Horizontally Integrated Or Vertically Divided?
Total Page:16
File Type:pdf, Size:1020Kb
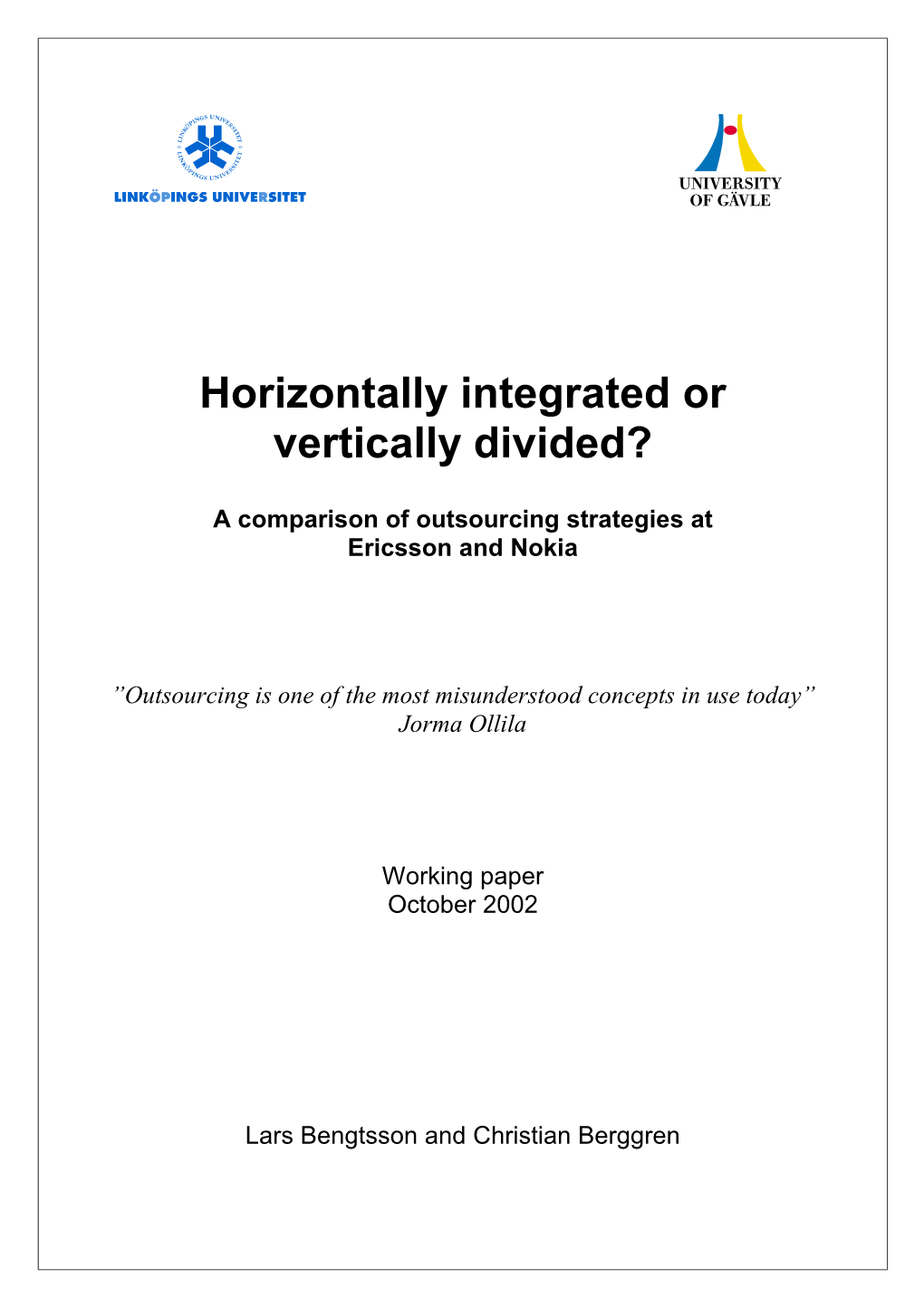
Load more
Recommended publications
-
02-03 Korthet
2 ERICSSON IN BRIEF 1999 - : In November, itu established wcdma as the standard for g mobile systems under the name imt Direct Spread. The decision was welcomed by Erics- son, which can now offer its operator customers all three major versions of this standard. : In terms of number of employees, the takeover of Qualcomm’s infrastructure division was Ericsson’s largest acquisition during , provid- ing Ericsson with a complete product portfolio of second- and third-generation mobile systems. It also accelerated the pace of work in the standardiza- tion area, which was appreciated by the industry as a whole, particularly by the operators. : Ericsson acquired the American companies Torrent and TouchWave and the Danish company Telebit a/s to further strengthen its position in the market for ip and datacom solutions. : In December, Ericsson and Microsoft announced that they would cooperate in the devel- opment and marketing of total solutions for wire- less Internet access. The parties will establish a ERICSSON’S MISSION is jointly owned company to market and supply to understand its mobile e-mail solutions. Ericsson will be the customers’ opportunities majority owner in the new company. and needs, and to provide : During , Ericsson achieved major communication solutions successes with engine, a solution for migrating better than any circuit-switched fixed telecommunications net- competitor. works to a next-generation network that can handle circuit-switched and ip-based, packet-linked traf- IN DOING SO, Ericsson fic. bt in the U.K., kpn in the Netherlands, Telia shall generate a in Denmark and Telefónica in Spain chose engine competitive economic during the year. -
Glossary of Acronyms
Glossary of Acronyms This glossary provides short definitions of a range of abbreviations· and acronyms in use within the cordless telecommunications field; many of the terms are defined in greater detail within this volume. ACCH associated control channel ACELP algebraic code-excited linear prediction, vocoder ACK acknowledgement protocol ACTE Approval Committee for Telecommunication Equipment ACW address code word ADM adaptive delta modulation ADPCM adaptive differential pulse-code modulation AGC automatic gain control AIN advanced intelligent network ALT automatic link transfer AM access manager AMPS American Mobile Phone System - US cellular standard API application programming interface ARA alerting/registration area ARI access rights identifier ARIB Association of Radio Industries and Businesses (Japan) ARQ automatic repeat request ATIS Alliance for Telecommunications Industry Solutions (USA) AWGN additive white Gaussian noise B echo balance return loss B channel user information bearer channel, 64 kb s-l, in ISDN BABT British Approvals Board for Telecommunications BCCH broadcast channel BCT business cordless telephone BER bit error ratio BMC/BMD burst mode controller/device BPSK binary phase shift keying, modulation BRA ISDN basic rate access BS basestation - the fixed radio component of a cordless link, single-channel or multichannel; term also used in cellular radio Glossary of Acronyms 507 BS6833 a standard for digital cordless telephones allowing for proprietary air interfaces (mainly specifying telephony-related aspects) (UK) -
End-Of-Life Treatment of Radio Base Station Transceivers in Europe, Japan and the USA – a Life Cycle Assessment Study
End-of-Life treatment of Radio Base Station transceivers in Europe, Japan and the USA – a Life Cycle Assessment study Anna Grunewald Jessica Gustavsson Stockholm 991210 TRITA-KTH-IM 1999:22 Lith-IKP-ING-EX--99/19--SE Preface This study was initiated by Ericsson Radio Systems AB and carried out as a co-operation between Ericsson Radio Systems AB, Linköping Institute of Technology and the Royal Institute of Technology in Stockholm during the summer and autumn of 1999. First of all, we would like to thank our supervisors during the project, Susanne Lundberg at Ericsson Radio Systems AB, Jörgen Furuhjelm at Linköping Institute of Technology and Lennart Nilson at the Royal Institute of Technology for valuable help and guidance throughout the project. We would also like to express our gratitude to Jens Malmodin, Richard Trankell and Elaine Weidman at Ericsson Radio Systems AB and to Fjalar Kommonen at FFK Ltd for all their help. One of the most difficult tasks in this study was to develop probable logistic scenarios for the take-back of discarded transceivers. We would like to take this opportunity to thank amongst others Rickard Slettmyr and Mattias Sundstedt at Ericsson Radio Systems AB and Mikael Hietarinta at Nippon Ericsson for taking time to help us with this. Finally, we would like to thank our contact persons at the involved recycling companies, who have provided valuable information to the study; Kazuo Suzuki at Total Environmental Recycling Management, Mike Ogle and Darrel Stoecklin at United Recycling Industries Inc., Johan Zwart at MIREC B.V., Lennart Edvinsson at Ragn-Sells Elektronikåtervinning AB, Anders Axelsson and Sune Nordström at AB Arv Andersson, Sören Brännström and Theo Lehner at Boliden AB, Lars Cronquist at Gotthard Aluminium AB and Christer Forsgren at SAKAB. -
News Alert 4 January, 2012
www.pwc.co m/in Sharing insights News Alert 4 January, 2012 No ‘business connection’ constituted in India for sale of GSM systems; payment for embedded software held as not in the nature of ‘royalty’ – Delhi High Court affirms decision of Income-tax Appellate Tribunal (Special Bench) in case of Ericsson AB, Sweden In brief taxable as ‘royalty’, either under the provisions of the Income-tax Act, 1961 (the Act) or under the India-Sweden Double Taxation Avoidance Agreement (the tax In a recent decision, in the case of Ericsson Radio Systems A.B. Sweden 1 (EAB), the treaty). Delhi High Court (HC) has upheld the Income-tax Appellate Tribunal (the Tribunal) Special Bench Ruling in case of Motorola Inc. v. DCIT 2 by holding that Facts EAB did not have a ‘business connection’ in India and that consideration/payment for supply of software (embedded in the telecommunication GSM system) is not • EAB is a company incorporated in Sweden. For the financial years (FYs) 1996- 97 and 1997-98 (relevant years), it was engaged in the business of manufacture 1 DIT v. Ericsson Radio System AB [TS-769-HC-2011 (DEL)] 2 Motorola Inc. v. DCIT [2005] 95 ITD 269 (Del) 1 PwC News Alert January 2012 and sale of telecommunication GSM systems (comprising equipment and • On appeal, the Commissioner of Income-tax (Appeals) (CIT(A)) granted partial software) to various cellular operators the world over, including in India. relief to EAB. Against the order of the CIT (A), the Revenue and EAB preferred an appeal to the Tribunal. These appeals and cross- appeals, along with • During the year under consideration, EAB entered into contracts with various appeals of other tax payers, namely Nokia and Motorola, were referred to the Indian cellular operators (ICOs) for supply of GSM systems. -
Real Time Sampling of Utilization at Ericsson Test Plants
LiU-ITN-TEK-A--10/035--SE Real time sampling of utilization at Ericsson Test Plants Marky Egebäck Sebastian Lindqvist 2010-06-10 Department of Science and Technology Institutionen för teknik och naturvetenskap Linköping University Linköpings Universitet SE-601 74 Norrköping, Sweden 601 74 Norrköping LiU-ITN-TEK-A--10/035--SE Real time sampling of utilization at Ericsson Test Plants Examensarbete utfört i kommunikations- och transportsystem vid Tekniska Högskolan vid Linköpings universitet Marky Egebäck Sebastian Lindqvist Handledare Torbjörn Wikström Examinator Di Yuan Norrköping 2010-06-10 Upphovsrätt Detta dokument hålls tillgängligt på Internet – eller dess framtida ersättare – under en längre tid från publiceringsdatum under förutsättning att inga extra- ordinära omständigheter uppstår. Tillgång till dokumentet innebär tillstånd för var och en att läsa, ladda ner, skriva ut enstaka kopior för enskilt bruk och att använda det oförändrat för ickekommersiell forskning och för undervisning. Överföring av upphovsrätten vid en senare tidpunkt kan inte upphäva detta tillstånd. All annan användning av dokumentet kräver upphovsmannens medgivande. För att garantera äktheten, säkerheten och tillgängligheten finns det lösningar av teknisk och administrativ art. Upphovsmannens ideella rätt innefattar rätt att bli nämnd som upphovsman i den omfattning som god sed kräver vid användning av dokumentet på ovan beskrivna sätt samt skydd mot att dokumentet ändras eller presenteras i sådan form eller i sådant sammanhang som är kränkande för upphovsmannens litterära eller konstnärliga anseende eller egenart. För ytterligare information om Linköping University Electronic Press se förlagets hemsida http://www.ep.liu.se/ Copyright The publishers will keep this document online on the Internet - or its possible replacement - for a considerable time from the date of publication barring exceptional circumstances. -
Corporate Governance and Innovation in Mobile Telecommunications: How Did the Nordic Area Become a World Leader?
STEP rapport / report ISSN 0804-8185 Johan Hauknes and Keith Smith Corporate Governance and R-12 Innovation in Mobile Telecommunications: • How did the Nordic Area 2002 Become a World Leader? Johan Hauknes Keith Smith STEP Group Instittue for New Technologies Hammersborg torg 3 United Nations University N-0179 Oslo, Norway Maastricht, The Netherlands Oslo, March 2003 Hammersborg torg 3, 0179 Oslo, Norway Telephone +47 2286 8010 Fax +47 2286 8049 http://www.step.no/ STEP publiserer to ulike serier av skrifter: Rapporter og Arbeids- notater. Publikasjonene i begge seriene kan lastes ned gratis fra våre internettsider. STEP Rapportserien I denne serien presenterer vi våre viktigste forskningsresultater. Vi offentliggjør her data og analyser som belyser viktige problemstillinger relatert til innovasjon, teknologisk, økonomisk og sosial utvikling, og offentlig politikk. STEP maintains two diverse series of research publications: Reports and Working Papers. Both reports and working papers can be downloaded at no cost from our internet web site. The STEP Report Series In this series we report our main research results. We here issue data and analyses that address research problems related to innovation, technological, economic and social development, and public policy. Redaktører for seriene: Editors for the series: Finn Ørstavik (1998-2000) Per M. Koch (2000) © Stiftelsen STEP 2000 Henvendelser om tillatelse til oversettelse, kopiering eller annen mangfoldiggjøring av hele eller deler av denne publikasjonen skal rettes til: Applications for permission to translate, copy or in other ways reproduce all or parts of this publication should be made to: STEP, Hammersborg torg 3 0179 Oslo, Norway PREFACE This research has been funded by the Key Action on Socio-Economic Research under the IMPROVING Programme of the European Commission under the Fifth Framework Programme. -
Communications Standards Review
COMMUNICATIONS STANDARDS REVIEW Volume 5, Number 1 January, 1994 IN THIS ISSUE The following reports of recent standards meetings represent the view of the reporter and are not official, authorized minutes of the meetings. ITU-T Study Group 8 Telematic Services, November 16 – 25, 1993, Geneva, Switzerland.................................3 ITU T Study Group 8 Roster, November 16 – 25, Geneva, Switzerland...................................................10 TR-30 Data Transmission Systems & Equipment, December 6 – 10, 1993, Orlando, FL...................................11 TR-30.1 Ad Hoc on V.34 Startup.................................................................................................11 TR-30.1, Modems...................................................................................................................12 TR-30.2, Data Transmission......................................................................................................13 TR-30.3 Data Communications Network Interfaces..........................................................................14 TR-30.4, DTE-DCE Protocols....................................................................................................15 TR-30 Partial Roster, December 6 - 10, 1993, Orlando, FL,................................................................18 Documents from IEEE P743 Working Group.........................................................................................19 TR-46 Mobile & Personal Communications 1800 MHz Standards December 6-10, 1993, Orlando, -
5Th Generation Mobile Technology‖ - a New Milestone to Future Wireless Communication Networks
International Journal of Science and Research (IJSR) ISSN (Online): 2319-7064 Index Copernicus Value (2013): 6.14 | Impact Factor (2015): 6.391 ―5th Generation Mobile Technology‖ - A New Milestone to Future Wireless Communication Networks Satya Prakash Rout Department of Electronics and Communication Engineering, TempleCity Institute of Technology and Engineering, Bhubaneswar, Odisha, India Abstract: This paper proposes a brief analysis in the future impact of 5G which has a great technology sense. It is achieved by reducingthe 5G technology to the fundamental core basically considering various scenarios like implication of this technology on mobile operators, changes in the network infrastructures and creating many commercial opportunities. This technology holds a promising growth in the applications which holds high and faster economic growth. 5G has promised to provide huge bandwidth with large coverage area to all the mobile users to play with high data rate differentiated services based on voice, video and data. Keywords: LTE, LTE-Advanced, 4G, QOS, WiMAX 2, High Order- MIMO, NFV, SDN, HetNets, WWAN, AMPS, WLAN 1. Introduction The wireless networks have progressed over the past 35 years to support the rising demand of connected devices, from 1G wireless network to LTE- Advanced wireless network.The cellular system employs a different design approach than most commercial radio broadcasting and television broadcasting use [1,2]. Radio and television systems normallyoperate at maximum power and with the tallest antennas allowed by the regulatory agency of the country. In the mobile communication system, the service area is divided into cells. A transmitter is designed to serve an individual cell. The system seeks to make efficient use of available channels by using low-power transmitters to allow frequency reuse at much smaller distances.The number of times each channel can be reused in a given geographic area Figure 1: Key differences between various generations of is the key to an efficient cellular system design. -
Mobile Telecommunications Sufhfnrt
Mobile Telecommunications Sufhfnrt Granada, Spain November 27-29 1996 Table of Contents European Third Generation Mobile Systems 1 J. S. Dasilva, B. Arroyo, B. Barini, D. Ikonomou, European Commission Preliminary Programme (Invited Papers) Chairmen: B. Fernandes, Chairman ACTS Mobile & Persomal Wireless Domain. J. S. Dasilva, Head of Unit, Mobile Communications European Commission. 1. Mobile Access Technologies - What's Next? 21 R. Steele, Multiple Access Communications, UK. 2. IMT-2000 (FPLMTS) Standardization 25 M. H. Callendar, C. Eng. MIEE, Canada. 3. A perspective of Third Generation Mobile Systems in Japan 26 A. Sasaki. 4. Shaping the wireless vision of Europe. The UMTS Forum 27 E. Candy. Session A1 - Radio interface for high speed trains Chairman: P. Moody, Smith Engineering Ltd., UK. 1. MOSTRAIN System Architecture 28 J. Irvine, University of Strathclyde, UK. J.P. Couvy, Thomson-CSF Communications, France. J. Laurila, Helsinki University of Technology, Finland. G. Mossakowski, De Te Mobil, Germany. P. Robin, Trialog, France. F. Delli Priscoli, University of Rome, Italy. 2. Applying scheduling algorithms to RF resources 35 J. Billion, A. Kung, P. Robin, Trialog, France. 3. Adaptive Nonlinear Equalization of Digital Radio Channels at 360 kbit/s and 2 GHz in the High-Speed-Train Environment 41 E. Bacarelli, R. Cusani, G. Di Blasio, S. Galli, M. Gneo, University of Rome 'La Sapienza', Italy. 4. Performance Potential of an Adaptive Radio Interface for MOSTRAIN 48 A. Arregui, J. Irvine, J. Dunlop, University of Strathclyde, UK. Session A2 - Architecture and signalling Chairman: I. Berberana, Telefonica I+D, Spain. 1. FRAMES BSS Network Architecture 54 R. Haferbeck, D. Ernst, Siemens AG, Germany. -
The Development of Mobile Telephony in Sweden Bengt G
Entrepreneurship in Technological Systems - The Development of Mobile Telephony in Sweden Bengt G Molleryd Akademisk Avhandling Som for avlaggande av filosofie doktorsexamen vid Handelshogskolan i Stockholm framlagges for offentlig granskning Tisdagen den 19 oktober 1999 kl.10.15 i sal Ragnar Handelshogskolan, Sveavagen 65. Entrepreneurship in Technological Systems - The Development of Mobile Telephony in Sweden ~ STOCKHOLM SCHOOL OF ECONOMICS "':,;, EFI, THE ECONOMIC RESEARCH INSTITUTE EPI Mission EFI, the Economic Research Institute at the Stockholm School of Economics, is a scientific institution which works independently ofeconomic, political and sectional interests. It conducts theoretical and empirical research in management and economic sciences, including selected related disciplines. The Institute encourages and assists in the publication and distribution ofits research findings and is also involved in the doctoral education at the Stockholm School of Economics. EFI selects its projects based on the need for theoretical or practical development ofa research domain, on methodological interests, and on the generality ofa problem. Research Organization The research activities are organized in nineteen Research Centers within eight Research Areas. Center Directors are professors at the Stockholm School of Economics. ORGANIZATION AND MANAGEMENT Management and Organisation; (A) Prof Sven-Erik Sjostrand Center for Ethics and Economics; (CEE) Adj Prof Hans de Geer Public Management; (F) Prof Nils Brunsson Information Management; (I) -
Insights from the History of Mobile Phones and Their Application to 5G*
May 2021 To open or not to open a technological system: insights from the history of mobile phones and their application to 5G* Is it a good business strategy for a creator of new technology to make that technology available to other companies in the industry, including its competitors? And if so, on what terms? Further, is it a good business strategy for a developer of new technology to allow third-party companies to develop applications for it? And if so, on what terms? These questions go to the core of what it means for a technological system to be “open” or “closed.” In the history of mobile phones, the first question—whether the creators of new technology are better off allowing other companies in the industry to have access to their intellectual property and, if so, on what terms—has generated controversies since the 1980s, when the Global System for Mobile Communication (GSM) second-generation cellular standard was being developed. Companies that created the technology underlying the GSM standard were reluctant to license their standard-essential intellectual property for free to users of the technology (the cellular carriers). This was especially true of Motorola, which reportedly held about 50% of the GSM standard-essential patents. In an attempt to resolve the problem, the European Telecommunications Standards Institute (ETSI), which was in charge of developing the GSM standard, introduced a policy that set the foundation for the licensing of standard-essential patents under “fair, reasonable, and non-discriminating terms.”1 The true meaning of this (so-called FRAND) terminology has been litigated often since it was introduced. -
Mobile Telephone History TOM FARLEY
Mobile telephone history TOM FARLEY This article describes how mobile telephones, for decades a near dormant technology, became the dynamic and perhaps most important communication tool of our lives. Commercial mobile telephony began in 1946. The cellular radio concept was published in 1947. But only since 1995 have mobiles become low cost, rich in features, and used world wide. We first examine mobile telephony’s early and bulky beginnings. Next, the long journey to analog cellular. Finally, full digital working, exemplified by GSM and now CDMA, providing services and features that make the mobile indispensable and Tom Farley is ubiquitous. We’ll see how early mobile telephony battled the same problems of today: government a freelance regulation, scarce spectrum, and hardware limitations. How Scandinavian, Japanese, and United States telecom writer groups independently crafted their own radio-telephone solutions. At 58, the relatively recent, spectacular success of today’s mobile telephone could hardly be guessed by its age. But its history reveals why this technology took so long to mature. And the present shows us that it was worth the wait. Introduction companies concentrated on providing landline tele- Public mobile telephone history begins in the 1940s phones and services first, but some mobile radio after World War II. Although primitive mobile tele- research and development still went on. Americans phones existed before the War, these were specially lead this low priority movement for three reasons. converted two way radios used by government or The United States was physically intact after the industry, with calls patched manually into the land- war, Bell Telephone Laboratories had a large group line telephone network.