length include Ward (1984); Bustin et al. (1985); Falcon and Snyman (1986); Diessel (1992) and Teichmüller (1989). This chapter is an overview focused on organic petrology (including coal petrology), its fundamental concepts, the analytical techniques and the main current applications. -
Coal Liquefaction
http://uu.diva-portal.org This is an author produced version of a paper published in International journal of energy research. This paper has been peer-reviewed but does not include the final publisher proof-corrections or journal pagination. Citation for the published paper: Höök, M. & Aleklett, K. ”A review on coal-to-liquid fuels and its coal consumption” International journal of energy research, 2010, Vol. 34, Issue 10: 848-864 URL: http://dx.doi.org/10.1002/er.1596 Access to the published version may require subscription. Published in International Journal of Energy Research Volume 34, Issue 10, October 2010, Pages 848-864 http://dx.doi.org/10.1002/er.1596 A review on coal to liquid fuels and its coal consumption Mikael Höök*, Kjell Aleklett* Corresponding author: [email protected], phone: +46 18-471 7643, fax: +46 18-4713513 * Uppsala University, Global Energy Systems, Department of physics and astronomy, Box 535, SE-751 21, Lägerhyddsvägen 1, Sweden, http://www.fysast.uu.se/ges Abstract Continued reliance on oil is unsustainable and this has resulted in interest in alternative fuels. Coal-to-Liquids (CTL) can supply liquid fuels and have been successfully used in several cases, particularly in South Africa. This article reviews CTL theory and technology. Understanding the fundamental aspects of coal liquefaction technologies are vital for planning and policy-making, as future CTL systems will be integrated in a much larger global energy and fuel utilization system. Conversion ratios for CTL are generally estimated to be between 1-2 barrels/ton coal. This puts a strict limitation on future CTL capacity imposed by future coal production volumes, regardless of other factors such as economics, emissions or environmental concern. -
Thermochemical and Catalytic Upgrading in a Fuel Context: Peat, Biomass and Alkenes
TRITA-KET R 138 ISSN 1104-3466 ISRN KTH/KET/R--138--SE Thermochemical and Catalytic Upgrading in a Fuel Context: Peat, Biomass and Alkenes Christina Hörnell Dissertation Royal Institute of Technology Department of Chemical Engineering and Technology Chemical Technology Stockholm 2001 SAMMANFATTNING Denna avhandling avser metoder för ökad användning av alternativa bränslen. Heterogen oligomerisering av alkener för tillverkning av huvudsakligen bränslen och smörjoljor behandlas också. I Sverige har energieffektiviteten ökat och beroendet av importerad råolja minskat betydligt sedan 70-talet men det finns fortfarande behov av ökad användning av alternativa bränslen. Väsentliga egenskaper hos råmaterialen av intresse för denna avhandling, biomassa och torv, beskrivs, liksom de huvudsakliga förloppen vid termokemisk omvandling. Utvecklingen av teknologierna för förvätskning och förgasning beskrivs. Artikel I redogör för huvuddelen av det arbete som utfördes inom ’Olja ur torv’- projektet vid KTH. I artikel II jämförs upplösningen i tetralin av flera olika råmaterial. Råmaterialens reaktivitet befanns vara biomassa > torv > kol. Artikel III handlar om upplösning av torkad torv i simulerade recirkulerande lösningsmedel. Upplösningsgraden var beroende av lösningsmedlets aromaticitet och halt vätedonerande komponent. Tjäror bildas oundvikligen då biomassa förgasas. Dolomit är en billig och väldokumenterad krackningskatalysator för dessa tjäror, då tillräcklig temperatur och uppehållstid föreligger återstår nästan enbart bensen och naftalen efter krackningen. Artikel IV redovisar en studie av hur tjärnedbrytningen påverkas av att kisel tillsätts en dolomitbädd. Avhandlingen behandlar också heterogen oligomerisering av alkener. Artikel V är en genomgång av publikationer och patent som erhållits inom området heterogen alkenoligomerisering, utvärderade med avseende på använda katalysatorsystem, betingelser och produktselektivitet. Nyckelord: torv, biomassa, förvätskning, tetralin, förgasning, pyrolys, tjärkrackning, dolomit, kisel, heterogen oligomerisering, alkener. -
Direct Coal Liquefaction: Lessons Learned
Direct Coal Liquefaction: Lessons Learned Ripudaman Malhotra SRI International Menlo Park, CA 94025 Presented at GCEP Advanced Coal Workshop, BYU, Provo, UT; Mar 16, 2005 Outline Why Liquefaction? Changing needs Overview of direct coal liquefaction process ♦ Types of processes ♦ Process evolution ♦ Current status Chemical Lessons ♦ Reaction pathways ♦ Coal structure: what is needed to liquefy coal Conclusions ♦ Opportunities for improvement Why Coal Liquefaction? Alternate source for liquid fuels: national energy security ♦ Germany, Japan, South Africa Production of a clean and reactive solid fuel: SRC ♦ Liquids are a secondary product that may improve economics Oil embargos in the 1970’s reinforced need for an alternate source of transportation fuel Low oil prices in the next two decades: declining interest Now? Energy security, efficiency, climate… Liquefaction Increasing H/C ratio is a must; Two options ♦ Reject carbon Most pyrolysis processes ♦ Add hydrogen Dry pyrolysis with hydrogen not effective Coal liquefaction; use a solvent to effect hydrogenation Products often solid at room temperature Liquefaction defined by solubility Coal Liquefaction Approaches Pyrolysis or mild gasification Direct coal liquefaction Indirect coal liquefaction Co-processing Bioliquefaction Substantial overlap in the chemistry of mild gasification, direct coal liquefaction, and co-processing Direct Coal Liquefaction Processes: 1970 to 1995 Single-Stage Process: SRC-II, H-Coal, EDS Two-Stage Process: NTSL, ITSL, RITSL, DITSL, CTSL, CMSL… ♦ Many variations depending on Use of catalyst in the two stages (therm-cat, cat-cat) Distillation between stages Separation of solids between two stages or after second stage Recycle of ashy bottom Operation in H-balance Single-Stage Processes Contact coal with a solvent (2:1) with hydrogen or with hydrogenated solvent at ca. -
Characterization of Coal Using Electron Spin Resonance: Implications for the Formation of Inertinite Macerals in the Witbank Coalfield, South Africa
Int J Coal Sci Technol (2018) 5(3):385–398 https://doi.org/10.1007/s40789-018-0212-7 Characterization of coal using electron spin resonance: implications for the formation of inertinite macerals in the Witbank Coalfield, South Africa 1,2 3 2 Ofentse M. Moroeng • Jonathan M. Keartland • R. James Roberts • Nicola J. Wagner1 Received: 8 June 2018 / Revised: 4 July 2018 / Accepted: 8 August 2018 / Published online: 17 August 2018 Ó The Author(s) 2018 Abstract Coal contains a significant concentration of free radicals as a result of the coalification process. One of the experimental methods sensitive to the presence of radicals is electron spin resonance (ESR), and differences in ESR spectra for different macerals may provide insight into coal-forming processes. In this study, ESR data along with the H/C atomic ratio (to infer the aromatic fraction) are used to characterize coal samples with the aim of assessing a fire-origin for dominant inertinite macerals. A medium rank C bituminous Witbank No. 4 Seam Upper coal (the parent) was density- fractionated to create vitrinite-rich and inertinite-rich samples. The parent sample consists of 42 vol% vitrinite and 49 vol% inertinite. The density-fractionated samples comprise of 81 vol% total vitrinite (dominated by collotelinite and collode- trinite), and 63 vol% total inertinite (dominated by fusinite, semifusinite, and inertodetrinite). The H/C ratio is 0.74 for the inertinite-rich sample, and 0.85 for the vitrinite-rich counterpart, suggesting the former sample is more aromatic. The ESR spectra obtained for the three samples were found to fit best using a Lorentzian distribution. -
Liquefaction of Peat and Biomass
-OOOCL i mini mi BG9700003 ENERGY FORUM 12-14-JUNE1996 INTERNATIONAL HOUSE OF SCIENTIST »F. J. CURIE", VARNA, BULGARIA STUDIES ON LIQUEFACTION AND PYROLYSIS OF PEAT AND BIOMASS AT KTH Emilia Bjdrnbom, Krister Sjdstrdm, Christina Hdrnell, Rolando Zanzi andPehr Bjdrnbom Department of Chemical Engineering and Technology, Chemical Technology Royal Institute of Technology, KTH, S-l 0044 Stockholm, Sweden Tel. (+468) 7908256, Fax. (+468) 1085 79 Abstract Thermochemical processes for conversion of peat and biomass have been studied at Kungliga Tekniska Hdgskolan, KTH, (Royal Institute of Technology, Stockholm) since the energy crisis in the seventies. Pyrolysis has mostly been studied as a tool for better understanding of both liquefaction and gasification of the fuels. Intensive work on the liquefaction has taken place mostly in the period between 1976 and 1990. The present activities are focused on the gasification and pyrolysis of biomass. Introduction The research on the thermochemical conversion of peat and biomass in Sweden was intensified after the energy crisis 1973 (Rensfelt et al., 1978; Bjdrnbom, P., 1976). Intensive studies on peat liquefaction took place at KTH until 1990 (Bjdrnbom, P., 1979, 1983; Bjdrnbom, P. et al., 1981, 1987; Bjdrnbom, P. and Bjdrnbom, E., 1988; Bjdrnbom, E. and Bjdrnbom, P., 1988; Bjdrnbom, E. et al., 1979 1980, 1986, 1988, 1991; Hdrnell et al., 1985). The decrease of the oil prices in the eighties cooled down the interest of the authorities in Sweden in the development of a process for direct liquefaction of peat and biomass. The activities on the gasification at KTH after the energy crisis aimed mostly the practical application of the process (Rensfelt et al., 1978). -
Liquefaction of Coal - Li Tingchen
COAL, OIL SHALE, NATURAL BITUMEN, HEAVY OIL AND PEAT – Vol. I - Liquefaction of Coal - Li Tingchen LIQUEFACTION OF COAL Li Tingchen Department of Chemical Technology for Energy Source, East China University of Science, and Technology,China Keywords: Direct liquefaction, indirect liquefaction, thermal decomposition, hydrogenation, de-heteroatom reaction, condensation reaction, hydrogen-donor solvent, catalyst, fossil energy, Fischer-Tropsch synthesis, liquid fuel, synthetic oil, synthetic gas, hydro-liquefaction, thermal rupture, radical fragment, active hydrogen, bond scission, coke, char, catalytic hydrogenation, isomerization, dehydrogenation, intermediate product, petrographic phase, kinetic behaviour, volatility, coalification degree, peat, lignite, bituminious coal, anthracite, extraction liquefaction, preasphaltene, asphaltene, vitrain, clarain, fusain, coal slurry, carbon disposition, thermal sinister Contents 1. Introduction 2. Direct Liquefaction 2.1 Physicochemical Principles 2.2 Major Factors Pertinent to Liquefaction 2.2.1 Coal as Raw Material 2.2.2 Solvent 2.2.3 Catalysts 2.2.4 Temperature and Pressure 2.3 Direct Liquefaction Process 2.3.1 Coal Liquefaction Processes at Earlier Stage 2.3.2 Some Advanced Liquefaction Processes 2.3.3 Solvent-Extraction Liquefaction Process 2.4 Current State of Direct Liquefaction of Coal 3. Indirect Coal Liquefaction 3.1 Fischer-Tropsch Synthesis Process 3.1.1 Catalysts 3.1.2 Process Parameters 3.1.3 Developments in Indirect Liquefaction 4. Conclusion GlossaryUNESCO – EOLSS Bibliography Biographical SketchSAMPLE CHAPTERS Summary Coal liquefaction is an industrial process in which coal as raw material, through chemical reactions, is converted into liquid hydrocarbon mixture, which, under further processing, becomes desired liquid fuels or chemical feedstock. Therefore, the main purpose of coal liquefaction lies in production of either synthetic oil as a partial substitute resource for crude oil or aromatic hydrocarbons as feedstock in organic chemical industry.