Renault F1 Team (Composite Diffuser) Case Study
Total Page:16
File Type:pdf, Size:1020Kb
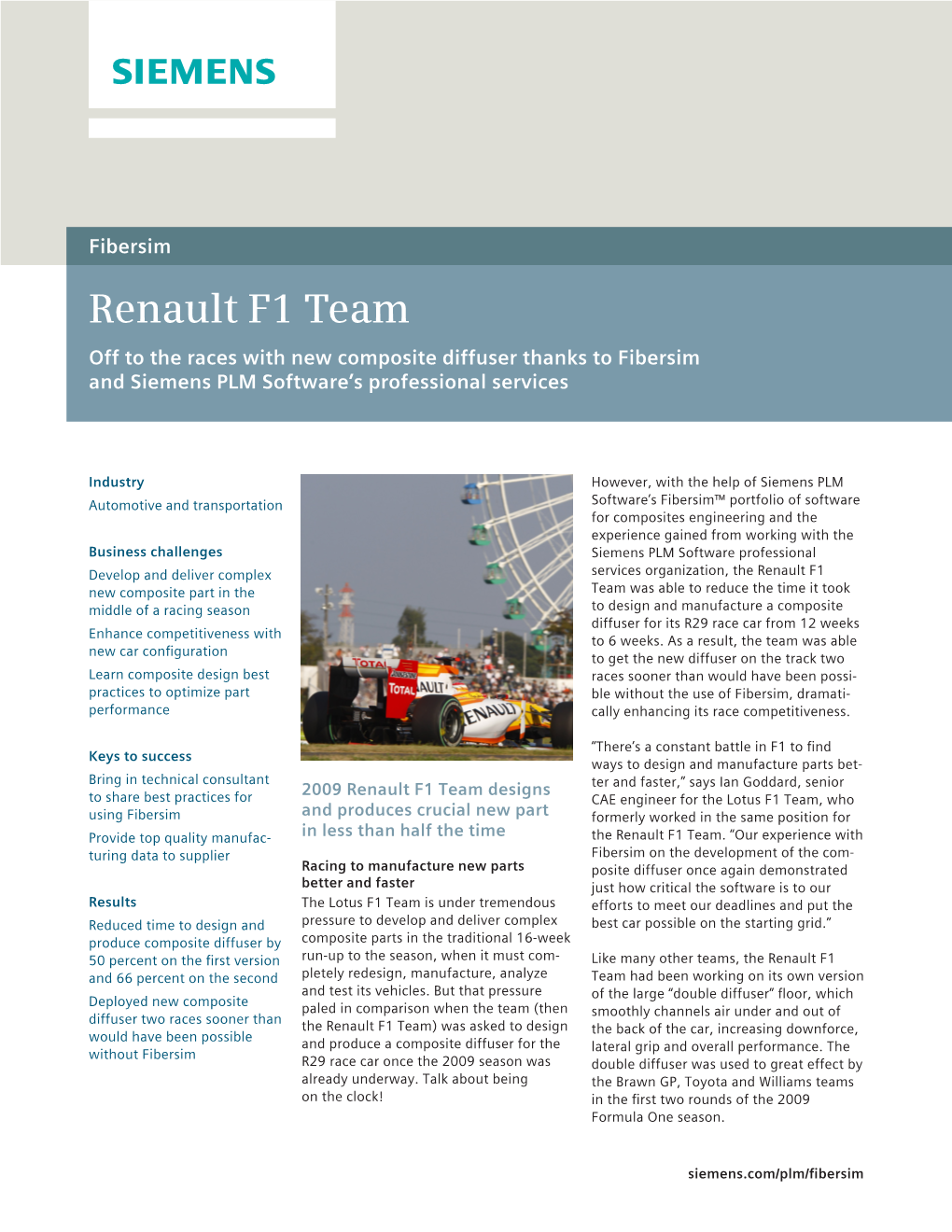
Load more
Recommended publications
-
Davide Signed with Alpine F1 Team in January 2021 As
ALPINE F1 TEAM PRESS PACK Already recognised for its records It is part of Groupe Renault’s Luca De Meo, CEO Groupe That’s the beauty of racing as In September 2020, Luca De Meo, and successes in endurance strategy to clearly position Renault: “It is a true joy to see a works team in Formula 1. announced the creation of Alpine F1 Team, and rallying, the Alpine name each of its brands. For Alpine, the powerful, vibrant Alpine We will compete against the naturally finds its place in the this is a key step to accelerate name on a Formula One car. biggest names, for spectacular a renaissance of Groupe Renault’s F1 team, high standards, prestige and the development and influence New colours, new managing car races made and followed one of F1’s most historic and successful. performance of Formula 1. The of the brand. Renault remains team, ambitious plans: it’s a new by cheering enthusiasts. I can’t Alpine brand, a symbol of sporting an integral part of the team, beginning, building on a 40-year wait for the season to start.” prowess, elegance and agility, with the hybrid power unit history. We’ll combine Alpine’s will be designated to the chassis retaining its Renault E-Tech values of authenticity, elegance and pay tribute to the expertise moniker and unique expertise and audacity with our in-house that gave birth to the A110. in hybrid powertrains. engineering & chassis expertise. ALPINE F1 TEAM | PRESS PACK | 2021 Alpine Today and Tomorrow As part of Groupe Renault’s strategic plan ‘Renaulution’, Alpine unveiled its long-term plans to position the brand at the forefront of Groupe Renault’s innovation. -
Renault Motorsport Strategy
Press Kit 2016 RENAULT MOTORSPORT STRATEGY Contents 01 Introduction 03 02 Renault Sport Racing 07 Q&A with Cyril Abiteboul 08 Q&A with Guillaume Boisseau 10 Q&A with Frédéric Vasseur 11 Q&A With Bob Bell 12 Q&A with Nick Chester 13 Q&A with Rémi Taffin 14 Renault R.S.16 Technical Specification 16 Renault R.E.16 Technical Specification 17 03 Jolyon Palmer 18 Kevin Magnussen 20 Esteban Ocon 22 04 Renault Sport Academy 24 Oliver Rowland 25 Jack Aitken 27 Louis Delétraz 28 Kevin Joerg 29 05 Renault Sport Formula One Team within the Renault-Nissan Alliance 30 Renault Sport Formula One Team Partners 31 06 Renault: 115 Years of Motorsport Success 34 Renault Motorsport Activities 40 Renault Sport Cars 42 Technology Transfer 45 Renault Press [email protected] www.renaultsport.com 2 Press Kit 3 February 2016 01 Introduction The forging of Renault Sport Racing and Renault Sport Cars is the next chapter in an already compelling story. For more than 115 years Renault has embraced the challenge of motorsport in multiple guises. It recognised the value of competitive activities for technical and commercial gain: in December 1898 Louis Renault drove the Type A Voiturette up the steepest street in Paris, the rue Lepic. The first orders for the ground-breaking car with direct drive flooded in. In 1902 the nimble, lightweight Type K, fitted with Renault’s first 4-cylinder engine, took victory in the Paris-Vienna rally. Again, many more cars were sold. Going through the years, in 1977 Renault introduced the first-ever turbocharged car to F1. -
Romain Grosjean
1 2015 LOTUS F1 TEAM PRESS PACK 2015 LOTUS F1 TEAM PRESS PACK 2 CONTENTS 3 Lean Mix: Matthew Carter CEO Q&A 18 Lotus F1 Team History in Numbers 4 Opportunity Knocks: Federico Gastaldi Q&A 19 The Socialites: Social Media Communications 5 Fighting Back: Romain Grosjean Q&A and CV 20 Partner Features 7 Bouncing Back: Pastor Maldonado Q&A and CV 23 Information on Official Team Partners 9 Man Friday: Jolyon Palmer Q&A and CV 26 Information on Official Technical Partners 12 Stepping Forward: Nick Chester Technical Director Q&A 29 Contact Details 14 E23 Technical Specification 15 Power Unit Specifications 17 Lotus F1 Team Statistics 2015 LOTUS F1 TEAM PRESS PACK 3 Lotus F1 Team’s CEO, Matthew Carter, looks at the challenges for the season ahead. MATTHEW MATTHEWCARTER How would you describe the 2015 benefit from 12 months of hard work; we are How big a change is it operationally What is possible from the year ahead? specification Lotus F1 Team? ready to return to our rightful place at the working with a new Power Unit partner Certainly far better race results than we saw CARTERLean and hungry to return to the kind of pinnacle of the sport. like Mercedes AMG High Performance last year! We expect to be back to regularly successes we’ve enjoyed in the past. We’ll Powertrains? points scoring and we’re fighting to get back get last year out of the way quickly; for What are the main challenges facing the It’s a significant change and one we believe to being on the podium. -
Eric Boullier Joins Renault F1 Team As Team Principal
Eric Boullier joins Renault F1 Team as Team Principal The Renault F1 Team is delighted to announce the appointment of Eric Boullier as Team Principal with immediate effect. With an engineering background, Eric Boullier joins Renault with a wealth of motorsport experience. Having started as a race engineer ten years ago, he moved into management with Team DAMS as Managing Director in 2003 and oversaw their racing operations in various categories including the GP2 Series. The 36-year-old Frenchman also acted as Team Principal for Team France in the A1GP Series between 2007 and 2009. Speaking at the announcement, Eric Boullier commented: “I am incredibly proud to be joining the Renault F1 Team as Team Principal. Renault is one of the most famous and successful names in motorsport and I look forward to leading the team into the new season. In the past Renault has demonstrated that it is one of the top teams in Formula One and I am sure that with hard work and determination we can challenge at the front once again.” A selection of photos of Eric Boullier are available for download from our media website: http://renault.latphoto.co.uk/ Eric Boullier key dates: 2009 : Gravity Sport Management, CEO 2003-09 : Team DAMS, Managing and Technical Director (GP2 Series, GP2 Asia, FRV6, Formula BMW Europe, Formula Le Mans). Winning Team in GP2 Asia, FRV6 and Formula Le Mans. 2007-09 : A1 Team France, Team Principal. Winning Team in 2007-08. 2002 : Racing Engineering, Chief Engineer (World Series by Renault) Winning Team in 2002 1999-2001 : Team DAMS, Race Engineer (F3000, official team Cadillac 24H du Mans) 1999 : IPSA (Institut Polytechnique des Sciences Avancées), diploma. -
Money Transfers and Currency Exchange
200fils www .dt.bh Tuesda y, August 25, 2015 Issue No. 675 3 Sierra Leone’s last known Ebola patient leaves hospital Sierra Leone’s last known Ebola patient was released from hospital Monday, rais www.dt.bh ing hopes the west African nation may finally have beaten the devastating epi- demic Twitter : - Will reaching#PollToday on an agreement Leek is a rich source of vitamins be the first step to solve the C and A which are important for Joint panel seeks govt@DTribune nod to postpone redirecting subsidy maintaining healthy skin. ongoing tensions between North and South Korea? SEE P A Hub to Everything Page 12 AGES 11-13 11 Tuesday, August 25, 2015 App of the week SAMSUNG UNVEILS the Phenomenal duo BRING YOUR PICS TO LIFE! This was bound to happen yet having to experience an app that has We got rid of some developed a portfolio of advanced computer vision technologies is still hard-worn crutches of a mind-blowing experience. Seene lets the mobile industry, you turn your mobile into a basic 3D and developed a scanner, creating pictures that appear device that actively come to life as they move in front of addressed some your eyes when you rotate the phone. With the invention of bringing static major pain points for moments into movements, the need consumers. Yes to record videos all the time becomes unnecessary; just flip through the –Hayssam Yassine, pictures to see them in action. Free for Head of the IM DivisionLiam at iPad and iPhone. Samsung Gulf ElectrFarrellonics Gizmo of the week martphone enthusiasts, major pain points for consumers,” particularly those who have always said Hayssam Yassine, Head of heldS a strong favoring to the Samsung the IM Division at Samsung Gulf family can rejoice for last week, not Electronics. -
Diari De La F1
DIARI DE LA F1: -1/11: S ACABA LA TEMPORADA 2009 AMB EL GP D ABU DHABI. -2/11: BRIDGESTONE anuncia que deixarà la F1 al final del 2010. -2/11: WILLIAMS confirma BARRICHELLO i HULKENBERG com a pilots pel 2010. -3/11: RED BULL anuncia que seguirà portant motors RENAULT. -4/11: TOYOTA fa públic que deixa la F1. -10/11: CAMPOS META presenta BRUNO SENNA com a pilot. -11/11: ROBERTSON, mànager de Raikkonen, visita la seu de McLaren. -11/11: Marc GENE fa una exhibició amb el Ferrari F1 pels carrers de València. -13/11: Luca COLAJANNI visita TV3. -13/11: BUTTON visita la seu de McLaren a Woking. -14/11: KUBICA estavella un Clio R3 contra una paret al ral.li de Sicília. -15/11: ALONSO apareix a les Ferrari Finals a Xest al costat de Massa i Montezzemolo. -16/11: MERCEDES compra el 75 1% de BRAWN GP, que es dirà MERCEDES GP. -16/11: McLAREN comprarà el 40% de les accions que Mercedes té de l equip de F1 a finals del 2010, i s assegura els motors Mercedes fins el 2015. -17/11: MANOR anuncia el fitxatge de TIMO GLOCK. -18/11: McLAREN anuncia el fitxatge de JENSON BUTTON, i RAIKKONEN diu que s agafa un any sabàtic a la F1 per centrar-se el 2010 en el WRC. -19/11: Jarno TRULLI i Mika SALO fan dues jornades de tests a la NASCAR a un circuit de Florida (EUA). -20/11: Es disparen els rumors que situen SCHUMACHER a Mercedes GP en el lloc de Button. -
Proactive the Official E-Magazine of Lotus Engineering
proActive The official e-magazine of Lotus Engineering ISSUE 39 | WINTER 2010 PARIS 2010 – A NEW ERA BEGINS THE LOTUS INTERVIEW: LOTUS DIRECTOR OF DESIGN DONATO COCO COMPOSITE DEVELOPMENTS IN MAINSTREAM BODY STRUCTURES FUEL EFFICIENCY IMPROVEMENTS USING VARIABLE VALVE ACTUATION CONNECTING MAN AND MACHINE – THE HMI SYSTEM FOR THE LOTUS CITY CAR 1 proActive CONTENTS WELCOME INDUSTRY NEWS 03-06 > JUST-AUTO EDITOR DAVE LEGGETT REVIEWS SOME OF THE I do not believe I am in creating the new cars that QUARTER’S LAST NEWS HIGHLIGHTS exaggerating when I say that will embody our brand DNA and Lotus took the recent Paris demonstrate our excellence LOTUS NEWS motor show by storm. Unveiling in lightweight architectures, NEW ENGINE RESEARCH PROJECT GETS FUNDING BOOST FROM 07-11 > a full range of five new cars, efficient performance, electrical THE TECHNOLOGY STRATEGY BOARD by any OEM’s standards, is and electronic engineering and driving dynamics. However we NEW LOW CARBON VEHICLE PROGRAMME TO DELIVER A unprecedented. It was a clear are proud that our work for REEVOLUTION IN PERFORMANCE OF PREMIUM ELECTRIC CARS statement of our intentions as third-party clients has increased NEW ADDITIONS TO THE LOTUS LINE-UP we reinvent the Lotus brand. in each of the last four years LOTUS ENGINEERING BRINGS GREEN TECHNOLOGY TO IBM Although the world may only and we are resolute in that trend AUDITORIUM recently have seen our exciting continuing - it is a key part of our GROUP LOTUS + RENAULT + GENII = LOTUS RENAULT GP future, it is not new to us. Our five-year plan. We are committed five-year plan was in place some to helping our existing clients time ago and we are racing down with our technologies and PARIS 2010 – A NEW ERA BEGINS 12-15 > the road to deliver it. -
Renault Sport Racing Press Pack 2020
FOREWORD This year, Renault will continue its very proud and long-standing history in Formula 1 into a new decade, our sixth consecutive in the sport. We are in the midst of an interesting period, as we continue to engage within established global markets, while simultaneously developing our brand and its awareness in bigger areas like China and India within the widespread transformation of the automotive industry. Our commitment to Formula 1 has led to inventive marketing initiatives to increase awareness of, and commitment to, our brand. I look forward in particular to supporting new activations from Groupe Renault and its markets around E-Tech technology, which has been inspired by long-standing Formula 1 innovation. Our presence in the sport is also a unique opportunity for the team’s partners and sponsors to build relationships with one of the most important car manufacturers in the world, and for Renault to benefit from their know-how in their respective fields. 2020 is also an important transition year for the team. We aim to recapture the positive momentum from our first three years since returning to Formula 1 while preparing for next season, which will represent a new cycle for all teams. Having completed our initial construction phase, we are more determined than ever to be ready to attack and take advantage of the 2021 technical changes. 2020 is also the last year under the current agreements that govern Formula 1’s commercial rights. The new agreements and rules, already in advanced negotiation, should represent a new opportunity for Renault Sport Racing and for Renault to take part in a more balanced, competitive sport. -
Formula One 1 Formula One
Formula One 1 Formula One Formula One Category Single seater Country International [1] Inaugural season 1950 Drivers 22 Teams 11 Constructors 11 Engine suppliers Cosworth · Ferrari · Mercedes · Renault Tyre suppliers Pirelli Drivers' champion Sebastian Vettel (Red Bull Racing) Constructors' champion Red Bull Racing [2] Official website www.formula1.com Current season Formula One Current season • 2013 Formula One season Related articles • History of Formula One • Formula One racing • Formula One regulations • Formula One cars • Formula One tyres Lists • Drivers • (GP winners • Champions • Runners-up) • Constructors • (GP winners • Champions • Runners-up) • Seasons • Grands Prix • Circuits • Race Promoters' Trophy winners • Points scoring systems • Engines • Tyres • National colors Formula One 2 • Sponsorship liveries • Racing flags • Red-flagged GPs • Fatal accidents • Drivers who never qualified • Female drivers • TV broadcasters • Video games Records • Drivers • (Wins • Poles • Fastest laps) • Constructors • (Wins) • Engines • Tyres • Races Organisations • FIA • FIA World Motor Sport Council • Formula One Group • Formula One Constructors Association • Formula One Teams Association • Grand Prix Drivers' Association Formula One, also known as Formula 1 or F1 and referred to officially as the FIA Formula One World Championship, is the highest class of single-seater auto racing sanctioned by the Fédération Internationale de l'Automobile (FIA). The "formula", designated in the name, refers to a set of rules with which all participants' cars must comply. The F1 season consists of a series of races, known as Grands Prix (from French, originally meaning great prizes), held throughout the world on purpose-built circuits and public roads. The results of each race are evaluated using a points system to determine two annual World Championships, one for the drivers and one for the constructors. -
Press Kit 2018 // FOREWORD
Press Kit 2018 // FOREWORD It is a great source of pride for Groupe Renault and its employees to see the Renault name once again working its way to the sharp end of Formula 1. Motor racing is an intrinsic part of the Renault DNA and from Formula E races in cities to rallying through to Formula 1, we have always achieved outstanding results. Renault Sport Formula One Team’s ambition is clearly to uphold the outstanding record of the past and the 2017 season has confirmed we are on the right track. We are a team on the rise. We have two very talented drivers who are hungry for results. Enstone is regenerated and the workforce has already increased by more than 35%. At Viry, our long-term commitment in several motorsport categories allows to develop a detailed plan for our facilities. Our investment has so far been successfully translated to the track as we rose from ninth to sixth in the Constructors’ Championship in 2017 and ended the year with the fourth fastest car. The success of the programme in just two years is testament to the resilient plan laid down early in the creation of the team and the strong job done by Cyril and the entire Renault Sport Racing teams. I am convinced year three will take us one step closer to the long-term aim: winning races and challenging for championships. We are equally satisfied with the results we are seeing off-track. Formula 1’s new owners, have developed various marketing initiatives that have enabled the sport to grow into an even bigger brand and engage more closely with fans; steps forward which are incredibly important for us as the only mass market car constructor in the sport. -
LOTUS:11 & Clubman Notes the Official Magazine of Lotus Club Victoria, Lotus Club Queensland Club Lotus Australia
17/11 December 2011 $8.00 LOTUS:11 & Clubman Notes The Official Magazine of Lotus Club Victoria, Lotus Club Queensland Club Lotus Australia Features: CLA & LCV Concours Tour de Goldfields Elite 1073 To start, the disclaimer: Carolyn Wilson & Gloria Wade At no time is there to be any interpretation of this article by Elise S2 owners, or owners of their derivatives, that an S1 Elise or an S1 Exige or a 340R is not the ultimate modern Lotus experience. Now that important point has been made, did I ever make comment about the glorious spring weather we have in SE Queensland? I can’t remember, but if I have never mentioned it, I should, it’s great. And it added to the relaxed state of the week-end at Cabarita, even though, as faithful Queenslanders, we had our doubts as to NSW being able to replicate our fabulous weather, at even so small a distance over the border into cockroach country and so much closer to the lands of the Mexican. We do respect the fact Mexicans don’t have particularly pleasant weather at any time of the year (which probably explains some club presidents not being able to CABARITA WEEKEND resist quoting results of some strange sporting code) thus, I always try to share our weather. 22 October 2011. By Clive Wade Sorry, I digress. The point of the article is to tell all you good folk, including our State of Origin losing friends in NSW, what a jolly good time we had in the far northern parts of NSW. -
It's All About the Passion
AUSTRIAN GP 21 June 2015 The Rosbergring IT’S ALL ABOUT THE PASSION AUSTRIAN GRAND PRIX 2015 Issue 169 The award-winning Formula 1 e-magazine is brought to you by: David Tremayne | Joe Saward | Peter Nygaard With additional material from Mike Doodson | Lise Nygaard LEADER 3 ON THE GRID BY JOE SAWARD 4 SNAPSHots 5 RENAUlt IN F1 - PAST AND FUTURE 18 NICO HULKENBERG, LE MANS WINNER 24 REMEMBERING MARK DONOHUE 28 THE HACK LOOKS BACK 36 AUSTRIA - QUALIFYING REPORT 39 AUSTRIA - RACE REPORT 55 AUSTRIA - GP2 AND GP3 70 THE LAST LAP BY DAVID TREMAYNE 74 PARTING SHot 76 © 2015 Morienval Press. All rights reserved. Neither this publication nor any part of it may be reproduced or transmitted in any form, or by any means, electronic, mechanical, photocopying, recording or otherwise, without the prior permission of Morienval Press. WHO WE ARE... ...AND WHAT WE THINK DAVID TREMAYNE is a freelance motorsport writer whose clients include The Independent and The Independent on Sunday newspapers. A former editor and executive editor of Motoring News and Motor Sport, he is a veteran of 25 years of Grands Prix reportage, and the author of more than 40 books on motorsport. He is the only three-time winner of the Guild of Motoring Writers’ Timo Makinen and Renault Awards for his books. His writing, on both current and historic issues, is notable for its soul and passion, together with a deep understanding of the sport and an encyclopaedic knowledge of its history. David is also acknowledged as the world expert on the history of land and water speed record breaking and is also passionate about Unlimited hydroplanes.