Maximum Fuel Utilization in Advanced Fast Reactors Without Actinides Separation
Total Page:16
File Type:pdf, Size:1020Kb
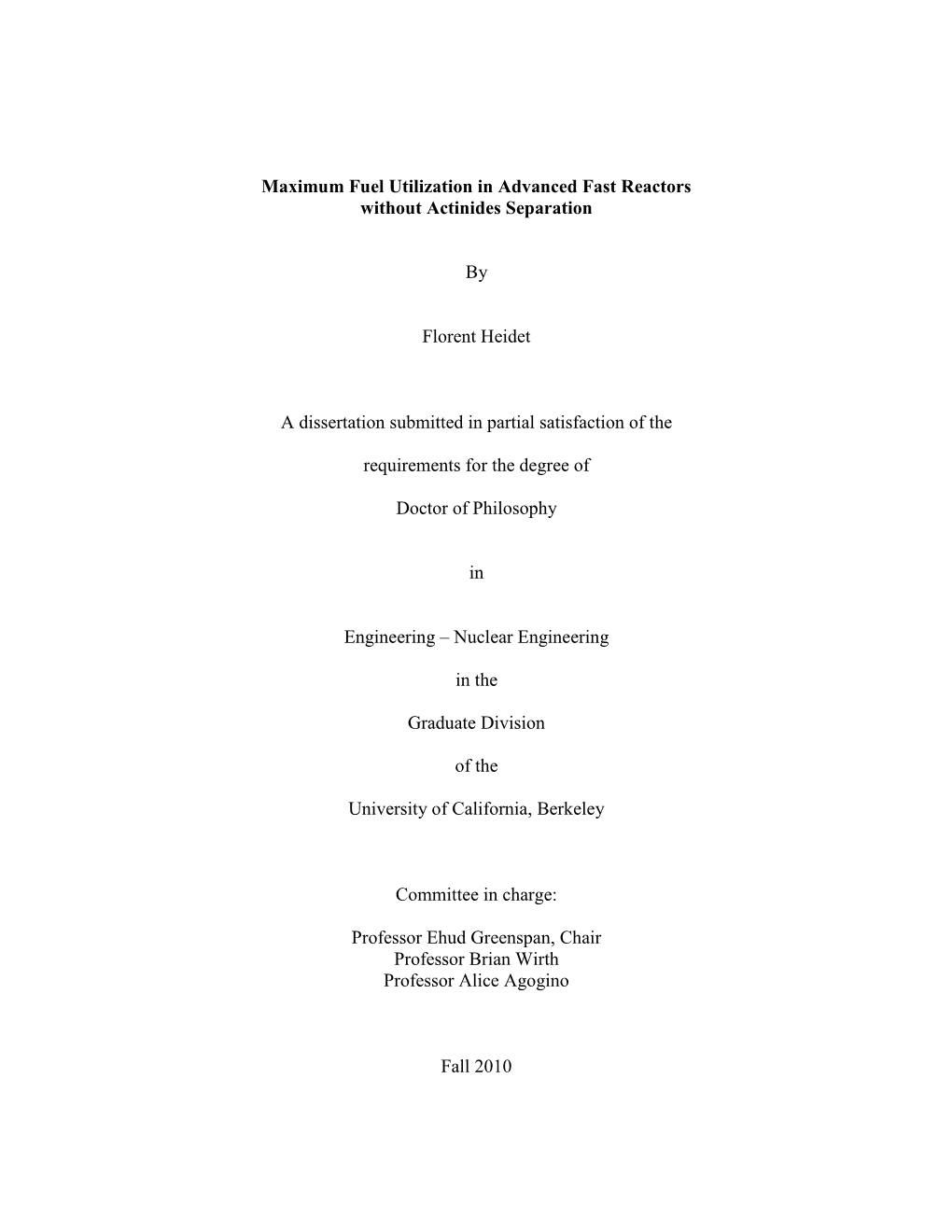
Load more
Recommended publications
-
Vver and Rbmk Cross Section Libraries for Origen-Arp
VVER AND RBMK CROSS SECTION LIBRARIES FOR ORIGEN-ARP Germina Ilas, Brian D. Murphy, and Ian C. Gauld, Oak Ridge National Laboratory, USA Introduction An accurate treatment of neutron transport and depletion in modern fuel assemblies characterized by heterogeneous, complex designs, such as the VVER or RBMK assembly configurations, requires the use of advanced computational tools capable of simulating multi-dimensional geometries. The depletion module TRITON [1], which is part of the SCALE code system [2] that was developed and is maintained at the Oak Ridge National Laboratory (ORNL), allows the depletion simulation of two- or three-dimensional assembly configurations and the generation of burnup-dependent cross section libraries. These libraries can be saved for subsequent use with the ORIGEN-ARP module in SCALE. This later module is a faster alternative to TRITON for fuel depletion, decay, and source term analyses at an accuracy level comparable to that of a direct TRITON simulation. This paper summarizes the methodology used to generate cross section libraries for VVER and RBMK assembly configurations that can be employed in ORIGEN-ARP depletion and decay simulations. It briefly describes the computational tools and provides details of the steps involved. Results of validation studies for some of the libraries, which were performed using isotopic assay measurement data for spent fuel, are provided and discussed. Cross section libraries for ORIGEN-ARP Methodology The TRITON capability to perform depletion simulations for two-dimensional (2-D) configurations was implemented by coupling of the 2-D transport code NEWT with the point depletion and decay code ORIGEN-S. NEWT solves the transport equation on a 2-D arbitrary geometry grid by using an SN approach, with a treatment of the spatial variable that is based on an extended step characteristic method [3]. -
The Effect of Burnup and Separation Efficiency on Uranium Utilization and Radiotoxicity
INL/CON-10-20154 PREPRINT The Effect of Burnup and Separation Efficiency on Uranium Utilization and Radiotoxicity Eleventh Information Exchange Meeting on Partitioning and Transmutation Samuel Bays Steven Piet November 2010 This is a preprint of a paper intended for publication in a journal or proceedings. Since changes may be made before publication, this preprint should not be cited or reproduced without permission of the author. This document was prepared as an account of work sponsored by an agency of the United States Government. Neither the United States Government nor any agency thereof, or any of their employees, makes any warranty, expressed or implied, or assumes any legal liability or responsibility for any third party’s use, or the results of such use, of any information, apparatus, product or process disclosed in this report, or represents that its use by such third party would not infringe privately owned rights. The views expressed in this paper are not necessarily those of the United States Government or the sponsoring agency. THE EFFECT OF BURNUP AND SEPARATION EFFICIENCY ON URANIUM UTILIZATION AND RADIOTOXICITY Samuel Bays, Steven Piet Idaho National Laboratory, United States Abstract This paper addresses two fundamental cradle-to-grave issues of fuel cycle sustainability. The two primary issues of interest are efficient use of the natural uranium resource (cradle), and management of nuclear waste radiotoxicity (grave). Both uranium utilization and radiotoxicity are directly influenced by the burnup achieved during irradiation (transmutation related) and where applicable the separation efficiency (partitioning related). Burnup influences the in-growth of transuranics by breeding them into the fuel cycle. -
Nuclear Fuel Cycles Technology Assessment
Clean Power Quadrennial Technology Review 2015 Chapter 4: Advancing Clean Electric Power Technologies Technology Assessments Advanced Plant Technologies Biopower Carbon Dioxide Capture and Storage Clean Power Value-Added Options Carbon Dioxide Capture for Natural Gas and Industrial Applications Carbon Dioxide Capture Technologies Carbon Dioxide Storage Technologies Crosscutting Technologies in Carbon Dioxide Capture and Storage Fast-spectrum Reactors Geothermal Power High Temperature Reactors Hybrid Nuclear-Renewable Energy Systems Hydropower Light Water Reactors Marine and Hydrokinetic Power Nuclear Fuel Cycles Solar Power Stationary Fuel Cells Supercritical Carbon Dioxide Brayton Cycle U.S. DEPARTMENT OF Wind Power ENERGY Clean Power Quadrennial Technology Review 2015 Nuclear Fuel Cycles Chapter 4: Technology Assessments Introduction and Background The Nuclear Fuel Cycle (NFC) is defined as the total set of operations required to produce fission energy and manage the associated nuclear materials. It can have different attributes, including the extension of natural resources, or the minimization of waste disposal requirements. The NFC, as depicted in Figure 4.O.1, is comprised of a set of operations that include the extraction of uranium (U) resources from the earth (and possibly from seawater), uranium enrichment and fuel fabrication, use of the fuel in reactors, interim storage of used nuclear fuel, the optional recycle of the used fuel, and the final disposition of used fuel and waste forms from the recycling processes. Thorium (Th) fuel cycles have been proposed also, but have not been commercially implemented). Figure 4.O.1 Schematic of the uranium based Nuclear Fuel Cycle 1 Quadrennial Technology Review 2015 Clean Power TA 4.O: Nuclear Fuel Cycles The nuclear fuel cycle is often grouped into three classical components (front-end, reactor, and back-end): Front End: The focus of the front end of the nuclear fuel cycle is to deliver fabricated fuel to the reactor. -
The Burnup Dependence of Light Water Reactor Spent Fuel Oxidation
GNA bNLI-I MOL.19980810.0383 PNNL-11 929 Nationail Labolratory Opeate Batelb fornimthe"• The Burnup Dependence of Light Water Reactor Spent Fuel Oxidation B. D. Hanson July 1998 z"D z co Prepared for the U.S. Department of Energy under Contract DE-AC06-76RLO 1830 ' DISCLAIMER This report was prepared as an account of work sponsored by an agency of the United States Government. Neither the United States Government nor any agency thereof, nor Battelle Memorial Institute, nor any of their employees, makes any warranty, express or implied, or assumes any legal liability or responsibility for the accuracy, completeness, or usefulness of any information, apparatus, product, or process disclosed, or represents that its use would not infringe privately owned rights. Reference herein to any specific commercial product, process, or service by trade name, trademark, manufacturer, or otherwise does not necessarily constitute or imply its endorsement, recommendation, or favoring by the United States Government or any agency thereof, or Battelle Memorial Institute. The views and opinions of authors expressed herein do not necessarily state or reflect those of the United States Government or any agency thereof. PACIFIC NORTHWEST NATIONAL LABORATORY operated by BATTEELLE for the UNITED STATES DEPARTMENT OF ENERGY under ContractDE-ACO6-76RLO 1830 Printed in the United States of America Available to DOE and DOE contractors from the Office of Scientific and Technical Information, P.O. Box 62, Oak Ridge, TN 37831; prices available from (615) 576-8401. Available to the public from the National Technical Information Service, U.S. Department of Commerce, 5285 Port Royal Rd., Springfield, VA 22161 This document was printed on recycled paper. -
Nuclear Reactors and Plutonium Production
Nuclear Reactors and Plutonium Production ISIS Course-Week 4 October 23, 2014 Nuclear Reactors • A nuclear reactor is an apparatus or machine in which fissile material can be made to undergo a controlled, self-sustaining nuclear reaction with the consequent release of energy. The Basic Parts of a Reactor http://en.wikipedia.org/wiki/Magnox • Fuel region • Heat removal equipment • Control system • Refueling capability Purposes of Reactors • Nuclear reactors are used for civilian purposes to – generate electricity – produce heat via steam – produce isotopes for medical, industrial, or research purposes – conduct research – propel surface ships, such as ice-breakers • Nuclear reactors are also used for military purposes to – produce plutonium for nuclear weapons – produce tritium for nuclear weapons – propel military submarines and surface ships – power aircraft and rockets (abandoned) Classification of Reactors • Power reactors – typically civilian, almost all now generate electricity. Some produced steam for district heating. Typically make large quantities of reactor-grade plutonium. • Research reactors – typically civilian aimed at making isotopes or conducting research. – In non-proliferation context, ostensibly civilian research reactors have also been used to make plutonium for nuclear weapons, e.g. Cirus and Dhruva reactors in India. The misuse of the Taiwan research reactor was planned. Is the Arak reactor in Iran in this category, ostensibly a civilian research reactor but in reality it would also have produced plutonium for nuclear weapons? • Propulsion reactors – either civilian or military • Production reactors – almost always military and dedicated to plutonium and tritium production for nuclear weapons, which means that the goal is the production of weapon- grade plutonium. Reactors • Reactor types vary greatly, some are far simpler to build than others • Production reactors and research reactors are the simplest to build. -
Fuel Burnup and Enrichment Extension Preparation Strategy
1 APPENDIX A: FUEL BURNUP AND ENRICHMENT EXTENSION 2 PREPARATION STRATEGY 3 4 Based on stakeholder interactions, the NRC staff is aware of industry’s plans to request higher 5 fuel burnup limits along with the deployment of near-term ATF concepts. Additionally, the staff 6 expects that the extension of fuel burnup limits, and the economic drive to achieve those 7 burnups, will result in requests to increase fuel enrichments to greater than the current standard 8 of 5 weight percent U235. Therefore, the staff is proactively assessing the current knowledge 9 and experimental database associated with extending both burnup and enrichment for light 10 water reactor (LWR) fuels. This plan focuses on the strategy to prepare the NRC for review of 11 future licensing actions in which industry requests to go beyond current licensed limits with 12 burnups up to ~75 GWd/MTU rod-average and enrichments up to ~8 weight percent U235. Staff 13 will continue to engage with industry and the fuel vendors on these topics and adjust this 14 strategy as industry plans for higher burnup and increased enrichments evolve. 15 16 Overview of Preparatory Activities 17 18 As with other ATF activities related to advanced cladding and fuel materials, the staff has 19 grouped its burnup and enrichment preparatory activities into four tasks. The highlights of each 20 task are briefly described below; subsequent sections within this appendix describe these tasks 21 in greater detail. 22 23 Task 1: Regulatory Framework: In-Reactor Performance 24 • Participate in coordinated PIRT exercises on in-reactor performance of fuels with 25 increased enrichment under a wide array of conditions, performance -based metrics, and 26 analytical criteria to ensure acceptable performance. -
Burnup Determinaton of Nuclear Fuel
MASS SPECTROSCOPY Original Papers Vol17.No4,December1969 Burnup Determinaton of Nuclear Fuel KIYOSHI I NOUE,*KAORU TANIGUCHI,*TOSHIFUMI MURATA,** HIDEHIKO MITSUI*AND AKIRA DOI* (Received August16,1969) A general description of burnup determining experiments is presented for making vivid a part of mass spectrometry,in comparison of results obtained from radiochemical and nondestructive analyses. Specimen of nuclear fuel was grains of uranium dioxide irradiated in a nuclear reactor for about200 days,and its burnup was found to be8,000MWD/T with sufficient consistency in the experimental results. 1.Introduction method is included in the first approach, Extensive studies on nuclear fuel and the second approach includes radio burnup analysis have been made in the chemical and nondestructive methods. past,since burnup is one of fundamental Both of the radiochemical and nondes quantities required in a fuel research structive methods essentially measure program.Burnup is also an important radioactivities of fission products formed quantity for design and operation of in a nuclear fuel.The former has an ac power reactors from a standpoint of ceptable precision with low cost and safety as well as operability. simple procedure,but the development A wide variety of methods have of a good method for the later remains been developed to determine burnup of an engineering target. irradiated fuel.Principal procedures This paper presents a general de used so far have been based on meas scription on the burnup determining ex ments of: periments for a uranium dioxide fuel (1)Changes in isotopic composition of specimen.Comparing the mass spectro fissioning elements in a nuclear metry method with the other methods, fuel brought about during irradia the contribution it can make to the tion. -
Burnup Credit Criticality Safety Analysis Using STARBUCS
ACTIVITIES OF THE OECD/NEA EXPERT GROUP ON ASSAY DATA FOR SPENT NUCLEAR FUEL I. C. Gauld Oak Ridge National Laboratory P.O. Box 2008 Oak Ridge, TN 37831-6370 USA [email protected] Y. Rugama OECD Nuclear Energy Agency 12, Bd des Iles – 92130 Issy-les-Moulineaux, France Management of spent nuclear fuel is a key issue for many NEA member countries. In nuclear criticality safety, the decision of many countries to advance burnup credit as part of their licensing strategy has heightened recent interest in experimental data needed to validate computer codes used in burnup credit calculations. This paper discusses recent activities of an Expert Group on assay data, formed under the OECD/NEA/NSC/WPNCS (Working Party on Nuclear Criticality Safety) to help coordinate isotopic assay data activities and facilitate international collaboration between NEA member countries developing or implementing burnup credit methodologies. Recent activities of the Expert Group are described, focusing on the planned expansion of the Spent Fuel Isotopic Composition Database (SFCOMPO), and preparation of a state-of-the-art report on assay data that includes sections on recommended radiochemical analysis methods, techniques, and lessons learned from previous experiments. I. INTRODUCTION Management of spent nuclear fuel is a key issue for many Nuclear Energy Agency (NEA) member countries. As interim storage facilities in many countries reach their design capacities, the need to optimize spent fuel storage is becoming an increasingly important issue to managing fuel cycle costs while reducing associated risks. In nuclear criticality safety, the decision by many countries to advance burnup credit as part of their licensing strategy has heightened recent interest in measurement data that are needed to validate computer code calculations for a burnup credit methodology. -
Reactor Fuel Isotopics and Code Validation for Nuclear Applications
ORNL/TM-2014/464 Reactor Fuel Isotopics and Code Validation for Nuclear Applications Matthew W. Francis Charles F. Weber Marco T. Pigni Approved for public release; Ian C. Gauld distribution is unlimited. September 2014 DOCUMENT AVAILABILITY Reports produced after January 1, 1996, are generally available free via US Department of Energy (DOE) SciTech Connect. Website http://www.osti.gov/scitech/ Reports produced before January 1, 1996, may be purchased by members of the public from the following source: National Technical Information Service 5285 Port Royal Road Springfield, VA 22161 Telephone 703-605-6000 (1-800-553-6847) TDD 703-487-4639 Fax 703-605-6900 E-mail [email protected] Website http://www.ntis.gov/help/ordermethods.aspx Reports are available to DOE employees, DOE contractors, Energy Technology Data Exchange representatives, and International Nuclear Information System representatives from the following source: Office of Scientific and Technical Information PO Box 62 Oak Ridge, TN 37831 Telephone 865-576-8401 Fax 865-576-5728 E-mail [email protected] Website http://www.osti.gov/contact.html This report was prepared as an account of work sponsored by an agency of the United States Government. Neither the United States Government nor any agency thereof, nor any of their employees, makes any warranty, express or implied, or assumes any legal liability or responsibility for the accuracy, completeness, or usefulness of any information, apparatus, product, or process disclosed, or represents that its use would not infringe privately owned rights. Reference herein to any specific commercial product, process, or service by trade name, trademark, manufacturer, or otherwise, does not necessarily constitute or imply its endorsement, recommendation, or favoring by the United States Government or any agency thereof. -
Performance Assessment of Spent Fuel Assemblies Removed from Shutdown Rbmk-1000 Power Units for Reburning in Operating Power Units
PERFORMANCE ASSESSMENT OF SPENT FUEL ASSEMBLIES REMOVED FROM SHUTDOWN RBMK-1000 POWER UNITS FOR REBURNING IN OPERATING POWER UNITS B. Kanashov, I. Kuzmin, A. Kostyuchenko, S. Perepelkin, V. Chesanov (Sosny R&D Company) INTRODUCTION The scheduled operating life-time of RBMK-1000 reactor units, that is 30 years, has already expired. Comprehensive analysis of the reactor conditions allowed to extend the operating life-time of RBMK units up to 45 years [1]. The additional time to operate each reactor will depend on its peculiarities, however, we can predict the NPP will shut down its reactors in the order of their commissioning. Table 1. RBMK units decommissioning schedule subject to their extended operating life-time NPP Unit 1 Unit 2 Unit 3 Unit 4 Leningrad 2018 2020 2024 2026 Kursk 2020 2023 2028 2030 Smolensk 2027 2030 2035 – A peculiarity of the RBMK reactors is non-stop core refueling. On the average, one burnt-up fuel assembly (FA) is replaced for a fresh one daily. Sometimes the irradiated assemblies that have not reached the maximum design burnup are reinserted into the core, which already contains the assemblies of different burnups. FA distribution in terms of burnup depends on the duration of the previous period. If the reactor was loaded with the same type fuel with approximately the same speed, the FA burnup distribution in the core does not change. In this case, the refueling is steady-state. Over the period of RBMK reactors operation, the enrichment of fresh fuel has experienced a staged growth. Nowadays, RBMK-1000 units are practically converted to uranium-erbium fuel enriched to 2.8 % in U-235 with erbium content 0.6 %. -
Advances by the Integral Fast Reactor Program De91 011174
I A // / A / ANL/CP--71374 ADVANCES BY THE INTEGRAL FAST REACTOR PROGRAM DE91 011174 M. J. Lineberry, D. R. Pedersen, of the EBR-11 reactor reactor with a uranium alloy metallic L. C. Waiters, and J. E. Cahalan fuel. ll Argonne National Laboratory f 9700 S. Cass Avenue The IFR safety approach for the Integral Fast Reactor (IFR) Argonne, Illinois 60439 concept capitalizes on the characteristics of metallic fuels and of pool-type liquid metal reactors to provide enhanced ABSTRACT safety margins. The fundamental safety approach guiding The advances by the Integral Fast Reactor Program at the IFR program is: Argonne National Laboratory are the subject of this paper. ; 1. A simple, economic, high quality fuel system must The Integral Fast Reactor (IFR) is an advanced liquid- ', be developed which will allow normal operation of metal-cooled reactor concept being developed at Argonne j reprocessed fuel with minimal fuel failures. National Laboratory. The advances stressed in the paper : 2. The metallic fuel system must be tolerant of fuel include fuel irradiation performance, improved passive , failures and local faults. safety, ^nd the development of a prototype fuel cycle ' 3. The reactor design must be such that for any system facility. failure, including those in the balance of plant, no active systems have to operate to maintain the INTRODUCTION reactor in a safe state. The Integral Fast Reactor (IFR) (Ref. 1) is an advanced 4. Even though the reactor can achieve passive shut- liquid-metal-cooled reactor concept being developed at down for any system failure, the reactor should be Axgonne National Laboratory. -
HTR-N Plutonium Cell Burnup Benchmark: Definition, Results & Intercomparison
PHYSOR 2004 -The Physics of Fuel Cycles and Advanced Nuclear Systems: Global Developments Chicago, Illinois, April 25-29, 2004, on CD-ROM, American Nuclear Society, Lagrange Park, IL. (2004) HTR-N Plutonium Cell Burnup Benchmark: Definition, Results & Intercomparison J.C. Kuijper 1, N. Cerullo5, F. Damian2, J.L. Kloosterman4, G. Lomonaco5, J. Oppe1, X. Raepsaet2, H.J. Ruetten3 1NRG, Petten, the Netherlands 2CEA, Saclay, France 3FZJ, Juelich, Germany 4IRI, Delft University of Technology, Delft, the Netherlands 5Universita di Pisa, Pisa, Italy In order to obtain a further validation of several reactor physics code systems to be used for the analysis of High Temperature gas-cooled Reactors (HTR) for plutonium burning applications, a HTR plutonium cell burnup calculational benchmark exercise was defined. For simplicity, the benchmark configuration only consists of a single spherical, 6 cm diameter HTR (“pebble”) fuel element containing coated (PuO2) fuel particles. The requested calculations concerned the tracking of the multiplication factor, nuclide densities in the fuel particles and other relevant parameters during the irradiation of the fuel element at constant power up to the unusually high burnup of 800 MWd/kgHM. Generally a good agreement is found between the results of 3 out of 4 participants, representing 4 out of 5 code systems. The remaining differences in results between the 3 participants can be largely attributed to differences in the modeling of the reaction paths, which are amplified by the unusually high flux levels typical to this particular benchmark. KEYWORDS: HIGH TEMPERATURE GAS-COOLED REACTOR, PLUTONIUM BURNING, HTR-N, EUROPEAN UNION FIFTH FRAMEWORK PROGRAM 1. Introduction In the “HTR-N” and “HTR-N1” projects of the European Fifth Framework Program [1-3] investigations are being made concerning the feasibility of burning plutonium in “High Temperature Gas-Cooled Reactors (HTR)”.