Failure Analysis of Stiffened and Unstiffened Mild Steel Plates
Total Page:16
File Type:pdf, Size:1020Kb
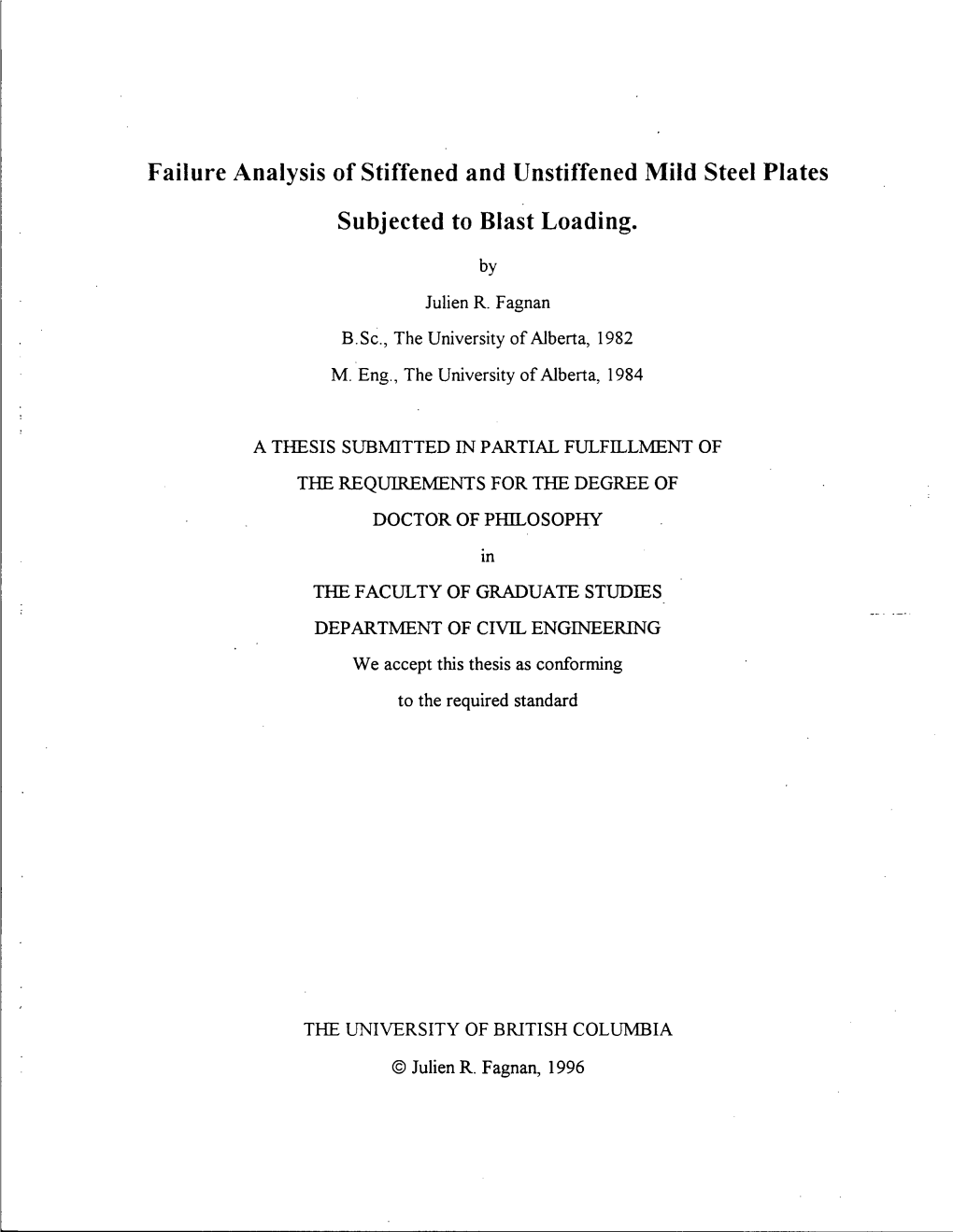
Load more
Recommended publications
-
PLASTICITY Ct 4150 the Plastic Behaviour and the Calculation of Plates Subjected to Bending Prof. Ir. A.C.W.M. Vrouwenvelder
Technical University Delft Faculty of Civil Engineering and Geosciences PLASTICITY Ct 4150 The plastic behaviour and the calculation of plates subjected to bending Prof. ir. A.C.W.M. Vrouwenvelder Prof. ir. J. Witteveen March 2003 Ct 4150 Preface Course CT4150 is a Civil Engineering Masters Course in the field of Structural Plasticity for building types of structures. The course covers both plane frames and plates. Although most students will already be familiar with the basic concepts of plasticity, it has been decided to start the lecture notes on frames from the very beginning. Use has been made of rather dated but still valuable course material by Prof. J. Stark and Prof, J. Witteveen. After the first introductory sections the notes go into more advanced topics like the proof of the upper and lower bound theorems, the normality rule and rotation capacity requirements. The last chapters are devoted to the effects of normal forces and shear forces on the load carrying capacity, both for steel and for reinforced concrete frames. The concrete shear section is primarily based on the work by Prof. P. Nielsen from Lyngby and his co-workers. The lecture notes on plate structures are mainly devoted to the yield line theory for reinforced concrete slabs on the basis of the approach by K. W. Johansen. Additionally also consideration is given to general upper and lower bound solutions, both for steel and concrete, and the role plasticity may play in practical design. From the theoretical point of view there is ample attention for the correctness and limitations of yield line theory for reinforced concrete plates on the one side and von Mises and Tresca type of materials on the other side. -
A New Strategy for Treating Frictional Contact in S Heii Structures
A New Strategy for Treating Frictional Contact in Sheii Structures using Variational Inequalities Nagi El-Abbasi A thesis submitted in confomiity with the requirements for the degree of Doctor of Philosophy Graduate Department of Mechanical and Industrial Engineering University of Toronto 0 Copyright by Nagi El-Abbasi 1999 National Library Bibliotheque nationale du Canada Acquisitions and Acquisitions et Bbliographic Services services bibliographiques 395 WeUington Street 395, nie Wellington OttawaON K1AON4 OttawaON K1A ON4 Canada canada The author has granted a non- L'auteur a accordé une licence non exclusive licence dowing the exclusive permettant à la National Library of Canada to Bibliothèque nationale du Canada de reproduce, loan, distribute or seil reproduire, prêter, distribuer ou copies of this thesis in microform, vendre des copies de cette thèse sous paper or electronic formats. la forme de microfiche/fiim, de reproduction sur papier ou sur format électronique. The author retains ownership of the L'auteur conserve la propriété du copyright in this thesis. Neither the droit d'auteur qui protège cette thèse. thesis nor substantial extracts fiom it Ni la thèse ni des extraits substantiels may be printed or otherwise de celleci ne doivent être imprimés reproduced without the author's ou autrement reproduits sans son permission. autorisation. A New Strategy for Treating Frictional Contact in Shell Structures using Variational Inequalities Nagi Hosni El-Abbasi, Ph.D., 1999 Graduate Department of Mechanical and Industrial Engineering University of Toronto Abstract Contact plays a fundamental role in the deformation behaviour of shell structures. Despite their importance, however, contact effects are usually ignored andor oversimplified in finite element modelling. -
On Generalized Cosserat-Type Theories of Plates and Shells: a Short Review and Bibliography Johannes Altenbach, Holm Altenbach, Victor Eremeyev
On generalized Cosserat-type theories of plates and shells: a short review and bibliography Johannes Altenbach, Holm Altenbach, Victor Eremeyev To cite this version: Johannes Altenbach, Holm Altenbach, Victor Eremeyev. On generalized Cosserat-type theories of plates and shells: a short review and bibliography. Archive of Applied Mechanics, Springer Verlag, 2010, 80 (1), pp.73-92. hal-00827365 HAL Id: hal-00827365 https://hal.archives-ouvertes.fr/hal-00827365 Submitted on 29 May 2013 HAL is a multi-disciplinary open access L’archive ouverte pluridisciplinaire HAL, est archive for the deposit and dissemination of sci- destinée au dépôt et à la diffusion de documents entific research documents, whether they are pub- scientifiques de niveau recherche, publiés ou non, lished or not. The documents may come from émanant des établissements d’enseignement et de teaching and research institutions in France or recherche français ou étrangers, des laboratoires abroad, or from public or private research centers. publics ou privés. 74 J. Altenbach et al. and rotations (and by analogy of forces and couples or force and moment stresses) is stated, see, e.g., [307]. Historically the first scientist, who obtained similar results, was L. Euler. Discussing one of Langrange’s papers he established that the foundations of Mechanics are based on two principles: the principle of momentum and the principle of moment of momentum. Both principles results in the Eulerian laws of motion [307]. In [214] is given the following comment: the independence of the principle of moment of momentum, which is a generalization of the static equilibrium of the moments, was established by Jacob Bernoulli (1686) one year before Newton’s laws (1687). -
Challenge Problem 2 - the Solution
Challenge Problem 2 - The Solution A building has a floor opening that has been The Challenge covered by a durbar plate with a yield stress of As an experienced engineer you realise that under increasing load the 275MPa. The owner has been instructed by his plate will eventually reach first yield after which the stress will insurers that for safety the load carrying capacity redistribute until the final collapse load is reached. You will appreciate of the plate needs to be assessed. The owner has that the steel will have some work hardening capability and that if calculated (possibly unrealistically but certainly transverse displacements are considered then some membrane action conservatively) that if 120 people each weighing will occur. However, opting for simplicity and realising that ignoring 100kg squeeze onto the plate then it must be able these two strength enhancing phenomena will lead to a degree of to cope with 100kN/m 2. He has found, in the Steel conservatism in your assessment, you decide that this is a limit analysis Designers’ Manual, that the plate should be able problem in which the flexural strength of the plate governs collapse. to withstand 103kN/m 2. This is rather close to the required load and looking in Roark’s Formulas for Unless you have specialist limit analysis software you will decide to Stress and Strain he finds that the collapse load is tackle this as an incremental non-linear plastic problem with a bi- more like 211kN/m 2 which he feels does provide linear stress/strain curve and a von Mises yield criterion. -
Ritz Variational Method for Bending of Rectangular Kirchhoff Plate Under Transverse Hydrostatic Load Distribution
Mathematical Modelling of Engineering Problems Vol. 5, No. 1, March, 2018, pp. 1-10 Journal homepage:http://iieta.org/Journals/MMEP Ritz variational method for bending of rectangular kirchhoff plate under transverse hydrostatic load distribution Clifford U. Nwoji1, Hyginus N. Onah1, Benjamin O. Mama1, Charles C. Ike2* 1 Dept of Civil Engineering,University of Nigeria, Nsukka, Enugu State, Nigeria 2Dept of Civil Engineering,Enugu State University of Science & Technology, Enugu State, Nigeria Corresponding Author Email: [email protected] https://doi.org/10.18280/mmep.050101 ABSTRACT Received: 12 Feburary 2018 In this study, the Ritz variational method was used to analyze and solve the bending Accepted: 15 March 2018 problem of simply supported rectangular Kirchhoff plate subject to transverse hydrostatic load distribution over the entire plate domain. The deflection function was chosen based Keywords: on double series of infinite terms as coordinate function that satisfy the geometric and Ritz variational method, Kirchhoff force boundary conditions and unknown generalized displacement parameters. Upon substitution into the total potential energy functional for homogeneous, isotropic plate, hydrostatic load distribution Kirchhoff plates, and evaluation of the integrals, the total potential energy functional was obtained in terms of the unknown generalized displacement parameters. The principle of minimization of the total potential energy was then applied to determine the unknown displacement parameters. Moment curvature relations were used to find the bending moments. It was found that the deflection functions and the bending moment functions obtained for the plate domain, and the values at the plate center were exactly identical as the solutions obtained by Timoshenko and Woinowsky-Krieger using the Navier series method. -
Analysis of Chromatographic Theories and Thermodynamics Calculation Procedure
International Conference on Nanotechnology and Chemical Engineering (ICNCS'2012) December 21-22, 2012 Bangkok (Thailand) Analysis of Chromatographic Theories and Thermodynamics Calculation Procedure Edison Muzenda developed a theory based on packed column distillation for Abstract—This paper presents the development of liquid –liquid chromatography. Equilibration of solute between chromatography, two mathematical methods for describing the mobile and stationary phases in each plate was assumed to chromatographic phenomena, band broadening processes as well as be complete. Plate to plate diffusion was considered to be the procedure for retention volume measurement and calculation. The negligible and the ratio of solute concentration in the phases plate and the rate theories for gas chromatographic phenomena are comprehensively discussed. The reduction of infinite dilution activity (partition coefficient) was taken to be constant irrespective of coefficients from retention data is explained. While the rate theory the amount of solute present (linear isotherm). Reference [4] can predict the influence of various factors on column performance, offered a promising improvement to Wilson’s earlier treatment the plate theory is more useful in the calculation of thermodynamic by correcting several of the physical impossibilities, which properties such as infinite dilution activity coefficients, enthalpy and developed from the theory. De Vault’s [4] treatment was entropy of mixtures. superior to that of Martin and Synge [3] in that it was based on the continuous distribution of the solute between the stationary Keywords—Band broadening, chromatographic phenomena, column performance, plate theory, retention volume, thermodynamic and mobile phases along the length of the column. Thus properties avoiding the hypothetical discontinuity of the plate model and this treatment was later confirmed by [5]. -
A Four-Node Plate Bending Element Based on Mindlin/Reissner Plate Theory and a Mixed Interpolation
INTERNATIONAL JOURNAL FOR NUMERICAL METHODS IN ENGINEERING, VOL. 21, 367-383 (1985) SHORT COMMUNICATION A FOUR-NODE PLATE BENDING ELEMENT BASED ON MINDLIN/REISSNER PLATE THEORY AND A MIXED INTERPOLATION KLAUS-JURCEN BATHEt AND EDUARDO N. DVORKINt Massachusetts Institute of Technology, Cambridge, Massachusetts, U.S.A. SUMMARY This communication discusses a 4-node plate bending element for linear elastic analysis which is obtained, as a special case, from a general nonlinear continuum mechanics based 4-node shell element formulation. The formulation of the plate element is presented and the results of various example solutions are given that yield insight into the predictive capability of the plate (and shell) element. INTRODUCTION Since the development of the first plate bending finite elements, a very large number of elements has been These elements are usually developed and evaluated for the linear analysis of plates, but it is frequently implied that the elements can ‘easily’ be extended to the geometrically nonlinear analysis of general shell structures. Our experiences are different. We believe that it can be a major step to extend a linear plate bending element formulation to obtain a general effective shell element, and with some plate element formulations this extension is (almost) not possible. Therefore, to obtain a general 4-node nonlinear shell element, we have concentrated directly on the development of such an element. As a special case, the shell element will then reduce to a plate bending element for the linear elastic analysis of plates. Some results of our efforts to develop a general 4-node shell element were presented earlier.4 Our objective in this communication is to show how the general continuum mechanics based shell element formulation of Reference 4 reduces to an attractive plate bending analysis capability, and to give some more insight into our shell element formulation. -
6.1 Plate Theory
Section 6.1 6.1 Plate Theory 6.1.1 Plates A plate is a flat structural element for which the thickness is small compared with the surface dimensions. The thickness is usually constant but may be variable and is measured normal to the middle surface of the plate, Fig. 6.1.1 lateral load middle surface of plate Fig. 6.1.1: A plate 6.1.2 Plate Theory Plates subjected only to in-plane loading can be solved using two-dimensional plane stress theory1 (see Book I, §3.5). On the other hand, plate theory is concerned mainly with lateral loading. One of the differences between plane stress and plate theory is that in the plate theory the stress components are allowed to vary through the thickness of the plate, so that there can be bending moments, Fig. 6.1.2. M Fig. 6.1.2: Stress distribution through the thickness of a plate and resultant bending moment Plate Theory and Beam Theory Plate theory is an approximate theory; assumptions are made and the general three dimensional equations of elasticity are reduced. It is very like the beam theory (see Book 1 although if the in-plane loads are compressive and sufficiently large, they can buckle (see §6.7) Solid Mechanics Part II 120 Kelly Section 6.1 I, §7.4) – only with an extra dimension. It turns out to be an accurate theory provided the plate is relatively thin (as in the beam theory) but also that the deflections are small relative to the thickness. This last point will be discussed further in §6.10. -
Higher Order Shear Deformation Plate Theory
View metadata, citation and similar papers at core.ac.uk brought to you by CORE provided by NORA - Norwegian Open Research Archives Higher Order Shear Deformation Plate Theory by Gjermund Mæsel Kolvik THESIS for the degree of MASTER OF SCIENCE (Master i Anvendt matematikk og mekanikk) Faculty of Mathematics and Natural Sciences University of Oslo May 2012 Det matematisk- naturvitenskapelige fakultet Universitetet i Oslo Preface This thesis has been written to fulll the degree of Master of Science at the University of Oslo, Department of Mathematics, Mechanics Division. Professors Noël Challamel and Jostein Hellesland at the University of Oslo have been my supervisors during this project. Professor Challamel's expertise on higher order theories has been of immense help. I would like to thank him for his motivating enthusiasm and welcoming presence. I feel fortunate to have made his acquaintance during his year at the University of Oslo. I would like to express my gratitude to professor Jostein Hellesland for his excellent guidance and advice throughout the project. His vast knowledge in solid mechanics and encouraging support is highly appreciated. i Abstract Several plate theories have been developed to describe the static and dynamic behaviour of plates. This thesis is predominantly a study of plate theories in- cluding shear eects, with emphasis on higher order shear deformation theories. The plate theories of Reddy and Shi are specically analysed. An eort to- wards the development of a unied higher order shear deformation plate theory is presented in this thesis. The buckling behaviour of some generic higher order shear plate models is inves- tigated in a unied framework. -
Stress Gradient Failure Theory for Textile Structural Composites
STRESS GRADIENT FAILURE THEORY FOR TEXTILE STRUCTURAL COMPOSITES By RYAN KARKKAINEN A DISSERTATION PRESENTED TO THE GRADUATE SCHOOL OF THE UNIVERSITY OF FLORIDA IN PARTIAL FULFILLMENT OF THE REQUIREMENTS FOR THE DEGREE OF DOCTOR OF PHILOSOPHY UNIVERSITY OF FLORIDA 2006 Copyright 2006 by Ryan Karkkainen This document is dedicated to everyone curious enough to ask the questions, persistent enough to find the answers, and honest enough to respect the truth always. ACKNOWLEDGMENTS I offer my sincere thanks to my committee and colleagues for their kind and invaluable assistance. Further thanks are due to the Army Research Office and Army Research Laboratory for their gracious funding of this project, and for their feedback and assistance. iv TABLE OF CONTENTS page ACKNOWLEDGMENTS ................................................................................................. iv LIST OF TABLES............................................................................................................ vii LIST OF FIGURES ........................................................................................................... ix ABSTRACT....................................................................................................................... xi CHAPTER 1 INTRODUCTION ........................................................................................................1 2 APPROACH...............................................................................................................10 Finite Element Micromechanical Method -
Prediction of Faulting from the Theories of Elasticity and Plasticity: What Are the Limits? (1998) Journal of Structural Geology, 20 (2-3)
OATAO is an open access repository that collects the work of Toulouse researchers and makes it freely available over the web where possible This is an author’s version published in: http://oatao.univ-toulouse.fr/27377 Official URL: https://doi.org/10.1016/S0191-8141(97)00089-8 To cite this version: Gerbault, Muriel and Poliakov, Alexei N.B. and Daignieres, Marc Prediction of faulting from the theories of elasticity and plasticity: what are the limits? (1998) Journal of Structural Geology, 20 (2-3). 301-320. ISSN 01918141 Any correspondence concerning this service should be sent to the repository administrator: [email protected] 0191-8141/98 $19.00+o.oo Prediction of faulting from the theories of elasticity and plasticity: what are the limits? MURIEL GERBAULT, ALEXEI N.B. POLIAKOV and MARC DAIGNIERES Laboratoire de Géophysique et Tectonique (U.M.R. 5573), CNRS-Université Montpellier Il, 34095 Montpellier 05, France Abstract-Elasticity, rigid-plasticity and elasto-plasticity are the simplest constitutive models used to describe the initiation and evolution offaulting. However, in practice, the limits of their application are not always clear. In this paper, we test the behaviour of these different models using as examples tectonic problems of indentation of a die, compression with basal shear, bending of a plate and normal faulting around a dike. By comparing the results of these tests, we formulate some guidelines that may be useful for the selection of an appropria te constitutive mode! of faulting. The theory of elasticity reasonably predicts the initiation of the fault pattern but gives erroneous results for large strains. -
Lecture 3 Plate Bending
Topics in Ship Structural Design (Hull Buckling and Ultimate Strength) Lecture 3 Plate Bending Reference : Ship Structural Design Ch.09 NAOE Jang, Beom Seon OPen INteractive Structural Lab 9.1 Small Deflection Theory "Long" Plates(Cylindrical Bending) . An equation relating the deflections to the loading can be developed as for the beam. Saddle shape . Cylindrical Bending: A plate which is bent about one axis only(a>>b) Transverse deformation does not occur, since such a deformation would required a saddle shape deformation. y x y = x y x EE E εy -εx y x y x y 0 ε E E x -εy (1-2 ) = x x E E = =E x1- 2 x x Plate in cylindrical bending 2 OPen INteractive Structural Lab Reference Poisson Ratio trans axial Strain Δεy induced by εy y x y E 1 ( ) x E x y z 1 ( ) y E y z x 1 ( ) z E z x y OPen INteractive Structural Lab 9.1 Small Deflection Theory Formulas between a beam and a long plate . E΄ : effective modulus of elastictiy, always > E. E E (1 2 ) → A plate is always “stiffer” than a row of beams . For a long prismatically loaded plate, the extra stiffness may be fully taken into account for by using E΄ in place of E. For simply supported plates: 5pb4 5 pb 4 (1- 2 ) == max 384E I 32 Et 3 . For clamped plates: pb4 pb 4(1- 2 ) == max 384E I 32 Et3 4 OPen INteractive Structural Lab 9.1 Small Deflection Theory Formulas between a beam and a long plate .