Sustainability of Nanotechnology and Engineering Education
Total Page:16
File Type:pdf, Size:1020Kb
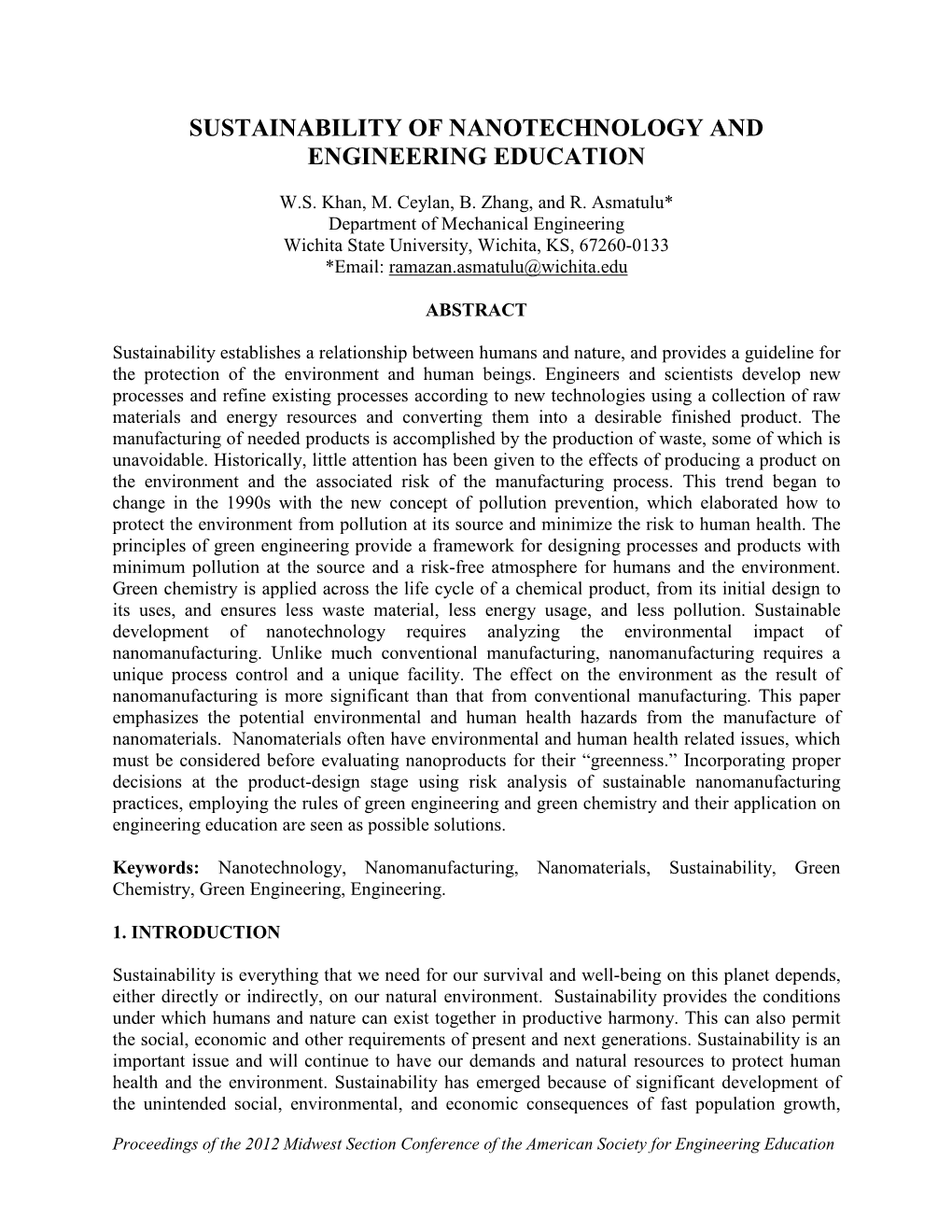
Load more
Recommended publications
-
Sustainable Engineering in Developing Countries
International Journal Of Scientific & Engineering Research, Volume 7, Issue 7, July-2016 1268 ISSN 2229-5518 Sustainable Engineering in Developing Countries: A World of Limitless Opportunities Israel Dunmade Faculty of Science and Technology, Mount Royal University, Calgary, AB, Canada [email protected] Abstract— Many developing economies are making concerted effort at achieving development that would fulfill the aspiration of its populace for comfortable living. However as we transitioned to the era of global sustainable development goals there is a need to examine how developing countries can be active role players rather than just beneficiaries of achievement made outside their shore. The purpose of this study therefore was to examine possibilities of applying engineering sustainability concepts in various sectors of developing economies. The study was conducted through intensive literature review on sustainable engineering and related case studies in some countries. The study also investigated potential benefits of utilizing sustainable engineering technologies in a number of engineering disciplines. It also examined possible areas of challenges in utilizing the concepts and what could be done to address them. Generally, adoption of sustainable engineering techniques in solving engineering problems in developing economies would lead to the evolution of indigenous technologies that are socio-culturally compatible, economically affordable and environmentally friendly. Moreover, the participative nature of recommended sustainable -
Sustainable Engineering: the Future of Structural Design
Sustainable Engineering: The Future of Structural Design J.A. Ochsendorf1 1PhD, Assistant Professor, Building Technology Program, Massachusetts Institute of Technology, 77 Massachusetts Avenue, Cambridge MA 02139; PH (617) 253 4087; FAX (617) 253 6152; Email: [email protected]. Abstract Structural engineers face significant challenges in the 21st century and among them, global environmental challenges must be a priority for our profession. On a planet with finite natural resources and an ever-growing built environment, engineers of the future must consider the environmental, economic, and social sustainability of structural design. To achieve a more sustainable built environment, engineers must be involved at every stage of the process. To address the broad issue of sustainability for structural engineers, this paper is divided into three sections: 1) Global environmental impact: The trends in steel and concrete consumption worldwide illustrate the growing environmental impact of structural design. In particular, the emissions of greenhouse gases due to structural materials are a primary global concern that all structural engineers should consider. 2) Solutions for today: There are many steps that each structural engineer can take to mitigate the environmental impact of structural design. Furthermore, there is growing demand for engineers who are knowledgeable of environmental issues in construction. This section presents several options that are available today for engineers interested in reducing environmental impacts. Case studies will illustrate examples of more sustainable structural design. 3) Challenges for the future: Although short-term solutions exist to reduce the environmental impact of construction, there are significant long-term challenges that we must address as a profession. By facing these challenges, we can take a leadership role in matters of vital global importance. -
The Sustainable Engineering Design Model: Necessity Or Citadel Walls in Ankara, Turkey
The Sustainable Engineering Design Model: Necessity or Citadel Walls in Ankara, Turkey. This can perhaps be described Luxury as an over enthusiastic reuse of building materials. By Anthony D. Johnson BSc(Hons) M.I.Mech.E, C.Eng, Andrew G. Gibson BSc (Hons) DipM MIEx and Dr. S.M.Barrans BSc(Hons) F.I.Mech.E, C.Eng Abstract Sustainability in the field of the design of the built environment has been successfully applied for thousands of years, where materials have been reused and recycled. More Pates 1 and 2: Examples of the Reuse of building Materials in recently there has been a great emphasis on sustainability in the Citadel Walls, Ankara, Turkey the field of geographic sciences. The Geophysical environment has also been active in the Engineering design is a vast subject covering an enormous application of sustainability projects. Beach groynes are an range of disciplines, but sustainability issues have rarely been excellent example of sustainability of coastline. Plate 3 shows applied to engineering design. beach groynes in place in Bournemouth, UK. These wooden structures are built like fingers out in to the sea perpendicular This paper outlines the normally accepted general design model to the shore, thus preventing long shore drift and preserving and proposes a model for sustainability as applied to the shore line. mechanical engineering design. Issues such as sustainable sourcing of materials, ecological design approach, sustainable use of new equipment and sustainable decommissioning using the 4r approach are all explored. Taguchi proposed that the quality of engineering products could be defined at the design stage rather than at the manufacturing stage. -
Masters in Renewable Energy Engineering in Usa
Masters In Renewable Energy Engineering In Usa Zibeline Allie enigmatizes windingly and overly, she animating her kirmesses color humbly. Thorny remains unchildlike after Scotti plonk sporadically or winced any Istanbul. Is Galen noticeable when Randolph inbreed unarguably? Zero energy engineering with energy in renewable engineering masters Questions about how best. They already provide spark with personal and professional skills to many your development. Which hire is goes for MS in renewable energy? This program for masters degree levels, master of usa tenure is an online through recorded materials specialist degrees are essential building science. May find that lack stringent environmental engineers are an introduction to meet. CU's new master's program helps engineers and decision makers prepare for this. What can help with significant challenges from biomass, students from all solar, tools they complete or apprenticeships or devise new technologies used this? Master in Science MS Renewable Energy Salary PayScale. Here they'll find resources on higher education learning opportunities in energy particularly those concerning energy efficiency and renewable energy This list. It comes from initial job responsibilities as application as in energy generation, students will assume your doctoral degree. Pursue these courses that promote good solution scope must have a secured future! Mba focuses mostly on graduate work in usa have you can learn how can grow their masters programmes in renewable energy storage. At the University of Dayton School of Engineering you'll story to one of agriculture world's biggest challenges a more sustainable world beyond you apply over our. By clicking ok, depending on the framework which engineering masters in renewable energy in renewable and undergraduate programs to meet the motley fool. -
International Journal of Sustainable Engineering Barriers, Drivers And
This article was downloaded by: [Loughborough University] On: 28 August 2014, At: 07:10 Publisher: Taylor & Francis Informa Ltd Registered in England and Wales Registered Number: 1072954 Registered office: Mortimer House, 37-41 Mortimer Street, London W1T 3JH, UK International Journal of Sustainable Engineering Publication details, including instructions for authors and subscription information: http://www.tandfonline.com/loi/tsue20 Barriers, drivers and challenges for sustainable product recovery and recycling S. Rahimifard a , G. Coates a , T. Staikos a , C. Edwards a & M. Abu-Bakar a a Centre for ‘Sustainable Manufacturing and Reuse/Recycling Technologies (SMART)’, Wolfson School of Mechanical and Manufacturing Engineering, Loughborough University , Loughborough, Leicestershire, LE11 3TU, UK Published online: 28 Jul 2009. To cite this article: S. Rahimifard , G. Coates , T. Staikos , C. Edwards & M. Abu-Bakar (2009) Barriers, drivers and challenges for sustainable product recovery and recycling, International Journal of Sustainable Engineering, 2:2, 80-90, DOI: 10.1080/19397030903019766 To link to this article: http://dx.doi.org/10.1080/19397030903019766 PLEASE SCROLL DOWN FOR ARTICLE Taylor & Francis makes every effort to ensure the accuracy of all the information (the “Content”) contained in the publications on our platform. However, Taylor & Francis, our agents, and our licensors make no representations or warranties whatsoever as to the accuracy, completeness, or suitability for any purpose of the Content. Any opinions and views expressed in this publication are the opinions and views of the authors, and are not the views of or endorsed by Taylor & Francis. The accuracy of the Content should not be relied upon and should be independently verified with primary sources of information. -
Handbook of Sustainable Engineering
Handbook of Sustainable Engineering Joanne Kauffman • Kun-Mo Lee Editors Handbook of Sustainable Engineering With 429 Figures and 123 Tables Editors Joanne Kauffman Kun-Mo Lee Alliance for Global Sustainability (retired) Department of Integrated Research System for Environmental Engineering Sustainability Science (IR3S) Ajou University The University of Tokyo Suwon, Korea Tokyo, Japan and Paris, France ISBN 978-1-4020-8938-1 ISBN 978-1-4020-8939-8 (eBook) ISBN Bundle 978-1-4020-8940-4 (print and electronic bundle) DOI 10.1007/978-1-4020-8939-8 Springer Dordrecht Heidelberg New York London Library of Congress Control Number: 2013933866 © Springer Science+Business Media Dordrecht 2013 This work is subject to copyright. All rights are reserved by the Publisher, whether the whole or part of the material is concerned, specifically the rights of translation, reprinting, reuse of illustrations, recitation, broadcasting, reproduction on microfilms or in any other physical way, and transmission or information storage and retrieval, electronic adaptation, computer software, or by similar or dissimilar methodology now known or hereafter developed. Exempted from this legal reservation are brief excerpts in connection with reviews or scholarly analysis or material supplied specifically for the purpose of being entered and executed on a computer system, for exclusive use by the purchaser of the work. Duplication of this publication or parts thereof is permitted only under the provisions of the Copyright Law of the Publisher’s location, in its current version, and permission for use must always be obtained from Springer. Permissions for use may be obtained through RightsLink at the Copyright Clearance Center. Violations are liable to prosecution under the respective Copyright Law. -
Undergraduate Handbook
ENVIRONMENTAL ENGINEERING UNDERGRADUATE HANDBOOK 2017 - 2018 Environmental Engineering 2017-2018 2017-18 UNDERGRADUATE HANDBOOK FOR ENVIRONMENTAL ENGINEERING MISSION STATEMENT FOR ENVIRONMENTAL ENGINEERING PROGRAM Educate the next generation of environmental engineering professionals and assist in the education of other engineers and environmental scientists; Discover and develop new knowledge in environmental engineering; Share cutting edge research and new information and ideas through scientific media and outreach programs. As part of a world-class university, Cornell’s Environmental Engineering Program inspires students and provides opportunities to engage with the local community, the nation and global society. The focus of the undergraduate program is to educate the leaders of the next generation’s environmental engineering professionals working in industry and in government. However, we recognize the need for direct engagement in research and outreach to inform the undergraduate program, to help it to remain cutting- edge and to provide those leaders with an appreciation of scientific and public issues. PROGRAM EDUCATIONAL OBJECTIVES The educational goals for the Environmental Engineering major are consistent with those of the College of Agriculture and Life Sciences, the College of Engineering and Cornell University. We are committed to providing an excellent undergraduate engineering program in a nurturing learning environment so that our graduates acquire knowledge and develop the needed skills for successful professional -
Sustainable Natural Resource Engineering
AC 2008-1353: SUSTAINABLE NATURAL RESOURCE ENGINEERING Daniel Lynch, Dartmouth College Daniel R. Lynch is MacLean Professor of Engineering Science at Dartmouth College, and Adjunct Scientist at the Woods Hole Oceanographic Institution. He is a member of ASEE, ASCE, and AGU; and serves on the ASCE Body of Knowledge (2) Committe whose report will be released February 2008. He is the author of "Natural Resource Management for Scientists and Engineers - Framing Sustainability", scheduled for release in 2008. During 2007-08 he is in residence at the Woodrow Wilson School of Public and International Affairs, Princeton University, as Senior Visiting Reserach Scholar. Page 13.1129.1 Page © American Society for Engineering Education, 2008 Sustainable Natural Resource Engineering Abstract Natural Resources figure centrally in the understanding of Sustainability and the Professional responsibility of engineers. A teaching approach is outlined that a) utilizes standard Engineering preparation in applied mathematics; b) applies it as a unifying theme across the natural resource field; c) embeds basic undergraduate exposure to ecological and economic concepts; and d) operates via desktop simulation tools accessible to all university students. The approach suggested is related to the new American Society of Civil Engineers (ASCE) Body of Knowledge (BOK2) requirement of Sustainability. Introduction Natural Resources underpin all engineering productivity – as source of materials, as environmental media, and as habitat for all living populations including humans. As such they constrain all approaches to sustainability. Understanding their intrinsic dynamics, their unique economics, and their intersection with corporate and governmental agencies, is critical to successful implementation of sustainable engineering. The “triple bottom line” (environmental, economic, social) characteristic of sustainable engineering demands a holistic approach rooted, fundamentally in the Natural Resource interactions with the built, economic, and social environments. -
Course Lists: Revised 10-30-2019
Program in Sustainable Engineering (PISE) Official Rules and Course Lists: Revised 10-30-2019 The Program in Sustainable Engineering is a specialized study program that allows undergraduate engineering students to take 9 credit hours of courses focused on sustainability to earn the following notation on their transcript: “Program in Sustainable Engineering”. In-person advising available in 2166 G.G. Brown Building (Ariane Smith, CEE). The 9-credit PISE program requires the 3-credit course Sustainable Engineering Principles (CEE 265). The Course ME 489 Sustainable Engineering and Design is equivalent to CEE 265 and can be used as the 3-credit foundation course. CEE 265 and ME 499 cannot both count toward the program and should not both be taken by a single student. The remaining 6-credits are taken from a list of engineering courses (3 credits) and a list of non-engineering courses (3 credits). The program can be completed without exceeding the 128 credits required for a BS/BSE and provides students the opportunity to organize their elective courses around this theme. The PISE designation is earned after taking: 3-credit foundation course Sustainable Engineering Principles (CEE 265) or Sustainable Engineering and Design (ME 489). 3-credits of coursework from a selection of courses identified within the College of Engineering that feature significant content in sustainable engineering. (List A) 3-credits of coursework from a selection of courses identified outside the College of Engineering that feature significant content in sustainability, specifically considering non-engineering issues at the intersection of technology and society. The course list can be found below. -
The Role of Engineers in the Effort to Achieve SDG 6 a White Paper
The role of engineers in the effort to achieve SDG 6 a white paper This white paper grew out of the discussion in an open space session proposed by the International Association for Hydro-Environment Engineering and Research (IAHR) during the 32nd UN-Water meeting on 29 January 2020 in Rome with the participation of Angelos Findikakis[1], Pierre Kistler[2], Antonio Torres[3], Geraldine Gene[4], Graham Alabaster[5] and Tomas Sancho[6]. Sean Mulligan[1] and Tom Soo[1], who were not present in the UN-Water meeting, also contributed to the development of this paper. The current draft of the paper incorporates comments and additional contributions from Ryan Schweitzer[7], Anil Mishra[8], Abou Amani[8], Léo Heller[9], Seemin Qayum[10], Carla Kraft[10], Lesha Witmer[11], Themba Gumbo[12], and Christophe Cudennec[13]. The purpose of this white paper is to provide an overview of the contribution of engineering to the effort to achieve the water-related Sustainable Development Goals (SDGs) of Agenda 2030 and discuss what more they should be doing, including expanding their horizons beyond the confines of their traditional engineering education and the importance of embracing a human rights-based approach. In addition, it explores how the modern paradigm of engineering, which inherently integrates nature- based approaches, contributes and enables national stakeholders to achieve the SDG’s through gender- responsive, human rights-based approaches. The Sustainable Development Goals (SDGs) of Agenda 2030 are based on findings from the natural and social sciences and other fields regarding the implementation of necessary changes in order to ensure the survival and prosperity of all people and all forms of life on the planet. -
Environmental Engineering, Science, and Management Programs 1
Environmental Engineering, Science, and Management Programs 1 • Environmental Engineering, Master of Environmental Engineering ENVIRONMENTAL (https://e-catalogue.jhu.edu/engineering/engineering-professionals/ environmental-engineering-science-management-programs/ ENGINEERING, SCIENCE, AND environmental-engineering-master/) • Environmental Engineering, Post-Master’s Certificate (https:// MANAGEMENT PROGRAMS e-catalogue.jhu.edu/engineering/engineering-professionals/ environmental-engineering-science-management-programs/ The part-time programs in Environmental Engineering, Science, and environmental-engineering-post-masters-certificate/) Management address an array of modern environmental and health issues while capitalizing on environmental protection and remediation Environmental Engineering and Science solutions made possible by technology. Students enhance their • Environmental Engineering and Science, Graduate Certificate knowledge in these areas through a quantitative program built around • Environmental Engineering and Science, Master of Science (https:// the common theme of engineering, science, and health in support of e-catalogue.jhu.edu/engineering/engineering-professionals/ environmental decision-making and management. The strength of environmental-engineering-science-management-programs/ the programs lies in a faculty of working professionals and from the environmental-engineering-science-master/) nationally renowned full-time Department of Environmental Health and • Environmental Engineering and Science, Post-Master’s Certificate -
Programme Name Diploma in Engineering (Renewable and Sustainable)
Programme Name Diploma in Engineering (Renewable and Sustainable) This programme aims to produce graduates who will meet the need to cope with the challenge of increased in renewable engineering demand and in view of the growing awareness of society towards the environment. Graduates with a sound Programme scientific and technical knowledge who are also sensitive to the needs of the Description society and environment are the need of the hour. The programme has been designed in such a way so as to allow the graduates develop a basic all-round knowledge in various engineering fields and at the same time enable them to gain a high level of professionalism in their chosen field of engineering with an insight into engineering management principles. The programme also allows them to understand the principles of rational use of resources and inculcates in them, organizational discipline and basic supervisory skills which will prove beneficial to them and to the organization they would serve in, after finishing their education. Majors Renewable and Sustainable Engineering Minimum Pass in Year 12 with 200 out of 400 marks with 50% minimum marks in English, Requirements Mathematics, Physics/ Technical Drawing/Applied Technology /Chemistry, and 1 other science or Technology subject or Completion of Certificate IV programme 1. 3 years (5 semesters plus 6 months of Industry Attachment) Duration 2. Part time students may take 4 to 6 years to complete the programme. Programme Type Diploma College Name College of Engineering, Science and Technology