Micromechanics of Engineered and Biological Systems
Total Page:16
File Type:pdf, Size:1020Kb
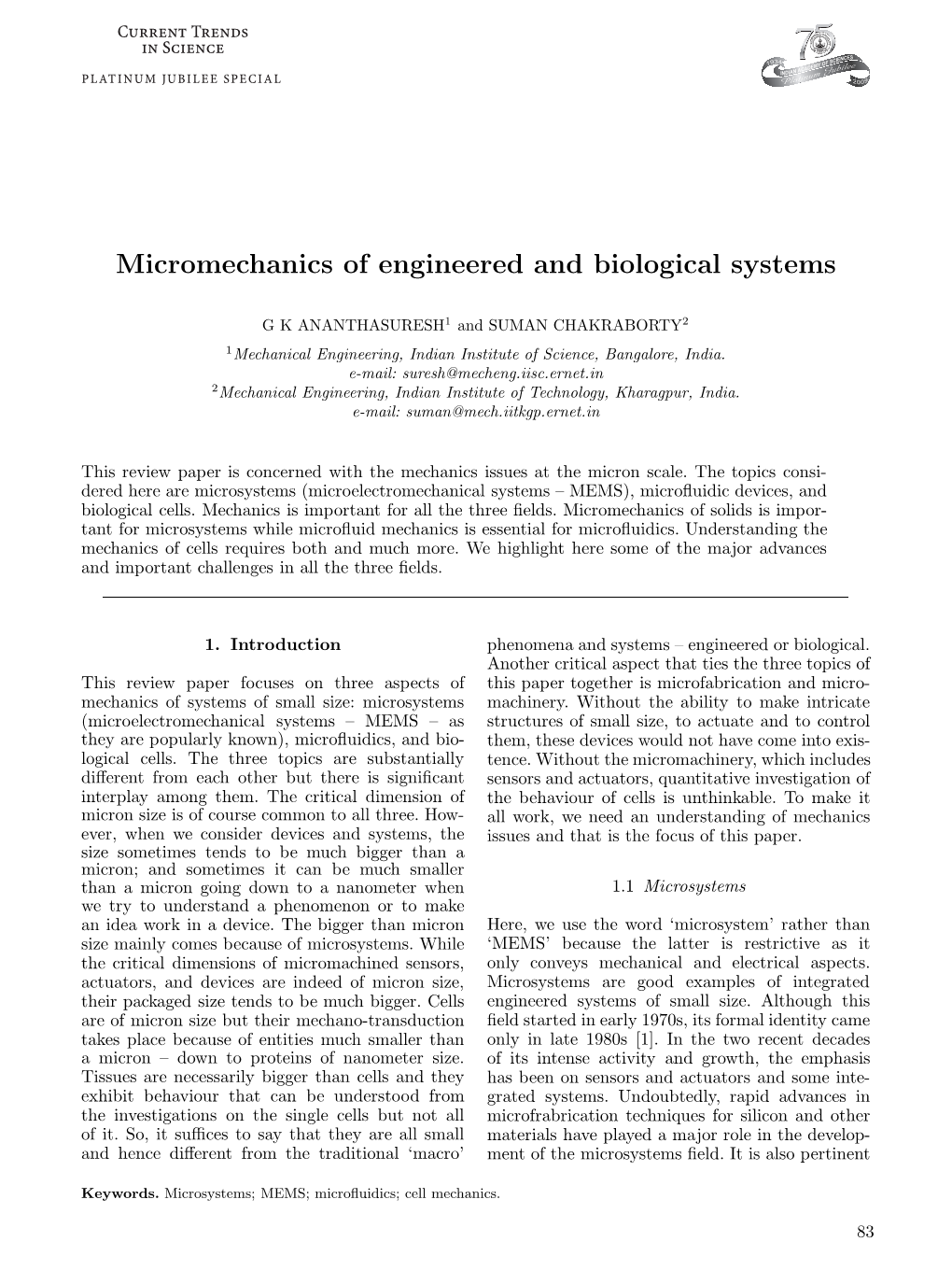
Load more
Recommended publications
-
Chapter 10: Composite Micromechanics
Application of the Finite Element Method Using MARC and Mentat 10-1 Chapter 10: Composite Micromechanics 10.1 Problem Statement and Objectives Given the micromechanical geometry and the material properties of each constituent, it is possible to estimate the effective composite material properties and the micromechanical stress/strain state of a composite material. The objectives of this project are (1) to determine the effective stiffness c c ν c ν c properties E1 , E2 , 12 , 23 of a unidirectional composite material and (2) to determine the strain concentration factor in the matrix region when the composite material is subjected to a uniform transverse normal strain in the X 2 direction. NOTE TO ME 424 CLASS: Only do Part (2). 10.2 Background A composite material is often defined as a combination of two or more materials fabricated in such a way that the individual constituents (materials) can still be readily identified in the final form. If designed properly, this combination of materials yields a composite material that exhibits the best properties of each constituent as well as some advantageous properties not exhibited by the individual constituents. One example of such a material is a unidirectional fiber reinforced composite, which is often used in aerospace structures. An idealized micromechanical view of a unidirectional fiber reinforced composite material is shown in Figure 10.1. In these materials, the fibers have a very small diameter and a very high length-to-diameter ratio. This geometry yields excellent stiffness and strength characteristics in the fiber, since the crystals tend to align along the fiber axis and there are fewer internal and surface defects than in the bulk material. -
Micromechanics As a Basis of Stochastic Finite Elements And
Micromechanics as a basis of stochastic finite elements and differences: An overview M Ostoja-Starzewski Department of Materials Science and Mechanics Michigan State University, East Lansing, MI 48824-1226 A generalization of conventional deterministic finite element and difference methods to deal with spatial material fluctuations hinges on the problem of determination of stochastic constitutive laws. This problem is analyzed here through a paradigm of micromechanics of elastic polycrystals and matrix-inclusion composites. Passage to a sought-for random meso-continuum is based on a scale dependent window playing the role of a Representative Volume Element (RVE). It turns out that the microstructure cannot be uniquely approximated by a random field of stiffness with continuous realizations, but, rather, two random continuum fields may be introduced to bound the material response from above and from below. Since the RVE corresponds to a single finite element, or finite difference cell, not infinitely larger than the crystal size, these two random fields are to be used to bound the solution of a given boundary value problem at a given scale of resolution. The window- based random continuum formulation is also employed in analysis of rigid perfectly-plastic mate rials, whereby the classical method of slip-lines is generalized to a stochastic finite difference scheme. The present paper is complemented by a comparison of this methodology to other existing stochastic solution methods. 1. INTRODUCTION a locally isotropic form The necessity to account for random effects in determining a.. = X(x, co) 5..e +2u(x, co)e.. n ^ the response of a mechanical system is due, in general, to »J iJ kk 'J {Li> three different sources: random external forcing, random is adopted by simply postulating one or both elastic constants, boundary conditions, and random material parameters. -
MICROMECHANICS of STRESS-INDUCED MARTENSITIC TRANSFORMATION in MONO- and POLYCRYSTALLINE SHAPE MEMORY ALLOYS; Ni-Ti
Advanced Materials for the 21st Century: The 1999 Julia R. Weertman Symposium, 1999 TMS Fall Meeting in Cincinnati, OH, USA., Oct. 31-Nov.4, pp.385-396 MICROMECHANICS OF STRESS-INDUCED MARTENSITIC TRANSFORMATION IN MONO- AND POLYCRYSTALLINE SHAPE MEMORY ALLOYS; Ni-Ti Y. Liang, M. Taya and T. Mori* Department of Mechanical Engineering University of Washington Seattle, WA 98195-2600 Abstract Stress-induced martensitic transformation in single crystals and polycrystals are examined on the basis of micromechanics. A simple method to find a stress- and elastic energy-free martensite plate (combined variant), which consists of two variants, is presented. External and internal stresses preferentially produce a combined variant, to which the stresses supply the largest work upon its formation. Using the chemical energy change with temperature, the phase boundary between the parent and martensitic phases is determined in stress-temperature diagrams. The method is extended to a polycrystal, modeled as an aggregate of spherical grains. The grains constitute axisymmetric multiple fiber textures and a uniaxial load is applied to the fiber axis. The occurrence and progress of transformation are followed by examining a stress state in the grains. The stress is the sum of the external stress and internal stress. The difference in the fraction of transformation and, thus, in transformation strains between the grains causes the internal stress, which is calculated with the average field method. After a short transition stage, all the grains start to transform, and the external uniaxial stress to continue the transformation increases linearly thereafter. The external stress at the end of the transition is defined as the macroscopic yield stress due to the transformation in polycrystals. -
Viscoelastic Behavior of Polymer-Modified Cement
applied sciences Article Viscoelastic Behavior of Polymer-Modified Cement Pastes: Insight from Downscaling Short-Term Macroscopic Creep Tests by Means of Multiscale Modeling Luise Göbel 1,2,*,†, Markus Königsberger 2,3 ID , Andrea Osburg 1 ID and Bernhard Pichler 2 1 F.A. Finger-Institute for Building Material Engineering, Bauhaus-Universität Weimar, 99423 Weimar, Germany; [email protected] 2 Institute for Mechanics of Materials and Structures, TU Wien—Vienna University of Technology, 1040 Vienna, Austria; [email protected] (M.K.); [email protected] (B.P.) 3 BATir Department, Université libre de Bruxelles (ULB), 1050 Bruxelles, Belgium * Correspondence: [email protected]; Tel.: +49-3643-584743 † Current address: Coudraystraße 11 A, 99423 Weimar, Germany. Received: 28 February 2018; Accepted: 21 March 2018; Published: 23 March 2018 Abstract: Adding polymers to cementitious materials improves their workability and impermeability, but also increases their creep activity. In the present paper, the creep behavior of polymer-modified cement pastes is analyzed based on macroscopic creep tests and a multiscale model. The continuum micromechanics model allows for “downscaling” the results of macroscopic hourly-repeated ultra-short creep experiments to the viscoelastic behavior of micron-sized hydration products and polymer particles. This way, the increased creep activity of polymer-modified cement pastes is traced back to an isochoric power-law-type creep behavior of the polymers. The shear creep modulus of the polymers is found (i) to be two orders of magnitude smaller than that of the hydrates and (ii) to increase considerably with increasing material age. The latter result suggests that the creep activity of the polymers decreases with the self-desiccation-related decrease of the relative humidity inside the air-filled pores of cement paste. -
MEMS Fabrication1
16 MEMS Fabrication1 Marc J. Madou 16.1 Wet Bulk Micromachining: Introduction Nanogen, Inc. 16.2 Historical Note 16.3 Silicon Crystallography Miller Indices • Crystal Structure of Silicon • Geometric Relationships between Some Important Planes in the Silicon Lattice 16.4 Silicon as a Substrate and Structural Material Silicon as Substrate • Silicon as a Structural Element in Mechanical Sensors 16.5 Wet Isotropic and Anisotropic Etching Wet Isotropic and Anisotropic: Empirical Observations • Chemical Etching Models 16.6 Etching With Bias and/or Illumination of the Semiconductor Electropolishing and Microporous Silicon 16.7 Etch-Stop Techniques Introduction • Boron Etch Stop • Electrochemical Etch-Stop Technique • Photo-Assisted Electrochemical Etch Stop (for n-Type Silicon) • Photo-Induced Preferential Anodization, PIPA (for p-Type Silicon) • Etch Stop at Thin Films-Silicon on Insulator 16.8 Problems with Wet Bulk Micromachining Introduction • Extensive Real Estate Consumption • Corner Compensation 16.9 Wet Bulk Micromachining Examples 16.10 Surface Micromachining: Introduction 16.11 Historical Note 16.12 Mechanical Properties of Thin Films Introduction • Adhesion • Stress in Thin Films • Strength of Thin Films 16.13 Surface Micromachining Processes Basic Process Sequence • Fabrication Step Details • Control of Film Stress • Dimensional Uncertainties • Sealing Processes in Surface Micromachining • IC Compatibility 16.14 Poly-Si Surface Micromachining Modifications Porous Poly-Si • Hinged Polysilicon • Thick Polysilicon • Milli-Scale Molded -
Chiral Metamaterial Predicted by Granular Micromechanics: Verified With
1 Chiral Metamaterial Predicted by Granular Micromechanics: Verified with 2 1D Example Synthesized using Additive Manufacturing 3 4 5 Anil Misra1*, Nima Nejadsadeghi 2, Michele De Angelo 1,3, Luca Placidi 4 6 7 8 1Civil, Environmental and Architectural Engineering Department, 9 University of Kansas, 1530 W. 15th Street, Learned Hall, Lawrence, KS 66045-7609. 10 2Mechanical Engineering Department, 11 University of Kansas, 1530 W. 15th Street, Learned Hall, Lawrence, KS 66045-7609. 12 3Dipartimento di Ingegneria Civile, Edile-Architettura e Ambientale, Università degli Studi 13 dellAquila, Via Giovanni Gronchi 18 - Zona industriale di Pile, 67100 LAquila, Italy 14 3International Telematic University Uninettuno, 15 C. so Vittorio Emanuele II 39, 00186 Rome, Italy 16 *corresponding author: Ph: (785) 864-1750, Fax: (785) 864-5631, Email: [email protected] 17 18 19 20 21 22 23 Continuum Mechanics and Thermodynamics 24 25 26 27 28 Abstract 29 Granular micromechanics approach (GMA) provides a predictive theory for granular material 30 behavior by connecting the grain-scale interactions to continuum models. Here we have used 31 GMA to predict the closed-form expressions for elastic constants of macro-scale chiral granular 32 metamaterial. It is shown that for macro-scale chirality, the grain-pair interactions must include 33 coupling between normal and tangential deformations. We have designed such a grain-pair 34 connection for physical realization and quantified with FE model. The verification of the 35 prediction is then performed using a physical model of 1D bead string obtained by 3D printing. 36 The behavior is also verified using a discrete model of 1D bead string. -
Micromechanics Models for Viscoelastic Plain-Weave Composite Tape Springs
AIAA JOURNAL Vol. 55, No. 1, January 2017 Micromechanics Models for Viscoelastic Plain-Weave Composite Tape Springs Kawai Kwok∗ Technical University of Denmark, 4000 Roskilde, Denmark and Sergio Pellegrino† California Institute of Technology, Pasadena, California 91125 DOI: 10.2514/1.J055041 The viscoelastic behavior of polymer composites decreases the deployment force and the postdeployment shape accuracy of composite deployable space structures. This paper presents a viscoelastic model for single-ply cylindrical shells (tape springs) that are deployed after being held folded for a given period of time. The model is derived from a representative unit cell of the composite material, based on the microstructure geometry. Key ingredients are the fiber volume density in the composite tows and the constitutive behavior of the fibers (assumed to be linear elastic and transversely isotropic) and of the matrix (assumed to be linear viscoelastic). Finite-element-based homogenizations at two scales are conducted to obtain the Prony series that characterize the orthotropic behavior of the composite tow, using the measured relaxation modulus of the matrix as an input. A further homogenization leads to the lamina relaxation ABD matrix. The accuracy of the proposed model is verified against the experimentally measured time- dependent compliance of single lamina in either pure tension or pure bending. Finite element simulations of single-ply tape springs based on the proposed model are compared to experimental measurements that were also obtained during -
Call for Papers | 2022 MRS Spring Meeting
Symposium CH01: Frontiers of In Situ Materials Characterization—From New Instrumentation and Method to Imaging Aided Materials Design Advancement in synchrotron X-ray techniques, microscopy and spectroscopy has extended the characterization capability to study the structure, phonon, spin, and electromagnetic field of materials with improved temporal and spatial resolution. This symposium will cover recent advances of in situ imaging techniques and highlight progress in materials design, synthesis, and engineering in catalysts and devices aided by insights gained from the state-of-the-art real-time materials characterization. This program will bring together works with an emphasis on developing and applying new methods in X-ray or electron diffraction, scanning probe microscopy, and other techniques to in situ studies of the dynamics in materials, such as the structural and chemical evolution of energy materials and catalysts, and the electronic structure of semiconductor and functional oxides. Additionally, this symposium will focus on works in designing, synthesizing new materials and optimizing materials properties by utilizing the insights on mechanisms of materials processes at different length or time scales revealed by in situ techniques. Emerging big data analysis approaches and method development presenting opportunities to aid materials design are welcomed. Discussion on experimental strategies, data analysis, and conceptual works showcasing how new in situ tools can probe exotic and critical processes in materials, such as charge and heat transfer, bonding, transport of molecule and ions, are encouraged. The symposium will identify new directions of in situ research, facilitate the application of new techniques to in situ liquid and gas phase microscopy and spectroscopy, and bridge mechanistic study with practical synthesis and engineering for materials with a broad range of applications. -
Variational Asymptotic Micromechanics Modeling of Composite Materials
Utah State University DigitalCommons@USU All Graduate Theses and Dissertations Graduate Studies 12-2008 Variational Asymptotic Micromechanics Modeling of Composite Materials Tian Tang Follow this and additional works at: https://digitalcommons.usu.edu/etd Part of the Applied Mechanics Commons Recommended Citation Tang, Tian, "Variational Asymptotic Micromechanics Modeling of Composite Materials" (2008). All Graduate Theses and Dissertations. 72. https://digitalcommons.usu.edu/etd/72 This Dissertation is brought to you for free and open access by the Graduate Studies at DigitalCommons@USU. It has been accepted for inclusion in All Graduate Theses and Dissertations by an authorized administrator of DigitalCommons@USU. For more information, please contact [email protected]. VARIATIONAL ASYMPTOTIC MICROMECHANICS MODELING OF COMPOSITE MATERIALS by Tian Tang A dissertation submitted in partial ful¯llment of the requirements for the degree of DOCTOR OF PHILOSOPHY in Mechanical Engineering Approved: Dr. Wenbin Yu Dr. Leijun Li Major Professor Committee Member Dr. Brent E. Stucker Dr. Thomas H. Fronk Committee Member Committee Member Dr. David E. Richardson Dr. Byron R. Burnham Committee Member Dean of Graduate Studies UTAH STATE UNIVERSITY Logan, Utah 2008 ii Copyright °c Tian Tang 2008 All Rights Reserved iii Abstract Variational Asymptotic Micromechanics Modeling of Composite Materials by Tian Tang, Doctor of Philosophy Utah State University, 2008 Major Professor: Dr. Wenbin Yu Department: Mechanical and Aerospace Engineering The issue of accurately determining the e®ective properties of composite materials has received the attention of numerous researchers in the last few decades and continues to be in the forefront of material research. Micromechanics models have been proven to be very useful tools for design and analysis of composite materials. -
As Filed with the Securities and Exchange Commission on June 30, 1999
As filed with the Securities and Exchange Commission on June 30, 1999 -------------------------------------------------------------------------------- SECURITIES AND EXCHANGE COMMISSION Washington, D.C. 20549 FORM 20-F |_| REGISTRATION STATEMENT PURSUANT TO SECTION 12(b) OR (g) OF THE SECURITIES EXCHANGE ACT OF 1934 OR |X| ANNUAL REPORT PURSUANT TO SECTION 13 OR 15(d) OF THE SECURITIES ACT OF 1934 For the fiscal year ended: December 31, 1998 OR |_| TRANSITION REPORT PURSUANT TO SECTION 13 OR 15(d) OF THE SECURITIES ACT OF 1934 For the transition period from to Commission file number: 1-13546 STMicroelectronics N.V. (Exact name of Registrant as specified in its charter) Not Applicable The Netherlands (Translation of Registrant's (Jurisdiction of incorporation name into English) or organization) Technoparc du Pays de Gex -- B.P. 112 Route de Pre-Bois 165, rue Edouard Branly ICC Bloc A 01637 Saint Genis Pouilly 1215 Geneva 15 France Switzerland (Addresses of principal executive offices) Securities registered or to be registered pursuant to Section 12(b) of the Act: Name of each exchange on Title of each class: which registered: Common Shares, nominal value Euro 3.12 per share New York Stock Exchange Liquid Yield OptionTM Notes due June 10, 2008 New York Stock Exchange Securities registered or to be registered pursuant to Section 12(g) of the Act: None Securities for which there is a reporting obligation pursuant to Section 15(d) of the Act: None Indicate the number of outstanding shares of each of the issuer's classes of capital or common stock as of the close of the period covered by the annual report: 142,478,106 Common Shares Indicate by check mark whether the registrant (1) has filed all reports required to be filed by Section 13 or 15(d) of the Securities Exchange Act of 1934 during the preceding 12 months (or for such shorter period that the registrant was required to file such reports), and (2) has been subject to such filing requirements for the past 90 days. -
Micromechanics-Based Prediction of the Effective Properties of Piezoelectric Composite Having Interfacial Imperfections
Micromechanics-based prediction of the effective properties of piezoelectric composite having interfacial imperfections Sangryun Leea, Jiyoung Junga, and Seunghwa Ryua,* Affiliations aDepartment of Mechanical Engineering, Korea Advanced Institute of Science and Technology (KAIST), 291 Daehak-ro, Yuseong-gu, Daejeon 34141, Republic of Korea *Corresponding author e-mail: [email protected] Abstract We derive an analytical expression to predict the effective properties of a particulate- reinforced piezoelectric composite with interfacial imperfections using a micromechanics- based mean–field approach. We correctly derive the analytical formula of the modified Eshelby tensor, the modified concentration tensor, and the effective property equations based on the modified Mori–Tanaka method in the presence of interfacial imperfections. Our results are validated against finite element analyses (FEA) for the entire range of interfacial damage levels, from a perfect to a completely disconnected and insulated interface. For the facile evaluation of the nontrivial tensorial equations, we adopt the Mandel notation to perform tensor operations with 99 symmetric matrix operations. We apply the method to predict the effective properties of a representative piezoelectric composite consisting of PVDF and SiC reinforcements. Keywords Piezoelectric composite, Eshelby tensor, Interfacial damage, Effective modulus 1. Introduction Piezoelectricity refers to the electric charge accumulation in response to an applied mechanical loading, or, conversely, the mechanical -
2000 Annual Report (Form 20-F)
As filed with the Securities and Exchange Commission on May 15, 2001 SECURITIES AND EXCHANGE COMMISSION Washington, D.C. 20549 FORM 20-F £ REGISTRATION STATEMENT PURSUANT TO SECTION 12(b) OR (g) OF THE SECURITIES EXCHANGE ACT OF 1934 OR T ANNUAL REPORT PURSUANT TO SECTION 13 OR 15(d) OF THE SECURITIES EXCHANGE ACT OF 1934 For the fiscal year ended: December 31, 2000 OR £ TRANSITION REPORT PURSUANT TO SECTION 13 OR 15(d) OF THE SECURITIES EXCHANGE ACT OF 1934 For the transition period from to Commission file number: 1-13546 STMicroelectronics N.V. (Exact name of Registrant as specified in its charter) Not Applicable The Netherlands (Translation of Registrant’s (Jurisdiction of incorporation name into English) or organization) Route de Pré-Bois ICC Bloc A1215 Geneva 15 Switzerland (Address of principal executive offices) Securities registered or to be registered pursuant to Section 12(b) of the Act: Name of each exchange on Title of each class: which registered: Common Shares, nominal value € 1.04 per share New York Stock Exchange Liquid Yield OptionTM Notes due June 10, 2008 New York Stock Exchange Liquid Yield OptionTM Notes due September 22, 2009 New York Stock Exchange Securities registered or to be registered pursuant to Section 12(g) of the Act: None Securities for which there is a reporting obligation pursuant to Section 15(d) of the Act: None Indicate the number of outstanding shares of each of the issuer’s classes of capital or common stock as of the close of the period covered by the annual report: 889,881,287 Common Shares Indicate by check mark whether the registrant (1) has filed all reports required to be filed by Section 13 or 15(d) of the Securities Exchange Act of 1934 during the preceding 12 months (or for such shorter period that the registrant was required to file such reports), and (2) has been subject to such filing requirements for the past 90 days.